铈的金刚石切割的分子动力学建模和仿真
摘要
结构相变和位错之间的耦合给理解金属铈在纳米尺度的变形行为带来了挑战。在目前的工作中,我们通过分子动力学建模和模拟阐明了超精密金刚石切割下铈的潜在机制。通过分配经验势来描述原子相互作用并评估两个面心立方铈相的性质,建立了金刚石切割铈的分子动力学模型。随后的分子动力学模拟表明,在切削过程中,位错滑移主导了铈的塑性变形。此外,基于原子径向分布函数的分析表明,在加工表面和形成的切屑中都发生了从 γ-Ce 到 δ-Ce 的微不足道的相变。通过对加工参数依赖性的研究,揭示了实现高质量铈加工表面的最佳加工条件。
背景
原子序数为 58 的铈 (Ce) 是最丰富的镧系金属之一。铈因其有趣的机械、物理和化学特性而具有广泛的应用。众所周知,金属零件的加工表面形态对其功能、性能和生命周期有很大的影响。例如,可以通过降低表面粗糙度或在加工表面引入残余压应力来有效提高金属零件的耐腐蚀性能[1,2,3]。最近,Yan 等人。采用一种新颖的基于尖端的机械加工技术在 Cu(111) 上制造周期性三角形微腔,这被证明是表面增强的拉曼散射基板 [4]。特别是对于用于储存氢的铈 [5],铈的表面光洁度强烈影响室温下铈与氢之间的反应。因此,实现铈加工表面形貌的高精度对其应用至关重要。超精密金刚石切割是获得高表面完整性、超低表面粗糙度、高平整度、低金相组织演变和低亚表面损伤的超光滑表面光洁度的重要制造技术 [6, 7]。然而,关于铈的金刚石切割的实验或理论工作鲜有报道。此外,由于在超精密金刚石切削过程中,刀具刃口半径与切削深度相当,工件材料的特性在切削过程中起着重要甚至主导的作用。因此,了解铈的加工机制因其复杂的变形行为具有挑战性。
首先,铈以其由 4f 电子离域驱动的异常丰富的压力-温度相图而闻名。在大气压和低于 110 K 的低温下,α-Ce(面心立方 (fcc))是稳定的。在 45 到 275 K 的温度范围内,α-Ce 转变为 β-Ce(双六方密堆积 (dhcp))。 γ-Ce (fcc) 在 270 到 999 K 之间的中等温度下是稳定的。在 999 K 和 1071 K 熔化温度之间的高温下,δ-Ce(体心立方 (bcc))是稳定的 [8,9 ,10,11]。特别是,在 295 K 和 8 kbar 以下,从三价低密度 γ-Ce 到密度更高的 α-Ce 的最迷人的同构相转变伴随着 20% 的大体积坍塌 [8, 12,13,14 ]。铈中电子结构和键合构型的相变引起的改变不可避免地对其变形行为产生强烈影响。具体而言,在刀具与工件接触区域形成的高温和高压可能导致金刚石切割过程中铈的相变。其次,金属铈具有受位错支配的相当大的延展性[15]。众所周知,位错形核和滑移在机械加工下 fcc 金属的塑性变形中起关键作用。然而,对于铈的金刚石切削过程中相变和位错之间的相互作用,人们仍然知之甚少。
加工机制的组成包括工件材料的微观变形行为及其与宏观加工结果在切削力、切屑轮廓和加工表面形态方面的相关性。作为加工实验的重要补充,分子动力学 (MD) 模拟已被证明是阐明不同类型材料的基本机械加工机制的有力工具。李等人。据报道,纳米划痕下单晶Cu(111)的最小磨损深度相当于塑性开始的临界穿透深度,随着探针半径的增加而增加[16]。最近,他们研究了 AlCrCuFe 高熵合金在纳米划痕下的机械行为和变形机制,并报告说由于合金材料具有良好的高温稳定性,因此比纯金属具有更大的表面堆积体积 [17]。高等人。研究了 bcc Fe 正交切削中塑性和缺陷的产生和演变 [18]。朱等人。报道了纳米划痕对探针形状依赖性的尺寸效应[19]。侯赛尼等人。研究了刀具刃口半径对单晶铜纳米加工的影响 [20]。刘等人。发现由于凹凸不平之间的干扰,静摩擦系数和动态摩擦系数之间的差异在 Cu(111) 的单个凹凸摩擦中消失了 [21]。罗梅罗等人。发现可以通过改变刀具前角和选择特定的晶格取向来增强铜基板正交切割过程中的附着力 [22]。杨等人。表明磨料自转速度和方向对抛光单晶铜加工表面的形态和质量有显着影响[23]。 Vargonen 等人。据报道,刮擦期间每个刮擦距离的尖端高度损失是法向应力和尖端锥角的函数 [24]。孙等人。证明 GB 对双晶铜的划痕有影响 [25]。陈等人。发现在铜的纳米切割中,水分子有效地降低了刀具和工件之间的摩擦[26]。吴等人。据报道,键能对摩擦有显着影响 [27]。此外,与实验研究相比,通过 MD 模拟可以方便地研究每个铈相的机械性能,这对于理解铈中相变和位错之间的相互作用至关重要。最近,张等人。通过 MD 模拟研究了硅纳米压痕弹塑性转变中相变和位错之间的相互作用 [28]。然而,据我们所知,目前还没有关于铈机械加工的MD研究的报道。
因此,在目前的工作中,我们首先通过构建工件和工具的原子配置,分配 Ce-Ce 和 Ce-C 原子相互作用的经验电位,以及表征铈的两个 fcc 相,建立了铈的金刚石切割的 MD 模型。利用建立的MD模型,对铈的金刚石切削进行MD模拟,阐明铈的基本加工机理,研究刀具前角和工件晶体取向对切削过程的影响。
方法
钻石切割的MD模型
图1为金刚石切割的MD模型,由单晶铈工件和金刚石刀具组成。铈工件的水平、垂直和纵向尺寸分别为 41、25 和 31 nm,由 100 万个 fcc 结构的 γ-Ce 原子组成。周期性边界条件仅适用于纵向。工件由两种原子组成,分别为底部原子和移动原子。厚度为 2 nm 的底部原子层固定在空间中,以防止工件发生任何刚性运动。移动原子的运动遵循牛顿运动方程,采用速度-弗莱特积分算法。在切割过程中监测工件中每个原子的温度,以表示产生的散热量。为了解决晶体取向的影响,考虑了垂直方向具有(010)、(110)和(111)自由表面的三个铈工件。具有锋利刃口的金刚石刀具,后角为9°,由金刚石结构中的0.1百万个C原子组成。利用-30°、-20°、-10°、0°、10°、20°和30°七个前角来解决前角的影响。考虑到金刚石相对于铈的超高硬度和超短切割距离,切割过程中金刚石刀具的磨损没有被考虑。因此,金刚石刀具被设置为刚体,即刀具中所有原子的坐标和速度每时间步更新一次,这样刀具作为一个整体运动而没有任何变形。
<图片>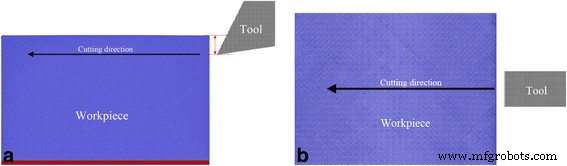
铈金刚石切割MD模型; (彩色在线)铈的金刚石切割MD模型。 一 前视图 和 b 俯视图 . 红色 和蓝色 代表底部和移动的 Ce 原子,灰色 表示C原子
图>模拟系统中存在三种原子相互作用,分别是铈工件中的Ce-Ce、铈工件与金刚石刀具之间的Ce-C、以及金刚石刀具中的C-C。由于金刚石切削刀具在切削过程中被视为刚体而没有任何变形,因此省略了 C-C 相互作用。由相互作用对势和电子嵌入能组成的嵌入原子方法(EAM)已被广泛用于描述金属系统,其可表示为
$$ {E}_{\mathrm{tot}}=\frac{1}{2}{\sum}_{i,j}{\phi}_{ij}\left({r}_{ij} \right)+{\sum}_i{F}_i\left({\rho}_i\right) $$ (1) $$ {\rho}_i={\sum}_{j\ne i}{\ rho}_i\left({r}_{ij}\right) $$ (2)其中 r ij 是原子之间的距离 i 和 j , φ ij 是原子 i 之间的对势 和 j , F 我 表示当原子 i 时产生的嵌入能量 被嵌入,ρ 我 是 i 处的电子密度 由除原子 i 之外的所有原子生成的原子 , 和 ρ j 是原子 j 的电子密度的函数 在原子 i . Sheng 等人对铈的 EAM 参数。用于描述 Ce-Ce 相互作用,它能够准确描述 fcc 铈相的体积弹性特性 [29]。用莫尔斯势来描述Ce-C相互作用,可以表示为
$$ {E}_{\mathrm{tot}}={\sum}_{ij}{D}_0\left[{e}^{-2\alpha \left(r-r0\right)}-2 {e}^{-\alpha \left(r-r0\right)}\right] $$ (3)其中 D 0 (0.087 eV) 是内聚能,α (5.14) 是弹性模量,r 0 (2.93 Å) 表示原子之间的平衡距离 i 和 j , 分别。莫尔斯电势的截止半径选择为 1.0 nm [30]。
创建的模拟系统首先在 NPT 系综(原子数 N , 恒压P , 和恒温 T )。然后,平衡的工件在标准系综(原子数N , 恒定体积 V , 和恒温 T )。切割方向在切割模型的不同视点用红色箭头表示。切削力定义为沿切削方向的分力。超精密加工实验中使用的切削深度为几微米。我们注意到,由于原子模拟中长度尺度的限制,工件的模拟尺寸和切割深度比超精密金刚石切割实验中使用的尺寸小几个数量级。我们还注意到,在当前的纳米切割 MD 模拟中采用的 100 米/秒的切割速度比超精密金刚石切割实验中使用的每秒数十微米的典型速度高几个数量级,给出了对积分时间步长为飞秒 (fs) 量级。共邻分析(CNA)用于识别晶格缺陷的类型[31],着色方案如下:绿色代表fcc原子,红色代表六方密堆积(hcp)原子,蓝色代表体心立方(bcc) 原子,灰色表示其他原子,包括表面原子和位错核。所有 MD 模拟都是使用 LAMMPS 代码执行的,积分时间步长为 1 fs [32]。并利用 OVITO 将 MD 数据可视化并生成 MD 快照 [33]。
铈相的表征
在目前的工作中,考虑了五个铈相,分别为 γ、α、β、ε 和 δ。表1列出了从文献[8,9,10,11]中收集的各相的结构参数和相关的温度-压力条件。然后根据表 1 构建每个相的体原子配置。然后,对构建的体配置进行单轴拉伸、剪切和均匀压缩的计算模拟,以推导出不同 Ce 相的机械性能。由于接近铈熔点的高稳定温度,δ-Ce的力学性能没有计算,因为很难对液相进行力学测试。表 2 列出了每个铈相的衍生弹性常数和机械性能。单晶 γ-Ce 相的计算杨氏模量为 24.17 GPa,这与其多晶对应物的纳米压痕报告的实验值 36.7 GPa 相当[10]。此外,C44 和 1/2(c11-c12) 的计算值相差 3 倍,这与使用非弹性中子散射技术的实验值非常吻合 [34]。表2表明,与其同构低密度γ-Ce相相比,更致密的α-Ce具有显着增强的机械性能。
图> 图>径向分布函数 (RDF),定义为粒子系统中的密度变化与以尖峰形式的参考粒子的距离。 RDF 可以从 X 射线光谱和中子衍射数据推导出 [35, 36]。因此,它是液体和固体结构表征的最重要工具之一,并且是微观原子排列和宏观性质之间的重要联系。在目前的研究中,RDF 用于表征不同铈相之间的结构差异。图 2a 绘制了五个铈相的 RDF 直方图,其中峰代表相应晶格结构的特征:γ-Ce 的第一、第二和第三最近邻距离分别为 3.64、5.13 和 6.3 Å; α-Ce 的第一、第二和第三最近邻距离分别为 3.41、4.85 和 5.92 Å; δ-Ce 的第一和第二最近邻距离分别为 3.53 和 6.75 Å; ε-Ce 的第一、第二、第三和第四最近邻距离分别为 2.96、3.33、4.91 和 5.69 Å; β-Ce 的第一、第二、第三和第四最近邻距离分别为 3.71、3.97、5.27 和 5.92 Å。为了证明通过采用的 EAM 电位参数预测两个 fcc 铈相之间的相变的可行性,对体 γ-Ce 进行均匀压缩,直到达到 20% 的体积坍塌。图 2b 显示了压缩前后的 RDF,分别与 γ-Ce 和 α-Ce 的 RDF 吻合良好,表明发生了最著名的 γ➔ α 相变 [12,13,14] .
<图片>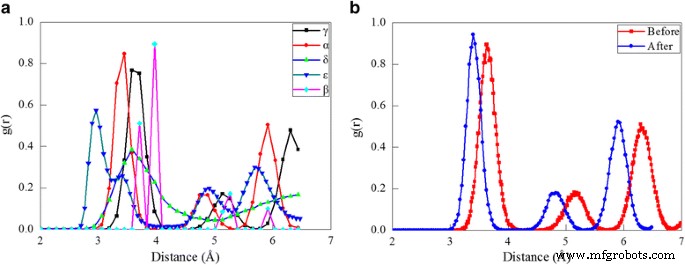
铈相的RDF分析; (颜色在线)a 铈相的 RDF。 b γ-Ce压缩前后的RDF
图>结果与讨论
铈的加工机制
首先进行 Ce(010) 金刚石切割的 MD 模拟,以阐明铈的基本加工机制。所使用的金刚石刀具的前角为0°。加工力的三个分量分别是水平方向的切削力、垂直于加工表面的法向力和纵向的横向力。图 3 显示了切割过程中切割力和法向力随切割长度的变化,根据切割长度分为三个区域。因此,每个区域中的子图显示了代表性的切割配置,其中原子根据其 CNA 值着色,并且未显示 fcc 原子以清晰显示缺陷。
<图片>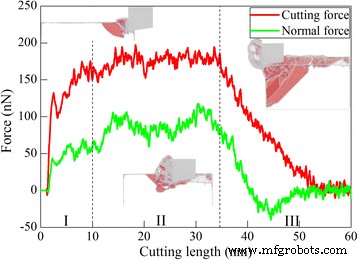
加工力的变化; (color online) 0°前角下Ce(010)金刚石切削过程中切削力和法向力随切削长度的变化。子图展示了不同区域的代表性缺陷配置,其中原子根据其 CNA 值进行着色
图>从图 3 中可以看出,当刀具刚好靠近工件时,由于刀具与工件之间的粘附,切削力和法向力都为负值。当刀具开始与工件接触时,材料首先发生弹性变形,同时切削力和法向力都迅速增加。图 3 显示切割力和法向力在切割长度为 2.3 nm 时迅速下降,表明塑性变形开始。在进一步切割时,切割力和法向力都随着连续成核事件引起的强烈波动而增加。从II区的子图中可以看出,在切削区附近产生了相当多的1/6 112 Shockley局部位错。切削力和法向力主要在 10 到 35 nm 的切削长度范围内围绕恒定值波动,表明切削过程是稳定的。 II区的位错主要位于金刚石刀具的前后。当切削长度达到 35 nm 时,刀具开始与工件分离,同时切削力和法向力均显着下降。区域 III 中的子图显示有相当多的位错被工件左侧挡住。切削力和法向力都趋于稳定,直到形成的切屑与工件完全分离。图3表明,在切削过程中,法向力小于切削力。
图 4a-d 显示了不同切割长度下工件内的瞬时缺陷结构。原子根据其 CNA 值着色,未显示 fcc 原子。因此,图 4e-h 显示了由原子高度着色的加工表面形态。缺陷演化的动态检查表明,工件的屈服伴随着来自右侧自由表面的 1/6 <112> Shockley 部分位错的形核及其随后在相邻 {111} 滑移面和沿 <110> 滑移方向的滑移。肖克利部分位错的运动伴随着以位错核为边界的堆垛层错的扩展。随着切削过程的进行,大量的局部位错从刀具前面的顶部自由表面发射出来,导致沿刀具前刀面形成大量切屑,如图4f所示。同时,刀具后面的位错向上移动,在顶部自由表面消失,导致加工表面显着恢复。图 4c 表明,当刀具接近工件的左边界时,位错的传播被左侧自由表面强烈阻挡,同时切屑体积显着增加,如图 4g 所示。图4d表明,切屑与工件完全分离后,由于顶部自由面位错湮灭,工件内的位错密度显着降低。
<图片>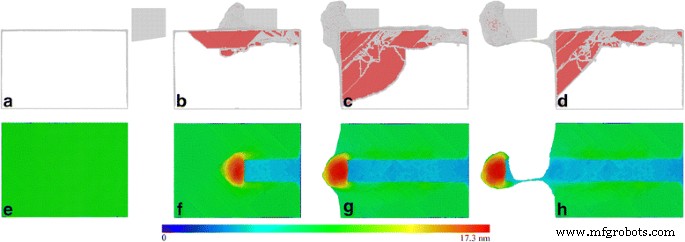
缺陷结构和加工表面形态; (彩色在线)瞬时缺陷结构的 MD 快照(顶行 ) 和加工表面形态 (底行 ) 在前角为 0° 下对 Ce(010) 进行金刚石切割。切割长度:a , e 0.0 纳米,b , f 18.8 纳米,c , g 44.8 纳米和 d , h 59.6 纳米。 顶行中的原子 和底行 分别根据它们的 CNA 值和原子高度着色
图>除了位错滑移主导的塑性外,金刚石切削过程中相变的概率也通过对工件内的缺陷区和形成的切屑进行RDF分析来评估。 fcc结构中的γ-Ce首先使用CNA算法在OVITO中排除,其余原子由缺陷区组成,包括bcc、hcp和其他原子。然后,对缺陷区域进行 RDF 分析。并且可以通过不同类型缺陷原子的数量来推断不同Ce相的数量。图 5a 显示加工表面下方缺陷区的 RDF 的三个峰与 δ-Ce 的 RDF 的三个峰完全吻合,表明发生了从 γ-Ce 到 δ-Ce 的相变。 δ-Ce在高温低压下稳定,发生γ➔δ相变表明切削过程中产生的高散热。此外,由于 δ-Ce 与 γ-Ce 相具有不同的机械性能,生成的 δ-Ce 导致后续切削过程中的加工不均匀。图 5b 表明在成形切屑中也检测到 δ-Ce 原子,这主要是由于在成形切屑和刀具前刀面之间的接触区域中发生了高温触发的 γ➔δ 相变。然而,缺陷区和切屑中形成的δ-Ce的数量非常少,表明在铈的金刚石切削中相变并不突出。
<图片>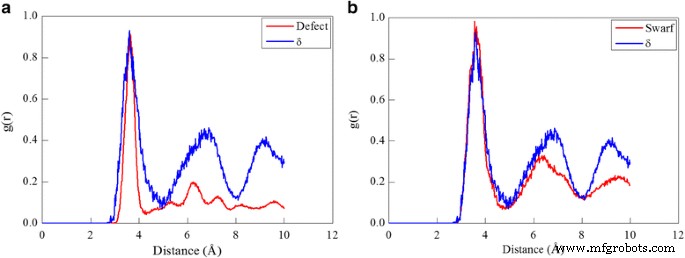
切削过程相变分析; (color online) 0°前角下Ce(010)金刚石切削过程中相变的分析。 a 的 RDF 工件和b 切割后的芯片
图>前角的影响
在对铈加工机理的基本认识的基础上,研究了刀具前角对金刚石切削加工的影响。图 6 绘制了七个前角的切削力和法向力的平均值。每个力分量的平均值是通过对 10 到 35 纳米范围内的切割长度中的瞬时力值求平均值来计算的。图 6 显示切削力高于每个前角的法向力。然而,对于较大的前角,两个分力的差值更加明显。此外,切削力和法向力都随着前角的增加而减小。根据Merchant 理论,随着前角的增加,对应于最小能量的剪切平面角也增加,从而降低切削力[37]。当前MD模拟揭示的前角相关加工力变化与Merchant的理论非常吻合。
<图片>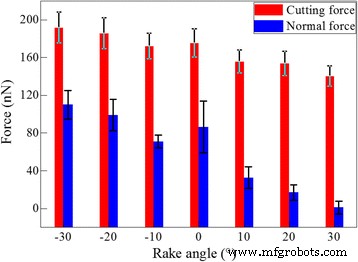
加工力的前角依赖性; (颜色在线)前角对加工力的影响
图>图 7a、b 分别显示了前角为 -30° 和 30° 的金刚石切割过程完成后加工表面下方缺陷结构的底视图。对于每个前角,位错类型和位错相对于自由表面的几何形状是相同的。然而,-30°前角的位错密度明显高于前角30°,表明发生了更复杂的塑性变形。图 7c 显示了不同前角金刚石切割后工件内残留的位错段数,表明位错密度随着前角的增加而减小。需要注意的是,Burgers 向量分类的位错类型包括 1/2<110> 完全位错、1/6<112> Shockley 部分位错、1/6<110> Stair-rod 位错和 1/3 <111> Frank 部分位错,在图 7c 中被考虑在内。在纳米切削过程中,工件材料的位错介导的微观变形与宏观加工结果在加工力和加工表面形貌方面具有很强的相关性。例如,位错的相互作用和反应导致固着位错结构的形成,阻止随后的位错运动;因此,由此产生的加工硬化导致加工力的增加。自由表面位错的湮灭导致加工表面的恢复,同时形成表面堆积[38]。
<图片>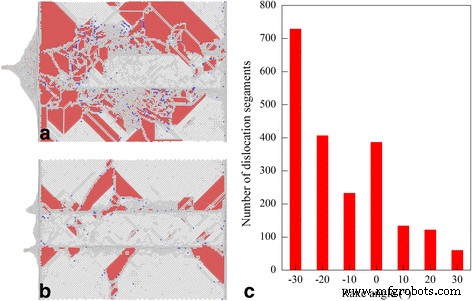
不同前角产生的缺陷结构; (彩色在线)前角为 a 的铈切割后缺陷结构的 MD 快照 −30° 和 b 30°。原子根据它们的 CNA 值着色。 c 前角相关位错数
图>图 8 显示了不同前角的切削加工完成后的加工表面形貌。前角为负值时所形成的凹槽两侧的表面堆积量比正值时更显着。此外,负前角的表面堆积分布不如正前角的均匀。图 8c 清楚地显示了前角为 -30° 时表面堆积沿形成的凹槽的不对称分布。从图 8 可以看出,表面堆积体积随着前角的增加而减小。因此,表明30°前角是切削铈金刚石的最佳前角,与其他前角相比,切削力最低,位错密度最低,表面堆积最低。
<图片>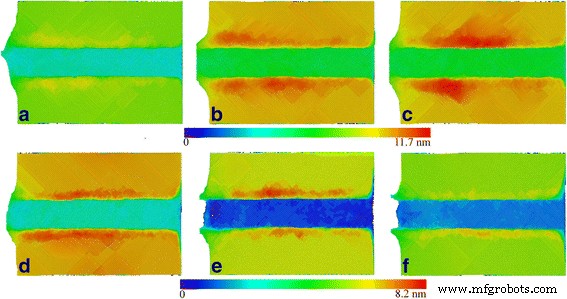
加工表面形态的前角依赖性; (彩色在线)不同前角的加工表面形态:a −10°,b −20°,c −30°,d 10°,e 20° 和 f 30°。原子根据原子高度着色
图>铈工件晶体取向的影响
还研究了在30°最佳前角下晶体取向对金刚石切割铈的影响。 Ce(010)、Ce(110) 和 Ce(111) 的所有加工参数都相同。图 9 显示了不同晶体取向下切削力和位错数的变化。 Ce(010)的切削力明显低于Ce(110)和Ce(111)。虽然位错数在 Ce(111) 中最低,但 Ce(010) 中的位错密度明显低于 Ce(110)。众所周知,滑移面和自由表面之间的几何形状随晶体取向而变化。对于 Ce(010) 和 Ce(110) 来说,四个 {111} 滑移面都倾斜于加工表面。然而,除了三个{111}倾斜滑移面之外,还有一个{111}滑移面平行于Ce(111)的加工表面。 While microscopic deformation of workpiece material is dominated by dislocation slips, the observed macroscopic machining results in terms of machined surface and machining force can also be influenced by machined surface morphology. Although the easy glide of dislocations on the {111} slip plane parallel to free surface is energetically favorable for the accommodation of plastic strain caused by cutting tool action, the resulting considerable surface pile up increases the machining resistance, which leads to a high cutting force.
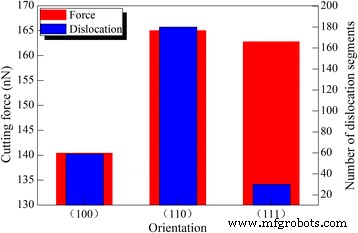
Crystal orientation dependence of cutting force and dislocation number; (color online) crystal orientation dependence of cutting force and dislocation number
图>Figure 10a–c presents machined surface morphology of Ce(010), Ce(110), and Ce(111), respectively, indicating that the crystal orientation has a strong influence on machined surface quality. The volume of surface pile up is the smallest for Ce(010), followed by Ce(111), and the largest for Ce(110). Correspondingly, the material removal in the form of chip is the most pronounced for Ce(010). Furthermore, it is seen that the surface pile up of Ce(111) on both side of formed groove presents the highest symmetry, while that of Ce(110) is the worst. Therefore, it is indicated that the crystal orientation of (010) is optimal for the diamond cutting of cerium due to its low machining force, low dislocation density, and low surface pile up.
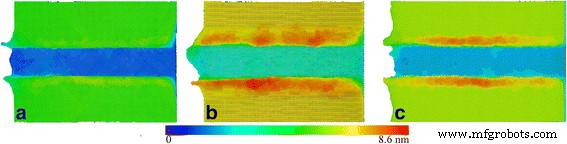
Crystal orientation dependence of machined surface morphology; (color online) crystal orientation dependence of machined surface morphology. Atoms are colored according to atomic heights. Crystal orientation. 一 (010). b (110). c (111)
图>结论
In summary, we perform MD modeling and simulation to elucidate the underlying mechanisms of cerium under the ultra-precision diamond cutting. The EAM and Morse potentials are respectively employed to describe atomic interactions within cerium workpiece and the interactions between cerium workpiece and diamond cutting tool. The elastic constants, mechanical properties, and propensity of phase transformation of cerium phases are evaluated, which demonstrates the feasibility of predicting phase transformation of cerium by the current established MD model. Subsequent MD simulations of diamond cutting reveal that the plastic deformation of cerium is governed by dislocation nucleation and subsequent glide, which is similar with other fcc metals. In addition, there is γ ➔ δ phase transformation occurred within both machined surface and formed chip. It is found that high quality of machined surface and low machining force can be achieved in the diamond cutting of cerium with the optimal machining conditions, i.e., a rake angle of 30° for a crystal orientation of (010).
纳米材料