为速度而生:按时制造优质飞机发动机
在关于飞机制造系列的第一篇文章中,我们将重点放在发动机零部件上,重点介绍工具制造商每天帮助客户解决的现实问题。我们还深入研究了目前航空航天零件制造及其周围发生的情况。
航空航天和国防工业现在的状况如何?推动快速制造飞机并按时交付是非常现实的——但这并非没有障碍或成本。
在零件制造层面,耐热和复合材料可能很难切割。因此,据我们采访的三大工具制造商称,航空航天制造商必须在其工艺工程、机器编程和工具选择方面变得非常具有战略意义。
对于构成喷气发动机的所有复杂部件来说,战略化是非常正确的,其中单个 75,000 美元的锻造部件是常态——报废一个昂贵的、不受欢迎的选择。速度虽然很重要,但并不优先于可预测、可靠的结果。
航空航天和国防:提高产量意味着需要先进的工具策略
德勤航空航天部门负责人罗宾·莱恩伯格在《2019 年全球航空航天和国防工业展望》报告中表示:“随着我们看到原始设备制造商提高生产率,供应商在提高产量方面仍然面临困难。” “为克服这一挑战,制造商应考虑将重点放在加强供应链、有效的项目管理以及使用先进技术来提高生产力和效率上。”
在其报告中,德勤预计 2018 年全年将有大约 1,600 架飞机,并预计将比 2019 年多出 100 架。生产需求通常意味着使用更高的吞吐量和多任务机器。它提到的“先进技术”包括从基于传感器的过程中的计量到高速多轴加工再到高度工程化的专业工具,这些技术适用于这个高度监管的行业所采用的任何材料规格。
德勤没有指出的是,一台先进的 5 轴机器可能需要六个月到一年的时间才能到货。因此,虽然这些是延期交货,但一些分包商正在使用现有的 3 轴系统或其他老化的机器进行管理——许多成品航空零件“供应商”在等待时不得不重新考虑工具策略,解释工具制造商。
“他们想要更快的制造方式,”山特维克可乐满专注于航空航天的全球工程经理 Bill Durow 说。 “无论是粗加工还是精加工,他们都希望以更高的速度运行它们。如今,正在生产的发动机数量正以我们在业内从未见过的速度增长。”
找到专为耐热高温合金(又名“HRSA”)设计的合适材质和刀片工具在今天是非常可能的。但模具制造商表示,对于这些新材料以及切割它们所需的几何形状,仍有一个学习曲线。
例如,设计用于切割 4140 钢的工具可能不是切割铬镍铁合金、钛或碳纤维增强塑料或“CFRP”的最佳工具。山高工具的工程师表示,在过去几年中,一些过去由钛制成的静态和旋转发动机部件现在正在由陶瓷基复合材料或“CMC”制成。
“所有这一切的艺术在于将它们组合在一起的协同作用,”山高刀具的西部区域和航空航天经理 Dave Todd 说。 “我们今天在航空航天领域的技能已经发生了变化,我们更像是一家与技术合作伙伴、一级供应商和学术界合作的咨询公司……很多工艺工程都是在我们的技术中心异地完成的。”
这三个工具制造商都有测试实验室,用于为客户验证潜在的解决方案。这三个人还更喜欢混合进行基于实验室的测试以及现场测试,以确保确切的策略在实际的物理生产线上有效。
正在考虑航空航天和国防领域的零件制造机会?阅读“制造 101:成为航空航天工业的一部分。”
切割区热量管理的问题及解决方案
燃油效率正在推动对使用难以加工的耐热材料的重量更轻的组件的需求。提高发动机性能的部分动力来自环境:更清洁的燃烧也更有效。
“工程要求将其归结为供应商级别,这意味着您必须对工具技术有更快的响应时间才能支持先进材料,”山高刀具的细分市场专家 Scott Causey 说。 “而且有些材料可能需要完全不同的刀具策略来简单地根据其复杂性进行切割:常规 HRSA 材料不会使用与陶瓷基复合材料相同的切割策略。”
CMC 材料是分层的,如果处理不当很容易破裂。
但也要考虑一下这一点:耐热材料——对于热得发烫的涡轮喷气发动机的效率来说非常出色——在切割时也会产生大量热量。工具等级本身需要一定程度的耐热性才能完成工作。
为了帮助满足对冷却液的需求,通过刀具的输送已成为高级加工刀具的一个重要细节。刀具制造商一直在寻找冷却液输送方面的新创新——包括一些具有多个端口的刀具,可以在最有效的时间在最直接的切削位置输送。
谈到冷却剂:冷却技术将走向何方?在“ 金属加工液、机器润滑油和冷却剂的未来 。”
聚焦飞机发动机
切割发动机零件形状和材料所需的几何形状需要尺寸思维。有形状独特的发动机叶盘和空气翼片,它们可以结合不同的材料——例如钛复合材料。
为了解决这个问题,这些制造商设计并测试了一系列旨在切割最具挑战性的材料的等级——铬镍铁合金、高温合金、钛和许多其他材料。还有另一种方式:他们根据需要构建定制的航空航天工具。这些定制工具通常成为所有客户的标准产品线。
三大主要模具制造商描述了 OEM 规范和航空零件的独特几何形状如何推动定制模具成为标准产品线——一旦在现场得到证明。这三个制造商都有航空航天项目,以及针对当今发动机部件应用优化的非常具体的零件,包括:叶盘/叶轮、翼型、涡轮盘、涡轮机壳、线轴、风扇壳和轴。
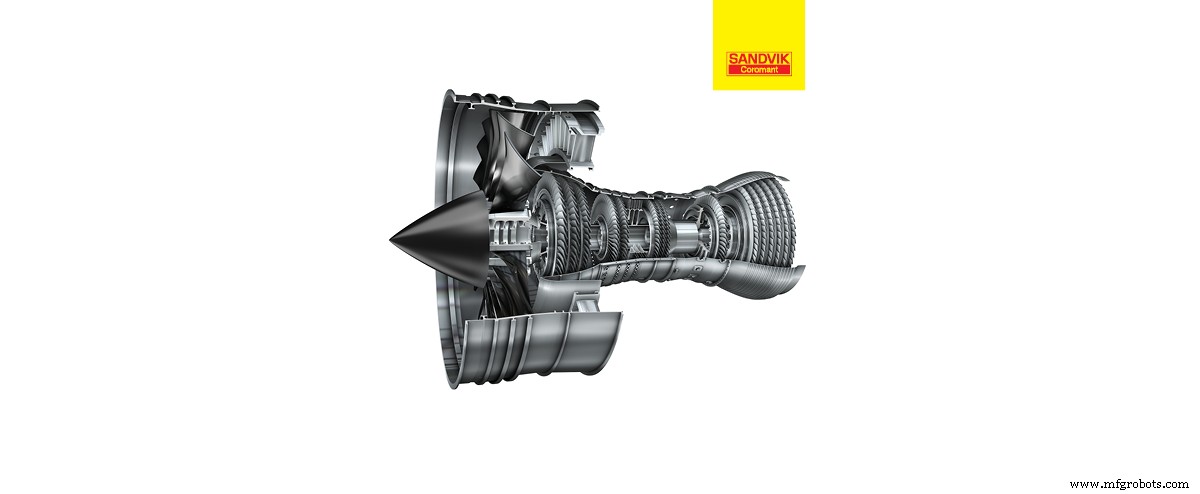
以下是在正确工具产生影响的情况下制造的真实引擎组件的四个示例。所有这些都包括一级航空航天制造商,他们的车间平均有 35 到 40 台机器,运行 365/24/7。这些绝不是这些制造商提供的发动机零部件的唯一领域。
山特维克可乐满 提高 Blisks 的生产力
挑战: 制作一个叶盘需要 7 天时间。镍基零件有一个深刀片和一个窄槽。用传统的铣削方法对长距离进行粗加工证明是无效的。芯片堆积过多。机器崩溃了。
“我们看到他们在做什么,只是烧毁立铣刀,满槽:来回,来回,来回,”杜罗说。 “他们有多余的工具,他们会把它们带到再磨车间,然后再使用它们……这需要花费大量时间并使用大量立铣刀。”
解决方案: 一种硬质合金切入工具,类似于在模具操作中所做的。此外,随后使用第二个直径较小的工具清理牙尖。
“我们把我们的测试件带回实验室,我们想出了使用暴跌程序的想法,”杜罗说。 “它工作得非常非常好。好消息是,我们几乎消除了另一个半精加工工序和二次清理。”
结果: 粗加工和半精加工的 7 天整体叶盘生产缩短了 4 天。它也最终成为叶盘应用程序的标准产品。
Kennametal 使用机翼节省大笔采购
挑战: 在电化学加工工艺或“ECM”中切割由铬镍铁合金制成的不规则形状的空气箔,其中工件由铋合金材料固定。无法大幅削减原材料,因此生产缓慢。脉动力会导致颤振和振动,并导致刀具寿命缩短。
解决方案: 设计了一种切削策略,可调整刀具的螺旋线、槽数和微观几何形状,以最大程度地减少推入重切削的可能性。对于较轻的切割,他们增加了螺旋并改变了直径和凹槽数,以确保通过旋转有三个接触点。
结果: 平滑切削,延长刀具寿命并提高最大金属去除率。客户能够取消即将订购的价值 100 万美元的新机器的订单。
山高工具 控制发动机盘上的切槽
挑战: 在固定风扇叶片的压缩机盘中,在热处理的 Inconel 718 中切割深槽导致的切屑控制问题。深切入程序会导致刀具破损和刀具寿命变差。
解决方案: 结合高压冷却液的多向车削和切槽系统。锯齿形、斜坡几何切削策略有助于减少切屑、减少热量并延长刀具寿命。
结果: 循环时间减少 15% 到 20%。获得了对过程的控制,并减轻了人工、耗时干预的负担。
肯纳金属消除了发动机外壳中的振动
挑战: 为发动机外壳移除一英寸的钛,但无法转动。现有工具的切削力太大,生产率很低。很难绕过特定的功能区域。
“发动机箱应该是圆形的吧?但事实并非如此,”肯纳金属公司航空航天和国防项目工程师马克·弗朗西斯说。 “它们充满了许多功能,消除了仅执行简单车削循环的能力……我想说 80% 的时间,材料是通过铣削来切割的。”
解决方案: 使用可以适应直径的专用工具,同时消除振动和推开。
结果: 稳定、可靠的生产线,具有可预测的金属切削效率。导致成为标准的定制工具。
生产过程和每个组件成本的重要性
请记住:大多数 1 级航空零件制造供应商运行的加工设备并不完全相同——即使他们可能使用相同的 OEM 规格制造相同的零件。模具制造商和金属加工专家必须了解每种加工环境以及适用于每种独特加工环境的设计策略。
独立地,作为竞争对手的所有三个工具制造商都希望非常清楚一件事:重点应该放在使用正确的工具来提高生产力,以真正对生产力和准确性产生影响。他们还认为,更全面地了解每个组件的成本指标有助于满足越来越多飞机的按时交付。
他们说,证据就是生产力。
航空航天生产率是真的吗?在 处加入对话 金属加工论坛 。 [需要注册]
工业技术