使用热通量传感器加速 RTM
起落架占飞机重量的 3-5%,长期以来一直致力于减轻重量以提高飞机效率。随着即将转向减少能源和排放的电力推进系统,这一点变得更加重要。
例如,Safran Landing Systems(法国韦利济)将通过集成到飞机起落架轮中的电动机实现发动机关闭、电动滑行,将氮氧化物、二氧化碳、一氧化碳和未燃烧的碳氢化合物排放量减少 51%、61%、73% 和 62 %, 分别。对于更可持续的航空而言,这是一个巨大的胜利,但电动机需要动力,而提供动力所需的电池很重。
因此,除一个问题外,对轻型起落架结构的需求似乎非常适合应用复合材料。 “由于起落架是单载荷路径结构,结构部件的故障可能导致严重的紧急着陆条件,”GKN Fokker Landing Gear(荷兰赫尔蒙德)的技术专家 Peet Vergouwen 说。 GKN Fokker Landing Gear 十多年来一直致力于证明复合材料起落架结构的技术可行性,包括为 F-35 Lightning II 开发碳纤维增强聚合物 (CFRP) 阻力撑杆 . “由于其重要性,起落架结构是商用飞机中最保守的结构之一。”因此,它们大多由高强度金属制成。
然而,这种趋势正在开始转变。 Clean Sky 2 正在寻求减轻 30% 的重量,但通过 HECOLAG(高效复合材料着陆齿轮)项目中的 CFRP 组件,用于两种应用。在第一个应用中,为现有的铝制上阻力开发了 CFRP 替代品 用于 A350-1000 前起落架,最初由 Liebherr-Aerospace(德国林登堡)开发和制造。 HECOLAG 的合作伙伴荷兰皇家航空航天中心(NLR,Marknesse)和 GKN Fokker Landing Gear 已根据利勃海尔的要求设计了这种 CFRP 拖曳撑。 NLR 使用内部开发的自动化预成型技术构建了 CFRP 阻力撑杆的功能原型,并由 GKN Fokker Landing Gear 进行测试。
在 HECOLAG 正在评估的第二个应用中,NLR 和 GKN Fokker Landing Gear 还开发了 CFRP 下侧撑 与赛峰起落架系统一起用于电动主起落架。 连续波 将在 2021 年晚些时候专门报告 HECOLAG 项目的整体结果,但在这里,重点是 INNOTOOL 4.0 子项目,在主题经理 GKN Fokker Landing Gear 的指导下使用树脂传递成型 (RTM) 推进 CFRP 起落架结构的高度自动化生产.具体而言,INNOTOOL 4.0 旨在展示传感器集成工具,这将引领生产更小工具、更轻量的工具以加快生产周期、更容易处理和降低能源消耗,以及提高自动化以降低成本和复合材料 4.0 智能过程控制。 INNOTOOL 4.0项目由欧盟地平线研究与创新计划下的清洁天空2联合项目资助,GAP编号为821261。
INNOTOOL 4.0 目标
Vergouwen 解释说,HECOLAG 第二部分的演示器(见开头图片)更像是一个通用部分。 “它用于展示零件设计、模拟和制造方法,这些方法将提供单通道飞机所需的性能、生产率和成本。”到 2017 年底,HECOLAG 联盟已经定义了初始 CFRP 演示器部件和生产工具,分析了工具的热行为并进行了性能试验。这个庞大而复杂的产品通过了初步设计审查,并于当年晚些时候达到了 4 级技术准备水平 (TRL)。 “基于从第一个演示者身上学到的问题和经验教训,我们正在寻找合作伙伴来开发 RTM 工具技术,以优化和缩短固化周期,”Vergouwen 说。清洁天空 2 合作伙伴征集于 2018 年发布,并授予 INNOTOOL 4.0 联盟,包括设备和自动化供应商 Techni-Modul Engineering(TME,Coudes,法国)和树脂注射专家 Isojet Equipements(Corbas,法国)。他们于 2019 年 4 月开始工作,并于 2021 年 3 月完成了最初的里程碑。
GKN Fokker Landing Gear 的 Vergouwen 指出:“复合材料部件必须与锻造钢和铝相比具有成本竞争力。” “这只有通过自动化才有可能实现,与当前的航空级、高压釜固化 CFRP 相比,可以实现非常少的工时和更实惠的材料。”
因此,INNOTOOL 4.0 试图将传感器集成到 RTM 工具中,该工具将监控和管理注射和固化过程,包括树脂流动前沿检测。 “目标是完全自动化——加载预成型件,按下按钮,成型设备将管理温度、压力、真空和固化,”TME 商业总监 Stéphane Besson 说。然而,这是 GKN Fokker Landing Gear 和 TME 首次进行固化监测。 “我们之前使用过温度和压力传感器,”Besson 说,“但没有使用过用于树脂流动和聚合的传感器。”
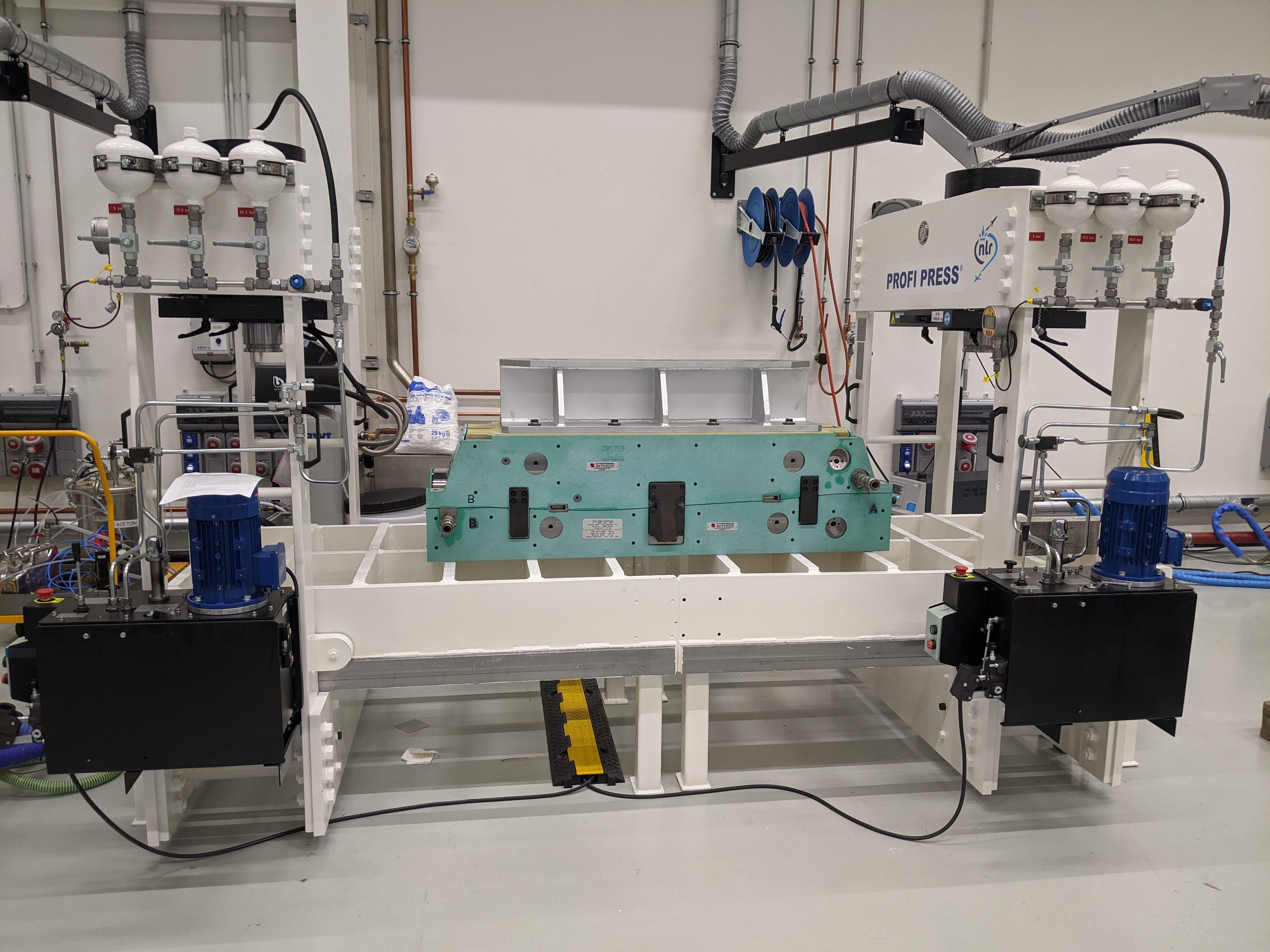
INNOTOOL 4.0 项目的初始里程碑要求 TME 和 Isojet 向 NLR 交付配备传感器的成型工具和注射系统,用于在 2021 年 3 月和 2021 年 4 月生产演示零件。同时,TME 将使用现有工具生产CFRP 板 - 尺寸为 600 x 600 毫米,厚度为 1-8 毫米 - 使用相同的传感器进行修改,以在其设施中进行过程控制试验。 Vergouwen 说:“这是您第一次更愿意在小规模上做的事情,而不是直接在具有高成本零件的大型工具上进行。”因此,TME 使用了不同的工具,但使用相同的传感器来展示其功能和深度。测试完成后,NLR 将重新使用主要的 HECOLAG 工具来生产新一轮的 CFRP 演示器,以进一步优化实际零件的过程控制。
RTM 生产工具设计
TME 开始使用 Dassault Systèmes(法国 Vélizy-Villacoublay)的 CATIA V5 软件进行机械和电气设计,使用 ANSYS(美国宾夕法尼亚州卡农斯堡)进行热和机械仿真来生产 RTM 工具设计。该工具将与 Isojet 的活塞式 1K-2K(用于单组分和两组分树脂)系统配对,以注入 Hexcel(美国康涅狄格州斯坦福德)HexFlow 2K RTM 6 和 Solvay(美国乔治亚州阿尔法利塔)1K PRISM EP 2400 单组分航空级环氧树脂,注射压力高达 20 bar。
“这种成型工具的形状非常复杂,”Besson 指出,“将 3D 干燥预制件中的不同厚度与封闭的管状形状相结合。这会产生复杂的厚度过渡,涉及预成型件组装、层端精度、内部温度梯度和树脂收缩等问题,以及如何优化内部心轴的加热方法和加热能力以缩短循环时间。为了缩短循环时间,工具的所有元素都必须易于使用、坚固耐用并允许快速加热和冷却。”尽管 INNOTOOL 4.0 项目简单地要求非金属模具解决方案,但由于在成型过程中最大限度地减少皱纹和确保纤维对齐所需的压力,设计了一套典型的上下钢模具匹配。
匹配的上下模具和芯棒被加热和冷却。 “匹配的模具使用集成的水回路,而心轴则是电加热的,”Besson 解释说。 “水循环提供快速加热和冷却以减少零件循环时间,而电加热在空间有限的心轴中实现了同样的效果。”
“另一个挑战是心轴中的零件数量,”贝松说。 “由于形状复杂,需要在成型后移除芯轴,它由六个自加热组件和两个支撑元件组成,传感器穿过这些元件以控制芯轴件的内部温度。在使用中,这些元件是在引导操作员的基础支架的帮助下手工组装的。”使用充气芯棒作为解决方案的工作将在更大的 HECOLAG 项目中完成,但未包含在 INNOTOOL 4.0 子项目中。
热通量传感器
TME 最初计划使用介电传感器来监测树脂流动和固化(参见“结合 AC 和 DC 介电测量对复合材料的固化监测”),但改用 TFX(瑞士邦古尔)的热通量传感器。 TME 项目经理 Jorge Lopez Torres 解释说:“随着开发的进展,我们希望传感器能够在不直接接触聚合物和复合材料的情况下进行测量。” “TFX 传感器实现了这一点,因为它们测量通过材料传播的热通量。”他指出,这与差示扫描量热法 (DSC) 中使用的测量方法基本相同,这是一种分析聚合物或复合材料固化状态的实验室技术。值得注意的是,TFX 传感器和 DSC 测试都测量聚合/固化过程中释放的热量,并得出热通量与温度和时间的关系曲线。
对于 TFX 传感器,温度数据来自热通量传感器内的内部温度传感器。尽管介电传感器类似地配备了内部温度传感器,但这两种传感器却大不相同。 “介电传感器在固化过程中直接测量聚合物的特性,”TFX 经理 Fabien Cara 博士解释说。 “热通量传感器不会在给定的瞬间给出材料的状态。然而,测量树脂流动和聚合过程中产生的热量可以很好地了解过程的行为以及每个零件的固化循环的可重复性。和 DSC 一样,我们需要看到固化过程的整个曲线,但我们监控固化的能力非常可靠。”
数十年的经验
成立于 2000 年的 Thermoflux,TFX 传感器已被全球 100 多家客户用于研发中心的试验和工业应用。 “我们在 15 多年前就开始与 RTM 合作,”Cara 说,“首先是与 BMW 合作生产汽车零部件,还有现在被称为 Institute de Soudure [(法国圣阿沃尔德)] 的技术中心。 2006 年和 2012 年,我们启动了两个大型项目,用于监测使用 RTM 和 3D 编织预制件制成的飞机发动机风扇叶片的固化情况。赛峰集团在巴黎附近的复合材料实验室为他们开发了一个数据采集系统。他们可以同时记录多达 100 个信号 [(热通量、温度和压力])并分析这些信号以进行固化和监控过程周期。” TFX 还与 Hexcel 在其位于法国 Les Avenières 的实验室合作,监控注入干燥瓶坯的热固性树脂的质量和加工周期。 TFX 传感器还用于 IRT-M2P(法国 Porcelette)的一个项目中,以演示压缩 RTM(了解更多)。 “我们的传感器对于压缩成型等快速工艺非常有效,包括使用 SMC 和 BMC 模塑料,”Cara 指出。 “我们还在 2016 年与 Huntsman Advanced Materials [(瑞士巴塞尔)] 一起赢得了 JEC 创新奖,该奖项名为‘在不到 1 分钟的时间内获得具有高压釜质量的结构环氧树脂部件’。”
TFX 拥有适用于各种类型的复合材料成型工艺的传感器,基于传热到传感器的方法:传导(RTM、压缩和注塑成型)、对流(高压釜、烤箱)和辐射(纤维缠绕、AFP)。 INNOTOOL 4.0 项目中使用的传感器是导电的,专为嵌入金属 RTM 模具而设计。 “它们在距工具表面和复合材料最多 1 毫米的距离内提供极其可重复的信号,”Cara 指出。
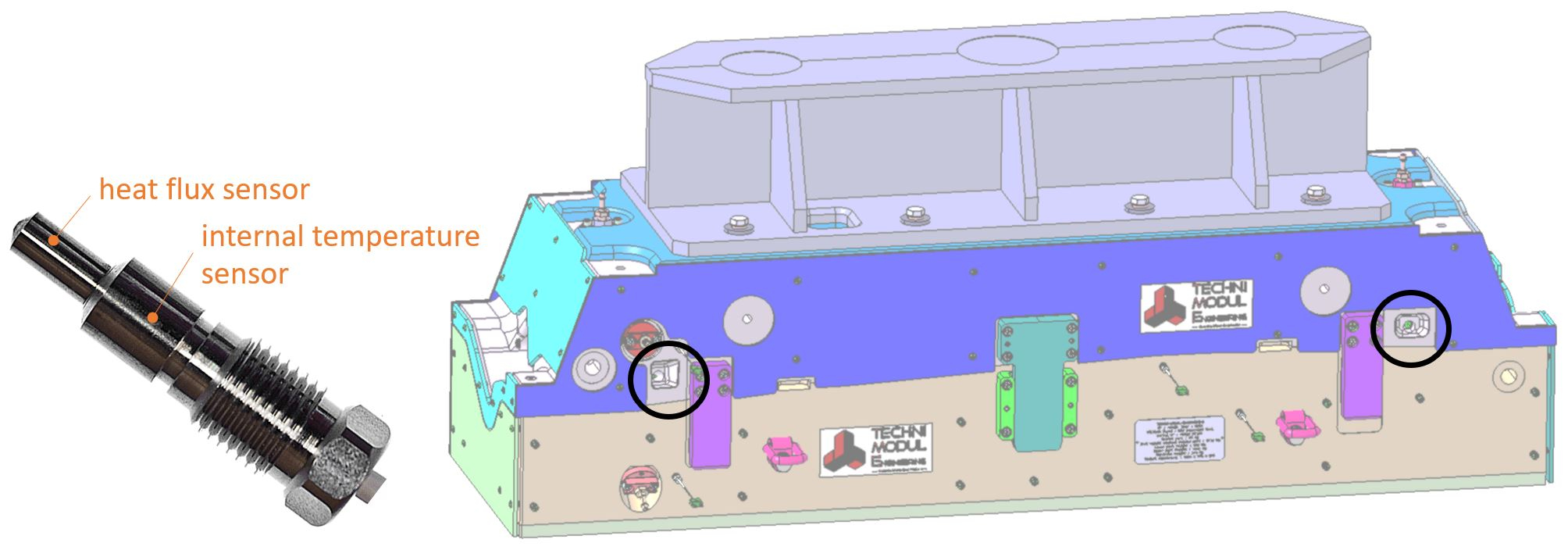
TME 将两个 TFX-191 传感器——一个在树脂入口处,一个在树脂出口处——安装到匹配的生产工具集的上模中,然后将其发送到 NLR(图 1、2)。 NLR 于 2021 年 3 月和 4 月使用该生产工具制造了 HECOLAG 演示器部件。TFX-191 传感器用于厚金属工具。
与此同时,TME 使用了一个更小的内部工具来制作样品 CFRP 板,并用两个更短的 TFX-224 传感器对其进行了修改,以获得更薄的工具(图 3)。然后,根据上述 INNOTOOL 4.0 目标,使用该 RTM 板工具集进行传感器演示试验。 “这些传感器与我们用于赛峰的传感器类似,”Cara 说,“但现在经过改进,变得更加紧凑和灵敏。”传感器放置在零件中心和树脂出口附近。除了热通量传感器之外,TFX 还开发并提供了两种数据采集系统——一套交付给 Isojet,一套由 TME 用于 CFRP 板试验。
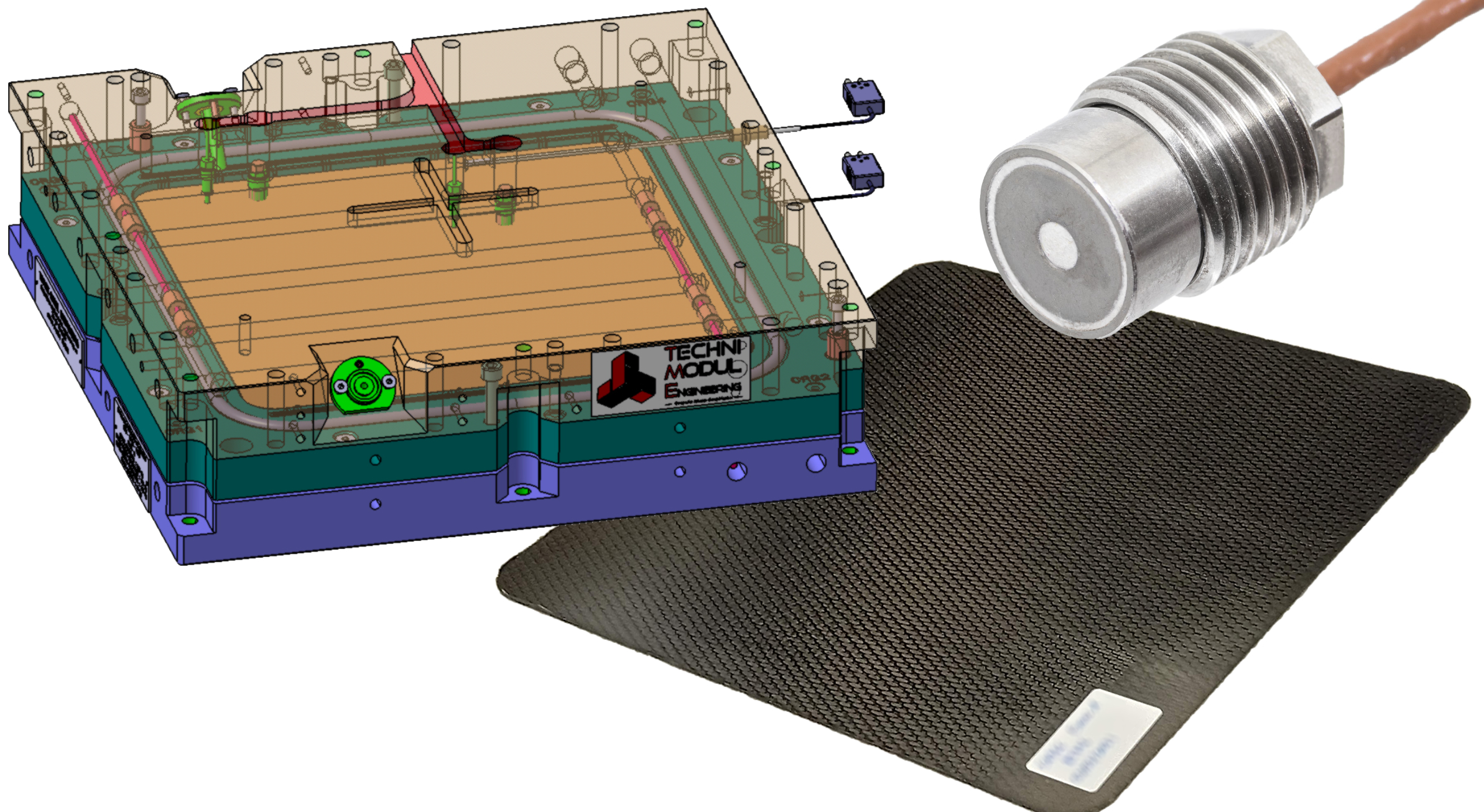
INNOTOOL 4.0 测试结果
TME 使用其经过 TFX 传感器修改的板工具进行的试验测试了两种不同的树脂——HexFlow RTM 6 和 PRISM EP 2400——以及零件厚度和整体固化时间的影响。 “传感器提供了很好的信号来监控固化周期,”Cara 说。 “该团队随后分析了固化曲线,并表明 RTM 6 的固化时间可以比规定的两小时固化时间减少至少 30 分钟。”
这可以在下面的曲线中看到,其中 t=0 小时是注射的开始。请注意,固化时间从温度达到 180°C 时开始,固化结束对应于相对固化水平的 99%(参见右侧的垂直轴)。固化结束也与原始热通量稳定相吻合。
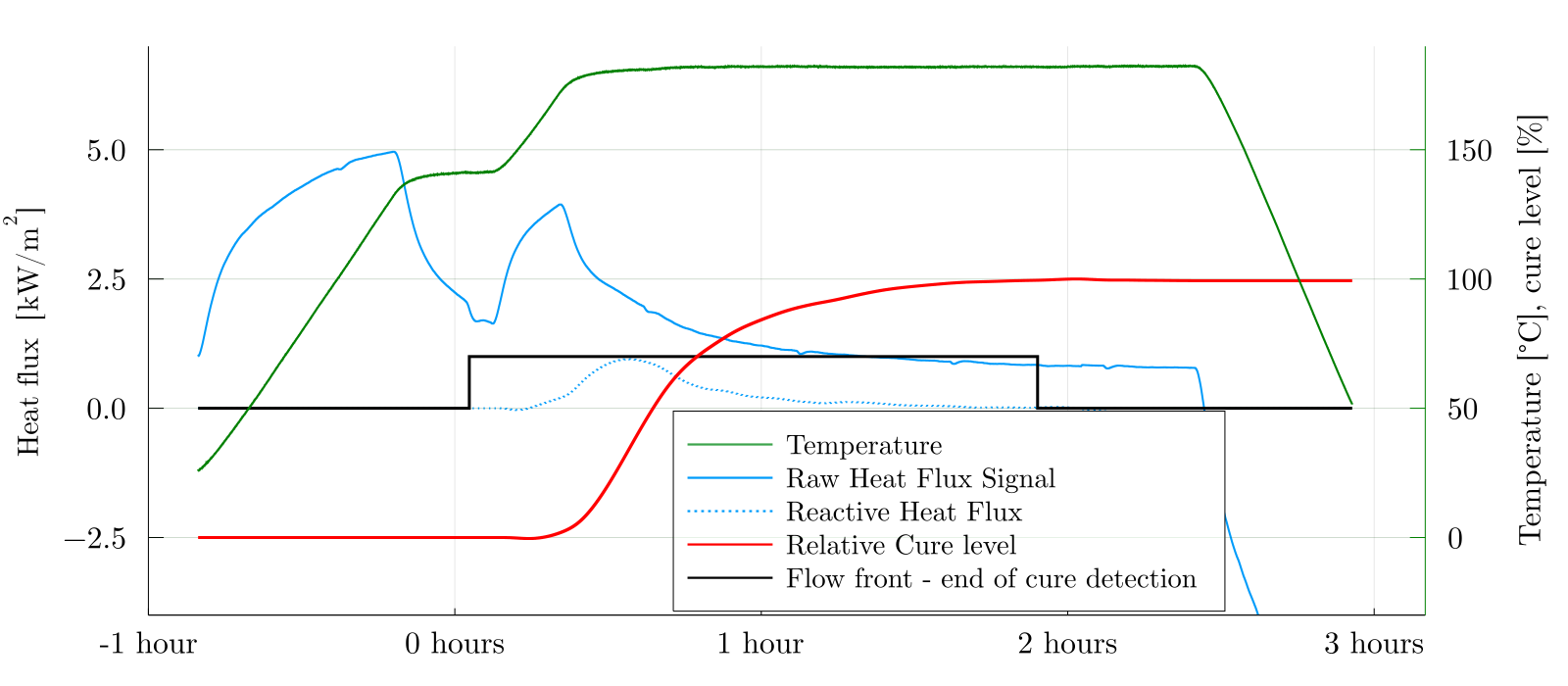
这是通过使用动态力学分析 (DMA) 对脱模部件进行固化状态测量来验证的,这是一种替代 DSC 的实验室技术,可测量复合材料的玻璃化转变温度 (Tg)。 “DMA 结果证实,对于 RTM 6 树脂,在 180°C 下固化 90 分钟后,Tg 保持不变,”他补充道。
还研究了厚度的影响。 “TME 在其传感器演示试验中测试的第一批 CFRP 板的厚度不到 2 毫米,”Cara 指出。 “这些板材还具有高纤维体积 (50-60%) 和缓慢的固化周期,以防止放热和潜在的热应力和零件质量问题。这对于航空航天部件来说是很正常的,但这意味着树脂很少,因此树脂反应释放的热通量很小。因此,我们实际上是在寻找由于在加热工具和零件的海洋中树脂固化而产生的热通量针。”
换句话说,正如 Cara 解释的那样,“大多数航空航天 RTM 固化周期都涉及在一个温度下注入树脂,然后在更高的第二个温度下逐渐固化。因此,当您完成注射时,您将工具加热到固化温度,这会在整个系统中产生很大的热通量。”然而,与 DSC 测试一样,使用热通量传感器监测固化的关键是测量聚合/固化过程中释放的热量,并在热通量与成型系统中的温度和时间的曲线中显示这些测量值。 “因此,我们发明了一种方法,可以帮助我们减去加热模具的基线以及该热量向零件的传导,从而可以确定树脂反应的热通量。”
因此,即使初始薄板的工艺条件非常具有挑战性,Cara 说,“我们仍然可以看到树脂反应的热通量。然而,通过制造更厚的零件,我们能够根据零件厚度准确地看到热通量水平的差异,这验证了我们对薄零件的固化监测。”请注意,上面的曲线(也显示在开场照片中)是在 3.2 毫米厚的板上使用 RTM 6 树脂获得的。
然而,树脂流动前沿检测的结果更成问题。 “对于出口附近的传感器,我们可以很好地看到流动,但对于靠近中心的传感器,树脂到达的时间很晚,”Cara 说。 “使用热通量传感器进行流前检测需要树脂流动来产生局部热场的变化。当树脂与预成型件的温度不同时,就会发生这种情况。”他指出大于 0.1°C 的 ΔT 足以进行检测。 “然而,对于薄 CFRP 板的试验,模具中的温度非常均匀,树脂到达非常缓慢。因此,热对比不足以检测树脂到达与整个系统中的热噪声。然而,由于流道 [预成型件和模具边缘之间的间隙,参见“制造 RAPM 的复杂几何部件”],树脂到达出口的速度更快,这有助于产生更大的热对比度,更容易检测和监控。 ”
Cara 建议使用 TFX 开发的新型有源传感器可以改进这种树脂流动前沿监测,该传感器在传感器内使用集成加热功能。他解释说:“这使传感器能够帮助提供固有困难的零件和流程所需的热对比度。”
扩展复合过程控制能力
“我们对迄今为止完成的工作感到满意,”托雷斯说,“但这只是第一步。目标是使用这些热通量传感器来管理生产环境中的复合材料加工。” Cara 说,这是可能的,根据树脂到达情况,自动将信号从传感器系统发送到注射设备,并根据固化曲线中的零斜率发送到压力机。 Torres 补充说,TME 拥有用于管理温度和压力的注塑机和 RTM 压机的过程控制系统。 “下一步,”他说,“是将 TFX 传感器集成到这些控制系统中,并通过笔记本电脑管理整个过程。” Cara 指出,TFX 传感器和数据采集还与压力传感器(例如,瑞士温特图尔的奇石乐)配合使用,以帮助实现整体过程控制,他的公司正在开发一种传感器,可以测量热通量、温度和 em> 单个集成设备中的压力。
但这种过程控制是否负担得起? Cara 表示,监控系统最初的 10-30,000 美元投资通常会在开发阶段获得回报,通过改进流程和零件理解减少试验和错误。 “然后,该系统继续在生产过程中节省成本、缩短周期时间、确保可重复性并及早发现偏差或不合格。”
在 GKN Fokker,Vergouwen 认为,一旦证明能够减少周期时间和提高成本,“那么就可以想象复合材料不仅适用于 INNOTOOL 4.0 和 HECOLAG 项目中展示的起落架组件类型,而且适用于所有类型的起落架组件。部分。这将打开我们的设计空间,使我们能够进一步推动轻型起落架的界限。” Besson 看到了更广泛的应用:“这种类型的过程控制可以开发用于各种模具和复合材料零件。”
树脂