证明多功能机身演示器的 LM PAEK 焊接
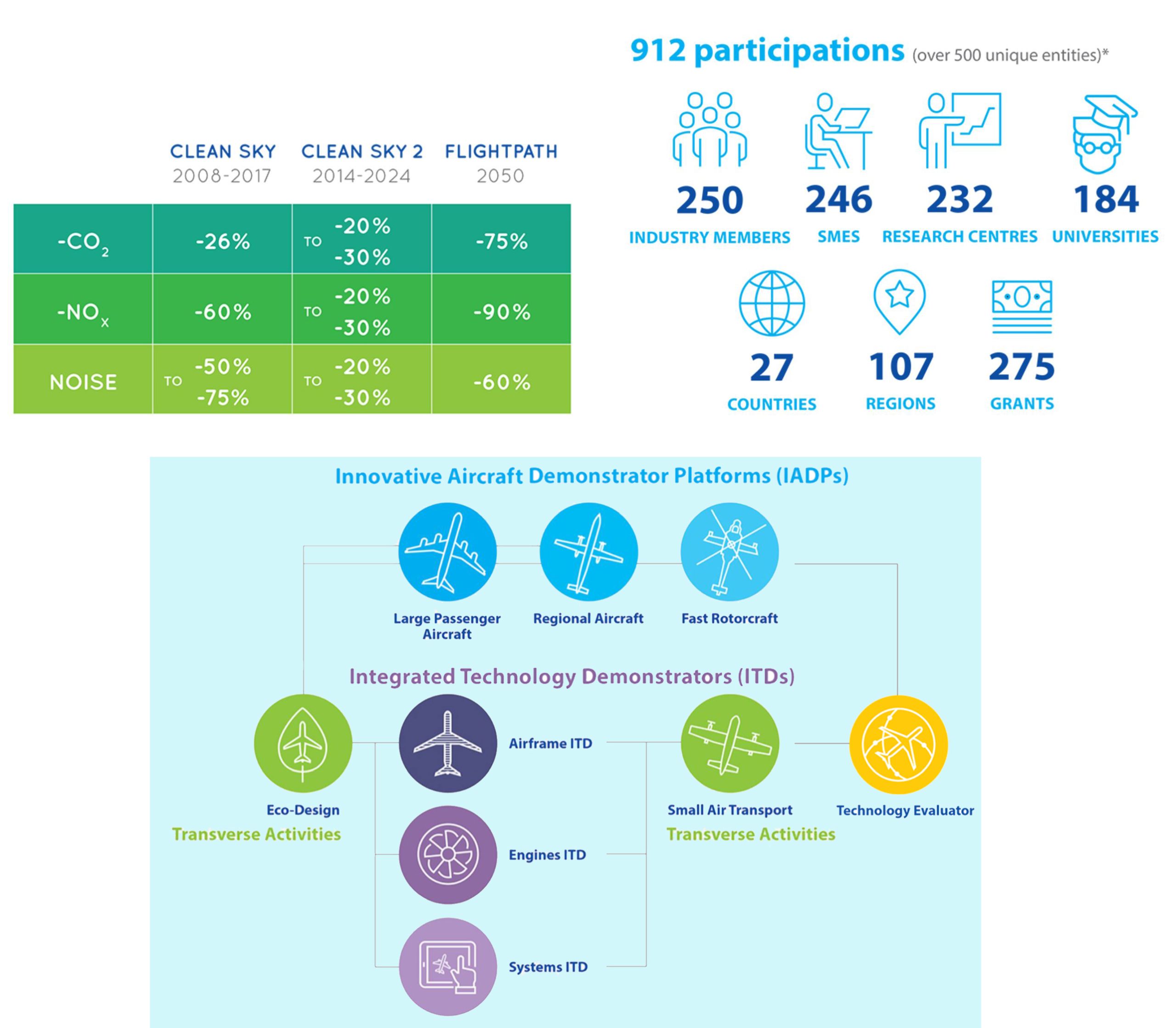
这种类型的航空研究始于欧盟委员会框架计划 (FP) 的研发资金,涵盖 FP2 (1987-1991) 到 FP7 (2007-2013)。这些项目极大地促进了各种技术的成熟,使其达到技术准备水平 (TRL) 6 并在空中客车 A350 等飞机上实施。
Clean Sky 2 的不同之处之一是它围绕大型示威者的组织。 MFFD 是在大型客机 (LPA) 创新飞机演示平台 (IADP) 中生产的三个全尺寸机身部分之一(见上图蓝色方块顶部的蓝色文字) .在 LPA IAPD 内有三个平台。 MFFD 位于“创新物理集成客舱-系统-结构”平台 2 内,该平台具有另外两个大型演示器。
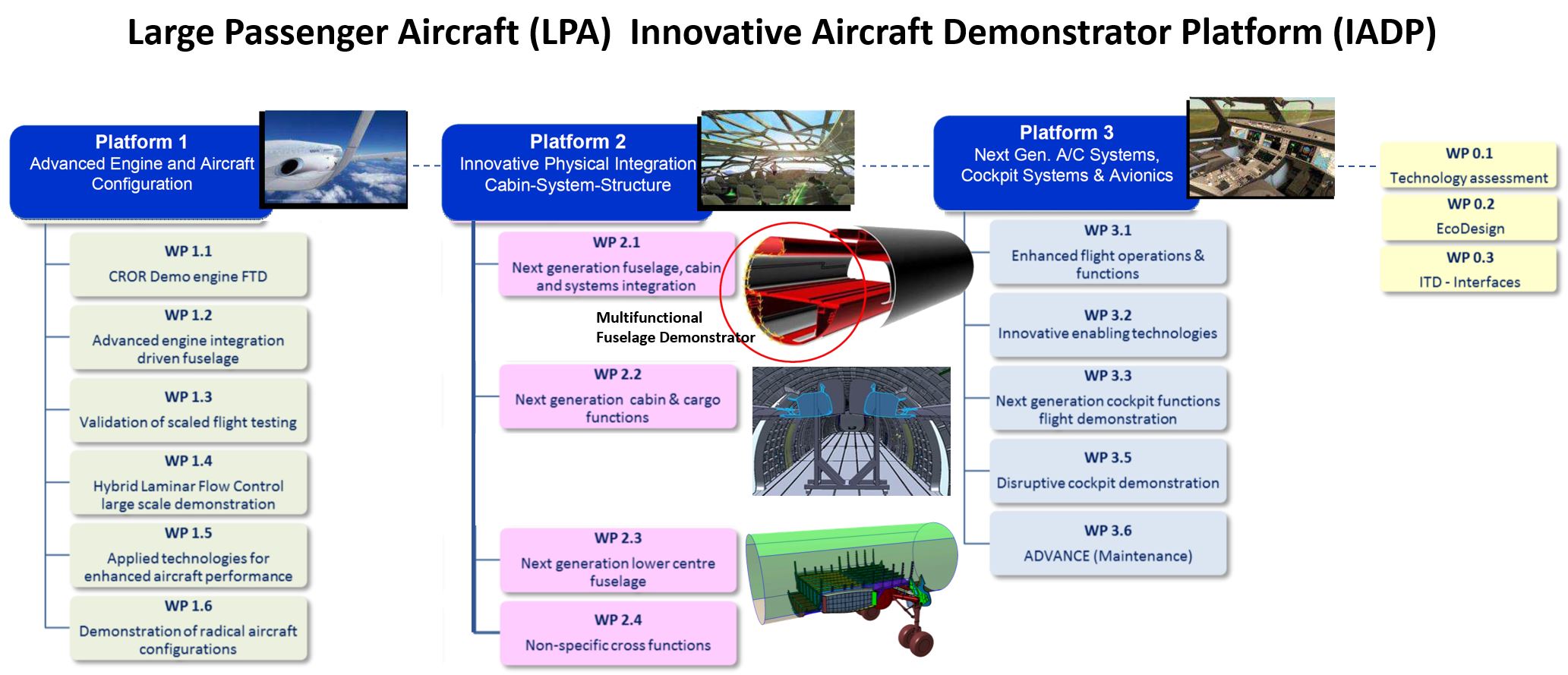
为了理解这意味着什么,我回顾了西班牙赫塔菲的空客机身研究与技术 (R&T) 工程师在 2015 年研究多功能复合材料时告诉我的话。他们说,本质上,“我们不再想要重复和制作外筒和内筒的浪费;我们希望将结构机身与机舱系统整合在一起。”我很难想象这意味着什么——直到我看到了 MFFD 的草图。
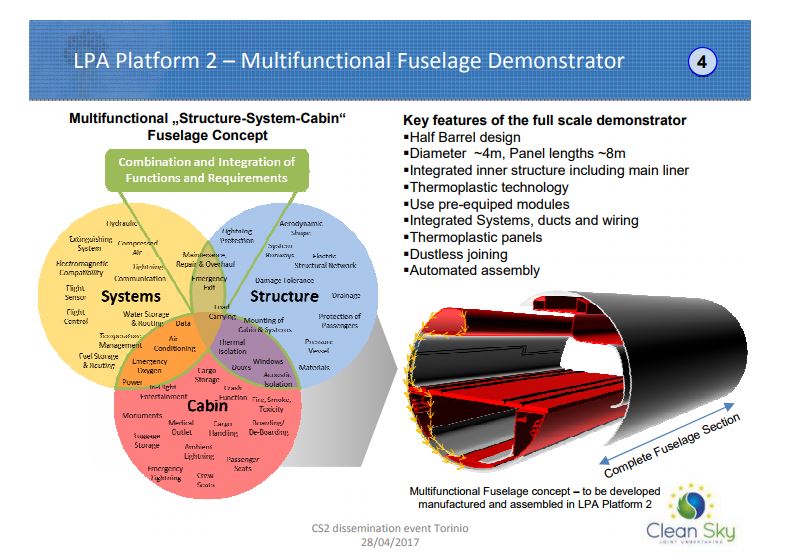
来源 | Clean Sky 2 (CS2) 传播和“热塑性复合材料演示器——欧盟未来机身路线图”。
“模块化、集成和创建通用平台是关键,”空中客车运营有限公司(德国不来梅)机身 R&T 典型机身、MFFD 计划负责人 Ralf Herrmann 说。我在此处引用 Clean Sky 2 网站上的 MFFD 页面:
Herrmann:“我们早就知道,在使用热塑性复合材料时,减轻重量和降低飞机生产经常性成本的好处 ——只能通过多个学科的融合来实现。这意味着只关注结构 无法充分发挥复合材料技术的优势。”
根据 Clean Sky 2 项目官员 Paolo Trinchieri 的说法,热塑性塑料的多功能性需要与设计方法相结合:“有必要消除功能的人为分离 在飞机预设计阶段,并在一开始就计划飞机制造、组装和安装的高生产率。”
Herrmann 之前是 FP7 项目 MAAXIMUS(通过扩展、集成和成熟的数字尺寸实现更实惠的飞机结构)的项目经理。从 2008 年 4 月到 2016 年 9 月,MAAXIMUS 包括 60 个合作伙伴,旨在展示高度优化的复合机身的快速开发和一次成功验证——通过同时成熟的虚拟和物理推动因素——实现 50% 的组装时间减少大机身截面,经常性成本降低 10%,结构重量减轻 10%,开发周期缩短 20%。 MFFD 的目标可以看作是一个扩展:
- 实现 70-100 架飞机/月的生产率
- 将机身重量减轻 1,000 公斤
- 将经常性成本降低 20%。
一个关键的推动因素是无尘加入 (无孔,无紧固件)通过焊接热塑性复合材料组件。 Herrmann 解释说,当前的飞机制造顺序方法——机身结构必须相当完整,然后才能安装系统、机舱和货物功能——既耗时又“对故障敏感”。相反,MFFD 追求的是预先配备的、高度集成的结构元件和系统模块,它们可以在很早、甚至在最终组装之前很久就安装完毕。
改为纵向接头和LM PAEK
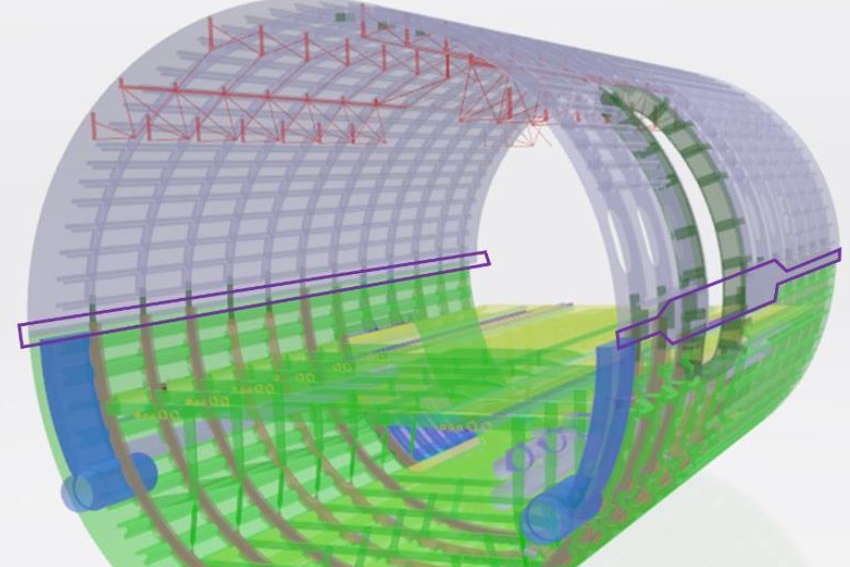
MFFD 项目活动于 2017 年开始。每年至少有一次提案征集 (CFP),其中项目负责人概述需要进一步发展的主题。如下图所示,CFP08(2018 年 4 月)中显示的偏置接头设计已被 CFP09(2018 年 9 月)更改为纵向接头。
“偏置接头提出了关于地板结构的可访问性和连接的问题,我们意识到在给定的时间范围内很难克服这些问题,”赫尔曼解释说。 “因此,我们决定退回到传统设计以降低风险。我们的主要兴趣是展示如何在主要组件组装 (MCA) 之前集成所有可以安装的系统和机舱元件。这也将是这种热塑性复合材料首次应用于大型客机的全尺寸主要机身结构。”
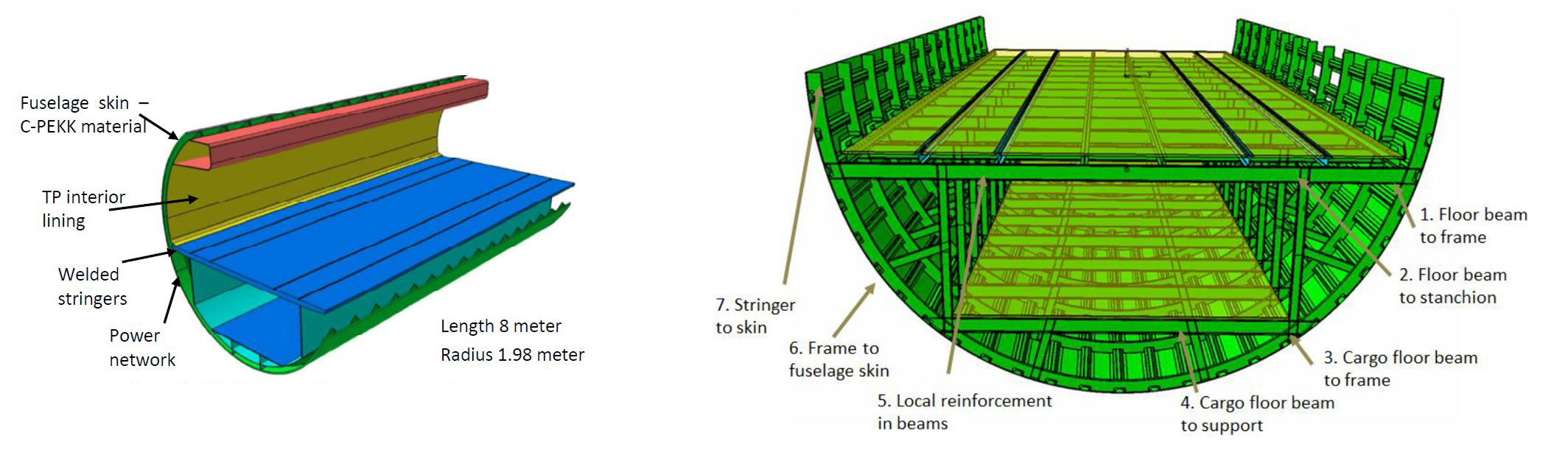
MFFD 设计在 2018 年从偏置接头设计变为更传统的纵向接头。SOURCE | CFP08 p.87(左)和 CFP09 p. 133(右)。
另一个变化是热塑性复合材料 (TPC) 基体材料。 CFP08 和 CFP09 中的 MFFD 主题是指碳纤维/PEKK(聚醚酮酮),但在 CFP10(2019 年 3 月)中,基准材料被描述为碳纤维和 PAEK(聚芳醚酮)。 PAEK 是包含 PEEK、PEKK 和 LM PAEK 的整个聚合物家族。
正如我在关于 PEEK 与 PEKK 与 PAEK 的博客中所述,Cetex 材料供应商 TenCate,现在是 Toray Advanced Composites,生产所有三种聚合物作为碳纤维增强胶带,并声称其性能基本相同。但是,Cetex TC1225 CF/LM PAEK 胶带在 305°C 熔化 而 TC1320 CF/PEKK 胶带在 340°C 熔化 .而且,根据 Toray Advanced Composites 全球首席技术官 Scott Unger 的说法,“LM PAEK 的流动性要好得多……而且可以以比 PEKK 和 PEEK 更高的速度进行加工。” TC1225 的成本也更低。
MFFD 下机身:令人惊叹的项目
STUNNING 是开发和制造装备齐全的 MFFD 下半部的项目名称。该项目旨在进一步成熟:
- 自动化组装流程
- 热塑性塑料制造和组装技术
- 集成设计和制造开发技术
- 开发先进的电气系统架构。
GKN Fokker(荷兰 Hoogeveen)项目经理兼 STUNNING 项目经理 Bas Veldman 解释说,MFFD 长 8 米,宽 4 米,半径为 2 到 2.5 米,这是单通道的真实规模A320 系列飞机。 “它类似于 A321,它不完全是圆形,而是大致呈蛋形(略高于宽度),”他补充道。
180°下机身部分将包括带有焊接纵梁和框架的下机身外壳、机舱和货舱地板结构以及相关的主要内部和系统元件。 “我们将提供大型、预装的模块,以实现非常快速的即插即用组装,”Veldman 说。
GKN Fokker 是 STUNNING 的主要合作伙伴,有四个部门参与其中,包括 Aerostructures(荷兰帕彭德雷赫特)、Fokker ELMO(荷兰胡格海德)、GKN Fokker Engineering 罗马尼亚(布加勒斯特)和 GKN Fokker Technologies(荷兰帕彭德雷赫特)。 GKN Fokker ELMO 是飞机线束和电气系统技术的供应商。 “它负责 STUNNING 的系统架构,并将专注于优化电气系统,”Veldman 解释说,“并与 CFP08 联盟 MISSION 合作开发创新的电源总线系统。”
“代傲航空(德国劳普海姆)负责内部结构,包括子系统和地板、侧壁面板及其连接方式、纪念碑接口和智能系统多端口,”Veldman 继续说道。 “NLR(阿姆斯特丹荷兰航空航天中心)负责制造机身蒙皮和纵梁,而代尔夫特理工大学则根据其在超声波焊接方面的专业知识协助组装。” (有关超声波焊接的更多信息,请参阅“焊接热塑性复合材料”。)
MECATESTERS 焊接测试程序
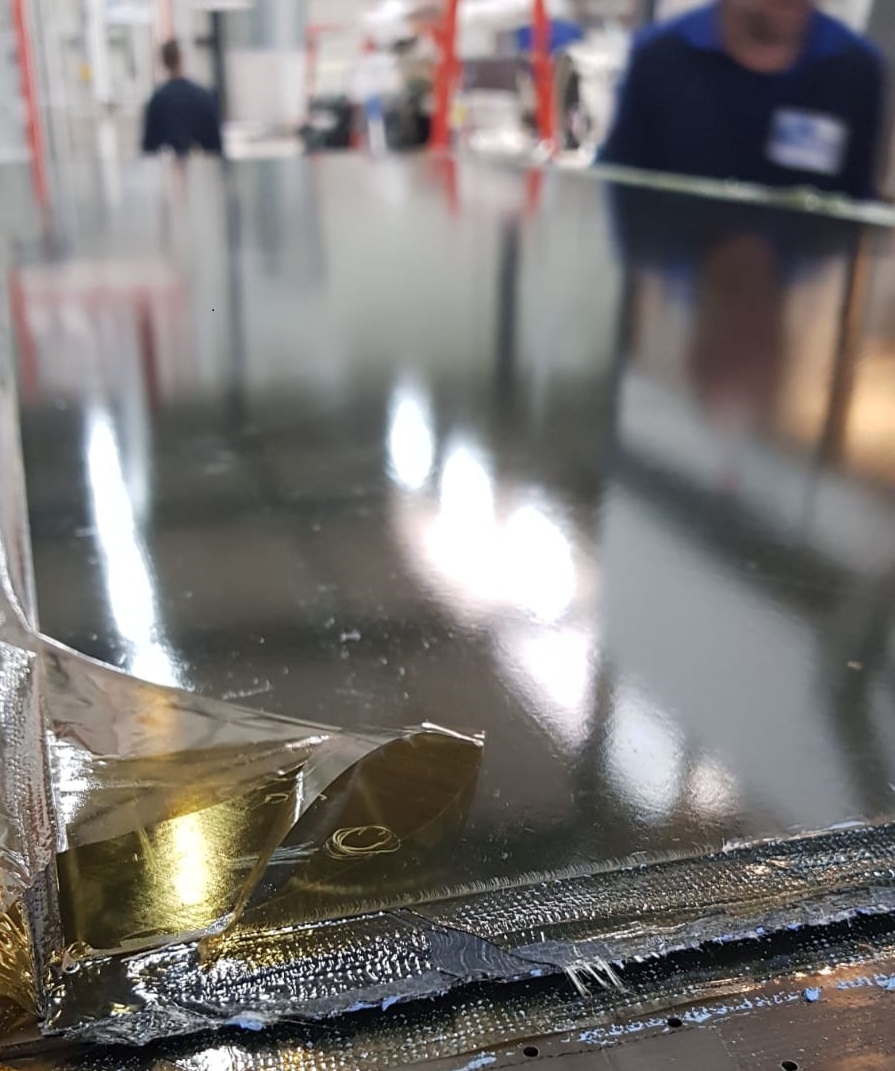
“STUNNING 推出了七个 CFP 主题,其中五个已经开始工作,包括 MAYA、MISSION、EMOTION、TCTool 和 MECATESTERS,”Veldman 说。后者是与 KVE Composites(荷兰海牙)和 Rescoll 合作的大型焊接测试程序 (法国佩萨克)于 2019 年 4 月开始,持续 30 个月。 Veldman 解释说,尽管 KVE 在织物和 UD 带热塑性复合材料的感应焊接方面有着悠久的历史,但迄今为止在飞机上飞行的感应焊接部件都使用了织物。 “在 STUNNING 中,我们正在建立 UD 增强材料和 LM PAEK 材料的最佳实践,并将感应焊接与典型使用负载和环境条件下的传导焊接进行比较。”尽管电阻焊和超声波焊接包含在其他 MFFD 工作包和 CFP 中(请参阅“加入两半 ”),感应焊和传导焊是MECATESTERS仅有的两种技术。
KVE 的 Labordus 解释说,对于三个 MECATESTERS 工作包(WP 1、2 和 3),KVE 将使用高压灭菌器固化的 TC1225 UD 碳纤维/LM PAEK 胶带制作所有测试层压板(参见“第一个 Toray LM-PAEK 层压板用于清洁天空 MECATESTERS 项目”)。 KVE 还将准备感应焊接样品进行测试,而 GKN Fokker 将生产传导焊接样品,而 Rescoll 将执行所有物理测试。 “Rescoll 这个名字来源于研究和拼贴,这是法语中的结合,”Labordus 说。 “他们以对所有类型粘合的研究而闻名,并为聚合物和复合材料提供了一个设备齐全的测试实验室,包括机械、环境、可燃性以及在航空航天、汽车、铁路和其他行业进行资格认证的所有可能的测试。”
工艺参数和测试
“我们实际上是从 WP 2 开始设置工艺参数,例如感应焊接温度和压力的上限和下限,”Labordus 说。 “例如,我们有一个名义 我们通常使用的压力,但我们会降低压力,直到我们开始看到像空隙这样的缺陷,然后我们将评估这些焊接特性以确定较低的压力边界。”测试还将评估焊接速度,这会影响焊接冷却速度和结晶度,并可能影响机械性能。 Fokker 将研究相同的传导焊接参数。
为了评估,MECATESTERS 程序将执行多项测试,包括:
- 根据 ASTM D5868–01 进行的剪切试验
- L 型材试样的拉断和剪切试验
- GIC 和 GIIC 分别符合 ISO 15024 和 ISO 15114
(这个韧性测试实际上会在WP 1中完成)
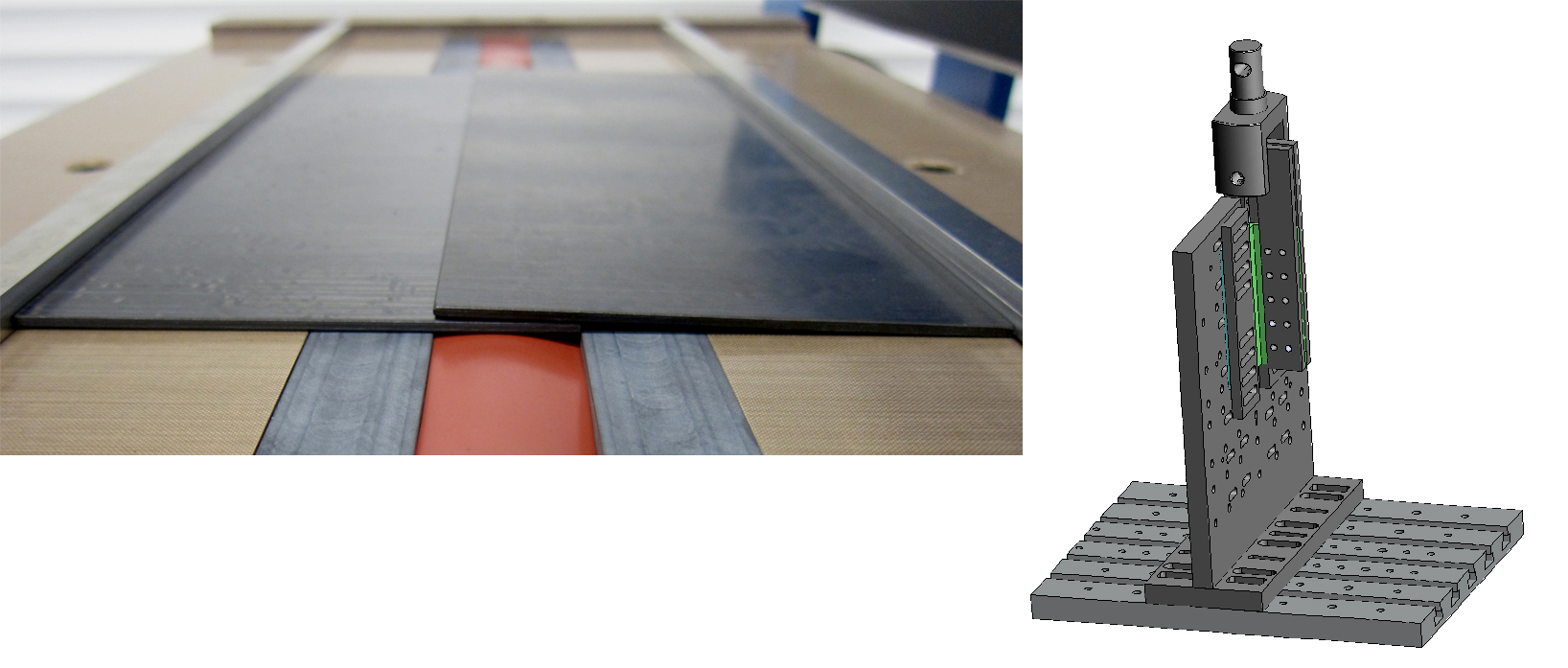
来自准备进行感应焊接的 UD 带层压板的单搭接剪切试样(左)和使用 Rescoll 开发的工具对焊接的 L 型材试样进行组合剪切和剥离测试的测试夹具(右)。来源 | KVE Composites, Rescoll.
“拉断测试方法来自 GKN Fokker 开发的内部标准,”Rescoll 工程师 Thomas Salat 解释说。 “对于剥离载荷,焊接型材的拉拔测试垂直于皮肤,”Labordus 指出,“并平行于剪切载荷的皮肤。剥离和剪切是两个极端,但我们还将测试反映实际使用中负载条件的这些新组合。”此测试将针对源自 MFFD 机身设计的两种不同层压板厚度(2.2 和 2.8 毫米)在室温 (RT)、低温 (-55°C) 和高温 (80°C) 下使用静态负载完成。
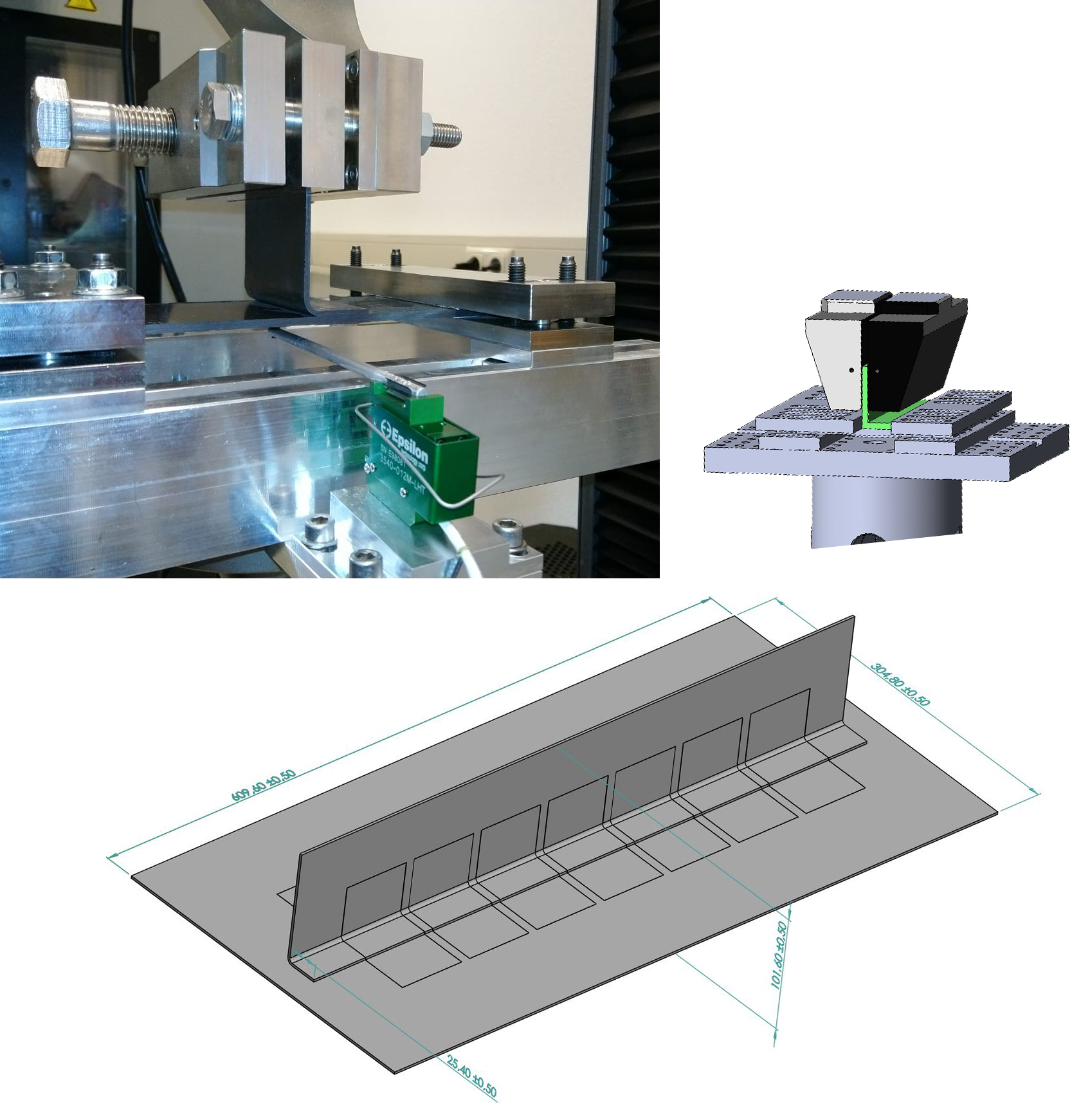
KVE Composites 对 L 型材试样的拉拔测试(左上)。在 MECATESTERS 中,这种类型的测试将使用 Rescoll 开发的夹具和测试装置来消除皮肤偏转(右上)。测试试样将从焊接面板(底部)上切割下来。来源 | Rescoll,KVE 复合材料。
表面准备、老化和疲劳
WP 1 将从韧性测试开始。 “对于裂化测试(GIC 和 GIIC),我们将在复合材料中产生裂纹并测量该裂纹在加载时的表现,”Salat 解释说。 “一个是静态测试,增加负载直到失败。我们还将进行动态测试,我们将静态负载重复一百万次,这需要一到两周的时间才能完成。我们将看看复合焊缝是否能承受这种疲劳。这种模式II是一种新的循环测试。我们正在开发一种取自欧洲大学发表的技术论文的方法,现在正在确定参数。”
同样在 WP 1 中,WP 2 中建立的焊接参数将用于检查表面处理以及老化和疲劳的影响。 “我们将研究表面污染物以及这些污染物如何影响焊缝,”Labordus 说。 “我们还将研究在印刷机和高压釜加工中常用的三种不同类型的脱模剂;特定类型的表面处理,包括打磨、研磨和等离子处理;并且还在被焊接的表面使用额外的树脂膜。此外,我们将研究纤维取向的影响,例如焊接界面处的正负45度。”
Salat 说,Rescoll 还将使用温度为 70°C 和湿度为 90% 的调节室来模拟使用中的老化。 “然后我们将进行标准测试,看看它是否会影响焊接性能。” Labordus 补充说,将在 100°C 和 120°C 下采集有限数量的样品,“以验证热塑性复合材料在 80°C 以上不会急剧下降的说法。”
除了动态裂化/GIIC 测试外,还将在单搭接剪切和拉断模式下进行疲劳测试。 “我们将从 80% 的静态失效载荷开始,然后在 100 万次循环中达到 50% 或 75% 的疲劳载荷,”Labordus 说。 “我们也会进行其他测试,但仍在讨论这些,”Salat 补充道。
焊接到短复合支架
虽然 WP 3 的细节仍在最终确定中,但它旨在研究由短纤维材料制成的压缩成型支架与 UD 层压板表皮的焊接。 “我们将再次对工艺参数进行基准测试并表征焊缝的机械性能,”Labordus 说,“但我们仍在努力定义用于测试的几何形状。”
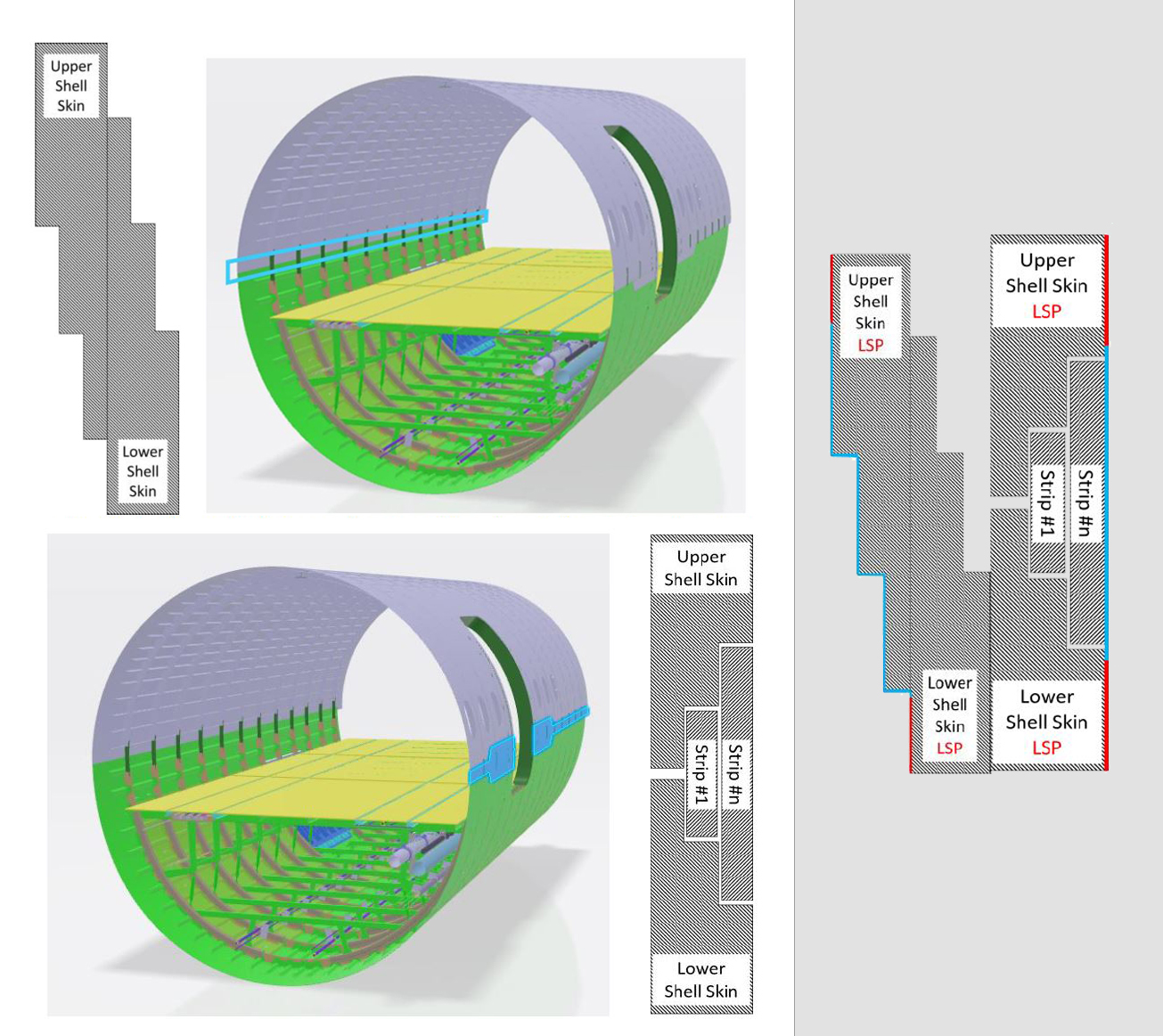
焊接到热塑性机身上的纵梁和夹子。来源:Clean Sky 2 11 th 提案征集 JTI-CS2-2020-CfP11-LPA-02-35,“用于长热塑性焊接接头的创新脱粘阻止功能”,图 2,第 1 页。 94.
焊接夹子和支架
正如 CFP10 主题 JTI-CS2-2019-CfP10-LPA-02-31 中所述,MFFD 下机身的所有框架夹和系统支架都将通过重复利用工厂废料制成的短纤维化合物注塑成型制造。主题经理 GKN Fokker 生产连续纤维 TPC 层压板。 CF/PAEK为基准材料,焊接为基准接合方法,但未规定具体焊接方法。
根据 CFP10 文本,MFFD 下机身将有 13 个框架和大约 36 个纵梁,需要大约 500 个框架夹(注意这些是需要结构测试的主要结构,总数包括用于测试的夹)和大约 270 个系统支架(它们是二级结构)按以下所示类型拆分:20系统支架(1)、120系统支架(2)、50系统支架(3)和80系统支架(4)。
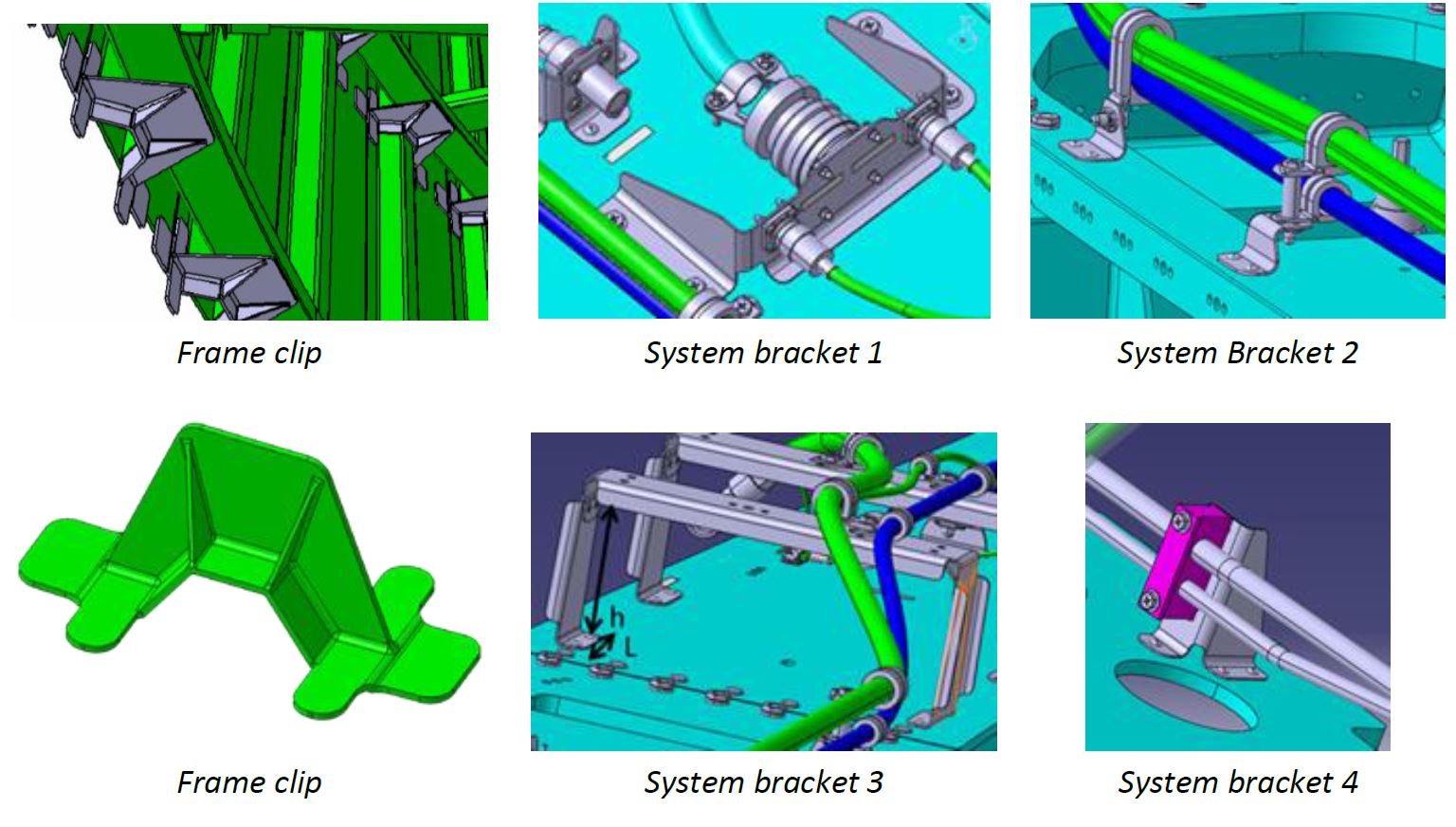
在 Clean Sky 2 主题 JTI-CS2-2019-CfP10-LPA-02-31,图 2 中交付的部件示例。来源 |清洁天空 2 CFP10,第。 146.
CFP10 中还有 MFFD 上机身主题 JTI-CS2-2019-CfP10-LPA-02-30,“热塑性基复合材料结构接头的创新焊接系统的开发”,由 Aernnova Composites Illescas(西班牙 Illescas)领导。计划于 2020 年第一季度之后开始,其范围是开发一种焊接系统,以实现加固部件(角撑板、楔形件、配件)和结构框架之间的结构结合,以获得高度集成的车门环绕结构 (DSS)。我希望在以后的博客中提供更多关于 MFFD 上机身的细节。现在,了解为什么 MECATESTERS 工作包 3 很重要,以及一旦 MECATESTERS、STUNNING 和 MFFD 完成后将实现多少就足够了。
加入两半
Veldman 解释说,一旦完成,MFFD 的下半部分将送往弗劳恩霍夫制造技术和先进材料研究所 IFAM(德国施塔德),与上半部分合并。 “我们致力于在 2021 年底前交付我们的一半机身,”他补充道。
如上所述,空中客车公司的 Ralf Herrmann 是 MMFD 项目的负责人;因此,空中客车整合了 Fraunhofer IFAM 和 CFP07 MultiFAL(机身装配线多功能自动化系统)联盟的工作— 为无数挑战制定解决方案。
其中一些在 11 th 的两个主题中有所揭示 提案征集(2019 年 11 月),均由空中客车牵头,将于 2020 年第四季度之后开始,标题为“用于关闭纵向筒形接头的工具、设备和辅助设备”:
- JTI-CS2-2020-CfP11-LPA-02-33,“:对接带集成和雷击保护连续性”
- JTI-CS2-2020-CfP11-LPA-02-34,“:重叠接头和框架耦合集成”
由 Airbus Bremen 的主题经理兼 MFFD 工作包负责人 Piet-Christof Woelcken 撰写,这些主题的主要挑战包括:
JTI-CS2-2020-CfP11-LPA-02-33
- 对接带接头 (下图3):
- 演示者的左侧(飞行方向)包括乘客门环绕。该区域的皮肤厚度变化需要阶梯式对接带集成,连接上下皮肤。
- 鉴于接头的复杂性,传导焊接 使用加热压板是首选的连接技术。
- 雷击保护的电气连续性 (下图4):
- 必须在机身外侧的两个纵向接头上实现金属雷击保护 (LSP) 的电气连续性。
- 预计为对接带集成提供的工具头可用于此目的。
JTI-CS2-2020-CfP11-LPA-02-34
- 重叠关节 (下图2):
- 演示者右侧(飞行方向)8 米长的搭接接头连接上下机身蒙皮。在纵向上,焊接区的表皮厚度低于 3mm。在圆周方向上,蒙皮具有阶梯式几何形状,以提高结构性能。
- 超声波焊接 是实现高生产率的首选连接方式。
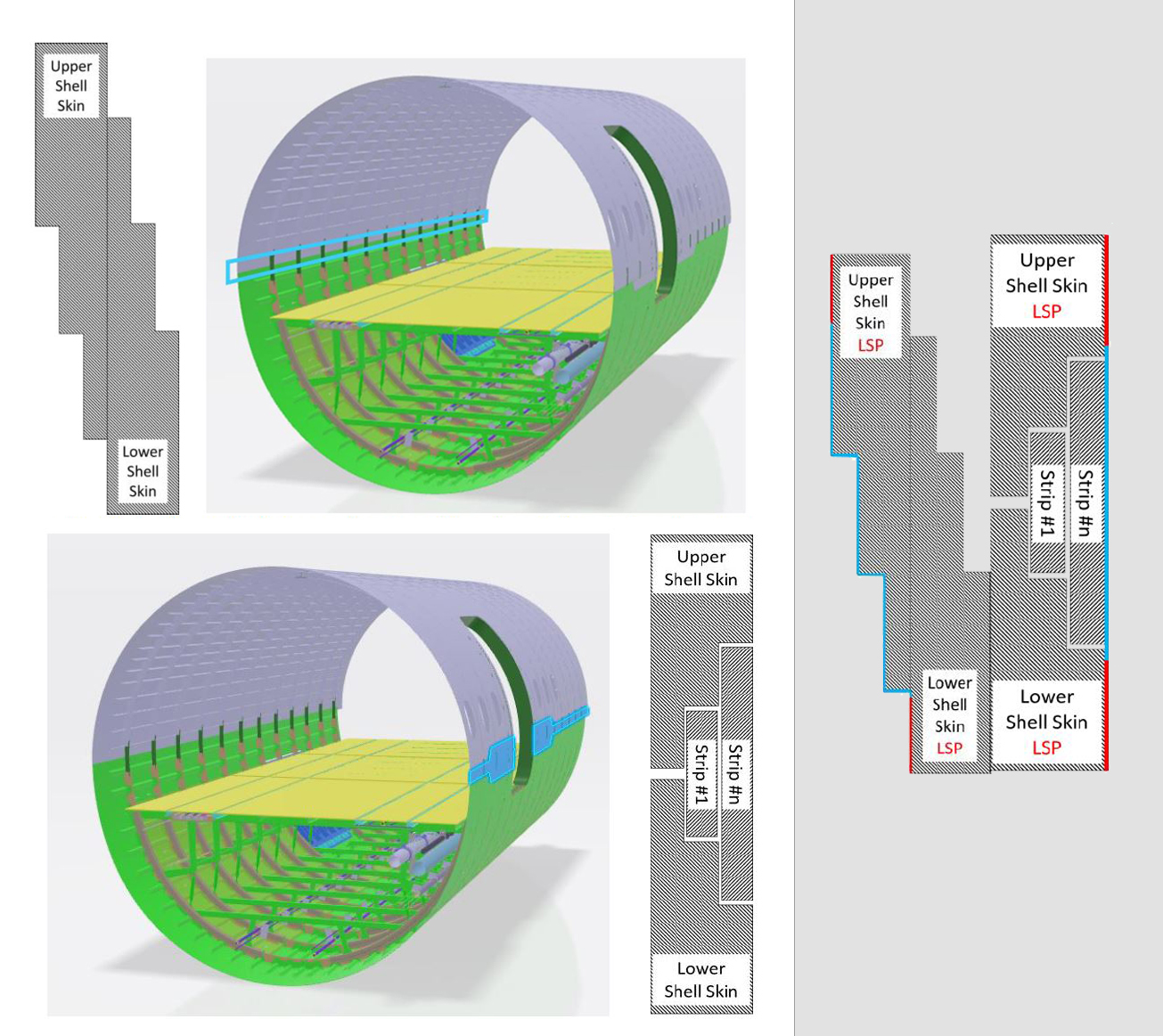
图。 2 (左上角) :重叠接缝:在重叠接缝设计中采用了阶梯式方法。注意下壳位于机身内侧。 图。 3 (左下) : 对接带集成:许多重叠的条带需要跨阶梯接头集成。请注意,对接带位于机身外侧。 图。 4 (右) :必须在 CFRP 机身外侧的纵向接头上实现金属 LSP 的电气连续性。红色表示预先配备的 LSP,蓝色表示将作为本主题的一部分应用的 LSP。来源 |晴空2 11 th 征集提案 JTI-CS2-2020-CfP11-LPA-02-33 和 -34,“对接带集成和雷击保护连续性”,第 78 和 86 页。
JTI-CS2-2020-CfP11-LPA-02-34
- 框架耦合集成 (图 5):
- 搭接接头:搭接接头下方的框架联轴器需要在结构上结合上壳框架和下壳框架。
- 对接带:对接带下方的框架连接器需要在结构上结合上壳框架和下壳框架并连接到皮肤。
- 电阻焊 是应对这一技术挑战的首选技术。
框架耦合集成。请注意,作为技术演示的一部分,每边的框架联轴器都不同。来源 |晴空2 11 th 提案征集 JTI-CS2-2020-CfP11-LPA-02-34,“用于闭合纵向筒形接头的工具、设备和辅助设备:重叠接头和车架联轴器集成”,图 5,p。 86.
焊接方法、工装头和公差
Herrmann 解释说,将在左侧通过对接带接头演示传导焊接,在右侧通过重叠接头演示超声波焊接,而电阻焊将用于框架联轴器。 “MFFD 将展示许多技术方法,因此它与制造实际机身不同,而是被设计为展示和成熟技术的工具,”他补充道。
开发焊接工具头
Woelcken 撰写的这两个主题的目标是为这些焊接接头开发所需的工具头。 “当你将两块焊接在一起时,你必须施加热量和压力,”他解释说。 “因此,这是在焊接过程中由工具头应用的。对于 Fokker 型传导焊接工艺,您在一侧主动施加热量和压力,而在另一侧施加来自支架的被动压力。对接接头是六根胶带的堆叠,在连接时,我们将堆叠放置并在焊接过程中对其进行加热。但是,由于 LM PAEK UD 胶带材料在焊接方面相对较新,因此我们必须了解工艺条件以及如何补偿公差。因此,我们必须定义材料和厚度,以及工具头的几何形状。”
“请注意,使用这种类型的对接接头是我们在飞机上的其他接头上所做的标准流程,”Woelcken 指出。 “对于 MFFD,我们希望保持上下机身与此标准做法保持不变,以最大限度地减少我们必须定制的材料量。”
公差的灵活性
Woelcken 指出,因为最上面的焊接表面基本上熔化成液体然后压在一起,“这为适应公差提供了很大的灵活性。”请注意,目前,热固性 碳纤维增强聚合物 (CFRP) 机翼和机身,通过使用液体垫片粘合剂解决了这些公差问题。尽管很少有人想公开讨论这个问题,但复合材料飞机结构中的匀场问题已得到广泛认可,并且已经公开了减少和/或消除它的举措,例如用于垂直尾翼的 Flexmont 组装方法。
“ 我们确实希望通过使用热塑性复合材料在解决公差方面获得优势,”Woelcken 说,“特别是通过利用我们的设计理念并利用我们在热固性 CFRP 和金属焊接方面的经验。关键是在加热和施加压力期间进行现场监测。”他强调热量是第一大参数。 “我很惊讶热塑性复合材料焊接工艺对压力的耐受性。主要挑战是如何控制这种压力以及它是如何下降的。目前,我们正在监测焊接接头的背面。”
Fraunhofer IFAM 自动化装配厂系统(左上) CFP07 工作主题开头的尺寸(右上角) 正在修改以适应 360° 机身,用于焊接 MFFD 的纵向和圆周接头。来源 | Fraunhofer IFAM 和 cfk-valley.com, Clean Sky 2 7 th 征集提案,JTI-CS2-2017-CfP07-LPA-02-22,p. 76.
装配自动化
在 7 th 提案征集,主题 JTI-CS2-2017-CfP07-LPA-02-22,“开发用于机身纵向和圆周接头的全尺寸自动化工厂系统”由 MultiFAL 联盟内的 Fraunhofer IFAM 领导。下面的摘录阐明了如何实施上面讨论的焊接工具头,现在正在开发中:
“要实现热塑性机身的组装过程,公差成为一个主要话题。机身外壳的定位和方向,以及焊接过程导致的变形,需要保持在公差范围内。可比较的精度可以针对纵向接头的最新工艺。 Here, the position error in each direction should be within 0.5 mm (in some exceptions up to 1 mm). … it can be assumed that a pre-load on the joint surface from both sides of approximately 1000N (independent of the welding technology) for a welding seam of 20 mm width is required by the automation system.”
Fraunhofer IFAM — which was also CTC Stade’s partner in developing the Flexmont VTP assembly process — describes its starting point:an in-house assembly plant system which can manipulate parts from 2 to 8 meters long and up to 6 meters high, including a 180° shell of a single-aisle aircraft. The system is enabled by a flexible arrangement of 10 cooperating hexapods (see “Reconfigurable Tooling:Revolutionizing composites manufacturing”), 24 linear units and modular rack elements. Vacuum grippers with 6-axis force and torque sensors adjust the pose and shape of the part, as required, to manage tolerances during assembly. The guidance and monitoring of these rapid, iterative adjustments is achieved through optical measuring devices.
According to the CFP07 text, Fraunhofer IFAM will modify this assembly plant system for holding a complete 360° fuselage, with work scheduled to begin in Q2 2018 and completed in 36 months.
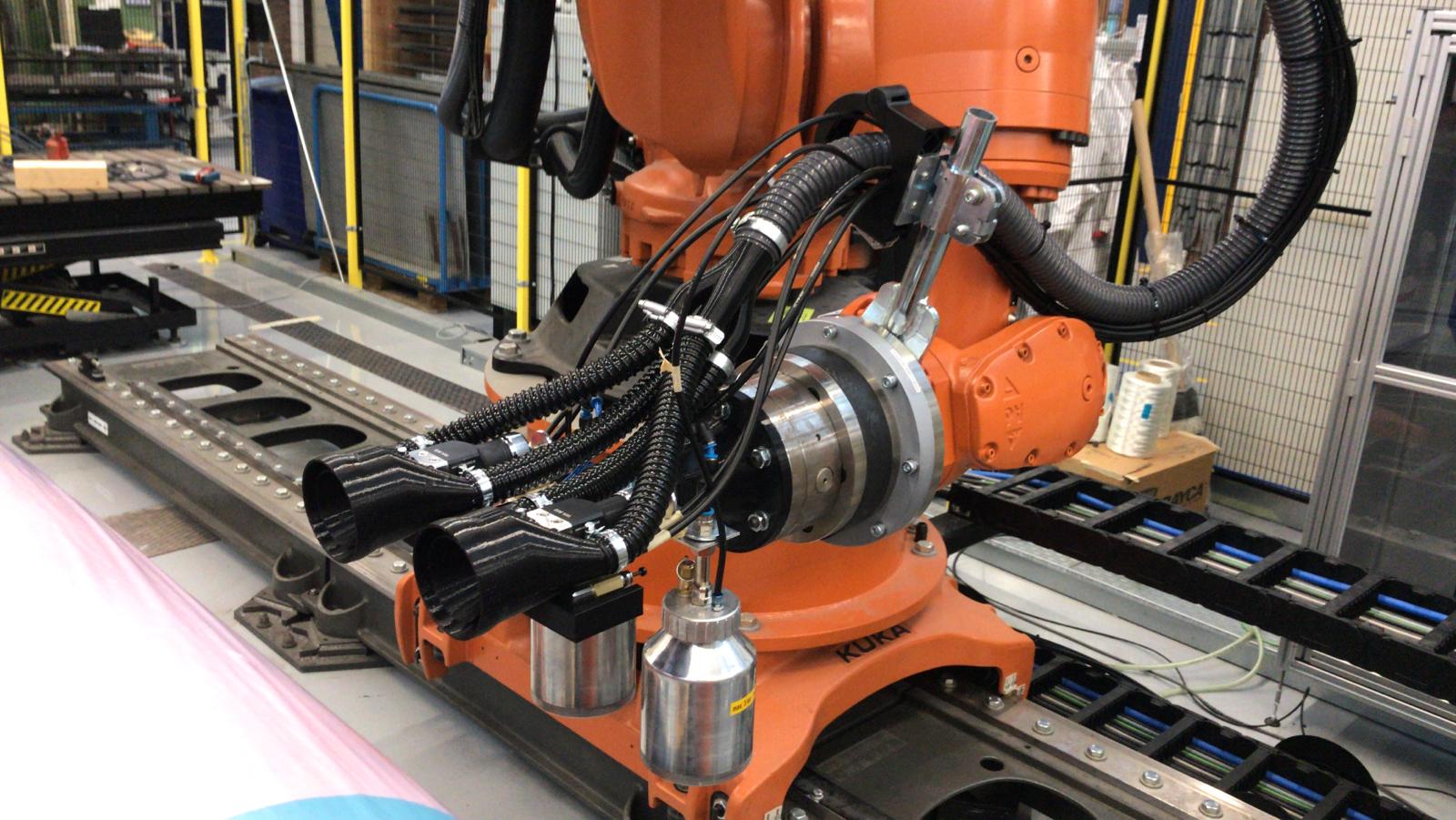
The STUNNING consortium is working with SAM|XL to develop automation for assembling the MFFD lower fuselage. SOURCE | samxl.com
Within STUNNING, activities are planned with the collaborative research center SAM|XL (Smart Advanced Manufacturing XL, Delft, Netherlands) to demonstrate automated welding techniques for assembling the lower fuselage. Specializing in automation for manufacturing large, lightweight composite structures, SAM|XL brings together TU Delft’s Aerospace Engineering group and Robotics Institute. GKN-Fokker is a major participant. One of the methods being investigated is sequential spot ultrasonic welding, which was proven in the Clean Sky 1 Eco Design project and TAPAS 2 as a fast and effective for connecting short fiber-reinforced brackets or clips to fuselage structures.
In her 2016 paper, titled “Smart ultrasonic welding of thermoplastic composites,” Villegas states that it is possible to scale up the ultrasonic welding process via sequential welding — that is, letting a continuous line of adjacent spot welds serve the same purpose as a continuous weld bead. Lab-scale sequential spot welding was used in the Clean Sky EcoDesign demonstrator’s TPC airframe panel, using flat energy directors to weld a CF/PEEK hinge and CF/PEKK clips to CF/PEEK C-frames (Fig. 6). Experimental comparisons with mechanically fastened joints in double-lap shear and pull-through tests showed promise. The process is further explored in 2018 papers {and 2019 papers} by Villegas’ TU Delft team member Tian Zhao {and in Villegas’ 2019 paper}.
— “Welding thermoplastic composites”, G. Gardiner, 2018.
The STUNNING consortium’s work with TU Delft and SAM|XL is adapting this technology to weld multiple system and semi-structural brackets, stiffening elements and stringers to the MFFD lower fuselage shell.
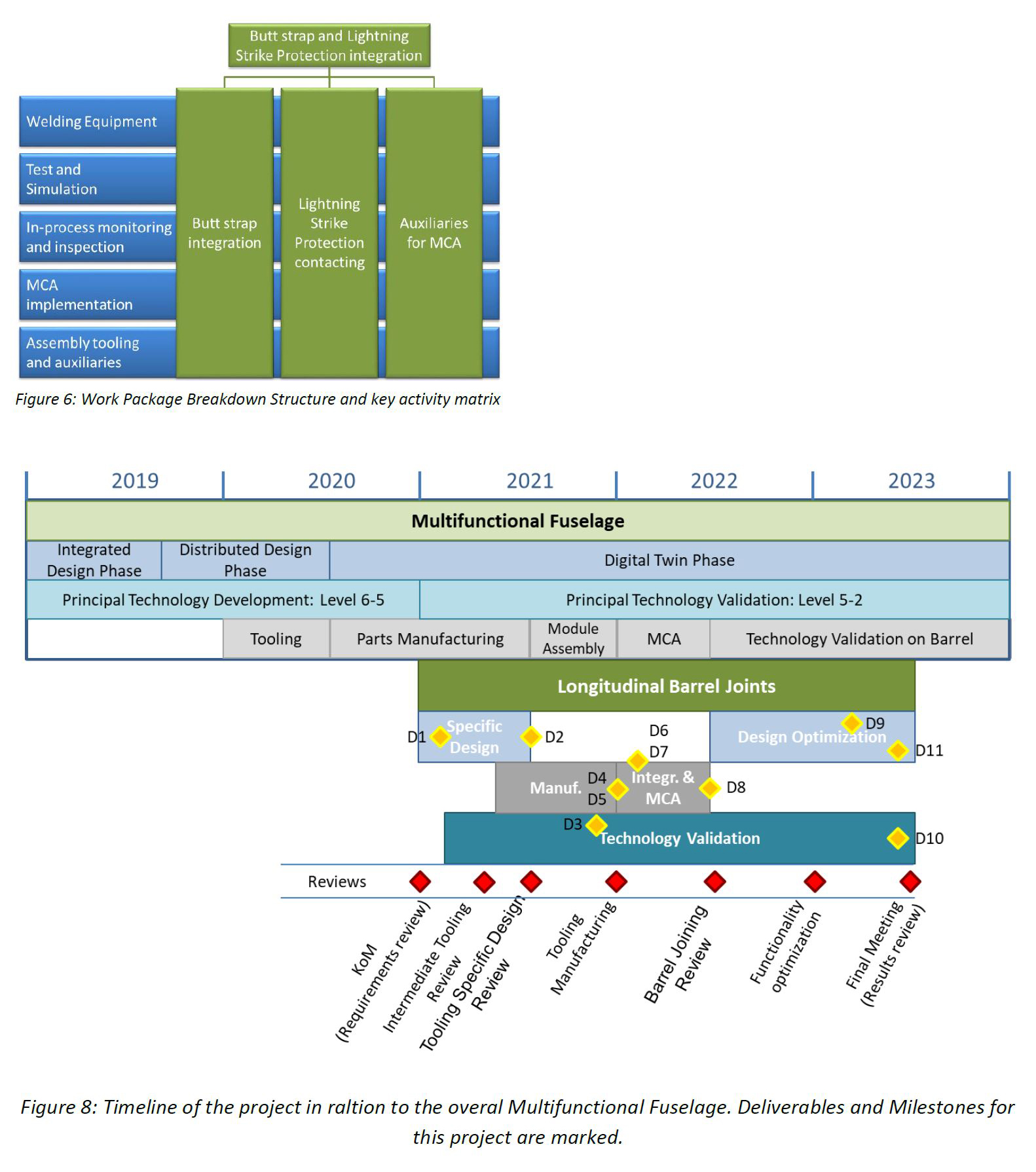
Work breakdown and timeline for MFFD assembly. SOURCE | Clean Sky 2 11 th Call for Proposals JTI-CS2-2020-CfP11-LPA-02-33, “Tooling, Equipment and Auxiliaries for the closure of a longitudinal Barrel Joint:Butt strap integration and Lightning Strike Protection continuity”, pp. 79 and 82.
Digital twin phase, 2020 and beyond
According to the Clean Sky website, the MFFD program reached an important milestone in Nov 2019 with the successful passing of its Critical Design Review (CDR). In the timeline above, the MFFD design enters a “Digital Twin Phase” in 2020-2021.这是什么意思? “Though we have wrapped up the majority of the design phase, we are taking it a bit further by working with a specific lifecycle management approach,” explains Herrmann. “We are modeling imperfections and nonconformities from the NDT results and process parameters during component manufacturing. We want to combine this Industry 4.0 data with lifecycle management so that we continue to tailor the design according to what we are actually manufacturing. We want to see how far we can push this and what we can accomplish by the end of Clean Sky 2.”
For 2020, the chief agenda is manufacturing. “We hope to present various parts as they come together this year,” says Veldman. What will the largest challenge be for the STUNNING program? “Assembly,” he answers. “Not so much within STUNNING, but our lower fuselage has interfaces with the door surround structure, multiple Airbus-delivered components and the whole upper fuselage. Getting everything delivered at the right time and then bringing it all together will require a number of developments yet.”
That brings us to perhaps the biggest question:Will thermoplastic composites be used on the next aircraft entering production in 2030-35? “For sure, we want to try to use the technologies we are working on,” says Herrmann, “but I cannot say if or when thermoplastic composites will be on future aircraft. The most important part for us is that they are an enabler for dustless joining regarding ramping production to more than 70 aircraft per month. We have to show that it is feasible, not only with metallics but also with thermoplastic composites.”
“By the end of this project, we will have a more complete understanding of thermoplastic composite welding and will gain approval for its use in large primary aircraft structures,” says Salat. “If we can use this for future aircraft, we can achieve significant weight savings and improved sustainability.” But perhaps just as important is Clean Sky’s ability to bring Europe’s aviation research and innovation stakeholders closer together. “We have quarterly meetings where I sit with all of the LPA steering committee,” says Veldman. “I’m talking to the whole of the European aerospace industry, and it most certainly helps to open up opportunities for the future, not only for companies who can supply to us, but for a wide range of collaborations.”
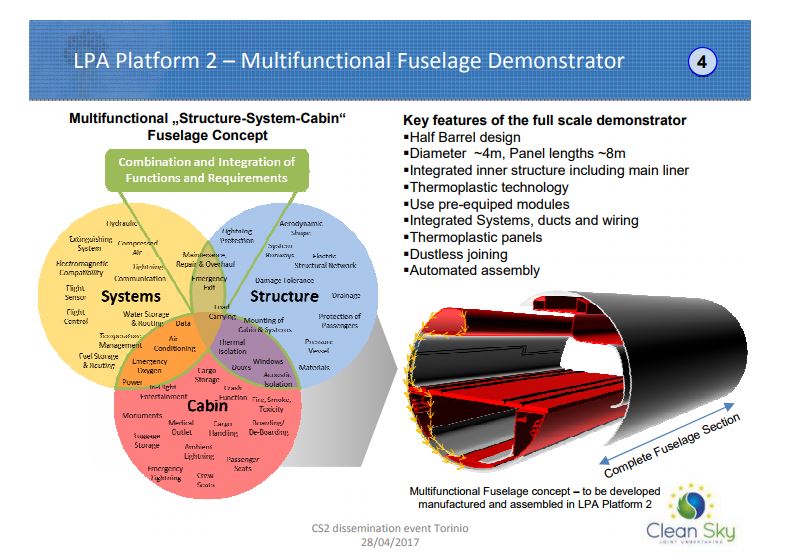
树脂