应用聚焦:3D 打印如何实现性能更好的液压元件
[图片来源:雷尼绍]
对液压元件设计和制造新方法的需求正在上升。一种使制造商能够探索液压制造新机遇的技术是 3D 打印。
从利勃海尔和福特到博世力士乐,公司转向 3D 打印以制造更节能、更轻且更便宜的液压元件。
今天的应用聚焦深入探讨了 3D 打印对液压系统和组件的好处,同时探索了该技术最激动人心的实例。
看看本系列中涵盖的其他应用程序:
热交换器的 3D 打印
轴承3D打印
用于自行车制造的 3D 打印
用于数字牙科和透明矫正器制造的 3D 打印
用于医疗植入物的 3D 打印
3D 打印火箭和航天器制造的未来
用于鞋类制造的 3D 打印
电子元件的 3D 打印
铁路行业的 3D 打印
3D 打印眼镜
用于终端零件生产的 3D 打印
支架的 3D 打印
涡轮机零件的 3D 打印
3D 打印如何支持核电行业的创新
为什么要对液压元件使用 3D 打印?
当涉及重载或需要重复运动时,液压是最有效的运动方式之一。
液压系统使用泵给液体加压,然后它的运动被用来为从起重机到汽车的一切事物提供动力。
液压系统每天都在我们身边。它用于车辆、建筑设备、建筑物和制造设施。
液压元件传统上通过机械加工或铸造制造。然而,许多液压设备制造商开始对使用 3D 打印生产液压元件(例如歧管、伺服阀和液压适配器块)感兴趣。但是,是什么让他们首先考虑这项技术呢?
据 Bosch Rexroth AG 工业液压业务部门负责人 Steffen Haack 称,影响液压行业的趋势有很多,包括:
- 能源效率(减少流动力,减少压力损失,提高效率)
- 降噪
- 减少水箱容积
- 更高的压力水平和减少的安装空间
- 改进材料和油性
- 更高的可用性和预测性维护
- 用户友好
- 安全
3D 打印,尤其是金属和沙子,在推动其中一些趋势方面发挥着重要作用,例如提高能源效率和缩小安装空间。
怎么样?通过采用先进的设计,可以整合新功能,减少组件的重量和尺寸,并提高整体液压系统的性能。
让我们深入了解 3D 打印对液压系统的好处。
减轻液压元件的重量和尺寸
3D 打印使液压元件制造商能够制造更轻、尺寸更小的零件。
以液压歧管为例。这部分有助于调节液压系统组件之间的流体流动,通常由实心金属块加工而成。
去除多余金属的成本很高,而且通常不会将多余的金属加工掉,从而导致零件的重量超过其可能承受的重量。
3D印刷有助于克服这个问题,因为它需要的材料量几乎与生产歧管所需的材料量相同。
在金属 3D 打印过程中,如选择性激光烧结,激光追踪零件的微米薄横截面,逐层选择性地熔化和融合金属粉末。这允许工程师控制进入零件的材料量,使用比 CNC 加工所需的更少的金属。
除了减轻组件的重量外,3D 打印还可以实现更紧凑的零件,更好地适应设计受限的空间。这一优势使得 3D 打印液压元件在需要高精度和轻量化的应用中特别受欢迎。
聚焦:Aidro 的 3D 打印歧管
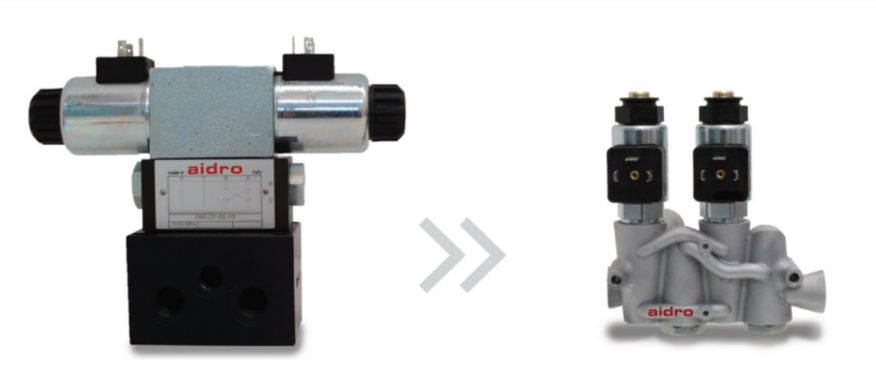
一个 3D 打印液压元件的例子来自意大利制造商 Aidro。
Aidro 用于农业机械的液压歧管经过重新设计,以节省其所用系统的重量和空间。3D 打印的铝制歧管与它所取代的装置具有相同的功能,但其性能只有其一半尺寸和比之前的歧管轻 75%。
部分整合
3D 打印还可以通过将多个部件集成为一个来缩小部件——这种方法被称为部件整合。
这使制造商能够消除组件的复杂组装,并增强零件的结构完整性,因为会导致泄漏的薄弱连接点更少。
优化效率
3D 打印使重新设计液压元件的内部几何形状成为可能,以优化流体流动并降低压降。
以歧管为例,工程师可以将流体流道精确定位在歧管内的位置需要并具有各种形状和尺寸。这意味着流道可以具有弯曲形状,并且与传统歧管相比,它们之间的间距更近,从而使成品更紧凑、更轻。
据报道,弯曲的流动路径可以将流动效率提高 30% 到 70%。
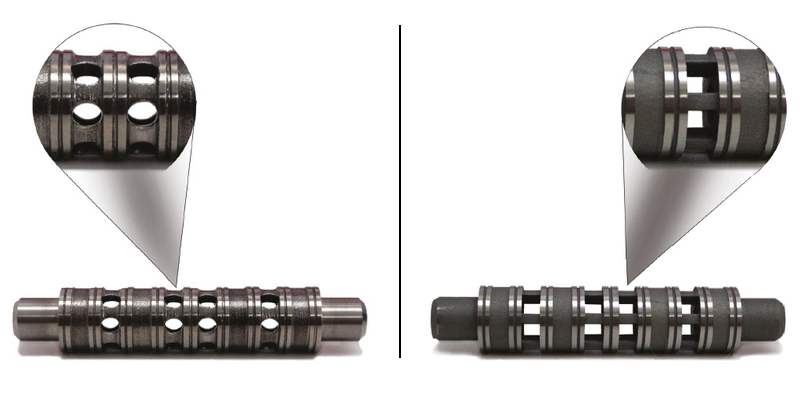
重新设计流道横截面的形状也可以有所作为。例如,阀芯中的流道通常是圆形的,因为它们是用旋转刀具加工的。
3D 打印使工程师可以将流路的横截面设计为方形而不是圆形,这样可以将流量增加多达 20% 并降低压降。
此外,传统的液压元件,如歧管,通常需要加工交叉钻孔通道,随后必须将其堵塞以防止漏油。然而,这些堵塞的通道会产生可能导致系统故障的潜在泄漏路径。 3D 打印首先消除了创建交叉钻孔通道的需要,从而消除了这个问题。
3D 打印液压元件的更多示例
3D 打印液压适配器块
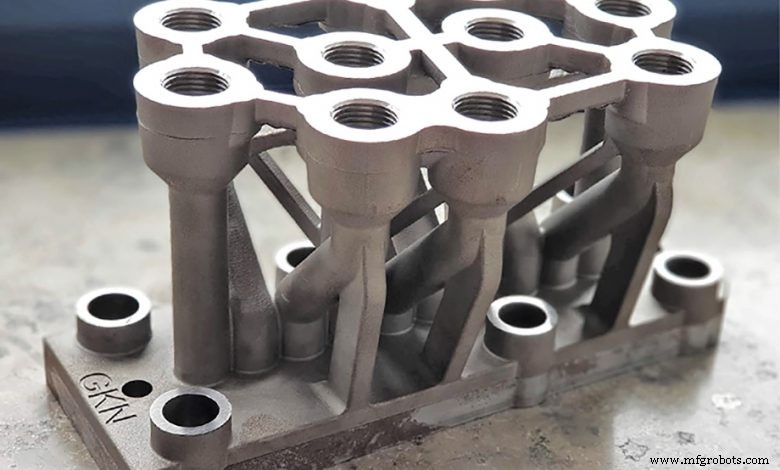
GKN Additive 已经 3D 打印了一个液压适配器块,这是一个歧管,用于引导液压系统中的流体流动,连接阀门、泵和执行器。
传统上使用的液压块往往采用块状设计,其中钻有一组内部通道。制造液压块的过程始于从上方和下方钻孔。
垂直孔然后通过水平通道连接,并在其中切割螺纹。为了防止油从开放的水平通道泄漏,它们用平头螺钉堵塞并密封。
但是,由于多种原因,该过程效率极低。首先,钻孔和铣削的边缘会产生锋利的毛刺,在后处理中难以触及。这些有时会在操作过程中断开并导致系统故障。
其次,尖角连接点产生湍流,导致能源效率低下。第三,未使用的水平通道会积聚污垢,降低液压系统的使用寿命。
3D 打印帮助 GKN Additive 克服了上述挑战,从而制造出性能更好的液压块。
液压块的重量从 30 公斤减少到 5.5 公斤,而没有牺牲任何功能。通过新设计,可以去除多余的材料并确保零件内没有孔重叠。
此外,新设计完全省略了未使用的水平通道,因此污垢无处堆积。最后,为了减少系统中的湍流,工程师用光滑的管道代替了尖锐的内角。
总结 3D 打印为此应用带来的好处,3D 打印使制造商能够改进组件的功能,同时使用更少的材料。这转化为更低的部件重量和更低的制造成本。
利勃海尔的 3D 打印液压阀块
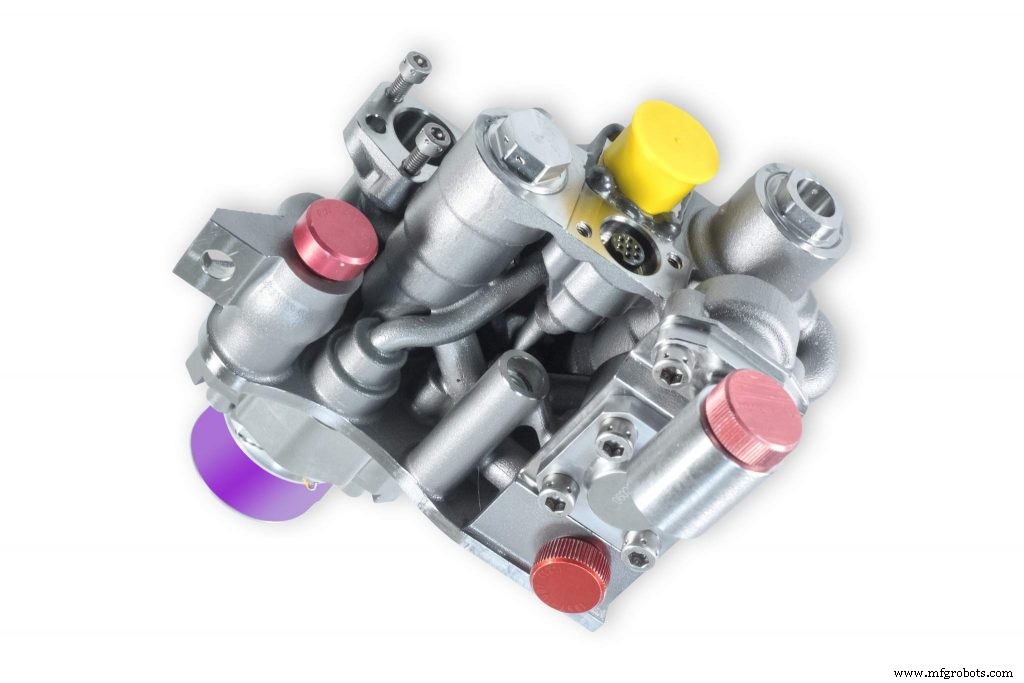
另一个液压 3D 打印的好例子来自利勃海尔集团。在 3D 打印的帮助下,该公司能够重新设计用于飞机的高压液压阀块,使其更轻、更高效。
利勃海尔团队将 10 个功能元件集成到新阀组中,消除了具有大量横向孔的复杂管道系统。结果是阀块重量减轻了 35%,由更少的部件制成。
该 3D 打印部件已在 A380 飞机的试飞中成功测试。
多明流体动力 通过 3D 打印重新构想其流体动力系统
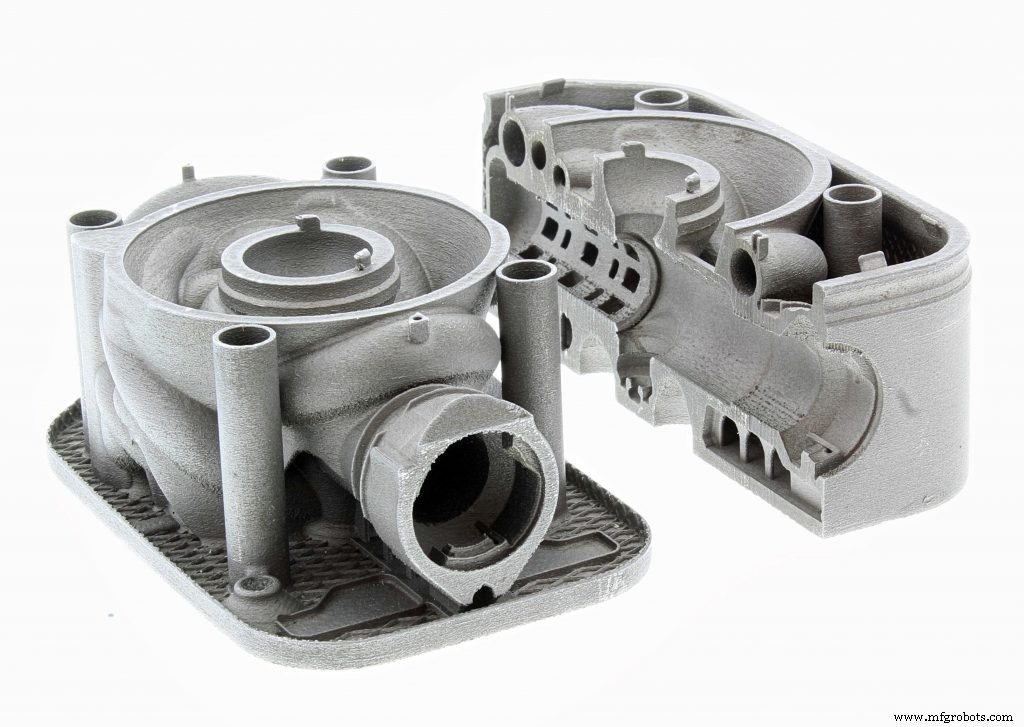
总部位于英国的液压系统制造商 Domin 已转向 3D 打印,以重新开发其用于将信号转换为压力的高性能直驱伺服阀。
Domin 表示,3D 打印使其能够更快地构建复杂零件且无需工具。例如,该公司设计了一款驱动器,其尺寸是原始尺寸的 25%,而功能则提高了 25%。该部件的生产成本降低了三分之一,制造时间已从 5.5 小时缩短至仅 1 小时。
这样的结果是用传统方法无法实现的,Domin 声称。
/>
福特 3D 打印进气歧管
虽然我们已经看到了为重型设备和飞机 3D 打印液压元件的例子,但福特一直在为汽车液压系统进行 3D 打印。
去年,这家汽车制造商展示了它声称是有史以来最大的 3D 打印金属进气歧管,它被放入工作车辆中。
那辆车是 Ken Block 的“Hoonitruck”福特皮卡。
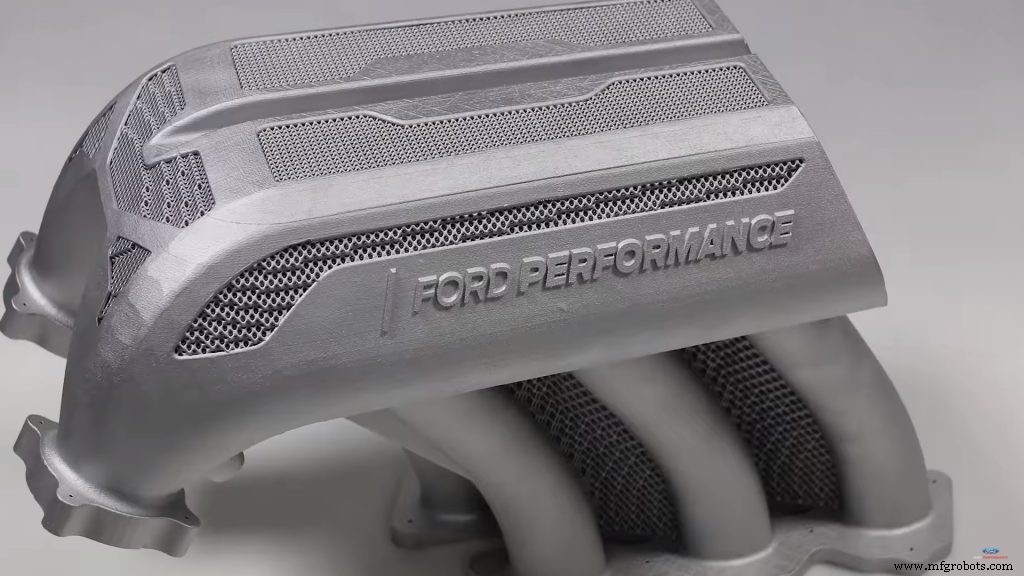
这辆车需要一个特殊的进气歧管来为发动机汽缸提供来自涡轮增压器的空气,福特决定转向金属 3D 打印。
该部件由铝材 3D 打印,使用 Concept Laser 机器,耗时 5 天完成。通过使用尖端的 CAD 软件,可以创建使用传统制造方法无法制造的复杂网络状结构。该设计针对更好的性能和更轻的重量进行了优化——最终部件的重量仅为 6 公斤。
博世力士乐将砂 3D 打印用于歧管
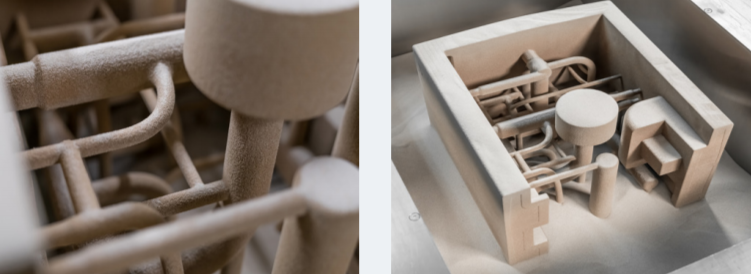
除了金属 3D 打印外,还可以选择 3D 打印砂芯,该砂芯随后可用于铸造液压元件。用于此应用的过程称为粘合剂喷射,它的工作原理是将粘合剂选择性地沉积在一层硅砂上。
几年来,博世力士乐一直在使用砂 3D 打印来生产控制块的铸芯。
在这样做的主要好处中,博世力士乐将机器组件(例如歧管中的过滤器)集成在一起的能力以及重量减轻多达 30% 的能力。
其他好处包括消除了对可能导致泄漏的辅助孔的需求,以及优化了提高能源效率的内部流道。
用 3D 打印重新构想液压元件
随着液压行业努力实现更节能和更小型的液压元件,3D 打印为开发和生产性能更好的设计提供了一种选择。
看到 3D 打印在交付周期、重量减轻以及成本和性能方面的优势,许多液压元件制造商开始为他们的产品探索这项技术。
展望未来,我们预计 3D 打印在生产液压元件方面的作用会增加,帮助液压行业的公司跟上当前和未来的趋势。
3D打印