自动化预成型,第 7 部分:填充 Gesellschaft
这是关于预成型的七部分系列的最后一部分。有关此系列的更多信息,请单击以下链接:
来源:填写社会组织
自动化案例历史
Fill 的第一台机器旨在为 Fischer 自动生产滑雪板。今天,需要 25% 的工人来生产原始年产量的 80%。另请注意,滑雪板采用混合设计,包括多层玻璃和/或碳纤维复合材料、木芯、钢边和多种塑料。
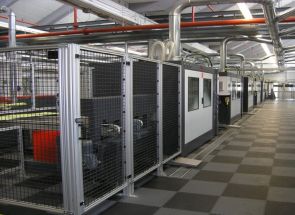
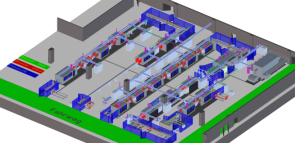
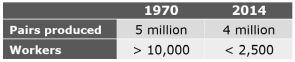
Fill 已提供多代生产复合滑雪板的自动化设备。
来源:Fill Gesellschaft 2017 CAMX 演示文稿。
宝马
随着 BMW 开发 i3、i8 和新 7 系车型(所有车型均使用碳纤维增强塑料 (CFRP) 复合材料),Fill 提供了一系列自动化解决方案。
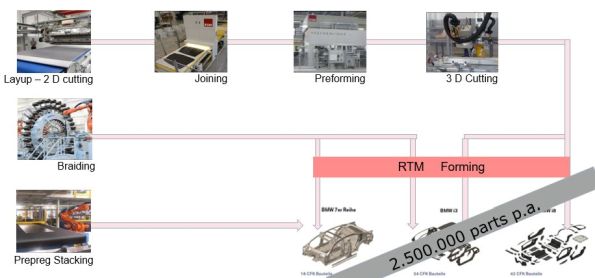
来源:填写Gesellschaft 2017 CAMX 演讲
复合单体壳
Fill 还为 Mubea CarboTech 开发了一条独特的生产线,能够为两种不同的车型生产 CFRP 单体壳:大众大众 XL1 和保时捷 918 Spyder。这条自动化生产线包括多件式驱动成型工具、高压树脂传递成型 (HP-RTM) 压力机、后固化和机加工能力。
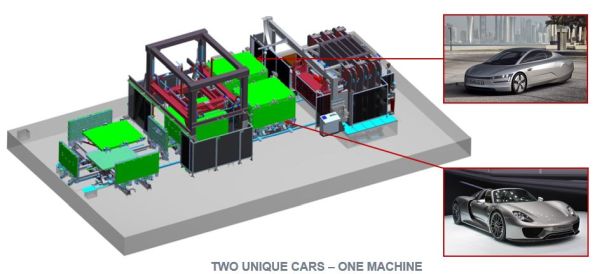
Fill 提供了一个Mubea CarboTech 的复合硬壳式生产线。
来源:Fill Gesellschaft 2017 CAMX 演示文稿
自动上篮
对于自动叠层,Fill 开发了适用于各种不同材料的系统,包括宽度达 3 m 的干织物(用于 BMW 的大批量生产)。用于风力涡轮机叶片的 SpeedLayer 800 自动梁帽铺设系统以 1.5 m/s 的速率和 ±1.5 mm 的精度应用宽度达 800 mm 的单向碳纤维预浸料。它可以处理 600 公斤的预浸料卷,并集成了工艺验证和质量保证功能。
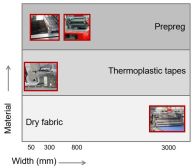
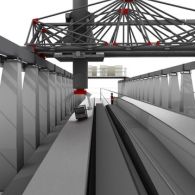
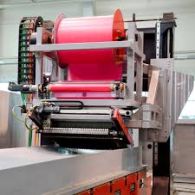
Fill 已开发一系列自动叠层系统(左),包括 SpeedLayer 800,用于使用宽度达 800 毫米的 UD 碳预浸料的风力叶片主梁帽(右)。
来源:Fill Gesellschaft 2017 CAMX 演示文稿
低成本柔性集成复合工艺 (LOWFLIP) 项目是一项为期 3 年(2013 年 10 月至 2016 年 10 月)的欧盟资助计划,其中包括 Fill 和其他九个合作伙伴,旨在使预浸料铺层自动化,以用于热压罐外 (OOA) 固化运输结构。它由三名示威者组成:
- 用于卡车拖车的 2.5 × 2.9 m 前壁
- 1.2 m 长的汽车横梁
- 1.0 × 1.2 m 加筋蒙皮飞机尾锥面板
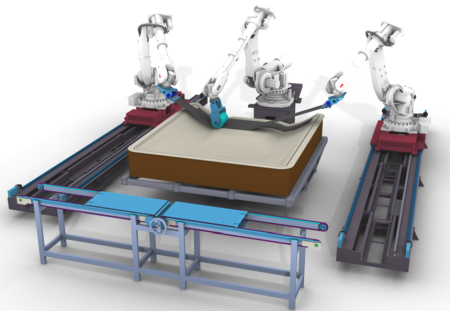
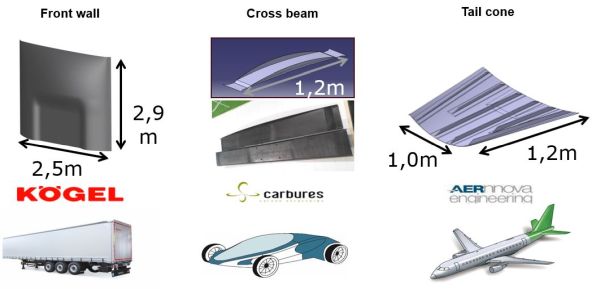
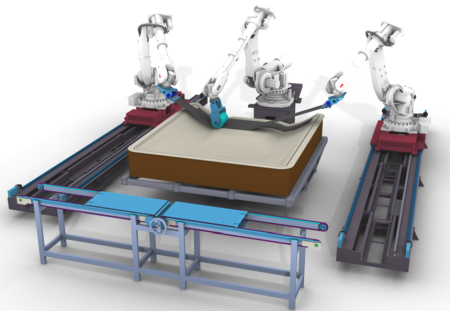
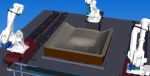
动画片
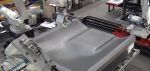
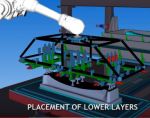
Fill 与 LOWFLIP 的九个合作伙伴合作开发了一种自动叠层单元,用于在没有高压釜的情况下生产大型复合运输结构。
来源:Fill Gesellschaft 2017 CAMX 演示文稿
“我们使用电阻加热将模具加热到 120°C,”Fill 复合材料和塑料能力中心负责人 Wilhelm Rupertsberger 回忆道。 “在自动叠层过程中,材料始终处于张力之下,”他补充道,“我们实现了直接在模具上的无皱褶皱。我们构建了一个人工流程,但使用机器人来提高可重复性。”
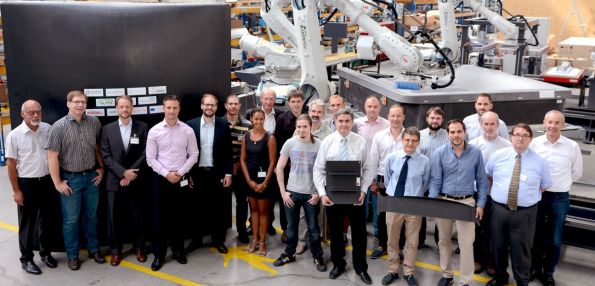
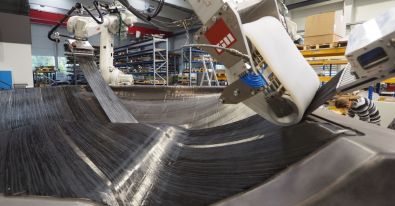
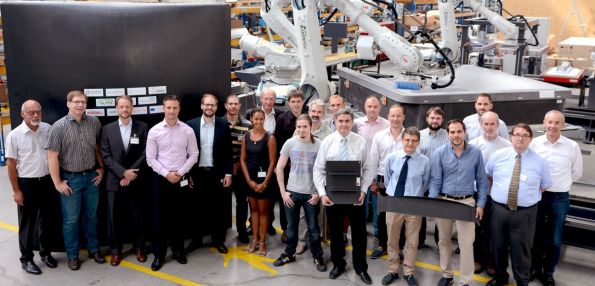
你可以看到左边的卡车拖车墙,以及上面的 LOWFLIP 团队照片中的汽车横梁和飞机尾锥面板演示.
来源:Fill Gesellschaft 2017 CAMX 演示文稿
多层到多层系统
Fill 的 Multi-Layup System 开发用于使用热塑性胶带生产汽车白车身 (BIW) 零件,如后壁和下保险杠加强筋。预计这些部件将包括包覆成型的肋条和其他特征,因此预制件的叠层周期需要与随后的注塑周期相匹配。
我的 JEC 2017 展后博客文章包括一个多叠层系统的视频,该系统从多个卷中送入胶带,同时放置每层所需的所有胶带,而不是依次放置,一次一个。这样就实现了每层10-15秒的循环时间。
填充现在进一步修改了系统并将其重命名为多层。它可以将多达 16 条宽达 50 毫米(每条 0.01-0.04 毫米厚)的胶带送入、切割和放置到旋转台上。铺带台可生产最大 1.6 × 1.6 m 的零件。胶带以 ≈500 m 2 的速度施加 /hr——每 12-15 秒施加一个完整尺寸的部件层,每个成品预制件的循环时间大约为 1 分钟。层没有完全合并,而是通过热粘合连接。当每个线轴用完胶带时,无需停机即可自动更换。
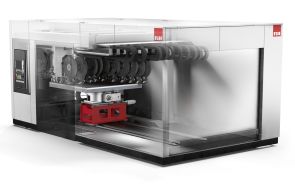
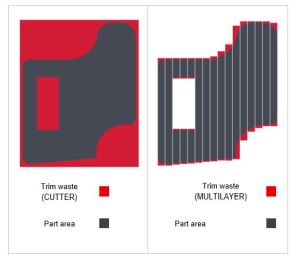
自动填充多层预成型系统可以显着减少修剪浪费,同时仅在需要的地方放置胶带并根据需要将它们定向以实现定制的层压板。
来源:Fill Gesellschaft 2017 CAMX 演示文稿
完成的预制件然后在压力机中合并。 “我们将 Multilayer 与自动固结压力机和 Engel 注塑成型单元集成在一起,共同提供 1 分钟的循环时间,”Rupertsberger 说。 Fill 在今年早些时候收到了来自斯威本科技大学(澳大利亚墨尔本)的第一个多层系统的订单,并将在 JEC World 2019(3 月 12 日至 14 日,法国巴黎)上首次现场演示该设备。
RTM 压力机和自适应注射
Fill 为 SGL Composites 提供了多台 RTM 印刷机,包括 HP-RTM 印刷机。
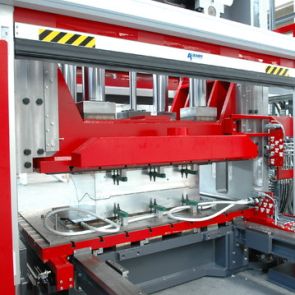
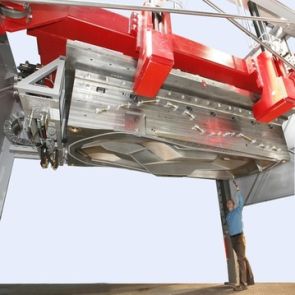
Fill 已提供用于复合材料生产的各种压力机,包括 HP-RTM 压力机到 SGL Composites(右)。
来源:填写 Gesellschaft
Fill 与 Airbus Operations(德国施塔德)和亚琛工业大学塑料加工研究所 (IKV) 合作,开发了一种创新的 RTM 自适应注射装置,最初用于航空复合材料结构。在使用 RTM 制造的零件可以在飞机上飞行之前,它们必须通过一个耗时且成本高的质量保证 (QA) 流程。为缩短此过程,RTM 成型工具配备了传感器,使 QA 能够在生产过程中在线部署。 IKV、Airbus 和 Fill 现在已将这些传感器集成到注射系统中,无需配备每一个成型工具。以与典型 RTM 系统中使用活塞注射系统相同的方式使用一次性墨盒,自适应注射单元配备了一个传感器盒,可以原位测量和记录以下数据:
- 温度
- 压力
- 树脂粘度
- 树脂系统的交联密度
- 玻璃化转变温度 (Tg)。
在确保成型件质量的同时,这些数据也可用于管理和控制注塑过程。这种工业 4.0 自适应注射系统正在为航空复合材料开发,并扩展到其他行业,例如汽车。
热悬垂成型
在我和 Sara Black 最近撰写的关于以色列高性能复合材料的旅游文章中,我们注意到大多数公司都在使用热悬垂成型。事实上,在 Elbit Cyclone,我们的导游 Jonathan Hulaty 说:“我不知道你是如何进行这种没有热悬垂成型的高速预浸料零件生产的,”指的是波音 787 组件的横梁和支柱。 FBM 和以色列航空航天工业公司也认为热悬垂成型机 (HDF) 是必不可少的。 Fill 多年来一直提供 HDF 系统,其中包括 FACC 生产的多个装置。它们基本上是真空成型系统,配备红外线或其他类型的加热元件和可重复使用的硅橡胶膜,用于在固化之前加热和压缩(减体积)工具上的预浸料叠层。 HDF成为下图完整航空复合材料生产线的关键部分。
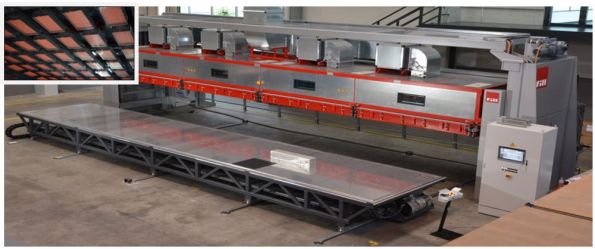
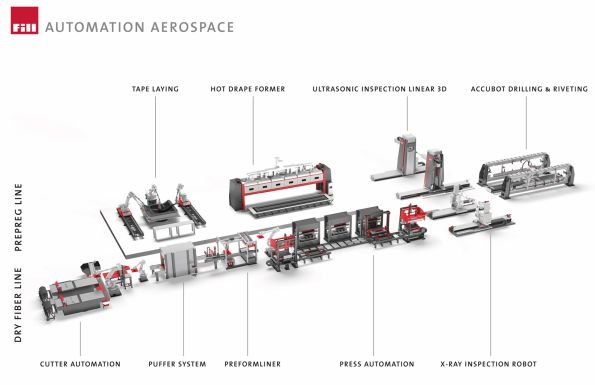
热悬垂成型已成为大批量生产预浸料复合材料航空结构的重要推动因素,并由 Fill 作为其全流程链解决方案的一部分实现自动化。来源: 填写 Gesellschaft
工业 4.0 碳纤维复合材料生产单元
2013 年底,Fill 开始与 Tier 供应商合作开发用于制造 CFRP 纵梁的生产系统,用于加固空客 A320 着陆襟翼外壳。安装后,该系统成功减少了工位数量,改善了生产流程,也提高了用户友好性。它包括:
- 自动成型工具存储
- HDF 站
- 将层压板加工成纵梁的冲压-车削提升站。
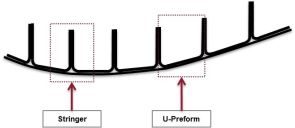
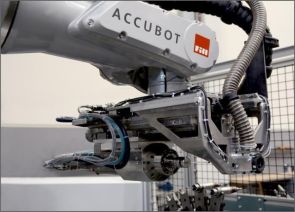
Fill 已开发用于由预浸料制成的起落架襟翼纵梁(左)的三代自动化生产单元(右)。
来源: 填写 Gesellschaft
用于生产相同类型零件的第二代系统于 2017 年投入使用。第一个系统专注于优化单个工作站,后来的系统旨在最大限度地减少手动任务并集成所有工具物流。三个关键的开发领域使这款第二代系统能够实现高重现性并显着提高生产力:
- 成型工具的手动检索和存储被全自动工具返回所取代,从而缩短了物流流程时间。这也减少了 50% 以上的空间需求。
- 子流程的进一步自动化减少了非生产时间。
- 所有记录和报告的工业 4.0 数字化。 Fill 开发的软件可以始终可视化过程并记录整个过程链中每个组件的历史记录。传感器检测工具和材料的可用性,以避免瓶颈并改善重新订购。
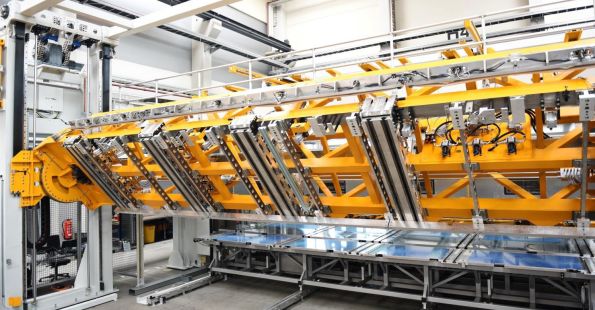
按转- 用于 A320 和 A350 起落架襟翼纵梁自动化生产单元的提升站。
来源: 填写 Gesellschaft
Fill 现在正在开发用于空客 A350-900 的着陆襟翼外壳的第三代生产系统。它也包括工具存储、成膜 (HDF) 站、冲压-车削提升站和自动工具返回,但通过用于高压灭菌器工具的运输系统得到了增强,用自动导引车 (AGV) 取代了以前的手动运输卡车和电动拖拉机)。 Fill 已经在研究未来的系统,研究如何进一步改善人机协作。
Accubot
甚至在复合材料行业开始表达他们对多操作工作单元的预期未来需求之前,Fill 就已经在开发第一个原型,它称之为 Accubot。这个想法是使用激光跟踪器进行空间补偿以及直接的外部测量系统来开发一个精确的机器人。该机器人将能够通过末端执行器切换功能,不仅成为无损检测 (NDT) 单元,还成为加工单元。 Accubot 应用包括:
- 钻孔
- 铆接
- NDT – 带喷射器的超声波
- 无损检测 – X 光
- 无损检测 - 计算机断层扫描
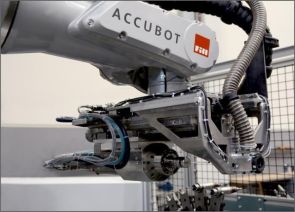
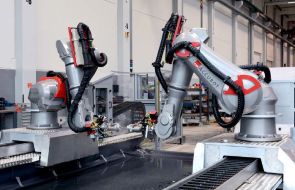
Accubot 用于钻孔(左)和使用高速超声波扫描的无损检测(右)。
资料来源:Fill Gesellschaft。
FlexHyJoin
Fill 是欧盟资助的混合连接灵活生产单元 (FlexHyJoin) 项目的成员。这个为期 3 年的计划旨在通过结合激光连接和感应连接技术,开发一种全自动试点工艺,用于在汽车应用中将金属支架/配件与热塑性复合材料连接起来。 Fill 设计并构建了自动化单元,包括软件和各种技术的集成。
Fill 的研究和开发仍在继续。它明白需要创新和智能的生产系统来使复合材料零件的制造更经济,并能适应更高的产量。并致力于根据客户的规模和特定需求开发这些系统。
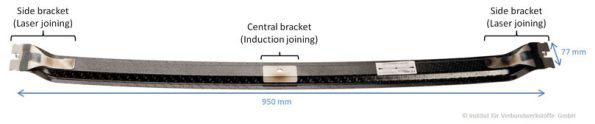
来源:FlexHyJoin。
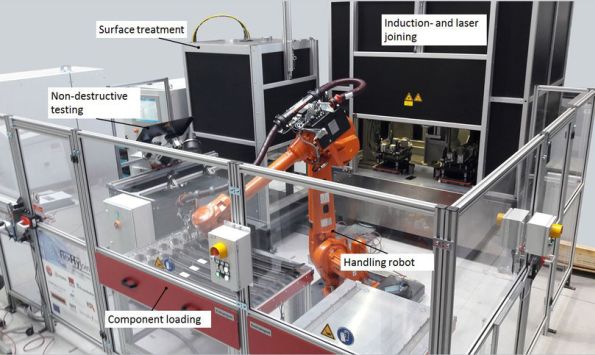
树脂