用于 RAPM 压缩成型的新型预浸料
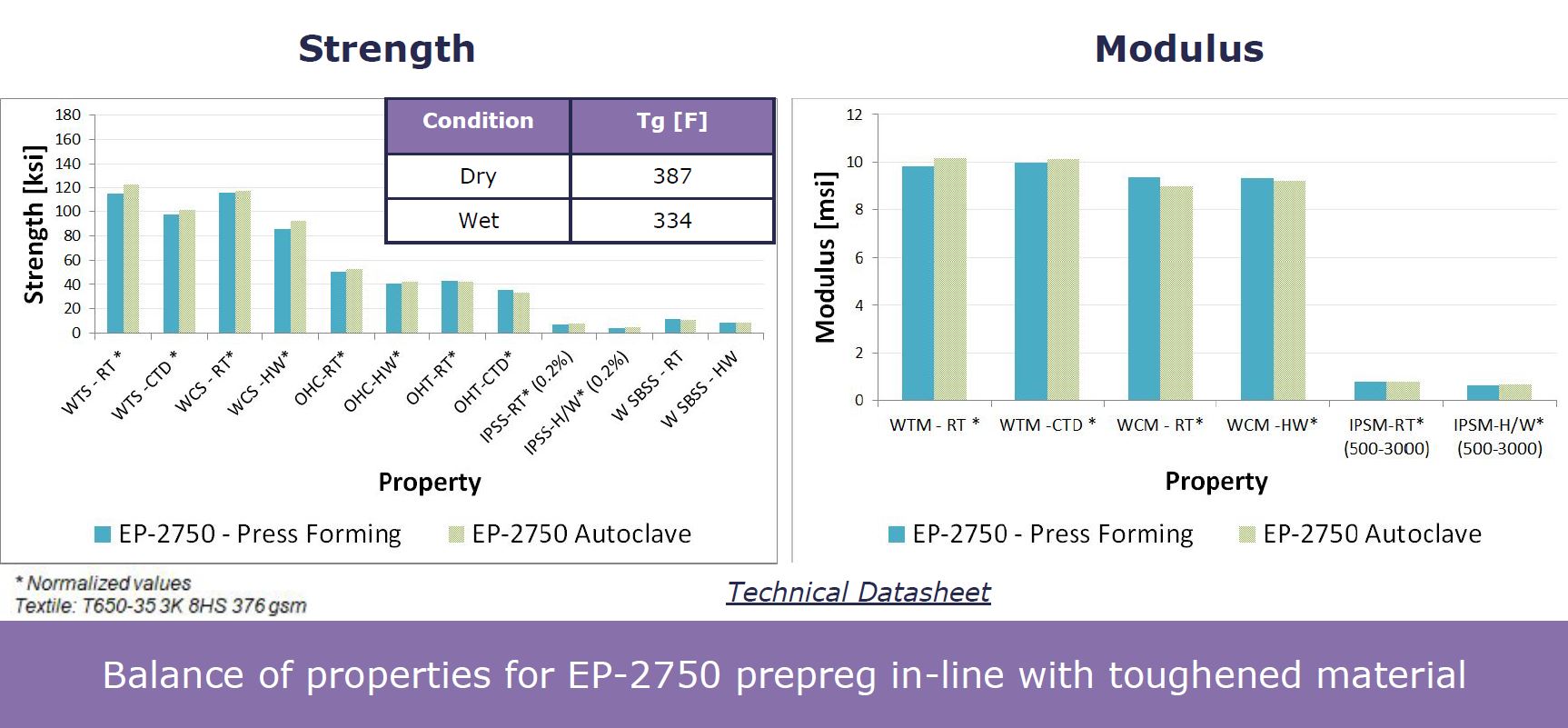
数十年来,碳纤维/环氧树脂预浸料一直是航空航天复合材料的基准材料,因为它具有高机械性能和精确的树脂/纤维含量,以及易于铺层和高压釜固化处理。然而,随着飞机和城市空中交通 (UAM) 制造商探索更高的生产率和更低的成本,压缩成型具有吸引力,与高压釜相比,它缩短了周期时间并提高了效率。在最简单的情况下,压缩成型包括预热成型材料,将其放入开放的工具腔中,并在温度下用液压固结,在此期间液体热固性材料转化为固体。然后将固化的零件弹出以进行任何所需的修整和精加工步骤。

将压制成型和预浸料相结合,不仅提供了具有预浸料性能和易于处理的高效、高速率工艺,还避免了在树脂灌注和树脂传递成型等工艺过程中用液态树脂填充干增强材料的一些复杂工艺动态(RTM)。特别是对于较小的飞机结构,预浸料压制成型可提供 <30 分钟的节拍时间,同时仍能实现高质量、复杂几何形状的零件。
索尔维复合材料公司(美国乔治亚州阿尔法利塔)是波音公司(美国伊利诺伊州芝加哥)领导的快速高性能制造 (RAPM) 计划的主要合作伙伴。 RAPM 是美国国防高级研究计划局(DARPA,美国弗吉尼亚州阿灵顿)于 2015 年推出的可定制原料和成型 (TFF) 计划的“成型”部分。其目标是实现快速、低成本和敏捷制造小型、形状复杂的复合材料部件,并提高复合材料在国防应用中与机加工铝竞争的能力。
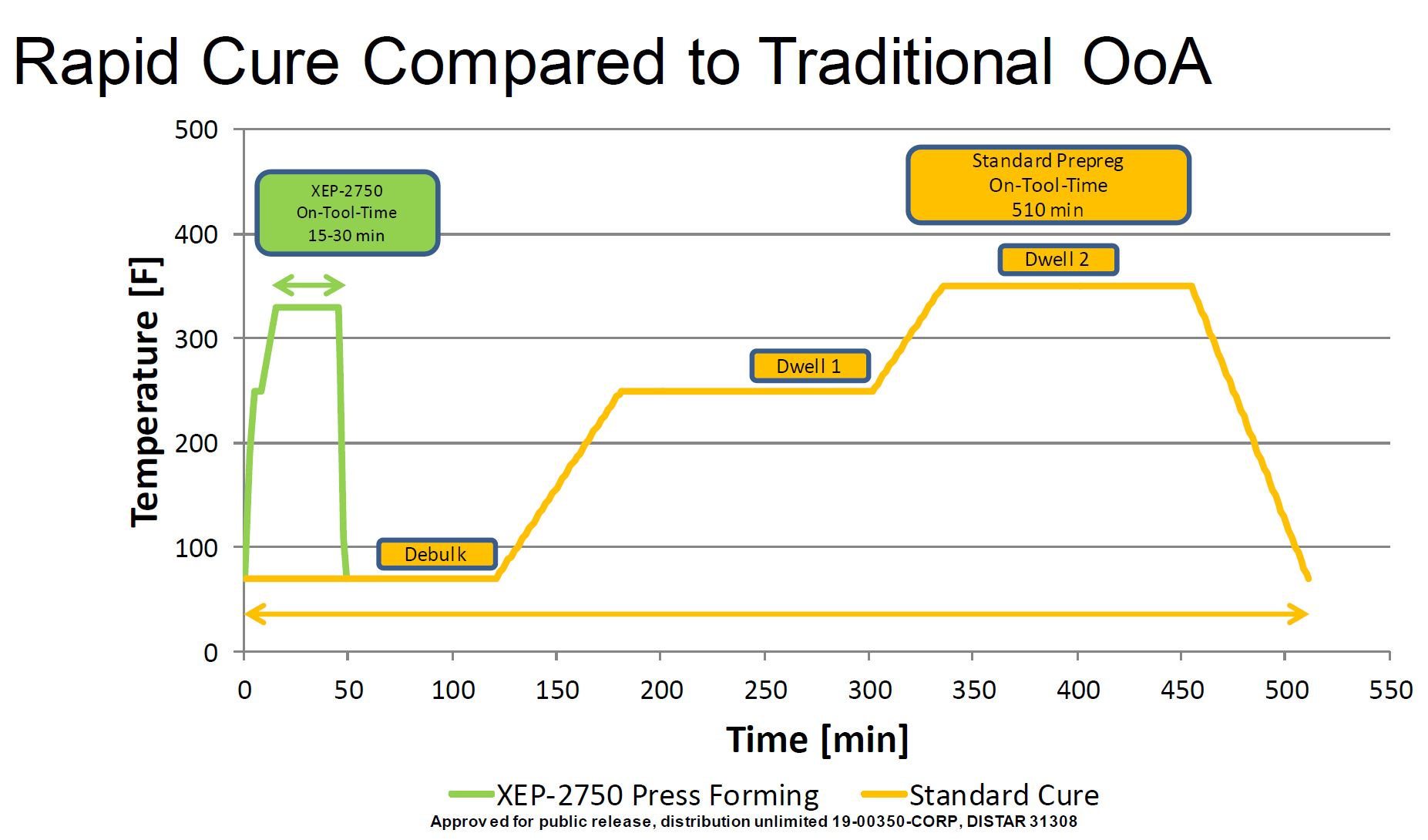
作为波音公司国防应用领域的长期供应商,索尔维还是商业航空航天新型解决方案的领导者,例如非高压釜 (OOA) 环氧预浸料 CYCOM 5320-1,以及汽车行业,例如1 分钟节拍时间,乙烯基混合 SolvaLite 730 预浸料。
RAPM 是 Solvay 测试和改进其实验系统 XEP-2750 的绝佳机会,该系统现已商业化为 CYCOM EP2750,该系统旨在连接航空航天和汽车复合材料的生产。该博客是 2020 年 5 月专题“革新复合材料成本范式,第 2 部分:成型”的在线侧边栏,回顾了该开发以及所使用的压缩成型工艺以及 CYCOM EP2750 为航空航天和汽车复合材料制造商提供的功能。>
此博客的参考资料包括:
- Timothy J. Luchini 的“航空航天生产部件的弹簧框架压力机制造”
1
, 亚历杭德罗·J·罗德里格斯
2
, Scott A. Rogers
2
, Aurele Bras
3
, 亚当·怀索尔
3
, 理查德·罗素
3
, 斯科特卢卡斯
2
, Gail L. Hahn
1
. SAMPE 会议论文集。北卡罗来纳州夏洛特,2019 年 5 月 20 日至 23 日。
- Aurele Bras 撰写的“用于高速压缩成型的航空航天结构零件几何形状的挑战”
1
, 亚历杭德罗·J·罗德里格斯
2
, 理查德罗素
1
, Timothy J. Luchini
3
, 特拉维斯亚当斯
3
, 亚当·怀索尔
1
, Scott A. Rogers
2
, 斯科特卢卡斯
2
, Gail L. Hahn
3
. 材料与工艺工程促进会——北美。SAMPE 会议论文集。华盛顿州西雅图,2020 年 5 月 4 日至 7 日。材料与工艺工程促进会——北美。
- “用于压缩成型的结构 xEP-2750 预浸料的快速高性能成型”作者:Timothy J. Luchini 1 , 亚历杭德罗·J·罗德里格斯 2 , Scott A. Rogers 2 , Aurele Bras 2 , 亚当·怀索尔 2 , 理查德罗素 2 , 斯科特卢卡斯 2 , Gail L. Hahn 1 . SAMPE 2019。
1 波音公司,圣路易斯,密苏里州 63134, 2 Solvay Composite Materials,美国加利福尼亚州阿纳海姆和 3 索尔维复合材料,英国 Heanor
- CompositesWorld 网络研讨会:“用于高速航空航天复合材料制造的汽车工艺”,作者为 Alejandro Rodriguez,Solvay Composite Materials,美国加利福尼亚州阿纳海姆
材料和工艺目标
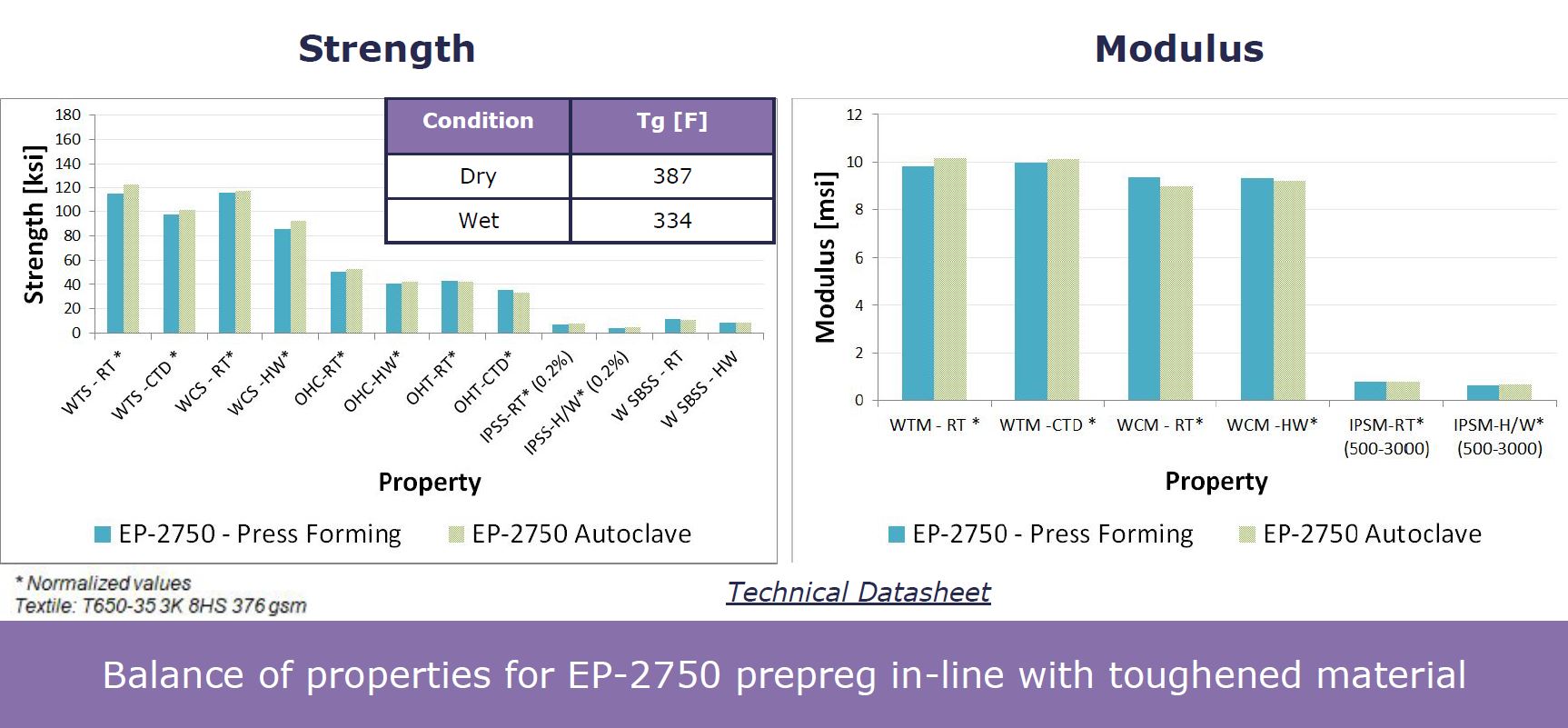
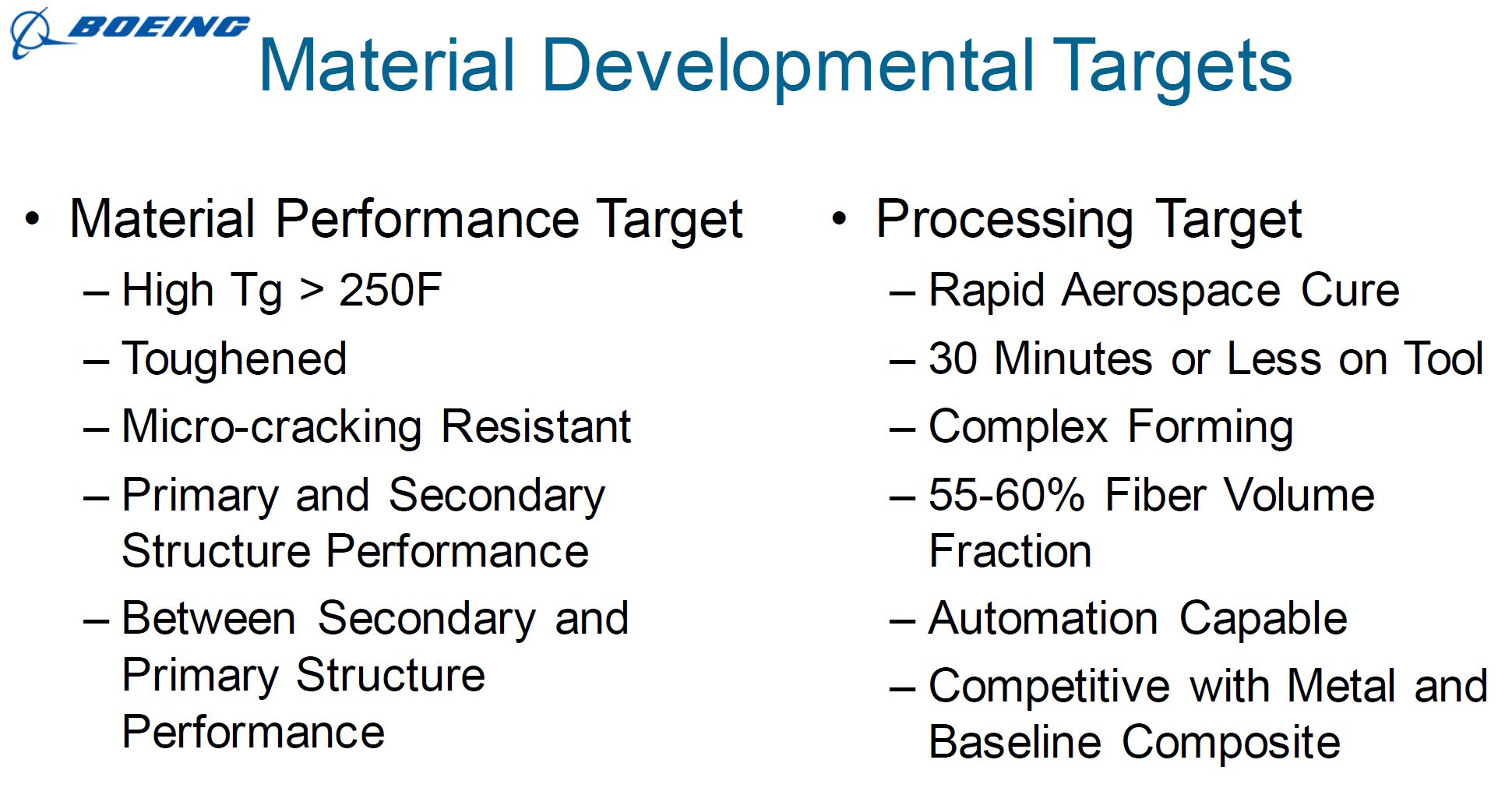
CYCOM EP2750 的开发是为了满足波音为航空增韧环氧树脂设定的性能目标,表现出高达 350°F 的玻璃化转变温度 (Tg) 的平衡、良好的缺口特性——例如,裸眼压缩 (OHC) 和裸眼张力(OHT) — 和耐溶剂性。这种新型预浸料适用于一级和二级航空结构,并与多种增强材料(例如碳纤维和玻璃纤维)兼容。
CYCOM EP2750 还具有使用自动化处理和压缩成型扩大生产的能力。这包括 330-370°F 下 15-30 分钟的工具固化时间,以及 350°F 下 1 小时的后固化。这种 30 分钟或更短的节拍时间使每个工具的年产量达到 10,000 个零件。
索尔维在 RAPM 计划期间使用了两种压缩成型方法:弹簧框架成型和双隔膜成型 (DDF)。两者都使用保持扁平坯料并在将其穿梭进入匹配的金属工具腔之前通过红外 (IR) 预热阶段的原理。然后压机按照自动程序关闭钢模,并在工具上的剩余时间内对预浸料施加全压。
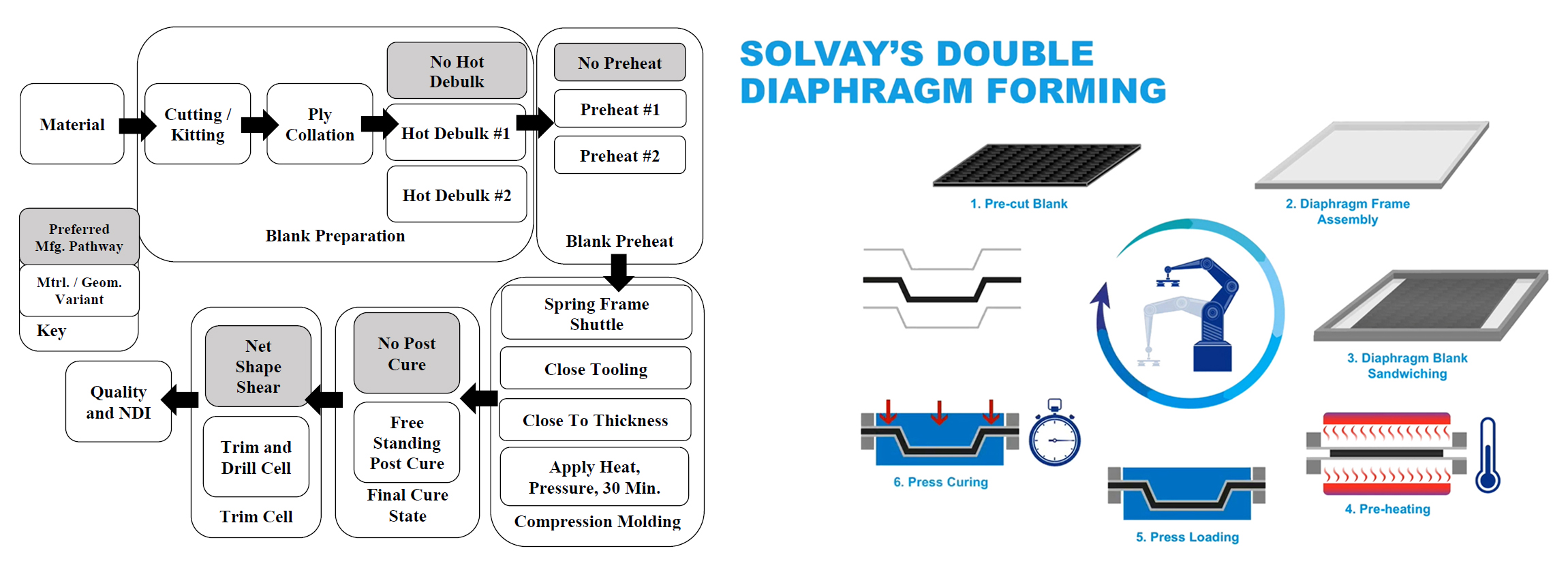
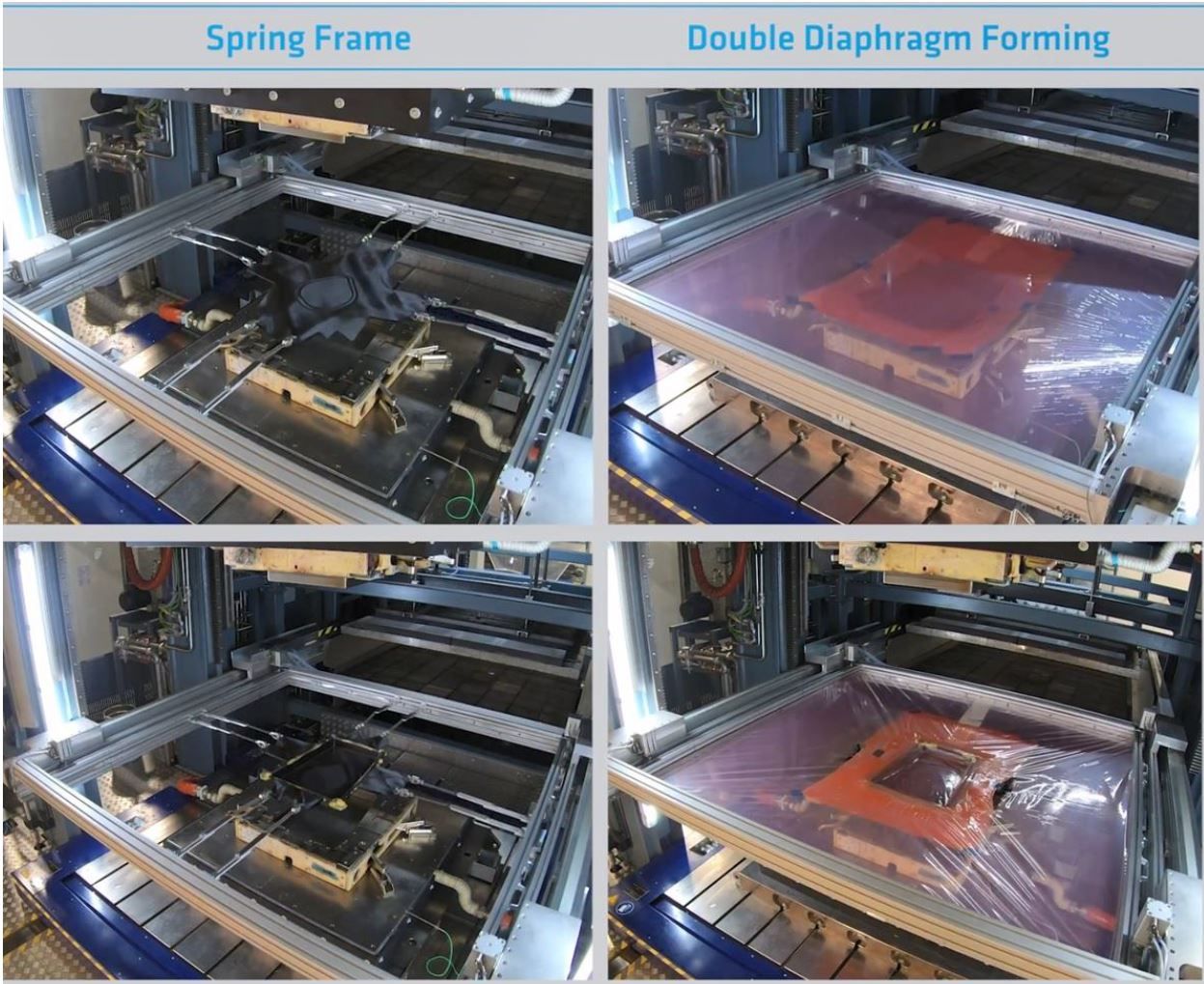
弹簧框架成型和 DDF 都使用匹配的金属工具,并提供热进热出方法,消除工具加热和冷却,以实现高速生产。两者都用于成功地成型多种类型的复杂几何零件,包括垫板、垂直法兰和厚度从 3.8 到 8.9 毫米的变化。这些零件是在英国 Heanor 的 Solvay 应用中心制造的 尽管在 RAPM 期间不可用,Heanor 现在拥有从预浸料辊到成型零件的全自动压缩成型线,使用 EP2750 和 takt 制造的航空零件的节拍时间为 15 到 60 分钟对于使用汽车预浸料的中小型零件,时间为 3 分钟或更短。索尔维认为 DDF 流程有多种好处,包括:
- 消除预成型步骤——从 2D 坯料到 3D 零件
- 无需脱模或清洁
- 与高压灭菌器相比,减少辅助材料(例如,呼吸器、放气器、装袋、胶带)
- 改进了购买到飞行与弹簧框架成型相比,因为连接弹簧夹所需的多余材料更少。
完全浸渍与部分浸渍保持压力
EP2750 有助于压缩成型的特性包括其低粘性用于自动取放处理以及与 CYCOM 5320-1 相比完全浸渍的性质,CYCOM 5320-1 部分浸渍以促进边缘呼吸,这是使用 OOA 处理的无空隙层压板所必需的。然而,由于施加了更高的压力,压缩成型利用了非常快速的强制树脂流动——例如,高达 350 psi(EP2750 的典型最大值),而高压釜加工中常见的 35 psi 和仅真空 OOA 加工中的 14.7 psi。
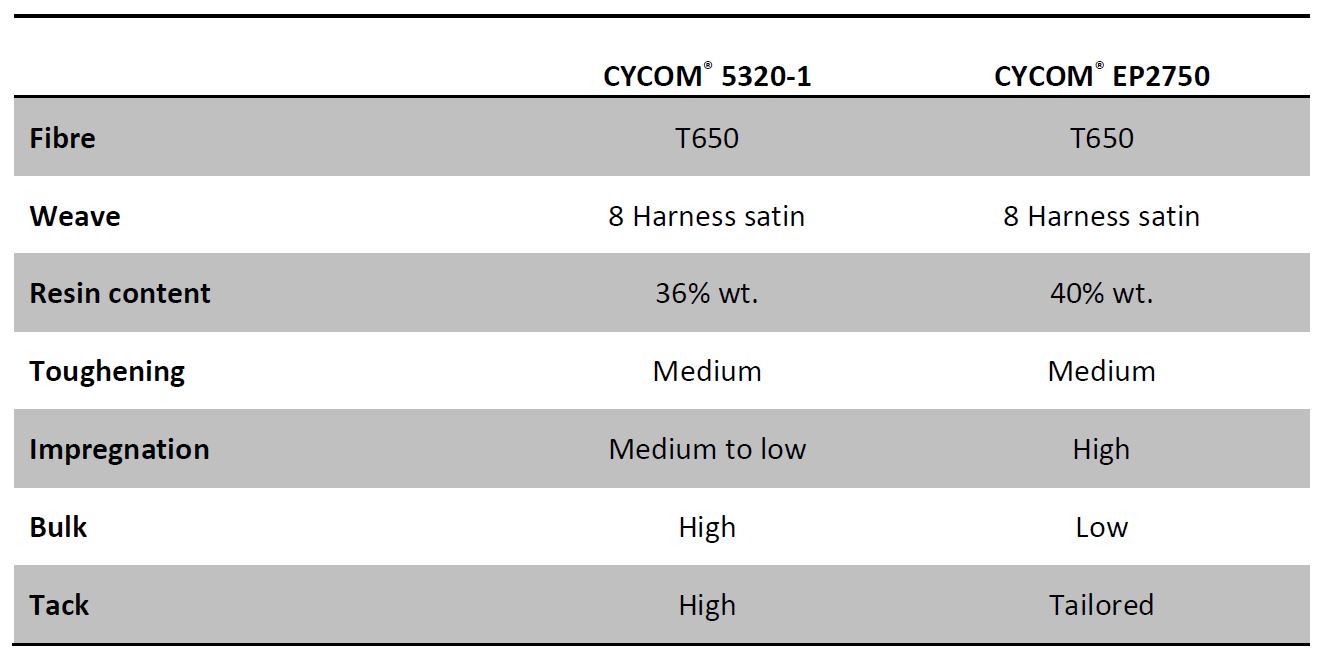
具有更充分浸渍的预浸料,即使树脂含量仅略高(CYCOM EP2750 中为 40%,而 CYCOM 5320-1 中为 36%)——在匹配的金属工具腔中压实和固化期间保持静水压力,从而降低风险干燥区域、固化部件厚度(CPT)不一致、起皱等缺陷,同时确保良好的表面质量。
值得注意的是,索尔维开发了一种获得专利的变压器薄膜,用于在使用树脂含量较低的 CYCOM 5320-1 预浸料时增加静水压力。将变压器薄膜应用于压缩成型之前的零件叠层,可增加树脂含量,并有助于使 CPT 达到 RAPM 零件成型试验的要求。
RAPM 零件成型试验
正如 CW 在 2020 年 5 月的专题文章中所解释的那样,CYCOM EP2750 是在 RAPM 的热固性预浸料轨道中试用的主要材料之一。包括在初始制造和开发阶段试用的探路者部件
TS-RAPM-001 和 -009 珠状检修面板、TS-RAPM-002 肋和 TS-RAPM-003 弯曲 C 形槽。这些零件在波音公司(全球多个地点)设计,模具在 C-Con 有限公司(德国慕尼黑)制造,零件在英国 Heanor 的 Solvay 应用中心制造,然后在美国加利福尼亚州 Solvay Anaheim 和美国密苏里州圣路易斯波音公司
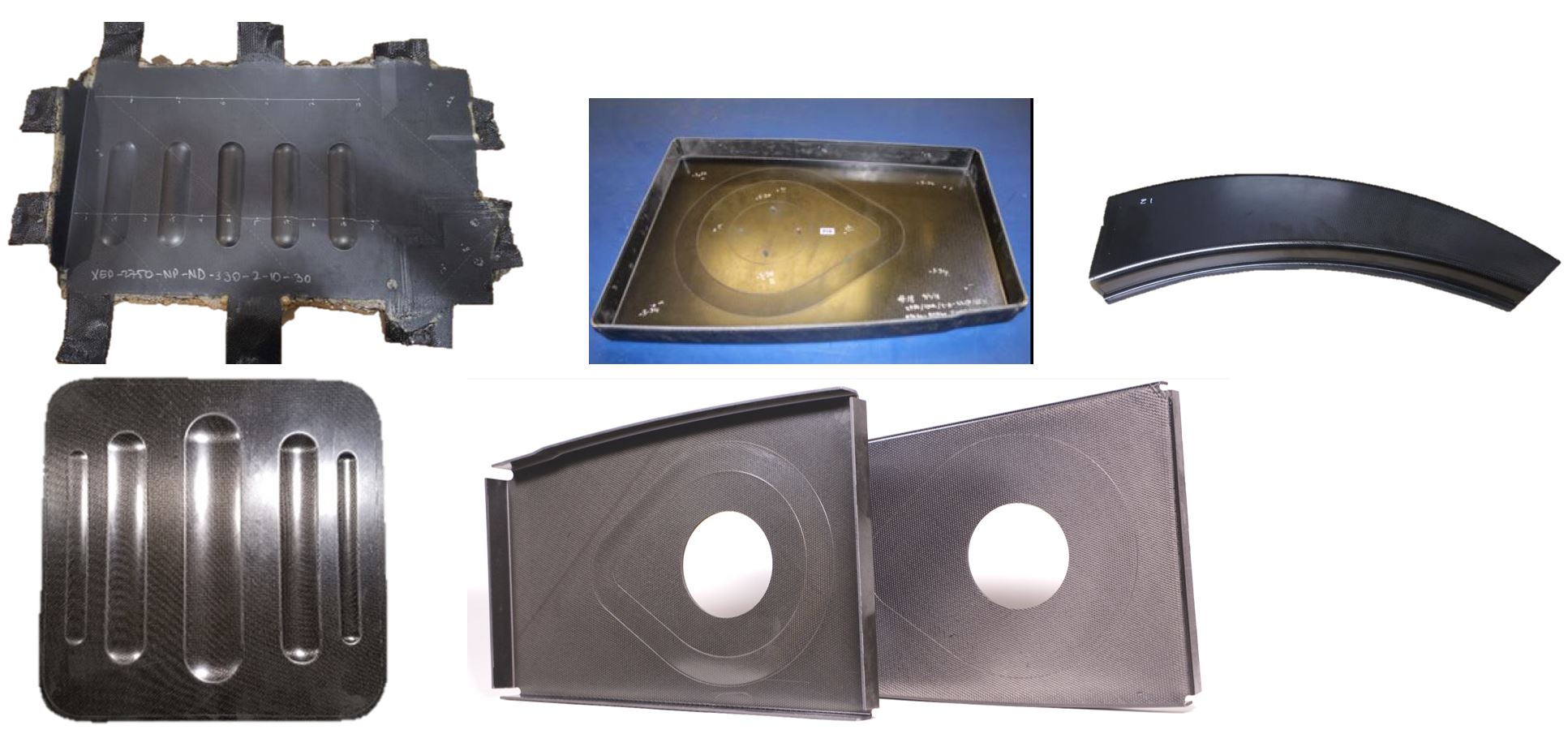
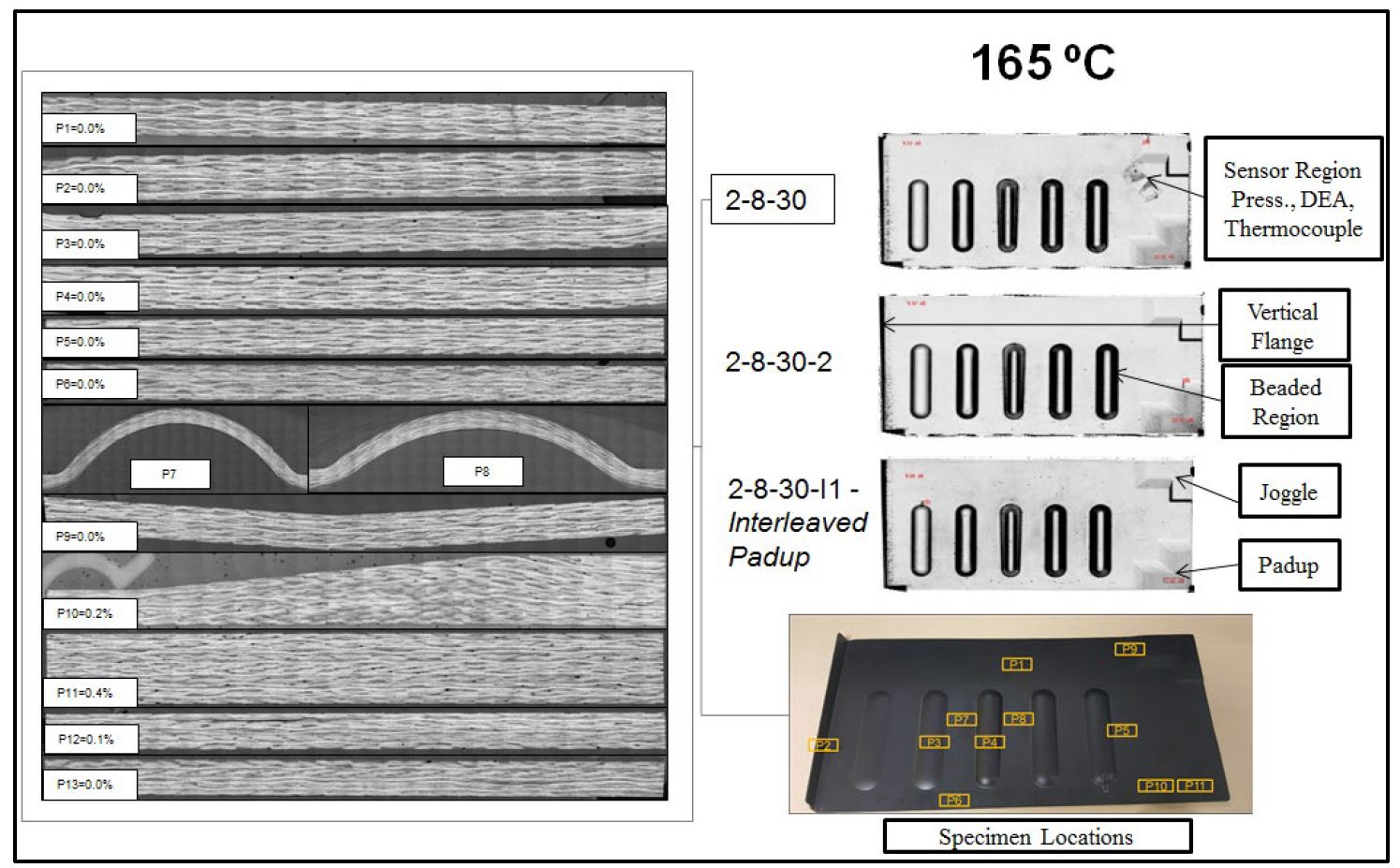

使用无损检测 (NDI) 评估表面质量,并对选定的面板进行横截面的孔隙率、短光束剪切、纤维体积分数、树脂含量、固化程度和玻璃化转变温度。
由于压缩成型的高固结压力,很容易实现低于 0.5% 的孔隙率水平。虽然必须针对每个不同的部分优化工艺参数,但一旦锁定,该工艺被证明是可重复的。
TS-RAPM-009 珠饰面板
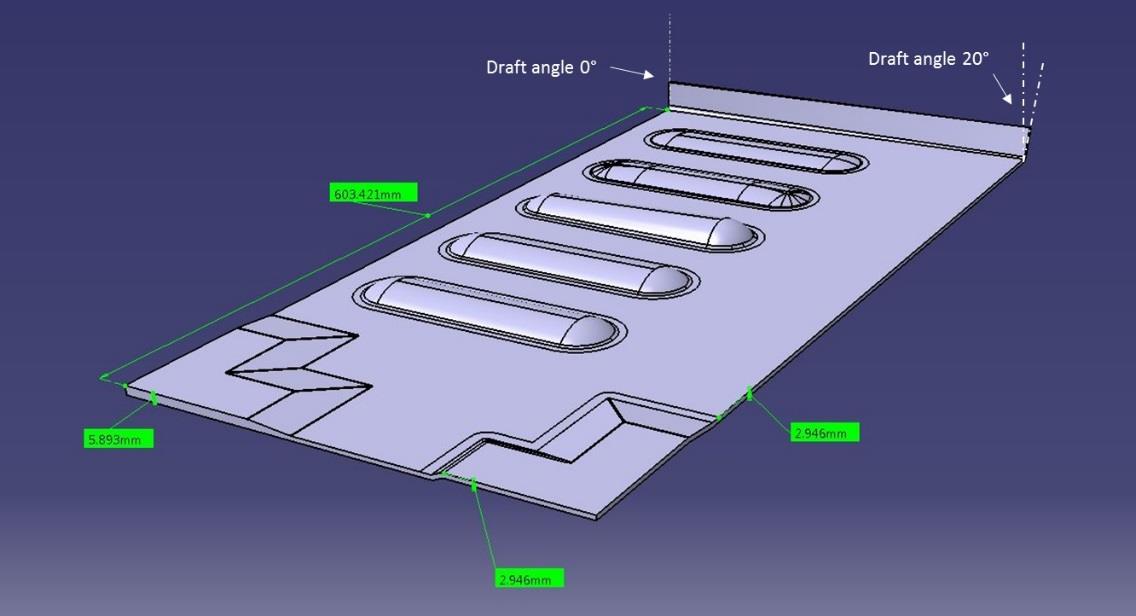
这个 600 毫米长的扁平部件具有各种几何形状的平行珠。一个角落的厚度从 3 毫米增加到 6 毫米(垫高),而对角的特点是厚度不变。相对的边缘包括一个垂直翼缘,其拔模角从 0° 到 20° 线性变化。
垫板滑动
最初的试验是在叠层表面堆叠垫层的情况下进行的。然而,由于填充层位于零件边缘附近,它们可能会被挤出零件,从而导致固化过程中的低压区域和孔隙率。解决方案是在层压堆叠内交错填充层。在后面的零件中没有看到打滑和孔隙率的风险,这些零件远离边缘并被周围材料有效锁定。
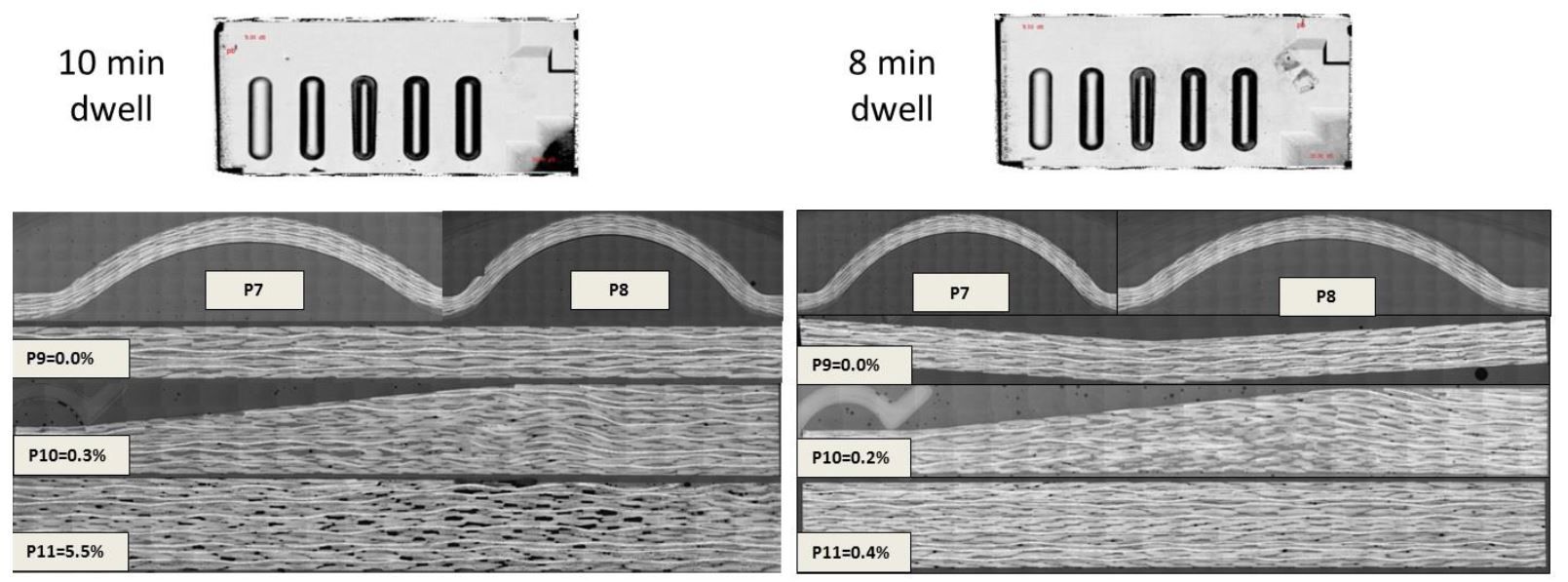
孔隙率随停留时间
如果停留时间太长,也会看到孔隙率增加。使用 8 分钟停留时间制成的串珠面板的空隙率低于使用 10 分钟停留时间制成的面板。在填充区域尤其如此,10 分钟停留时间为 5.5%,停留 8 分钟时间为 0.4%。较短的停留时间保持较高的树脂流动,有效地润湿纤维并通过固化维持工具腔内的压力。
较长的停留时间允许树脂流动和压力降低,特别是在垫块区域,因为它靠近工具腔的边缘,没有剪切边缘或截面减少。因此,工具腔中的压力在零件边缘处降低,尤其是在横截面较大的较厚区域。这里没有压力也加剧了垫层滑动的风险。 “在设计工具时,工具腔周围截面的减少将有助于建立和保持压力,特别是对于厚度不同的零件,”波音公司研究员兼 RAPM 项目首席研究员 Gail Hahn 解释说。 “您需要呈现某种形式的挤压或密封,以促进腔体中的静水压力状态。”
TS-RAPM-002 肋
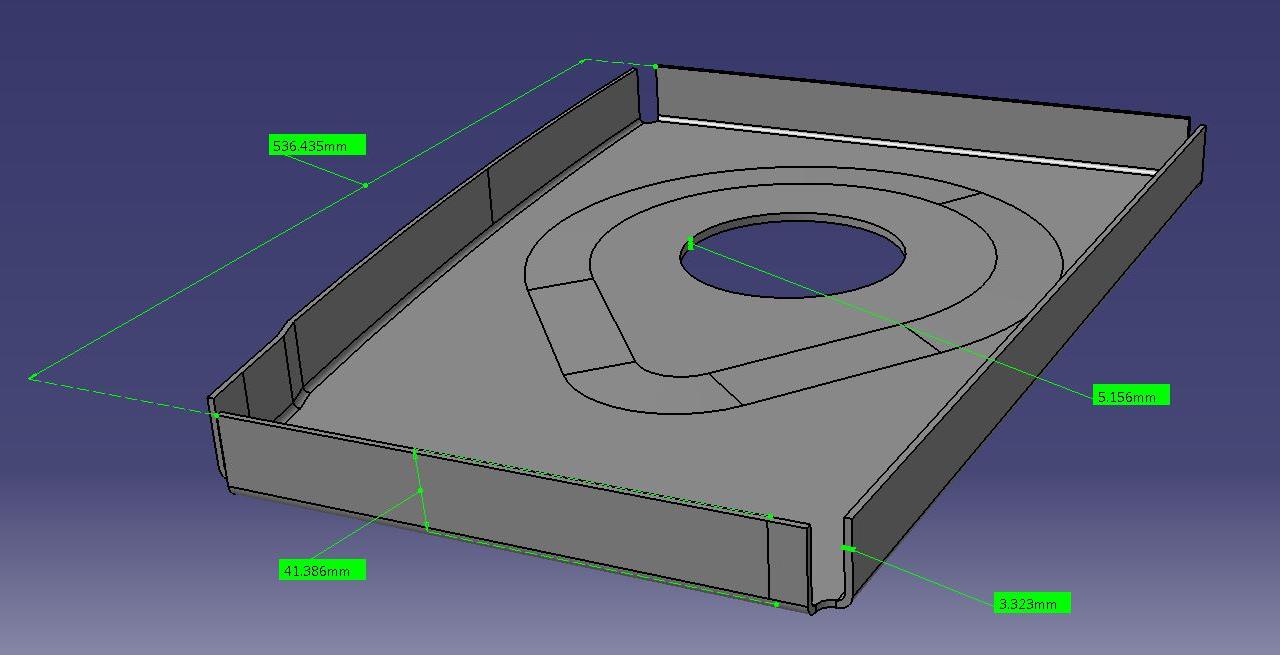
确定 TS-RAPM-009 珠饰板的加工参数后,对 TS-RAPM-002 肋条重复该过程,其最长边缘为 540 毫米。肋在中心的厚度从 3.3 毫米增加到 5.2 毫米,最终修整部分的拉深深度为 42 毫米。所有四个边缘都有垂直法兰。请注意,弹簧补偿角度是在串珠面板试验期间确定的,然后应用于肋的工具几何形状。串珠面板试验还导致更高的张力能力和弹簧框架上的弹簧位置模块化。
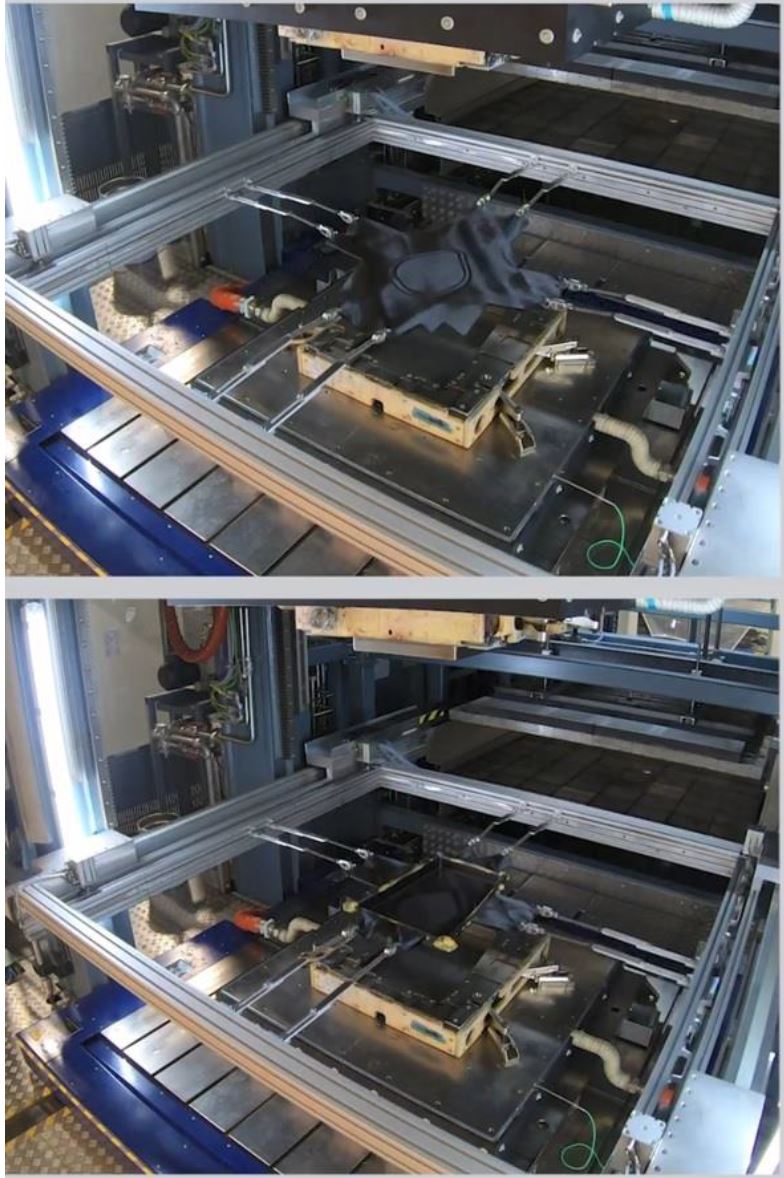
夹具的多余材料
肋条是使用弹簧框架成型和 DDF 制成的。由于肋的深拉,需要多余的材料来连接弹簧框架夹,但使用 DDF 时可以减少这种情况。另一个问题是工具设计限制了弹簧夹在工具腔内紧邻的空间。
CPT 的变化
肋条平坦部分的固化层厚度 (CPT) 高于其垂直边缘。有理由认为零件的几何形状将树脂保持在中央平坦区域内,并指出垂直法兰充当树脂密封。这有助于中心平坦区域的压实和零件精加工。然而,垂直法兰在工具闭合过程中受到强烈的剪切,这会导致表面粗糙但不会产生孔隙(见下面的孔隙率数据)。 CYCOM EP2750 是一种较低的松散材料,有助于减轻这种影响——其较低的厚度减少了剪切。
纸幅厚度随预浸料树脂含量的变化
质量调查显示可重复的肋条具有 <0.1% 的孔隙率和最小的纤维起皱/波纹度。然而,虽然假设零件厚度变化会通过匹配的模具加工最小化,但对材料加工参数和成品零件 CPT 的审查表明,虽然加强筋垂直翼缘中的工具间隙是固定和一致的,但腹板厚度可以作为函数变化预浸料树脂含量(小于 +/-2%)和工艺的影响 - 由于允许树脂在腔内迁移,因此法兰和腹板之间的 CPT 可能会有所不同。
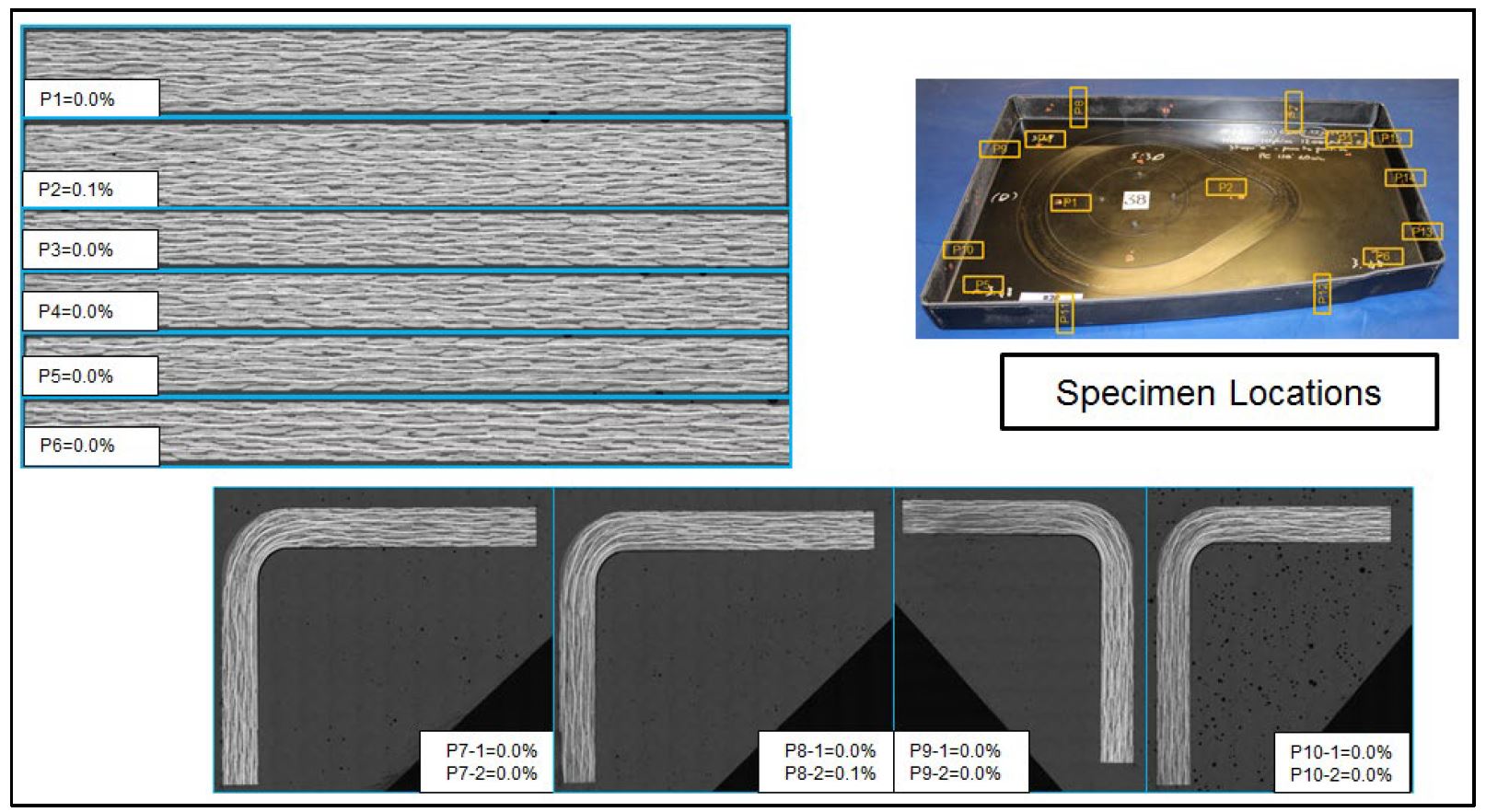
TS-RAPM-003 弯曲 C 形通道
这部分长 640 毫米,最后修整件上有一个 40 毫米深的 U 形截面。截面内半径大于外半径,厚度从窄端的6.6毫米增加到宽端的8.8毫米。由于其厚度,C 通道部件比前面讨论的部件重得多。因此,弹簧框架比以前的零件需要更多的连接点。
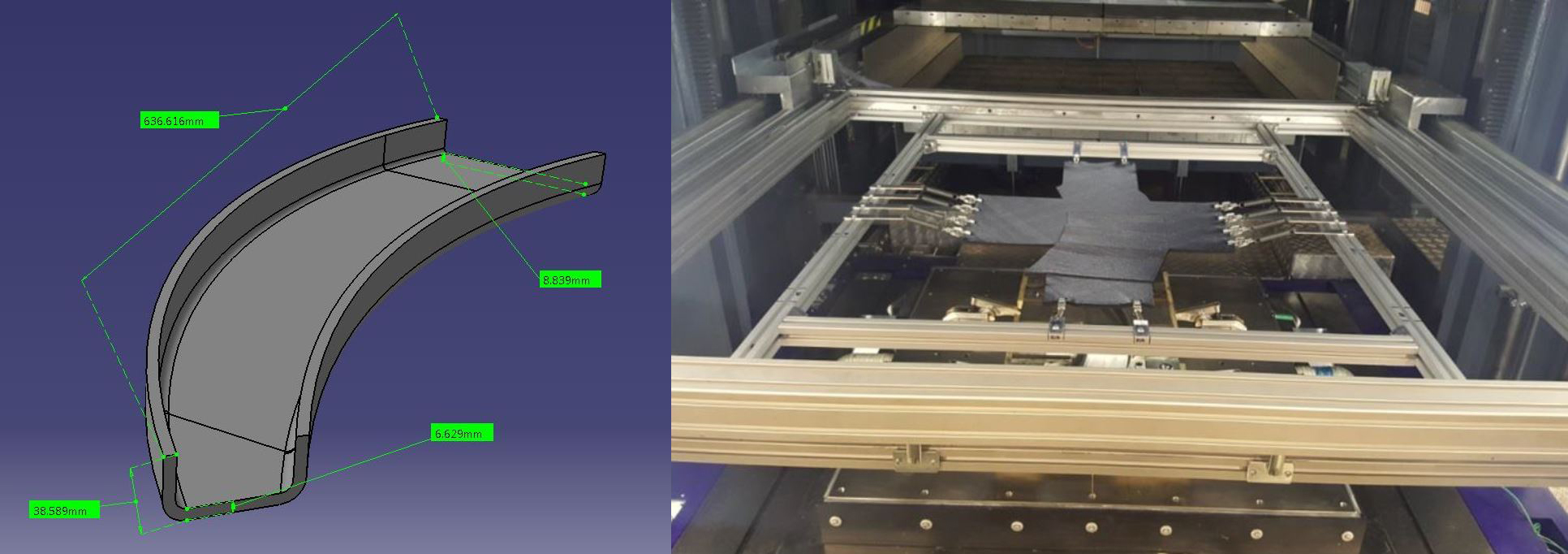
双重保压以在厚部件中保持压力
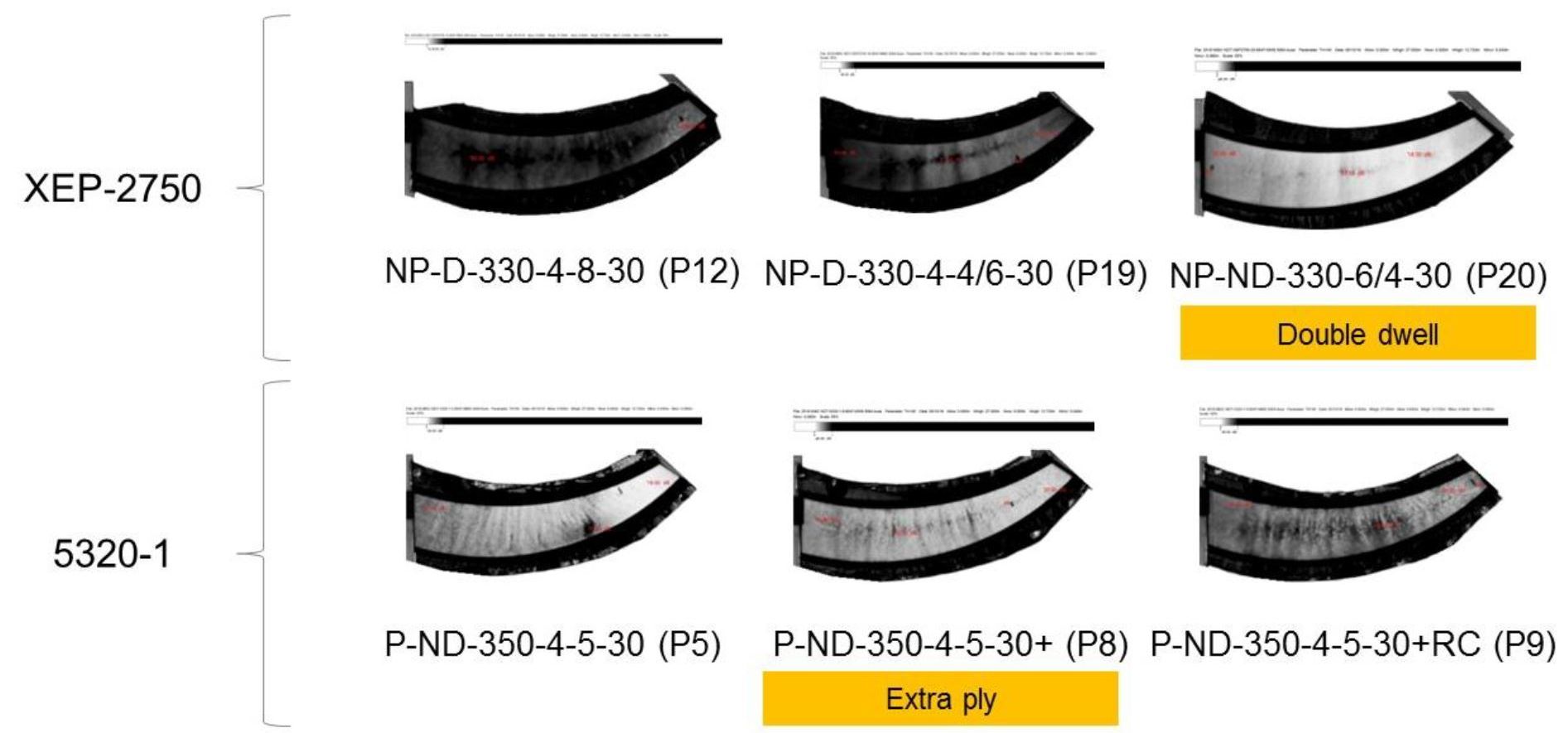
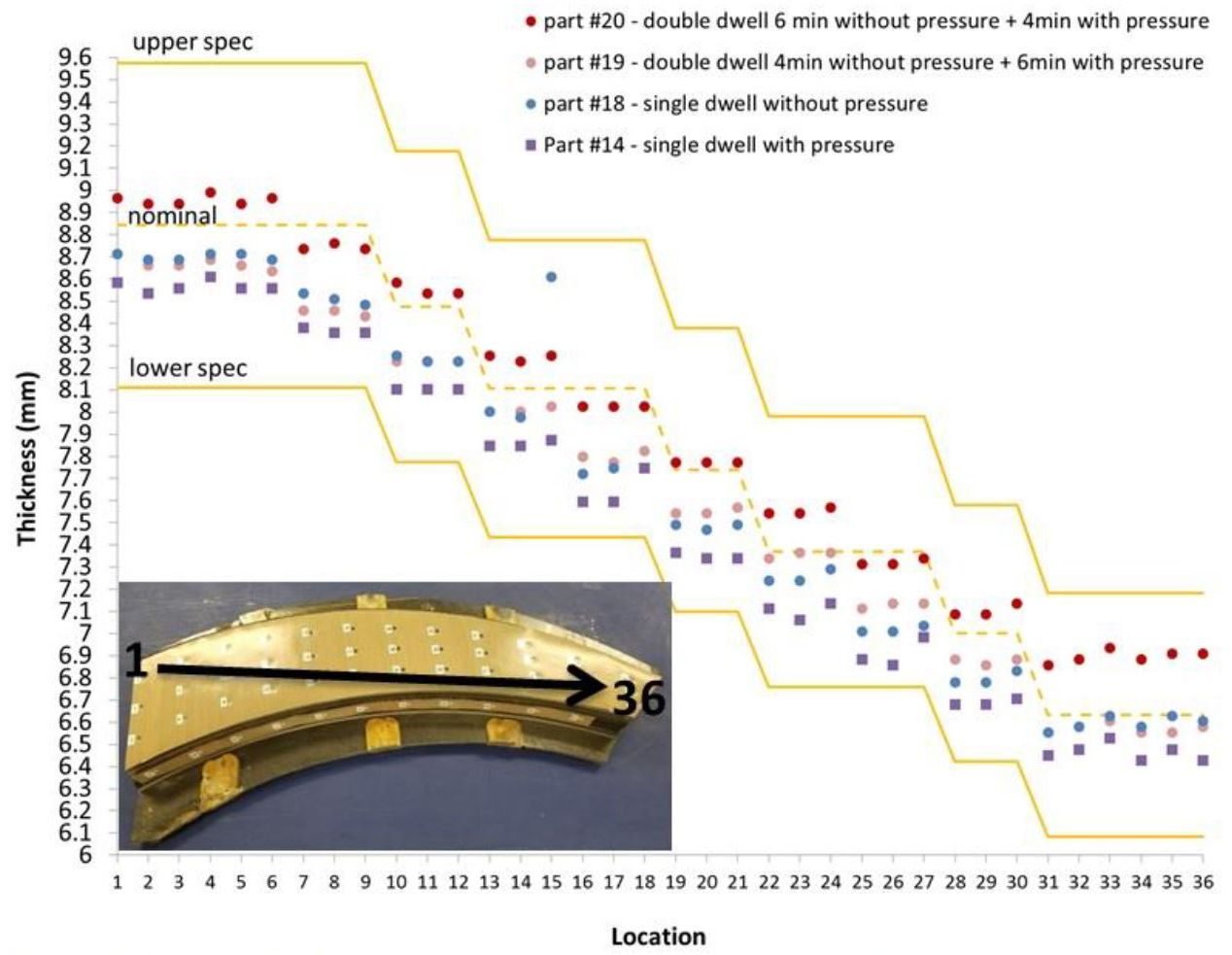
对于使用预固结坯料的零件,成型零件的 C 扫描突出显示了从内半径向外半径传播的皱纹。灰度表示皱纹也带有孔隙。
CYCOM EP2750 预浸料零件的这些皱纹和孔隙通过使用“双停留”去除 过程。这包括在材料粘度增加后立即在保压期间施加一定量的压力。 “这是使用印刷机提供的数据和流程开发过程中的工具确定的,”Hahn 解释说。 “基本上,在完全施加压力之前有两个逐步建立压力的步骤。因此,压力-时间曲线具有与树脂粘度曲线相似的形状。在体积厚度处的初始停留用于提高树脂粘度,以防止材料装料 [坯料或预制件] 变薄。如果装料的厚度很大,则使用两次保压来防止由于树脂收缩而造成的压力损失。第一次停留在 X 的间隙,第二次停留在 Y 的间隙,Y
上面的图 18 显示了双停留对 C 通道零件厚度的影响。使压力与树脂粘度相匹配,使更多的树脂能够保留在部件内,从而润湿纤维以降低孔隙率和增加厚度,以达到所需的标称,同时保持低纤维变形。然而,RAPM 团队强调,这种双重保压工艺仅适用于较厚的零件,并指出它会导致不同厚度零件的 CPT 不均匀。
此处讨论的 RAPM 零件试验为使用预浸料压缩成型高速制造航空航天结构零件提供了知识。经验教训包括:
RAPM 已经表明,预浸料压缩成型可以生产高质量的航空级结构,同时减少周期时间和劳动力。这使复合材料能够更好地参与航空航天应用的贸易研究,同时提供更多的重量减轻和组件性能(例如,抗腐蚀、抗裂和抗疲劳等)。
索尔维和波音公司合作改进了新型 EP2750 预浸料系统,将节拍时间缩短至 20 分钟,这要归功于材料化学、预浸料和工艺知识以及自动化的结合。
除了上面讨论的制造开发部件,RAPM 还生产了几个挑战和过渡部件,旨在挑战 初步发展和过渡 有潜力在国防应用中战胜机加工铝的候选人。其中包括:
从这些零件试验和其他 RAPM 制造特征研究中汲取的结果和经验教训将在 2020/2021 年发布。
索尔维还展示了 EP2750 在汽车部件中的表现,例如 B 柱尺寸为 36 x 16 x 2 英寸,厚度为 0.0725 英寸,包括 5 层 Solvay THORNEL T650-35 标准模量 3K 丝束碳纤维和 376克/平方米 8 线束缎布。这部分是在英国 Solvay Heanor 使用 DDF 制造的。与经过高压灭菌的标准预浸料相比,CYCOM EP2750 和 DDF 的组合可将循环时间缩短 60%,将节拍时间(生产线上开始一个零件和下一个零件之间的时间,即生产线的脉冲时间)缩短 85% .
RAPM 经验教训和进一步的零件试验
索尔维汽车零部件试验
树脂