安全气囊外壳原型对 3D 打印复合材料进行测试
一个多世纪以来,均胜安全系统公司(美国密歇根州奥本山市)一直致力于为各种市场设计、制造和销售安全组件,包括安全气囊、安全带、方向盘和汽车安全电子设备行业。
该公司最近进行了一项可行性研究,以探索其他现有材料和工艺改进产品(例如驾驶员安全气囊 (DAB) 外壳容器)的潜力,从而实现了利用复合增材制造的概念验证。
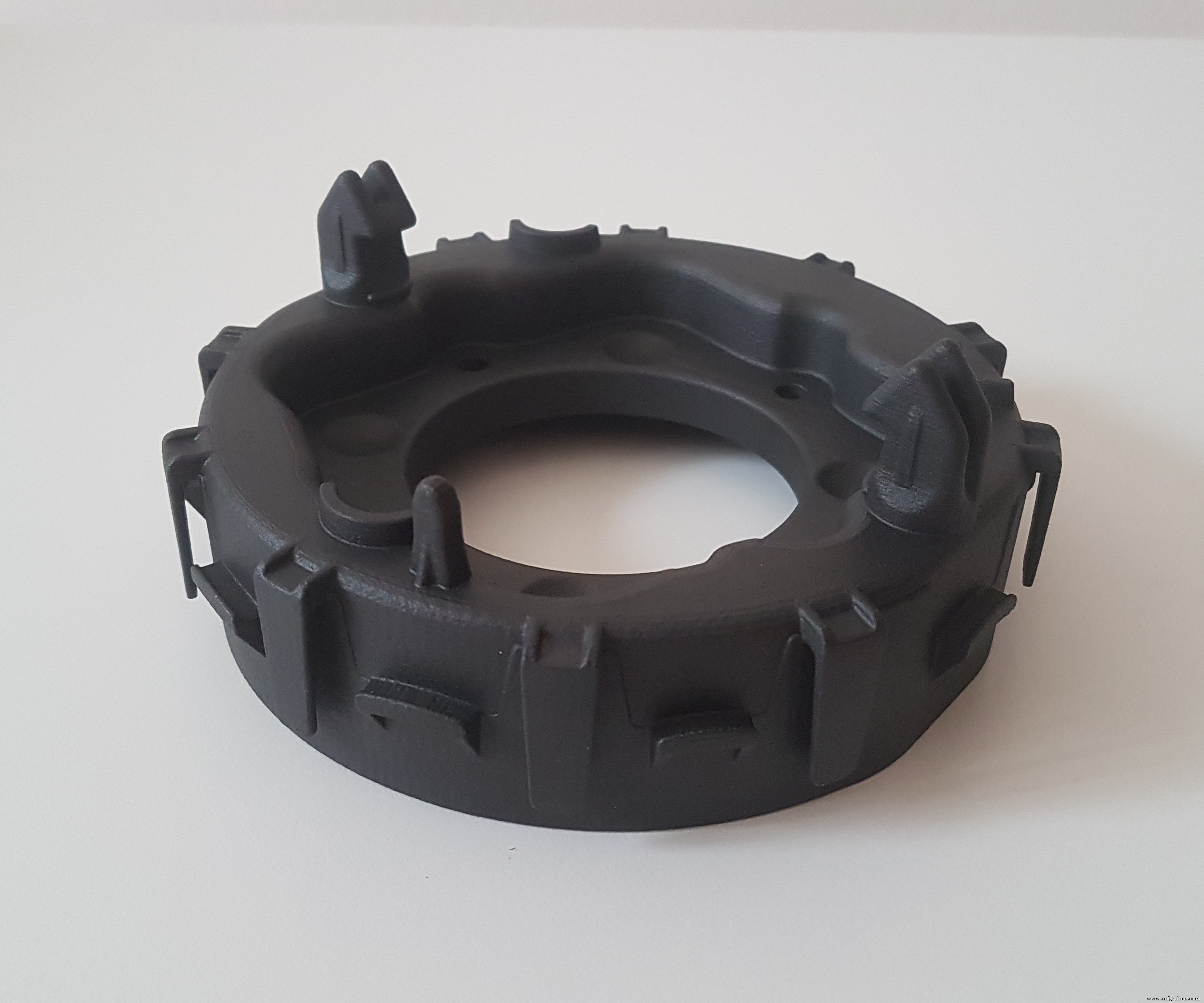
一个完整的安全气囊系统包括一个充气机、一个安全气囊垫、一个罩子和一个带有连接点到方向盘的外壳。气囊垫本身位于外壳和盖板的空间内。
DAB 外壳部件的性能至关重要。除了在车辆行驶时将整个安全气囊系统固定到位,该部件还必须能够承受在安全气囊展开时施加在安全气囊系统上的力。测试时,零件使用的材料需要在-35°C和+85°C的温度范围内具有足够的强度、抗冲击性和热稳定性。
原始容器是通过传统的注塑成型工艺制造的,由含 40% 玻璃纤维的聚酰胺 (PA) 制成。在可行性研究中,均胜安全系统团队的目标是在几天内快速生产出功能原型部件,他们希望找到一种与原始材料具有相似机械、热学和性能特性的材料。
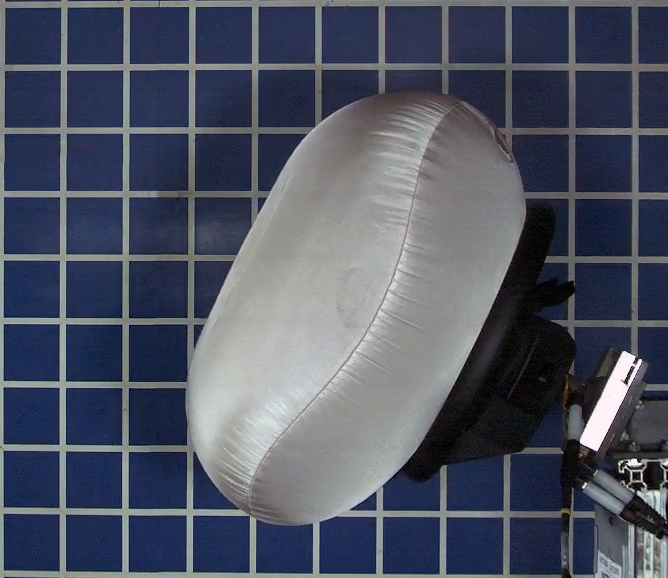
均胜创新团队进行了市场分析以寻找合适的材料,最终转向 CRP Technology(意大利摩德纳)为其 Windform TOP-LINE 系列高性能复合材料及其内部 3D 打印服务。
具体而言,该团队选择了 CRP 的 Windform SP 碳纤维/PA 材料,该材料的性能甚至比他们以前用于零件的材料还要高。这些零件将采用精选的激光烧结 (SLS) 增材制造工艺制造。
该团队能够快速生产原型零件并在完整的安全气囊模块中对其进行测试,证明重新设计的零件具有高强度和抗冲击性,以及在一定温度范围内的热稳定性。与原始注塑成型工艺相比,使用 SLS 还可以更快地生产新零件,并且无需昂贵的模具。
“这个机会开启了与 CRP Technology 进一步合作的各种能力和考虑,”均胜安全系统核心工程材料团队的开发工程师 Samer Ziadeh 说。
纤维