非高压灭菌器 VBO 后梁,热塑性肋材目标明日之翼
空中客车公司(法国图卢兹)正在与航空复合材料制造商合作,为公司的明日之翼 (WOT) 计划开发非高压釜 (OOA) 结构。这些结构将于 2021 年交付给空中客车公司,并将组装成一个演示机翼,该机翼将进行测试和评估,以用于下一代单通道飞机的潜在用途。何时宣布这样的计划是未知的,也有很多猜测的主题,但整个航空复合材料供应链都将自己定位为下一代飞机制造的一部分,无论是为空中客车公司还是波音公司,或两者兼而有之。
>连续波 已经在有关 Spirit AeroSystems(美国堪萨斯州威奇托)生产的下机翼蒙皮和 GKN Aerospace(荷兰 Hoogeveen)生产的热塑性肋的报道中报道了部分 WOT 活动。加入 WOT 工作的是飞机制造商和飞机结构供应商 Daher(法国巴黎),该公司为该项目开发、制造并交付了一个 OOA 后梁和五个热塑性肋。
“Daher 很自豪能够参与这个 WOT 计划。这一发展证实了 Daher 作为热塑性技术和热固性集成功能结构领域的世界领导者之一,以及飞机制造商的强大合作伙伴和复杂零件的一级合作伙伴,”Daher 研发副总裁 Dominique Bailly 说。
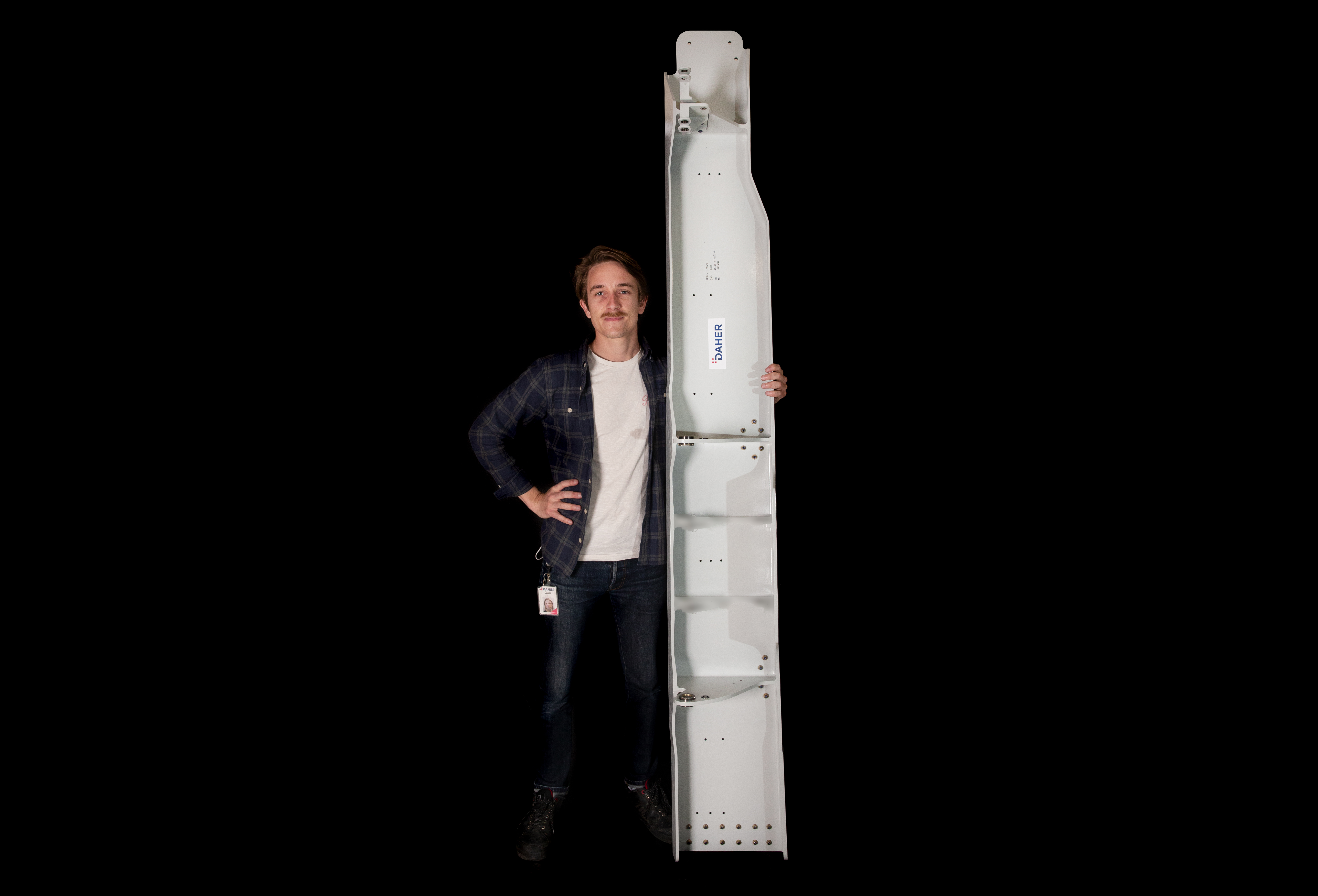
高性能翼梁
WOT 演示机与任何商用飞机机翼一样,具有多个翼梁结构。为 WOT 开发的 Daher 后翼梁位于油箱外部,是紧邻机身的两个翼梁中第二近的,位于起落架上方。它的长度超过 2 米,厚度超过 10 毫米,并且必须满足重要的强度和刚度要求——“几吨应用在特征上,几十吨用于展向方向的剪切和牵引力,”拜利说——因为它靠近机身和起落架系统。
此外,负责该翼梁的 Daher 首席工程师 Alexandre Condé 表示,空中客车公司正在寻求开发一种高度自动化的制造工艺,使公司能够减轻飞机重量并经济高效地满足 60-100 架飞机的生产速度每月。 Daher 提出了一种设计,能够替换 15 个金属部件和紧固件,这些部件和紧固件是基准复合材料翼梁设计的原始设计。 “我们的想法是集成最多的功能,以实现成本效益和减轻重量,”Condé 说。
由此产生的翼梁结构是 Daher 于 2018 年为达索航空公司(法国巴黎)公务机开发的仅 OOA 真空袋 (VBO) 热固性翼梁的副产品。 Bailly 说 Dassault 翼梁是用 Hexcel 的(美国康涅狄格州斯坦福德)M56 环氧树脂预浸料、固化的 OOA VBO 制成的。随后,随着 Daher 参与空中客车 WOT 计划,该公司决定采用 Dassault 翼梁的设计、工艺和理由并将其应用于新的空中客车 WOT 结构,选择 Hexcel M56 350°F 固化 OOA 环氧树脂,预浸入Hexcel AS4碳纤维织物和IM7 UD碳纤维。
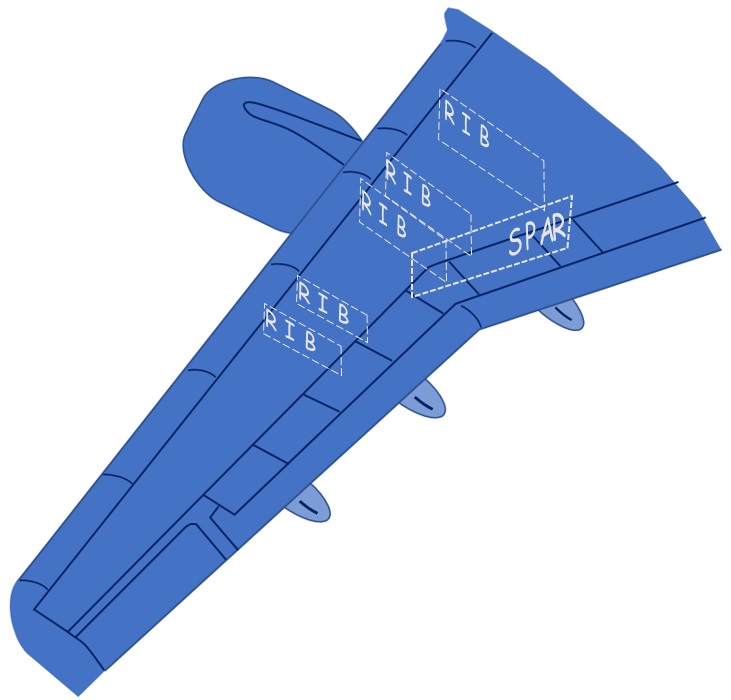
用于制造翼梁的制造过程是使用科里奥利复合材料(法国奎文)系统的自动纤维铺放 (AFP),该系统将材料应用于阳模。固化在烘箱中的真空袋下进行。 Condé 说,所得零件的孔隙率为 0.1%。
Condé 表示,之所以选择预浸料而不是液态树脂成型,其原因与预浸料在过去 30 年中已成为航空航天制造的主要材料相同:它提供一致且可靠的树脂/纤维体积,从而能够生产出尺寸一致且可靠的零件和质量。 “仅在真空条件下使用这种新一代 OOA 树脂,固化后复合材料厚度中的纤维含量具有完美的稳定性,”Condé 说。 “此外,部件的重量非常稳定,因为您没有将树脂推到纤维外面。”
Daher 表示,它是第一个在 2020 年末交付 WOT 组件的合作伙伴——为英国布里斯托尔的空中客车提供一个支柱——以集成到第一台 WOT 演示机中;该公司正在交付另外两个。除了这个演示阶段,Daher 还在考虑翼梁制造的工业化,并致力于制造系统设计 (MSD) 分析,以估计和模拟下一代单通道全速生产的操作、设施、设备和人员需求飞机。
多个肋骨,多个尺寸
Daher 开发肋骨的努力 因为 WOT 计划更加复杂和苛刻。该公司在机翼内部设计了五根不同尺寸和尺寸的翼肋;其他肋条是铝和复合材料的组合设计,包括由 GKN Aerospace 设计的热塑性复合材料肋条。
Bailly 解释说,在之前与 Dassault Aviation 合作的一个项目中,Daher 已经展示了其使用热塑性复合材料设计和制造相对较小的加强筋的能力。借助 WOT,该公司有机会将其技能扩展到更大(约 2 米长)、更高负载的加强筋的开发。
此外,根据 WOT 目标,Daher 的目标是到 2023 年底技术准备水平 (TRL) 为 6。两个项目 [WOT 和 Dassault Aviation],我们将证明我们能够覆盖机翼的整个肋骨部分——这就是想法,”Bailly 说。
“我们利用该计划研究了制造零件的不同方法并比较了机械行为,并研究了对制造的影响。与此同时,我们正在进行模拟以预测组件行为,如回弹或冲压效应。目的是减少开发过程中的试验,从而减少非经常性成本,”Condé 说。
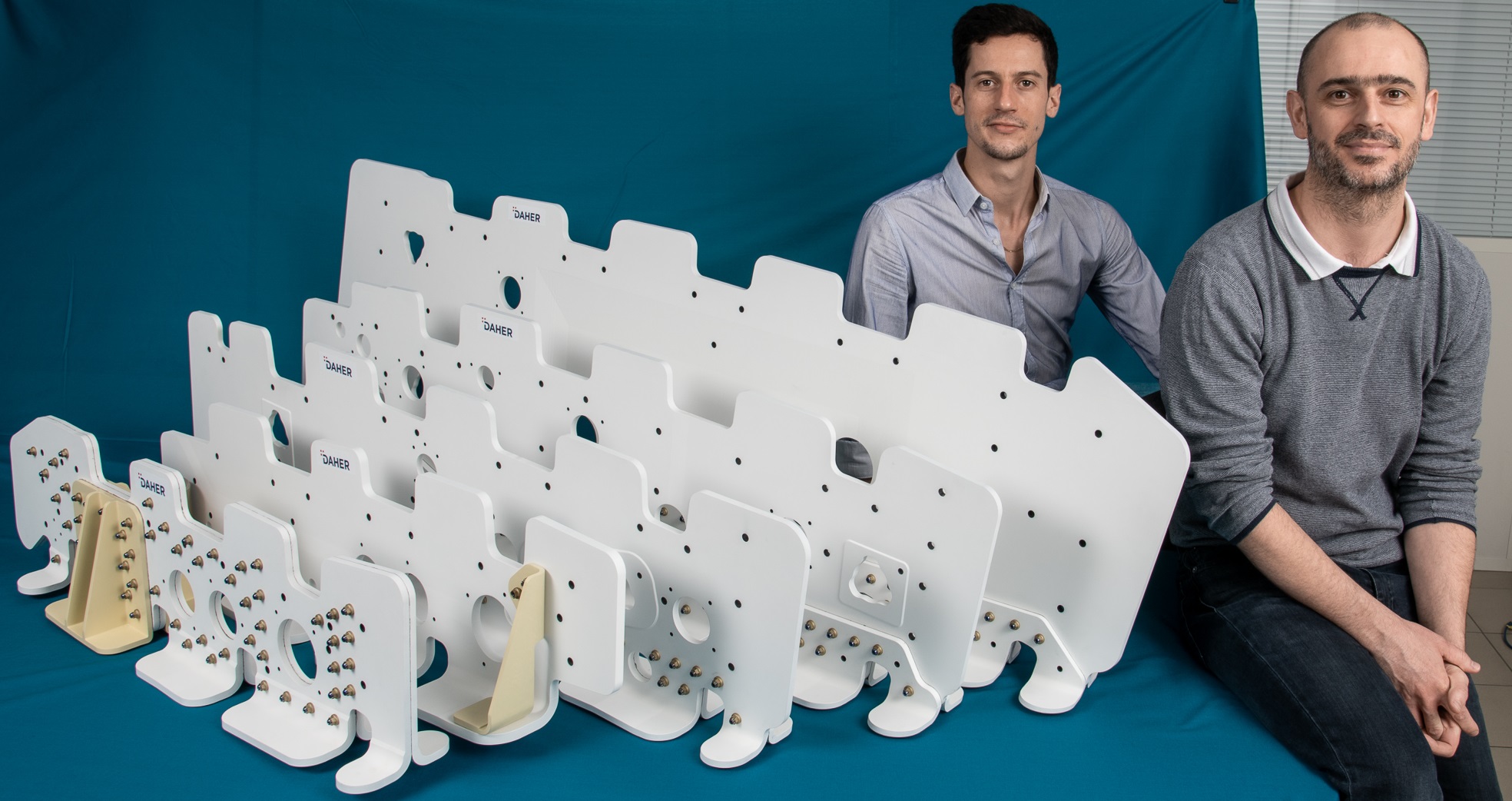
与翼梁一样,开发始于试样、元素和细节级别,然后在制造最终的全尺寸部件之前制造小尺寸部件。 Condé 指出,每个级别都进行了测试,包括 Daher 为肋骨特征开发的特定测试。
对于所有五个肋条,Daher 最终决定使用由 Toray Advanced Composites(美国加利福尼亚州摩根希尔)提供的单向 (UD) 碳纤维/低熔点聚芳醚酮 (PAEK) 胶带,使用 Victrex(英国兰开夏郡克利夫利斯)制造的树脂)。为了制造加强筋,使用 AFP 制作扁平坯料,然后进行烘箱固结——在某些情况下,材料在冲压成型之前进行预固结。根据需要,额外的法兰或其他组件以机械方式固定在冲压成型的零件上。
每根肋都是根据其沿机翼的位置、尺寸规格和载荷要求(1 吨到 50 吨)设计的,因此每根肋在几个方面都是独一无二的。最大的肋骨长 2 米,宽 1 米。无论如何,每个都从一个扁平的腹板开始,该腹板被冲压成“L”形,以沿着零件底部形成一个法兰,在那里它连接到机翼蒙皮。为了增加稳定性,一些肋条由两个“L”形部件组成,背对背机械固定,形成带有双向法兰的“T”形。
特殊功能包括一个支架(由热固性复合材料制成),用于与附在肋骨上的襟翼轨道连接,以及一系列孔或层落入某些肋骨中以减轻零件重量。
“在我们设计的整个过程中,我们必须管理复杂性与成本,”Bailly 说。 “这一直是我们的想法,做一些简单但具有成本效益的事情。” Condé 指出,从生产率的角度来看,简单性也是关键。 “如果它太复杂,从客户的角度来看,在他们想要的非常高的利率下,这将没有竞争力。”
给设计带来复杂性的一个挑战是每个肋条的相对厚度——最大的肋条高达 12 毫米。较厚的织物在冲压成型时容易起皱或成型不正确,而较厚的部分可能难以加工成成品形状。
对于加工,Daher 根据零件需求混合使用水刀切割和机械加工,以减轻零件厚度问题并管理温度。此外,在 12 毫米厚的肋条上,该团队在部件中间设计了一个层板落窗,以减轻整体部件重量。除了解决这些潜在问题之外,Condé 指出,叠层窗口还使 Daher 能够“在零件上尝试不同类型的制造特征,以增加我们对零件行为的理解。”
印章成型过程被证明是一个更大的挑战。 “我们必须想出一种新的冲压方式来降低皱纹的风险,”Bailly 说。 Daher 最终开发了一种解决问题的专有方法。
后续步骤
除了 WOT,Daher 正在评估生产热塑性肋的替代制造方法,同时计划在未来开发一条完整的生产线以实现高速制造。
例如,虽然 WOT 演示者使用紧固件,但 Bailly 指出,通过 2019 年收购热塑性复合材料和感应焊接专家 KVE Composites(荷兰海牙),Daher 拥有未来焊接组件的能力。 “我们正在开展另一个独立项目,以在 UD 厚部件焊接方面达到更高的 TRL 水平 [用于下一代单通道飞机],”他说。
Daher 还致力于开发一条完整的生产线,以在未来生产热塑性肋条。 “我们确实在改进概念并减少所有任务所需的机器数量并降低流程成本,”Bailly 说,其目标是与大批量飞机生产目标相匹配。
树脂