大型零件加工测试卧式机床能力
多功能平台以最高效率处理处理
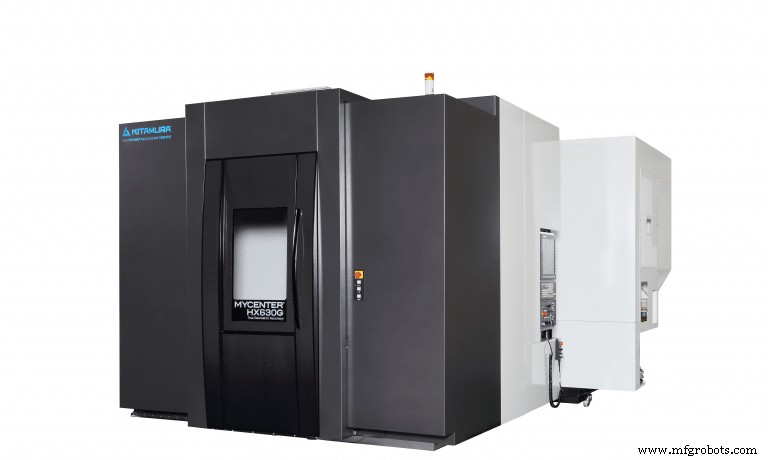
卧式加工中心 (HMC) 是多功能的四轴机床平台,并且越来越多的五轴机床平台通过最大限度地减少零件处理来最大限度地处理多面大型零件。它们用于航空航天、汽车、发电和通用工程等多种行业。
凭借其近乎普遍的生产能力,HMC 为制造商提供了多种选择,使其不易受到石油和天然气等任何一个行业的周期性潮起潮落的影响。 HMC 很容易实现自动化。它们通常配备用于安装墓碑零件的双托盘、单个工件,或者它们可以通过包含六个或更多托盘的托盘池实现自动化。对于无人值守的熄灯生产,可以使用线性柔性制造系统(由储料器进料并由导轨引导、高架龙门机器人或底座安装的六轴机器人照料)。单个大型工件的范围从发动机缸体到油田钻头、泵壳和歧管,以及安装在墓碑上的组件系列。
配套机器,大型零件
伊利诺伊州威灵市 Kitamura USA Inc. 助理销售经理 Sal Swierczek 表示,在加工大型零件时,机床的刚性及其基本结构对加工效率、准确性和一致性至关重要。
“Kitamura 的 HXiG 系列 HMC 的工作台尺寸范围从 250 到 1250 mm,配备 8,000 rpm 或 12,000 rpm 四步齿轮驱动主轴,可提供 430 到 900 ft-lb 的扭矩,用于切割特殊材料,”他说。 “根据 Kitamura 的专利工艺,这些 HMC 采用油冷双滚珠丝杠,采用内部感应淬火和研磨,表面光洁度低于 4 µm,可实现出色的配合、精度和长期可靠性。手刮技术的精湛工艺可实现 ±0.002 毫米全行程和 ±0.001 毫米可重复性的一致精度。”
Swierczek 表示,首先要考虑的当然是工件是否适合机器的工作范围,无论是在工作台上装载一个零件还是装载多个零件以提高产量。 “关键的机器选择标准包括机器容量(包括整体机器尺寸)、主轴功率、刚性、刀具数量、刀库尺寸选择以及刀具锥度和尺寸,”他说。 “Kitamura 卧式机器有一个标准的两站 APC [自动托盘更换器],可以选择增加在现场使用托盘池的托盘数量。”
Swierczek 补充说:“自动化能力解决了当今车间面临的挑战之一,那就是难以找到熟练的操作员和能够处理熄灯加工的劳动力。”
卧式加工中心为零件加工提供了急需的灵活性。 “与三轴加工中心相比,全四轴加工中心最大限度地减少了零件处理,将零件翻转的次数从六次减少到两次,”Swierczek 说。 “通过加工中心上的第四轴,操作员可以从正面和两侧接近零件,然后重新定位以进行最终加工。”
此外,随着商店业务的增长,Kitamura HMC 可以扩展到全五轴加工。 Kitamura 提供自己的 Arumatik-Mi,图标驱动的 CNC 控制,与 FANUC 编程兼容。 Arumatik-Mi 控制器通过监控加工过程中的主轴负载来自动检测刀具磨损并控制切削进给率。通过适应切削条件的变化,最大限度地延长刀具寿命并显着缩短循环时间。其他好处包括减少非切割时间以及防止机器崩溃和/或人为错误。
大型零件加工机
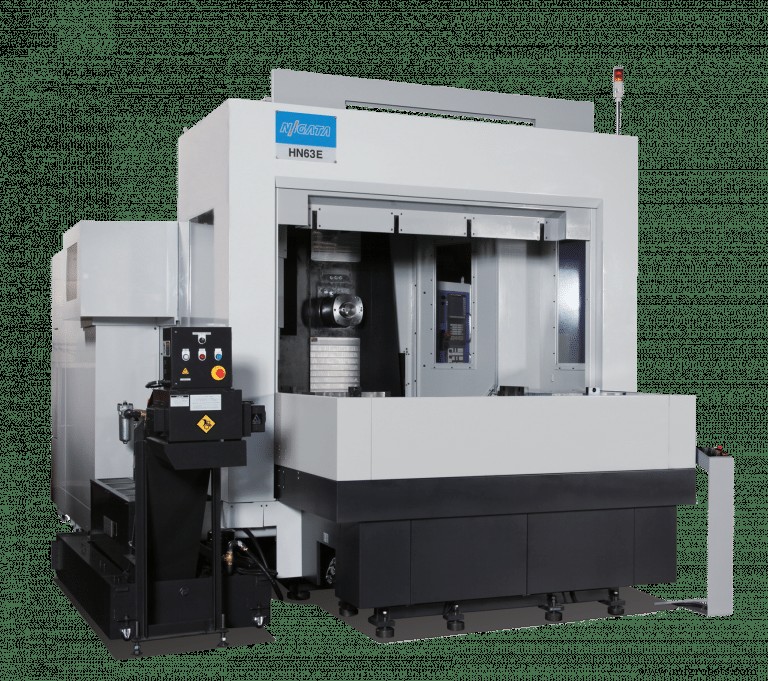
对于大型零件加工,马萨诸塞州萨德伯里的 Methods Machine Tools Inc. 提供两条卧式加工中心生产线:Niigata 和 KIWA Japan。 “KIWA Japan 生产线以高速、高可靠性加工而闻名,通常适用于车间以及一级和二级汽车车间,”运营副总裁 Dale Hedberg 说。 “Niigata 产品线专为需要低频加工和重金属去除率的重型切削应用而设计。”
Niigata 产品线包括五轴 HN50E-5X 和 HN63E-5X、四轴 HN50 至 HN1600、HN800 至 HN1600-BAR 以及 HN800 和 HN1000-FC 端面和轮廓机床。机器平台的工作台尺寸为 500 毫米至 1,600 毫米。主轴锥度尺寸为 CAT-50 BIG Plus、HSK100A,主轴可选 6,000、8,000、12,000 和 15,000 rpm。
Hedberg 说:“该行业目前正朝着卧式加工中心的五轴平台发展趋势,新泻提供 500 和 630 毫米两种尺寸。” “在航空航天和能源行业,Niigata 专注于低频加工应用,这得益于机器的自然阻尼特性。在钛合金和铬镍铁合金的高扭矩加工方面,低频加工正成为一个流行的短语,以延长刀具寿命和延长主轴的使用寿命,”他解释道。
机器的铸件和金属对金属的接触表面自然具有抑制切削力振动的能力,这些接触表面是手工刮削的,用于配合表面光洁度。据 Hedberg 介绍,能源和发电领域的典型应用包括法兰、压裂头和叶盘。
在使用 HMC 进行大型零件加工时,每个轴的行程直径精度和刚度对于实现精度和可重复性尤为重要。 Hedberg 说,“五轴加工的美妙之处在于,您不需要复杂的夹具或定制的工件夹具,除非您要加工可能需要窗式夹具或某种特殊夹紧方法的独特零件。”主页>
以应用为中心的 HMC
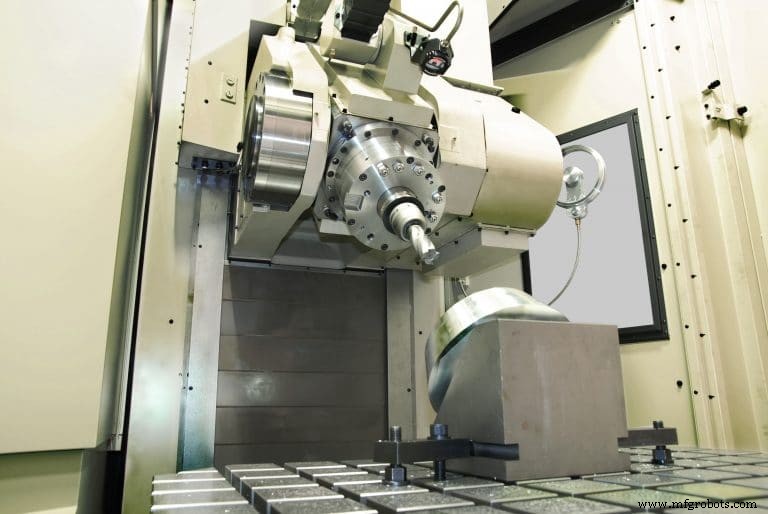
据总裁罗伯·哈德森 (Robb Hudson) 称,位于新泽西州富兰克林湖的三井精机美国公司着眼于客户对开发新型卧式加工中心的需求,特别是在当前最受大型零件加工应用追捧的型号上。 “今天,对大型零件的需求肯定来自航空航天,这是目前喷气发动机系列零件和结构部件的一大推动力。其他目标市场包括模具、外太空和国防以及工业燃气轮机行业,”他说。
“我们的卧式加工中心具有 1 m 及更大的托盘和配套工作台配置,可容纳 1,000 至 10,000 lb [453-4,535 kg] 的重量,被认为是我们的大型零件机器。需要注意的是,我们在这个尺寸范围内的机器都源于推动开发的客户。我们没有制造机器然后寻找市场。它们都源于客户对特定应用的需求。”
三井精机机器均具有相同的主要技术特征,可考虑用于大型零件制造。 Hudson 说:“我认为有两类——大型零件也需要大量去除材料,另一种是笨拙且需要较轻切割的零件。三井精机从事需要对坚韧材料进行重型切削的大型零件领域。因此,我们的机器具有大量的质量、刚度、大型箱形导轨、大直径滚珠丝杠以提供足够的推力、强大的轴向扭矩和特殊的伺服电机,以在工作范围内移动零件并适应必要的切削力。”
Hudson 表示,所有这些功能以及控制和构造精度都是为应用提供适当性能所必需的。他补充说,夹具是大型零件制造中的重要元素,通常与它所夹持的工件一样大而重。
自动化更容易
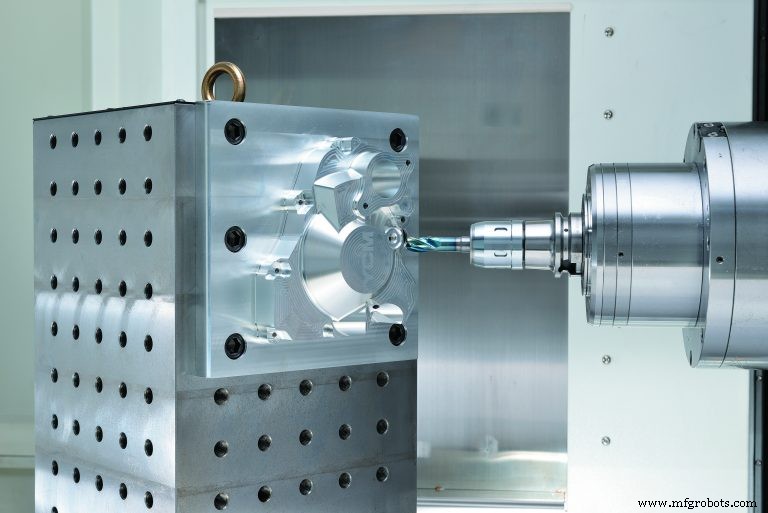
加利福尼亚州卡森市 YCM Technology (USA) Inc. 区域销售经理 Mel Gay 表示,虽然使用任何类型的机器设置自动化都很复杂,但 HMC 似乎更容易实现自动化,因为它们的产量很大。
“收回投资资金的速度始终是 HMC 采购的首要关注点,”他说。 “流行的尺寸为 500/630 毫米,小型加工车间至少可容纳 60-120 件工具,大型工厂可容纳 240 件或更多工具。更大的工具容量允许以最少的设置时间完成更复杂的工作,尤其是在多托盘单元配置的情况下。”
在 IMTS 上,YCM 展出了 NH500A 6 APC,目标是汽车等大批量生产的行业。 NH500A 有一个 30 hp、20,000 rpm 的主轴和一个 500 x 500 mm 的托盘。
“生产力始于带有肋结构的高刚性 T 型基础,”盖伊说。 “YCM 将这一基础与一体式铸造主轴箱和双壁立柱设计相结合。直驱主轴采用精密陶瓷滚珠轴承,可实现更高的切削动力和更高的主轴转速。”
据 Gay 介绍,所有轴上的高精度滚柱式导轨可实现 2,362 ipm (60 m/min) 的快速进给率和高达 1,575 ipm (40 m/min) 的切削进给率。精密托盘分度系统可容纳六托盘 APC,以实现单个组件或零件系列的高吞吐量。
“所有这些功能都允许利用最新的切削工具技术,改进零件加工并降低总拥有成本,”他说。
美国制造的大型 HMC
位于伊利诺伊州霍夫曼庄园的 DMG Mori 在其位于加利福尼亚州戴维斯的工厂生产四种型号的卧式加工中心。 NHX 4000 和 NHX 5000 是第三代 40 锥度机器,配备 400 和 500 毫米托盘; NHX 5500 和 NHX 6300 是第二代 50 锥度机器,配备 500 和 630 毫米托盘。
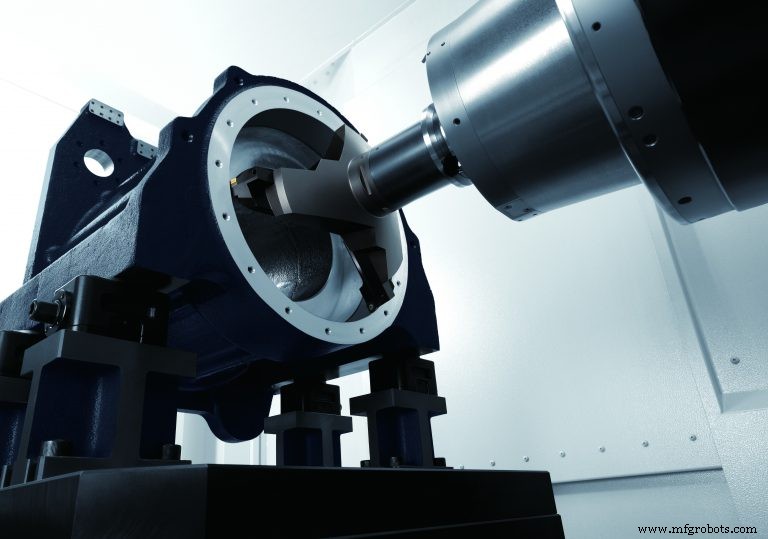
“我们的水平仪专为满足能源、航空航天、工业设备和合同制造行业客户的重切削和高精度要求而设计,”开发和产品管理执行副总裁 John McDonald 说。
典型的工件包括用于能源行业的大型阀门和涡轮机零件;工业设备中的发动机、差速器和变速器外壳;和航空航天中的结构部件。材料范围从钛或不锈钢到铸铁或铝——一切都取决于应用。
“我们的客户通过使用托盘池系统进行高混合生产或使用我们卧式加工中心标配的集成式通过工作台夹具液压系统的专用机器人装载,通过自动化实现高生产率,”麦克唐纳说。 “大型零件加工和重切削取决于优化的机器结构。我们所有的卧式机床都具有完全有限元优化的结构,包括重型三点支撑铸铁床身结构、powerMASTER 主轴(50 锥度机床)和滚柱直线导轨。线性标尺是我们所有机器的标准配置,使我们的客户能够在机器的长使用寿命内保持最高精度。”
标准 50 锥度 powerMASTER 主轴转速为 12,000 rpm,可选配 16,000 rpm 高速版本。 NHX 6300 还可选配 8,000 rpm 高扭矩主轴,用于对难加工金属进行重载切削,例如特殊材料和重铸铁。
DMG Mori 的 CELOS 控制界面提供了一系列用于工艺优化的应用程序。为了与工业 4.0 倡议保持一致,CELOS 控制界面简化并加速了零件加工的所有阶段,从构思到成品,从单个零件的制造一直到批量生产。
DMG Mori 表示,CELOS 应用程序可实现作业、流程和机器数据的一致管理、文档编制和可视化,以及连接车间和更高级别的公司结构,从而为一致的数字化和无纸化生产奠定基础。此功能甚至可以从装有 CELOS PC 版的办公计算机上实现。
“我们还提供技术循环,使我们的客户能够轻松实现复杂的加工过程,”McDonald 说。 “例如,机器振动控制 (MVC) 允许操作员在重型加工过程中找到稳定的切削进给和速度。另一方面,机器保护控制 (MPC) 提供主轴振动监控、刀具负载监控和碰撞检测,以防止或减少损坏。通过收集和分析这些数据,CELOS 控制界面正在帮助
车间最大限度地提高生产力,实现更高的精度,并使主轴每天运行更多小时,”McDonald 说。
施工能力
位于北卡罗来纳州夏洛特的 Okuma America Corp. 加工中心产品专家 Errol Burrell 表示,Okuma 的卧式加工中心(如 MA-600HII)是汽车、模具、能源和航空航天行业的热门选择。
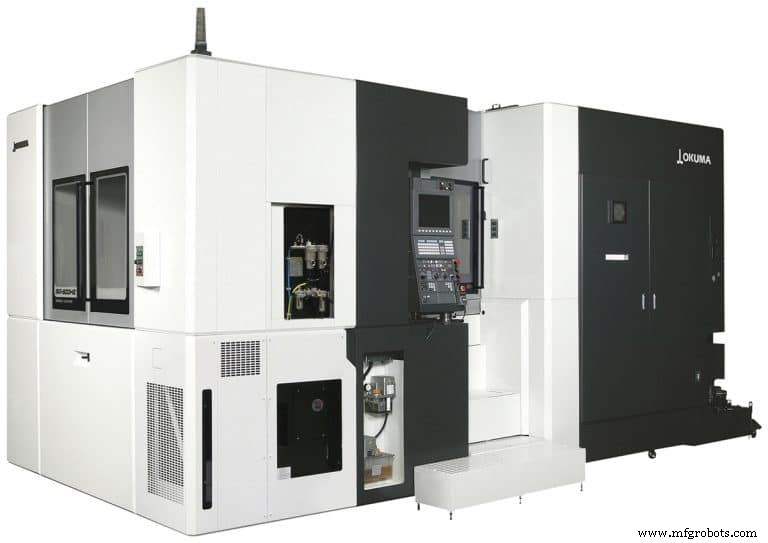
“由于它们始终如一的热稳定性,它们为加工大型零件提供了准确性和稳定性,”他说。 “通过 Okuma 的 TAS(热轴稳定器)软件对机器进行热分布测试,并将有关可能的热变形的数据实时反馈到控制系统中,以进行任何必要的补偿。”
MA-600HII 是一款 50 锥度机床,配备 6,000 rpm 主轴和标准 40 刀库,可升级到 60 刀甚至高达 285 或 400 刀,因此非常适合车间或生产制造. MB-8000H 与 800 毫米工作台几乎是同一平台,而下一个尺寸更大的是 MB-10000H,采用盒中盒设计而不是立柱。
Burrell 说,Okuma 机器在每个配合表面上都经过手工刮削,以在更长的时间内提高精度和生产率,从而降低成本并实现最大的盈利能力。
泵壳等典型的油田部件受益于 Okuma 独特的 Turn-Cut 能力。 “对于泵壳,我们的 Turn-Cut 功能允许在 Okuma 卧式加工中心上打开法兰,”Burrell 说。 Turn-Cut 是 Okuma HMC 上提供的一种编程选项,允许机器创建包括圆形和/或角度特征的孔和直径。这使用户能够在执行标准 CNC 加工功能的同一平台上打开大型不平衡零件的功能。 Turn-Cut 无需购买专用机器、工具、夹具或附加组件。
Turn-Cut 不会影响机器的性能或使用寿命。据大隈称,当需要重铣削时,配备 Turn-Cut 的 Okuma HMC 仍然像以往一样强大。最重要的是,Turn-Cut 允许加工工作,而无需使用辅助机器进行车削应用。阀门、管道或歧管型零件等零件是 Turn-Cut 的理想选择。
在 IMTS,Okuma 展示了其 Tower Pallet 自动垂直托盘系统。它备有 12 个 20 x 20 英寸(500 x 500 毫米)的托盘,每个托盘在两个层面上的最大负载能力为 1,100 磅(500 千克)。该公司表示,集成的 APC 系统通过伺服电机驱动的旋转系统实现快速加载/卸载时间,以实现熄灯操作。
全第四轴,自动化
肯塔基州佛罗伦萨的 Mazak 公司根据产品介绍,除了大型桥式立式加工中心、带车削的五轴立式加工中心 (INTEGREX) 和 VARIAXIS 五轴耳轴式机床外,还提供全系列 HMC专家贾里德·莱克。
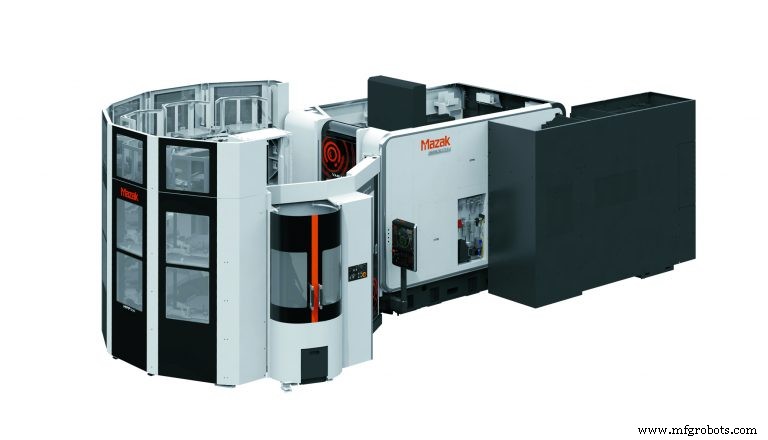
“使用 50 锥度主轴的大型零件加工是在配备 800 至 1,600 毫米工作台/托盘的机床上完成的,包括配备 1,250 至 1,600 毫米工作台的 Quill 系列 HMC,以及配备 630 毫米工作台的 HCN-6800用于汽车和能源部件的大型发动机组。”
50 锥度生产线包括该系列中的三个附加型号(HCN-8800、HCN-10800 和 HCN-12800),配备 10,000 rpm 标准和可选的 8,000 rpm 和 6,000 rpm 50 hp 主轴,用于钛、不锈钢的更高扭矩加工和其他外来金属。 Leick 说,对于航空航天和半导体行业的大型铝结构零件的加工,可以使用 16,000 rpm 的主轴。
他说,马扎克提供全四轴 HMC,约占公司销售的所有 HMC 的 60%。具有标准 0.0001o 定位的四轴 HMC 允许旋转用于钻孔复合角度、分度 90o 和向后旋转的双侧或四侧夹具。全四轴操作可实现轮廓加工,可用于减少循环时间,使加工更容易,尤其是复杂零件。
可用的自动化系统包括 Mazak 的 PALLETECH 系统,该系统可以在 FMS 配置中容纳大量机器和轨道引导机器人,以及 Mazak 用于 400 和 500 mm 机器的新型多托盘池 (MPP) 单机自动化系统。 “我们在轨道上使用六轴 FANUC 机器人实现了 HMC 的自动化,这些机器人将零件定位在不同的工位,以进行激光打标、清洗和去毛刺,”Leick 说。
Mazak HCN-5000 HMC 现在可与公司的 MPP 系统一起使用,这是一种占地面积小的基本自动化解决方案。据 Leick 介绍,那些缺乏容纳传统线性水平托盘堆垛机所需占地面积的商店现在可以实现自动化以实现连续生产。
MPP 提供了更大的 Mazak PALETECH 系统的便利性,同时占用的空间减少了 30%。他说,每个轴上的伺服电机,以及使每个托盘与储料器中心保持相同距离的两级托盘布置,确保了快速稳定的装卸。
旨在随着生产需求的增长而扩展,制造商可以重新配置系统的标准 10 托盘储料器以容纳 16 个托盘以增加产量。考虑到 HCN-5000 的大型、重型零件操作,Mazak 使这款最新的 MPP 成为其最大的零件尺寸容量版本。该系统容纳 500 平方毫米的托盘,可容纳直径达 800 毫米、高度达 1,000 毫米的工件。
自动化控制系统