为复合材料工艺优化和控制定制超声波传感器
这篇博客是我对 CosiMo(“可持续移动复合材料”)项目报告的后续。该项目由 Faurecia Clean Mobility(法国南泰尔)于 2018 年启动,旨在展示复合电池盒盖的“智能制造”。 1,100 毫米长和 530 毫米宽的挑战部分采用无纺玻璃纤维和单向碳纤维增强材料以及金属和泡沫插入物,复杂的几何形状包括各种半径和从 2.5 到 10 毫米不等的厚度。该部件使用热塑性树脂传递模塑 (T-RTM) 成型,其中注入己内酰胺单体,然后在热压循环期间原位聚合以形成聚酰胺 6 (PA6) 复合材料。该项目的主要目标是研究使用基于传感器的闭环过程控制的全自动过程。
本博客更详细地探讨了 CosiMo 挑战部分中使用的 74 个传感器网络,尤其是奥格斯堡大学(UNA,德国奥格斯堡)开发的超声波传感器,以及如何使用来自所有传感器的数据构建一个过程的数字模型(数字孪生)。
基于 CosiMo 的成功以及对基于传感器和 AI 的制造开发开发中心的需求,UNA 与 CosiMo 项目合作伙伴德国航空航天中心 (DLR) 轻量化生产技术中心合作,组建了奥格斯堡 AI 生产网络( ZLP,奥格斯堡)和弗劳恩霍夫铸造、复合材料和加工技术研究所 (Fraunhofer IGCV)。 “我们正在建立一个 5,000 平方米的新设施,我们将合作运营,”UNA 教授兼奥格斯堡人工智能生产网络主任 Markus Sause 博士说。 “我们将拥有自动化生产单元,其中许多单元专注于复合材料技术,这将使我们能够展示人工智能的能力。”
CosiMo 传感器网络
对于 CosiMo 项目,74 个传感器被集成到由 Christian Karl Siebenwurst GmbH &Co. KG(德国迪特富特)提供的钢 RTM 模具中,用于模制 T-RTM 电池盒盖。用于在树脂注射、渗透(流动前沿监测)和原位聚合过程中监测工艺参数,该网络包括:
- 1 个真空传感器
- 奇石乐(瑞士温特图尔)的 4 个压力/温度传感器
- 奇石乐的 4 个温度传感器
- Netzsch(德国塞尔布)的 8 个介电分析 (DEA)/温度传感器
- 奥格斯堡大学开发的 57 个超声波传感器。
在我关于 CosiMo 的初始报告中,我讨论了这个传感器网络如何用于研发,而不是标准生产:
“对于工业批量生产,没有人会安装这么多传感器,这不是我们所期望的,”DLR ZLP 的 CosiMo 制造项目负责人 Jan Faber 说。 “但是对于这项研究调查,这个大型传感器网络非常精确 并帮助我们全面了解流程 和物质行为 .我们可以看到响应过程中的局部效果 零件厚度或集成材料(如泡沫芯)的变化。”
那么,这个网络是如何设计的呢? “大多数是超声波传感器,因为它们的成本最低,”Faber 解释说。 “我们在网格中以规定的距离使用它们。在某些位置,我们取出超声波传感器并放入奇石乐温度/压力或 Netzsch DEA/温度传感器。对于这些特定的传感器,DEA 和 Kistler,我们只是尝试将一个靠近树脂进入的浇口,然后再远离一个。因此,我们可以在看到模具温度一段时间后监控树脂到达的位置。”
为什么要使用不同类型的传感器? “一项研究任务是比较信号并查看不同传感器的性能,”Faber 说。这很重要,因为不同类型的传感器基于不同的测量原理。例如,DEA 传感器测量树脂的交流阻抗,树脂可以分成不同的部分,进而在聚合物中表现出不同的效果。与此同时,奇石乐使用压阻式传感器,该传感器依赖于基于硅的惠斯通电桥——一种用于测量动态电阻的电路——连接到薄膜,该薄膜形成安装在模腔壁上的传感端。膜在压力下延伸,这会改变硅惠斯通电桥的电阻,进而输出电信号。 “我们还使用了奇石乐的新型 4001a 传感器,它可以测量压力和温度,”Faber 指出。 “在工具中同时选择局部点的两个值非常有用。”
UNA 超声波传感器
CosiMo 部分网络中使用的大多数传感器是 UNA 开发的超声波传感器。 Sause 指出,它们之所以受到青睐,不仅是因为它们的成本低(<10 欧元),还因为它们可以提供广泛的信息。
超声波传感器已用于检查成品复合材料部件已有数十年历史,而且在注塑成型方面也有着悠久的历史。超声波传感器将高频声波发送到介质中并测量其反射(脉冲回波)和/或传输。在 CosiMo 项目中,标称频率为 2,000 kHz。在模具中安装的 57 个超声波传感器中——距离型腔表面 20 毫米——10 个在传输模式下工作,其余的在脉冲回波模式下工作。超声波传感器测量波的速度和振幅的减少(衰减);两者都对聚合物的性质敏感。此外,可以将波速计算为压力和温度的函数,但必须根据所研究的聚合物校准超声数据。
“我们开发的超声波传感器实际上与市售的传感器没有太大区别,”Sause 说。 “它基于一种压电材料,这种材料在将弹性运动转换为电信号方面非常敏感。但是,典型的传感器可以在高达 150°C 的温度下工作,我们必须匹配 200°C 以上的热塑性塑料成型的高温,这对传感器电子设备来说有点挑战。”
“我们还必须设计用于将传感器正确集成到模具中的机械系统,”他解释说,“这需要弹簧加载和良好的密封以提供良好的耦合。传感器必须满足大量要求;所以,我们不得不从头开始设计它。我们还对整个系统进行了适当的声学设计。”
聚合和流动前沿监测
“声学关注模具中材料的弹性,”Sause 继续说道。 “基本上,液体中的刚度与聚合完成时的刚度不同。我们正在有效地监控这种转变。我们在每个传感器位置观察从模具到聚合物材料的界面处波反射的声学强度,从而随着时间的推移持续跟踪固化。”
Sause 和 Faber 等人解释了这种测量的机制。等人,在 SAMPE Europe 2021 会议论文中,“使用己内酰胺对 T-RTM 制造中的原位聚合进行基于传感器的过程监测”。预制件浸渍前后的声学信号回波幅度之比取决于模具与零件界面处的反射指数 R。随着聚合的进行,这将接近一个恒定值。理想情况下,一旦聚合接近完成,R 的变化将为零。
还可以从声学传输信号中提取超声波穿过浸渍预制件的传播时间。这很有帮助,因为通过预成型件的声速与聚合度有关。对于在 SAMPE Europe 2021 论文时完成的实验,从传感器位置处的预制件完全润湿到聚合完成之间的时间为 240 秒。
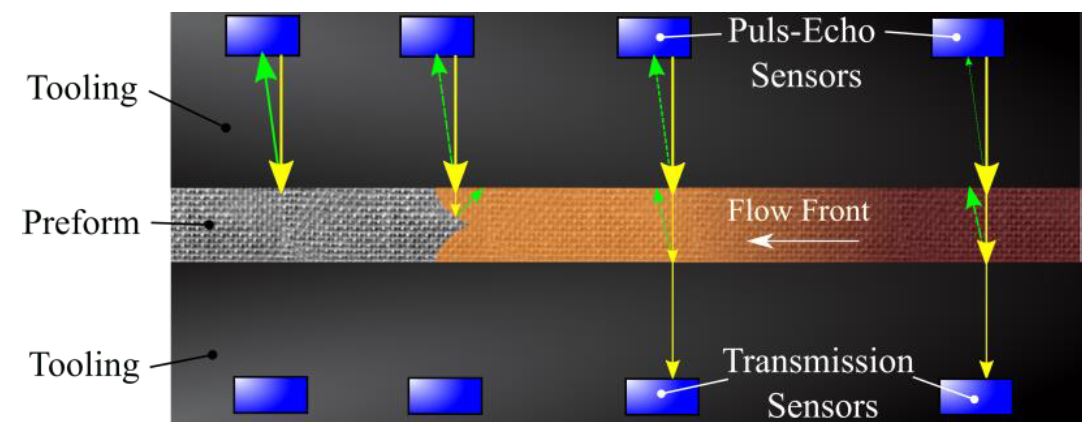
“我们还可以在注射过程中监测流量,”Sause 解释说,“因为随着聚合物流动前沿通过传感器,声学信号信息会发生变化。”在 SAMPE Europe 2021 论文中也证实,在注射开始后 15 秒,当所选传感器的己内酰胺流动前沿到达时,声学信号从初始归一化值 1 突然下降到 0.85-0.9 之间。
开发流程的数字孪生
Sause 表示,开发超声波传感器实际上只是 UNA 在 CosiMo 项目中所做工作的一小部分,“甚至不是最吸引人的部分。”他指出,真正的成就在于数据分析和过程数字模型的开发,以在零件制造过程中实现闭环控制。
“我们试图做的是提供有关模具中实际发生的情况的信息,”他补充道。 “我们已经建立了或多或少地根据温度和压力调整过程的路线,但我们现在正在做的是通过在每个传感器位置进行主动脉冲来利用声学信号信息。这使我们能够确定各种因素,例如流动前沿的形状、它到达预制件每个部分的时间以及每个传感器位置的聚合度。”
“理想情况下,您可以建立设置以启用闭环控制并在过程中进行调整,”Sause 说。 “这些将包括注射压力、模具压力和温度等参数。您还可以使用这些信息来优化您的材料。”
数字孪生的开发是一个多阶段和多合作伙伴的努力。它从分配给 DLR ZLP 的工作包之一开始。 “我们建立了一个基于 2D 板的模拟,我们想在其中使用 ESI Group(法国朗吉斯)的 PAM-RTM 模拟软件来模拟填充和聚合,”Faber 说。 “我们从项目合作伙伴 ITA(德国亚琛工业大学纺织技术研究所)和 SGL Carbon(德国威斯巴登)那里获得了瓶坯渗透率数据,以及来自奥格斯堡大学的热塑性聚合物反应的反应模型。然后,我们将所有这些都集成到模拟中,并尝试查看我们实际上可以与真实传感器数据接近的程度。”
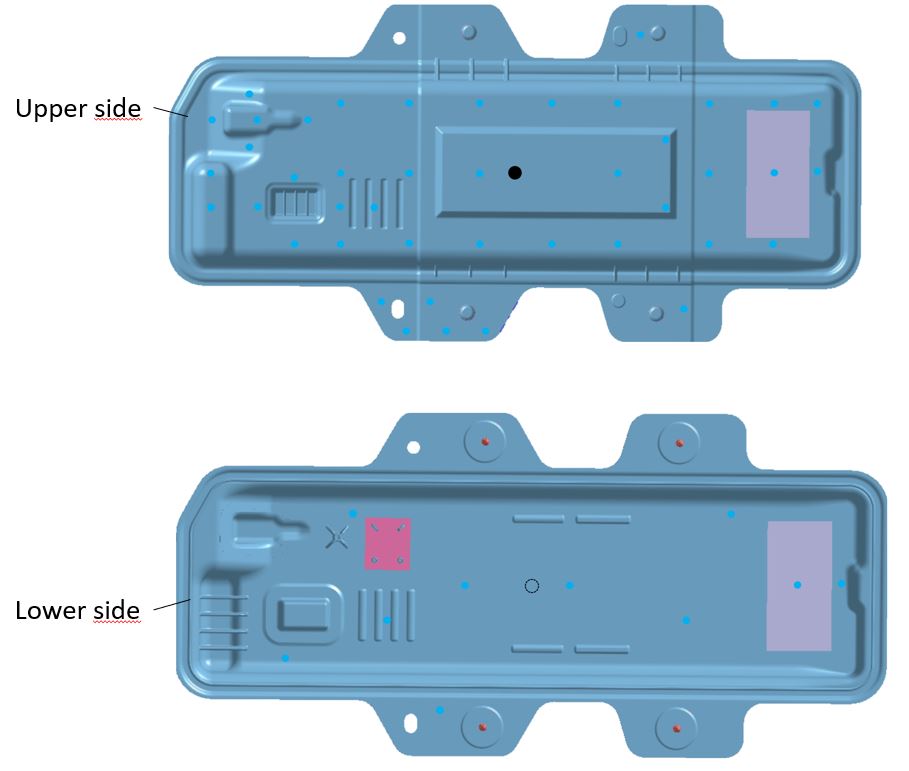
CosiMo 项目演示器部件的上下模具中的淡蓝色圆点提供了整个过程中特定点的数据。然后在数字孪生仿真中使用它在传感器位置之间进行插值,并对整个零件的过程进行建模。图片来源:CosiMo 项目,DLR ZLP 奥格斯堡,奥格斯堡大学
“我们发现,基于 2D 板模型,我们实际上非常接近填充,”Faber 继续说道。 “但是我们在聚合过程中遇到了一些我们无法在模拟中描述的温度影响。例如,这种聚合反应是放热的,您会看到实际数据中温度传感器的温度略有增加,但模拟中的增加要高得多。所以,这是我们继续做一些工作的领域。”
团队希望从模拟中发现的一件事是完成聚合所需的时间。 “我们真正想要的是在模具中所需的最短时间,”Faber 指出。该信息源自仿真模型,并且与所有仿真一样,依赖于多种类型的传感器和 AI 算法。例如,Netzsch 提供了用于介电分析的介电传感器,但也为该过程的部分数字孪生提供了帮助。 “他们建立了预测性 AI 模型来研究注入内部的机制,并预测聚合应该在什么时间完成以及聚合状态是什么,”Faber 说。
(请注意,Netzsch 结合了其在材料表征、动力学模拟和传感器技术方面的能力,在 AI 和云解决方案方面建立了新的产品。这种类型的集成解决方案已在 CosiMo 中成功展示,以提供聚合度和聚合度的实时评估。将以 sensXPERT 品牌进行商业化。)
从传感器和模拟的完整网络中,发现 96% 是达到的最大聚合,需要 4.5 分钟。 “因此,这比灌注过程快得多,但比使用热固性塑料的高速注射要慢得多。”
“传感器数据适合数字孪生模型,”Sause 说。 “我们的想法是让模型与通过传感器信息进行数值稳定的过程同时运行。蓝点提供了一个粗略的超声波传感器网格,然后我们能够在这些点之间进行插值。例如,我们能够提供一段视频,说明 CosiMo 部件中的流动前沿如何根据来自我们传感器的测量数据随时间变化。”
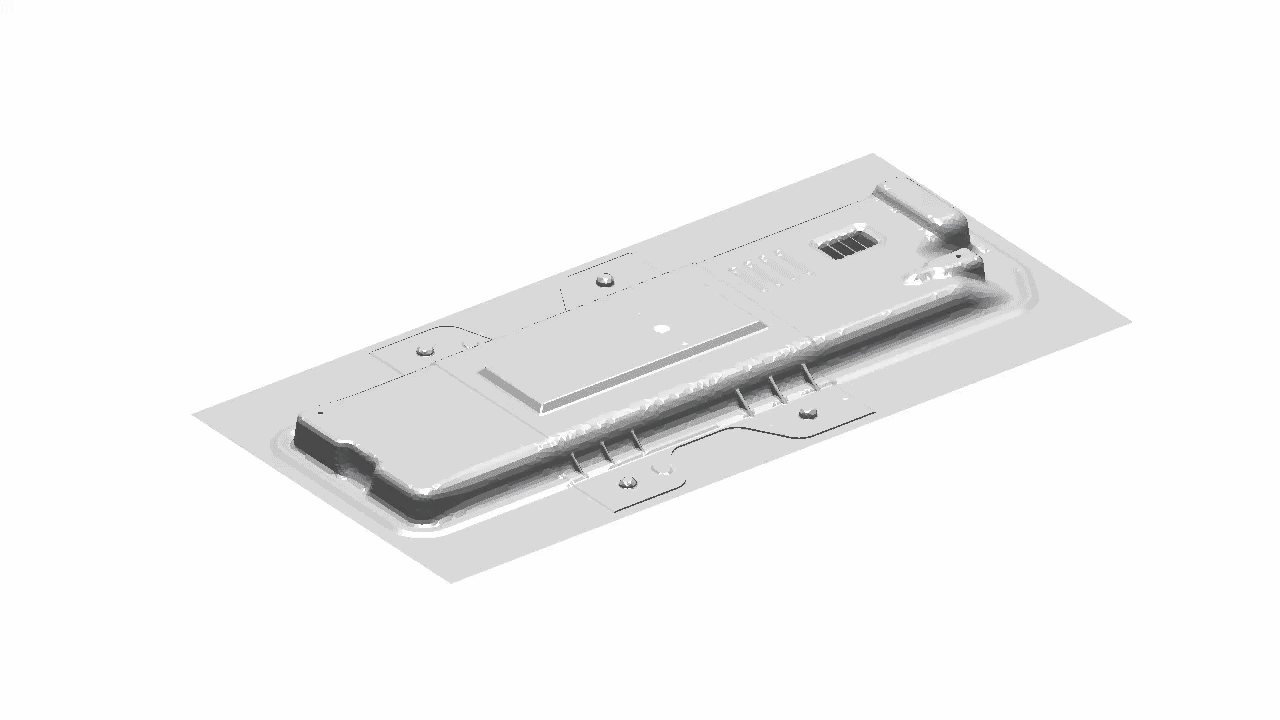
如何验证聚合速率预测? “我们有几种方法,”索斯说。 “首先,UNA 的一名博士生正在对己内酰胺-PA6 材料系统的反应动力学进行全套建模。因此,他同时研究红外光谱、流变数据和来自介电分析传感器的数据,为该系统的固化动力学提供非常精确的材料模型并验证该模型。因此,我们使用相同的模型来交叉验证我们的传感器。”
数字孪生的架构
Stieber 等人描述了数字孪生如何运作的架构。阿尔。在 2020 年的技术论文“迈向制造复合结构的实时过程监控和机器学习”中:
它由三部分组成:T-RTM 机器、模具中的现场传感器和数字孪生。这种结构和数字孪生尤其是在开发时考虑了以下目标 O1 - O4:
- O1:使用工具的原位传感器监控每个复合材料部件的制造过程。
- O2:实时可视化每个制造过程,以获得进一步的过程洞察。
- O3:根据模拟和真实数据训练机器学习模型,以预测制造过程的结果。
- O4:使用经过训练的机器学习模型来减少生产废品。
然后,传感器将数据提供给数字孪生的边缘分析,然后可用于预测未来的流动前沿动态,确定每个纺织品预制件的纤维体积含量,预测干点并检测可以减少废品的异常情况。>
T-RTM 机器包括两个现成的组件:一台 Wickert(德国普法尔茨州的兰道)440 千牛顿热压机和 KrausMaffei(德国慕尼黑)的 T-RTM 注射装置。这两台机器以及整个传感器网络都连接到一个负责控制整个制造过程的 PLC(可编程逻辑控制器)。
由于传感器需要实时预处理以将原始数据转换为有关流动前沿或树脂固化的更高级别信息,因此使用 iba AG 的 ibaPDA 数据采集单元直接在边缘记录预处理数据(德国菲尔特)。因此,传感器数据被记录并与一致的时间戳合并,该时间戳链接到过程数据和零件信息以及每个目标 O1 和 O2 的传感器数据。
为了自动优化制造过程,存储的数据用于训练机器学习 (ML) 模型以解决目标 O3。例如,这些模型负责从传感器网络重建树脂的流动前沿,预测流动前沿进展,以及——理想情况下——调整过程参数以优化过程实例或后续运行的结果.由于真实数据通常不足以训练可靠的模型,因此数字孪生团队使用 PAM-RTM 模拟运行来增强测量数据。在使用模拟数据进行预训练后,数字双胞胎用真实世界的数据进行了微调。这种策略被称为迁移学习,并已在计算机视觉和自然语言处理应用中成功采用。机器学习可能实现的高级分析可提高预测能力和过程可视化以及闭环控制。
用于工业复合材料生产的传感器集成
那么,复合材料零部件制造商如何在自己的生产过程中应用这项技术来开发闭环控制呢? Sause 说使用多种类型的传感器来交叉验证流动和固化/聚合监测并提供补充信息是有意义的。然后是定义传感器放置的问题,包括在每个位置放置哪些类型。 “例如,”他指出,“您不需要到处都需要压力和温度传感器,而是需要那些关键数据点的地方,例如树脂入口、复杂的几何点等。”
多少个传感器? “对于 CosiMo,我们使用了 74 个传感器,但对于半米的零件,您会使用更少,也许 35-40 个,具体取决于您的几何形状和感兴趣的关键点,”Sause 说。 “这也取决于生产过程。例如,航空航天领域的一些流程已经使用了几十年并且已经非常成熟。对于这些,您可能不需要很多传感器,并且可以在开始时无需太多开发工作即可集成它们。但其他流程更加未知,需要更多的前期工作。对于 CosiMo,我们正在考虑将 T-RTM 与 PA6 原位聚合一起使用,例如,这不像使用环氧树脂的 RTM 那样有据可查。”
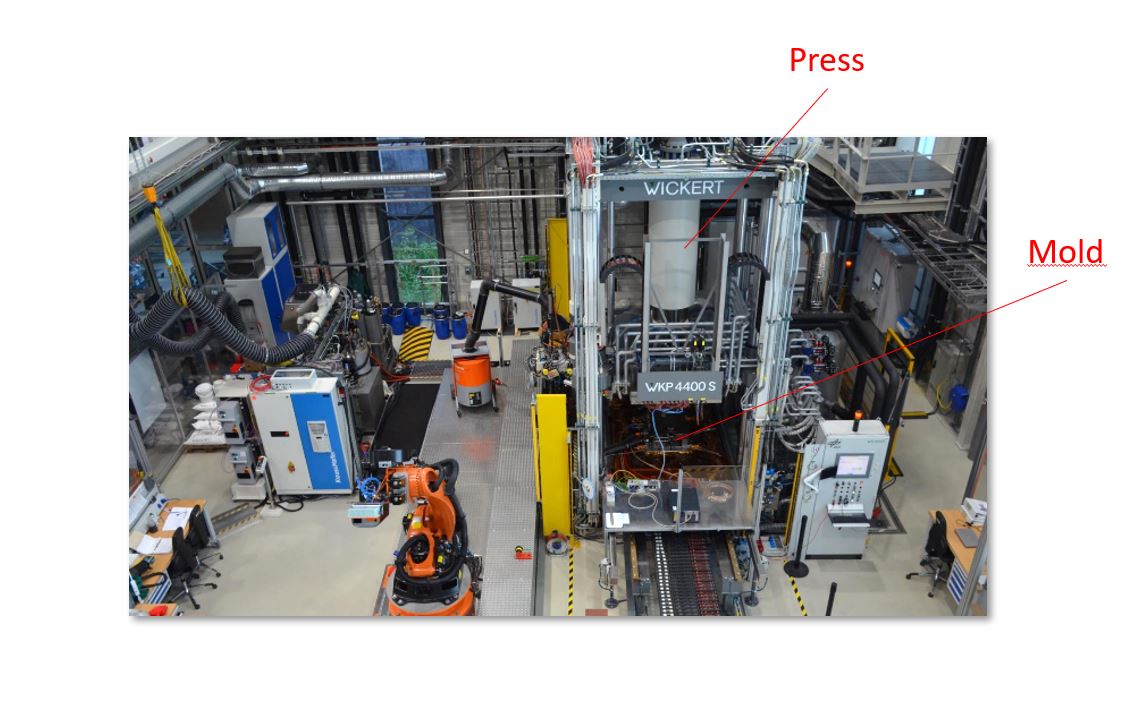
CosiMo 项目的制造设备包括一台 Wickert 440-kN 压力机和 KraussMaffei 注塑机。本系列照片来源:CosiMo 项目,DLR ZLP 奥格斯堡,奥格斯堡大学
构建数字模型需要多长时间?这是否总是需要实现闭环控制? “同样,这取决于您的流程以及您想要达到的水平,”Sause 说。 “首先,通过集成传感器信息,您可以直观地了解处理黑匣子内部发生的情况以及要使用的参数。
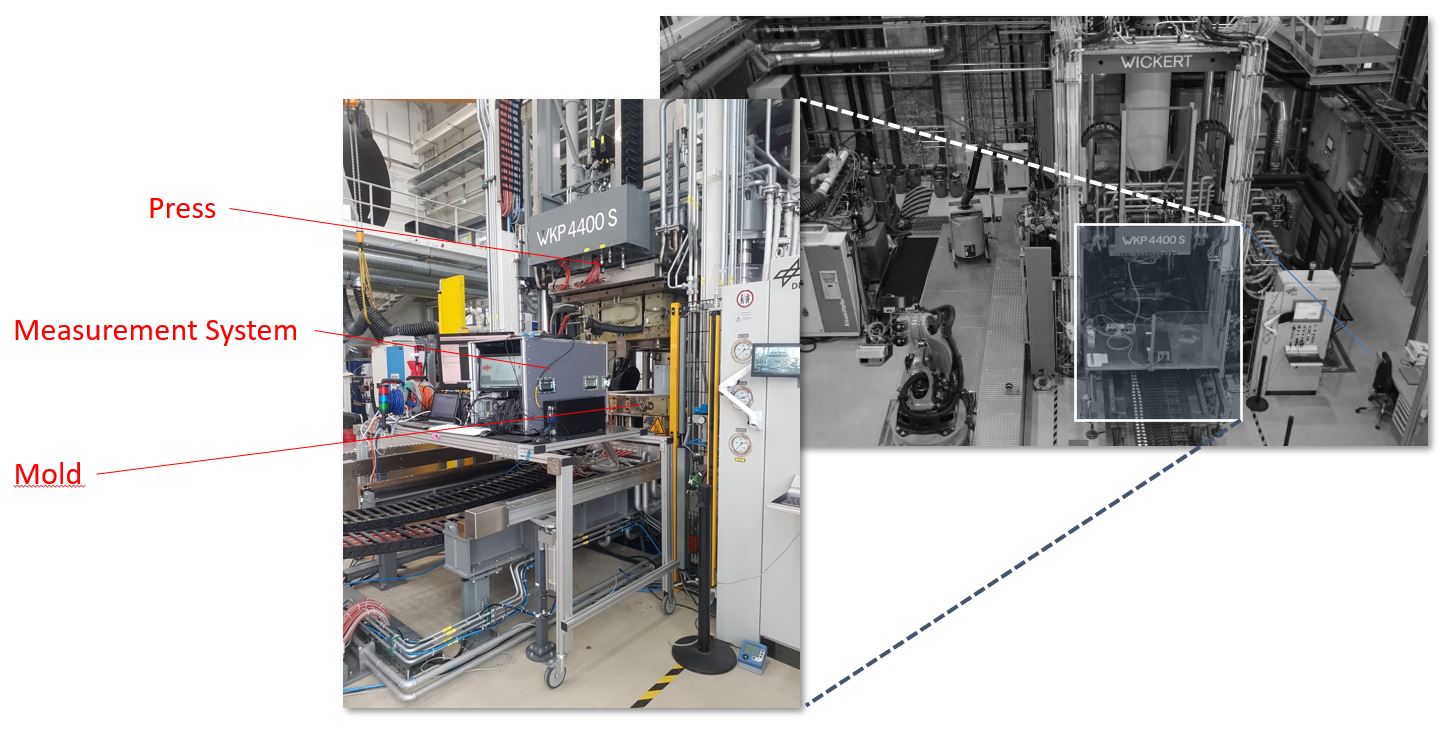
CosiMo 开发的闭环控制系统还集成了 iba AG 的模内传感器和数据采集系统(此处显示了测量系统)。
一旦达到第一个目标,就需要通过几个步骤来实现闭环过程控制。半途而废,也许是有了可视化,您可以自己按下停止按钮,以适应流程并防止废品。所以这也是一个开始。然后你可以开发数字孪生,但它需要训练数据。因此,您必须以某种方式提供它,这意味着您可以生成几个部分用作输入数据。但是,您还需要生产低质量的零件。因此,这取决于您是否愿意投资于机器学习方法的培训。”
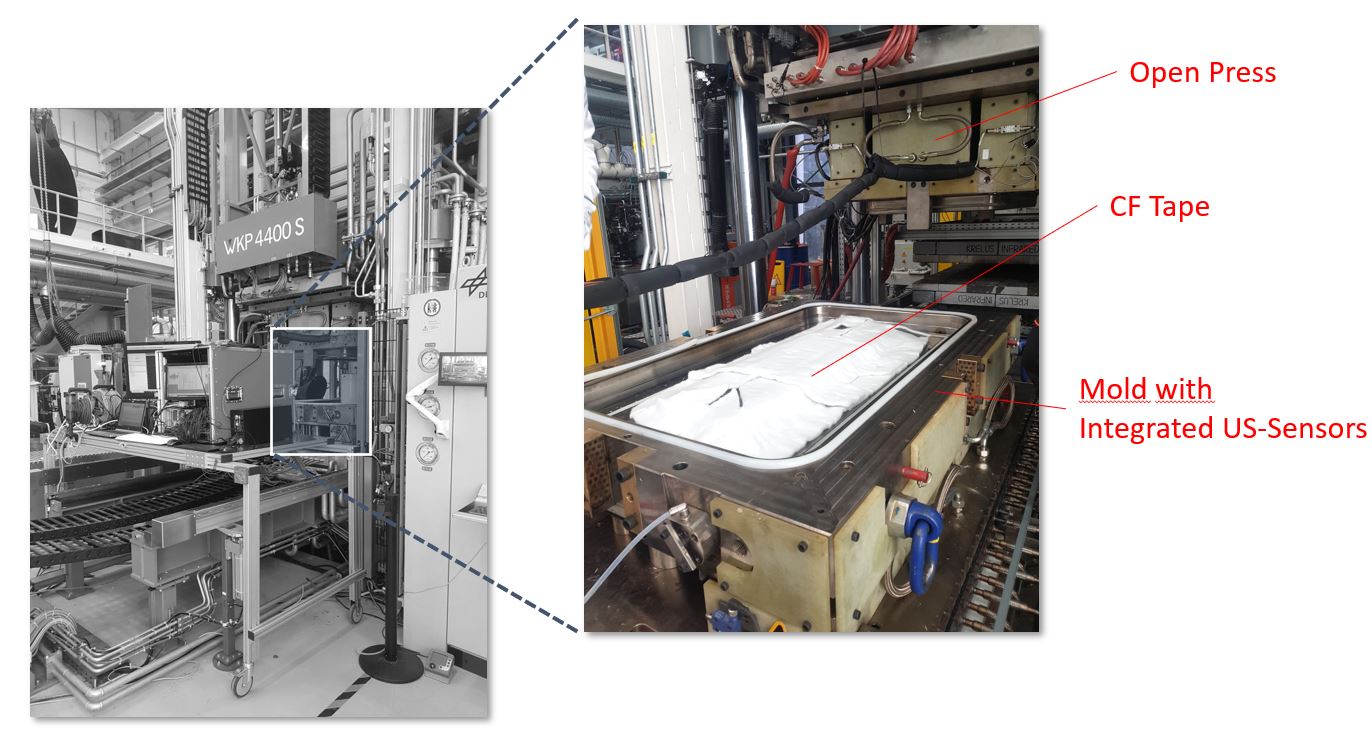
经过训练,数字孪生可以优化过程参数并提供闭环过程控制。
然而,Sause 确实承认 CosiMo 中采用的迁移学习方法“在一定程度上可以迁移到类似的几何形状或材料系统以及其他不会完全改变情况的变体。因此,您可以通过这种方式构建您的数据库,并有可能使用已获取的数据来识别效率趋势。然后,您可以将其用于解决您可能同时遇到的其他问题。”
因此,开始的方式似乎是:开始使用传感器并构建与传感器配合使用的数字模型,以便您了解您的过程? “当然,”索斯说。 “而且我可以向你保证,今天生产中使用的大多数机器仍然非常愚蠢。许多机器没有任何传感器可以为您提供数据库以提供有关正在发生的事情的反馈。所以,是的,传感器系统的集成将是第一步。但是你需要做一个系统的 数据获取,并提供数据存储架构,以便能够对数据进行处理 .你实际上看到很多公司都集成了传感器,但他们对数据不做任何事情。”
人工智能生产网络
在回答上述问题时,Sause 不断回到 UNA 内部的各个团队以及可以提供传感器集成和数字孪生服务的衍生公司。为此,UNA、DLR ZLP 和 Fraunhofer IGCV 于 2021 年 1 月启动了奥格斯堡人工智能生产网络。 “协作框架来自我们过去与 DLR 和 Fraunhofer 的项目,”Sause 说。 “我们正在从 CosiMo 获取基于 AI 的生产开发蓝图,现在将其扩展到非常广泛的范围。因此,例如,我们在 CosiMo 中的工作预算为 1000 万欧元,但对于 AI Production Network,初始资金为 9200 万欧元。这将使我们有可能启动许多新的研究项目,例如 CosiMo,以在制造业中利用人工智能。我们不仅在复合材料领域工作,而且非常关注它们。”
使用超声波传感器改进 CNC 加工是一个已于 2021 年启动的项目。“有一个项目即将开始回收陶瓷基复合材料 (CMC),”Sause 说,“我们将有几个项目之间有紧密的联系。增材制造和专门回收的纤维增强材料的再利用。”
至于每个组织将扮演的角色,Sause 解释说没有竞争,因为每个机构都有分配的预算。 “我们都有自己的份额,因此可以像过去一样自由合作。此外,我们对彼此以及我们的能力、优势和劣势都非常了解。一起工作很有趣,因为我们知道我们能做什么,不能做什么。许多想要与我们合作的公司已经与我们联系,我们现在正在讨论如何从我们的能力方面找到理想的匹配。”
对于 5,000 平方米的生产设施,“我们将一起运营,”Sause 说。 “我们计划在 2023 年初开业并开始安装机器。我们将提供将各个单元链接在一起的自动化生产设置。其中许多将专注于复合材料生产技术。我们还将这样做,向行业合作伙伴展示和演示人工智能在这样的生产环境中可以做什么。我们还希望有来自行业的合作伙伴进来,并在我们的设施中放置机器,以便我们可以一起运行项目,看看如何为他们的站点链接和集成新的解决方案。”
树脂