自动化航空复合材料生产:液态成型还是焊接热塑性塑料?
随着原始设备制造商和供应商探索支持下一代飞机的材料和工艺,正在展示两种不同的方法。第一个是干纤维预制件的液体成型,例如,在 Spirit AeroSystem(苏格兰普雷斯蒂克)的用于空中客车 A320 扰流板的高速树脂传递成型 (RTM) 生产线以及空中客车领导的明日之翼 (WOT) 计划中它使用非卷曲织物 (NCF) 的自动放置和液体树脂灌注,然后在烘箱中进行高压釜 (OOA) 外固化(参见“高速、自动化航空航天 RTM 生产线提供下一代扰流板”和“更新:下机翼”皮肤,明日之翼”。)
第二种是热塑性复合材料 (TPC),例如,在 Clean Sky 2 多功能机身演示器 (MFFD) 中,使用自动纤维放置创建硬化蒙皮——上半部分原位固结,下半部分采用高压釜固结一半 - 然后通过焊接组装。这些程序使用自动化来提高生产率和质量,同时降低成本。但它们如何比较?
德国航空航天中心 (DLR) 结构与设计研究所在奥格斯堡运营着轻量化生产技术中心 (ZLP)。在众多复合材料制造项目中,PROTEC NSR 和 Fast Lane RPB 提供了一个独特的机会,可以分别比较双通道空客 A350 的液态成型热固性后压舱壁 (RPB) 与单通道空客的热塑性 RPB A320。这两个项目都与这些结构的一级供应商 Premium Aerotec Group(德国奥格斯堡 PAG)合作,并在评估周期时间和成本的同时展示了自动化。
液态成型 TS 隔板
“多年前,我们在 AZIMUT 项目中与 PAG 合作,分析复合材料制造的手动流程,”ZLP Augsburg 组装和连接技术主管 Lars Larsen 博士说。 “我们的第一个自动化解决方案是用于上层,然后我们致力于实现更多操作的自动化。” DLR PROTEC NSR 项目经理 Marcin Malecha 博士解释说,PROTEC NSR 的主要目标是将这些用于 RPB 生产的专业解决方案纳入单一自动化流程。
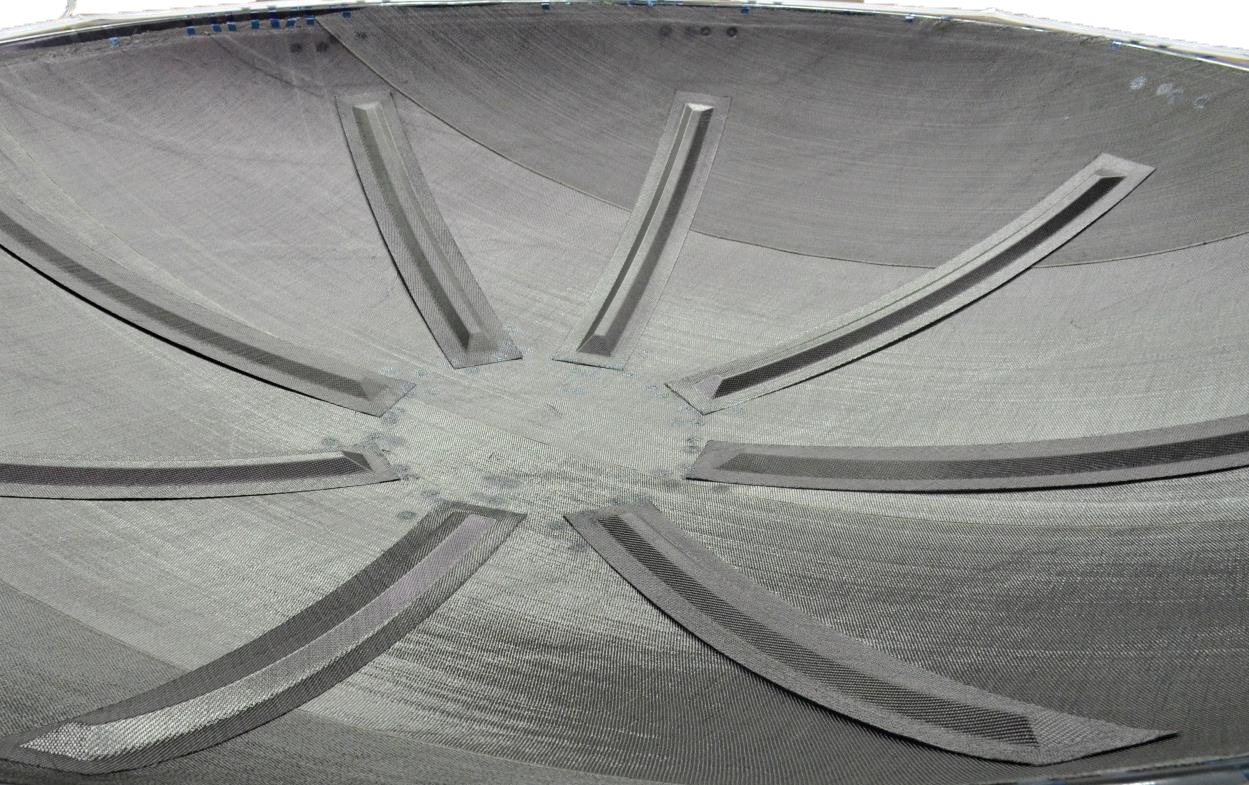
瓶坯和夹具。 创建真空袋装干燥瓶坯的工艺步骤如下图 1 所示。使用空客专利的真空辅助工艺 (VAP) 注入 RTM6 环氧树脂,该工艺采用半透膜来降低孔隙率。预成型叠层包括两组 16 层,最长 5 米,使用 5 线缎碳纤维织物全长 1.27 米。嵌入在这两组之间的是 25 个形状复杂的加强件,尺寸可达 1.5 x 2.5 米。顶部放置了八根纵梁。
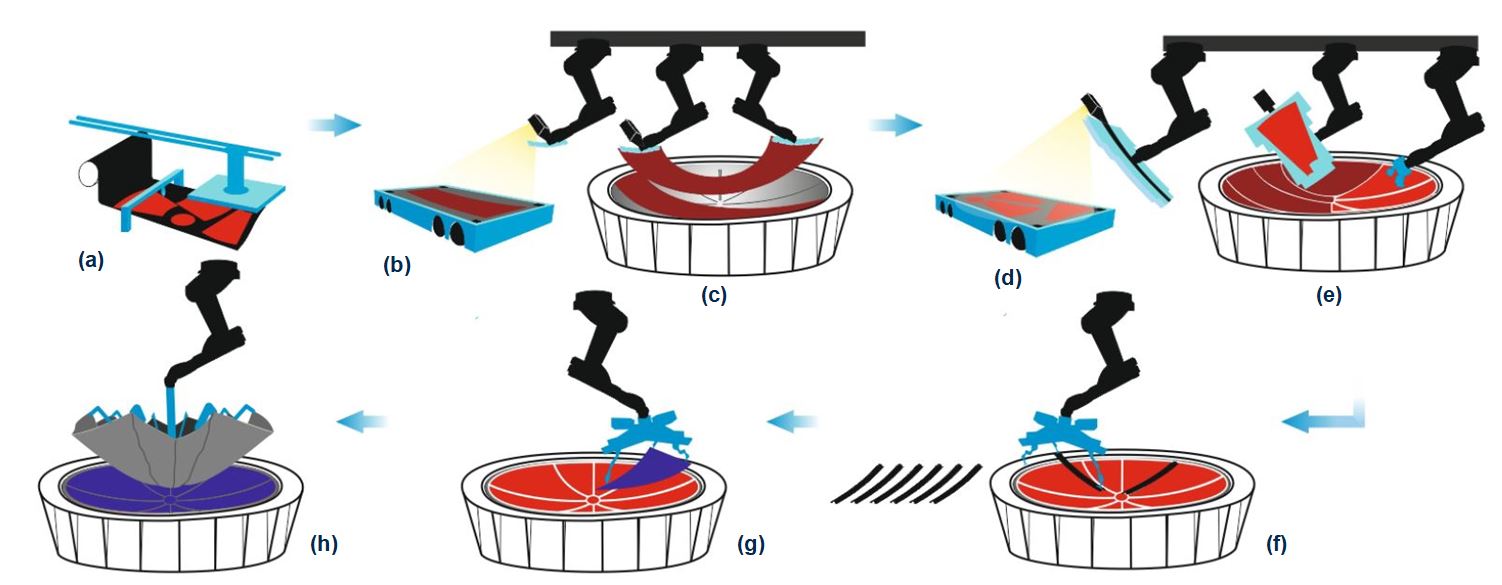
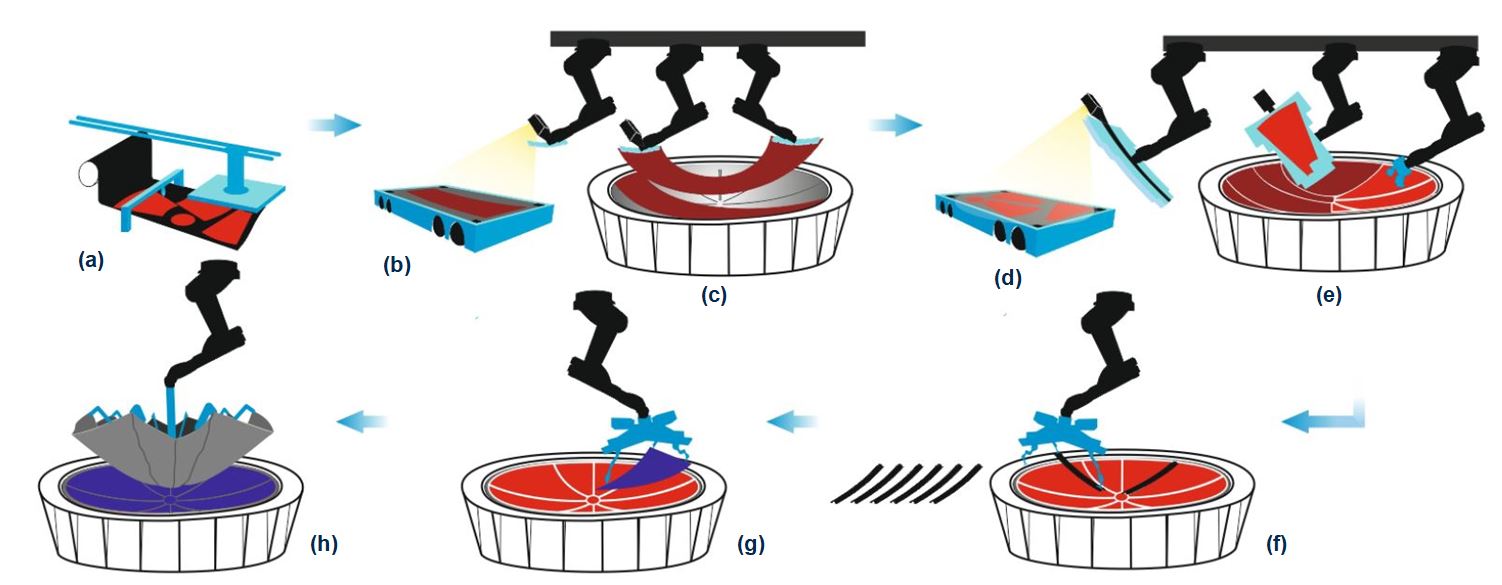
“开发能够在悬垂和处理方面达到必要精度的工具和夹具是最大的挑战之一,”拉森指出。这部分是由于需要三种不同悬垂机制的复杂层混合:
- 直接从必须适应模具形状的卷筒应用全幅材料。
- 大切割结构层的悬垂 两个机器人协作,每个织物边缘一个,以拾取和创建模具的目标几何形状 确保贴合前无皱折。
- 适用于最大 1.5 x 2.5 米的小型异形层 .
“对于协作机器人,我们开发了包含六个通过球形关节连接的模块的末端执行器,”Larsen 解释说。 “这允许末端执行器以类似于蛇的方式变形,符合模具的目标几何形状。集成加热装置在织物运输和成型时激活织物中的粘合剂,一旦放置就保持其 3D 形状和位置。”
自动悬垂和放置
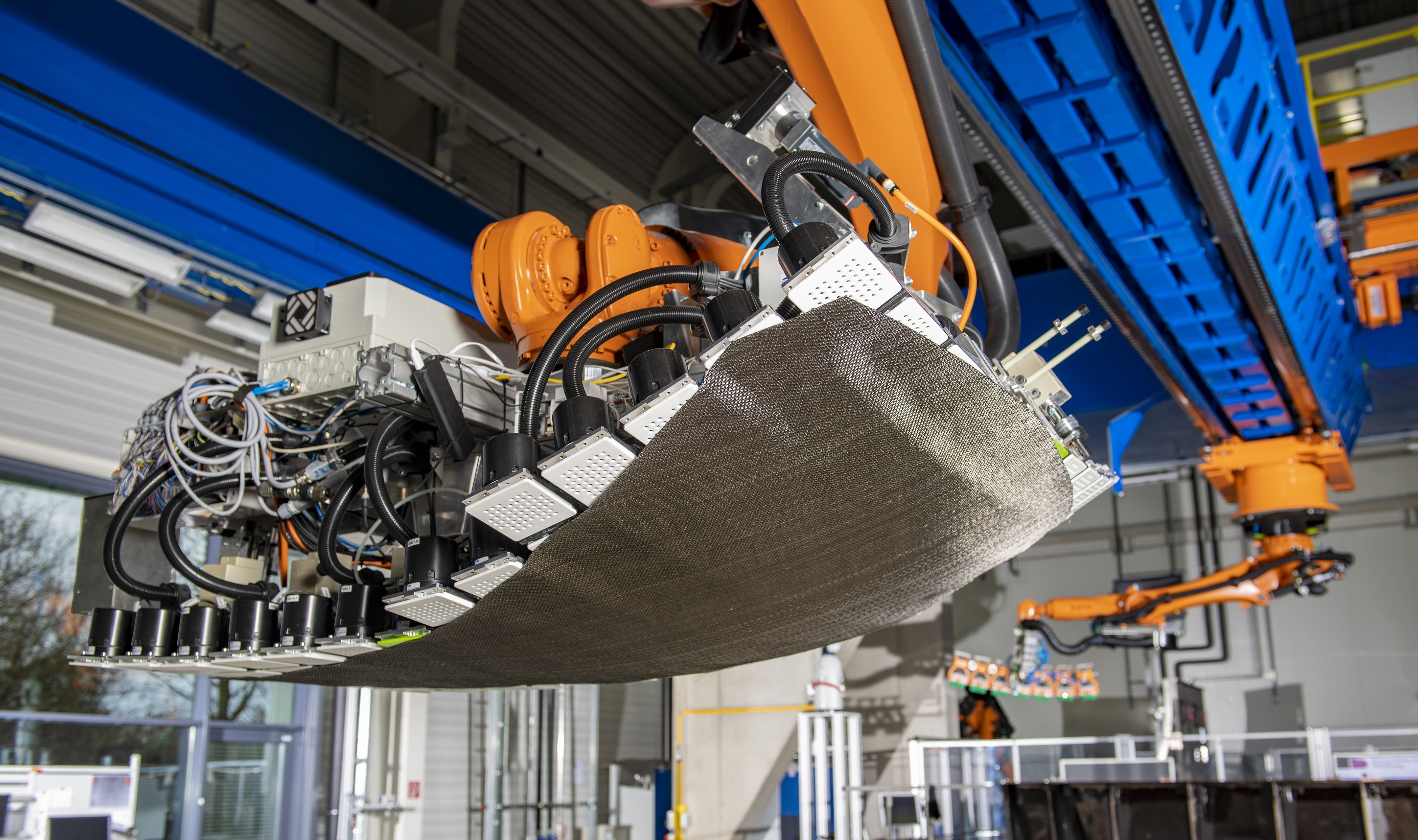
末端执行器具有一个夹具,它使用 127 个配备真空吸力的模块来拾取切割的织物层,然后转换成 3D 形状,然后在放入模具之前对其进行加热。图片来源:德国航空航天中心 (DLR) 结构与设计研究所
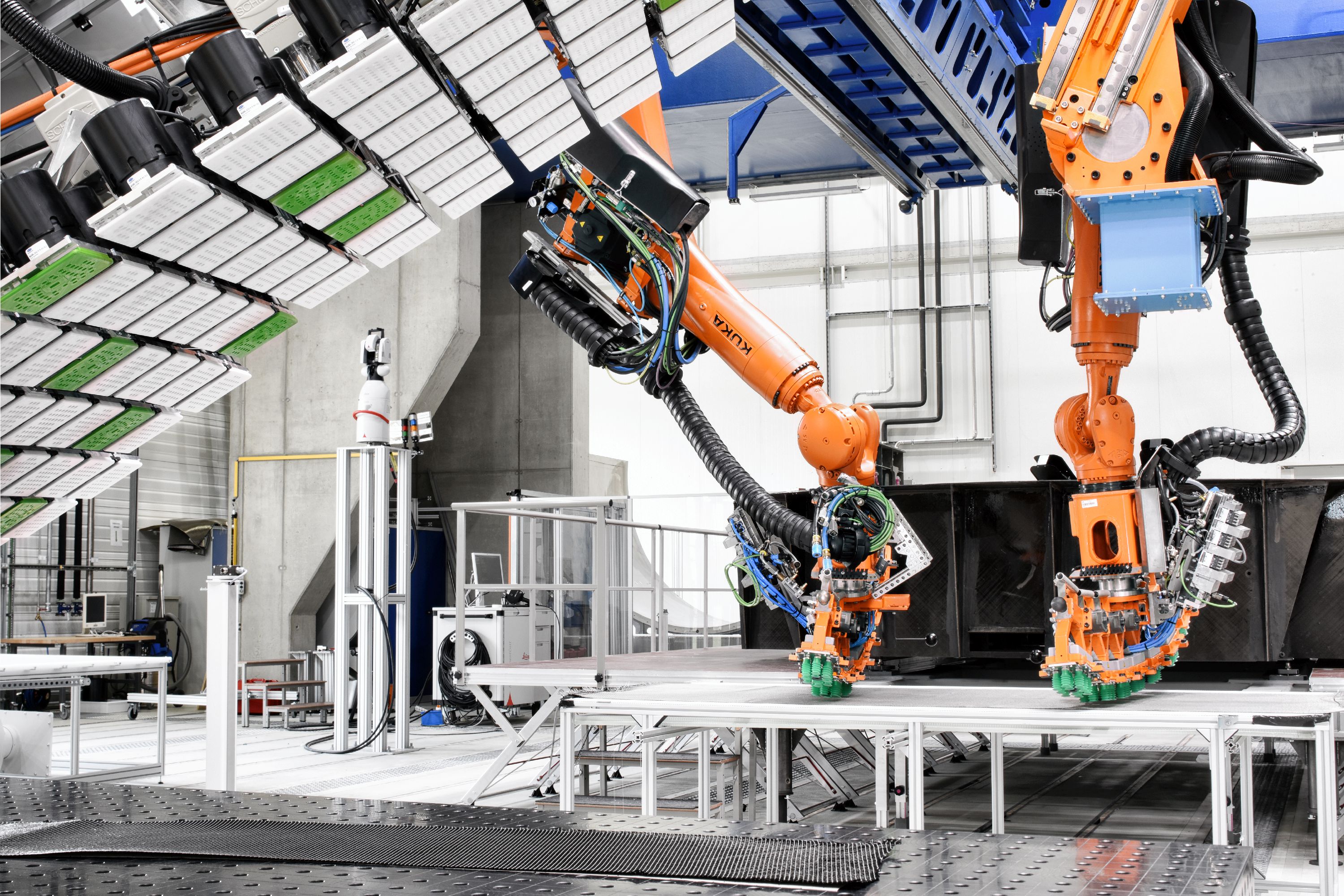
在这里,可以看到 127 个模块的抓手(左)和协作机器人(背景)。图片来源:德国航空航天中心 (DLR) 结构与设计研究所
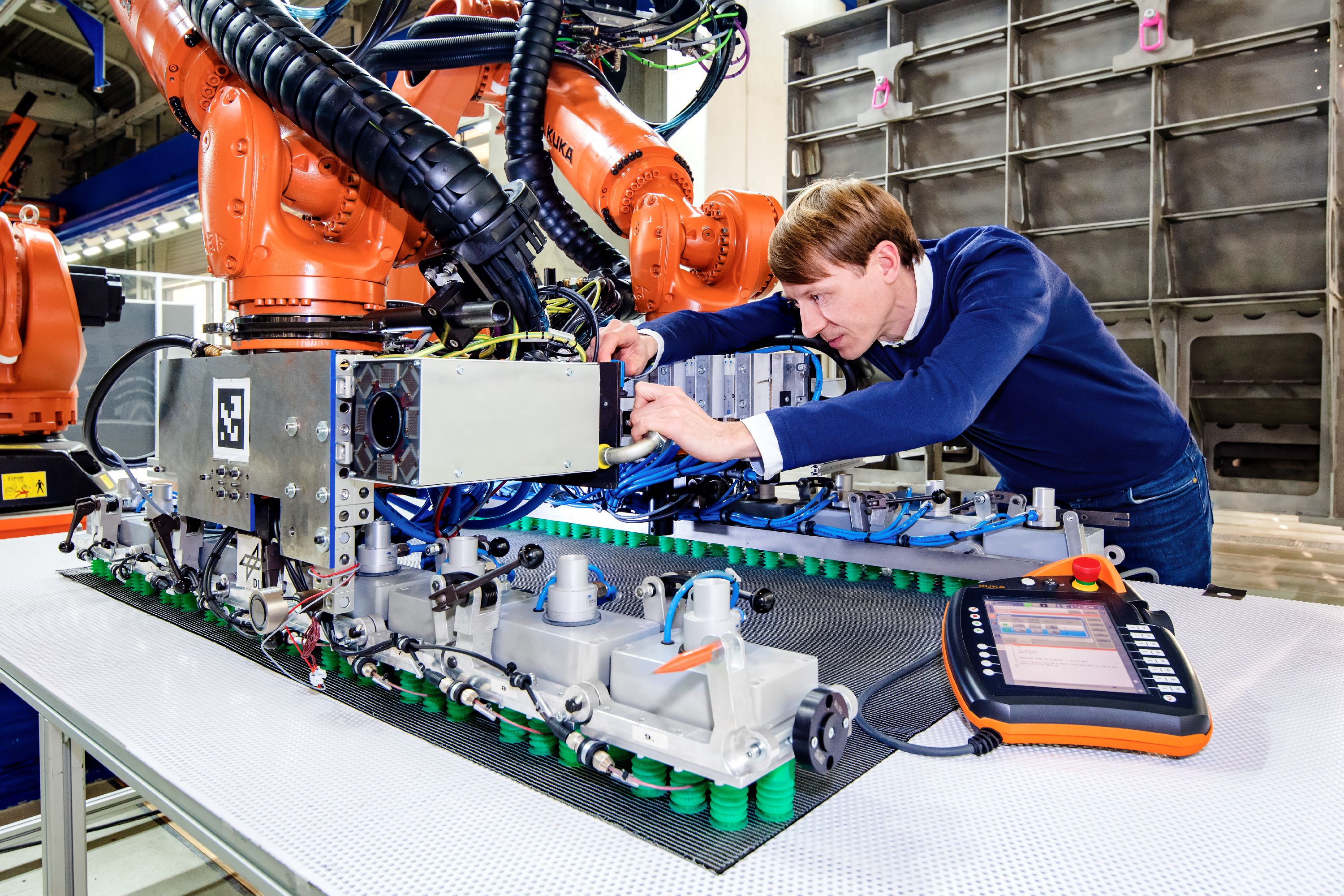
对于协作机器人,开发了包含六个通过球形关节连接的模块的末端执行器。图片来源:德国航空航天中心 (DLR) 结构与设计研究所

每个机器人都会捡起大织物层的边缘。然后,在将织物放入模具之前,他们一起运输层片以创建所需的目标几何形状。图片来源:德国航空航天中心 (DLR) 结构与设计研究所
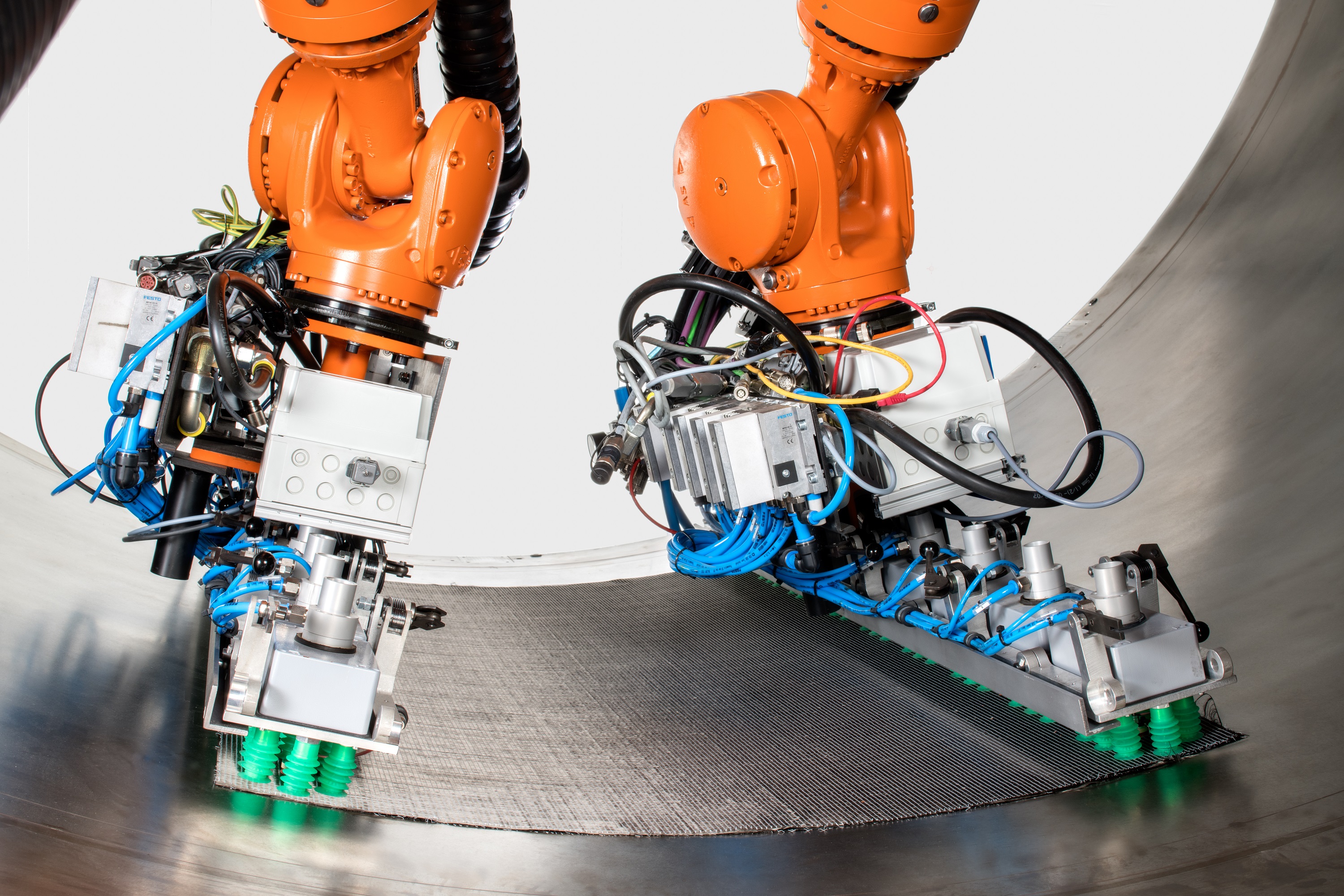
图片来源:德国航空航天中心 (DLR) 结构与设计研究所
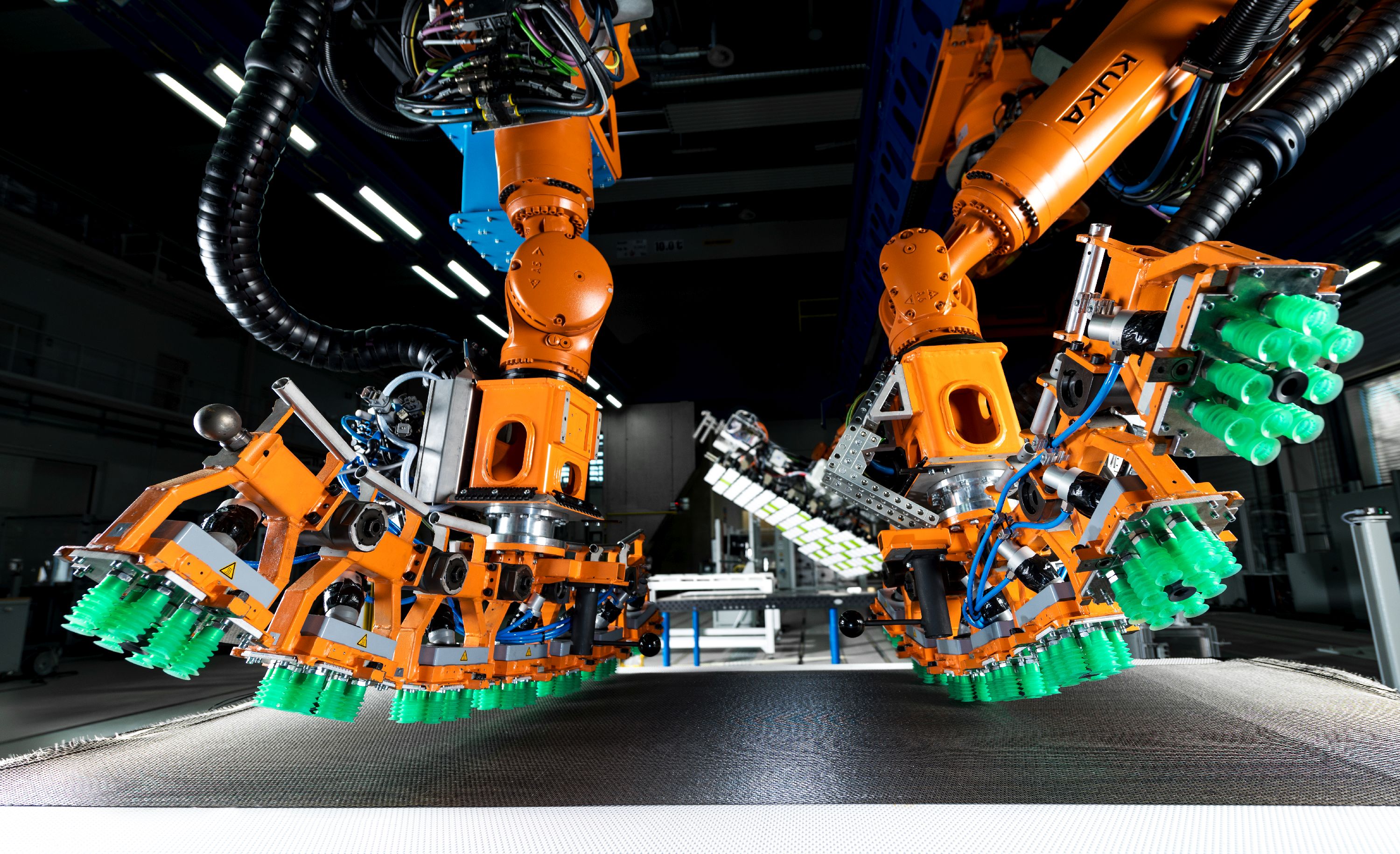
协作机器人末端执行器的特写。图片来源:德国航空航天中心 (DLR) 结构与设计研究所
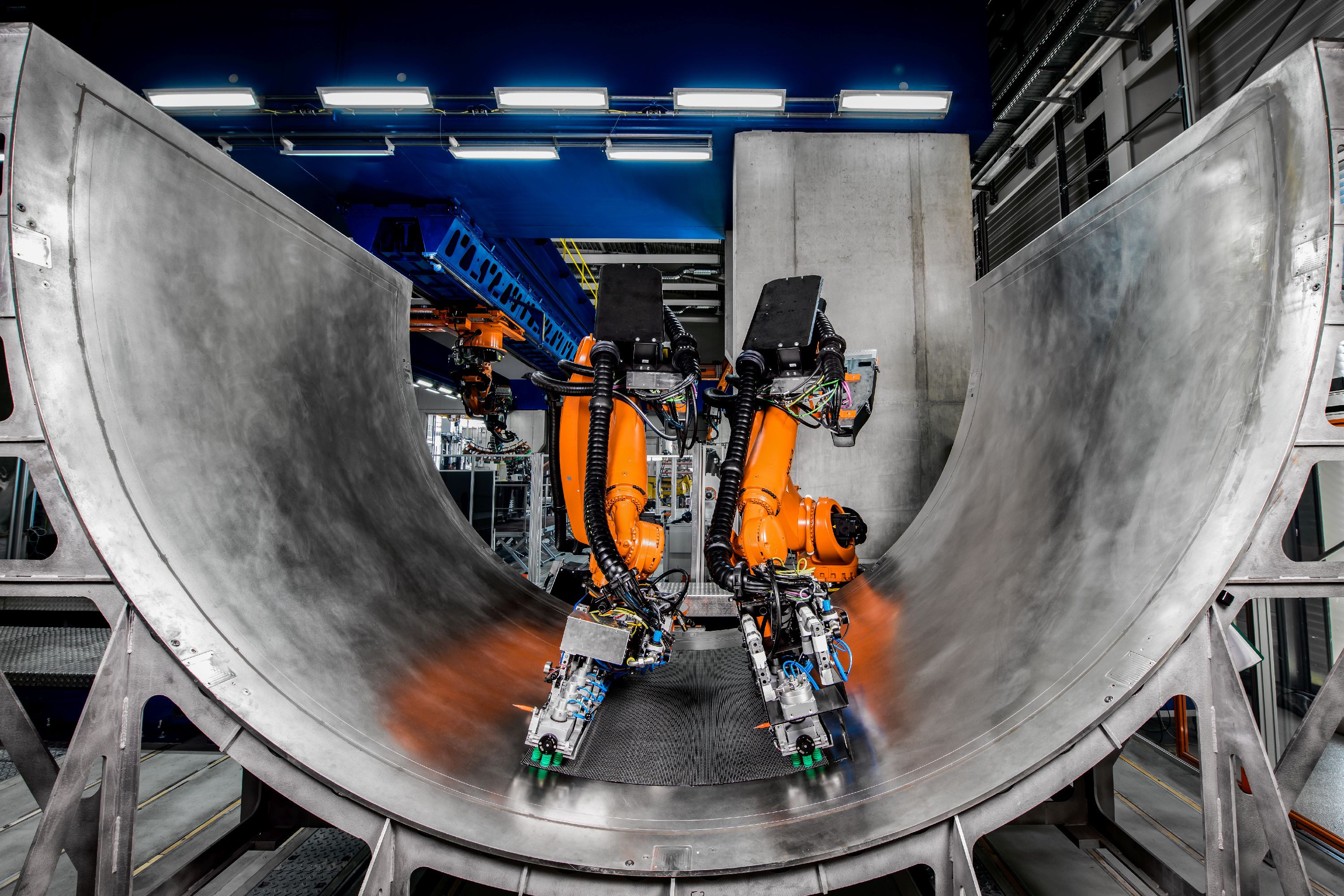
DLR 最初为 A320 后压舱壁开发的这个系统现在也已在机身面板上进行了演示,根据他们的数字设计文件,该系统旨在灵活用于各种大型飞机结构,而无需重新教授机器人。图片来源:德国航空航天中心 (DLR) 结构与设计研究所
上一页下一页对于小的成型层 高达 1.5 x 2.5 米,开发了第二种夹具,它使用 127 个配备真空吸力的模块进行拾取。 “这个夹具在 2D 状态下拾取材料,然后将其弯曲到目标几何形状,”Malecha 解释说。 “它必须决定将 127 个模块中的哪个模块固定住,哪个模块可以滑动以将 2D 层片转换为 3D 形状。因此,它与手的工作方式非常相似。我们做了很多实验,积累了在哪里持有和释放的经验。可以通过模块对材料的夹持强度来调整力。”
在线检查。 模块化夹具中的光学传感器监控悬垂过程。放置层后,末端执行器结合 Leica T-Scan(Hexagon Manufacturing,Cobham,英国)和 Profactor(奥地利斯太尔)基于相机的光纤角度测量系统进行质量检查。 “我们首先测量了纤维角度并与 CAD 文件进行了比较,”Malecha 说,“然后我们测量了每块的边缘,并根据 CAD 文件检查了它的位置。”
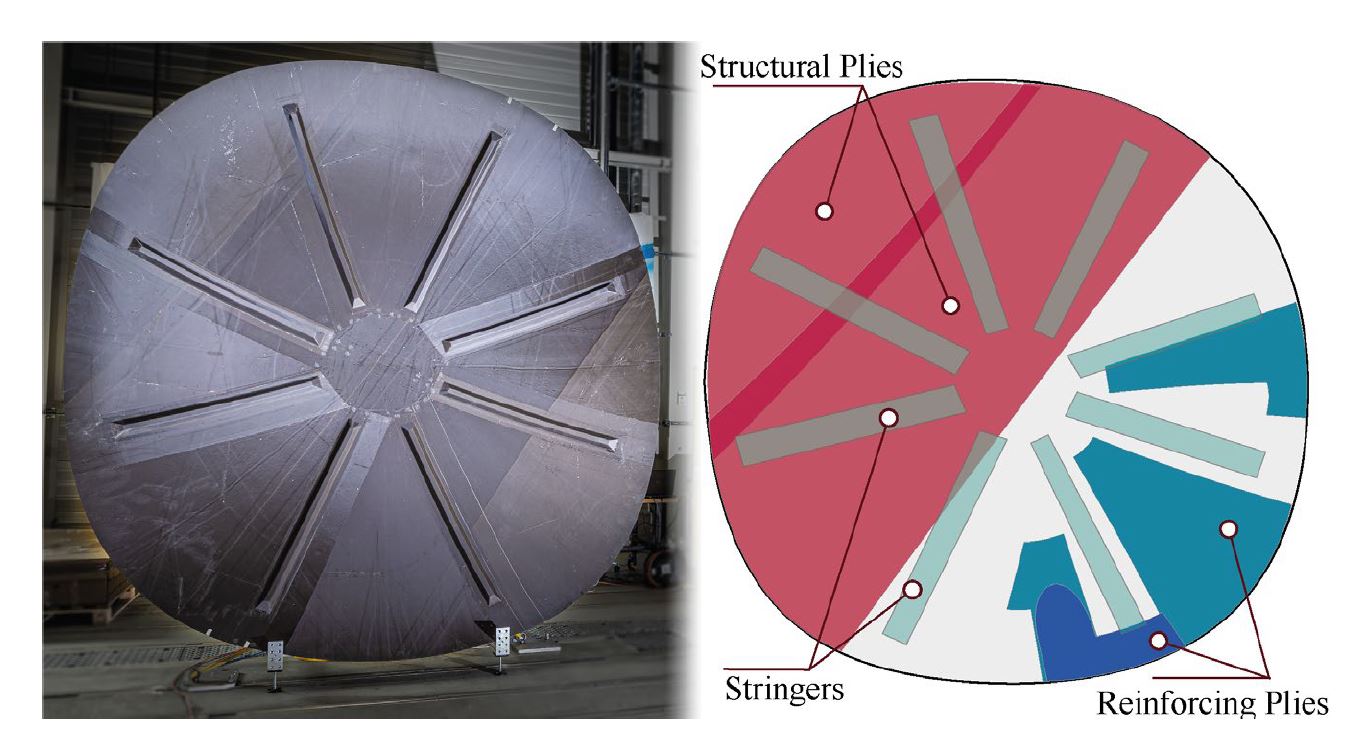
纵梁和真空袋。 完成预制件后,顶部连接了八个加强筋(纵梁)。为此,开发了多运动夹持器,并用于应用真空袋辅助材料。该夹具包括三个独立的小型 6 自由度 (DOF) 机器人和一个刚性臂,全部安装在工业 6 自由度机器人的中心法兰上。真空袋装辅助材料——剥离层、穿孔离型膜和树脂流动介质(工具侧辅助材料)——经过预切割和预连接,专为它们的放置位置而设计。 “它们不必披上,只需放置即可,”Malecha 指出。预制的半透膜通过带有“伞状”机构的末端执行器以半自动化的方式应用,而粘性胶带和外部真空袋的放置仍然是手动的,但也可以自动化。
周期时间和成本。 对于 Malecha 来说,最大的挑战是构建基于模块化、人工智能 (AI) 的制造执行系统 (MES) 来监控和控制流程链。 “我们必须构建数据管理系统,将完全不同的流程整合在一起,然后通过 MES 通过一个数据交换端口对它们进行命令,”他解释说。 “我们可以根据需要随时使用它们,与遵循严格的制造订单相比,可以实现更大的灵活性和更广泛的用途。”
PROTEC NSR 技术于 2019 年 1 月通过制造全尺寸演示器进行验证,并在 2019 年年中达到 TRL 5-6 的成熟度水平。与 PAG 目前的最先进技术相比,这种自动化工艺链将卷布应用的周期时间缩短了 58%,并将裁剪层的取放时间缩短了 50%。这些操作的制造成本分别降低了 11.5% 和 31%。
热塑性RPB
“该项目于 2018 年与 PAG 和 Institut für Verbundwerkstoffe(IVW,Kaiserslautern,德国)开始,旨在展示热塑性复合材料在大型零件和主要结构中的可能性,”Fast Lane RPB 项目经理兼专家 Stefan Jarka 博士解释说ZLP 奥格斯堡的焊接技术。 “RPB 并不是真正主要的,因为机械要求没有机翼或机身那么高,但它展示了大型、平坦、略微弯曲的结构的可能性。在短短四个月内,我们开发了一个演示器 A320 RPB,作为如何将现有铝结构转换为热塑性复合材料的示例。”
该演示器使用 Cetex 碳纤维 (CF) 织物/聚苯硫醚 (PPS) 有机片材(Toray Advanced Composites,Nijverdal,Netherlands)和电阻焊。被焊接的两个表面之间的电阻元件产生热量并保留在焊接结构中。 GKN Fokker(荷兰 Hoogeveen)几十年来一直使用这种技术来生产飞机起落架门和固定前缘。对于这款 A320 RPB,ZLP 团队使用 CF 电阻元件代替传统的不锈钢网。
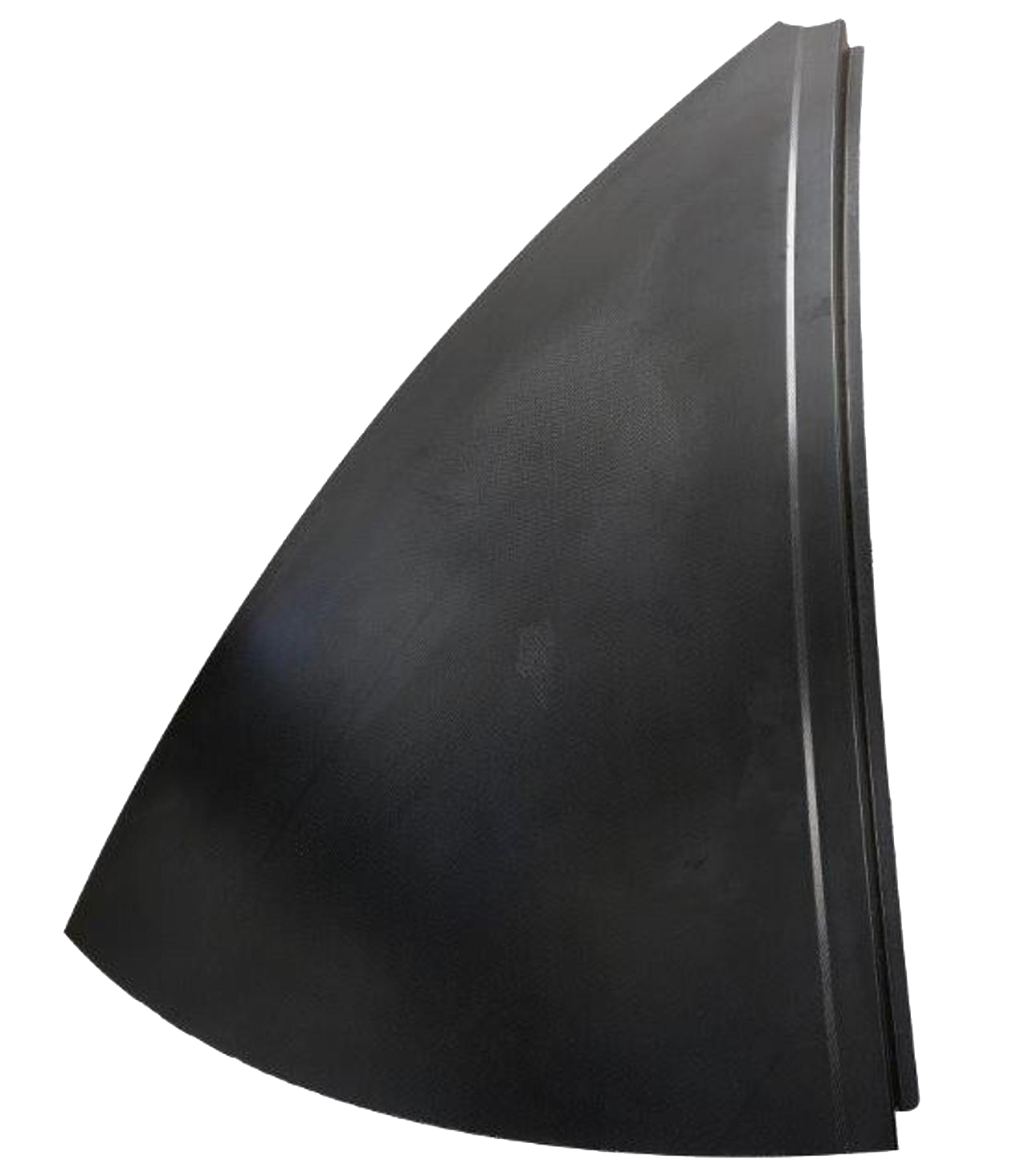
“热塑性复合材料 RPB 的价格相同或更便宜,但材料要贵得多,”拉森指出。因此,由于自动化而降低生产成本是关键,因为使用八个相同的花瓣部分也是如此。 “需要这些部分来形成零件的双曲线形状,”Jarka 解释说。 “热成型作为一个单一部件需要非常大的压力机,这太昂贵了。因此,IVW 使用匹配的金属工具对八个较小的部分进行了压制成型,然后我们使用自动焊接进行了组装。热塑性塑料压制成型的自动化水平高于热固性复合材料。您主要使用匹配的金属模具,高温但恒定的温度是主要问题,但这也使得自动化冲压周期非常快。”
演示器 RPB 的整体工艺步骤如图 2 所示。“我们使用的焊接工艺并不新鲜,”Jarka 说,“但必须进一步开发以连接 1.5 米长 [和 40 毫米- 3米直径部分的宽]接缝并集成质量检测系统。首先使用定位夹具将部件固定到正确的位置,然后施加电能以在焊接区产生塑料熔体。”
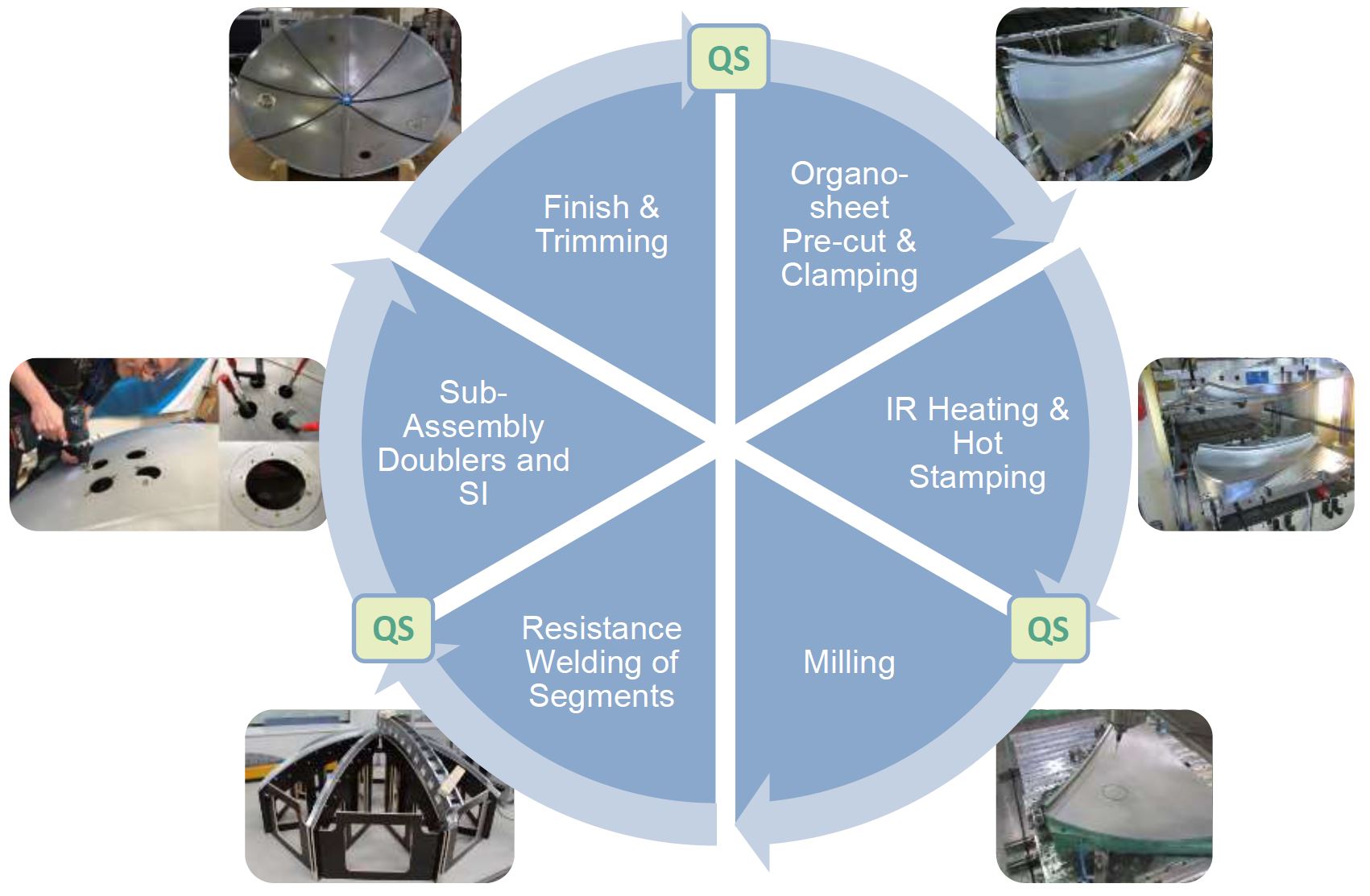
图。 2. 热塑性RPB工艺步骤
用于生产冲压成型的 CF/PPS 有机片材的八个部分(底部)的工艺步骤,然后通过电阻焊接将它们连接起来形成演示器 A320 隔板。图片来源:德国航空航天中心 (DLR) 结构与设计研究所
整合质量保证。 “我们尝试了闪光灯和超声波激活的热成像,但用它来测量焊接区域并不容易,”Jarka 解释说。 “热成像非常快,但它并不能轻易告诉你是否有良好的整合。”相反,他们使用标准测试台制作多个焊接样品,测量电流、电压和温度。 “然后我们用超声波检测 (UT) 对它们进行了检查,并在工艺参数和良好的固结度之间建立了相关性,”Larsen 说。 “如果我们有好的参数,那么我们就有一个好的部分。我们还建立了一个过程模拟,将我们在焊接过程中获得的数据与我们建立的初始基线进行比较。”
自动化和循环时间。 “在汽车零部件的规模上,整个过程非常快,”Jarka 说。 “我们在 2019 年的审查中达到了 TRL 3,并且已经成熟到 TRL 4。我们将在 2021 年底达到 TRL 6。”在大流行之前,PAG 曾表示将在 2021 年之前将热塑性 RPB 投入生产。尽管未来不太明朗,但热塑性 RPB 仍被视为能够实现“明天的机身”,将重量从 41 公斤减至 35 公斤,加工组装时间缩短 75%,整体零件成本降低 10% 以上。
比较 TS 和 TP 复合材料
“热塑性塑料工艺速度非常快,与铝相比,您可以更便宜,甚至可以满足每月 100 架飞机的生产速度,”Jarka 说。 “RPB 既适用于热塑性焊接,也适用于自动化,”Malecha 说。 “干纤维、液体成型 RPB 的自动化成本更高。”
“但这种自动化很有趣,因为您可以通过仅自动化一些子流程来获得真正的收益,”Larsen 说。 “例如,通过自动化辅助设备,我们可以在大约一个小时内完成真空装袋,大约比手动过程快 10 倍。”然而,他承认成本是实施这种改进的主要障碍。 “数字工具、机器人和开发的成本对于 RPB 等单个部件来说太高了。但是,如果我们可以开发一种模块化方法,您可以将这个系统用于许多零件,那么这种成本可以分摊得更广,在计算时可以减少时间和劳动力。” ZLP 确实做到了这一点,正如 CW 中所述 2020 年 7 月的专题:“复合材料 4.0:数字化转型、自适应生产、新范式。”
“热固性和热塑性复合材料结构之间的比较还不多,”Malecha 说。 “但我们开始比较热固性和热塑性工艺。”他指出,下一个目标是证明热塑性熔接线具有飞机机翼和机身所需的特性。例如,大型集成液体模制机翼也必须表现出这种性能。这正是 MFFD 和 WOT 计划旨在实现的目标。我们正在等待他们以及许多其他 Clean Sky 2 和 EC 项目的结果,以展示下一步的进展。
树脂