复合插件作为 A 柱的结构加强件
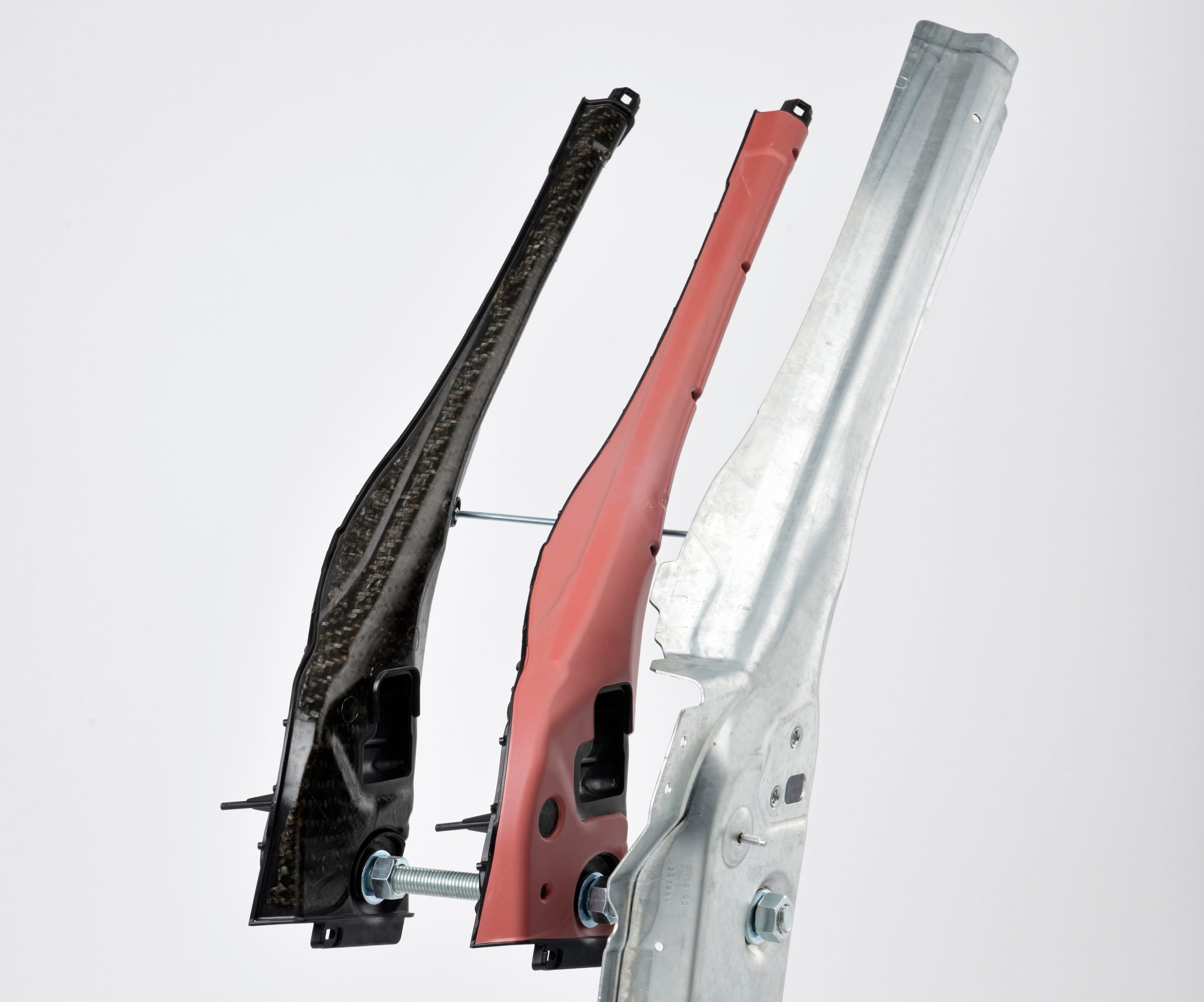
3D 混合动力 A 柱从车辆门槛板向上延伸,容纳门铰链并将挡风玻璃固定在侧面。来源 |朗盛股份公司
保时捷(德国斯图加特)911 Cabriolet 今年推出的是第一款采用轻型混合金属复合材料 A 柱制造的汽车,专为敞篷车和敞篷跑车设计。
混合金属复合材料支柱包含一个由高强度钢制成的插件,内部由基于聚酰胺 6 的朗盛(美国宾夕法尼亚州匹兹堡)Tepex dynalite 102-RG600(6)/47% 连续成型坯料支撑纤维增强热塑性复合材料,由聚酰胺 66 基短玻璃纤维填充 Durethan AKV30H2.0 制成的肋状结构。该结构通过摩擦与 L&L Products(美国密歇根州罗密欧)开发的 L-5235 结构泡沫粘合在一起。朗盛表示,其 Tepex 系列热塑性复合材料特别适用于具有严格安全要求的乘用车结构部件。
混合嵌件的强度和刚度确保 A 柱与以前采用高强度钢管的设计一样能够承受侧翻。但是,它轻了5公斤。减重是在车辆的“温室”区域实现的,降低了汽车的重心,从而提高了车辆的动力性。
“混合 A 柱的出色机械性能表明,基于钢板、Tepex 坯料、Durethan 的聚酰胺 6 或聚酰胺 66 变体作为后注塑材料和结构泡沫(如 L-5235)的混合嵌件也提供了可观的用于结构轻量化车身设计的潜力。这尤其适用于电动汽车,因为它们的重型电池具有很高的冲击质量,”朗盛高性能材料 (HPM) 业务部门 Tepex 汽车部门负责人 Henrik Plaggenborg 解释说。 “减轻重量也扩大了使用这项技术的电动汽车的范围。”
混合复合材料元件的其他潜在应用包括加强横梁和侧梁、B 柱和 C 柱、承重电池部件或对安全至关重要的车门部件。
混合复合元件由 L&L Products 在其位于法国斯特拉斯堡的工厂开发和制造。增强元件制造的第一步涉及使用混合成型技术在一次操作中成型和包覆成型 Tepex 坯料。然后将所得复合材料部件涂上一种环氧基泡沫粘合系统,该系统可响应热量而膨胀。涂层部件安装在车身上,并与其一起进行阴极浸涂 (KTL) 工艺。 KTL 工艺的高温导致结构泡沫膨胀并与高强度钢板粘合,高强度钢板也固定在 A 柱外壳上,以生产增强型混合插件。最后一步是在保时捷开发的完全自动化的制造过程中进行的,并受到持续的质量控制。
插入件和 A 柱的开发过程得到了朗盛 HiAnt 客户服务部门的支持。 “服务包括模拟 Tepex 坯料的成型(悬垂)、模拟回注填充和计算翘曲。我们还确定了材料特性来模拟 A 柱的机械行为,并将这些数据提供给保时捷,”HPM 应用程序开发专家让-玛丽·奥利维 (Jean-Marie Olivé) 说。
树脂
- 了解复合材料
- 朗盛在结构支架应用中演示 Tepex 复合材料
- Fraunhofer 委托自动化 Engel 生产单元进行热塑性复合材料研发
- 热塑性胶带继续显示出复合航空结构的潜力
- UAMMI, Impossible Objects 为美国空军制造复合材料部件
- Impossible Objects 与巴斯夫合作进行复合 3D 打印
- INEOS Styrolution 为 StyLight 热塑性复合材料建立生产基地
- AeroLas 探索热塑性混合纱线的新纺纱技术
- Techsil 推出用于复合基材的透明环氧粘合剂
- 复合材料 + 金属:中空混合技术
- SABIC 推出用于建筑和施工的复合板
- Rhodes Interform 为 AMRC 制造复合印刷机