革新复合材料成本范式,第 2 部分:形成
DARPA 的可定制原料和成型 (TFF) 程序中的 RAPM 子程序编译了当前/过去生产的分析数据以及它自己的多个零件成型试验的经验数据,以生成这些曲线。目标是更好地了解复合材料零件和工艺的贸易空间。
所有图片来源:波音公司、DARPA
可定制原料和成型 (TFF) 计划由国防高级研究计划局(DARPA,美国弗吉尼亚州阿灵顿)于 2015 年启动,旨在快速、低成本和敏捷地制造用于国防的小型复杂形状复合部件飞机。这个为期 48 个月的计划旨在提高复合材料的成本竞争力,以利用其与机加工铝相比的重量减轻以及耐腐蚀和开裂的优势。在本系列的第 1 部分中,CW 探索了 TFF 的愿景及其可定制的通用成型原料 (TuFF) 子项目,该项目开发了一种具有高机械性能和类金属成型性的短纤维片材。
在本文中,TFF 的第二个子项目将重点从原料转移到成型:由波音公司(美国伊利诺伊州芝加哥)领导的快速高性能制造 (RAPM,发音为“wrap-em”)。该计划于 2016 年 7 月开始,并在众多出版物中展示了其结果,包括 6 篇论文和 SAMPE 2019 的两次演讲。正如波音技术研究员和主要调查员 Gail Hahn 和 Tom Tsotsis 所解释的那样,RAPM 的目标是“彻底改变小型复合部件,可广泛用于国防应用。”
“我们的愿景是通过汽车效率实现航空航天性能,”Hahn 说。该计划与汽车复合材料和零件制造商合作,包括 Solvay Composite Materials(美国佐治亚州 Alpharetta)和 SGL Composites(奥地利 Ried 和 Ort im Innkreis),但实现航空航天性能并不总是那么简单。 “虽然低温、快速固化的环氧树脂很容易用于汽车应用,但它们还不能满足航空航天要求,”Tsotsis 说。 RAPM 确实使用了针对航空级树脂灌注部件的新型快速固化两部分环氧树脂。然而,最初,SGL 的成型系统不能超过 130°C,这阻碍了达到 30 分钟工具时间的目标。
“我们的目标是实现最多 30 分钟的工具使用时间,从而能够使用高速工作单元来降低系统级成本,从而与机加工铝具有成本竞争力,”Tsotsis 说。 “在波音内部,我们决定这将满足我们在国防应用方面所看到的一切,”哈恩补充道。 “当我们可以使用热塑性塑料 2 到 6 分钟时,为什么要把它设置在这里?因为热塑性塑料需要更高的温度处理,并有相应的工具限制,我们的目标是为我们的供应链提供充足的选择。”
随着该计划的推进,它向航空航天材料和制造商甚至实验系统开放,例如 Solvay 的 XEP-2750。 “我们最初认为我们能够全面评估这个系统,就像我们在 2007 年至 2012 年与 DARPA 项目‘非高压釜制造技术’的工作中使用 CYCOM 5320-1 所做的那样,”Hahn 说。尽管不可能进行相同程度的评估,但 XEP-2750 现在已被 Solvay 商业化为 CYCOM EP-2750(参见在线边栏“用于 RAPM 压缩成型的新型预浸料 ”) 并从大量 RAPM 零件试验和经验教训中受益。
“我想要的只是一些能够在贸易研究中战胜铝的小型复合材料部件的工艺,”复合材料行业和 TFF 项目顾问 Jeff Hendrix 在谈到他的 RAPM 目标时说。那么,RAPM成功了吗? 连续波 探索该计划为制造数百个零件所做的努力,通过多种材料和工艺比较了十几种航空零件配置,同时寻求减少时间和成本的方法。
程序框架
RAPM 与主要行业合作伙伴合作,在三个主要方面对零件进行了试用:
- 树脂灌注 与 HITCO Carbon Composites(美国加利福尼亚州加德纳)和 SGL Composites 合作
- 热固性预浸料 与 Solvay Composite Materials(英国希诺尔和美国加利福尼亚州阿纳海姆)、Fiber Dynamics(美国堪萨斯州威奇托)和 Reinhold Industries(美国加利福尼亚州圣达菲斯普林斯)一起成型
- 热塑性成型 与 ATC Manufacturing Inc.(美国爱达荷州 Post Falls)和 TxV Aero(美国罗德岛布里斯托尔)合作
成型试验分两个阶段完成:初始“制造开发”阶段(图 1),随后是“挑战与过渡”(C&T)部件(图 2)到挑战 初步发展和过渡 有潜力战胜机加工铝的候选人。
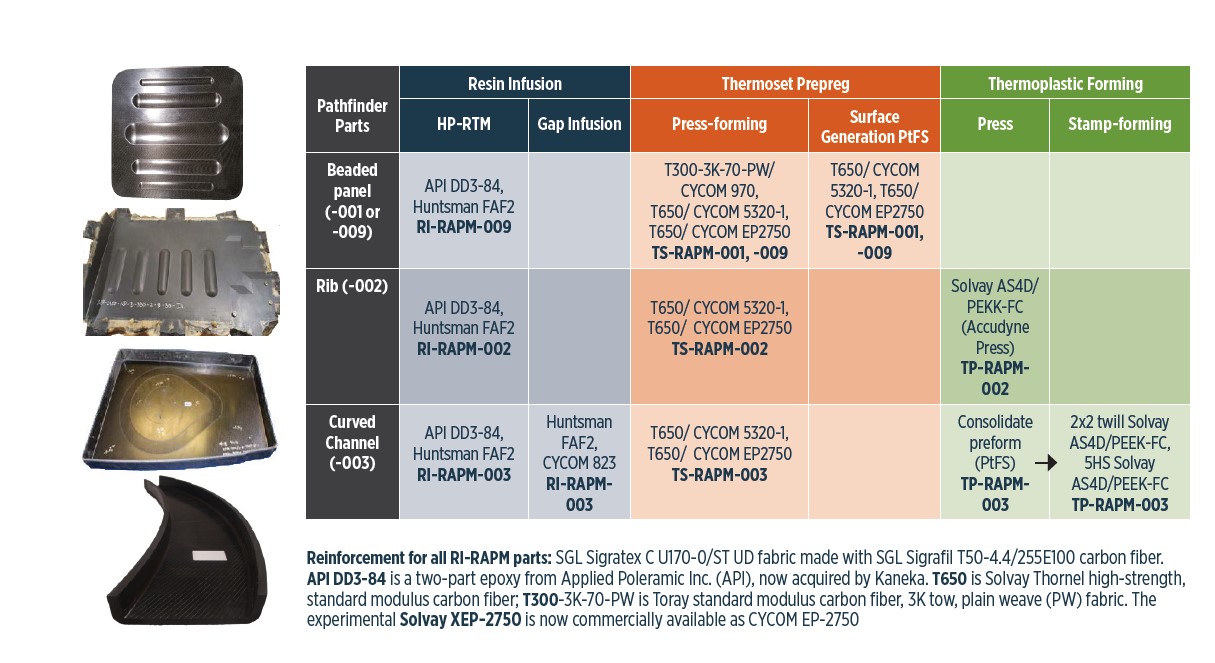
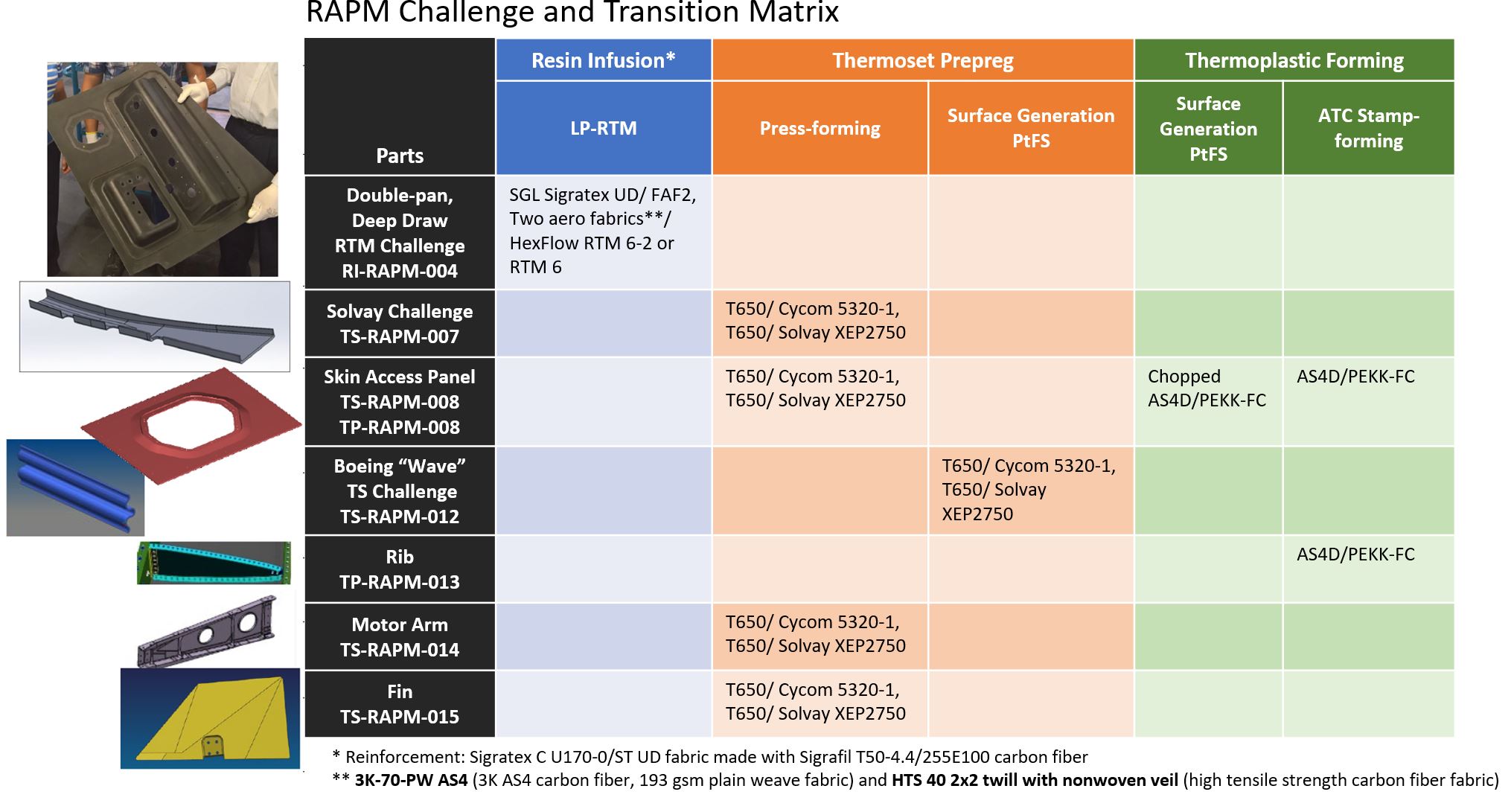
制造业发展 试验使用了三种主要部件配置:串珠面板(有两种类型)、带衬垫的肋条(层板积层)和弯曲的 C 形槽。这些航空航天零件的常见特征可能会导致制造挑战:串珠面板具有多个平面外特征,加上垫高、垫低和垂直边缘;肋板有一个带有多个 90 度边缘的衬垫,并且其中一个边缘有一个铰链;并且C形槽的内外半径不同,翼缘的曲率不同,腹板的层板下降明显。
目标是为三个轨道中的每一个制定设计和制造指南。 “第一次尝试时看起来并不性感,”Hahn 回忆道。 “但他们帮助确定了可接受的半径和零件几何形状,从而生产出不会出现不需要的纤维变形的零件以及参数的最佳组合,例如施加在工具上的张力、温度、压力和时间。”
所有三个 RAPM 材料和工艺轨道都包括使用 Surface Generation(英国拉特兰)生产到功能规范 (PtFS) 像素化加热控制和工具系统的试验(参见在线边栏“RAPM 开发与 PtFS ”),位于美国密苏里州圣路易斯的波音 R&T “这是因为我们正在寻找一种可以在灵活费率的环境中容纳所有三种材料/工艺的工作单元,”Hahn 说。 “我们能够探索不同的温度控制方法和成本。”波音 PtFS 电池的最高温度为 440°C,夹紧力为 150 吨,有效零件体积为 750 x 750 x 100 毫米。
尽管最初的设想是使用 TuFF 短纤维片材,但由于这些材料在开始时无法使用,RAPM 继续使用替代材料。这实际上对复合材料行业有利,因为替代品涵盖的材料更能反映该项目之外正在使用和开发的材料:汽车有机片材和航空级预浸料、实验环氧树脂、半结晶热塑性塑料和切碎的预浸料。因此,结果和发现涉及所有类型的复合材料制造商,而不仅仅是国防领域的制造商。
轨道 1:树脂灌注/RTM 制造
该领域的制造开发试验始于汽车类材料和工艺。零件由 SGL Composites 使用高压树脂传递成型(HP-RTM,300 bar)和 C T50 标准模量、50K 碳纤维非卷曲织物(位于德国瓦克斯多夫的 SGL Carbon)制成,分为三部分配置:RI-RAPM-009 、RI-RAPM-002、RI-RAPM-003(图1)。这些用于确定高质量成品零件所需的预成型参数。波音圣路易斯公司也使用其 PtFS 系统对 RI-RAPM-003 进行了间隙输注(压缩 RTM,或 C-RTM)试验。
计算流建模用于更好地了解如何注入这些部件、分析工艺行为以优化材料和工艺参数并评估注射方案。
评估了如何以及何时对不同类型的预制件几何形状施加张力以最大程度地减少纤维变形的工具方法。这些设计更改针对修改后的 C 通道几何形状进行了验证,然后进行了计算机断层扫描 (CT) 分析。吸取的经验教训应用于随后的 C&T 阶段,转向低压 RTM (LP-RTM) 以降低成本。
在这些探路者零件试验中,在几个深拉半径中发现了分层。 Tsotsis 认为,这是由工具中树脂的初始固化不足(因为 SGL 的蒸汽加热系统将工具内温度限制在 130°C)和零件去除过程中的热/机械平面外应力相结合造成的。 “因为树脂强度还没有得到足够的发展,这些异常可能已经在工具上完全固化后消除了,他建议道。 “SGL 无法同时满足工具和 直到将油加热(而不是仅蒸汽)添加到工具中,才能在 130°C 以上固化,”Hahn 指出。这是在制造开发试验后添加的。
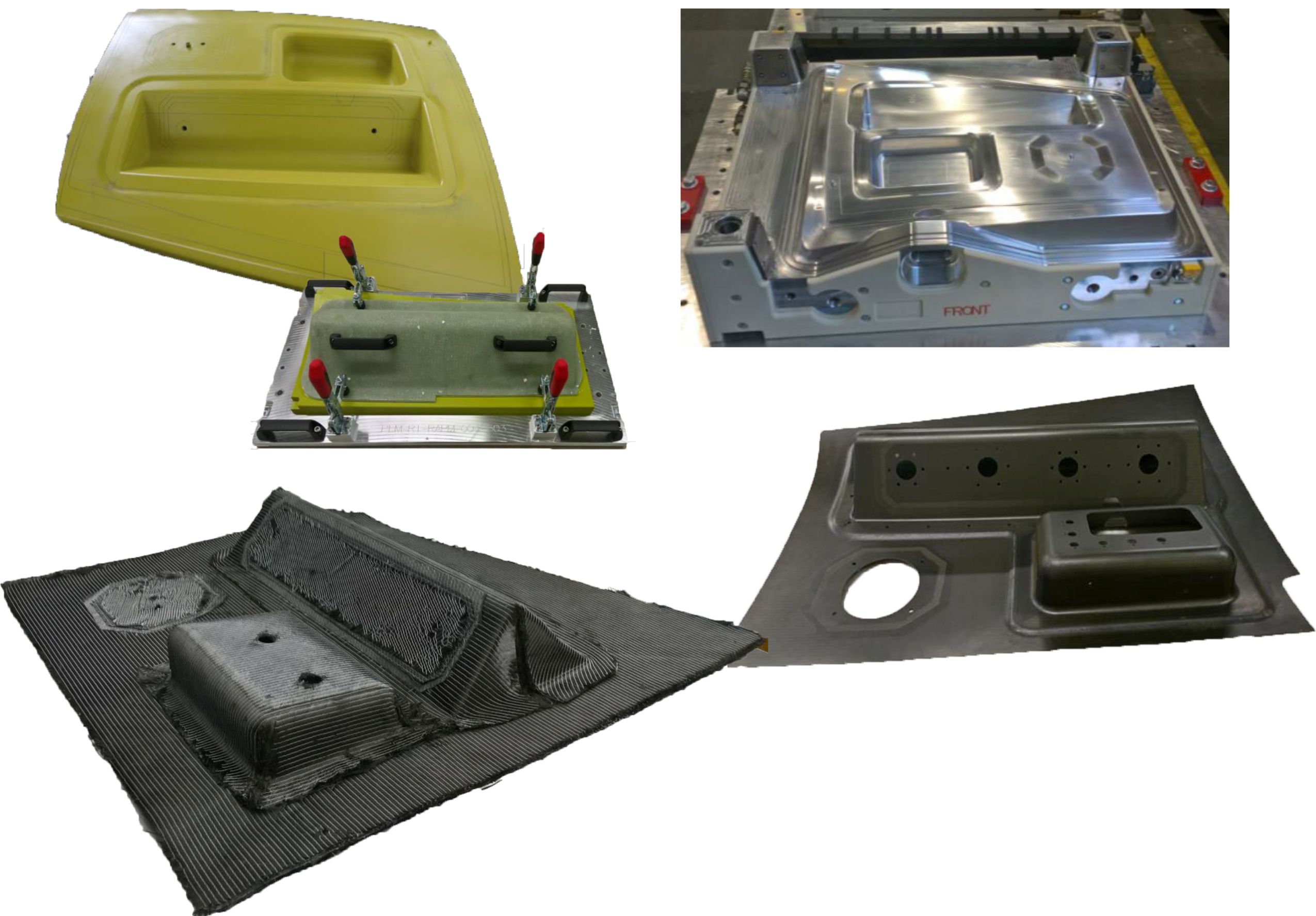
深抽挑战部分
然后将制造开发试验的结果用于开发挑战和过渡试验。 RI-RAPM-004 深拉挑战部分(图 3)的建模也完成了,它具有两个深拉:一个 5 厘米的矩形区域和一个从矩形过渡到 V 形的 10 厘米区域。受生产盘组件的启发,其复杂的几何形状确保了不均匀的树脂流动路径。 Huntsman(瑞士巴塞尔)使用 PAM RTM 软件(ESI 集团,法国巴黎)对使用 FAF2 两部分环氧树脂(Huntsman,美国德克萨斯州伍德兰兹)和 SGL Carbon NCF 150 的 LP-RTM 工艺进行了流动建模-克每平方米双轴和 190 克每平方米单向 (UD) 增强材料。
RI-RAPM-004 包括一个用于蒙皮的预制件、一个用于每个深拉部分以及两个堆积区(图 3)。这些预成型元件使用不同的叠层以满足设计的面板厚度(参见“制造 RAPM 的复杂几何部件 ”).
“低压预成型和 LP-RTM 允许使用具有成本效益的工具(与钢相比):带有手动夹具的预成型工具由基于聚氨酯的 Raku-Tool 材料制成(RAMPF Tooling Solutions,Grafenberg,德国);固化工具为5083铝材。
最初的 RI-RAPM-004 试验显示出口附近的流动出现意外异常,抬升了表面层,导致纤维变形。反转入口和出口解决了问题。在 130°C 工具中灌注和初始固化后,部件在 180°C 下进行后固化 60 分钟,然后加工成最终形状。十个高质量部件被交付给波音公司,用于自动超声系统 (AUSS) C 扫描。
完成的挑战部件显示出完全的固结、出色的纤维排列和良好的质量。这些部件的玻璃化转变温度为 197°C,纤维体积分数 (FVF) 为 49.5%,这是所用 NCF 的典型值。与当前的预浸料工艺相比,部件叠层件数减少了三分之二以上,并且接触人工估计减少了 90%。 RAPM 还使用符合航空航天标准的树脂和织物制作了具有挑战性的部件——以测试其开发的工具和工艺的适应性——以及通过无损检测 (NDT) 生产要求的制造部件。
轨道 2:TS 预浸料成型

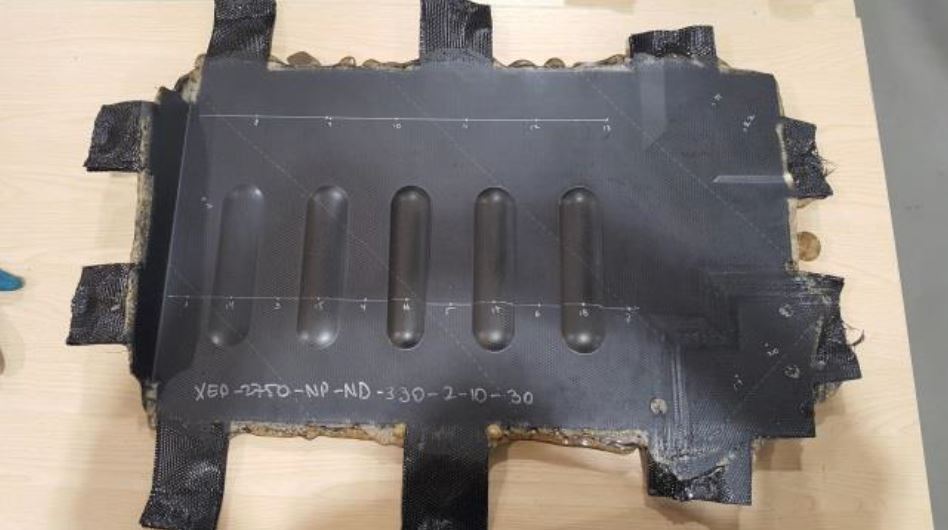
三个制造开发热固性 (TS) 预浸料零件是在英国 Heanor 的索尔维应用中心使用弹簧框架冲压和/或双隔膜成型 (DDF) 制造的。所有三个部件均使用基于索尔维树脂的环氧预浸料制造,包括 CYCOM 5320-1、CYCOM 970 和 CYCOM EP-2750 航空航天系统。 “CYCOM 5320-1 是我们处理非高压釜 (OOA) 部件的首选,但它也用作高压釜的合格系统,”Hahn 说。 “CYCOM 970 是溶剂与热熔预浸料的选择,[CYCOM] EP-2750 是我们的压制成型系统,因为它针对工艺的物理和动力学进行了优化,我们展示了它可以生产出最好的零件。”>
弹簧框架冲压和 DDF 是等温压缩成型工艺,其中热固性预浸料被切割、整理并合并为 2D 预成型件。然后预制件被预热,穿梭到匹配的金属工具中,并在传统的液压平板压力机中成型。预成型件可以通过弹簧框架(图 4)保持张力,这减少了成型过程中材料压缩区引起的起皱。或者,DDF 将预制件夹在两个隔膜之间,无需模具清洁和脱模。预制件用胶带粘在其中一个隔膜上,基本上将其保持在张力下,尽管不是直接 或像弹簧框架一样可剪裁。在 RAPM 中,弹簧类型、位置和张力使用模拟为每个零件进行了优化,弹簧框架也是如此。例如,串珠面板 TS-RAPM-009 使用了一个可以上下驱动的框架,以定制与压力机关闭平行的装料成型。
RAPM 在 15-30 分钟的初始固化后移除尺寸稳定的部件,然后批量后固化以提高速率能力,从而最大限度地减少了部件在工具上的时间。还使用单个工具集对零件系列进行了研究——例如,沿机翼长度具有三个不同法兰角的 C 型通道——以最大限度地利用单元格。指导 RAPM TS 方法的其他目标包括:
- 自动整理和成型以最大程度地减少人工
- 177°C 固化的航空航天机械性能
- 钢制工具,每个工具集可加工超过 1,000 个零件。
开发到“波浪”挑战部分
形成热固性预浸料制造开发部件,一次索引一个变量,直到达到足够的部件质量。评估了压力机关闭速度、关闭位置和关闭压力等变量,目的是将材料固结在流变曲线的正确点上,以产生内部静水压力,最大限度地减少树脂渗出并防止固化推进得太远,以避免开裂就职。一旦成型参数设定好,就会制造三到五个零件来验证工艺的可重复性,然后进行质量测试。由于高固结压力(20.7 巴),珠状面板的孔隙率小于 0.5%。还生产了可重复的、高质量的肋骨。
然后将学到的经验应用于波纹“波浪”挑战部件 TS-RAPM-012,以展示具有紧密半径(12.7 毫米)曲率形状的厚(6.3 毫米标称厚度)UD 层压板的压缩成型。为了满足要求,该部件使用了中间模量(IM7;Hexcel;美国康涅狄格州斯坦福德)碳纤维 UD 胶带的准各向同性铺层。 108 型玻璃纤维织物外层和 8 线束缎纹织物中的 Solvay THORNEL T650 标准模量碳纤维可保护 UD 纤维并防止与金属部件配合的一侧发生电偶腐蚀。使用 Solvay CYCOM 5320-1 环氧树脂可缩短(≤ 30 分钟)等温固化循环,并在 177°C 下进行 2 小时独立后固化。
波浪挑战部分是使用波音公司的 PtFS 工作单元和带有集成真空和树脂密封件的 P20 钢模具面成型的。工具腔比标称层压板厚度更薄,以解决材料树脂含量的变化,保持高质量零件的内部静水压力。
测试了三个工艺参数,包括冷成型(不加热预成型层)、热压实预固结和预制坯预热。冷成型因耗时且无用而被拒绝。为了预固结,将层压板真空袋装到带有编织玻璃纤维透气板的板上,并在 116°C 烘箱中在完全真空下进行 40 分钟的减压。尽管自动化红外预热是工业生产的标准,但在这些试验中,预热包括将预成型坯放入热模具 (179°C) 中,并在不接触的情况下尽可能关闭 3 分钟。然后将零件压缩成型。
完成的九个试验中的 8 个(#0-8)生产了最高质量的零件,主要归因于预固结。从中取出的样品符合厚度(其他部件的问题)和层压板质量,纤维体积为 59-63%,空隙率为 0-0.6%。
第 3 道:膀胱成形的 TP 肋骨和 C 通道
RAPM 选择了制造开发试验中的 TP-RAPM-002 加强筋来演示从原材料到成品复杂零件的单步压缩成型,并选择 TP-RAPM-003 弯曲通道进行两步法。圣路易斯波音公司使用 Accudyne Systems(美国特拉华州)压机成型 -002 肋,并使用 PtFS 设备加固 -003 C 通道的坯料。第二步,ATC Manufacturing 将 C 型槽坯冲压成零件。
对于 -002 肋,RAPM 使用了由 Solvay 提供的 12 英寸宽的 UD 胶带:12K AS4D 碳纤维(美国康涅狄格州斯坦福德的 Hexcel)增强聚醚酮酮 (PEKK)。 -003 C 通道使用来自 Cramer Fabrics Inc.(美国新罕布什尔州多佛市)的织物:2x2 斜纹布中的 3K AS4 (Hexcel) 未上浆碳纤维,粉末涂层聚醚醚酮 (PEEK);纤维面积重量为250克/平方米;树脂含量42%。
热塑性 (TP) 成型问题
TP 复合材料在比热固性材料更高的温度下加工——例如,PEEK 为 390°C,PEKK 为 375°C——这存在许多问题。能够承受这些高工艺温度的工具材料是有限的。此外,零件加工和移除之间的大温度增量使得难以保持均匀的工具温度。补救措施是热浸泡和/或缓慢上升和下降,这会延长循环时间。
高温还带来了热膨胀系数 (CTE) 挑战。模具材料的 CTE 通常与 TP 层压板不同,这会导致 TP 层压板从模具上收缩,从而降低施加的压力并防止完全固结。此外,TP 层压板的 CTE 沿碳纤维是恒定的,但呈垂直于纤维的双线曲线。这会导致 TP 层压板在加热和冷却时出现不同的平面内收缩和平面外收缩,也应在模具设计中加以解决。
TP 层压板也可能因加工而收缩,因为树脂体积随着从液体变为固体而减少。正是在这个冷却阶段,当关键的树脂基体结晶发生时,需要精确控制温度均匀性和层压压力,以确保成品部件的高质量特性。
另一个问题是模具需要完全密封以在成型过程中容纳熔化的 TP 液体。 “在 375°C 到 390°C 的温度下密封工具是很困难的,因为很少有合适的垫圈可以承受这个温度和 TP 成型压力为 300 至 500 psi 或更高,”Hahn 说。 “我们只能使用金属垫圈或匹配的金属工具来提供密封功能。弹性模具将非常有益,但是目前所有的弹性体都会在 TP 成型温度下分解。”
圣路易斯波音公司需要新的工具在只有垂直驱动的液压机中固结期间在肋的垂直元件上产生水平压力。它的解决方案是一个薄铝气囊(使用类似的系统来形成 TP-RAPM-003,图 5)。在高温下用惰性氩气加压,气囊膨胀以在固结过程中对所有零件表面施加均匀的压力。
顶部和底部工具由 410 不锈钢制成,与 UD 碳纤维/PEKK 层压板的面内 CTE 相匹配。在压制周期中,带有铝制气囊的上部工具下降并将叠层缓慢压入下部工具的母腔中。在这个一步过程中,气囊比最终零件厚度小 30%,以容纳大部分未固结的带预制件。该工具安装在带有电加热筒的传统压力机中,连接到 12 个独立控制区域 - 加上压板的六个主要区域 - 以控制加强筋法兰和腹板中的工具表面温度。
这些成型试验生产的复合材料部件具有合格的 NDI 结果。然而,气囊工具的设计需要进一步开发,以改进将叠层成型为零件的紧密内半径,并保持均匀的表面厚度。
整合 PEEK 织物坯料
对于 TP-RAPM-003 弯曲 C 通道,使用的粉末涂层 PEEK 2x2 斜纹织物具有相对较高的体积系数。 Boeing St. Louis first consolidated the layup, which dropped from 32 to 24 plies along the length of the part, into a flat blank with a tapered cross-section, and then sent the blanks to ATC Manufacturing, which stamped the final part with vertical flanges.
As with the rib, Boeing used a forming bladder and steel top and bottom tools. The bladder was changed to AZ31 magnesium, which better resists rupture versus aluminum. The C-channel tool was designed to operate within the Surface Generation PtFS forming cell to enable more rapid heating and cooling versus the conventional press with cartridge heaters used for the rib.
The C-channel tooling approach was developed to increase flexibility for multiple parts. The layup was placed onto the bottom tool, which was heated to the material’s glass transition temperature (Tg) to maintain pliability without melting. A volume reducing frame that included a pressure-sealing gasket was placed on top of the bottom tool, leaving a cavity slightly larger than the part layup (Fig. 5). Heat and hydraulic pressure were applied from the top tool through the bladder to the layup. Once at forming temperature, argon gas was applied to the bladder, forcing it down into the frame cavity to apply pressure to the tapered blank. The tool temperature was then increased through the melt phase of the material while maintaining bladder pressure, which prevented material from flowing across the lower tool while in melt phase.
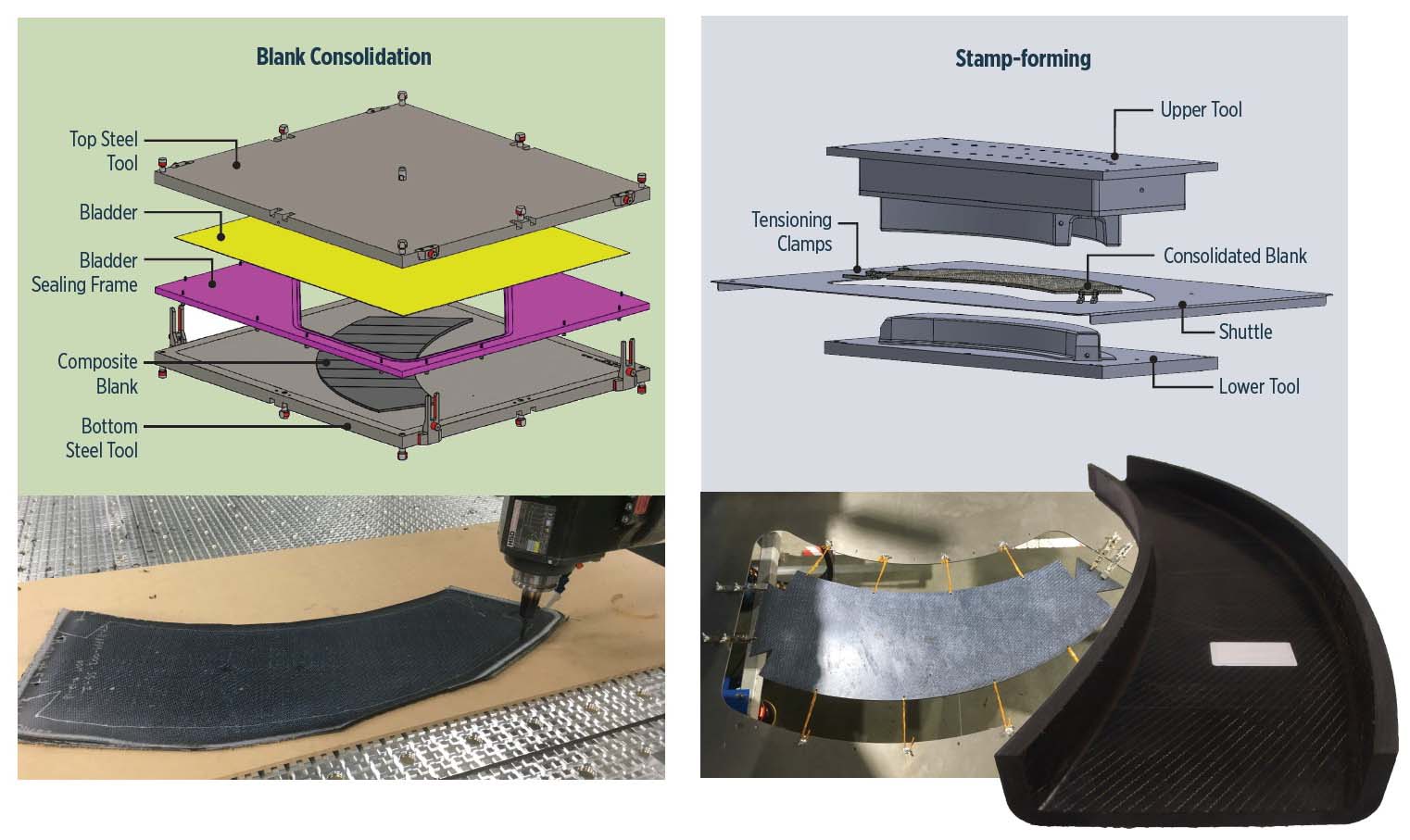
Preforming cycle time comprised 55 minutes for bladder and TP charge to reach process temperature and 30 minutes to cool below the PEEK crystallization temperature. Pressure ranged from 1.4 to 9.7 bar and was maintained manually from a high-pressure tank with a valve. With the recent incorporation of a pressclave system into the PtFS cell, autoclave-like control of vacuum and pressure (±3 psi) in the press mold cavity will be automated in the future.
TP stamp-forming
Consolidated blanks for the -003 C-channel were sent to ATC Manufacturing for stamp-forming, in which the blank is heated sufficiently above melt temperature to ensure polymer flow. It was then transferred to a rapidly closing press to form and cool the part quickly. The forming tool in the press is kept at constant temperature, enabling rapid cycle times by eliminating ramp-up and cool-down. The tool temperature must be between melt temperature and Tg to develop the required level of thermoplastic matrix crystallinity in a short time, yet ensure the part can be removed without deformation. A series of blanks with implanted thermocouples was used to validate the complete thermal cycle for stamp-forming the C-channel.
Forming simulations using Aniform software (Enschede, Netherlands) showed the highly drapable PEEK fabric blank still posed a risk of wrinkling in compression areas, namely the inner (smaller radius) flange. Thus, a tensioning system (Fig. 5) comprising shuttle plate and clips held the blank in tension as the matched metal tools closed to form it. Despite this, the flange face in compression still showed buckling as fiber was pushed inward at the inner radius. “All three RAPM tracks struggled to make this part,” Hahn contends. “Its geometry was extreme, and not so indicative of a real part, but more designed to push what we could achieve in formability.”
The manufacturing development trials led to challenge and transition parts that included multiple versions of the TP-RAPM-008 skin access panel, the TP-RAPM-013 rib with joggles on the flanges and a bladder study using three different geometries of the TP-RAPM-017 panel (Fig. 2). Boeing St. Louis produced all of these except for the TP-RAPM-013 rib, which ATC produced. “Even though this part was made with UD tape, which is typically more challenging to form versus fabric, we were able to form these parts very well,” says Trevor McCrae, R&D director for ATC Manufacturing. Overall, the TP forming trials showed that stamp-forming can produce complex geometries that might not be possible with conventional compression molding.
Learning to cut cost vs. aluminum
RAPM has demonstrated novel forming capability in all three tracks and amassed numerous lessons learned, ranging from how to position pad-ups to prevent slippage during compression molding to guidelines for part geometry to maximize quality and minimize tooling cost. “Understanding the effects of out-of-plane features, radius-to-thickness ratio and distance between geometric details becomes key as you move to small parts,” Hahn observes. “Standardizing features such as radii, curves and flange angles can help mitigate cost drivers, for example, reducing tooling costs, the number of forming trials during development and the need for multiple scans during NDI (nondestructive inspection) by enabling a standard AUSS shoe for a family of parts.”
Another cost driver RAPM highlighted was the time-consuming pre-consolidation step during TS prepreg compression molding. “Low-bulk and higher resin content prepregs widen the process window and increase repeatability for high-quality parts,” Hahn explains. “Solvay has developed a patent-pending ‘transformer film’ which can be applied to lower-impregnation prepregs before compression molding as a method of guaranteeing hydrostatic pressure in the mold cavity during consolidation.”
Although RAPM won’t officially end until fall 2020, followed by additional published results, findings so far for selected parts, which are based on real defense programs, show that composites can compete with machined aluminum (Fig. 6). Though the selected resin infusion and TP parts reduce recurring costs — e.g., materials, machine time, etc. calculated over total parts per family assuming non-recurring infrastructure is in place — the TS-RAPM-012 wave assembly actually shows a 7% increase vs. machined aluminum. However, it does achieve desired weight savings, and at a premium that is actually within the margin mandated by Hendrix:“No one is going to pay 2X for the weight savings composites offer; they must cost within 10 percent of aluminum.” However, he does concede, “There are still non-recurring time and cost issues to figure out, such as tooling and the development required to successfully form the shape.”
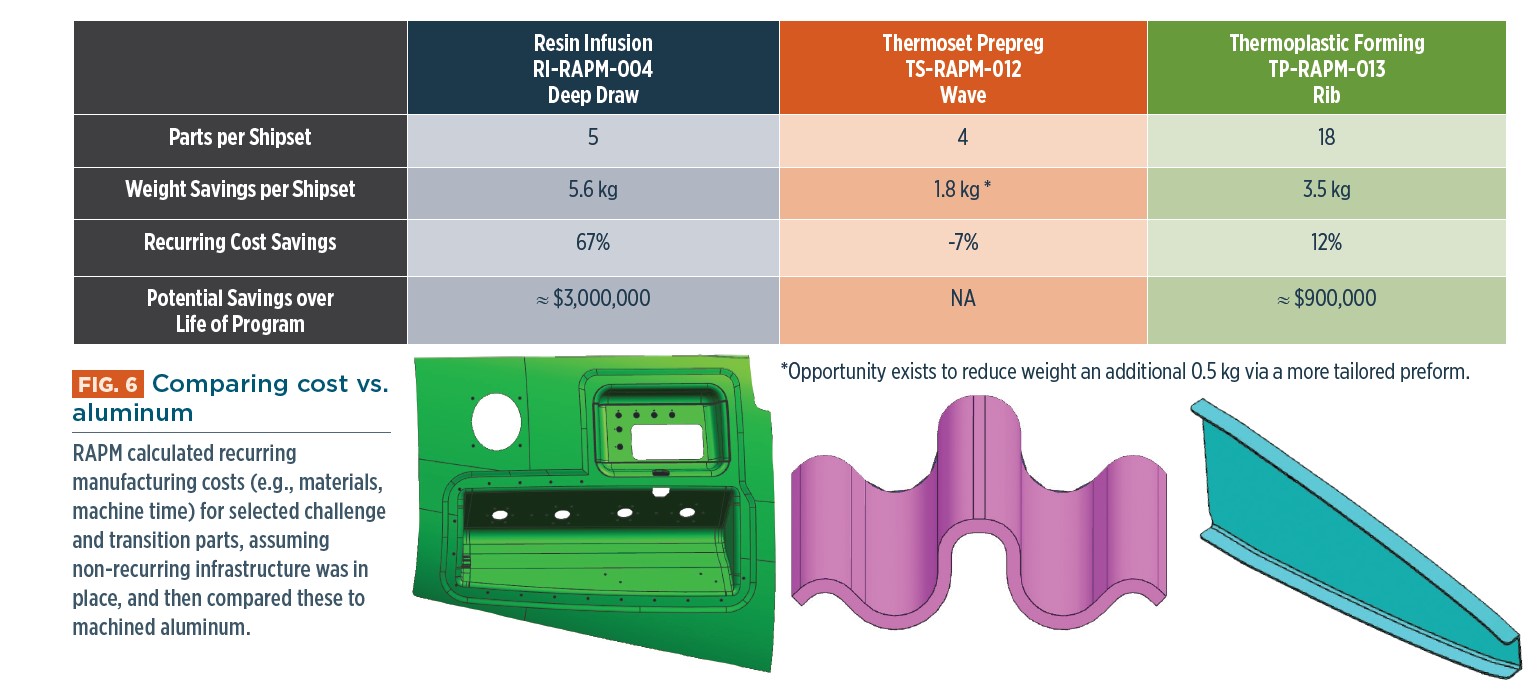
Expanding options
Although resin infusion wins for large parts, says Hahn, TS and TP stamping look pretty good for small parts. “Initial tooling cost for resin infusion is hard to overcome unless the metal parts are very complex, requiring a lot of machining,” she explains.
“Thermoplastics look good for high volume, but a subcontractor for a given program might not be set up to do thermoplastics. However, thermoset stamping might be a very good option, even for low-volume replacement parts. Because defense applications are so wide-ranging, it is important to have more than one material and process in a trade discussion.” Hahn notes that RAPM has opened up new materials and proven aerospace materials can work in automotive-type processes. “We also brought in new manufacturers.”
Hendrix agrees that RAPM’s aerospace and automotive manufacturing exchange was beneficial. Further, he was impressed with Solvay’s and SGL’s ability to form complex shapes without fiber distortion or other defects. “What it takes to make aesthetic auto parts actually has benefits,” he concedes. “You can’t have wrinkles or bad surface finish; they have to be perfect. But it still took multiple trials and significant development for them to form the RAPM parts. I’m not sure defense programs will want to invest in this non-recurring engineering if they’re dealing with small quantities. The economics will be on a case-by-case basis, but tooling and development remain issues we need to address.” Hahn adds, “We are publishing lessons learned, enabling more informed trade studies with expanded options and establishing a reasonably open basis for industry discussion.” 连续波 will continue this discussion with an update once RAPM wraps up later this year.
树脂