Deere 借助 AI 解决焊接气孔问题
焊接是重型设备制造行业不可或缺的一部分,技术人员在焊接过程中面临的挑战之一是气孔——焊缝金属中存在空洞。
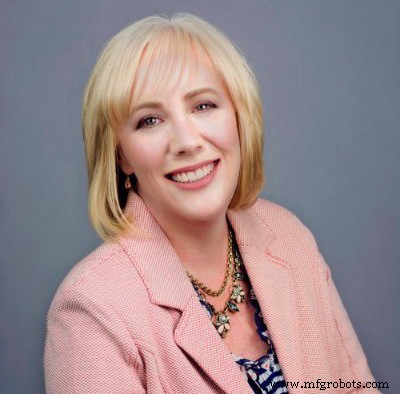
这些空洞削弱了焊接强度,需要返工甚至报废整个有缺陷的部分。
这可能既昂贵又耗时。虽然训练有素的焊接工程师可以通过听觉和视觉检查来检测孔隙率,但这些工程师可能很难找到。在嘈杂和烟雾缭绕的工厂环境中,他们也可能难以听到或看到缺陷。
现有的自动化监控系统经常会遇到很高的误报率、减慢生产速度并增加成本。
生产农业、建筑和林业机械的约翰迪尔与英特尔合作,针对这一问题构建了基于人工智能 (AI) 的解决方案。
长期以来,机器视觉解决方案一直难以为焊接应用创建,因为极其恶劣的环境会产生烟雾和火花,可能会给相机放置带来困难。
为了克服这些挑战,我们与 John Deere 和我们的合作伙伴合作创建了一个 AI 解决方案,该解决方案在焊缝附近放置了一个摄像头,提供了超出人眼能力的洞察力。
该解决方案利用英特尔 OpenVINO(视觉推理和神经网络优化)工具包逐帧检查流式视频,寻找缺陷。
当人工智能模型识别出缺陷时,该解决方案会立即关闭焊接机器人,以便技术人员可以安全地进行干预。整个行业过去在焊接过程中处理焊接气孔问题的尝试并不总是成功的。如果在制造过程的后期发现这些缺陷,则需要返工甚至报废整个组件,这可能具有破坏性且成本高昂。
基于我们与 Deere 的试点,该解决方案能够以高达 97.14% 的准确率检测孔隙缺陷——为制造商节省了巨大的成本和生产力。单机方案不依赖任何第三方电源或焊接机器人模型,真正实现了可扩展性。
端到端的集成系统还使制造商能够连接新的和现有的焊接设备,捕获多个计算密集型图像数据流,并将机器学习模型部署到边缘设备。
焊接质量挑战当然不是约翰迪尔独有的。迪尔的独特之处在于其方法。该公司的工程师正在利用人工智能和机器视觉来自动化质量检查,使他们能够在问题发生时检测到问题,从而推动工厂车间的快速决策,自动化 QA 流程以提高质量、降低成本并提高工厂吞吐量。
在与 Deere 合作时,我们的重点是确保解决方案的使用寿命,以支持公司未来可能存在的其他质量或效率需求。
对于希望为现有制造设备、流程和管理增加智能的公司而言,这是一个重大收获。与解决方案提供商合作至关重要,他们可以帮助解决当今的挑战,同时确保互操作性和可扩展性,以实现未来的灵活性和易用性。
“焊接很复杂。这种人工智能解决方案有可能帮助我们比以前更高效地生产我们的机器,”迪尔建筑和林业部门的质量总监 Andy Benko 说。
自动化控制系统