推进 OOA 注入的翼盒
由于航空航天业预计将从 COVID-19 大流行中恢复过来,之前对高速生产的推动已转向紧急推动以减少对地球和人类的环境威胁。这项工作包括限制温室气体 (GHG) 排放、能源和水的使用以及产生无法回收的废物。尽管这些举措是在 COVID 之前持续进行的,但现在它们的重点得到了提高,因为生产复合结构的成本要低得多。 Clean Sky 2 泛欧航空计划资助了所有这些领域的研究和开发,并显着推进了各种纤维增强复合材料技术。
Clean Sky 2 的第七次提案征集(CFP07,2017 年 10 月)中包括空中客车防务与航天公司(Airbus DS,西班牙加的斯)对创新和灵活的试验工厂的要求,以使用自动化光纤生产高度集成的翼盒飞行演示器放置(AFP)和液体树脂灌注。
还有其他注入树脂和/或非高压釜 (OOA) 机翼盒演示器,包括 GKN Aerospace(英国雷迪奇)于 2013 年推出的 OOA“混合”机翼盒;由北爱尔兰贝尔法斯特 Spirit AeroSystems 公司生产的空中客车 A220 机翼在高压釜中使用树脂转移灌注;以及 AeroComposit(俄罗斯莫斯科)为 MS-21 生产的 OOA 机翼 喷气式客机。然而,所有这些都使用机械紧固件组装了离散的复合材料纵梁加强型蒙皮和翼梁(参见“使用最少紧固件实现 OOA 机翼的途径”)。
空中客车 DS 在 Clean Sky 2 中要求的翼盒向前迈进了一步,将加强的下蒙皮与加强的前后翼梁相结合,从而实现更完整的模块 紧固件将与剩余的机翼组件一起送出组装。
这种翼盒也将使用窄(0.25 或 0.5 英寸宽)干碳纤维带和高温 (180°C Tg) 固化树脂,但具有节能、低成本的加热系统和基于传感器的数字控制和模拟来预测和管理过程,缩短开发过程中的试错循环,并实现对制造人员的快速培训。这种数字化将演变为包括增强现实移动应用程序 (app),该应用程序还提供用户和维护手册、流程序列定义、无纸化流程和零件跟踪以及将 CATIA 模型投影到零件上,以帮助精确放置加强筋预制件、模具插件和碳纤维增强聚合物(CFRP)垫板。
也许最苛刻的是,该项目要求所有模具和制造设备都具有便携性和灵活性,易于在任何制造现场部署,并且随着更先进的模具、加热和复合材料 4.0 过程控制技术的出现,能够适应其他零件设计和升级。
正如 Airbus DS 复合材料开发工程技术和工艺负责人 Luis Rubio 所解释的那样,“该项目的最终目的是证明一种替代技术(预浸料和高压釜)具有更低的成本、更短的交货时间和环境足迹可以达到类似的设计公差和质量水平。”
MTorres(Torres de Elorz,西班牙)回应,申请时没有合作伙伴。 “我们拥有所有内部能力:AFP、灌注、干胶带材料和自动化,”MTorres 复合材料应用技术高级经理 Sebastian Diaz 解释说。该公司获得了创新输液机身制造系统 (IIAMS) 项目,该项目由欧盟地平线 2020 计划根据第 820845 号赠款协议提供资金,并于 2018 年 10 月开始工作。
外翼盒演示器
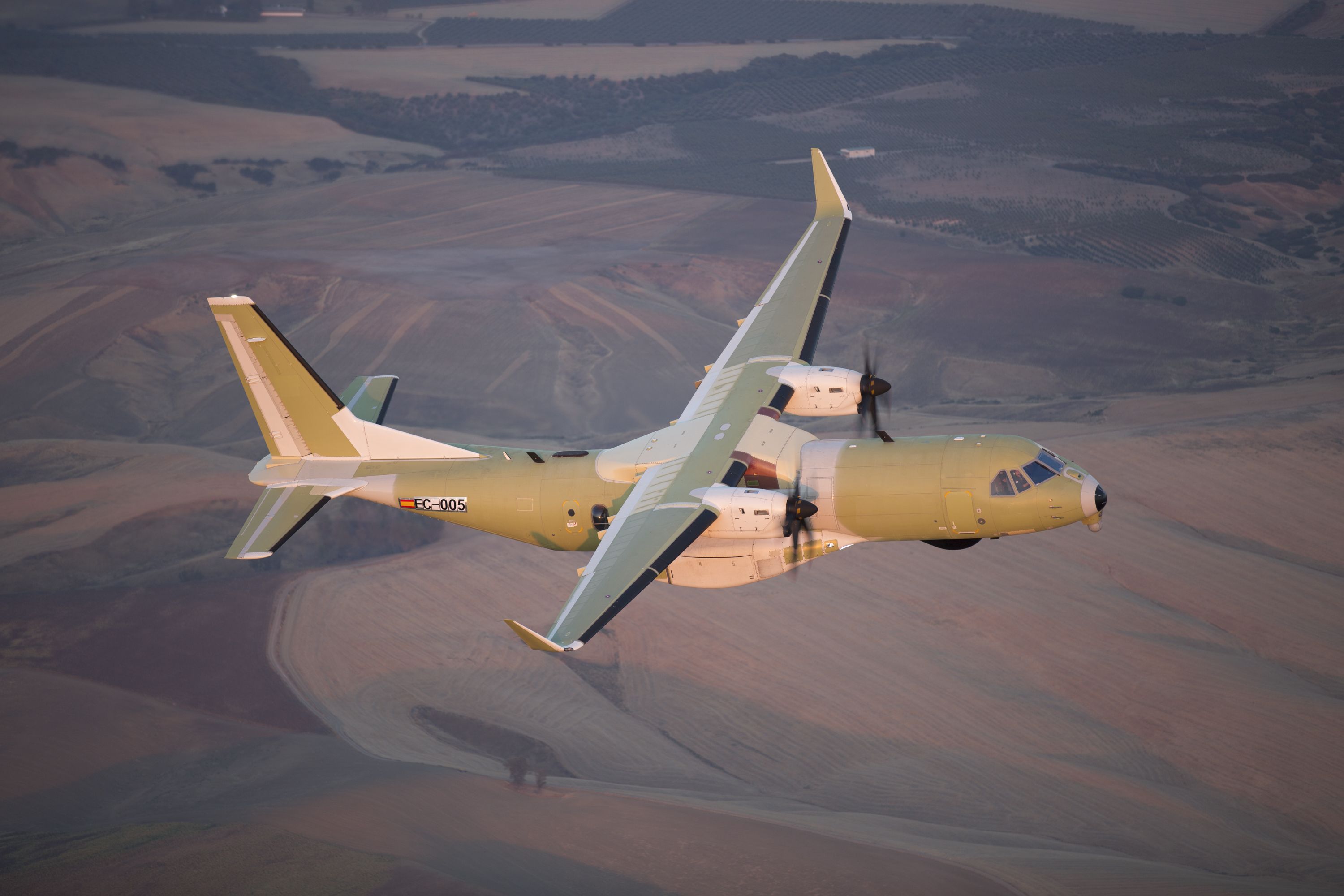
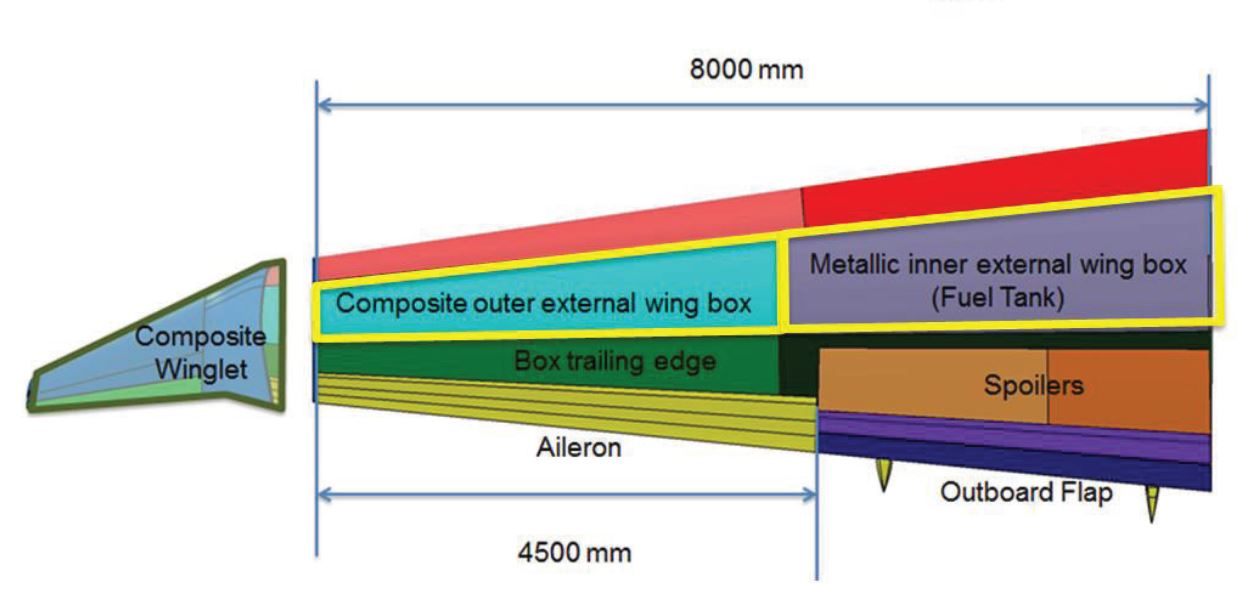
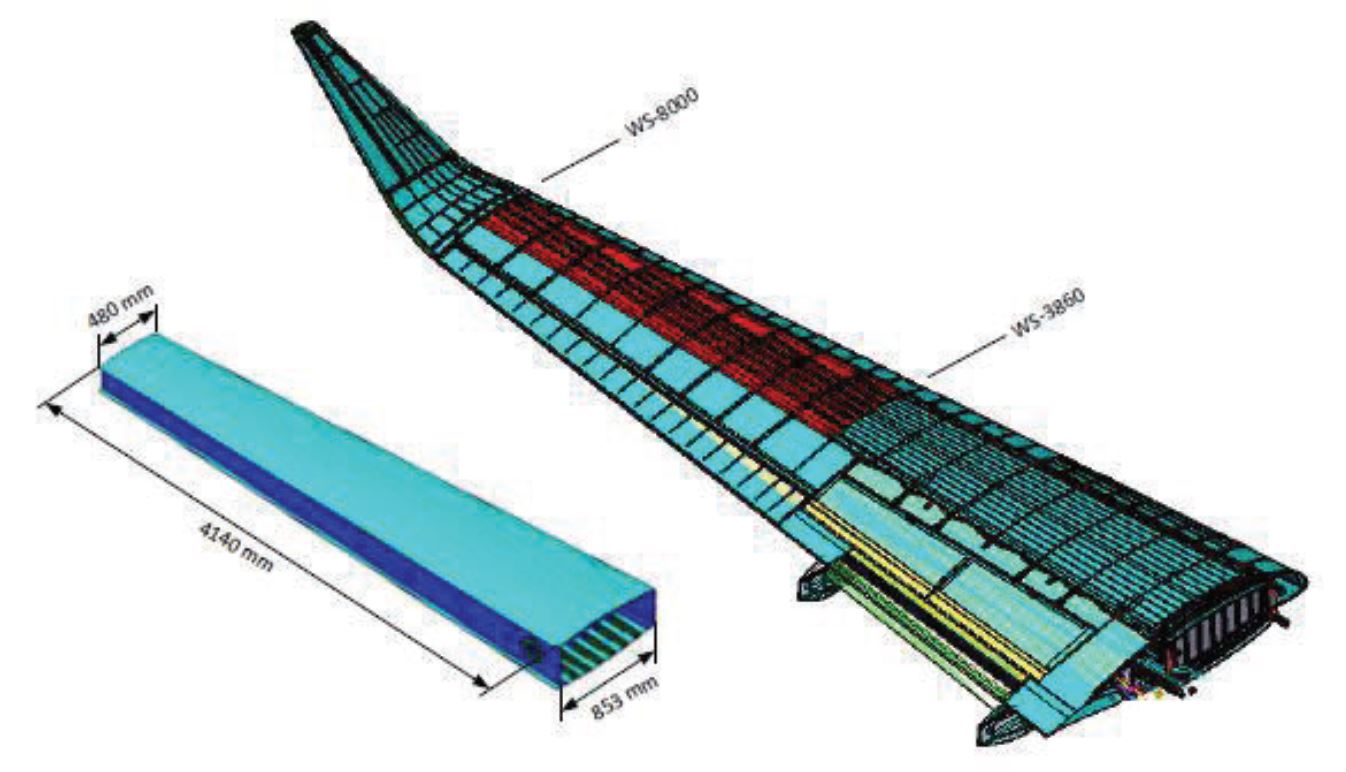
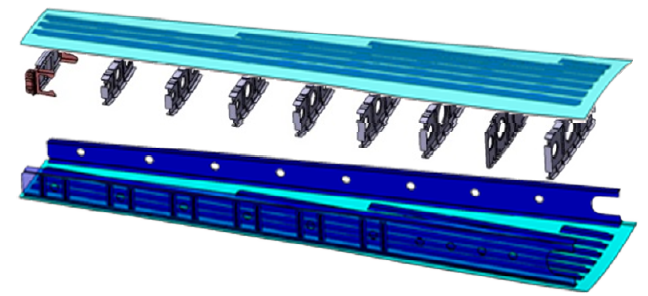
空中客车 DS 选择的演示机是基于其 C-295 双涡轮螺旋桨军用运输机(图 1)的外翼盒,在西班牙塞维利亚的圣巴勃罗生产。这个 4.14 米长的复合材料外侧扭矩箱与内侧金属配合 扭力箱。复合材料翼盒还与小翼、前缘和后缘相连。
“我们要制造两架 4 米长的演示机,左右翼,将安装用于飞行试验,”迪亚兹说。 “制造是一个一次性过程,没有二次粘合。我们只制作了“U”,包括带有六个集成纵梁的下蒙皮和每侧的翼梁。蒙皮、纵梁和翼梁的厚度各不相同。翼梁的 J 形及其加强筋的集成在制造过程中非常具有挑战性。我们还面临着如何通过这种制造过程保持严格的公差和精确的几何形状的挑战。这种精度至关重要,尤其是在组装到内翼盒和小翼的根部。”
创新的工业制造设计由 Mtorres 开发,而 Airbus DS 提供零件设计规范。 “我们轻松地合作设计了最佳制造工艺,验证了我们的工艺可以生产这种设计,反之亦然,”迪亚兹说。
自动热灌注中心 (ACTI)
根据空客 DS 规范,用于生产翼盒的所有工具和制造设备必须是便携式的,能够使用标准车辆运输到其他设施,并且无需特殊措施即可快速设置。这导致了自动化热灌注中心 (ACTI) 的发展,该中心执行纵梁和翼梁的热悬垂成型;注入纵梁、翼梁和皮肤;和治愈周期。热悬垂成型 (HDF) - 开发为航空结构中的加热减瘤和航空航天外的加热预成型 - 去除叠层中的空隙并将纵梁和翼梁的二维坯料转换为成型的预成型件(参见“热悬垂成型”)。
ACTI 的有用内部区域大约为 5.5 x 2.2 米,看起来类似于传统的 HDF 系统,具有钢框架和电子升降的上半部分,配有锁定和其他安全装置。固化工具和多个热悬垂成型工具位于 ACTI 内部。 “没有施加压力,只有真空,”迪亚兹指出。 “ACTI 使用带有气流的加热空气,该气流被定义为在热悬垂成型和灌注过程中提供快速的热传递。”
他还指出,该系统是自动调平的。 “ACTI 结构(和固化工具)的刚度设计为在仅两个支撑部分的简单支撑条件下符合操作负载下的公差,”迪亚兹解释说。 “这意味着放在地板上时尺寸精度保持不变,无需进一步调平或其他几何调整。 ACTI 还具有低能耗和低制造成本的特点。”
后者在很大程度上是由于用多个预成型件的组装代替了多个固化部件的组装,然后将它们灌注并固化成单个集成结构。 “固化工具也是组装工具,”迪亚兹说。 “所有元件都是组装到固化工具中的干燥预成型件,然后在单次注射过程中共同注入。”不需要装配夹具,并且通过工具中的创新元素实现了严格的公差。
这种方法的另一个关键方面是去除破坏性和非破坏性测试 (NDT),而是依靠在各个制造步骤中收集的过程数据来验证过程质量并标记不合规格的参数。与 ACTI 一起使用的传感器收集温度、真空、树脂流动和固化状态。 “空气温度和零件温度都受到监控,”迪亚兹说。 “该工具集成了热电偶,可以跟踪模具和零件表面的温度。”所有数据都被记录、分析并用于打印图表并帮助指导制造决策。
“无论是在 IIAMS 中还是在未来的项目中,数据都有助于在早期阶段改进流程设置,”迪亚兹解释说。使用直接安装在 CFRP 固化工具中的 Netzsch(Selb,德国)介电传感器监测树脂流动和固化状态。 “我们需要非接触式皮肤传感器,因为树脂和模具之间没有直接接触,”迪亚兹说。 “当树脂到达时,传感器会监测介电场的变化,然后在固化过程中变成固体。我们使用这些数据来缩短治愈周期。”
在项目后期,传感器和 ACTI 与 MTorres 开发的人机界面 (HMI) 相结合,允许从计算机进行真正的过程控制,包括真空和温度,以及通过进料阀的树脂流动。据空客 DS 称,其目标是通过使流程更加精简和智能,促进集成复合材料主结构的大规模生产。
轻量级工具和便携性
Mtorres 生产了两套模具——一套用于右翼,一套用于左翼。 “具有相同几何形状的零件,如加强筋,只有一组,”迪亚兹指出。 “尽可能共享其他工具。”
使用单一的一体式固化工具形成皮肤的 3D 形状,所有其他预制件都位于其上。迪亚兹说,该工具的左右版本长约 4.5 米,是使用 CFRP 制成的。 “这使得保持公差变得更容易,因为我们设计的工具与零件采用相同的铺层和加工工艺,因此 CTE 非常接近最终零件的 CTE。这些 CFRP 固化工具也很轻,大约 200 公斤,因此可以用小型电动叉车移动。如果我们将金属用于 4.5 米长的工具,这是不可能的。”
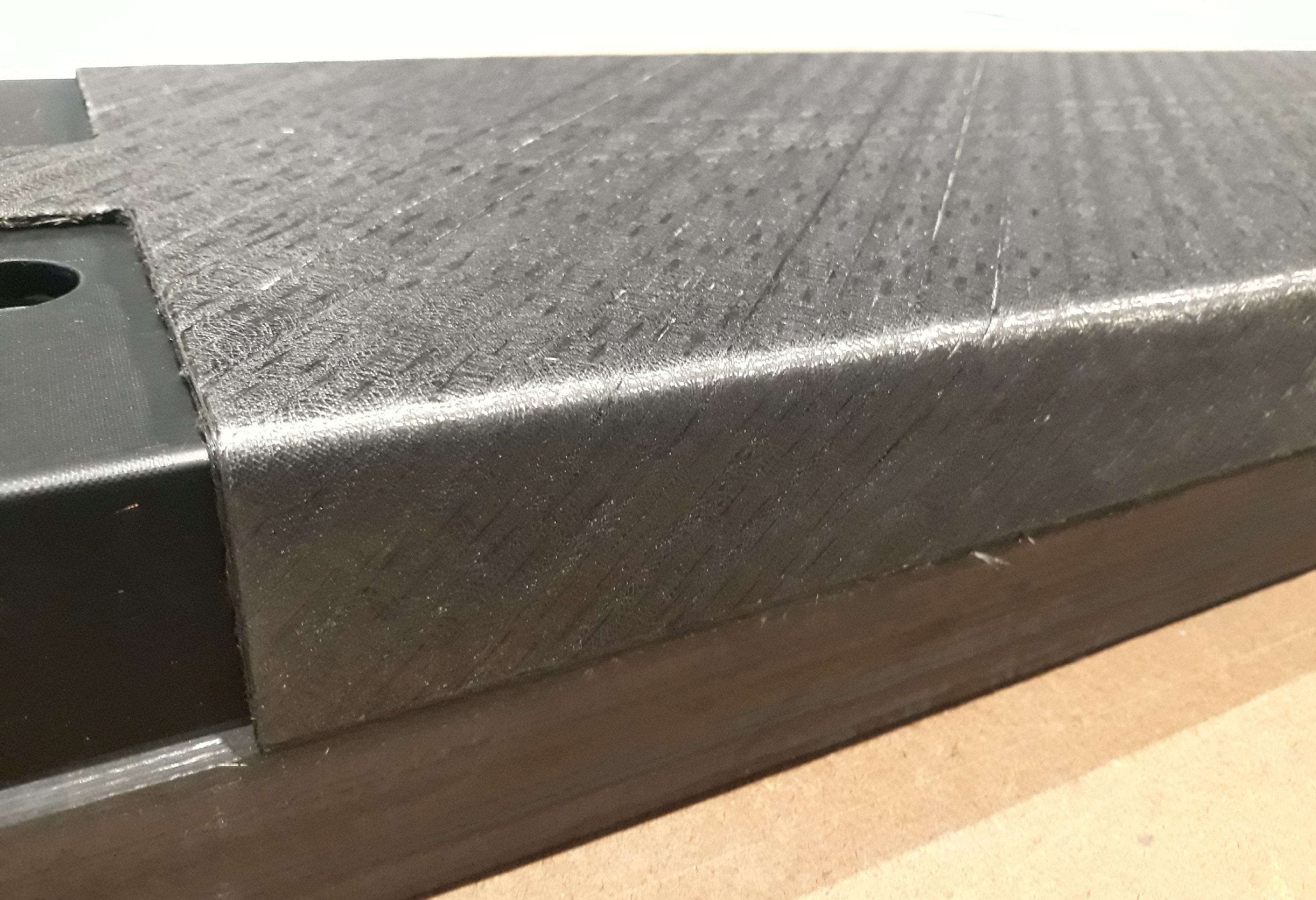
其余的工具 - 衬板、定位器和 HDF 工具 - 可以轻松地手动管理。纵梁、翼梁和翼梁加强筋预制件的 HDF 使用男性 (IML) 工具,也由 CFRP 制成。在使用过程中,它们被安装在铝制桌子上并设置在 ACTI 内。
AFP 使用新型干纤维胶带
所有翼盒结构元件——蒙皮、纵梁、翼梁、翼梁加强筋——都是使用 Mtorres AFP 技术生产的干纤维带。 “提案电话说使用快速和廉价的材料,”迪亚兹说。 “但是市售的干纤维胶带,尤其是来自较大供应商的干纤维胶带并不那么容易购买,我们拥有制造自己材料的专业知识(参见“用于液态模塑复合材料的新型干胶带”)。因此,我们使用了由 Mitsubishi Rayon(日本东京)50K 高强度 (HS) 纤维制成的 0.5 英寸宽、每平方米 300 克 (gsm) 的干碳纤维胶带。我们的胶带经过精心设计,可在输注过程中以及在使用我们的 AFP 头进行叠层过程中促进并表现良好。我们知道 AFP 叠层、热悬垂成型和树脂灌注的所有参数,如果我们需要进行任何小的更改,我们可以,因为我们有可用的胶带生产线。”
MTorres 还使用 Hexcel(法国 Les Avenières)的 200gsm 胶带测试了其翼盒制造工艺,该胶带由其中间模量 (IM) 纤维制成。 “虽然我们的工艺可以很好地处理两种类型的胶带,”迪亚兹说,“在开发阶段,与市售材料相比,使用我们的材料铺设更容易、更便宜——宽度和刚度经过精心设计,使其性能从到桌子上的线轴顺畅而快速。它也很容易获得。”

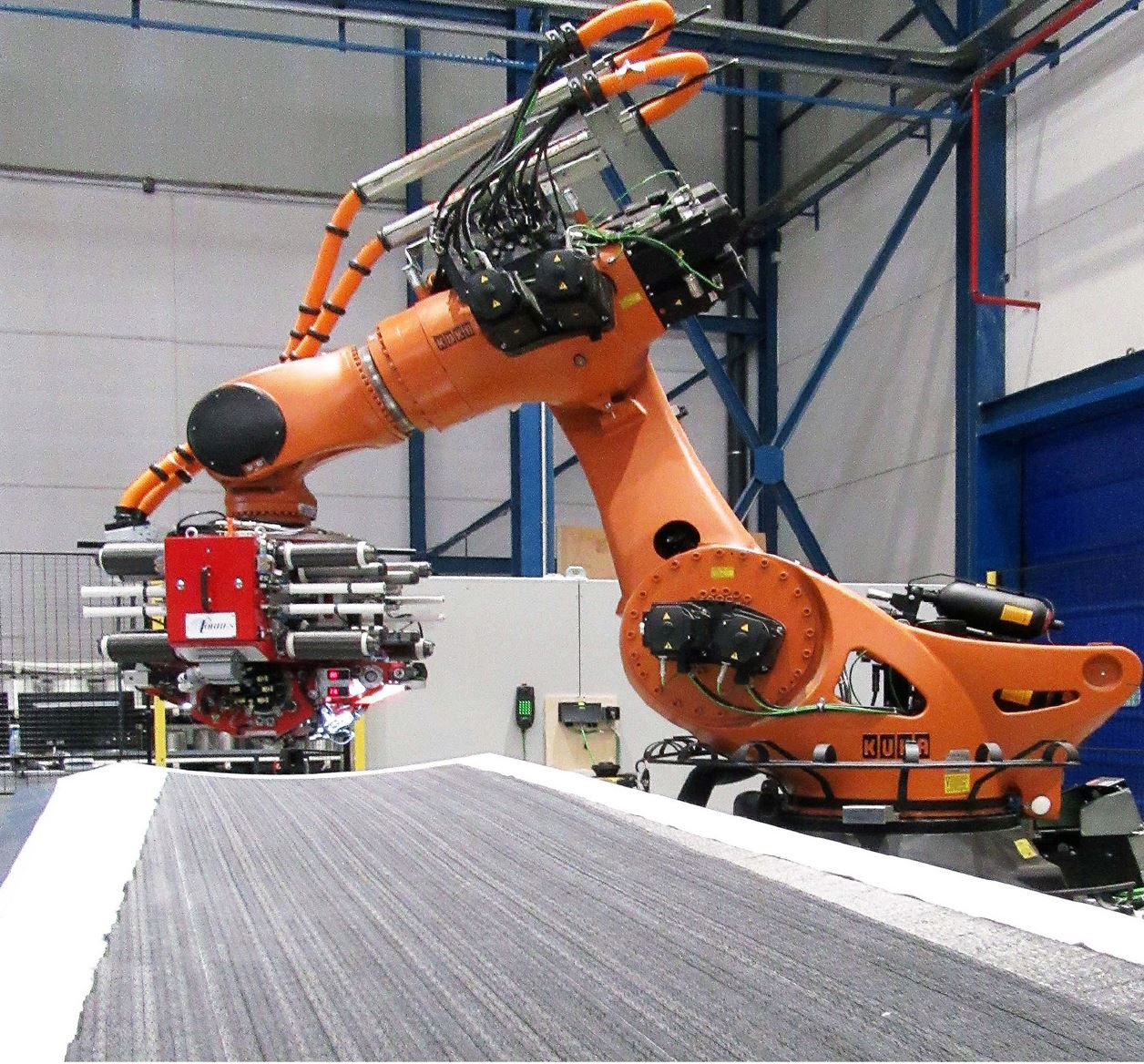
第 1 步。 AFP 用于铺设翼盒蒙皮(如图所示)以及用于纵梁、翼梁和翼梁加强筋的 2D 毛坯。 照片来源,所有步骤: IIAMS 项目,空中客车防务与航天,MTorres。
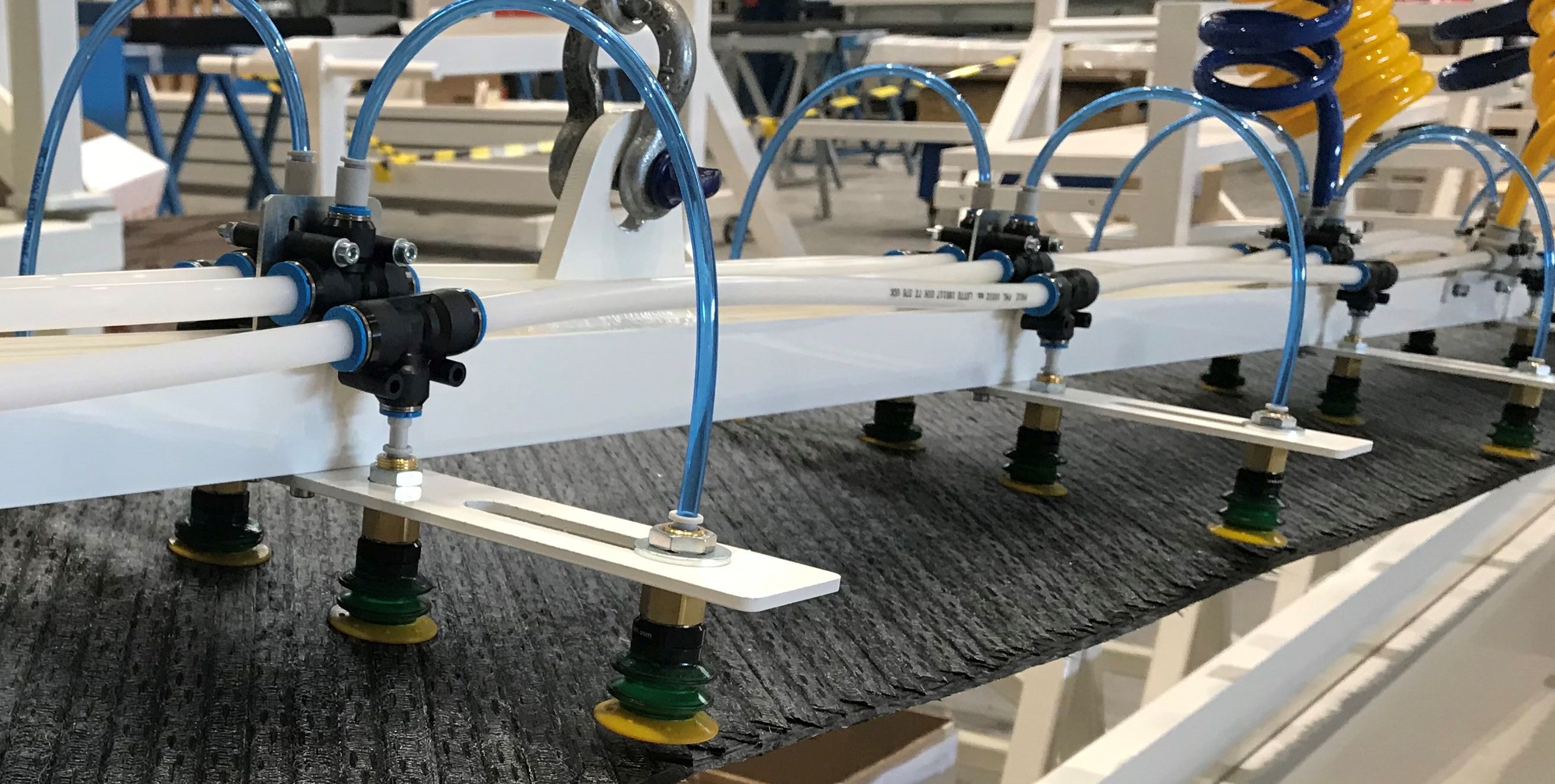
第 2 步。 平带坯料从铺叠台运送到热悬垂成型工具。
他指出 AFP 遵循了两种策略:一种用于下蒙皮,另一种用于纵梁、翼梁和翼梁加劲肋。将皮肤(3-6 毫米厚)铺设到固化工具顶部的最终 3D 形状(步骤 1),使用 一种半透膜——空中客车公司在其真空辅助工艺 (VAP) 灌注中获得专利。将纵梁、翼梁和翼梁加强筋作为扁平坯料 (2D) 放置在真空台上,然后移动到 HDF 工具上以实现其最终的 3D 形状(步骤 2)。
加热预成型
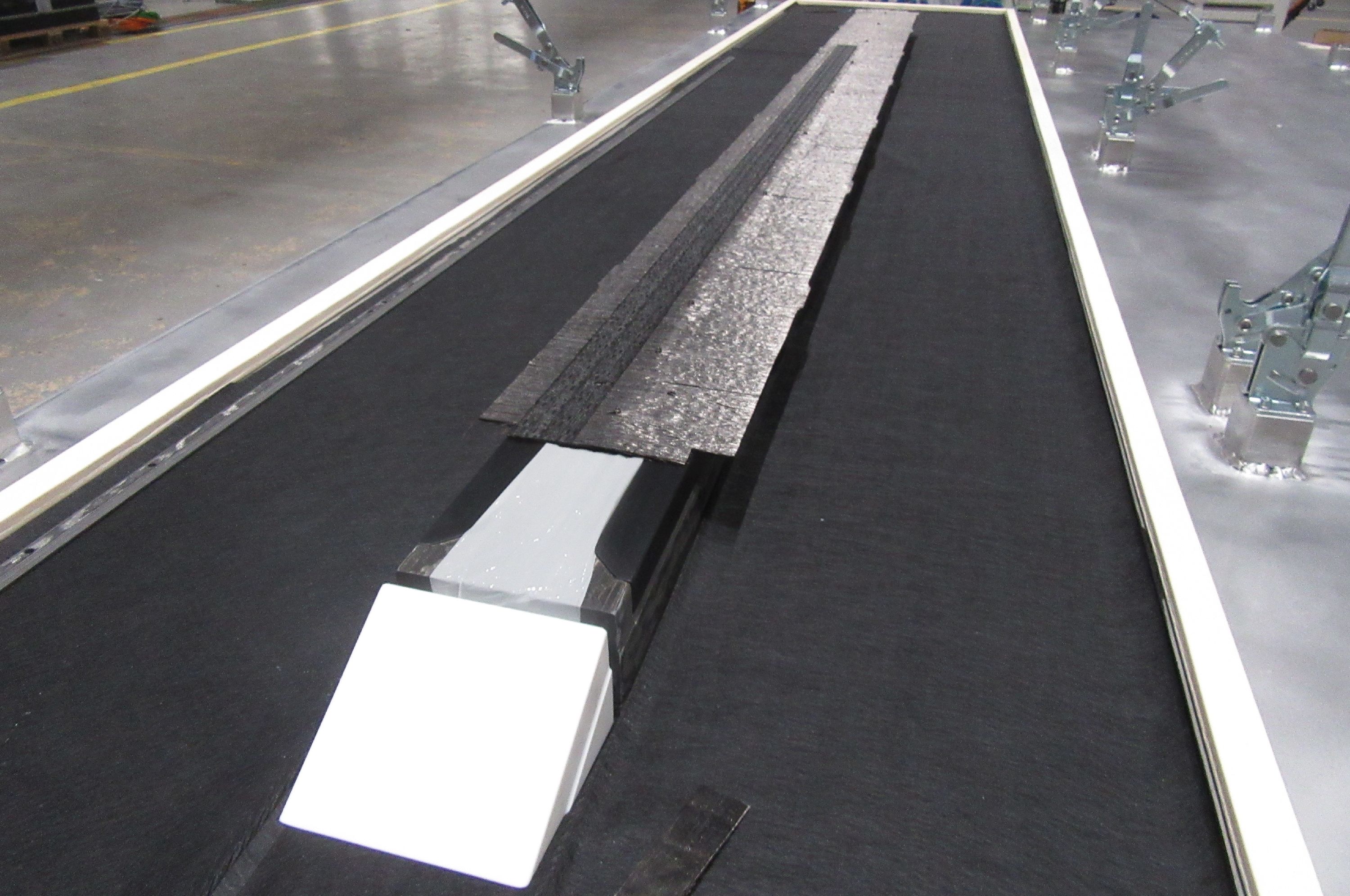
第 3 步。 纵梁毛坯放置在公 HDF 工具的顶部。
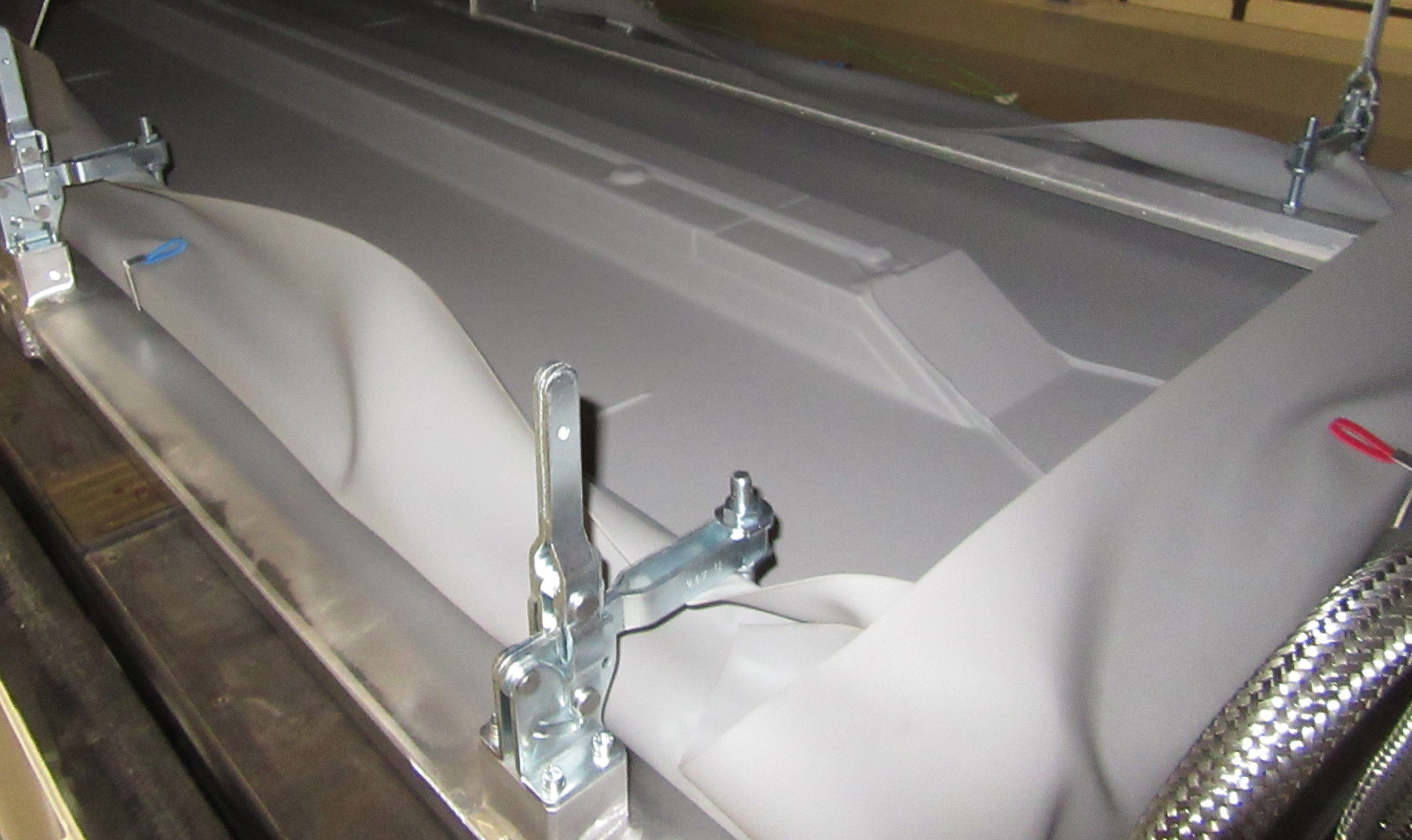
“我们使用带有真空夹具的龙门将用于纵梁、翼梁和翼梁加强筋的扁平坯料从铺设台移至热成型站,”迪亚兹解释说。 “自动化系统可以在平坦的状态下移动坯料并将它们放置在凸成型工具上 [步骤 3],而不会产生皱纹。”成型工具安装在铝成型台上,该成型台放置在 ACTI 中。将可重复使用的硅胶真空袋(Mosites Rubber Co., Fort Worth, Texas, U.S.)放置在坯料的顶部,然后在 ACTI 中将其加热至 130°C 并使用真空压力成型(步骤 4)。 “当达到温度设定点时,通过控制阀按照预定义的斜坡平稳施加真空,”迪亚兹说。
他指出,干胶带更容易预成型/热悬垂成型,“因为层与层之间的粘合比预浸料更柔软。尽管是干燥的材料,它是 HDF/加热减瘤,其中由于胶带中包含粘合剂,最终的预制件保持形状。”
对于纵梁和翼梁加强筋,将坯料形成为两个 L,然后将其背靠背放置在固化工具上以形成 T 型纵梁/加强筋。六个蒙皮纵梁中的每一个都不同,需要不同形状的坯料来制造预制件。 24根加强筋的长度也各不相同。
前后 J 形梁包括一个形成 C 形的坯料,面向机翼盒的内部,另一个坯料形成为面向外部的 Z 形——两者背对背放置。翼梁的翼盒外侧也有正弦形支脚(步骤 7 中的箭头)。 “在将坯料移至成型站之前,我们在平铺台上切割了翼梁脚的形状,”迪亚兹说。 “之后在这个区域没有任何东西可以修剪或铣削。坯料直接放置在阳成型工具上,翼梁脚位于工具左侧,顶部法兰位于工具右侧。”
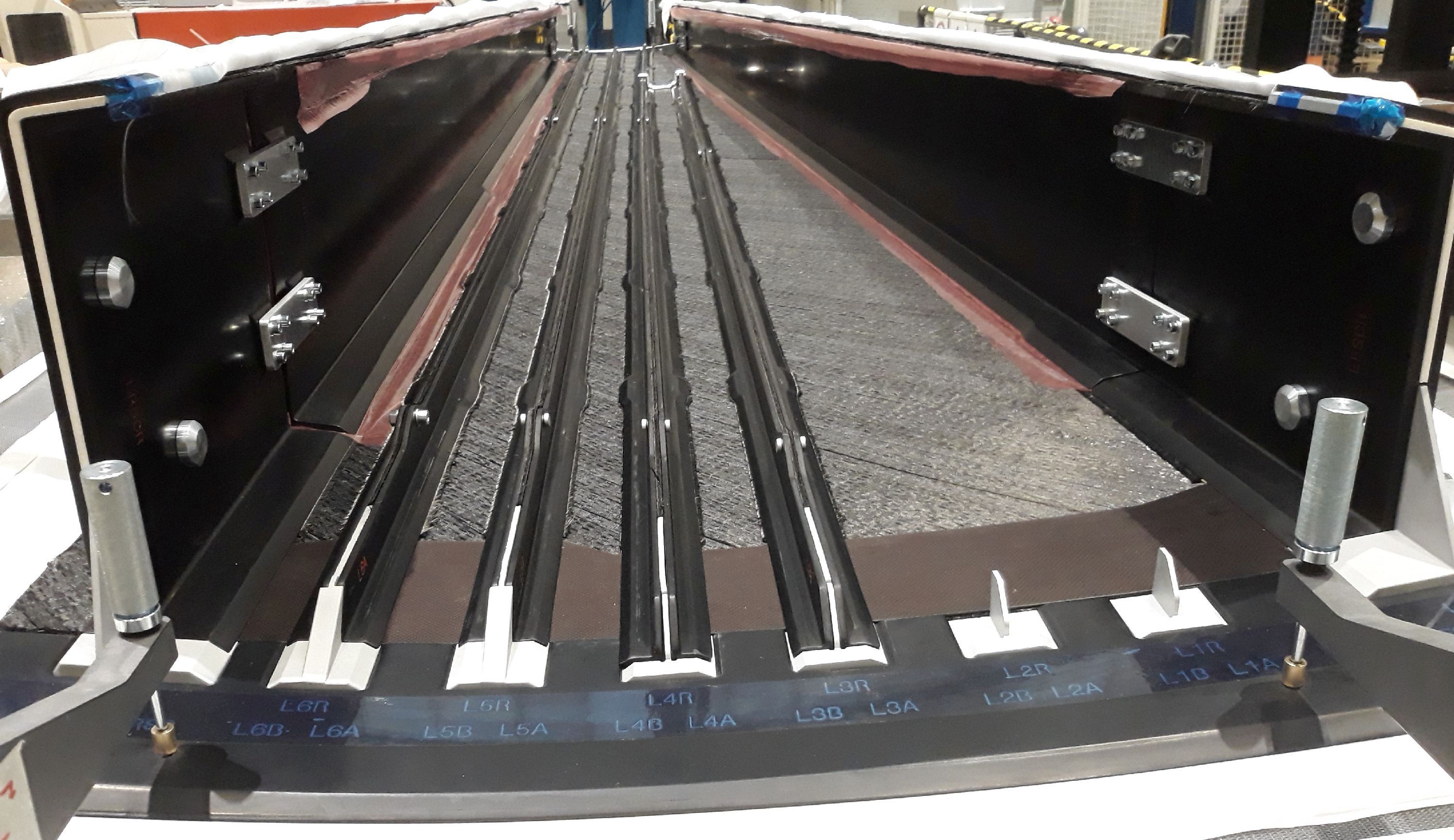
图。 3. 精确的瓶坯放置。 J 形梁和纵梁的预成型件使用双金属圆柱体(在最左侧和最右侧可见)、白色定位器和带有纵梁/定位器切口的 CFRP 垫板进行定位。 照片来源: IIAMS 项目,空中客车防务与航天,MTorres。
一次性输液
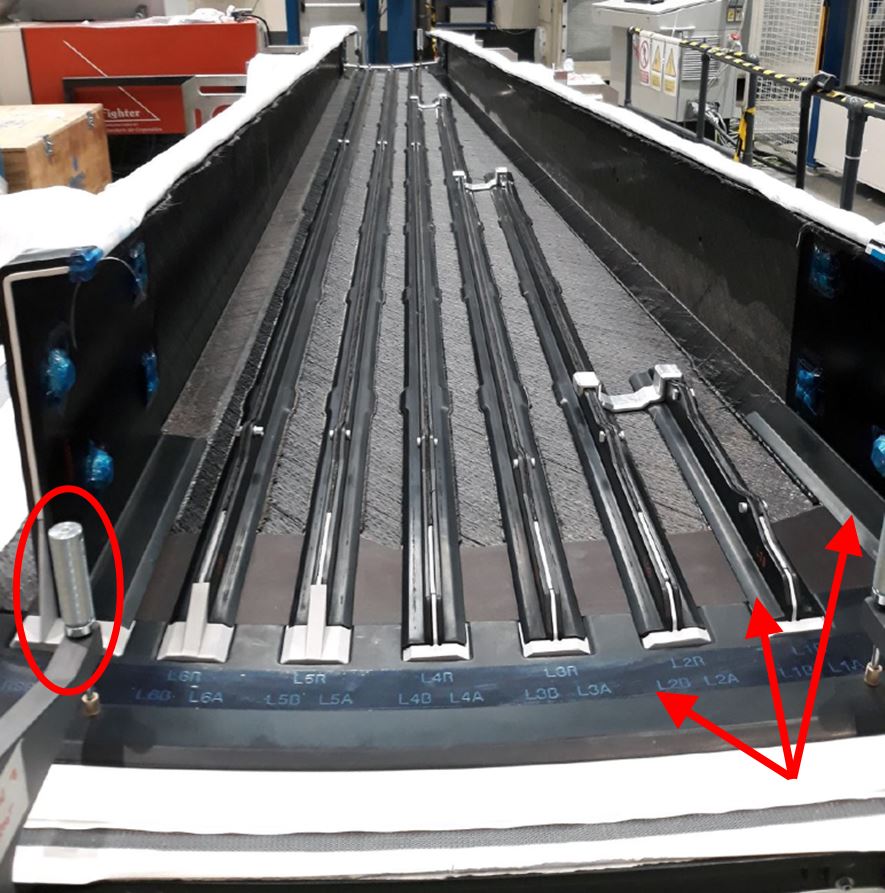
第 5 步。 纵梁和梁预制件放置在下蒙皮上,由圆柱形(圆形 ) 和白色定位元素。黑色 CFRP cauls(箭头 ) 还用于帮助定位纵梁 和 放置在纵梁和 J 形梁的顶部。
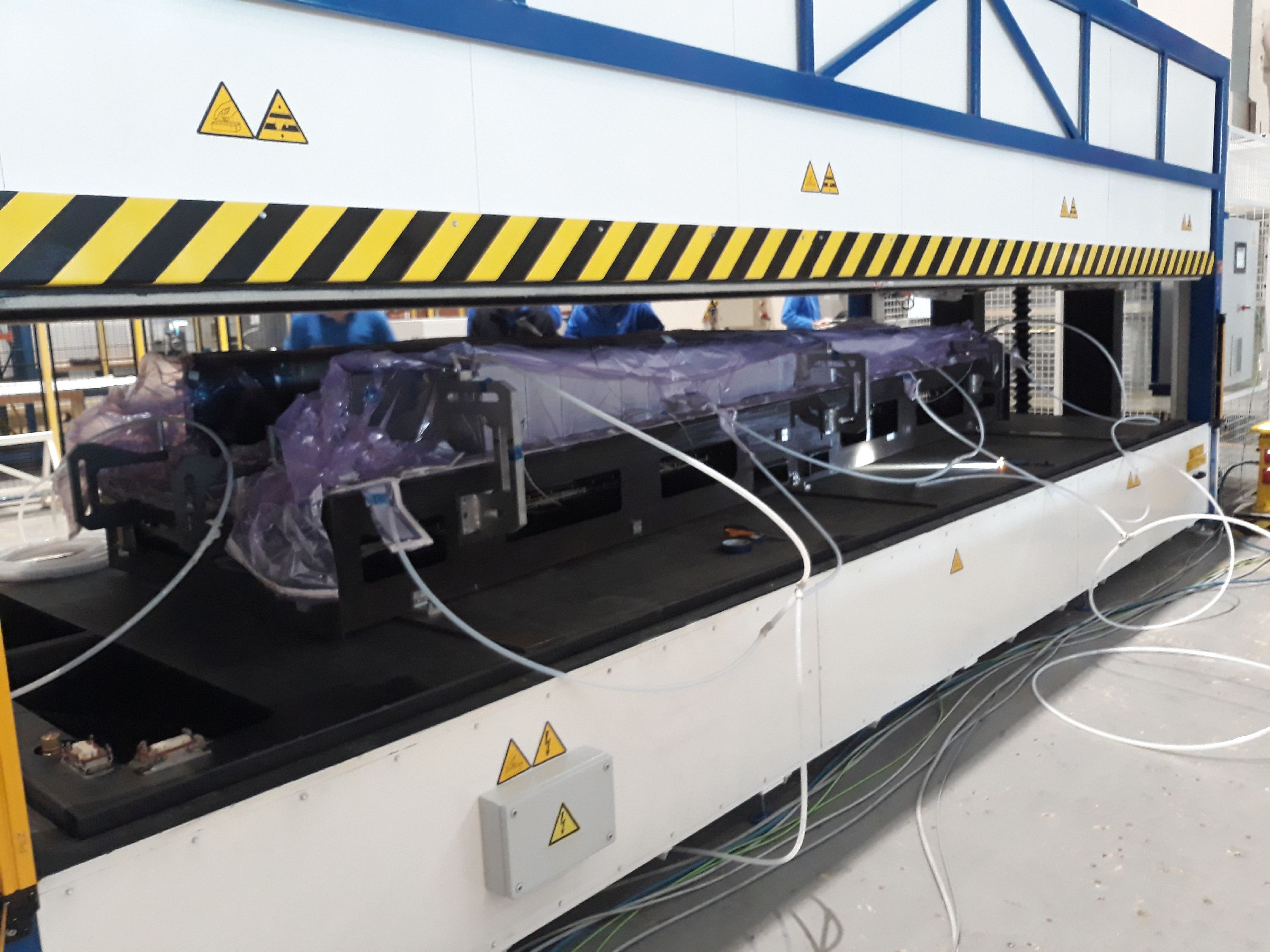
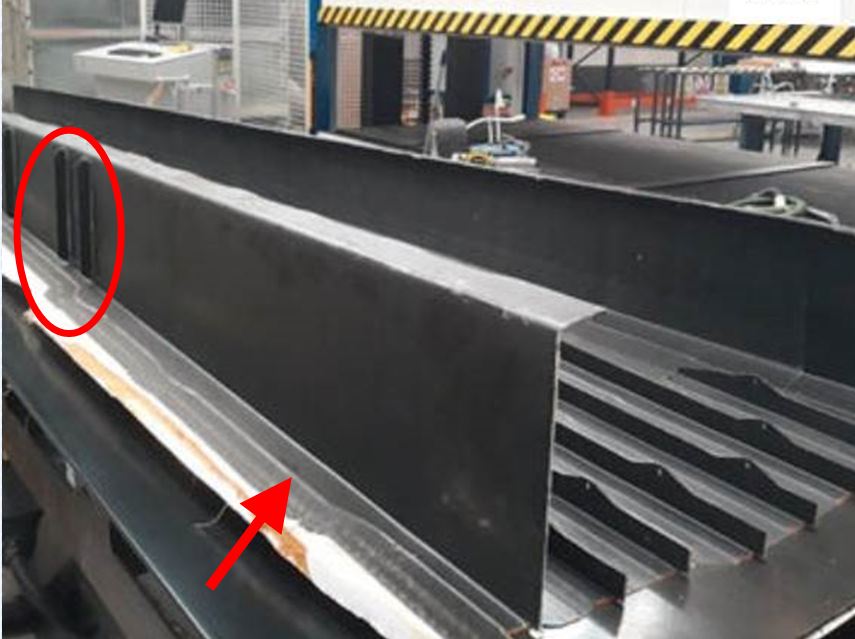
第 7 步。 在 MTorres 完成的初始演示展示了带有两个加强筋的 J 形梁(圈出 ) 及其正弦脚 (arrow ).
下一步是将纵梁、翼梁和翼梁加强筋预制件放置在已经铺设的下机翼蒙皮上(步骤 5)。 “当我们将每个预制件放在皮肤和固化工具上时,我们正在对每个预制件进行索引,”迪亚兹说。在第 5 步左侧的翼梁末端和图 3 中两个翼梁的末端可以看到用作定位元件的圆柱体。这些图像还显示了用于纵梁和 J 形翼梁的白色定位装置。最终的瓶坯组装中有13个这样的定位器,每一个都不同。
垫板也是瓶坯定位和放置系统的关键部分。它们用于在复杂叠层和/或几何形状的区域保持均匀的压力和温度的传统目的,但也将是灌注的关键,如下所述。可以在步骤 5 和图 3 中的纵梁和翼梁末端看到带有纵梁预制件切口的黑色 CFRP 垫板。
“纵梁预制件的位置取决于该覆盖层的位置,”迪亚兹解释说。 “我们开发的用于监控和控制制造过程的数字技术包括一个增强现实应用程序,可将 CATIA 模型投影到叠层上。这用于帮助引导垫板、定位元件和预成型件的放置。它还显示了接下来要执行的步骤。该应用程序允许在平板电脑上自我支持,以便所有员工都可以轻松访问所有信息。”
然后将最后一组黑色 CFRP 垫板放置在用于 T 型纵梁的 L 型预制件的顶部,并沿着每个 J 型梁的内部和外部,向上延伸到法兰上,并向下延伸到底部外侧的脚上。翼盒,如步骤 5 和图 3 所示。“翼梁还在端部内侧使用了一种垫板,以提高接头区域的精度,”迪亚兹说。 “所有这些垫板都在 HDF 过程中使用,并通过叠层保持附着在预制件上。”
然后用剥离层和真空袋膜覆盖具有垫板的完成的干燥预成型件组件。然后将整个蒙皮、纵梁和翼梁组件放入 ACTI 中,并将工具加热至 120°C。 Hexcel RTM6 环氧树脂被加热到 70°C 并在通过单个树脂进料位置灌注之前脱气。 “ACTI 准备从四个位置进料树脂,”Diaz 指出,“但经过大量的模拟和测试,我们决定使用单个树脂入口更容易、更便宜。”
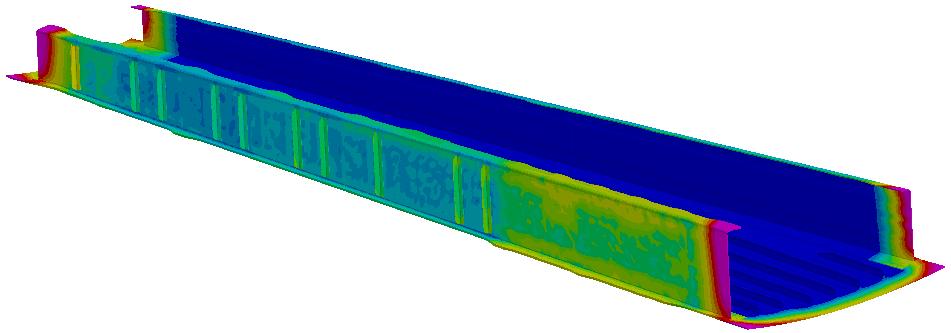
即使只有一个入口,输液过程也非常复杂,包括三种不同的模式。 “我们首先使用 PAM-RTM 软件 [ESI Group, Paris, France] 进行了流动模拟,”Diaz 说。 “完全润湿所需的流动前沿和参数是如此复杂的组合。例如,翼盒中心的树脂流动速度更快,但要弄湿所有加强筋是一项挑战。”
带有半透膜的 VAP 对下蒙皮效果很好,但这被沿纵梁和翼梁内部的高温流动网格所取代。 “角落是最难润湿的区域,”迪亚兹指出,“但它们也是保持装配公差以及沿边缘最关键的区域。”这可以在图 4 中流动模拟的红色区域中看到。“在这些区域中,开发了一种定制方法来实现所需的精确尺寸,”他解释说。我们还在梁的周边和顶部使用了真空端口。”
正如模拟所预测的那样,灌注相对较快,然后在 180°C 下固化两小时,仅使用热空气,不使用加热工具。脱模后,然后使用超声波测试 (UT) 检查每个翼盒演示器。这是作为 IIAMS 项目可交付成果的一部分完成的,以分析演示者的质量。然而,这一过程的工业应用将减少传统的无损检测,有利于数字传感器和更快的在线检测工具,如视觉系统。
据迪亚兹说,虽然灌注固化周期与高压釜固化的预浸料翼盒相似,但整体周期时间应该更短。 “之后我们已经消除了大部分组件,我们也不需要像预浸料那样做任何垫片,但我们的质量是一样的。例如,最后一层表皮和第一层纵梁之间的粘合不需要中间的粘合膜,以提高机械性能并考虑公差。”这显然更有效,但他指出,零件生产率最初并不是驱动因素。 “这种方法不是与单个零件的制造竞争,而是与完整的翼盒组件竞争。”
完整的演示程序,认证路径
“我们只有 18 个月的时间来完成这个项目,其中包括设计工艺和工具以及制造工具和演示器,”迪亚兹说。 “到 14 个月,我们已经准备好在 2020 年 2 月下旬 [第 3 步] 在 JEC 展示第一台演示器,但随后 JEC 因大流行而被取消。尽管该项目于 2020 年 9 月下旬完成,但如果减去由于 COVID-19 导致我们无法工作的月份,我们实际上是在 16 个月完成的。由于我们的内部设计能力和能力,我们能够保持这个非常紧张的时间表使用我们的 AFP 和 CNC 铣床制造模具原型。”
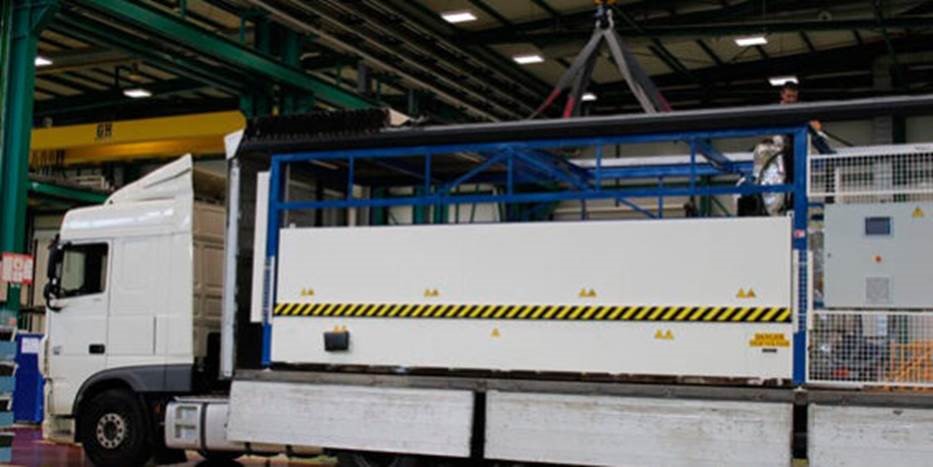
第 8 步。 ACTI 成型/固化设备和翼盒工具被提升到一辆标准的移动卡车上,并搬迁到西班牙加的斯的空中客车 DS。
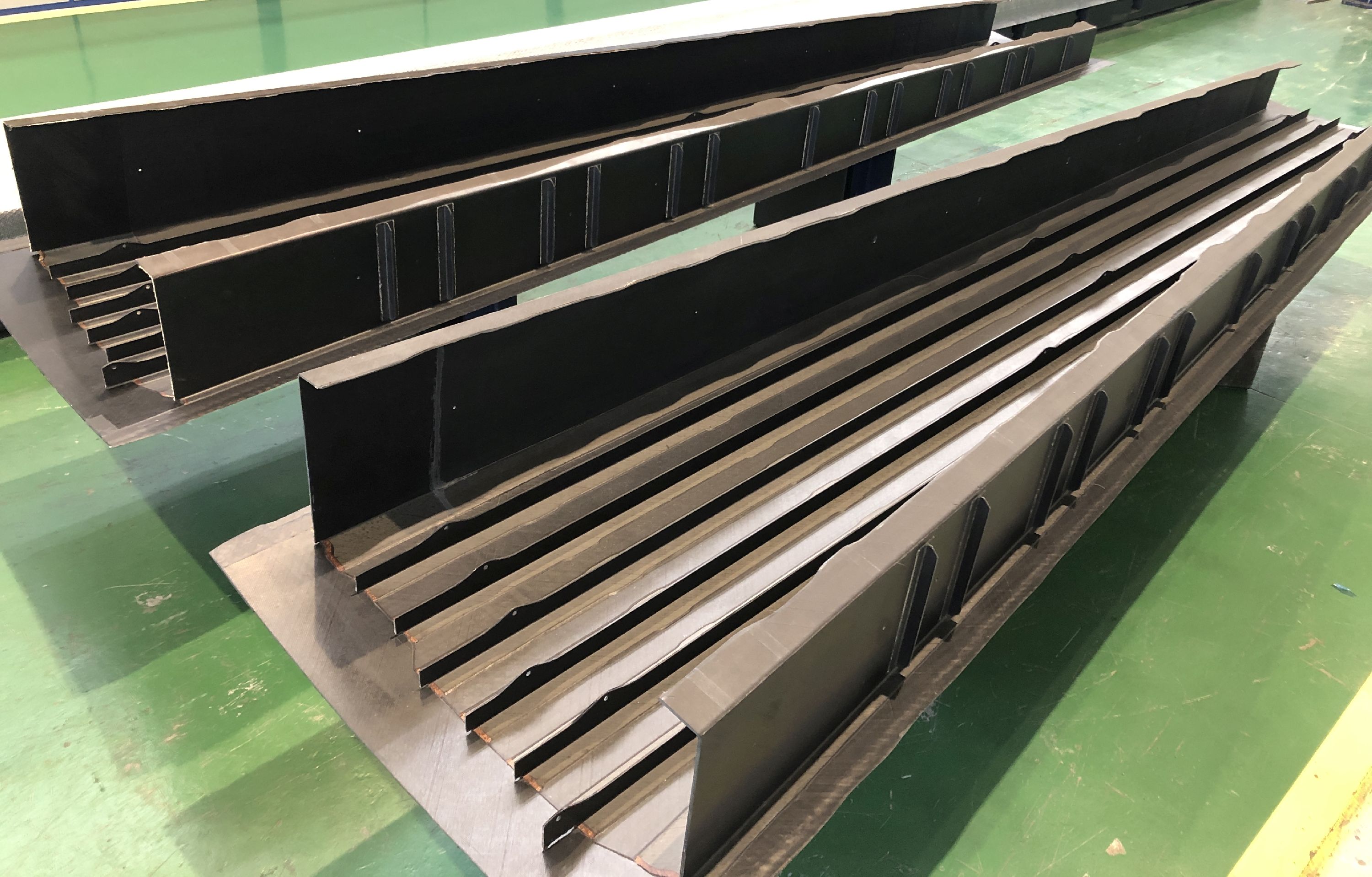
MTorres 制造了一个 1 米长的简化演示器,用于检查所有工艺参数。然后,生产了第一个全尺寸演示器。然后将模具和制造设备搬迁到加的斯的 Airbus DS(第 8 步),在那里生产了最终的演示机。这也是该项目可交付成果的一部分,证明该设备可以在多个地点轻松运输和安装。
正如侧边栏“IIAMS 机翼盒认证路线图”中所解释的那样,空中客车 DS 在清洁天空计划中发挥了关键作用,从绿色支线飞机 (GRA) 集成技术演示者 (ITD) 的联合领导者在清洁方面取得进展Sky,AIRFRAME ITD 的联合负责人,以及 Clean Sky 2 内区域综合飞机演示平台 (IADP) 中飞行试验台 2 (FTB#2) 的负责人。 FTB#2 将包括其他复合材料和机身发展,包括驾驶舱和其他机翼组件。
事实上,所有准备 FTB#2 的项目都是空客更广泛、长期战略的一部分。目标是开发一种更轻、更高效的未来涡轮螺旋桨飞机机身,以及更便宜、使用更少能源、制造液体和辅助材料的生产工艺,同时产生更少的废料并提高可回收性。
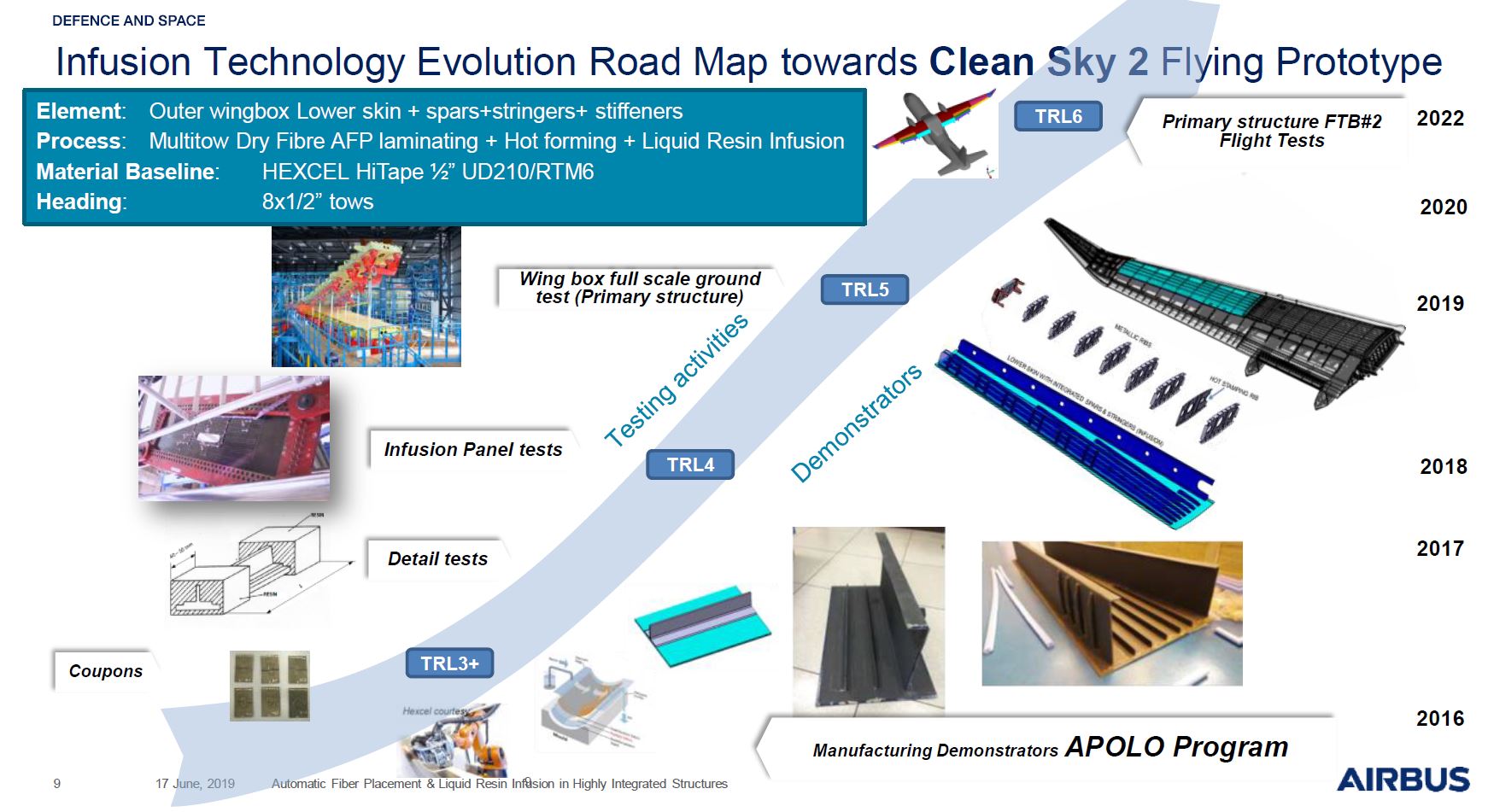
A.E. Jiménez Gahete 在 2020 年 9 月的 Materiales Compuestos 中解释说:“我们 [Airbus DS] 正在逐步完成整个机身结构测试金字塔,从试样到外机翼的全尺寸结构测试。 文章标题为“通过干纤维铺放和液态树脂灌注制造的空中客车国防和航天高度集成的翼盒部分。”材料特性测试、设计细节测试矩阵和设计允许的子组件测试都已完成,并取得了积极的结果。 MTorres 在此测试中提供了帮助,包括制造测试试样和零件,以及验证机翼盒制造过程和设计细节的演示器。 Gahete 说,只有最后的外翼全尺寸静态和功能测试仍然存在,以获得 FTB#2 飞行资格。
“一次性输液可以减少关节、减轻重量并增加健壮性,”迪亚兹说。 “新型干胶带 Mtorres 已开发出在加工(AFP、热悬垂成型和灌注)以及零件的结构特性方面都取得了出色的成果。”他指出,从历史上看,树脂灌注复合材料能否与高压釜固化预浸料具有相同的结构性能和公差一直存在疑问。
“使用软 [非金属] 工具在单次工艺中获得相同的公差是我们最大的挑战,”他承认道。 “但我们已经证明这项技术是有效的,它可以生产未来飞机所需的大型主要结构。我们的下一步是继续推进生产系统的数字技术和便携性。”
树脂