热塑性复合结构替代安全关键制动踏板上的金属
汽车行业在 1990 年代将加速踏板从金属转变为注塑成型的短玻璃热塑性塑料。然而,制动踏板——具有挑战性的刚度、强度和扭转载荷要求的安全关键部件——需要更长的时间来转换。一级汽车供应商 Boge Rubber &Plastics Group(德国达梅)表示,它是第一家满足 OEM 要求的热塑性复合材料制动踏板性能和成本目标的供应商。独特的设计、三种不同的材料和定制的生产工艺使该公司能够生产出更坚固、更坚固、重量更轻且成本更低的踏板。
找到一个重要的利基
Boge 是汽车行业减振和动力总成/底盘安装以及轻型塑料模块和踏板盒(包括制动器、离合器和加速踏板的组合)产品的开发商和生产商。自 2008 年以来,它已使用短玻璃包覆成型化合物生产连续纤维有机片材汽车零部件。2018 年,它在混合物中添加了单向 (UD) 热塑性胶带。通过持续的工艺创新,周期时间和成本得以减少,业务也增加了。>
“在 2015 年,我的老板来找我说,'你所做的这些改变很好,丹尼尔,但如果你能找到一个更大的市场,产量真的很重要,'”-Ing 博士回忆道.博格全球创新中心高级经理/轻量级团队负责人 Daniel Häffelin。博格工程师团队接受了挑战,并集思广益如何提高光纤效率以降低成本并获得更多业务。
“Organosheet 是一种很棒的产品,但您必须以正确的方式使用它,仅在需要时使用,”Häffelin 解释道。 “我们已经使我们的生产过程变得非常精简,因此通过进一步缩短周期时间我们不会获得太多收益。我们推断,降低成本的最佳方法是通过更有效地使用该纤维来减少我们使用的无尽纤维的数量。”
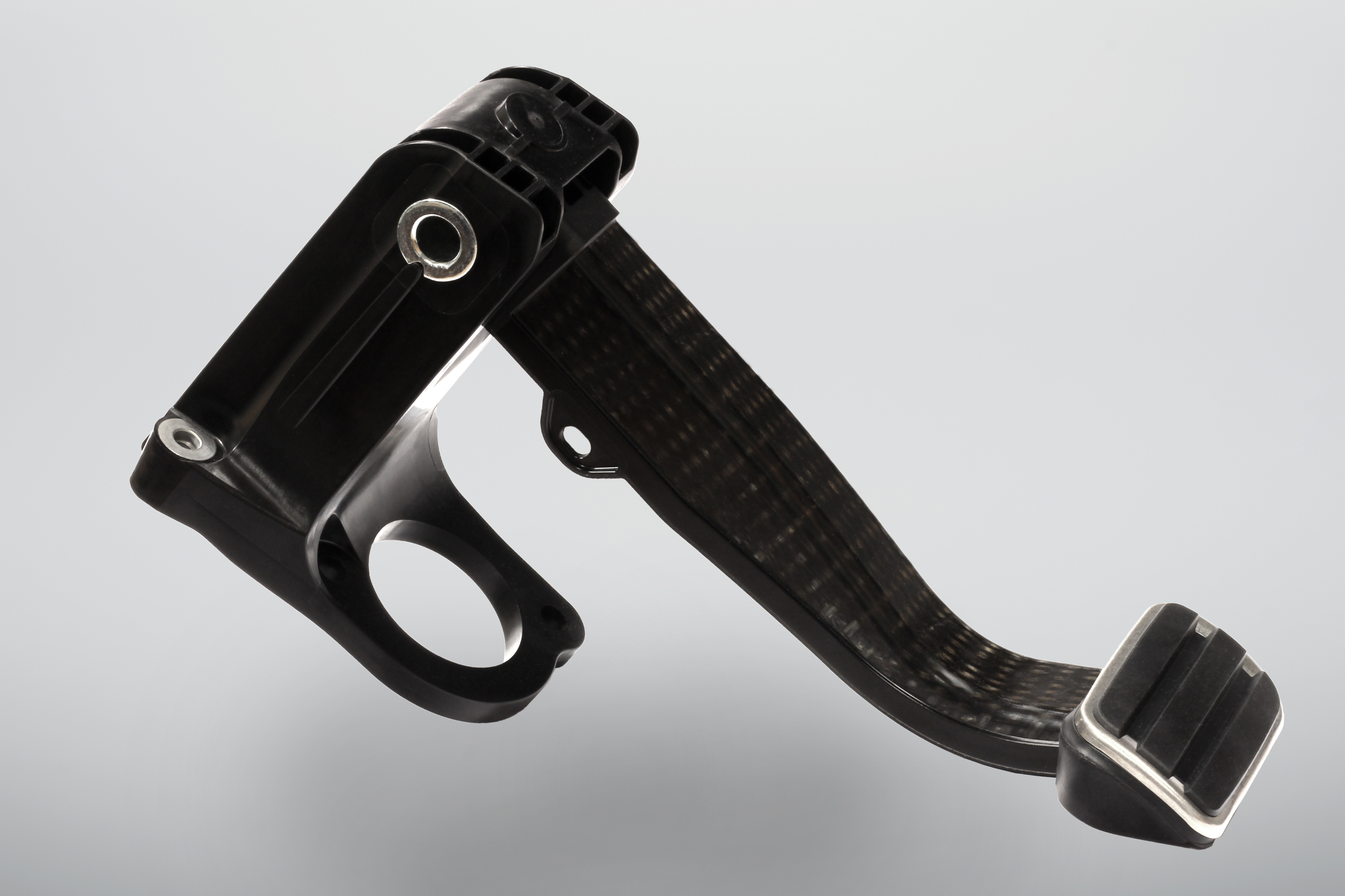
简单地使踏板更小或更薄也是行不通的,因为制动踏板的尺寸和形状存在实际限制,更不用说由于其安全关键性质而具有挑战性的性能规格。最有意义的是找到更好地控制纤维取向的方法,以优化承受最高峰值载荷的部件区域的局部特性,从而提供减少不太关键区域的壁厚的机会。
“我们寻求一种方法来局部‘引导’纤维,这样我们就可以将它们放置在我们需要它们的地方,以保持刚度和强度,”博格橡塑集团首席执行官 Torsten Bremer 博士补充道。 “我们知道,原则上,这是可能的,因为我们已经考虑过用于体育用品和医疗的拾放机器,但它们太贵了。那时我们决定需要一个新流程。”
“我们已经与一家德国原始设备制造商合作,寻找制造满足其性能和成本要求的全复合材料制动踏板的方法,”博格塑料与橡胶集团执行副总裁兼塑料产品线负责人 Burkhard Tiemann 回忆道。 “我们对客户说,‘我们将开发一种使用 UD 胶带和有机片材的新工艺。’他们对我们说,‘如果你能进一步减少质量和成本,我们就会这样做。’这是我们的起点。我们在 2015 年做出了重大承诺,即我们可以提供更便宜、更轻且可以大批量生产的全复合材料制动踏板。制定细节并交付我们的第一批产品花了三年时间。”
光纤转向
复合制动踏板必须满足与现有钢或铝制踏板相同的性能规格。这包括负载高达 3,000 牛顿的特殊故障模式要求和最大负载下的类似钢的挠度。鉴于这些要求和有限的可用包装空间,承载最大载荷的踏板的主要外壳结构需要连续纤维增强。因此,该团队决定使用有机板来形成踏板主干。然后,UD 胶带将用于局部增加刚度/强度,并在零件区域的峰值应力期间加强内壁,该区域随后将在预成型期间弯曲成 U 形槽。在需要肋条等功能几何形状的区域,指定了短切玻璃包覆成型化合物。该团队认为这种混合方法可以提高纤维效率,同时减少材料使用量、平均壁厚和循环时间。

该团队开始密集的模拟工作,以优化生产过程中的纤维位置。 Boge 工作的基础是 2011-2014 年德国公共资助的一项名为 SoWeMa(全自动封闭轻量制造链的软件、工具和机器开发)的研究计划。
“SoWeMa 的研究涵盖了我们在一年后为自己的企业提出的许多问题,”Häffelin 解释道。 “因为设计是 Boge 核心技术的一部分,我们从 SoWeMa 程序的基础开始,并为各向异性铺层结构构建了我们自己的 FE(有限元)仿真功能。”
重点领域之一是胶带铺设和肋结构的组合拓扑优化。 “我们创建了一个迭代周期来优化胶带的放置并相应地调整肋结构,因为两者在零件的刚度和强度上联系在一起,”中车创新中心 FEA 工程师 K. Siebe 继续说道。 “由于 UD 胶带、有机片材和短纤维材料的材料组合是独一无二的,并且它们的应用受特定湿度和温度窗口的限制,因此我们构建了自己的材料卡,以更准确地表征这些材料在物理测试期间的表现。 ”
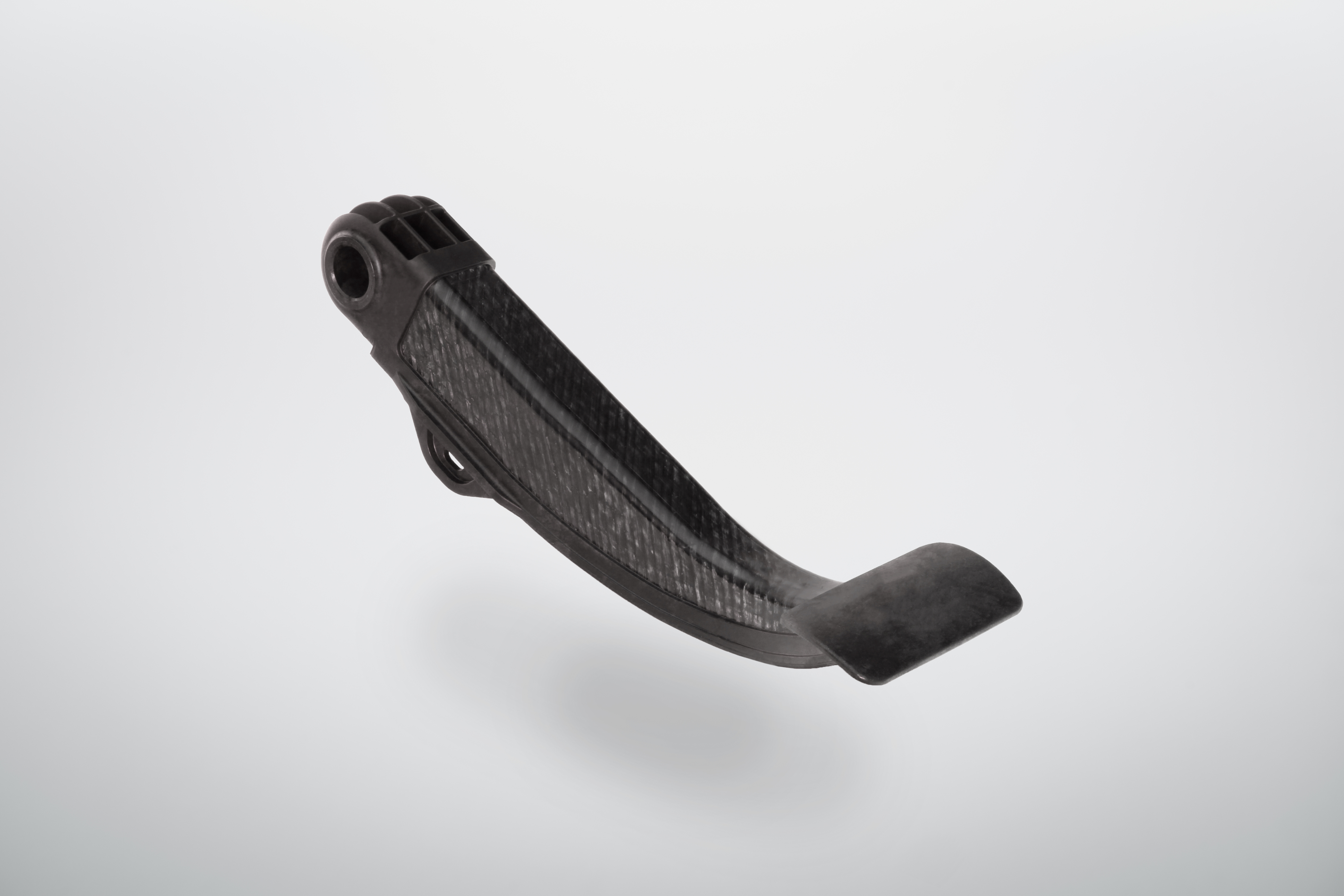
Boge 根据模拟结果和给定的踏板设计为每种材料指定了层结构和纤维结构。 Lanxess Deutschland GmbH(德国科隆)供应纤维体积分数 (FVF) 为 45-50% 的有机片材。 FVF 为 55-60% 的 UD 热塑性胶带由 Celanese Corp.(美国德克萨斯州欧文市)提供。用于此应用的短玻璃注射化合物的纤维重量分数 (FWF) 为 40-60%,由多个来源提供。所有材料均为黑色,并具有聚酰胺 6 或 6/6(PA6、PA6/6)矩阵。为满足客户规范,PA6 是所有三种复合材料类型的默认树脂。然而,根据制造过程中的湿度和温度水平,以及空间限制和踏板几何形状,Boge 也可以使用 PA6/6 进行包覆成型树脂,因为这两种聚合物非常相似,可以很好地粘合。
三步生产
在设计的同时,该团队还进行了三步生产过程。在第一步中,通过使用预切割和预固结的有机板作为稳定的基础来创建定制的纤维坯料,在此基础上战略性地粘贴与负载路径对齐的 UD 胶带条,以加强零件的外壳结构。在第二步中,坯料被移动并依次加热、固结和成型/悬垂。第三步,用短玻璃化合物包覆成型,形成肋状结构。
为了实现快速循环时间,该系统采用了机器人处理。该团队希望包括的一个关键工艺特征是可以灵活地将任何长度、任何方向和任何位置的胶带放置在有机片壳的一侧,并将这些胶带用激光钉在壳上,这样它们就不会移位
团队做出的另一个决定不是在铺层后立即预加固剪裁好的毛坯,而是在悬垂/预成型和包覆成型之前。该团队认为无论如何都必须在悬垂/预成型过程中重新加热材料,并且为了经济高效,他们必须将总循环时间保持在接近 1 分钟。因此,Boge 在悬垂/预成型之前使用快速升温和高压加热和固结坯料,以在胶带和有机片材之间形成牢固的机械粘合。加热停止,零件温度开始下降,因为仍然热的固结坯料在再次移动之前进入悬垂腔,并在第二个腔中用肋条和其他功能特征包覆成型。所有三种材料之间都实现了牢固的机械键,并具有经验证的聚合物链渗透。无需模具后整理。
为了满足这些安全关键部件的质量要求,该团队还开发了一种快速、准确且符合工业 4.0 的系统,该系统使用视觉、力、时间、压力和温度传感器来检查制造过程中的每个步骤的材料。然后系统存储该数据并将其与每个踏板的唯一标识号相关联。这确保了所有涉及的材料、班次和流程设置的 100% 可追溯性。
迄今为止的成就
Boge 的定制、全自动和质量控制流程在 2018 年实现了从原型到大批量批量生产的一步。大约每分钟生产一个新踏板,目前的制造单元每年可以生产多达 100 万个零件。全复合踏板使用的有机板比早期设计少 33%,标称壁厚从 3 毫米下降到 2 毫米。踏板的重量也减轻了 50-55%,但达到或超过了钢的强度要求。较轻的踏板改善驾驶触觉 对于消费者而言,整个系统在生命周期结束时是 100% 可回收的。按照目前的工艺,复合踏板的成本与铝相当,而成本略高于钢。其他汽车和体育用品的应用正在开发中。
随着汽车制造商将资源转移到车队电气化,未来会怎样? “随着线控驱动 [机电驱动系统] 和动力总成电气化变得越来越普遍,油门踏板可能会消失,但制动踏板会保留下来,”Häffelin 沉思道。 “但是,我们可能会在制动踏板中看到更大的电子集成,包括传感器。这将大大增加零件的复杂性,使复合材料更多 比金属更具竞争力。”
CW 中更详细地解释了材料使用、工艺步骤和设备标准 2021 年 1 月的后续文章“定制工艺每分钟生产复合制动踏板。”
树脂
- 长纤维增强尼龙复合材料取代铝制电机外壳
- 完全由自然资源制成的连续纤维增强热塑性复合材料
- 索尔维扩大热塑性复合材料产能
- Oribi Composites,Packard Performance 越野动力运动热塑性复合材料车轮的合作伙伴
- Fraunhofer 委托自动化 Engel 生产单元进行热塑性复合材料研发
- 索尔维完成南卡罗来纳州设施的安装,增加了美国热塑性复合材料的产能
- 联盟致力于碳纤维热塑性复合结构的解决方案
- INEOS Styrolution 为 StyLight 热塑性复合材料建立生产基地
- Xenia 推出 CF/PP 热塑性复合材料
- 在深海中崛起的热塑性复合管
- NIARs NCAMP排位昙卡热塑性复合
- TenCate 在巴西庆祝热塑性复合材料联盟的组装