混合金属-热塑性复合材料结构的自动连接
实现工业规模的混合连接
FlexHyJoin 展示了一种大规模生产过程,用于生产带有焊接金属支架的热塑性复合材料屋顶加强筋,用于组装成金属白车身,就像该项目的用例菲亚特 Panda 城市车。来源 |静脉注射
混合金属复合材料结构继续受到汽车和航空航天应用的关注,通过将“正确的材料放在正确的位置”来减轻重量并提高性能。热塑性复合材料 (TPC) 因其快速加工(包括焊接和热成型能力)而对此类多材料结构具有吸引力。然而,到目前为止,将复合材料连接到金属上主要依赖于机械紧固件,这需要钻孔会损坏承重纤维。也已使用粘合剂粘合,但许多热塑性塑料难以以这种方式粘合;此外,粘合剂会增加材料和重量。例如,宝马 i3 使用碳纤维增强塑料 (CFRP) 底盘和塑料车身面板,使用 16 公斤粘合剂,这部分抵消了复合材料的减重潜力。
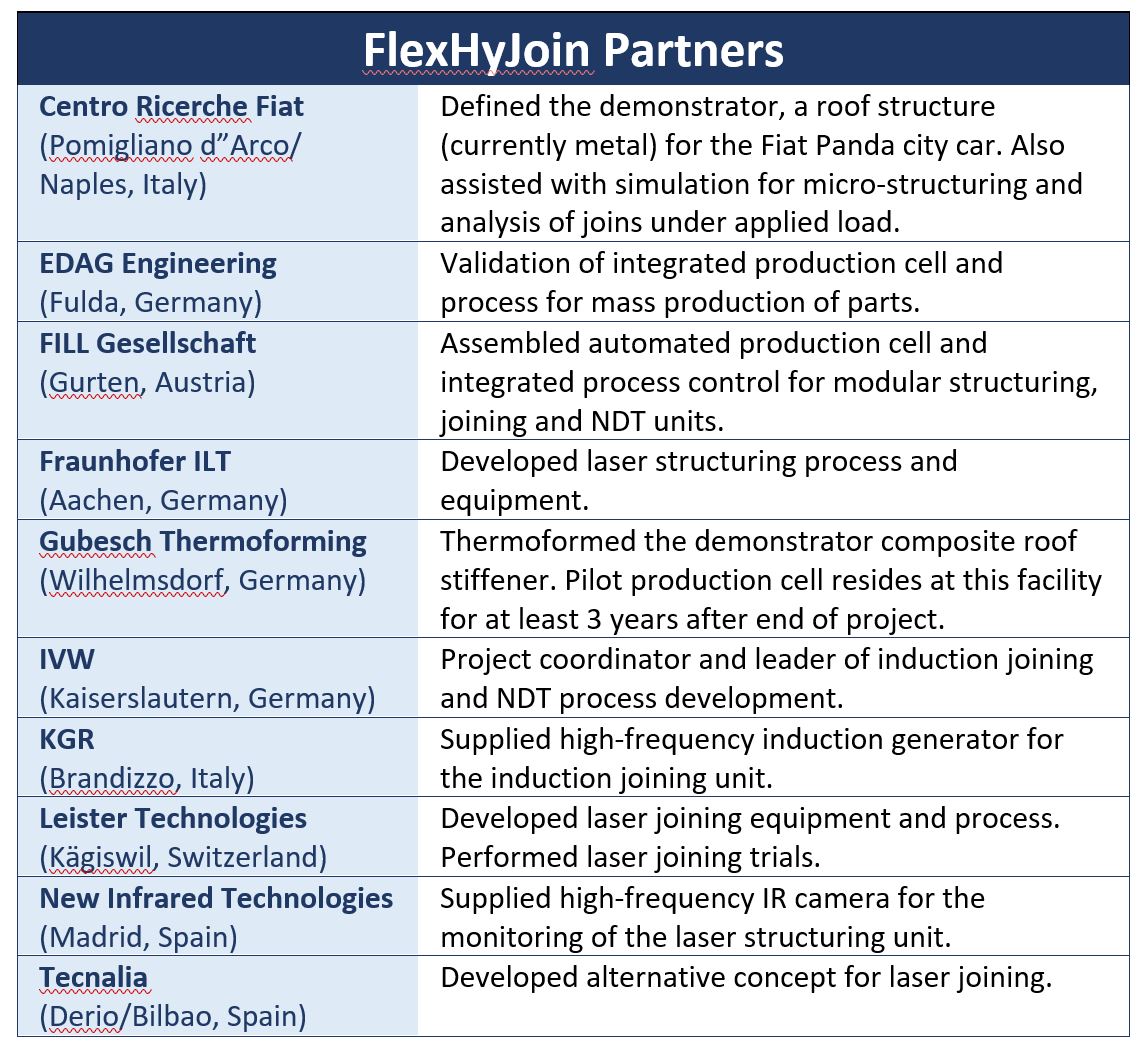
FlexHyJoin 是一个由欧盟地平线 2020 研究和创新计划资助的项目,于 2015 年 10 月至 2018 年 12 月进行,旨在解决连接 TPC 和金属部件的挑战。在 Institut für Verbundwerkstoffe (IVW) — 莱茵兰-普法尔茨州的一家非营利研究机构和德国凯泽斯劳滕技术大学的协调下 — FlexHyJoin 汇集了来自欧洲各地的 10 个合作伙伴,开发了一个自动化流程,使 TPC 汽车车顶成为可能结构以组装成金属白车身 (BIW)。该策略是通过激光预处理金属支架并通过感应和激光连接将它们连接到屋顶加强筋来生产重量中性、高强度的连接 - 无需粘合剂或紧固件。这是在具有集成过程控制和在线无损检测 (NDT) 的单个自动化生产单元中实现的。
混合演示器在 140 秒内
项目合作伙伴 Centro Ricerche Fiat(Pomigliano d’Arco/那不勒斯,意大利)提供了演示器部件的规格 — Fiat Panda 的车顶加强筋 目前由钢制成的城市汽车。对于 FlexHyJoin,该部件由 Gubesch Thermoforming(德国威廉姆斯多夫)使用由 Bond-Laminates(Brilon,德国)。为了将这个 TPC 屋顶加强筋加入Panda 的钢 BIW,一组由 0.7 毫米厚的 DC04 钢制成的侧支架(左右)被激光连接到两端。使用感应连接连接由相同材料制成的中心支架。 FlexHyJoin 表明这两种连接方法都可以用于工业混合结构的生产。
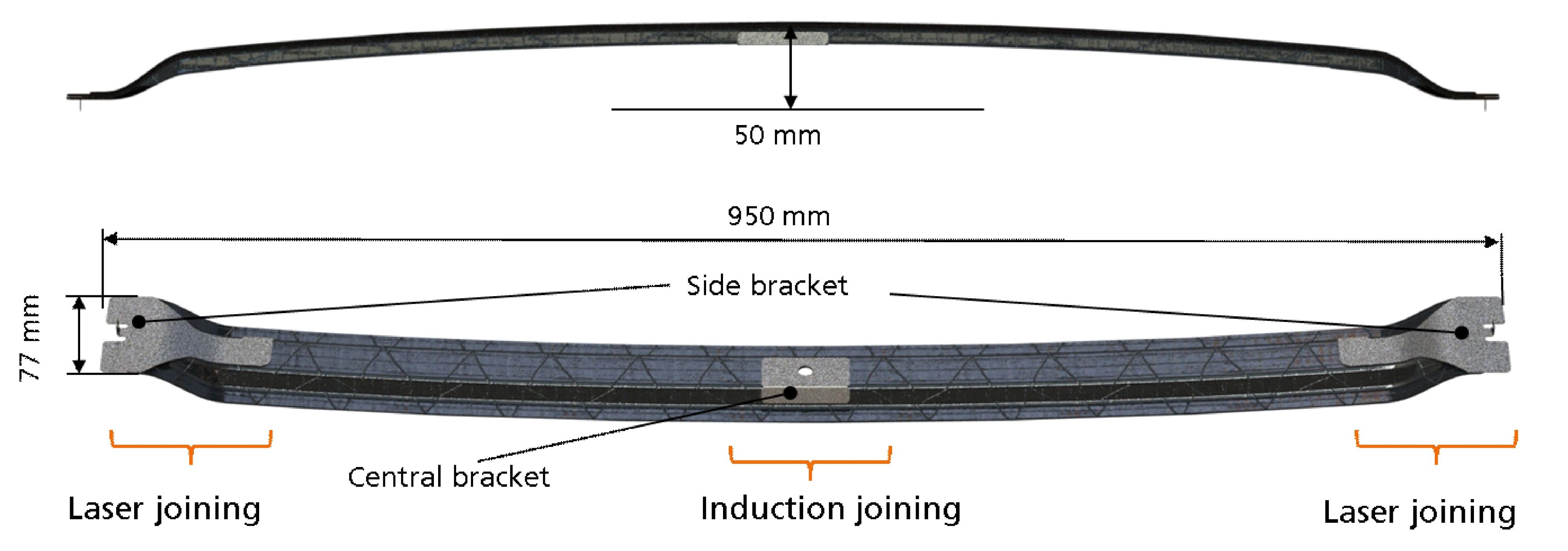
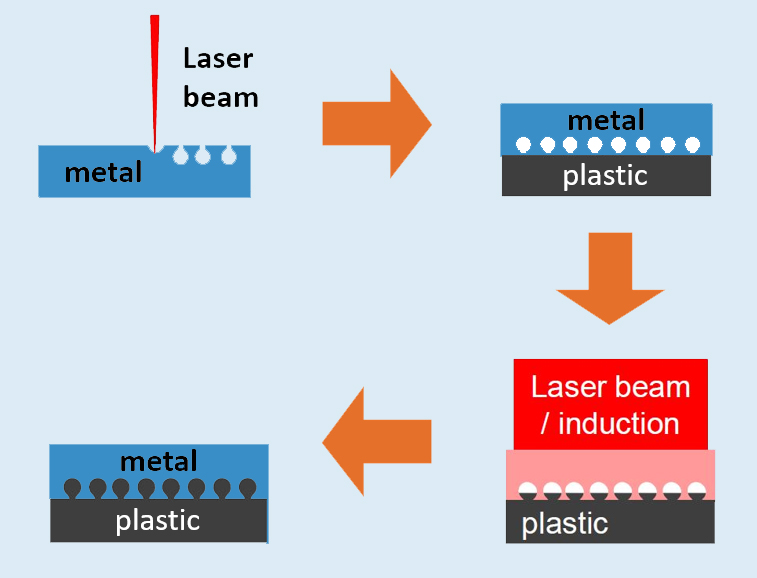
图。 1 混合连接的表面结构
FlexHyJoin 演示了将钢支架激光和感应连接到冲压的 GF/PA6 屋顶加强筋(顶部 )。这些混合接头依靠对金属支架的表面处理来产生底切,在连接过程步骤中,这些底切会填充熔化的塑料(底部 )。
来源 |静脉注射
简单地将 PA6 基体熔化到钢支架上不会产生足够强度的连接来满足结构要求。因此,在连接之前需要进行激光表面处理。 “支架的表面通过激光进行结构化以产生底切,”负责组装和集成自动化生产单元的 Fill Gesellschaft(奥地利古尔滕)的项目经理 Johannes Voithofer 解释说。 “经过处理的支架被放置在复合材料部件上。然后在连接过程中施加热量和压力,使复合材料中的 PA6 基体流入激光诱导的底切 [见图 1]。”结构化工艺是由另一家合作伙伴弗劳恩霍夫激光技术研究所(ILT,亚琛,德国)开发的,其结果是将材料粘合和机械锁定相结合的金属复合材料连接。
然后将连接的零件转移到无损检测站,在那里使用一种热成像技术扫描它们是否存在缺陷。 “卤素聚光灯用于复合材料表面的调制加热,”IVW 研究助理兼开发 FlexHyJoin NDT 和过程控制的负责人 Vitalij Popow 解释说。 “这导致复合结构内出现振荡的温度场。我们随着时间的推移分析表面的热响应并识别接头中的缺陷。”全自动测试在生产单元内针对每个制造的组件完成。该过程的验证是在大约 400 个关节上进行的。
目前配置的 FlexHyJoin 自动化生产单元并行运行激光成型、连接和无损检测,循环时间分别为 81 秒、98-108 秒和 100 秒,不包括机器人在工作站之间传输零件的时间。 Voithofer 表示,每个完成的混合部件的循环时间大约为 140 秒。
图。 2 实现工业规模的混合连接
FlexHyJoin 试点生产单元具有三个模块化工作站,用于表面结构化、连接和无损检测。该单元的单个搬运机器人将部件从装载抽屉转移到每个工位,将成品混合部件放置在相邻的抽屉中。来源 | IVW和填充
激光结构化
激光成型工艺在金属支架的连接表面上产生带有底切几何形状的线条。对于 FlexHyJoin,底切的宽度为 75 微米,深度为 215 微米。这些测量值以及线数和线的整体模式都可以定制,并且在理想情况下可以匹配以满足零件和周期时间要求。
“连接表面上微结构的位置和数量可以适应组件中的负载,”IVW 研究助理兼 FlexHyJoin 感应连接单元开发团队负责人 Stefan Weidmann 解释说。 “微结构之间的距离可以在接合表面的高负载区域减小,在负载较小的区域增加,从而实现有效的微结构工艺。”
通过使用由 IPG Photonics(德国布尔巴赫)提供的高功率单模光纤激光器烧蚀金属支架表面来实现结构化。这种 YLR-1000-WC 激光器在 1,070 纳米的发射波长下具有 1,000 瓦的最大输出功率。 Fraunhofer ILT 聚合物加工团队负责人 Christoph Engelmann 解释说:“我们将单模光纤激光器用于微结构工艺,因为它具有高聚焦性,可保持大约 40 微米的光斑尺寸。
激光器包含在安装在 ABB 1200 机械臂上的光学头内。 “在光学头内部,我们有两个电流计反射镜,可以在 240 毫米 x 240 毫米的工作场中偏转光束,”恩格尔曼详细说明。 “此外,还有一个可移动的镜头来跟踪 z 高度(z-shifter)。我们只使用机器人将扫描头定位在金属部件上方,然后光束被反射镜偏转,微结构每条线的 z 位置由 z 移位器调整。因此,在加工过程中头部没有移动。通过这种方式,我们能够处理 2.5D 零件,对于每条离散线保持相同的 z 位置,但能够在线之间进行调整。”
“出于安全原因,结构单元和连接单元都是封闭的,”Voithofer 解释说,并指出了试生产单元中的黑色机柜(图 2)。因此,在激光操作期间,自动门/门保持降低,打开以移除成品部件和插入新部件。
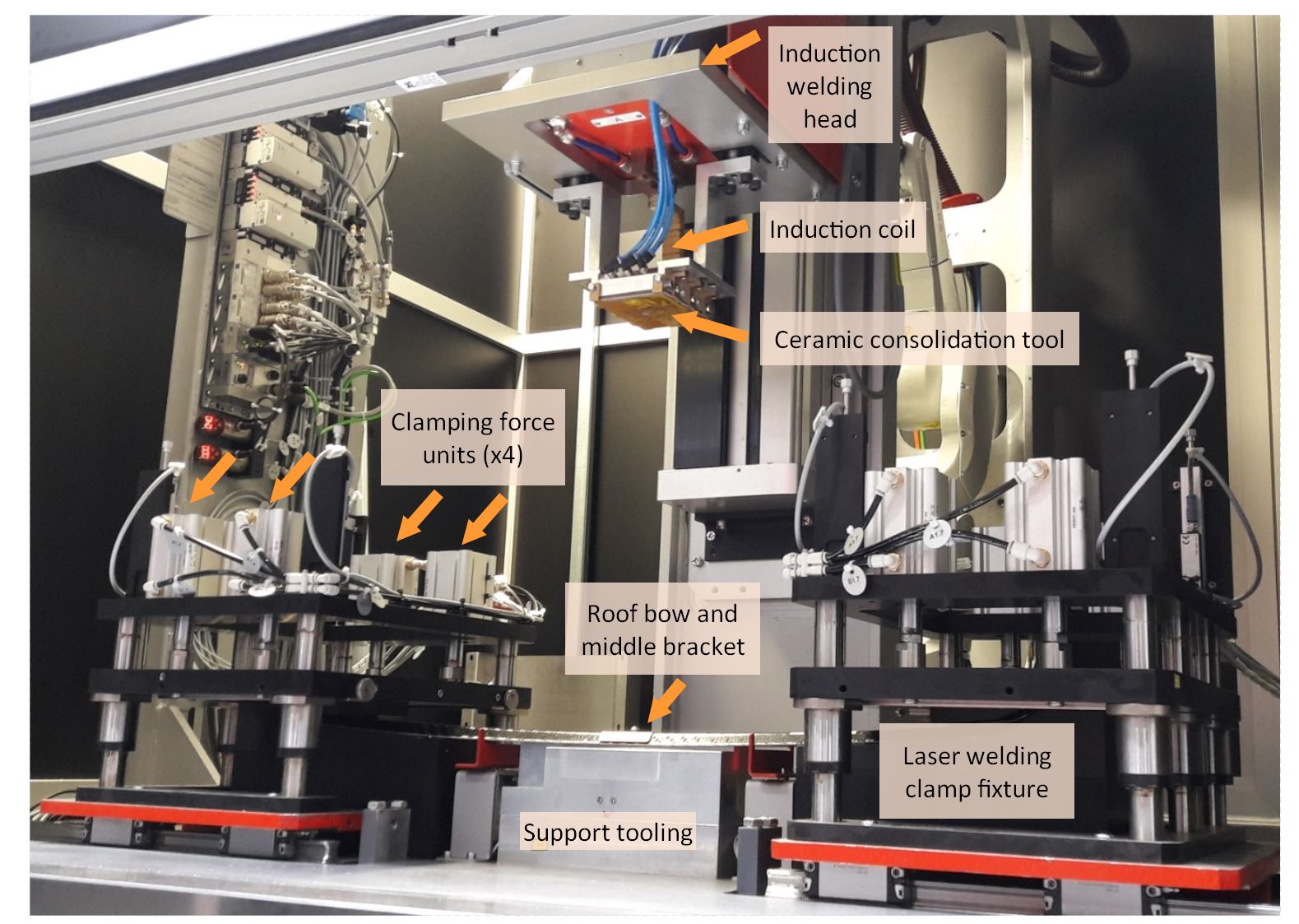
图。 3 感应和激光连接单元
在连接单元中,感应连接用于连接中间支架,而激光连接用于连接复合材料车顶弓两端的侧支架。来源 | IVW和填充
感应和激光连接
与结构单元相邻的是连接单元,它包括两个不同的操作:中心支架的感应连接和左右侧支架的激光连接。 “对于具有中等复杂性的较大零件,如中心支架,感应连接是一种更合适的连接方法,”魏德曼说。 “带有感应器的陶瓷固结工具对连接区域施加压力,并且对电磁场是可渗透的,从而将有效的能量输入到金属支架中进行加热。这对于扁平形状很方便,但对于复杂形状(例如侧支架的几何形状)更具挑战性。因此,对这些使用激光连接更有效。” Weidmann 补充道:“感应连接最适合大型零件和中等复杂度的零件,而激光连接更适合高度复杂的零件。”
复合屋顶加强筋中的钻孔将其对准支撑工具的顶部,其形状与热成型加强筋的曲率相匹配。中心支架上的激光切割孔将其定位在车顶加强筋上,而侧支架则根据与车顶加强筋末端相匹配的形状对齐。
“中心括号使用 discontinuous 感应加入。 “这本质上是准静态压力连接,”Weidmann 说,“这只是意味着它是一个静态过程,在一个地方实现区域连接,但在 z 方向上有移动,因为复合材料的厚度会因在(感应)连接过程中施加的固结压力。”
感应连接单元包含一个 KGR(Brandizzo,意大利)高频发生器,为感应线圈提供交变电场。头部通过电动机和主轴移动(图 3),使陶瓷固结工具向下压到金属支架上。固结工具中的感应线圈使金属发热,从而熔化复合基体并形成接头。 “在整个加热和冷却过程中都会施加压力,”魏德曼指出。
侧支架的激光连接与感应连接同时开始。位于支撑工具两侧的两个夹紧装置可以对侧支架施加 4,000 牛顿的夹紧力。 “为了最大限度地减少复合材料和金属部件之间的间隙,夹紧是必要的,”Voithofer 解释说。 “这可以防止接头中出现空隙。”施加夹紧力后,激光头移动到位。它配备了由 Leister Technologies (Kägiswil, Switzerland) 提供的 LineBeam 二极管激光器。 Leister 的 Johannes Eckstaedt 解释说,这种激光器在 980 纳米的发射波长下具有 600 瓦的最大输出功率。光束通过光学透镜形成 27 毫米 x 1 毫米的线,并聚焦在金属支架上。激光头安装在机械臂上,使其能够沿着成形的支架表面移动。 “我们为支架的每个区域设置不同的速度,以实现均匀的接合温度,从而降低热应力以获得最佳接合效果,”Eckstaedt 说。
通常,激光接合可以使用透射接合或热传导接合。对于激光透射接合,被接合的复合材料对于选定的激光波长必须是透明的。然后激光穿过复合材料,撞击支架的金属表面并加热它。然而,这种方法没有用于 FlexHyJoin 演示器,因为屋顶加强筋的有机薄板层压板不是激光透明的。相反,使用了热传导连接的替代方法。这只是将激光直接应用于金属表面,金属表面将热量通过金属基材传导至复合材料,在 220-300ºC 下熔化 PA6 基体并形成接头。 Voithofer 说:“由于钢支架的高导热性,激光热量可以快速传播,从而有效地连接侧支架。”
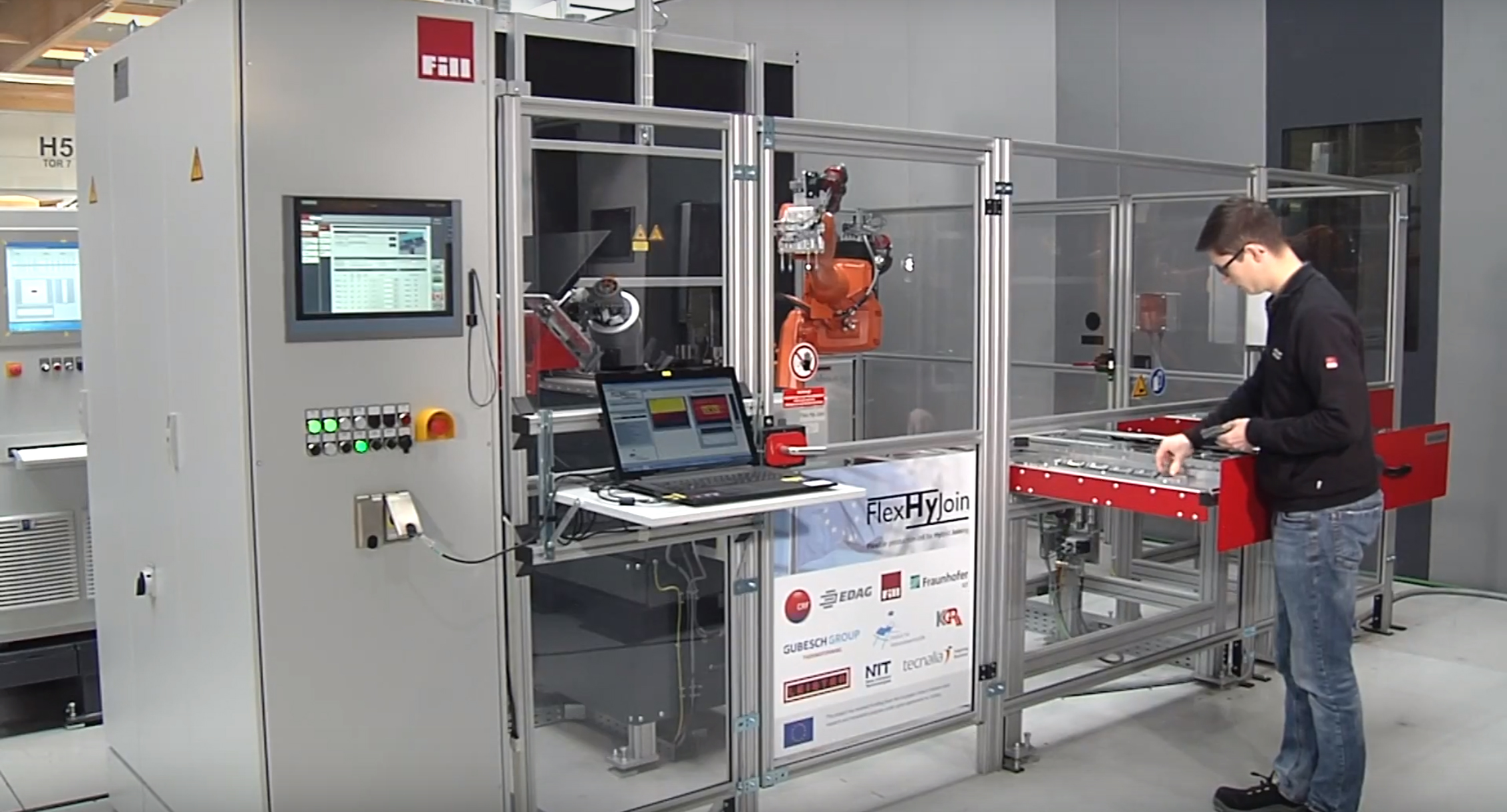
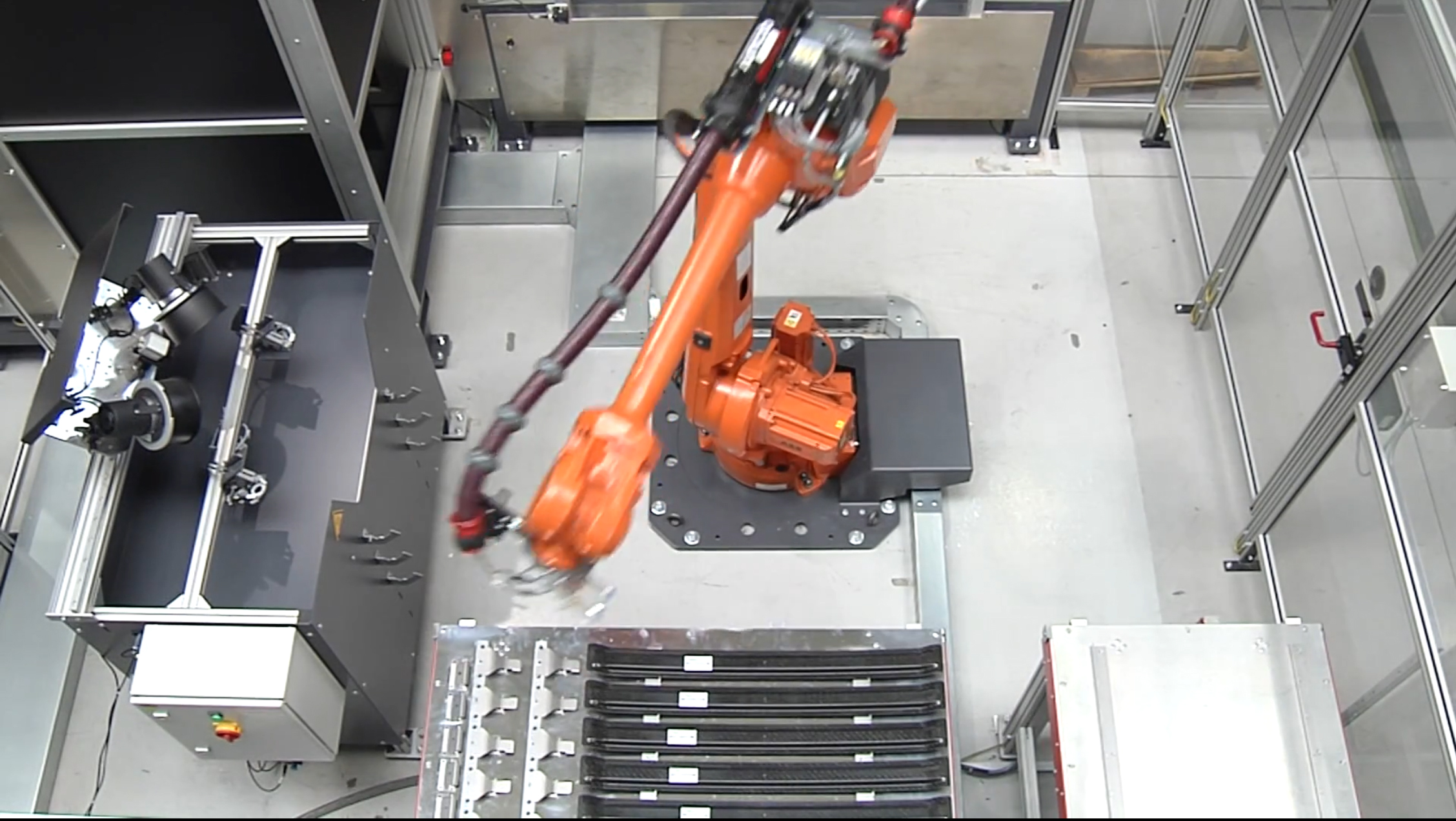
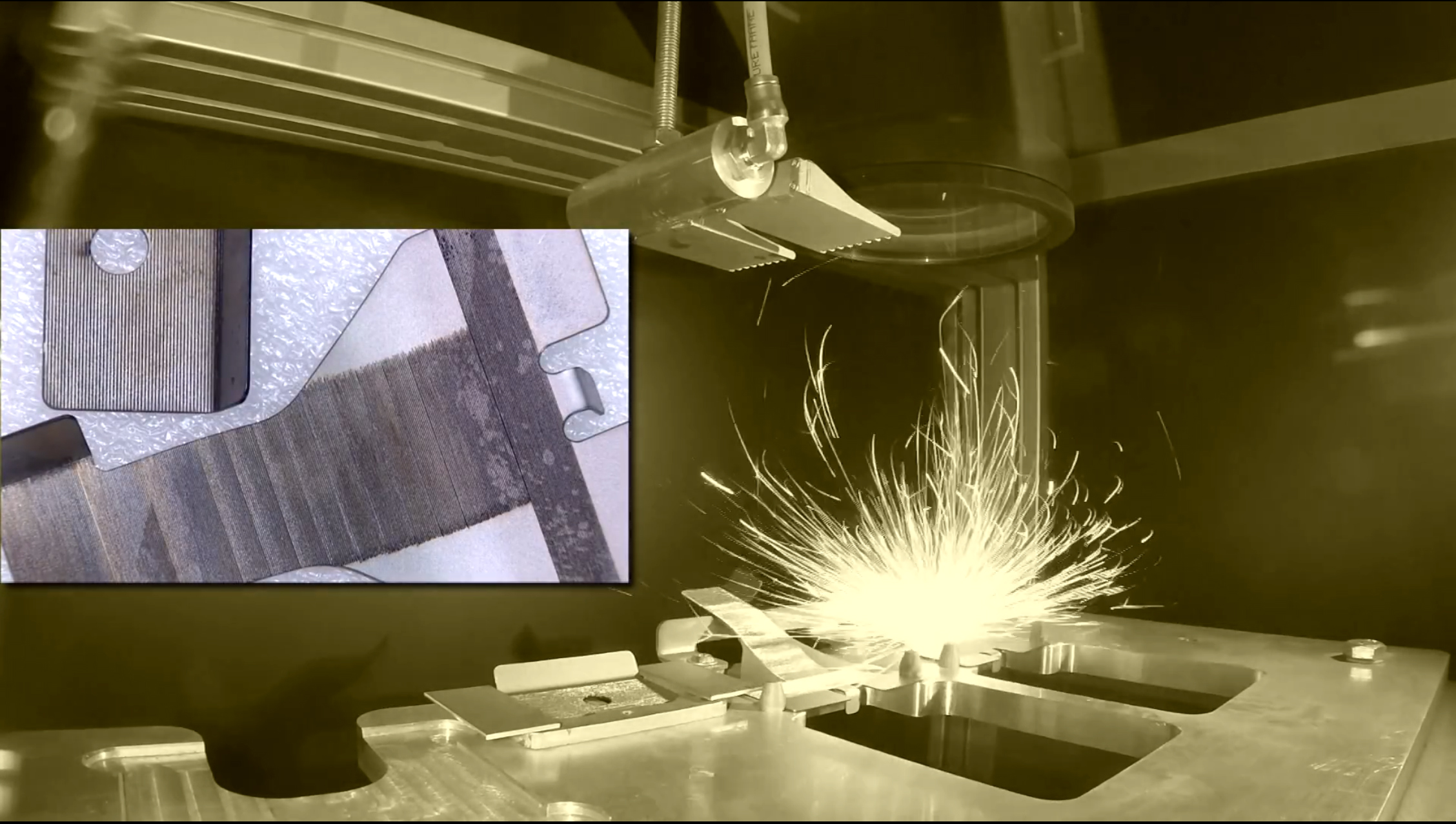
第 3 步。 在结构单元内,高功率光纤激光器在支架表面形成底切,以连接到复合屋顶加强筋中。
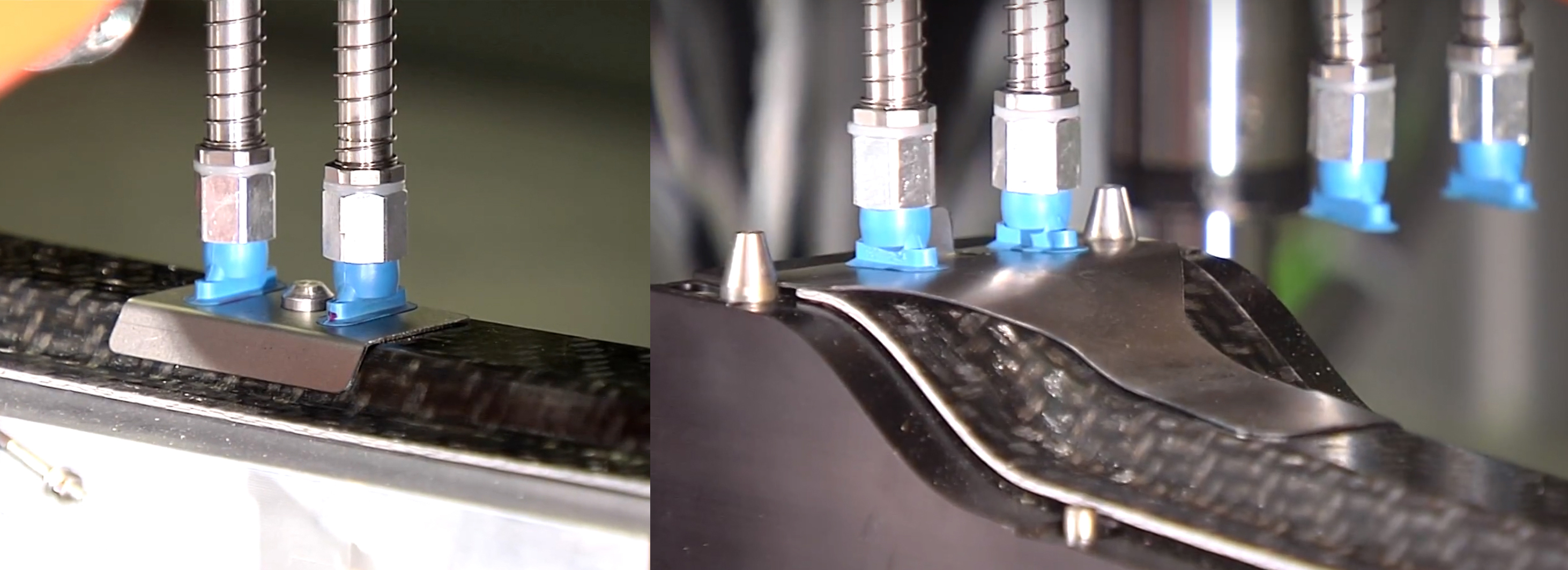
第 5 步。 机器人返回结构单元,拿起处理过的支架,将它们结构化的一面朝下放在 TPC 车顶弓上。
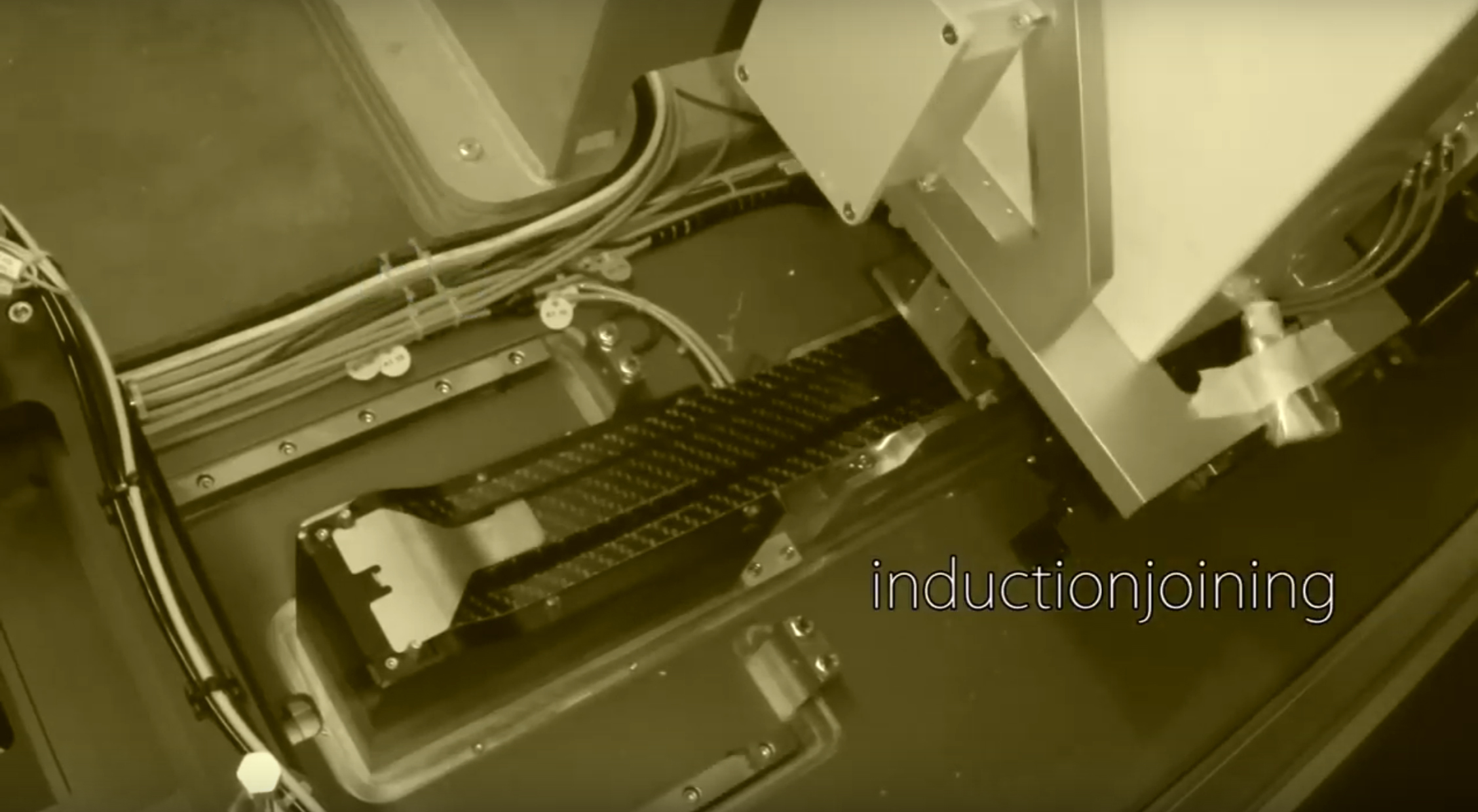
第 6 步。 然后机器人将夹紧装置放置在三个支架上。感应连接单元下降到中心支架上。感应线圈使金属支架发热,熔化下面复合材料的 PA6 基体。
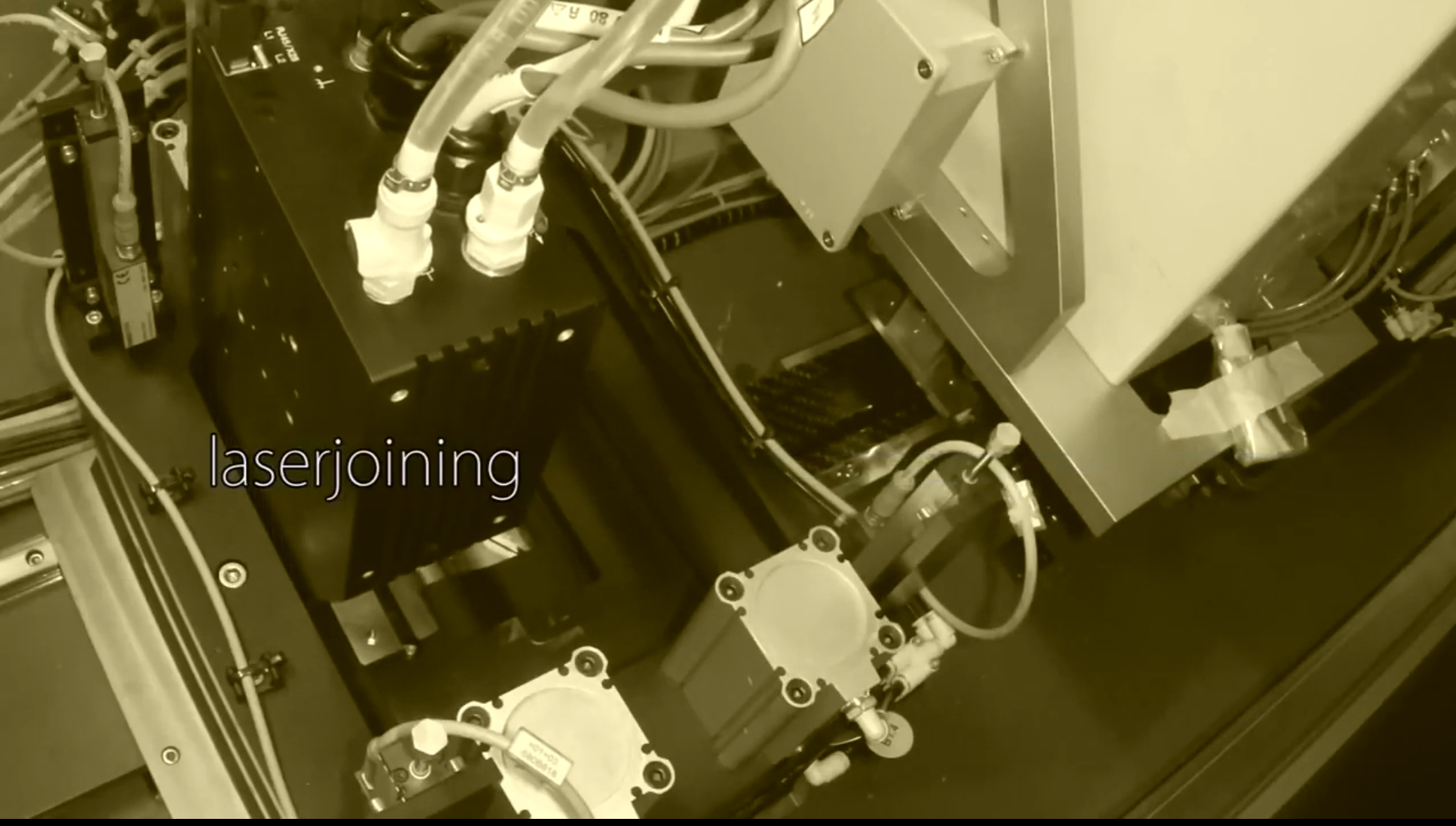
第 7 步。 感应连接完成后,降低激光连接单元以连接左侧和右侧支架。激光加热金属,使下面的 PA6 基体熔化到底切中,形成高强度连接。
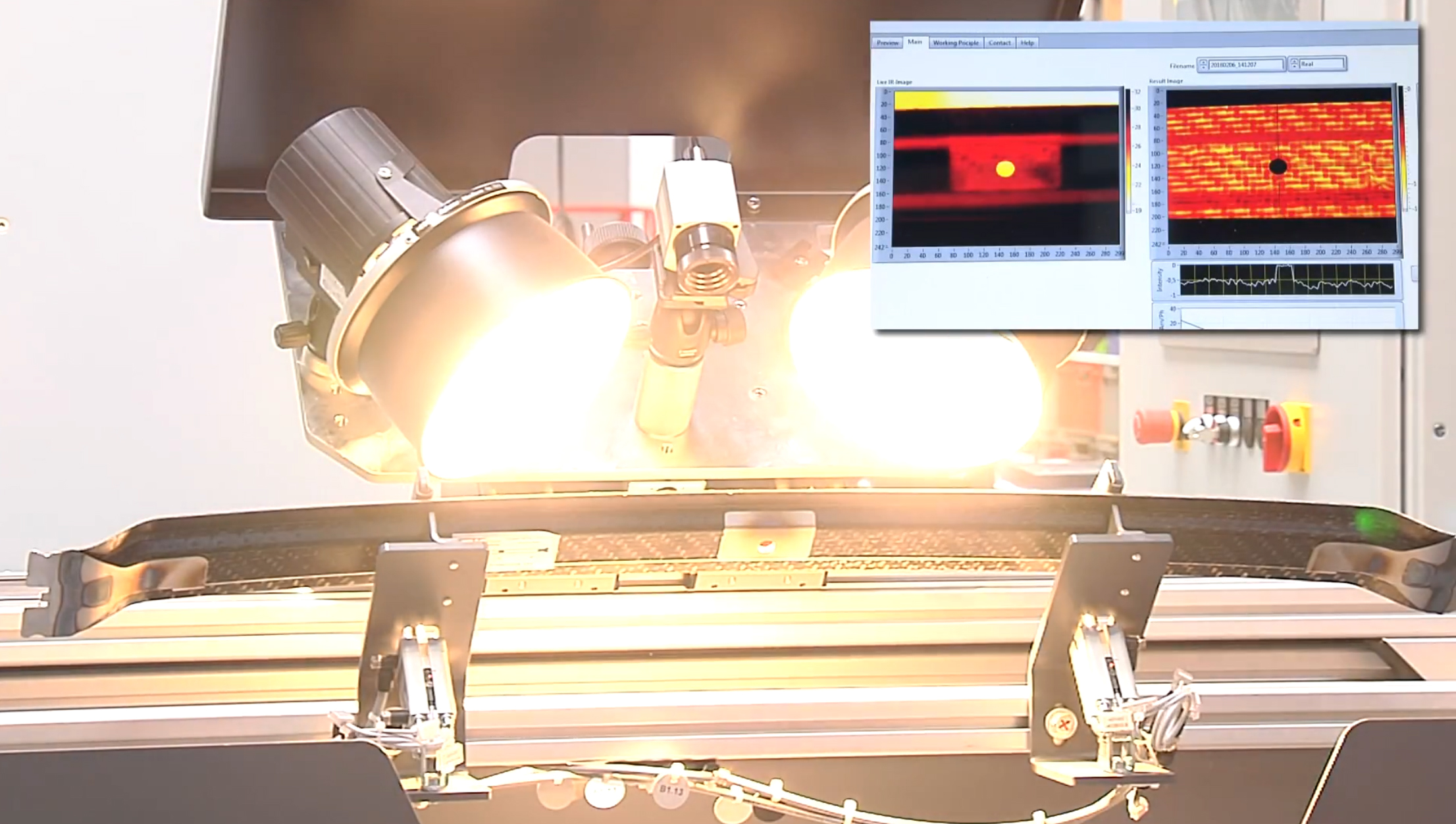
加入过程控制
控制两个连接过程的基本方法是测量温度和时间与一组通过测试定义的优化参数。 “因此,我们制作了具有不同参数的连接测试样品,并使用特殊的测试设置对每个参数集进行了机械测试。对于侧支架,开发了剪切测试和剥离测试的组合,对于中心支架,我们使用了压力负载测试,与搭接剪切测试相当,但您用推力代替拉力,以获得剪切负载在连接区域,”Popow 说。这些特殊测试的设置是与 EDAG Engineering GmbH(EDAG,Fulda,德国)一起设计的,该公司还对测试结果进行了分析。按照此程序,确定了连接工艺的最佳参数集,然后用于中试生产单元。
“感应连接过程已提前校准,”魏德曼说。 “我们知道我们在大约 30 秒后达到接合温度,但出于安全原因,我们也会现场测量温度以避免过热。”远程测量表面辐射的高温计用于测量感应连接区域中的已知热点。 “但由于高水平的原位辐射光和热,它无法提供激光连接的准确测量,”他解释说。然而,接触式传感器可用于激光连接区域的复合侧,但它们不适用于感应连接过程,因为它们通常由金属制成,会因感应而发热并使测量结果失真。
“所有接头的加热区域也被压制工具和夹具覆盖,”魏德曼指出。 “因此,作为质量保证方法,我们已经验证了连接前后由于压力和热量引起的部件厚度变化。”这种厚度变化是由集成在屋顶加强筋定位工具中的距离传感器测量的(也如图 3 所示)。 “当我们将零件压在一起时,距离传感器就会移动,”他解释说。 “当我们施加热量和连接压力时,熔化的基体聚合物流入激光结构的空腔,并被轻微挤压出连接区域,直到接头冷却。这会导致距离传感器记录的厚度变化。” Weidmann 和 IVW 团队将此距离与零件质量相关联。 “厚度变化 - 换句话说,压实 - 大于 0.1 毫米意味着接头质量良好,”魏德曼指出。
在线无损检测
IVW 开发了另一种质量保证方法——在线热成像测试。 “对于质量保证,主要目的是查看连接区域的属性,”Popow 解释说。 “但这非常困难,所以我们在零件完成后对连接处的复合材料侧进行了热成像。”
IVW 选择了一种称为锁定热成像的主动热成像技术,因为它提供了比其他主动方法(例如脉冲相位热成像)更好的信噪比,并且还可以检查更深的缺陷。 “基本思想是将热量放入复合材料中,然后将热量传导到连接区域并返回表面,”Popow 说。 “使用锁定热成像技术,组件在几个 期间。然后我们随着时间的推移分析这种反应。如果复合材料表面和连接区域之间存在由于空隙或缺陷而导致不均匀的区域,则会在热响应中显示出来。”
热响应被捕获为图像。组成这些图像的点是像素,是图片元素的缩写。每个像素也是一个测量点。因此,分析了整个检查区域上每个像素的温度信号。 “因此,您可以获得每个像素的幅度和相位信息,然后软件再次将其重建为图像,可以进行目视检查,”他补充道。但它也为测试的 126 个零件提供了大量的测量结果。 “我们将这些无损检测结果与 EDAG 进行的机械测试结果相关联,”Popow 说。他的团队还在移除支架后测试了连接区域——即破坏性测试。 “因此,我们将三组测试结果关联起来,现在可以从热成像结果的视觉分析中识别低强度与高强度粘合区域,”他说。
用于批量生产的集成单元
Weidmann 说,FlexHyJoin 的最大成就之一是将所有技术单元(每个单元由不同的项目合作伙伴开发)集成到一条自动化、优化的生产线中。在 Fill 集成设备的 Voithofer 解释说:“运送给我们的每组设备都使用不同的控制器。我必须设计一个主 PLC 来控制所有不同的过程单元。”这包括由 Fill 提供的激光外壳和单元的搬运机器人。 “让所有这些流程步骤协同工作也非常困难,因为它们需要不同的时间,”他补充道。
Voithofer 首先为每个处理单元和机器人开发一个架构,考虑如何定位这些单元以获得最佳流程。 “我们的概念是将三个工作站——结构、连接和无损检测——模块化,放在三个独立的外壳中,”他说。 “通过这种方式,我们可以提取单个单元并在贸易展览或其他示范项目中使用它们,然后将它们归还。因此,工作单元是模块化的,但又是集成的。”
Fill 在连续复合材料生产的此类系统集成方面数十年的经验帮助实现了 Popow 认为的 FlexHyJoin 最伟大的壮举:从实验室规模转向工业规模。 “我们是第一个实现此类工艺的财团,该工艺适合大规模生产与金属结合的复合材料,”他说。 “该工艺可用于许多汽车部件,例如稳定杆、保险杠和车门,”Voithofer 指出。 “轻型 BIW 中有许多复合材料部件与金属部件相连。”
多行业适配
但是,在将电池投入批量生产之前,需要进行一些更改。 Voithofer 说:“我们不再将激光器的结构和连接保留在单独的外壳中,而是将它们合二为一。” “这将消除在这些过程之间打开和关闭外壳门的需要,从而缩短周期时间。”他还将在传送带上线性连接所有站点。因此,该生产线将连续运行,在离开单元准备组装成 BIW 之前,部件被拾取并放回每个工位的传送带上。这将进一步缩短周期时间。此外,能够容纳数百个零件的扩展抽屉将使生产线能够在整个班次中运行,而无需再补给。
尽管该试点生产单元是针对汽车行业的,但 Popow 指出,它可以轻松适应航空航天、体育/消费品和工业应用。 “这实际上是主要准则之一,”魏德曼说,“它必须能够连接不同的几何形状和零件。唯一的变化应该是感应连接压实工具、用于激光连接的夹具和支撑工具。细胞的主要部分应该保持不变。”他指出,IVW 还展示了钛和钢与编织碳纤维/聚苯硫醚 (PPS) 有机片复合材料的混合连接,目前正在开发聚醚醚酮 (PEEK) 和聚醚酮酮 (PEKK) 演示。 “这只是需要调整连接工艺以适应更高的温度并重新定义最佳工艺参数,”魏德曼说。 “该电池对各种材料开放,包括铝和铜以及其他热塑性复合基质系统,如聚丙烯和聚乙烯。”
“项目合作伙伴合作得很好,很高兴能够进一步发展,”他指出。 “我们认为这种类型的生产非常有前景,到目前为止我们从行业收到的回应表明,有很多公司也看到了这种前景。”
树脂