Wing of Tomorrow 肋骨:一次性、热塑性、OOA 整合
空中客车公司的明日之翼 (WOT) 计划于 2015 年启动,在过去六年中一直在探索用于单通道商用飞机机翼的更具成本竞争力、更高吞吐量的材料、制造和组装技术(参见CW em> 之前对 WOT 计划的报道)。
根据荷兰 GKN 航空航天全球技术中心 (Hoogeveen) 的主任 Arnt Offringa 的说法, GKN Aerospace(英国布里斯托尔)一直非常积极地参与 WOT 计划,包括开发通过树脂传递模塑 (RTM) 和四个铝翼肋制成的翼梁演示器。 GKN Aerospace 最近交付的另一项技术演示涉及开发具有成本竞争力的热塑性复合肋条,以及用于一次性、非高压釜 (OOA) 制造的创新模块化压力机系统。
向热塑性塑料迈进
2018年,GKN Aerospace开始内部讨论可用于生产五架演示器的材料和制造技术
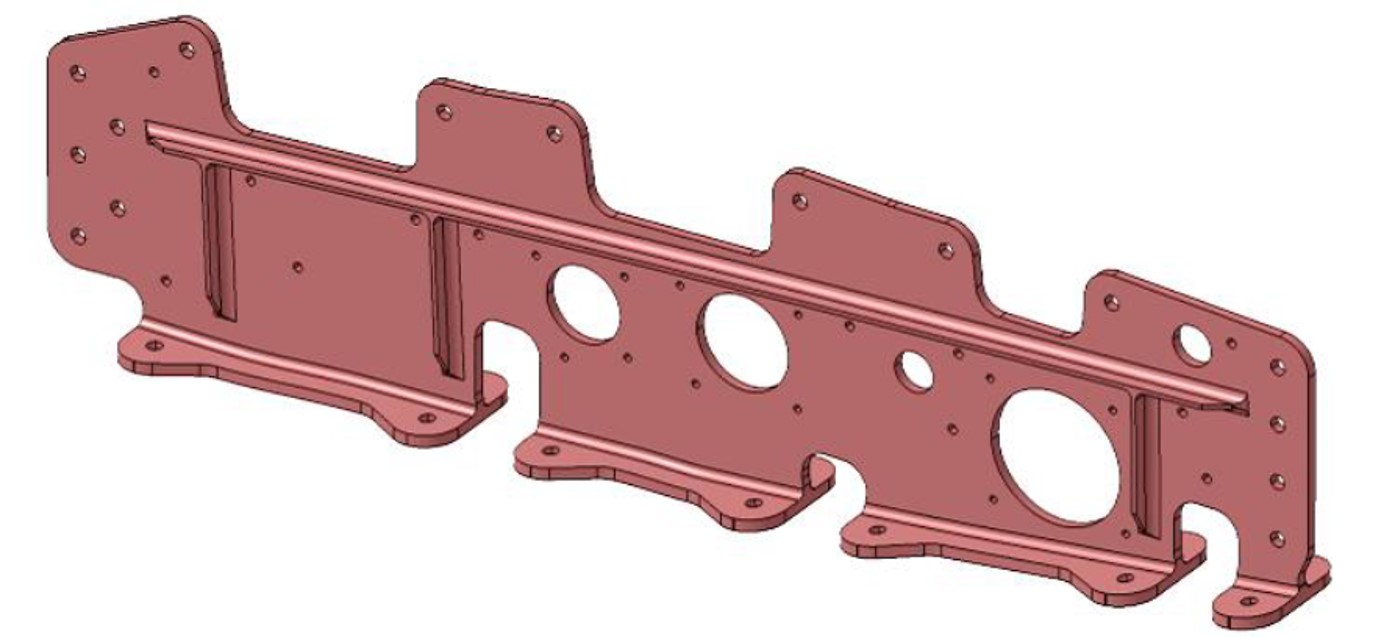
设计肋条。 为了实现轻薄的零件,肋条设计(顶部)结合了 GKN 的对接技术(底部)和注塑成型的加强筋填料(中间,以绿色显示)。
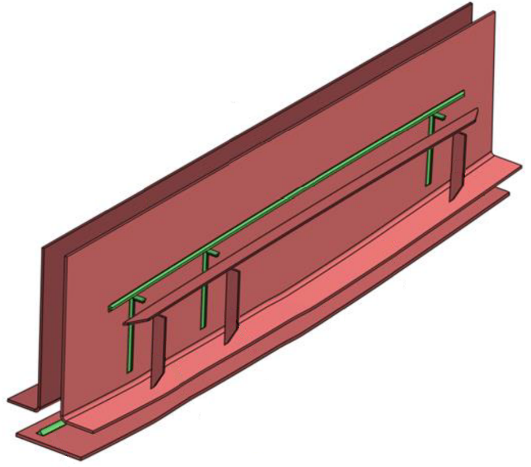
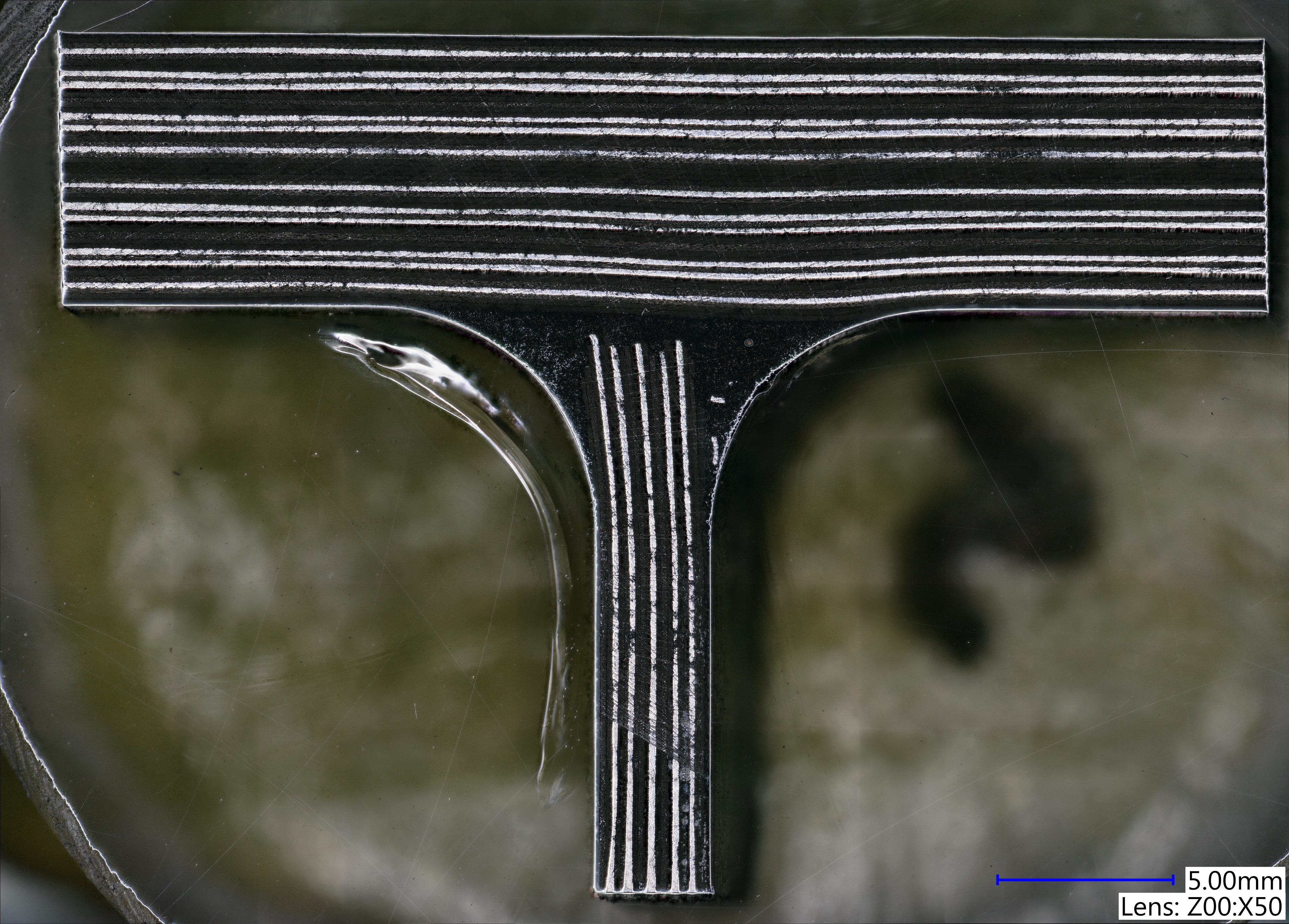
WOT 计划的肋骨。 GKN Aerospace 比较了几种材料选择,包括热固性和热塑性复合材料。铝是商用飞机肋的传统材料,被选择用于生产四个较大的内侧肋,但对于较小的外侧肋,该公司决定探索一种复合材料选项。 Offringa 指出,由于 WOT 演示器将是复合机翼,因此开发可与铝竞争的复合肋是合乎逻辑的步骤。
“复合机翼上的复合肋有几个好处,”他说。 “首先,将复合材料与复合材料结合使用意味着材料之间的热膨胀没有差异,就像复合材料机翼上的金属肋一样,反之亦然。其次,您不会有腐蚀方面的问题或顾虑。复合材料还意味着减轻重量。最后但并非最不重要的一点是,使用复合材料使检查更容易。”
Offringa 解释说,一旦组装好最终的机翼,典型的金属肋就需要人工目视检查。然而,由于肋骨位于机翼内部,这意味着需要在底部机翼蒙皮中切割大型椭圆形舱口,以便人类可以进入机翼进行检查。 “如果您使用复合肋材,则肋材的疲劳度会降低,需要检查的潜在疲劳裂纹也会更少。检查变得更加简单和不那么密集,您不再需要在机翼蒙皮中建造舱口。它将是一个连续的翼皮,”他说。
从热固性或热塑性复合材料中可以获得重量减轻、耐腐蚀和较少侵入性检查的好处。 “我们进行了一项内部研究,研究了重量、成本和工业化,在比较了不同的技术后,我们选择了热塑性塑料,因为它在成本方面具有最大的潜力和最佳的商业案例,”Offringa 说.
由于距离空中客车公司位于英国的 Filton 机翼技术中心更近,WOT 演示器将在那里进行测试,GKN Aerospace 的英国布里斯托尔分公司是该公司 WOT 工作的主要枢纽。然而,考虑到 GKN Aerospace Netherlands 从其作为 Fokker Technologies 时代起就在热塑性塑料方面的专业知识,GKN Aerospace 的两个团队联手打造了肋板演示器。 “设计是在英国完成的,但制造开发是在荷兰完成的,因此 GKN Aerospace 的不同团队之间的合作非常好,”Offringa 说。
空中客车 WOT 负责人 Sue Partridge 指出:“与合作伙伴的合作是明日之翼计划的一个重要方面。通过整合我们的资源,我们可以制定解决方案,利用我们两个组织的能力获得更好的结果。”
对于交付给空客的 WOT 肋,GKN Aerospace 使用了 Solvay(比利时布鲁塞尔)的 APC 碳纤维/聚醚酮酮 (PEKK-FC) 胶带,该胶带基于该公司的 Novaspire PEKK-FC (FC) 快速结晶配方。 Offringa 指出,Toray Advanced Composites(美国加利福尼亚州摩根希尔)的低熔点碳纤维/聚芳醚酮 (PAEK) 材料也正在评估作为未来肋结构的一种选择。
设计下一代翼肋
典型的单通道飞机机翼上有 20 多根肋。热塑性复合材料演示肋是演示机翼上的第 14 条;其他人将展示替代材料和工艺。
Offringa 说,热塑性复合肋材通常通过小型飞机的冲压成型制造。然而,GKN Aerospace 排除了传统的冲压成型作为 WOT 肋的一种选择,因为商用飞机机翼,即使是像 WOT 演示机这样的窄体,也被置于非常高的压缩和拉伸载荷下。
“如果你要冲压形成传统意义上的热塑性肋条,那么你必须制作一个非常厚的肋条,用厚腹板使其更坚固,这样它就可以承受作用在它上面的力,”Offringa 说,考虑到减重要求,这不是可取的。此外,冲压成型将无法在连接到下机翼蒙皮的肋上创建双面底部法兰组件;需要制造一个额外的部件并用螺栓连接到肋的其余部分。 GKN Aerospace 需要一种制造工艺,为团队的设计提供更大的灵活性。
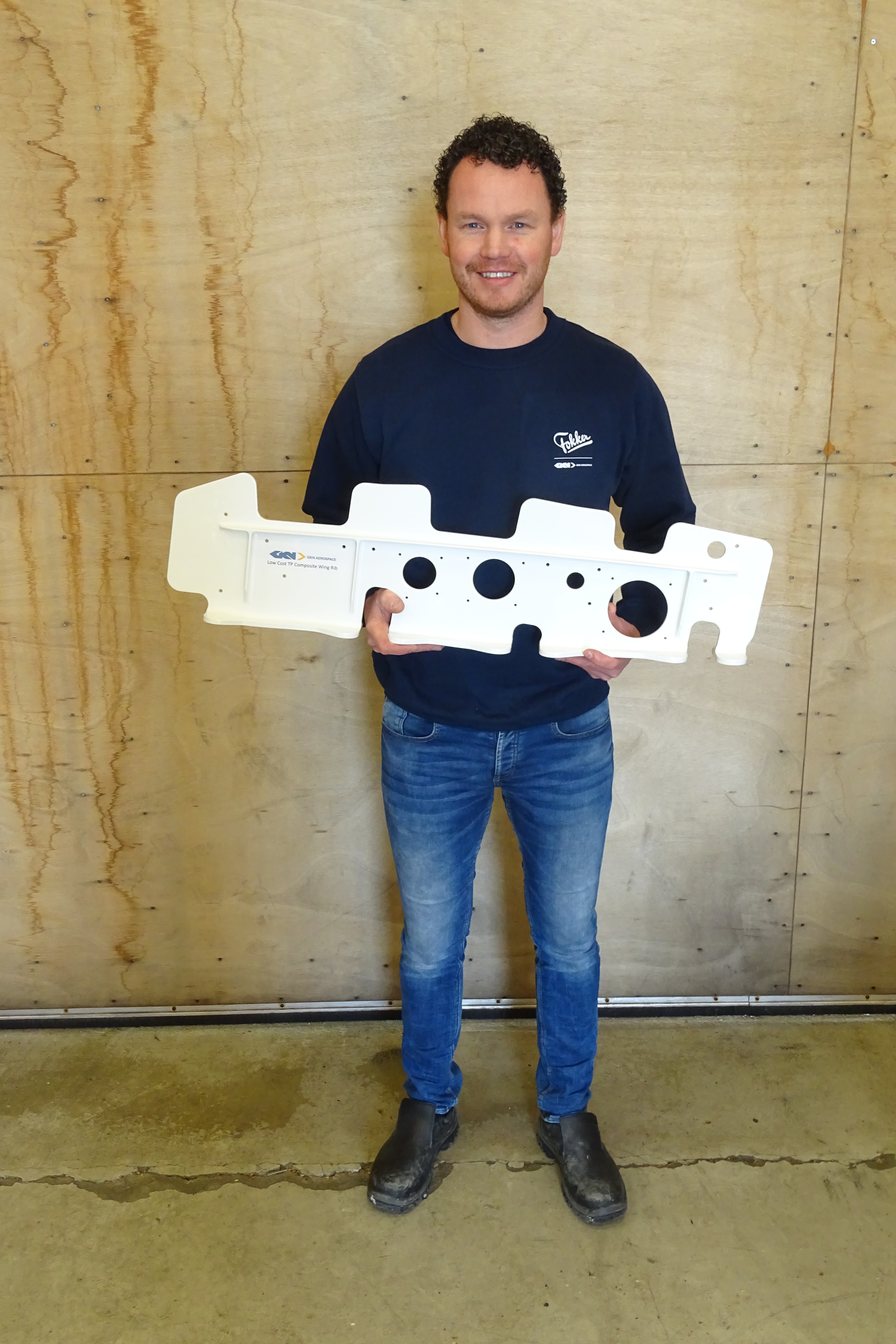
GKN Aerospace 的 90 厘米长、24 厘米高的热塑性肋具有垂直腹板和从肋底部延伸的双向 8 毫米厚的法兰。为了满足重量要求,卷材的厚度仅为 7 毫米。为了防止屈曲和增加刚度,腹板通过使用 GKN Aerospace 的对接技术的 3 毫米厚的加强元件进行加强,该技术使用扁平加强筋预成型件和注塑“填充”材料来创建坚固、连续的接头(参见“热塑性塑料”主要飞机结构又向前迈进了一步”,以了解在使用索尔维碳纤维/PEKK-FC 胶带制造的湾流机身面板上使用该技术。
“我们知道,如果我们能够在复合材料中制造出这种形状并使其坚固,那么我们就会有一个非常轻巧的设计,并且我们正在寻找减轻重量的方法。但问题是,您如何以高性价比和高效率制造出如此复杂的形状?这就是我们努力打造这款新产品的地方,”Offringa 说。
一步,OOA 制造
该过程建立在 GKN Aerospace 之前用于 TAPAS(热塑性经济实惠的主飞机结构)项目以及使用该公司对接技术的湾流机身面板开发的技术之上。对于 WOT 肋,GKN Aerospace 开发了一种 OOA、一步固结工艺。 “我们第一次离开高压釜,将之前的工作提升到了一个新的水平,”Offringa 指出。
首先,将单向 (UD) 热塑性胶带切割成正确的宽度,然后使用层压机将扁平元件预成型为两个 L 形腹板预成型件。腹板预制件、用于法兰的扁平预制件以及构成纵梁的较小预制件和注塑填充元件都被装入一个工具中,该工具放置在类似于树脂传递成型的模块化共固压机内(RTM) 按。压力机关闭,气囊系统用于从水平和垂直方向产生压力,模拟高压釜中的压力。集成电阻加热系统使复合材料在冷却固结之前短暂地达到熔化温度。
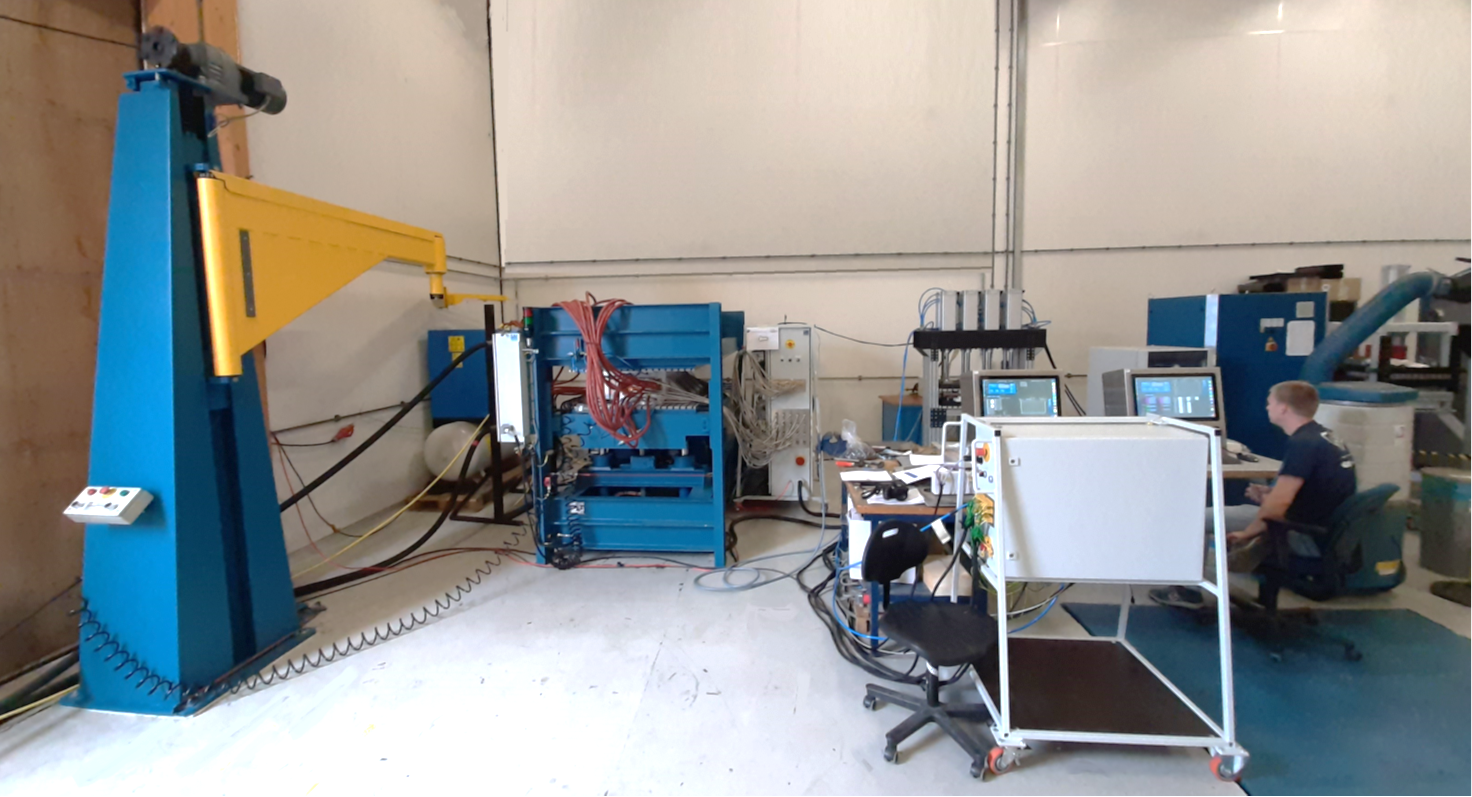
“我们将大部分开发工作投入到调整和优化工具上,”Offringa 说。该系统采用模块化设计;可以更换工具以适应不同尺寸的肋或其他类型的零件,同时保持相同的加热和冷却系统。尽管这些肋不是必需的,但 GKN Aerospace 在其技术中心开发的压力机可以容纳长达 6 米的零件,其中还可以包括其他面板或横梁。
加工热塑性塑料时,过程控制系统是关键。热塑性塑料在比热固性塑料更高的温度下熔化,必须在受控、一致的过程中冷却,以最大限度地减少翘曲和最大限度地提高结晶度。 “从头到尾控制确切的过程非常重要,”Offringa 说。 “加热循环的热管理非常重要。” (有关使用热塑性塑料时过程控制的问题和重要性的更多详细信息,请参阅本文中的“热塑性塑料 (TP) 成型问题”边栏)。
特殊的工具功能用于使薄的集成加强筋能够轻松地从工具中释放出来。脱模的部分接近净形,然后修整形成成品。从进刀到出刀,整个过程大约需要 45 分钟。这意味着一台压力机可以在 8 小时的班次中生产大约 15 个翼肋。
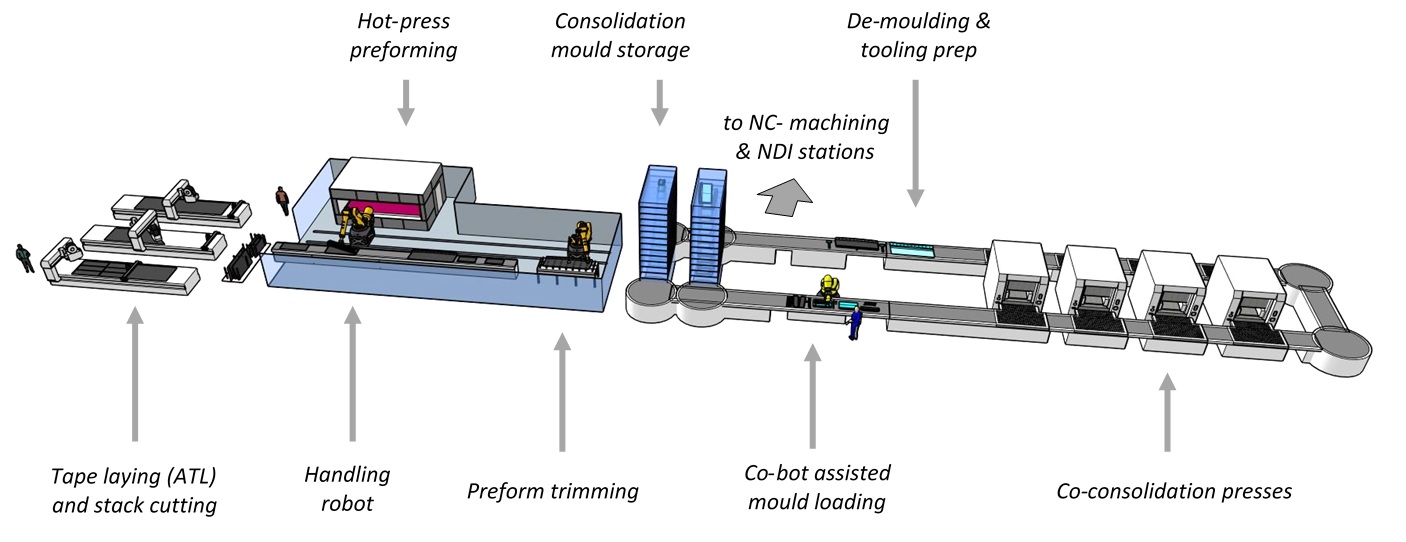
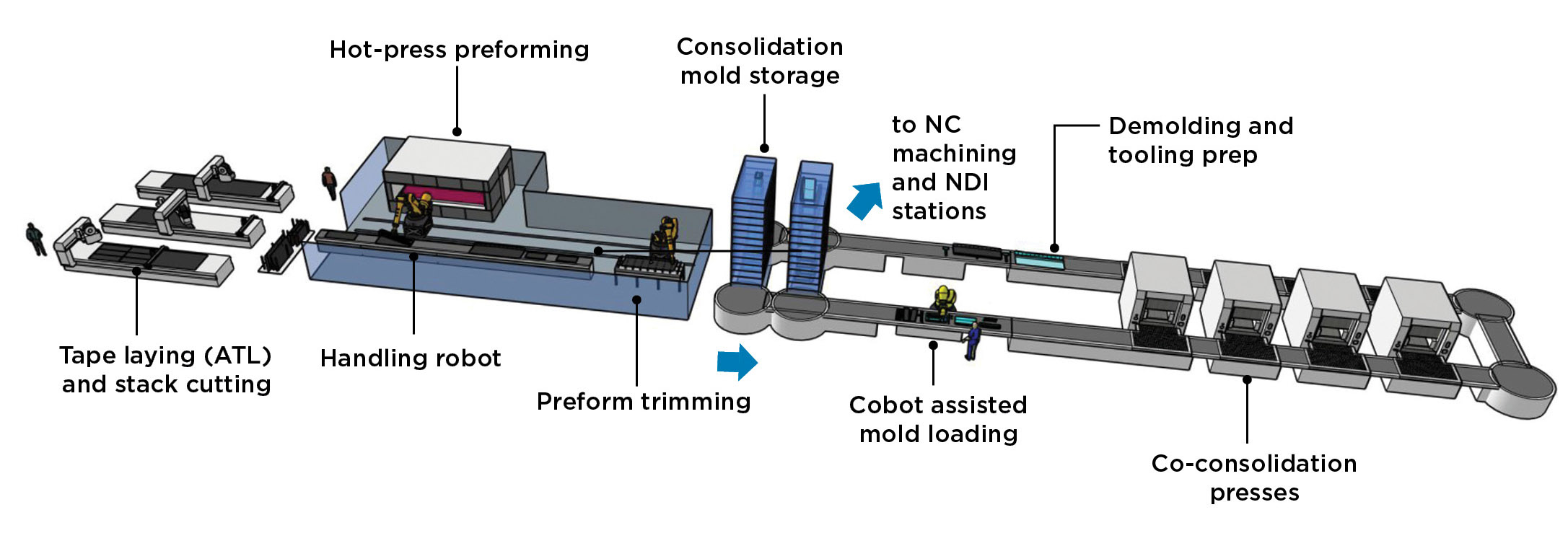
“它最终成为一个简单的制造过程,”Offringa 指出。 “我们同时做很多事情:共同巩固不同形状的预制件,创建具有双向法兰的肋底部,同时我们正在使用对接技术加强腹板。但最终,我们将材料的所有元素放入一个工具中,然后在一个处理步骤中创建一个同质的部件。”
测试、交付及其他
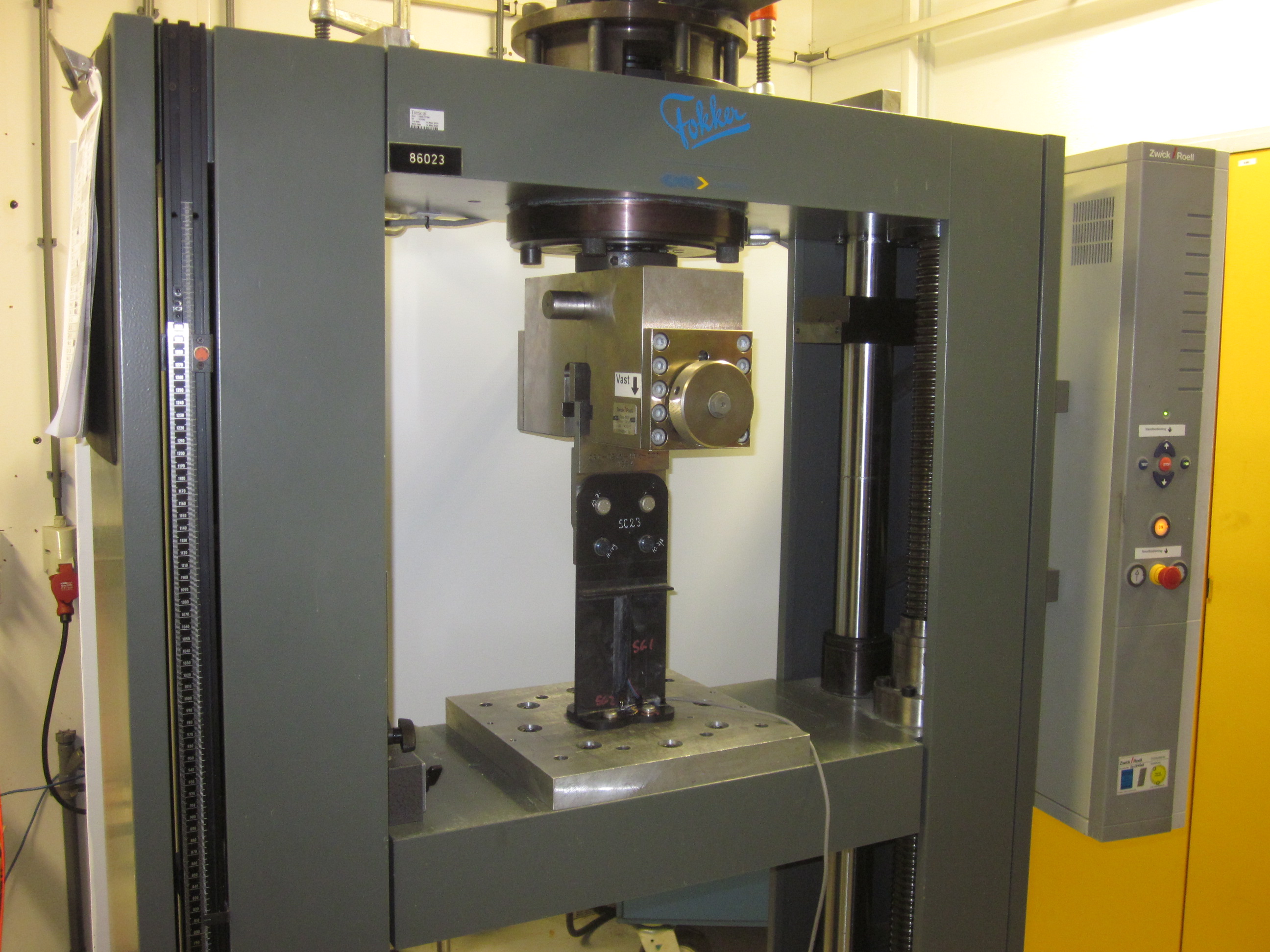
测试。 在 GKN 的怀特岛和 Hoogeveen 工厂测试了子组件以满足拉伸和压缩强度要求。
2019 年底,肋材子组件在 GKN Aerospace 的怀特岛和 Hoogeveen 设施进行了测试,Offringa 表示它们“大幅”通过了拉伸和压缩载荷要求。他补充说:“它很坚固,很坚韧,很容易制造。这是一个完全符合我们希望的概念。” Offringa 表示,与铝制版本相比,热塑性复合材料版本可显着减轻重量,并且具有成本竞争力。
该公司已向空中客车公司交付了三根肋条,其中一根将在 WOT 演示机上进行组装和测试。 GKN Aerospace 继续致力于优化其商业航空航天肋的工艺和材料,包括明日之翼及以后。
树脂
- 完全由自然资源制成的连续纤维增强热塑性复合材料
- 索尔维扩大热塑性复合材料产能
- Fraunhofer 委托自动化 Engel 生产单元进行热塑性复合材料研发
- DLR 结构与设计研究所提高热塑性复合材料机身结构的成熟度
- 索尔维完成南卡罗来纳州设施的安装,增加了美国热塑性复合材料的产能
- 热塑性胶带继续显示出复合航空结构的潜力
- 非高压灭菌器 VBO 后梁,热塑性肋材目标明日之翼
- INEOS Styrolution 为 StyLight 热塑性复合材料建立生产基地
- Xenia 推出 CF/PP 热塑性复合材料
- 在深海中崛起的热塑性复合管
- NIARs NCAMP排位昙卡热塑性复合
- TenCate 在巴西庆祝热塑性复合材料联盟的组装