热塑性初级航空结构又向前迈进了一步
热塑性复合材料的优点,如韧性、相对较高的平面外强度和可持续性/可回收性,吸引了飞机设计 几十年来,工程师们一直对热塑性复合材料主结构的概念有所了解。但是飞机制造 工程师一直不确定是否要找到一种经济高效的方法来将他们从 CAD 模拟推进到生产车间。然而,他们并没有被吓倒:全球仍在继续努力开发必要的制造技术——也许没有荷兰像荷兰那样顽强。
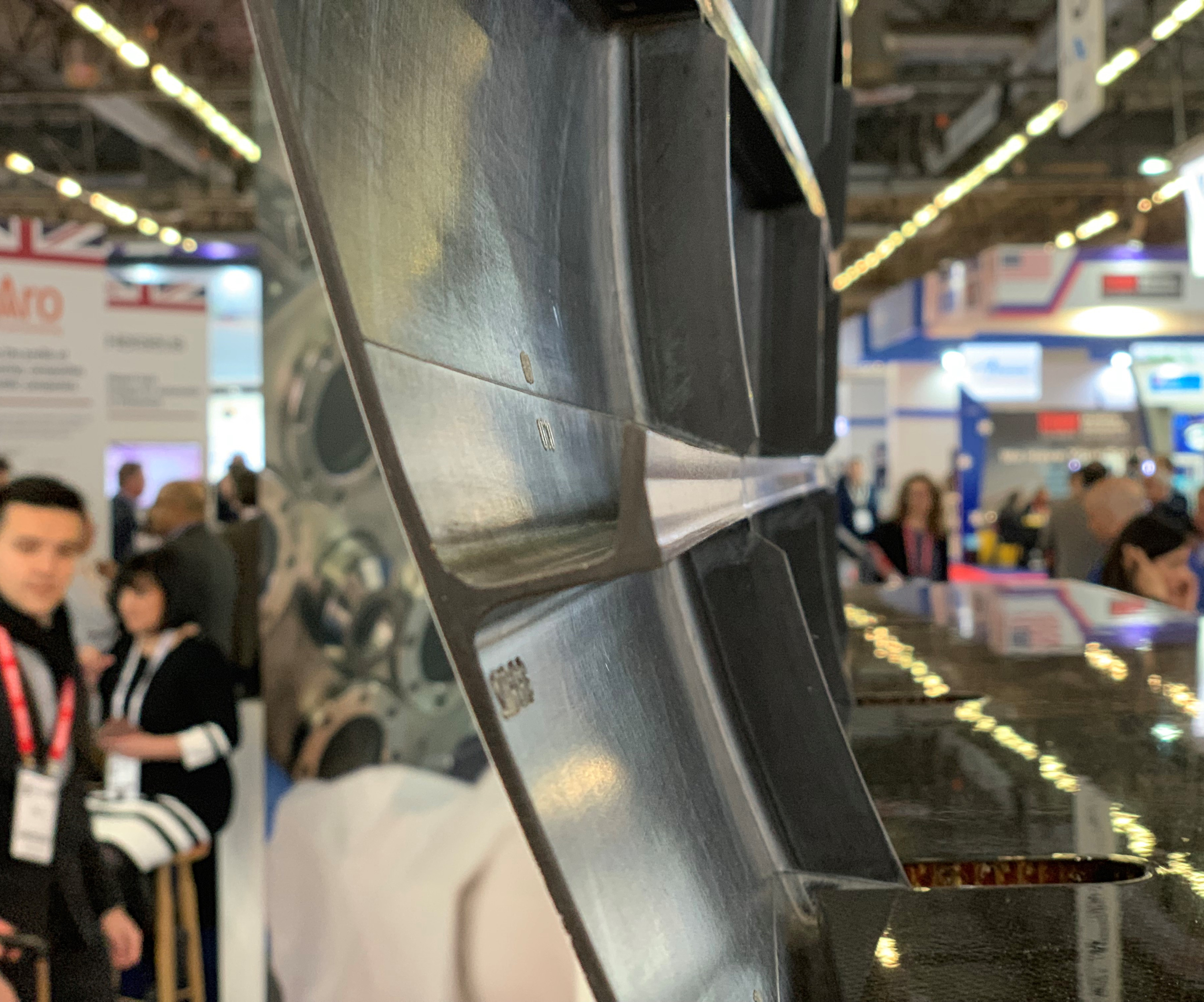
一体式 L 型纵梁。 GKN Fokker 碳纤维/PEKK 机身,专为湾流设计和制造,采用弯曲的纵向 L 型纵梁,略呈钝角,便于工具释放。 连续波 照片|杰夫·斯隆
2009 年,九家荷兰工业公司和研究机构与空中客车公司(法国图卢兹)一起成立了热塑性经济型飞机主结构(TAPAS)联盟。该倡议在 2014 年扩大到 12 个合作伙伴,并继续作为 TAPAS2。针对空客在 TAPAS2 下开发的应用,GKN Fokker(荷兰 Hoogeveen)最近开发了一种机身演示器,使用所谓的“对接正交网格技术”,能够经济高效地生产热塑性复合材料机身设计。
随着湾流航空航天公司(美国佐治亚州萨凡纳)与 GKN Fokker 合作推进其 TAPAS2 机身技术,为可能的应用指明了道路材料和工艺到一个完整的机身。新开发的机身面板(今年早些时候在 JEC World 上展出)背后的故事是设计和制造方法的进步之一,而且是更彻底集成的设计-制造工程方法。
“传统上,”GKN Fokker 总工程师 Andries Buitenhuis 解释说,“无论是使用织物还是单向胶带,设计师大多坚持使用 0 度、90 度和 45 度方向的传统层。他们将独立于其他学科,在他们的叠层台上工作。”新方法是一个集成的数字化设计-制造软件平台(通过 TAPAS 开发),其中来自不同学科的工程师都在查看相同的数字模型,并能够将更复杂的零件设计概念化。 “这为前所未有的优化可能性开辟了一个全新的世界,”Buitenhuis 继续说道。 “在复杂的形状上,纤维方向可能无处不在。我们可以构建非常规的层压板,并重新审视设计允许、制造间隙和重叠、半径……。您可以局部优化结构的强度。”这些扩展的设计选项更充分地利用了自动纤维铺放 (AFP) 机器的纤维转向能力,以及下文讨论的其他制造能力的进步。
事实证明,这种集成数字系统提供的设计自由对于商务喷气机面板的设计和制造必不可少。在 TAPAS2 机身设计中,碳纤维/聚醚酮酮 (PEKK) 面板(由索尔维的 APC PEKK-FC 制成)具有焊接、无紧固件的框架与皮肤连接,这是该设计成本效益的重要因素。 GKN Fokker 热塑性复合材料技术负责人 Arnt Offringa 解释说:“我们预计铝制机身外壳可以实现成本平价,这是因为铝制外壳是铆接的。”与传统的复合材料解决方案相比,取消机械紧固件预计将使飞机主要结构的成本降低 20%,重量减轻 10%。当然,大部分成本和重量的节省来自消除紧固件本身以及安装它们的劳动力成本。同样重要的是消除复合材料部件中的孔以容纳紧固件——这些孔需要额外加固,因此增加了重量。
GKN Fokker 在 2017 年 12 月与空中客车公司合作的加压机身达到了技术准备水平 (TRL) 3(概念验证),展示了与铝机身面板的成本平价,在 TAPAS2 下。在此过程中,GKN Fokker 团队扩展了对这种热塑性塑料的愿景从商用客机到公务机应用的机身技术。
湾流的兴趣
GKN Fokker 在湾流热塑性复合材料部件方面的成功工作历史使与公务机制造商的合作成为合乎逻辑的下一步。 “众所周知,湾流多年来一直在使用热塑性复合材料部件,”湾流先进结构和材料计划 (ASMI) 经理马克查普曼说。他补充说,机身面板项目“是我们一直在做的事情的自然发展,从更简单的部件开始,转向主要结构部件。” GKN Fokker 与湾流合作开发了许多热塑性复合材料二次部件,包括尾升降舵和方向舵以及 G650 上的地板面板。
2015 年,Offringa 和 Buitenhuis 向湾流介绍了 TAPAS2 项目的开发,查普曼和他的团队认识到从 TAPAS2 结果中获益的潜力。 “我们看到了潜在的减重优势、更好的抗冲击性和韧性以及增强的性能,”查普曼回忆道。无紧固件设计也很吸引人。查普曼说,“焊接技术将使我们能够更有效地组装机身”,而不是机械固定的组装。
与 GKN Fokker 的合作支持湾流对更复杂机身形状的研究和开发,这些机身形状在使用金属结构生产时可能在经济上不可行。 “到目前为止,您只能拉伸成型金属,”查普曼指出。 “复杂形状所需的拼接和支撑结构不是很有效。” Offringa 同意:“这种复杂的几何形状很难用传统技术制造。”
加盟设计制造
为了实现无紧固件、可生产的设计,GKN Fokker 的方法侧重于承受机身接头所承受的两个关键力:机舱压力和工具掉落等冲击。机舱压力将径向力施加在机身上,从而在框架与蒙皮的接合处产生高负载。在传统设计中,机身框架包括纵向纵梁穿过的“鼠标孔”。在机舱压力的作用下,这些鼠孔作为不连续点,会受到高剥离力的影响——这是无紧固件设计的主要问题,因为与金属相比,复合材料的面外强度较低。撞击还会在框架与皮肤的接合处产生高载荷,因为框架在撞击下不会弯曲。
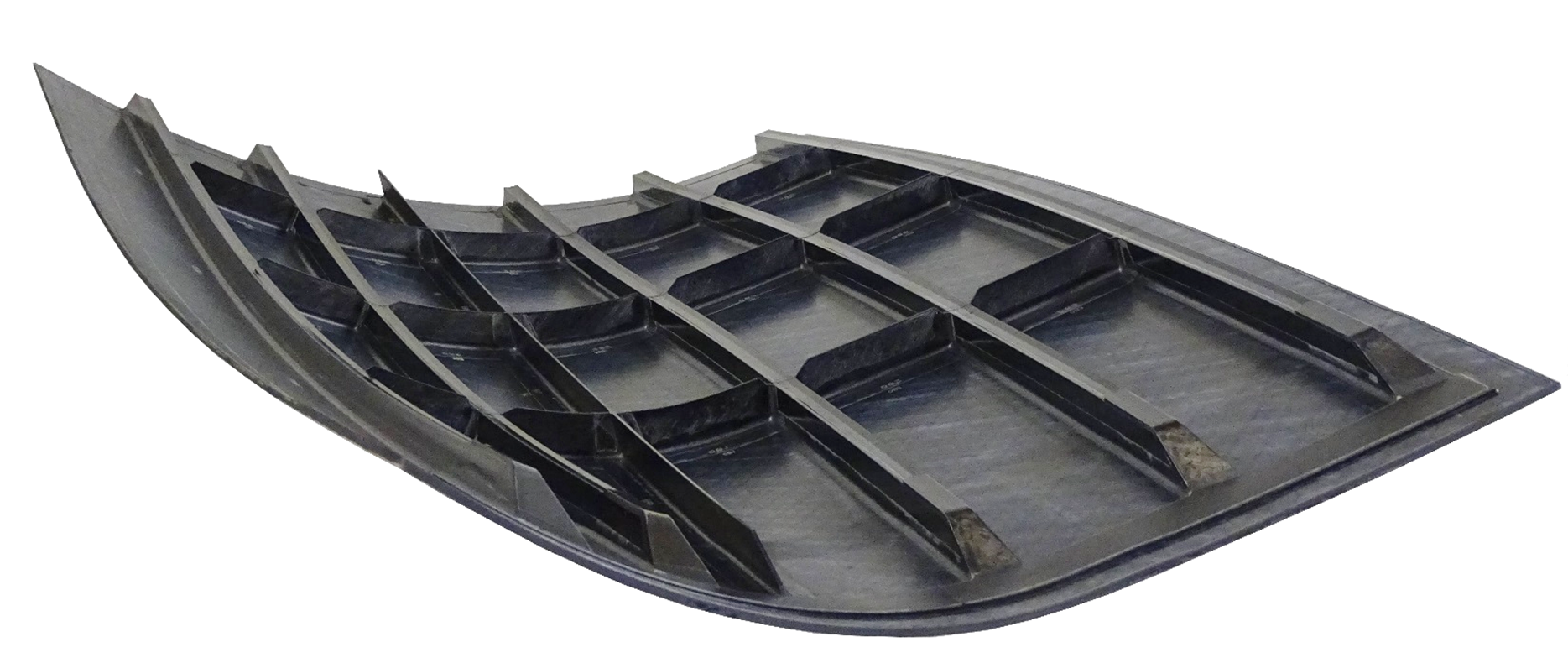
双曲率。 热塑性复合材料机身面板可容纳湾流公务机后机身的复杂几何形状,采用纤维导向的 AFP 蒙皮叠层和正交网格的共同固结。请注意圆周叶片纵梁,这些纵梁后来焊接到框架上。来源 |吉凯恩福克
GKN Fokker/Gulfstream 团队知道,用金属或传统的复合设计制造方法来应对复杂曲率带来的挑战是不可行的。 Buitenhuis 尤其指出,“如果没有光纤转向,就不可能有复杂的机身设计。” AFP 机器的这种功能使设计师能够根据外壳的复杂形状在局部优化纤维取向,并与标准的 0/45/90 纤维取向选项不同。 “用于形状和重量优化的纤维转向是该项目最重要的进步之一,”查普曼认为。
GKN Fokker 在该公司为快速热塑胶带铺设而开发的超声波 AFP 机器上制作机身面板的蒙皮。胶带是单向的,与织物胶带相比,这也提高了层压性能。
在 TAPAS 和 TAPAS2 下开发的新概念成功处理由机舱压力和冲击力产生的高负载以及其他性能需求,现在用于湾流面板,被描述为“对接接头正交加强带有焊接框架的皮肤。”拆开这个描述突出了三个关键的设计特征和实现它们所需的制造发展:(1) 正交网格,(2) 对接接头和 (3) 焊接技术。
正交网格
面板的强度要求部分通过完全互连的正交网格加强来满足。这种正交网格消除了与鼠标孔相关的峰值载荷,消除了剥离力被放大的点的设计。正交网格由连续的纵向纵梁和框架组成,该框架包括两个不同的部件:不连续但连接的圆周叶片纵梁和焊接在其顶部的框架。
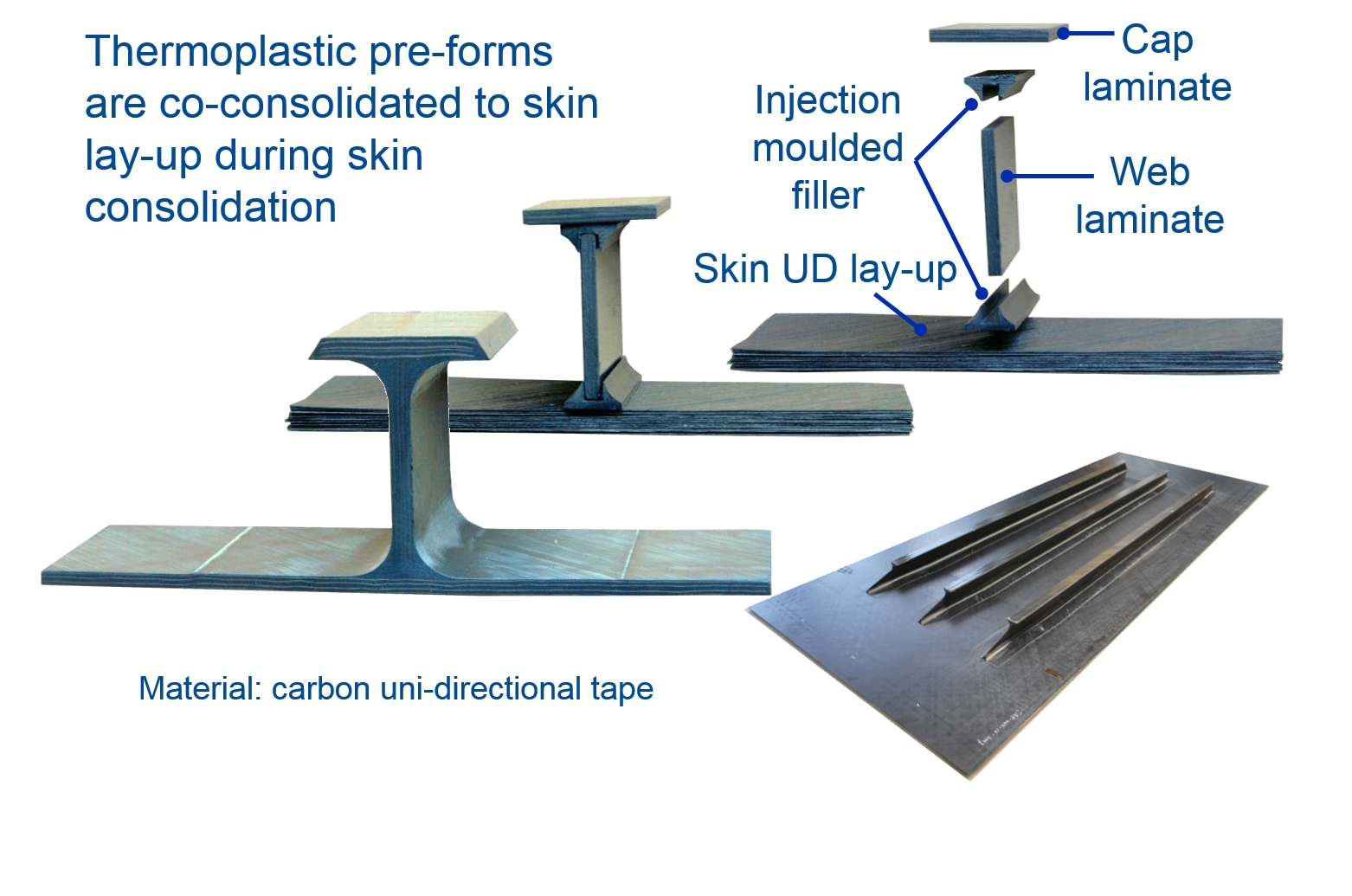
具有成本效益的对接接头。 GKN Fokker 对一种对接接头进行了创新并获得专利,该对接接头使用具有成本效益的短纤维注塑元件和连续纤维扁平层压板用于纵梁腹板和帽(此处为 T 纵梁;湾流面板包含L 纵梁具有相同的技术)。来源 |吉凯恩福克
因此,这代表了新一代机身加强筋设计,该设计在多年的正交网格发展过程中得到了发展。最初,GKN Fokker 使用 T 型纵梁,其中纵向和周向构件的帽是连续的,并在拐角处重叠。然而,与框架连接需要移除圆周帽。因此,T型纵梁变成了L型纵梁,框架变成了带框架的圆周叶片纵梁,然后焊接到它们上面。
需要进行另一项修改,因为纵向和周向使用的弯曲纵梁使工具释放更具挑战性。因此,L 纵梁设计为帽与腹板的角度超过 90 度,因此工具件始终可以侧向滑出纵梁网格。
对接
GKN Fokker 不仅开发了正交网格设计,而且还开发了一种新的网格制造方法以及网格到皮肤的连接机制。 “网格的制造成本可能高得惊人,”Offringa 指出,“但我们的网格是由扁平层压板和简单的注塑‘填料’构成的。”
更具体地说,GKN Fokker 将其获得专利的对接技术应用于湾流面板(也应用于之前的 TAPAS 面板)。 T 型或 L 型纵梁组件的腹板和帽,以及叶片纵梁组件,均由预成型件制成,预成型件由平面碳纤维/PEKK 层压板水刀切割而成。连接元件(皮肤到网和网到帽)是注射成型的,pi 形填充物,由短纤维碳/PEKK 材料制成。树脂和碳纤维类型均与网格构件中的类型相匹配。
蒙皮和正交网格在 Invar 内模线 (IML) 工具中共同固结。该工具具有凹槽,可将正交网格组件和工具块装入其中。然后将 AFP 形成的表皮放置在 IML 上,然后将整个组件装袋并高压灭菌。
焊接
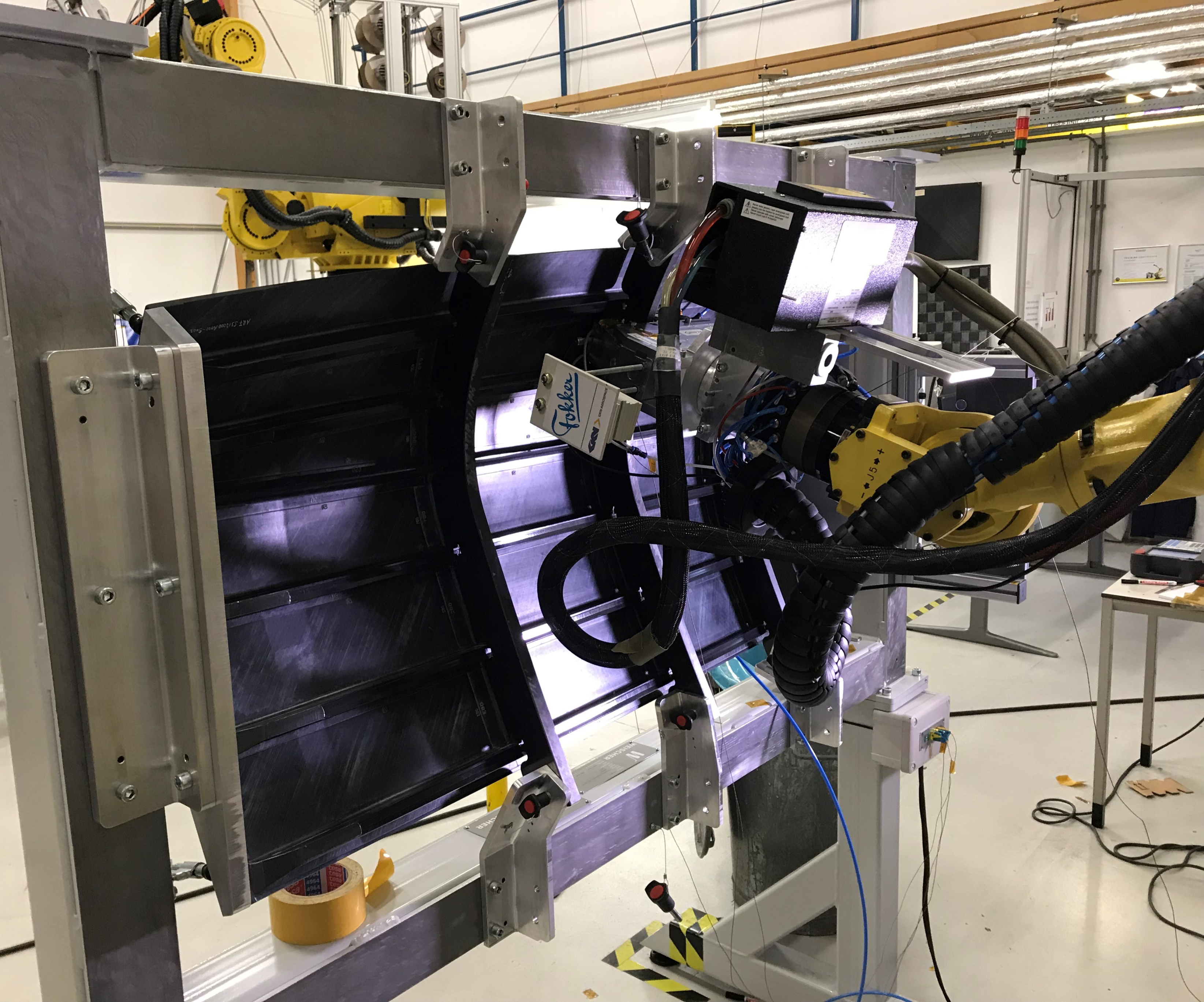
自动焊接。 为提高热塑性复合材料机身面板的经济可行性,GKN Fokker 开发并采用了机器人焊接技术。来源 |吉凯恩福克
正交网格和对接设计的结合使正交网格和框架通过焊接无紧固件连接。 TAPAS 团队成员在 TAPAS2 阶段开发了多种焊接技术,包括感应、传导和超声波焊接技术。湾流面板采用传导焊接将框架腹板连接到圆周叶片纵梁。这项任务是在焊头安装在机器人上的情况下完成的——这是另一项有助于提高可制造性的成本效益。
一步一步
GKN Fokker 于 2017 年开始与湾流合作,为机身面板创造设计概念。随后在 2018 年和 2019 年设计和制造了几个曲面面板,具有里程碑意义的第一个面板演示器在今年的 JEC World 上展出。
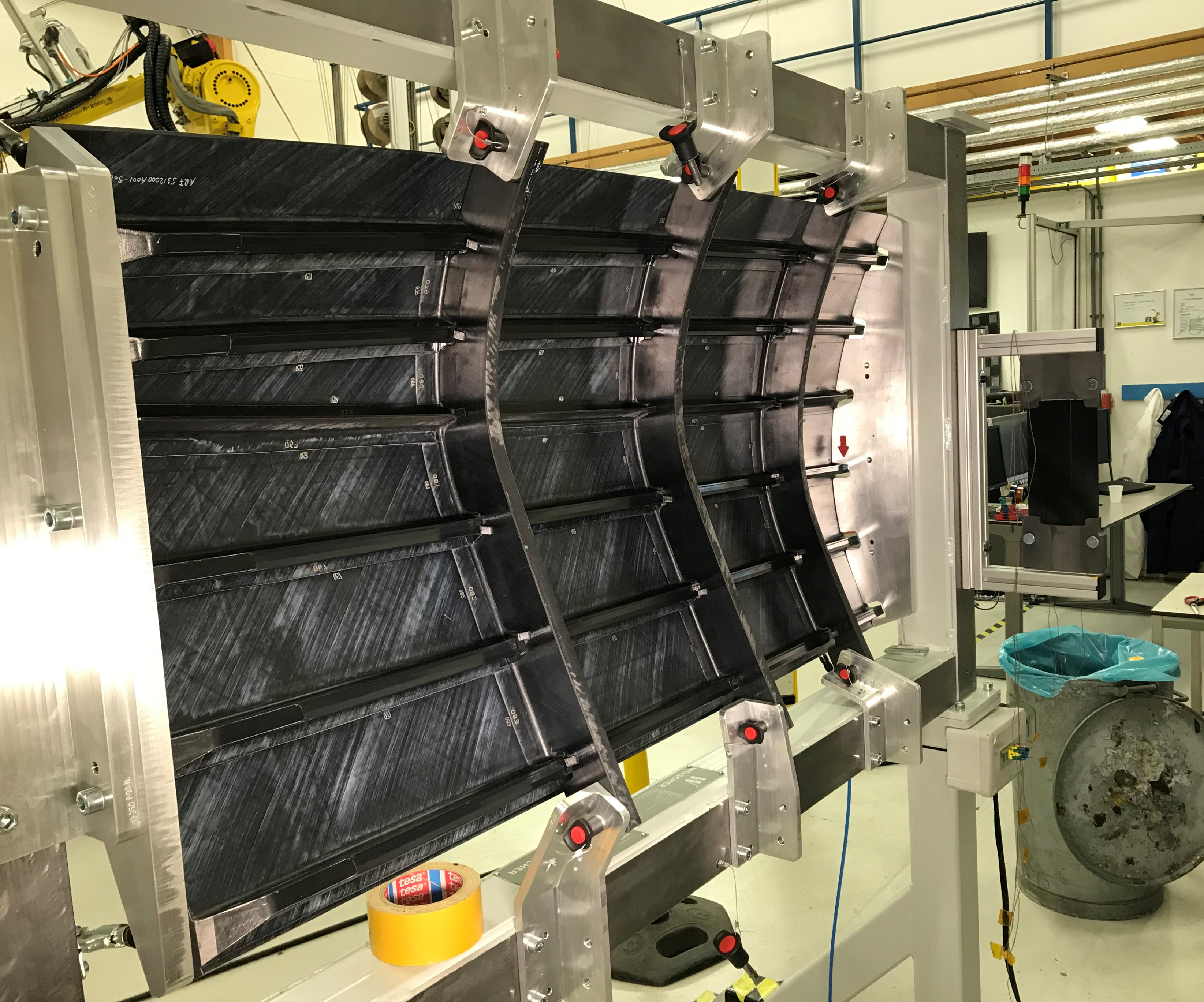
完成的组件。 随着框架元件焊接到圆周叶片纵梁上,湾流机身面板已准备好在公司致力于生产热塑性复合材料机身时进行测试、评估和持续开发。来源 |吉凯恩福克
GKN Fokker 正在继续制造面板,并预计在今年晚些时候实现 TRL4(组件验证)。 “我们目前正在讨论走向完全成熟的道路,”Offringa 报告说。查普曼指出面板设计不针对特定平台,面板测试将有助于加深湾流对材料特性和性能的理解。关于热塑性复合材料主要结构的更广泛的商业案例,包括喷气式飞机的性能、制造成本、使用成本和耐用性,查普曼评论说:“随着我们在研发道路上走得更远,我们将更好地了解这些。目前,我们的重点是使这些复杂的形状具有成本效益。”
树脂