增材制造增加了大型海洋结构的多功能性
快速构建不同迭代零件的能力——无需开发或购买昂贵的专用工具——是增材制造 (AM) 经常用于零件原型设计的原因。然而,随着材料和印刷技术的不断改进,越来越多的公司能够将增材制造的速度和多功能性扩展到最终用途部件中,特别是对于快速生产新设计的能力是一种资产的短期或一次性应用.
最近,两家公司已经证明复合材料 AM 技术可以为定制大型海洋结构提供解决方案,例如自主水下航行器 (AUV) 和摩托艇。
用于可定制 AUV 生产的大幅面 3D 打印
自主水下航行器是一种能够在水下行驶的无人机器人车辆,无需与船只进行物理连接或由人类操作员远程控制,并且通常配备有摄像头或传感器,用于国防、海洋研究或近海勘测应用中的各种用例。通常,AUV 的外壳要么包含一个大型金属压力容器,要么由热成型塑料或复合材料制成。然而,这两种选择都需要开发和购买专用工具,这可能很昂贵,并且限制了 AUV 客户可以适应的定制量。 AUV 制造商 Dive Technologies(美国马萨诸塞州昆西市)发现复合 3D 打印解决了传统制造的许多局限性。
2018 年,Dive Technologies 的联合创始人 Bill Lebo、Jerry Sgobbo 和 Sam Russo 决定成立自己的公司,设计并推出一款功能更强大的新型 AUV,以满足客户对长航时和大有效载荷能力的需求。
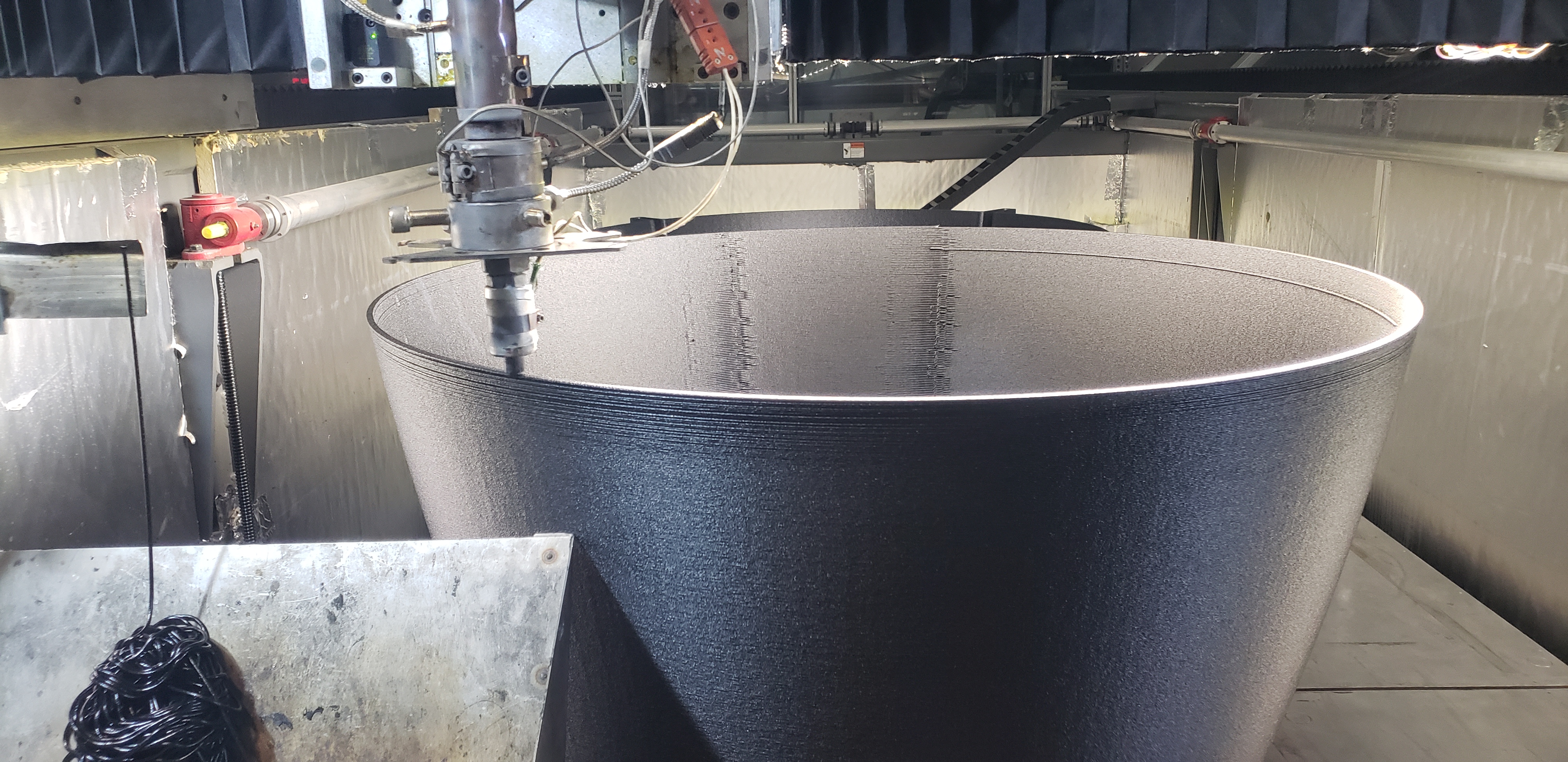
他们和他们的团队开发的是 DIVE-LD,这是一种 19 英尺长、4 英尺直径的商用 AUV,能够下潜至 6,000 米,航程可达 500 英里,承载高达 1 立方米的有效载荷。最初,该团队假设其车辆的最终结构将使用热成型塑料作为外壳。为了探索和测试设计,Dive Technologies 与橡树岭国家实验室(ORNL,美国田纳西州橡树岭)讨论了使用 3D 打印进行快速原型制作的问题。通过 ORNL,Dive 团队认识了大幅面增材制造 (LFAM) 专家增材工程解决方案(AES,美国俄亥俄州阿克伦市),并开始与 AES 团队合作开发 AUV 船体形式的制造工艺。>
然而,在 3D 打印原型的工作过程中,Dive Technologies 意识到 LFAM 快速生产成品的潜力 组件,而不仅仅是原型。 3D 打印原型组件不仅比预期更好地满足零件要求,而且在量产车辆中采用增材制造还可以节省模具成本,使 Dive 能够比使用传统方法更快地生产最终产品,并实现新的、更高水平的快速定制客户。
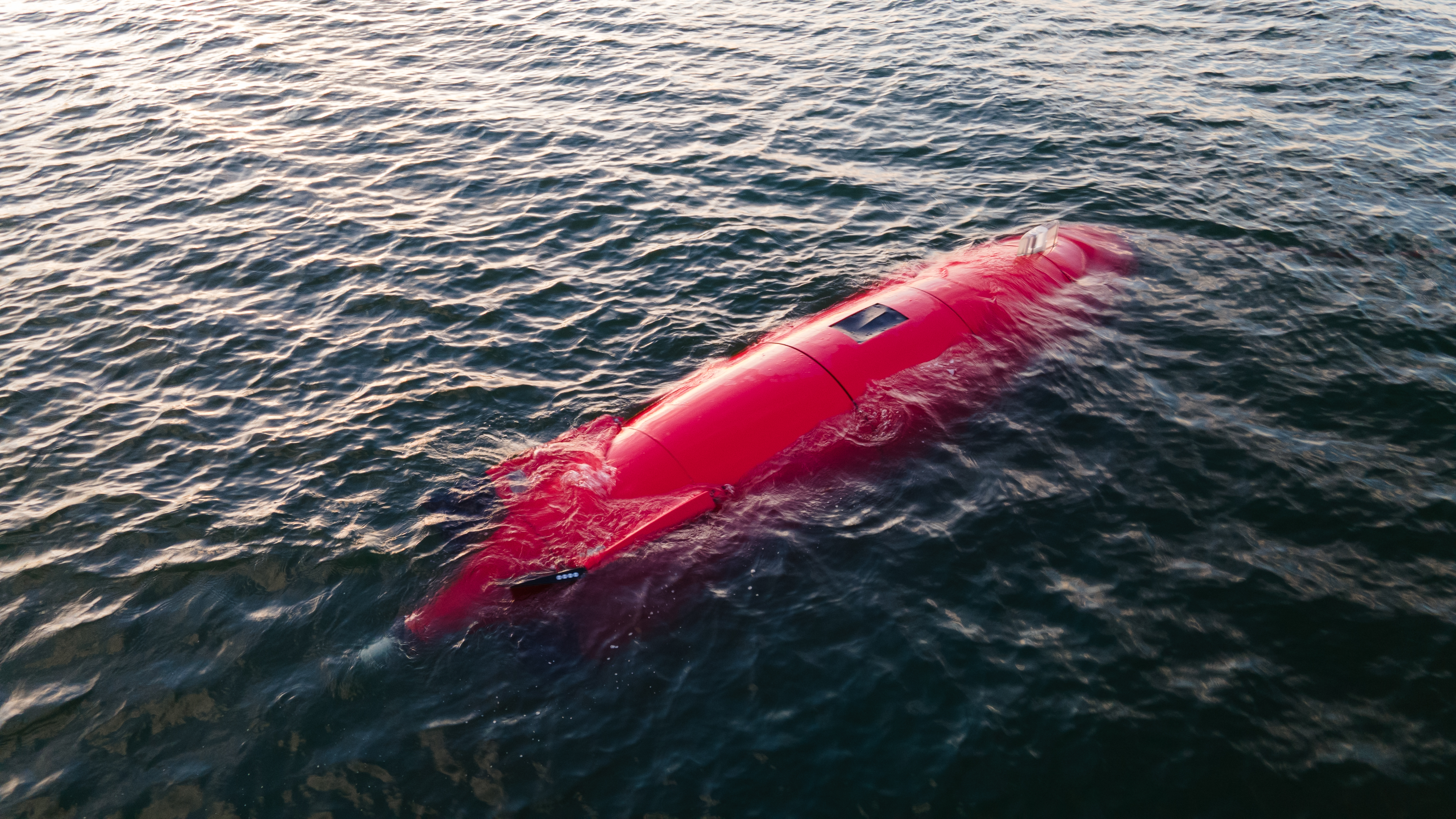
DIVE-LD 的外壳包括九个管状整流罩,使用 AES 的四台辛辛那提公司(美国俄亥俄州辛辛那提)大面积增材制造 (BAAM) 3D 打印机之一打印。这些整流罩由 Sabic(沙特阿拉伯利雅得)提供的短切纤维填充 ABS 打印而成。根据 AES 的联合创始人兼副总裁 Andrew Bader 的说法,AES 可以在不到两天的时间内打印出完整船体的所有部件。交付给 Dive 后,3D 打印的整流罩使用每个整流罩的四个紧固件进行机械固定,并进行涂层以产生光滑的流体动力学外表面。在 2020 年成功进行初步测试后,Dive 将在今年春天制造第一批客户车辆,并将于 2021 年 6 月交付第一批订单。
据 Russo 称,AM 已成为 Dive Technologies 未来车辆和产品价值主张的核心部分。与 Dive 的合作也是 AES 和复合 3D 打印的一大进步。 Bader 补充道:“通常当人们想到 3D 打印时,他们会想到原型、固定装置和工具,因此这展示了 3D 打印的其他功能。”
要了解有关 Dive Technologies 和 AES 的更多信息,请阅读“大幅面 3D 打印使 AUV 的免工具快速生产成为可能。”
用于多功能摩托艇设计的连续光纤增材制造和自动化
自 2015 年为其连续纤维制造 (CFM) 工艺申请专利以来,Moi Composites(意大利米兰)已经探索了其基于沉积的连续纤维 3D 打印 CFM 技术的一系列应用。 CFM 的标志包括 Moi Composites 的定制设计软件、机械臂的使用、紫外线固化和“混合”制造——更传统的复合材料层压在 3D 打印结构核心之上。最近,该公司通过名为 MAMBO 的演示摩托艇展示了其 CFM 技术,该技术是一种更具成本效益、更快和更具创新性的海洋结构设计的解决方案。
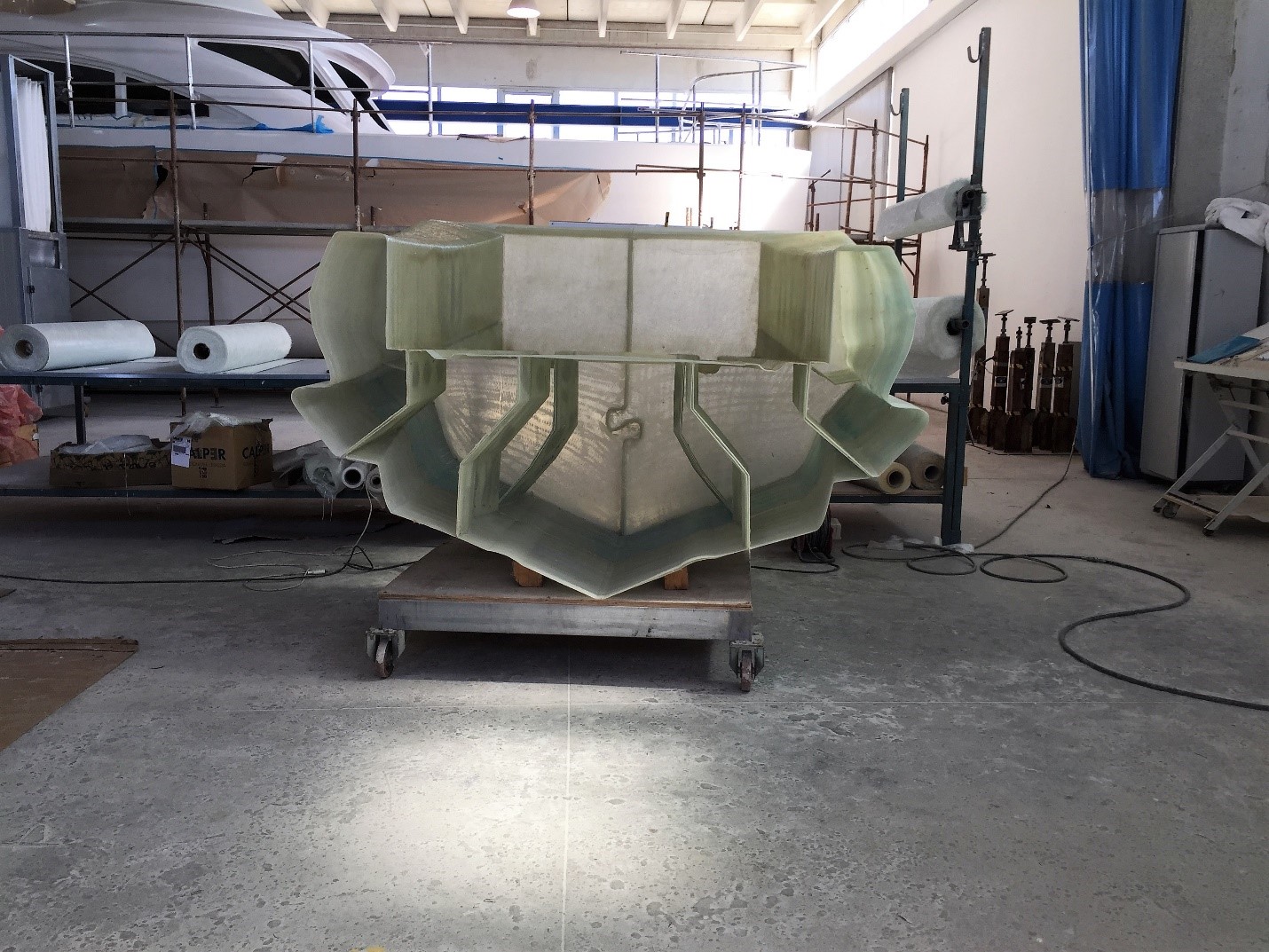
据 Moi Composites 联合创始人 Gabriele Natale 称,他和其他联合创始人 Michele Tonizzo 于 2017 年参加了热那亚船展,并意识到许多船体使用的工具成本和传统玻璃纤维灌注工艺限制了船舶设计师探索新产品的能力。和更复杂的设计。 Natale 意识到他们的无模连续纤维 3D 打印技术可能是一种可行的解决方案,“从那时起,我们开始制定计划,并开始与海洋行业的合作伙伴会面。”
由此产生的 MAMBO 船长 6.5 米 x 宽 2.5 米,干重约 800 公斤,配备导航系统、软木地板、白色真皮座椅和 115 马力发动机。 Moi Composites 与海洋设计工程工作室 MICAD(意大利莱切)合作开发了该船的结构设计概念,将有机形状结合到其结构元素中,其灵感来自 Sonny Levi 著名的 Arcidiavolo 双体船。 Autodesk (San Rafael, CA, U.S.) Fusion 360 CAD和NETFABB增材制造软件用于组件的设计和流体动力学分析。
船体和甲板由欧文斯科宁(美国俄亥俄州托莱多)提供的单向无碱玻璃和乙烯基酯树脂印刷而成,设计制造成 50 个不同尺寸的独立部分。一半的截面在 Moi Composites 的米兰工厂打印,另一半在位于英国伯明翰的合作伙伴 Autodesk 先进制造工厂 (ACF) 中打印 Moi Composites 的 CFM 3D 打印技术和双 Kuka(德国奥格斯堡)机器人用于设施。根据 Autodesk 增材制造团队的研究经理 Dominique Müller 的说法,Autodesk 技术中心的 CFM 系统允许快速打印船只,还使 Autodesk 能够更好地了解 Moi 使用 Autodesk 软件远程驾驶的技术.所有组件的总打印时间约为两个月。
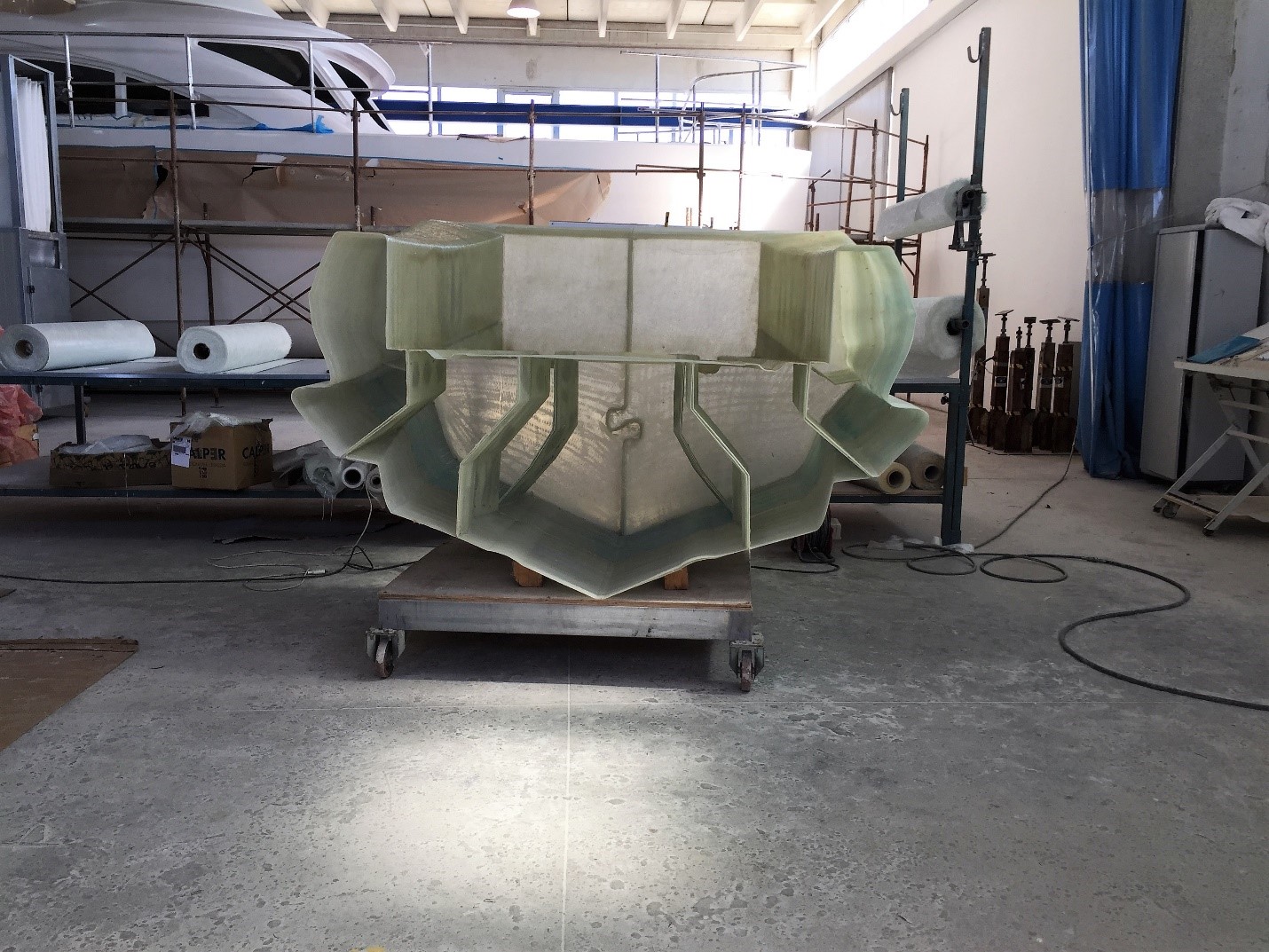
打印出来的零件被运往意大利米贾诺的 Catmarine 造船厂,在那里将它们拼凑在一起并粘合在一起。在类似于 Moi 用于假肢和其他部件的混合制造过程中,然后通过手工叠层将整个船体与以 PVC 泡沫为芯的额外玻璃纤维/聚酯层层压在一起,Natale 说,其厚度随结构而变化。在船体和甲板完全组装、打磨并涂上凝胶后,Moi Composites 的合作伙伴为这艘船配备了推进、导航和其他系统,以完成这艘船。
最初的海上试航和稳定性测试于 2020 年秋季进行,MAMBO 的航速最高可达 26 节; Moi Composites 计划在 2021 年夏季继续进行海试,以取得该船的认证。

“增材制造、数字化和自动化可以加速新概念和未来项目的创建,因为对于您想要设计的每艘船,您都需要创建一个新模具。使用此技术,您可以轻松修改 3D 模型并再次打印。这对于短期或一次性船只来说是完美的,”Natale 说。
有关 MAMBO 的更多信息,请阅读“MAMBO 测试水域以 3D 打印大型海洋结构。”
树脂