流程计划估算和成本核算
在本文中,您将了解流程计划估算和成本核算以及与之相关的各种术语,以便清楚地理解。
流程计划估算和成本核算
成本评估
只有对制造产品所需的成本有一个很好的了解后,流程设计才会完成。一般来说,成本最低的设计会在自由市场上取得成功。因此,了解构成成本的要素至关重要。
成本要素: 产品或成本要素的构成可以大致分为(1) 经常性成本或制造成本或运营成本和(2) 非经常性费用。它们可能再次被归类为直接成本 , 间接成本 而资本成本 属于非经常性费用。经常性成本包括所有直接和间接成本,而资本成本则属于非必需成本。
直接费用
直接成本 是可以直接归因于特定产品制造的那些因素的成本。其中包括材料和劳动力成本。 材料成本 是进入成品的材料的成本,包括从原始库存中切除的所有废物。 人工成本 因机器而异,通常通过将操作所需的时间乘以人工费率来计算。因此,必须估计设置和执行操作的时间以找出其人工成本。
间接费用
间接成本 是那些只能间接归因于特定产品制造的因素的成本。它们有时被称为开销 或成本 .间接费用通常通过将操作时间乘以间接费用率来计算。这样的比率是通过将适用于制造单位一段时间(例如一个月或一周)的总间接成本除以同一时期内直接人工的总小时数获得的。
大写费用
资本成本 是一次性成本或非经常性成本,包括可折旧的设施,如厂房、建筑或制造设备和工具,以及非折旧的资本成本,如土地。资本成本是通过按小时或在生产的零件之间分配主要机器和工具成本来确定的。
总成本 产品的成本是制造该产品的直接成本加上归因于该产品制造的任何间接成本。
为了让工艺工程师使用成本数据作为工具来帮助分析制造问题,成本可能会更高方便地分为固定成本和可变成本。
Fixed costs include preparation costs such as of tooling setting up, etc., and also the interest and depreciation costs which are independent of the quantity of the product manufactured.
Variable costs are those costs which vary as the quantity of product made varies. This includes the direct labour and material costs, and also that part of the indirect costs which will vary as production varies. The total cost of a product can also be seen to be fixed cost plus variable cost.
Cost Structure
Cost structure : The elements of cost can be combined to give the following types of cost:
1。 Prime cost : Prime cost or direct cost is given as :
Prime cost =Direct material + Direct labour + direct expenses.
2。 Factory cost : Factory cost or works cost is given as :
Factory cost =Prime cost + Factory expenses.
3。 Manufacturing cost :This is given as :
Manufacturing cost =Factory cost + Administrative expenses.
4。 Total cost : Total cost is given as :
Total cost =Manufacturing cost + Selling and distributing expenses.
5。 Selling price : Selling price is given as :Selling price =Total cost + Profit.
STANDARD COSTS
In cost accounting actual or recorded costs or standard or predetermined costs are used. The nomenclature actual cost is misleading. Usually average labour rates are used rather then the actual ones and arbitrary allocations are made for use of capital equipment and for general and administrative costs. Also actual costs are compiled long after the job in completed. This approach is chiefly aimed at financial accountability than cost control.
Standard costs are based on the proposition that there is certain amount of material in a part and a given amount of labour goes into the part’s manufacture. In a given period of time costs tend to vary around some average cost per unit or per hour. Through the use of standard costs, guesswork is reduced and a standard that measures performance is established. Each part and assembly has a standard cost card on which is recorded the standard material, labour, and overhead costs, and the total cost.
The system of standard costs consists of two parts :(1) a base standard and (2) a current standard. The base standard is determined infrequently, e.g., once a year, and the current standard represents the later cost. The difference between the two is the cost variance.
ESTIMATING LABOUR COSTS
All direct and in direct costs excluding labour costs are determined by the accounts department of the plant. Process planners are mostly concerned with labour costs which are directly related to the process of manufacturing. However, the total time required by workers to perform an operation may be divided into following classes :
1。 Set-up time : This is the time required to set up elements to prepare for the operation. The elements include:time to study the blue print or to do any paper work, time to get tools from tool-room, time to install the tools on the machine. Set-up time is performed usually once for each lot of parts. If 20 min are required for a set-up time must be charged against each piece. The time for each or the elements is taken from standard tables usually available with the estimators.
2。 Man or handling time : This is the time the operator spends loading and unloading the work, manipulating the machine and tools, and making measurements during each of the operation.
3。 Machine time : This is the time during each cycle of the operation that the machine is working or the tools are cutting.
4。 Tear down time : This is the time required to remove the tools from the machine and to clean the tools and the machine after the last part of the lot or batch is machined. This occurs only once in a lot.
5。 Down or lost time : This is the unavoidable time lost by the operator due to breakdowns, waiting for the tools and materials.
The time to perform an operation also includes time for personal needs, time to change and re-sharpen tools, etc. which are taken to be about 20 per cent of the sum of all other times. Besides, there are inspection or checking times which vary from instrument to instrument.
Each operation on a particular type of machine tool is divided into a number of small elements. These elements can be standardized, measured and then recorded. This is mostly done under Time and Motion study . Standard data is also available for various times. Machining times are calculated with the help of formulae for each machining operation which takes into account the feeds, speeds, depth of cut and tool travel plus tool approach.
Machine time : All machining times can be calculated with the basic formula
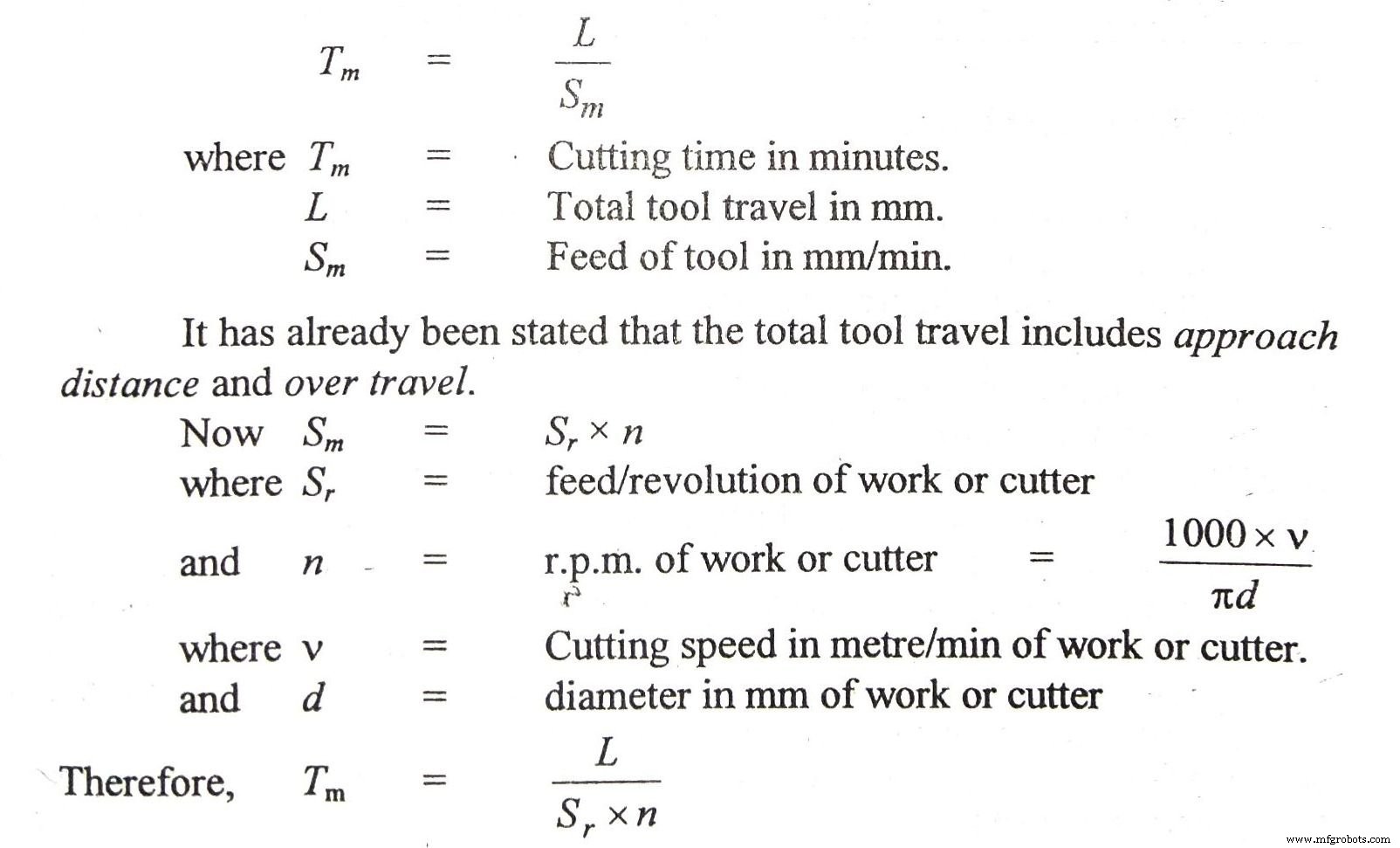
Calculation of machining time for each operation and their feed, speed and depth of cut have been given in each chapter or they may be available in hand books.
Methods of Costing
The method used to develop cost evaluation fall into three categories:methods engineering , cost by analogy , and statistical analysis of historical data .
In the methods engineering approach, that is usually followed, the separate elements of work are identified in great detail and summed into the total cost per part. A typical, but simplified example, is the production of a simple fitting from a steel forging.
工业技术