Fraunhofer IPT 开发用于储氢、发动机叶片等的热塑性复合材料
Fraunhofer IPT 开发包括(从左上角顺时针方向)热塑性复合材料航空发动机风扇叶片、使用激光成型和 AFP 的混合复合金属结构、复合材料的结构健康监测 (SHM) 和热塑性复合材料带加工系统,例如 PrePro 2D 和 PrePro3D 系统由 Conbility 商业化。图片来源:Fraunhofer IPT
2020 年 12 月,我发表了一篇关于弗劳恩霍夫生产技术研究所(IPT,德国亚琛)如何为热塑性碳纤维增强聚合物 (CFRP) 航空发动机风扇叶片开发全自动胶带铺设和成型的文章。事实证明,热塑性复合带的原位固结 (ISC) 是弗劳恩霍夫 IPT 非常了解的一个话题,在最初与 ISC 先驱 Accudyne Systems Inc.(美国特拉华州纽瓦克)和自动化公司一起推动了这项技术的发展Dynamics,现为 Trelleborg Sealing Solutions Albany(TSS Albany,Niksayuna,NY,美国)。 [有关这些 ISC 先驱的更多信息,请参阅“将热塑性航空结构固化到位,第 1 部分和第 2 部分”。]“自 1988 年以来,IPT 一直活跃于激光辅助绕带 (LATW),它仍然是我们的主要主题之一,”弗劳恩霍夫 IPT 纤维增强塑料和激光系统技术总工程师兼部门负责人 Henning Janssen 博士解释说。他指出,LATW 技术发生了很大变化,尤其是在过去的 10-15 年中。该博客详细介绍了 Fraunhofer IPT 在更广泛的范围内开发 LATW 和热塑性复合材料的详细信息,以及该研究所对该技术的未来发展方向。
激光绕带的演变
“当我们 30 年前开始时,激光技术还没有为热塑性复合材料的高速加工做好准备,”Janssen 说。 “你可以想象,特别是在控制方面,你只有一个模拟摄像机。现在,我们拥有更好的技术。例如,当我们在 2008 年开发紧凑型激光绕线头时,这导致了 AFPT Germany(德国 Dörth)的成立,我们不得不使用 16 像素 x 16 像素的相机,其帧率仅为 8每秒帧数。现在,我们可以轻松获得 640 x 480 像素和每秒 50 帧或更多的处理速度。”他解释说这很重要,“因为使用我们开发的激光绕带,主要优点之一是您可以查看 过程,并在几毫秒内改变处理能力。这为您提供了一个很好的优势,例如,当您处理复杂的几何形状时,例如压力容器的圆顶,缠绕速度减慢,您必须降低激光加热功率。然后,您必须在绕组沿油箱气缸恢复速度时重新调整。这在 15 年前是不可能的,因为激光、控制系统和热成像技术还没有准备好,或者太昂贵,也不如我们今天拥有的那么强大。
Janssen 继续说道,“因此,在数字方面已经发展了很多。例如,现在我们提供类似数字孪生的东西,您可以在其中将所有传感器信息映射到压力容器上,以便您可以比较制造的零件与数字设计的零件,以评估零件质量并预测性能。使用虚拟过程传感器和模型还使我们能够预测由其加工历史定义的层压强度。”他指出,这很重要,因为使用热塑性胶带的 LATW 使用快速加热和冷却,其中材料和零件属性在缠绕过程本身期间确定,因为缺少热后处理步骤。因此,具有快速过程控制的能力至关重要。
Janssen 说,材料方面也取得了进展。 “二十年前,可用的热塑性复合胶带材料数量有限,例如 Cytec 的 APC-2,现在是 Solvay(美国乔治亚州 Alpharetta),”他解释道。 “但是现在,有更多的材料符合工业应用的条件,而且还有很多商品材料,例如用碳纤维和玻璃纤维增强的聚丙烯 (PP),以及聚酰胺六 (PA6),例如,在汽车工业中被大量使用。现在也有 LATW 的应用,它们更倾向于批量生产。例如,电动马达中的固定套筒和其他部件受到推动。这些是简单的热塑性复合材料环或管,但每年的产量为 10,000 至 50,000 个。”
ambliFIBRE,石油和天然气管道
Janssen 上面描述的 LATW 中的部分数字控制是在 ambliFIBRE 项目(2015-2018)中开发的。 “在那个项目中有很多合作伙伴,”他说,“但一个是贝克休斯(英国纽卡斯尔和美国德克萨斯州休斯顿),我们使用我们的 LATW 设备制造他们的非金属管道。”请注意,在 2018 年 ambliFIBRE 结束后不久,贝克休斯宣布与沙特阿美(沙特阿拉伯利雅得)成立合资公司,以扩大非金属管道的使用,包括可能使用碳纤维增强塑料 (CFRP)。
贝克休斯现在的目标是加快在能源领域引入非金属材料,还有其他公司也在使用基于激光的管道技术,例如 Magma(英国朴茨茅斯)。 (参见“在深海上升的热塑性管道”和“Magma Global 提供高压复合立管……)。
“将激光胶带缠绕用于热塑性复合材料立管和出油管也很常见,”Janssen 说。 “虽然这在其他行业还不是常识。”他补充说,最近对 LATW 的关注主要集中在储氢罐上,但该技术已经有了更广泛的应用。
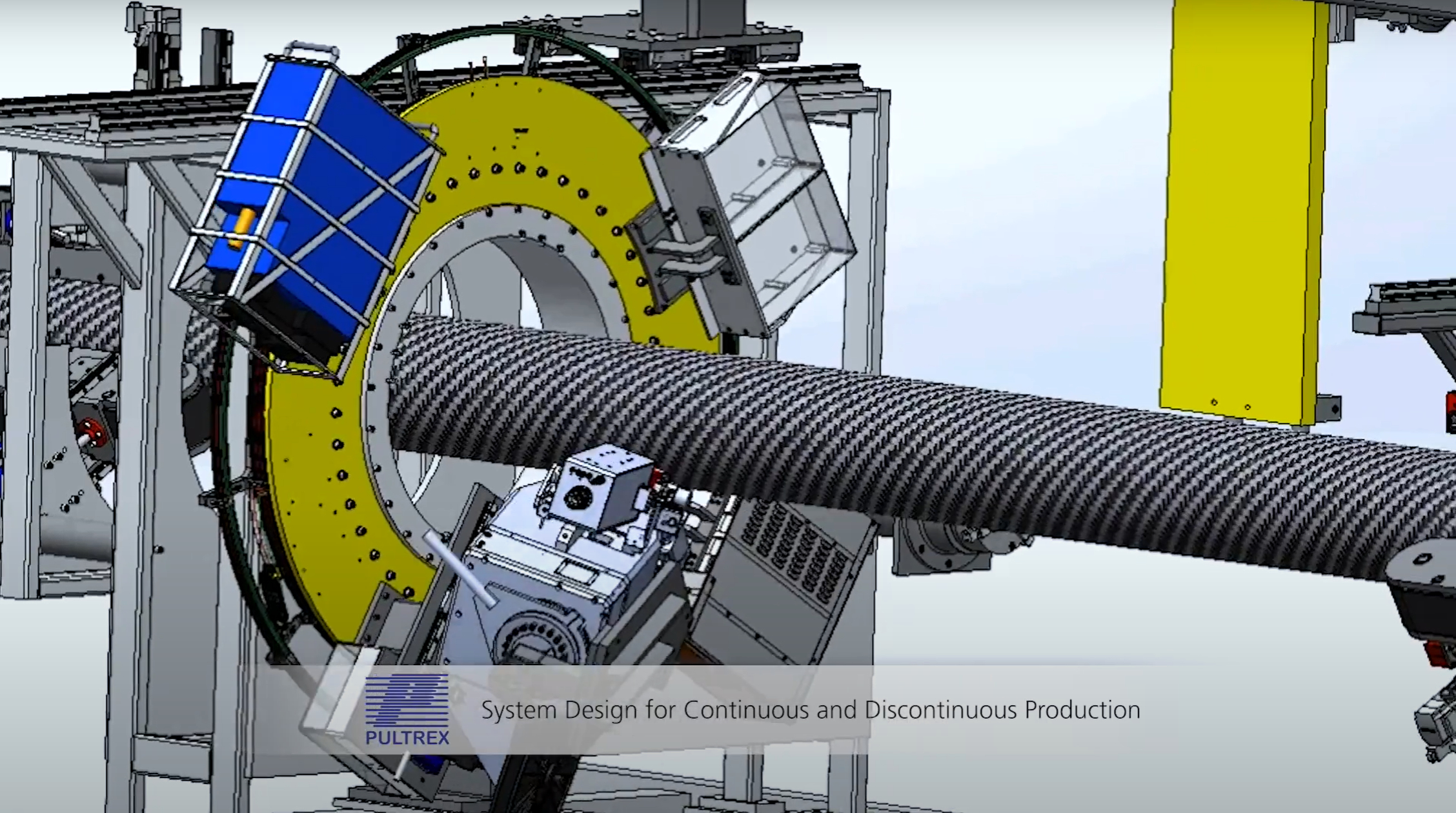
在 ambliFIBRE 项目中,Fraunhofer IPT 开发了用于不连续(例如罐)和连续胶带缠绕的数字过程控制模型,例如,生产数公里长的管道。图片来源:ambliFIBRE 项目的 Fraunhofer IPT 视频
“而我们 Fraunhofer IPT 为这些应用提供的服务是关键,”Janssen 说。 “显然,我们研究所并没有运行一条完整的连续管生产线,但我们为客户提供的是材料测试和产品认证。例如,有一个基于 DNV-GL F114 的测试金字塔,从对聚合物和纤维的鉴定和测试开始,然后按比例放大到复合层压板的微观结构或细观结构。因此,我们在试样级别进行了大量测试,然后扩展到较小的管道和代表性管道,例如,因为缠绕为您提供与压制或自动敷带 (ATL) 不同的属性。”
此外,他指出,“因为您的材料具有不同的应力,许多这些复合材料都在较小的管道中进行了测试,例如 2-3 英寸到几米长。因此,我们进行此测试,然后将我们的流程理解应用于实际零件长度,例如 2-3 公里。这非常有趣,因为该长度的处理时间可能跨越几天,您必须考虑收缩以及其他因素,例如环境空气温度的变化,这可能会产生相当大的影响。”
储氢罐中的 LATW
Janssen 说,Fraunhofer IPT 自 2000 年以来一直与石油和天然气公司合作。“然后,八年前,我们发现这与氢罐所需的技术几乎相同,”他回忆道。 “现在我们在 IPT 有一项关于氢制造以及燃料电池中的碳纤维复合材料的重大举措。我们正在建立一个耗资 8000 万欧元的自动化燃料电池制造工厂,并且还在投资一个新的、相当大的卷绕设施,以便我们可以生产长达 7 米、直径达 2.5 米的零件,我们也将使用这些零件用于大型压力容器。”
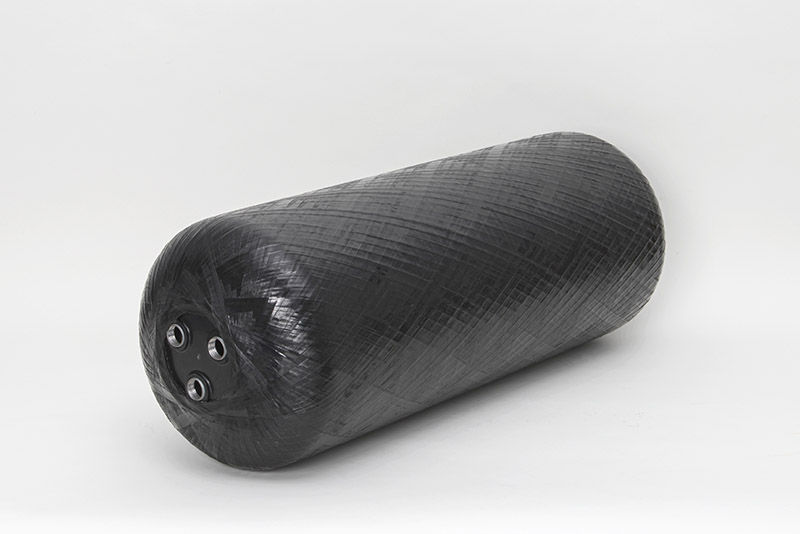
Janssen 说,使用热塑性复合带的 LATW 还不是压力容器制造的最先进技术,“因为热塑性塑料的化学性质及其加工和耐用性仍在研究中。但我们坚信,热塑性塑料提供的低渗透性、韧性和可回收性很重要。”他还看到了热塑性塑料在 V 型压力容器中的潜力,它们是全复合材料,但不使用单独的热塑性塑料内衬。 “这些可能为某些移动储氢应用提供未来的解决方案,例如燃料电池电动卡车。”
“我们还看到传统的热固性 纤维缠绕在最小缠绕角度方面受到限制,”Janssen 说。 “例如,您必须以不小于 10° 的光纤角度绕螺旋层绕圆顶。因此,您不能将 0° 增强材料放入传统的纤维缠绕罐中。”然而,他认为,“在经典的 LATW 中,传入的热塑性预浸料直接焊接到基材上,因此您可以朝任何方向前进,这为您提供了更多的设计自由度。我们目前正在与汽车行业的合作伙伴一起开展项目,以开发安全、节能且易于回收的用于储氢的热塑性压力容器。”
热塑性复合材料风扇叶片
Janssen 说,Fraunhofer IPT 在涡轮机械方面拥有非常强大的背景。 “我们在亚琛有 国际涡轮机械制造中心,或 ICTM, 一个竞争前的社区,我们与发动机制造商及其供应商在竞争前的研发项目中共同合作,以开发和提高制造技术。”
他指出,在过去的 20 年中,重点主要是加工压缩部分和涡轮机的先进产品的钛或镍基合金,例如叶片集成盘(叶盘)。在冷段,GE 于 1990 年代开发了复合材料部件(例如碳纤维复合风扇叶片),现在已在 GE90 和 GEnx 中使用。 “然而,现在,陶瓷基复合材料 (CMC) 被视为喷气发动机热部的下一代材料,”Janssen 说,“能够以更轻的重量实现更高的温度,从而提高效率。”
“与金属相比,复合材料零件的制造非常不同,”他继续说道。 “在金属中,你从大量材料开始,然后通过减法加工(主要是机加工)来获得零件,这样设计就不会那么依赖于制造。在复合材料中恰恰相反,复合材料总是需要某种生成过程。因此,我们决定从制造的角度解决新颖的风扇叶片策略。”
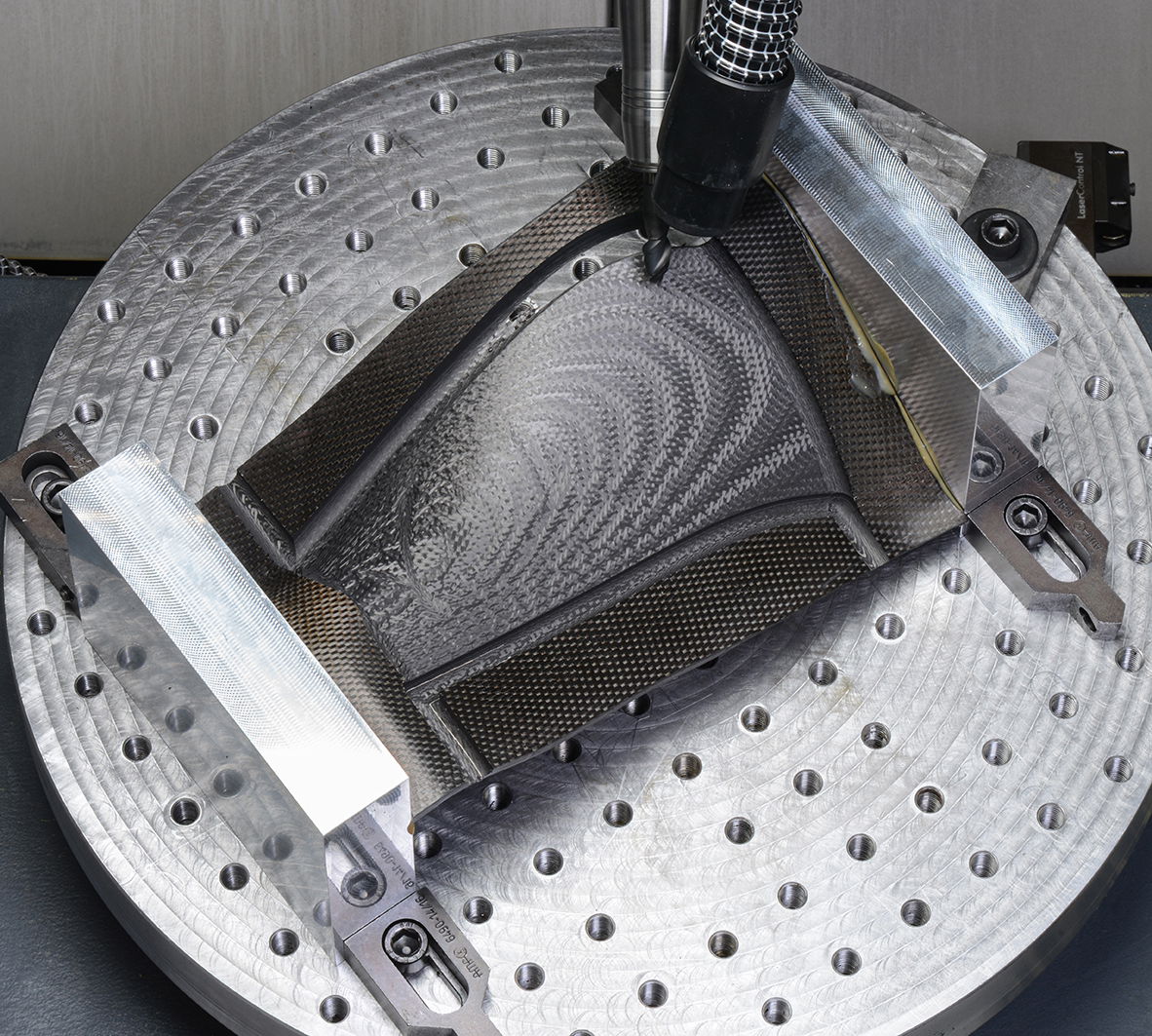
他还提到了清洁天空 2 联合项目,其中弗劳恩霍夫领导生态设计活动。 Fraunhofer IPT 专注于发动机的生态设计,包括生命周期评估和环境影响评估。 “这就是我们开始研究热塑性复合材料的原因,”他解释道。 “到目前为止,我们处于非常低的 TRL [技术准备水平]。目前,开发是关于制造和尝试不同的工艺路线,例如近净形状叠层和一点热成型——这更像是一个校准步骤——然后是加工方面的精加工。因此,我们还有很多工作要做。”
与此同时,Fraunhofer IPT 正在将其在金属航空发动机部件加工方面的专业知识扩展到复合材料,使用其数字技术来监控和评估每个叶片的加工参数。但复合材料的目标难道不是从这种减材制造转向更多的增材制造以减少浪费吗? “是的,但对于某些工艺路线,需要进行机加工以满足尺寸公差,”Janssen 说。 “我们现在正在做的是非常接近净形状。”
他指出,目前正在开发的设计是根部厚度为 0.75 英寸的热塑性层压板,尖端仅 2 毫米厚。 “然后有不同的设计策略,我们与设计工程师一起讨论。另外,您是否有高压釜或压力步骤用于那种非常高负载的零件?这也将在内部应力方面发挥作用,因为我们知道该叶片在旋转过程中有点扭曲。当然,鸟击是一个关键问题。”对于后者,Janssen 将热塑性塑料的韧性提高视为推动因素,并指出 PPS(聚苯硫醚)复合材料用于机翼前缘正是出于这个原因。
热塑性复合材料的未来应用
我询问了在发动机短舱中使用热塑性复合材料的可能性 ,据 2021 年 3 月的航空周刊报道,这可能有助于为最近的四次叶片脱落事件提供解决方案 文章:
“……叶片碎片撞击发动机罩或机舱的部分造成的损坏引发了一系列事件,导致包括发动机进气口和风扇罩的部分在内的大片结构破裂离开。”在所有四起事故中,飞机机身均受损,2018 年 4 月西南航空公司 1380 航班的其中一个窗户被移开,造成乘客死亡。
“工业界对在发动机舱中使用热塑性复合材料有一些兴趣,”詹森说,“然而,这是一个长期的发展。”这种发展的一个问题是航空当局的认证,这是弗劳恩霍夫 IPT 活跃的另一个领域。 “我们现在正在与认证机构讨论如何通过以数字方式证明新的制造工艺符合当前和不断发展的标准来帮助减少认证工作。所以,这是一种新的思维方式。在 21 世纪的制造业中,可用的数据太多了,这不仅仅是通过测试来验证一种工艺或一种设计,然后将其冻结。”换句话说,今天对工业 4.0 和复合材料 4.0 的强调是传感器和支持人工智能的软件将不断收集数据并开发智能,然后不断优化制造,反过来,将智能发送到数字线程中以改进设计。这确实与今天的制造业大不相同。
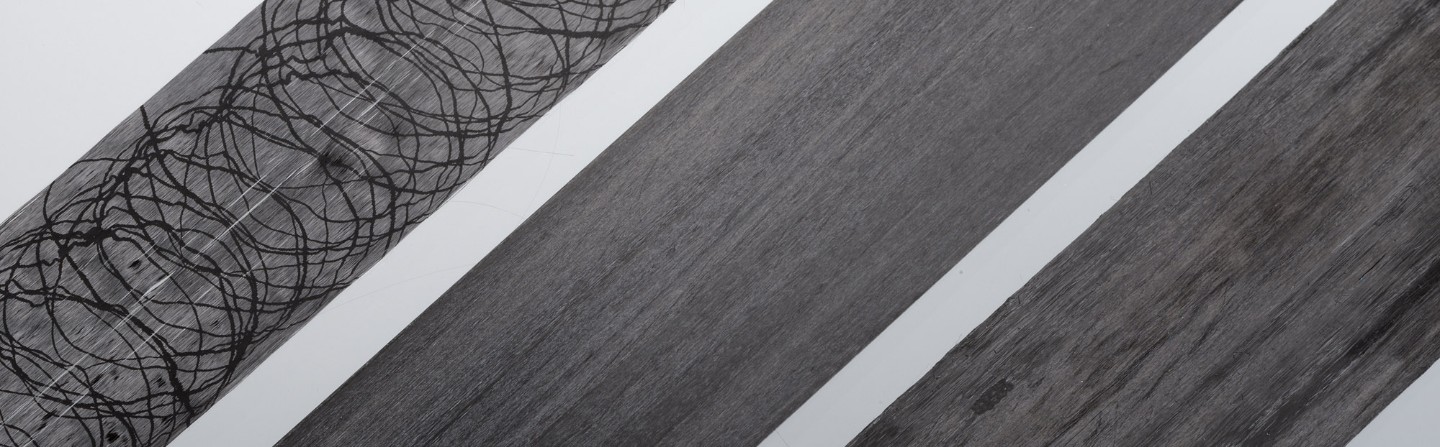
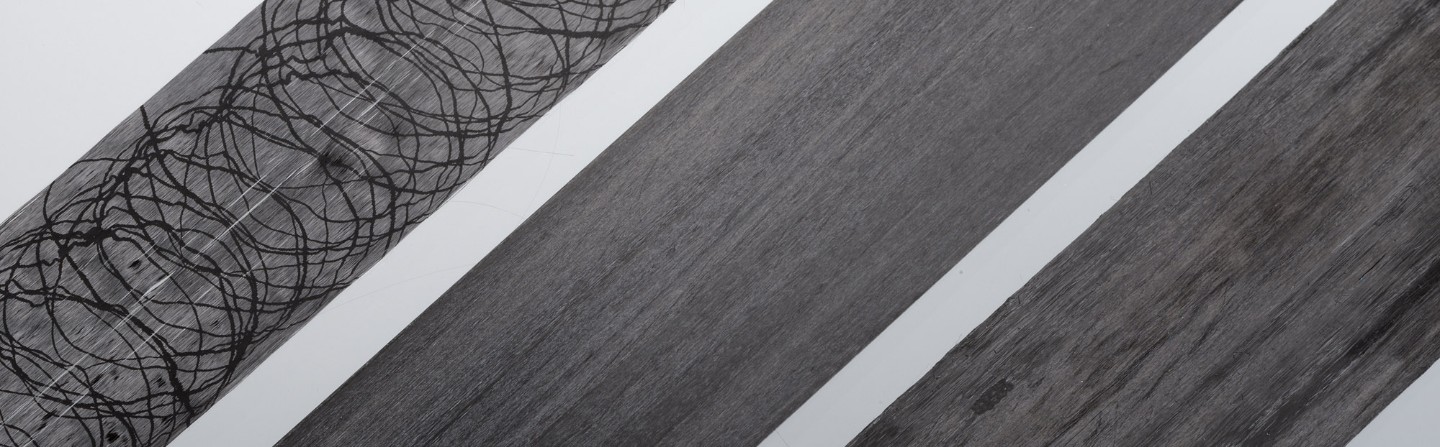
弗劳恩霍夫 IPT 的认证工作,Janssen 说,“可以帮助启用新技术,例如用于发动机零件的热塑性复合材料——也就是说,一旦所有方面,包括技术、设计和风险管理,都被考虑在内。”他断言,热塑性复合材料具有巨大的潜力,可以帮助克服品种中的关键挑战 工业部门,并指出 Fraunhofer IPT 正在努力克服热塑性复合材料的加工复杂性——例如,利用新可用的数字制造方法。 “此外,只有在考虑到整个生命周期(包括再利用和回收利用)后,才能充分利用热塑性复合材料的潜力,”Janssen 说。 “因此,Fraunhofer IPT 也在致力于热塑性复合材料的机械回收。我们认为,通过考虑制造过程中产生的数据和复合材料部件整个生命周期中产生的数据,有可能获得高价值的回收材料。”
树脂