在镁合金上化学镀 Ni-P-Al2O3 复合涂层的沉积工艺和性能
摘要
提高镁(Mg)合金化学镀镍磷(Ni-P)涂层的耐蚀性和耐磨性。 Ni-P-Al2O3 涂层是由复合镀液在镁合金上制成的。最佳的 Al2O3 浓度由镀液和镀层的特性决定。采用扫描电子显微镜(SEM)观察了不同时间Ni-P-Al2O3复合涂层的形貌生长演变。结果表明,纳米Al2O3颗粒可能减缓Mg和Ni 2+ 的置换反应 在沉积过程的早期阶段,但它对 Ni-P 自催化还原过程的速率几乎没有影响。涂层的抗腐蚀和显微硬度测试表明,Ni-P-Al2O3 复合涂层由于更合适的 Ni-P-Al2O3 涂层的晶面间距和晶粒尺寸,比 Ni-P 涂层表现出更好的性能。热冲击试验表明,Al2O3 颗粒对涂层的附着力没有影响。此外,复合镀液的使用寿命为4.2金属周转率,表明其在镁合金领域具有潜在应用。
背景
镁 (Mg) 合金由于密度低、比强度高和可加工性优良而引起了广泛的关注和科学研究 [1, 2]。因此,镁合金通常用于航空航天、电子和汽车领域[3, 4]。然而,由于镁合金在抗腐蚀和耐磨性方面存在不良缺陷,因此限制了其应用[5, 6]。因此,镁合金的表面防腐减摩方法,如微弧氧化膜、化学转化涂层、热喷涂、物理气相沉积、电镀和化学镀等,已被开发出来[7,8,9, 10,11,12,13]。
化学镀镍磷(Ni-P)是镁合金最有效的表面技术之一,具有低成本、高效、耐腐蚀、耐磨等优异的综合优势[14, 15]。因此,化学镀Ni-P涂层在镁合金的防腐领域发挥着重要作用。为了进一步提高Ni-P涂层的性能,通常在化学镀液中加入纳米颗粒,如SiC、ZrO2、TiO2、SiO2和Al2O3等,制备Ni-P纳米颗粒复合涂层[16,17, 18,19,20]。根据之前的研究 [20,21,22,23],纳米粒子有效地提高了 Ni-P 涂层的性能。尽管Ni-P纳米颗粒复合涂层与Ni-P涂层相比具有较高的性能,但存在三个问题需要注意。首先,纳米粒子在化学镀液中容易聚集形成活性中心,降低镀液的稳定性。其次,复合镀液的工艺参数通常决定了镀层中纳米颗粒的含量和分布,也是提高镀层性能的关键因素。第三,纳米粒子与Ni-P共沉积的过程是影响涂层性能的另一个因素。因此,这些因素值得关注。纳米 Al2O3 颗粒是一种廉价的磨料,具有高硬度和良好的化学稳定性 [24, 25]。它可以很好地分散在化学镀镍浴中。因此,Ni-P-Al2O3 复合涂层通常被用作防腐和抗磨涂层,以保护钢或铜基体。然而,只有少数报道集中在镁合金基材上的化学镀 Ni-P-Al2O3 [20, 22, 26]。此外,关于镁合金上Ni-P-Al2O3镀层的生长过程和复合镀液稳定性的研究也比较少见。因此,需要对复合镀液的性能和Ni-P-Al2O3的共沉积工艺进行更多的研究。
在目前的工作中,为了进一步提高镁合金基体上 Ni-P 涂层的性能,我们在镀液中分别采用硫酸镍和乳酸体系作为主要盐和络合剂。同时,在化学镀Ni-P镀液中加入纳米Al2O3粉末。为了获得适用于 AZ91D 镁合金的合适的化学镀复合镀液,该镀液的工艺参数通过沉积速率和涂层性能进行评估。此外,还进行了周期性循环测试,以评估最佳工艺条件下镀液的使用寿命和稳定性。为了研究纳米Al2O3颗粒对涂层生长过程的影响,讨论了Ni-P涂层的沉积行为和相结构。此外,还根据形貌和结构分析了涂层的耐腐蚀性、显微硬度和附着力等性能。结果表明,Ni-P-Al2O3复合镀层的性能优于Ni-P镀层,化学镀复合镀液具有良好的使用寿命稳定性。因此,我们的研究结果对于化学镀Ni-P纳米颗粒复合涂层在镁合金上的应用具有重要的参考价值。
方法
复合涂层的制备
在这项工作中,采用尺寸为 2 cm × 1 cm × 0.5 cm 的 AZ91D 压铸镁合金作为实验材料,其化学成分重量百分比为:8.5 Al、0.34 Zn、0.1 Si、0.03 Cu、0.002 Ni , 0.005 Fe 和 0.02 其他,其余为 Mg。 AZ91D 基板被连续抛光,没有。 500 和 1000 SiC 纸,用去离子水冲洗,在 65 °C 的碱性溶液中浸泡 5 分钟,然后在铬酸溶液(CrO3 200 g/L)中酸洗 60 秒。之后,将镁合金基板浸入浓度为380mL/L的氢氟酸溶液中进行活化处理约10分钟。每一步都用去离子水清洗镁基板。镁合金化学镀镍的基本浴液组成及操作条件如下: 35 g/L NiSO4·6H2O、35 g/L乳酸、30 g/L Na2H2PO2·H2O、10 g/L NH4HF2、3 mg /L稳定剂,pH值4.5~7.0,温度70~90℃。化学镀浴保持在玻璃烧杯中,该烧杯置于恒温控制的水浴中。采用数显电动搅拌器提供搅拌力。纳米Al2O3颗粒的平均粒径约为50nm。化学镀前,纳米Al2O3颗粒在超声波条件下充分分散在镀液中。
电镀浴的沉积速率和稳定性测试
为了研究纳米 Al2O3 颗粒对化学镀镍浴沉积速率的影响,沉积速率用公式 1 表示。 (1).
$$ v=\frac{\Delta w\times {10}^4}{\rho St} $$ (1)其中 v , ρ , S , t , 和 △w 表示沉积速率 (μm/h)、Ni-P 涂层的密度 (~ 7.9 g/cm 3 ), Mg 衬底的表面积 (cm 2 )、沉积时间 (h) 和涂层重量 (g)。此外,使用电子天平(AR2140,Ohaus)通过称重方法估计涂层中纳米Al2O3颗粒的含量。为了评价化学镀液的稳定性,采用周期循环试验(或金属翻转,MTO)来评价化学镀液的使用寿命和稳定性。这里,1 MTO 定义了 Ni 的沉积重量等于 Ni 2+ 的初始浓度 在浴缸里。以1升电镀液为例,从电镀液中得到约7.8克Ni \( \left({C}_{{\mathrm{Ni}}^{2+}}=7.8\kern0.5em \mathrm {g}/\mathrm{L}\right) \) 作为 1 MTO。此外,一个新鲜的混合溶液(\( {\mathrm{Ni}}^{2+}:{\mathrm{H}}_2{\mathrm{PO}}_2^{2-}=1:3 \)当镀液的沉积速率较低时,将其添加到镀液中。稳定性试验直至镀液分解结束。因此,MTO 的表达式可以表示为等式。 (2).
$$ \mathrm{MTO}=M/m $$ (2)M 和 m 代表Ni的累积沉积重量和Ni 2+ 的浓度 分别在镀液中。
材料表征
通过使用扫描电子显微镜(SEM,Hitachi S-4800)观察涂层的表面形貌。通过X射线衍射仪(XRD,D/Max-2200,日本)用CuKα研究涂层的结构 辐射 (γ =0.154 nm).
电化学测量
在电化学分析仪(CHI800,Chenhua,China)上进行动电位极化测试。采用经典的三电极结构在 3.5 wt% NaCl 水溶液中进行电化学实验,该结构由一个工作电极(样品,1 cm 2 )、一个反电极(铂)和一个参比电极(饱和甘汞电极)。在动电位扫描实验中,首先将样品浸入电解质溶液中 30 分钟以稳定开路电位 (E 0)。 Tafel 图由记录的数据转换而来,腐蚀电流密度 (i corr) 是通过外推阳极和阴极 Tafel 线的直线部分来确定的。实验扫描速率为 5 mV/s,在 25 °C 下进行。采用HXD-1000显微硬度计和维氏压头,载荷100 g,耐久时间15 s,对不同复合涂层镁合金的显微硬度进行了评价。进行热冲击试验以评估涂层的附着力[23]。描述如下:在空气气氛中,将带有Ni-P涂层或Ni-P-Al2O3涂层的Mg基体置于高温箱式电阻炉中,以20℃的升温速率加热至250 ± 10℃。 °C min −1 然后在冷水中淬火。这个过程重复了20次。
结果与讨论
图1显示了纳米Al2O3颗粒的浓度、搅拌速度、pH值和温度对复合涂层沉积速率和Al2O3含量的影响。如图 1a 所示,随着 Al2O3 颗粒浓度从 0 增加到 15g/L,沉积速率略有下降。另一方面,随着Al2O3颗粒浓度从0增加到10g/L,复合涂层的Al2O3含量逐渐增加。但当 Al2O3 颗粒浓度高于 10 g/L 时反而降低。这种变化是由于颗粒在高浓度下聚集,这削弱了 Ni-P 与 Al2O3 的共沉积行为。在图 1b 中,当搅拌速度设置为 300~400 rpm 时,复合涂层的沉积速率和 Al2O3 含量分别为 18 μm/h 和 3.6%。结果表明,在该搅拌速度范围内,Al2O3 颗粒在镀液中的分散性最好。对于酸性复合镀液,pH 值对镀层沉积速率和 Al2O3 含量的影响如图 1c 所示。当pH值在6.0~6.5范围内时,最大沉积速率可达18.5 μm/h,而涂层的Al2O3含量几乎随pH值增加而增加。图 1d 表明复合镀层的沉积速率和 Al2O3 含量都随着温度的升高而增加,这是因为离子和颗粒的活性提高了,并且复合镀液在高温下的反应速率也加快了。然而,镀液的稳定性和涂层的孔隙率在高温(> 85°C)下会变差[13, 22]。根据以上分析结果,确定镁合金复合镀液的初步工艺参数和操作条件,即35 g/L NiSO4·6H2O、35 g/L乳酸、30 g/L Na2H2PO2·H2O、 10 g/L NH4HF2,10 g/L纳米Al2O3颗粒,3 mg/L稳定剂,pH =6.0~6.5,T =85 °C,搅拌速度为350 rpm。
<图片>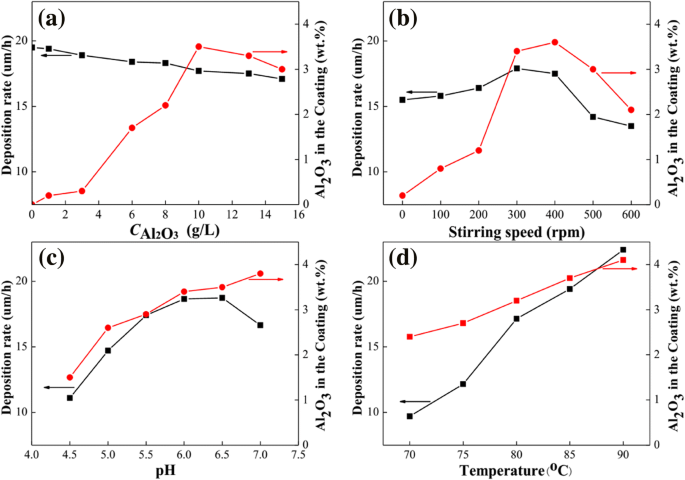
工艺参数对镀层沉积速率和Al2O3含量的影响
图>为了研究 Ni-P-Al2O3 涂层的沉积过程,镁合金表面形貌图像随沉积反应时间的变化如图 2 所示。为了对比分析,图 2a-c 表示 Ni-P 的沉积过程涂层,而图 2d-f 显示了 Ni-P-Al2O3 (3.6 wt%) 复合涂层的共沉积过程。图2a为Mg基体在镀液中浸泡0.5分钟后的形态图,大量立方结构颗粒分布在其表面。这些立方颗粒被确认为 MgF2,主要在 HF 活化过程中形成,与文献报道一致 [23, 27]。然而,图 2d 的图像形态与图 2a 明显不同。主要区别表明,图 2d 中的 MgF2 颗粒小于图 2a 中的颗粒。此外,在Mg基体表面观察到许多纳米Al2O3颗粒。形貌的变化源于Al2O3颗粒在高温和搅拌过程中不断撞击镁合金表面。当化学镀 Ni-P 时间达到 5 分钟时,如图 2b 所示,Ni 颗粒逐渐长大,然后覆盖整个镁合金表面。但对于化学复合镀层(见图 2e),在镁合金表面观察到较大的 Ni 颗粒和纳米 Al2O3 颗粒,并且 Ni-P-Al2O3 涂层在 5 分钟内没有完全覆盖镁基体。这表明复合镀液中Ni-P-Al2O3 镀层的生长速率低于不含Al2O3 颗粒的镀液中Ni-P 镀层的生长速度。这是支持复合镀浴中沉积速率低的原因的证据。当化学镀时间进行 30 分钟时,Ni-P 涂层和 Ni-P-Al2O3 涂层的形貌分别如图 2c、f 所示。对于Ni-P涂层,表面呈现致密的节状结构,平均尺寸为3μm。但在图 2f 中,Ni-P-Al2O3 复合涂层的平均结节尺寸明显小于 Ni-P 涂层。此外,可以清楚地观察到纳米Al2O3 颗粒嵌入Ni-P 涂层中。重要的是,从Al2O3颗粒的表面分布来看,图2f中Al2O3颗粒的分布明显小于图2c,e。该结果表明,沉积反应时间为 5 分钟后,Ni-P 的沉积占主导地位,而 Al2O3 颗粒的沉积成为次要的。从涂层中 Al2O3 颗粒的相对含量也可以得到类似的推论(图 1)。也就是说,Al2O3颗粒对沉积过程的影响主要存在于化学镀镍初期。
<图片>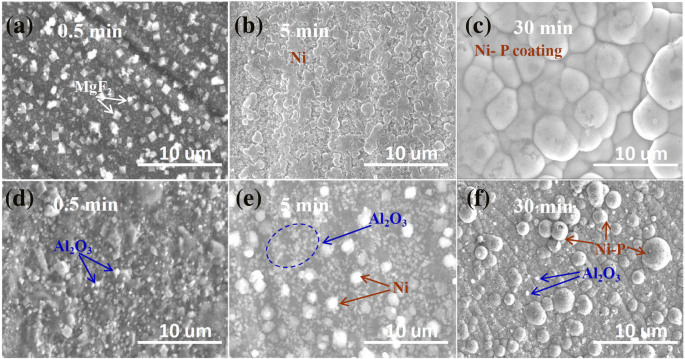
Ni-P涂层的表面形貌(顶部,a -c ) 和 Ni-P-Al2O3 复合涂层(底部,d -f ) 在不同的沉积时间
图>为了探究纳米Al2O3颗粒对Ni-P涂层结构的影响,AZ91D镁合金、Ni-P涂层和Ni-P-Al2O3复合涂层的XRD图谱如图3所示。图3 镁合金晶面衍射角主要集中在30°~70°范围内,例如α (10\( \overline{1} \)0) 32.2°, α (0002) 34.2°,β (10\( \overline{1} \)1) 36.8°, etc. 对于涂有Ni-P涂层的镁合金,Ni-P涂层的衍射图谱在44.7°处呈现展宽峰和高强度衍射,可以归因于镍的面心立方 (fcc) 相的 (111) 晶面(表 1)[28]。此外,这种宽峰的存在表明形成了具有混合非晶结构的 Ni-P 涂层。镀Ni-P-Al2O3 (3.6 wt%)复合涂层后,在25.6°、43.5°和73.2°处可以明显地发现三个新的衍射峰。这些峰归因于 Al2O3 与 PDF 卡号相比的特征衍射峰。 88-0826。因此,Ni-P-Al2O3 复合涂层沉积在镁合金表面。此外,Ni-P-Al2O3复合涂层中Ni的(111)晶面衍射峰偏移45.2°(见表1),表明纳米Al2O3颗粒对(111)晶面间距有一定影响尼。根据布拉格公式,nλ =2d sinθ (n =1, 2, 3, ..., λ = 0.154 纳米,d 和 θ 分别代表晶面间距和衍射角),Al2O3 颗粒使 Ni 的(111)晶面间距减小了约 3%。此外,Ni-P涂层和Ni-P-Al2O3复合涂层中Ni的(111)衍射峰分别用高斯函数拟合。结果表明,Ni-P-Al2O3 复合涂层中该衍射峰的半峰全宽(FWHM)比 Ni-P 涂层中的更宽(表 1)。根据谢勒公式,D =Kγ /B cosθ (D , K , B 分别代表晶粒、谢乐常数和 FWHM),与 Ni-P 涂层相比,Al2O3 颗粒使 Ni-P-Al2O3 复合涂层的晶粒减少了约 8%。这说明纳米Al2O3颗粒细化了Ni晶粒尺寸,这与上述SEM观察结果一致。
<图片>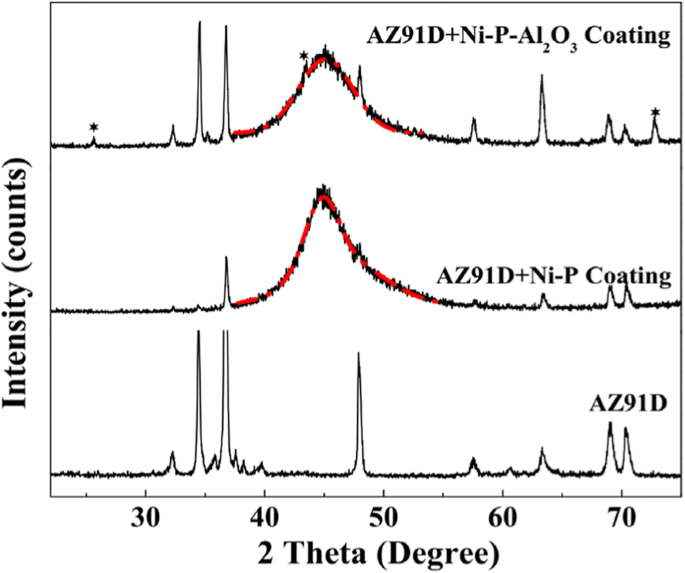
AZ91D基体、Ni-P涂层和Ni-P-Al2O3 (3.6 wt%)复合涂层的XRD图谱
图> 图>图4和表2分别显示了AZ91D镁合金基体、Ni-P涂层和Ni-P-Al2O3复合涂层在室温下3.5 wt% NaCl水溶液中的极化曲线和防腐参数。极化曲线中的阴极反应对应于析氢,而阳极极化曲线是耐腐蚀最重要的特征反应过程[29]。对于 AZ91D 镁合金基板,当施加的电位增加到阳极区域时,观察到激活控制的阳极过程。此外,它在电解液中溶解严重,其腐蚀电位(E corr) 在 − 1.47 V 处读取。但是对于 E Ni-P 涂层的 corr,与镁合金基体 (- 1.47 V) 相比,它显示出显着的正移至 − 0.51 V,腐蚀电流密度 (i corr) 从 1.4 × 10 −4 明显降低 A/cm 2 基板的 3.1 × 10 -6 A/cm 2 Ni-P 涂层(见表 2)。对于Ni-P-Al2O3 (1.7~4.2 wt%)复合涂层,这里涂层的Al2O3含量是通过称重法得到的。如表 2 所示,所有的 E 复合涂层正移和i的corr 与Ni-P涂层相比,复合涂层的corr降低,表明Ni-P-Al2O3涂层具有更高的耐腐蚀性能。在此,含 3.6 wt% Al2O3 的 Ni-P 涂层显示出最高的 E corr (− 0.35 V) 和最低 i corr (4.5 × 10 −7 A/cm 2 )。然而,E corr 和 i Ni-P-Al2O3 (4.2 wt%) 的 corr 变为 − 0.41 V 和 1.0 × 10 -6 A/cm 2 , 分别。可能是Al2O3颗粒增加了Ni-P涂层的孔隙率,降低了复合涂层的性能。因此,复合涂层的Al2O3含量对复合涂层的耐腐蚀性能有重要影响。它还与涂层的晶面间距和晶粒尺寸等结构有关(图3)。
<图片>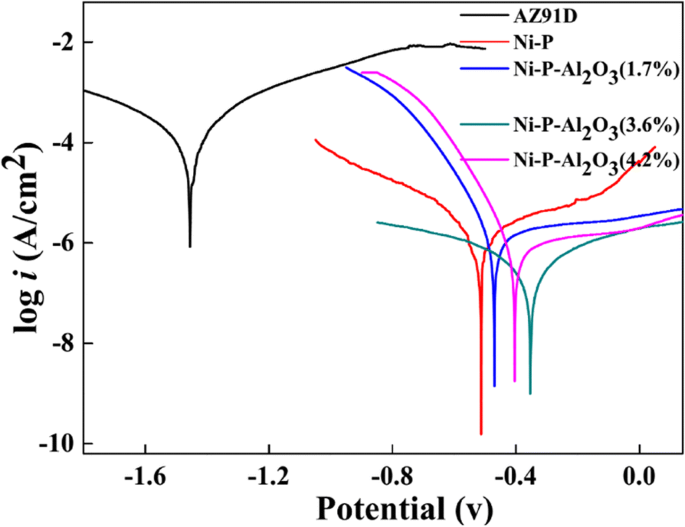
AZ91D基体、Ni-P涂层和Ni-P-Al2O3复合涂层的极化曲线
图> 图>为了测试涂层的显微硬度,所有涂层的平均厚度为 18 μm,由沉积速率和沉积时间估算。镁合金基体和不同Al2O3含量涂层的显微硬度测试结果如图5所示。如图5所示,AZ91D镁合金裸露的显微硬度仅为120 HV左右,而镀有Ni-P涂层的镁合金基体的显微硬度高达520 HV。比基体高约400 HV,说明Ni-P涂层能有效提高基体涂层的硬度。因此,Ni-P涂层提高了镁合金基体的耐磨性。此外,Ni-P-Al2O3 复合涂层的显微硬度在涂层中的 Al2O3 含量从 0 增加到 3.6 wt% 时表现出相当大的增加趋势。因此,Ni-P-Al2O3 (3.6%) 复合涂层在 638 HV 时显示出最高的硬度值。其原因源于纳米Al2O3 颗粒优化了Ni-P 合金的相结构(见图3)并提高了涂层的显微硬度。然而,复合涂层中Al2O3的含量达到4.2 wt%,涂层的显微硬度反而下降到576 HV。这意味着较高的纳米粒子含量可能会影响Ni-P晶体结构,导致复合涂层性能不佳。
<图片>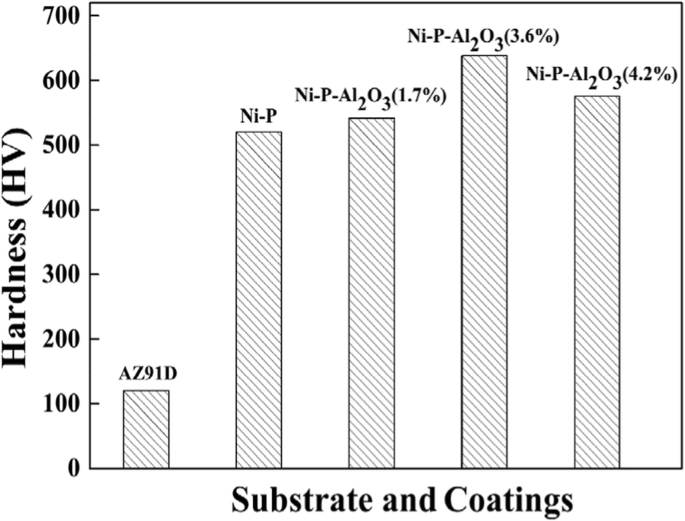
AZ91D基体、Ni-P涂层和Ni-P-Al2O3复合涂层的硬度
图>镀层与镁合金基体的附着力按实验部分进行热冲击试验。通过 20 次循环测试,Ni-P 涂层和 Ni-P-Al2O3 复合涂层都很好地附着在镁合金基体上。试验过程中未观察到裂纹、起泡、剥落等缺陷,表明Ni-P或Ni-P-Al2O3涂层与镁合金基体具有良好的附着力,抵抗热冲击过程。此外,还使用扫描电镜观察了涂层与镁合金基体之间的横截面形貌图像。如图6所示,通过热冲击试验进一步表明涂层和基材之间没有明显的缺陷。重要的是,热冲击试验和截面观察表明纳米Al2O3颗粒对复合涂层的附着力没有影响。
<图片>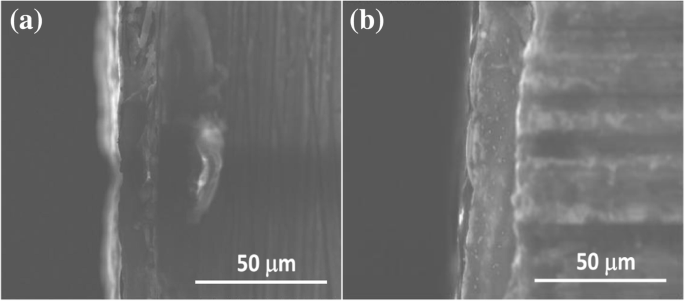
Ni-P涂层的横截面形貌图像(a ) 和 Ni-P-Al2O3 (3.6 wt%) 复合涂层 (b )
图>在目前的工作中,分别制备了不含和含纳米 Al2O3 颗粒 (10 g/L) 的 1-L 镀液。此处计算镀液中初始镍源含量为7.8 g,镀液负载量为0.5 dm 2 /L。根据周期循环试验规则(参见实验部分),首先对化学镀Ni-P镀液的MTO进行了评价,得到约48.2g Ni-P合金。在这里,通过使用 EDS 分析确定了 Ni-P 涂层中 90% 的镍含量(见图 7)。因此,涂层中镍的含量可以计算为 43.4 克。也就是说,通过使用方程,不含 Al2O3 颗粒的镀液的 MTO 为 5.6。 (2).对于化学镀 Ni-P-Al2O3 复合镀液,从复合镀液中总共沉积了 38.8 g Ni-P-Al2O3 涂层。同样,通过 EDS 分析确定了 86.45% Ni、9.84% P、1.96% Al 和 1.75% O(图 7)。因此,复合镀层中镍的含量可计算为33.5 g,复合镀液的MTO为4.2。从周期循环试验结果来看,复合镀液的使用周期比化学镀Ni-P镀液少1.4MTO。这意味着纳米Al2O3 颗粒会降低化学镀液的使用寿命。尽管如此,Ni-P-Al2O3复合镀层在镁合金领域仍有潜在应用。
<图片>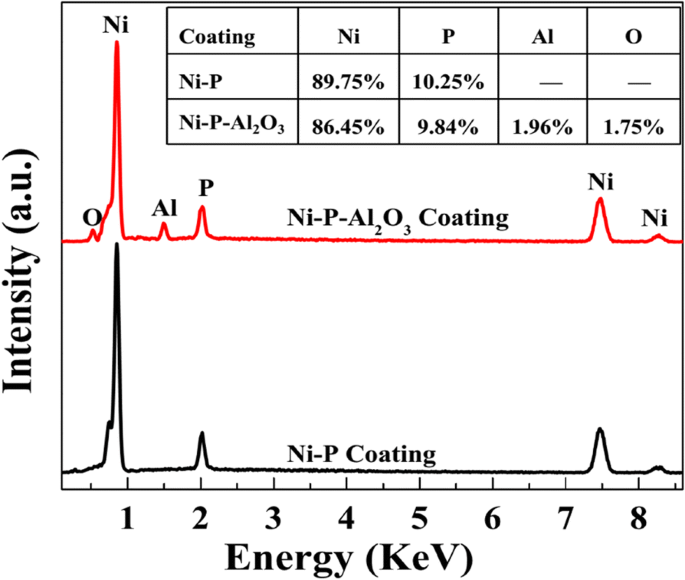
Ni-P涂层和Ni-P-Al2O3复合涂层的EDS光谱
图>结论
总之,我们获得了在镁合金上共沉积 Ni-P-Al2O3 涂层的化学镀复合镀液和操作条件,即 35 g/L NiSO4·6H2O、35 g/L 乳酸、30 g/L Na2H2PO2 ⋅H2O、10 g/L NH4HF2、10 g/L纳米Al2O3颗粒、3 mg/L稳定剂、pH =6.0~6.5、T =85 °C,搅拌速度为 350 rpm。复合涂层的形貌表征和相结构分析表明,纳米 Al2O3 颗粒对涂层的生长过程和相结构(晶面间距和晶粒尺寸)有重要影响。 3.6 wt%的Al2O3含量有效地提高了Ni-P涂层的显微硬度和耐腐蚀性。此外,附着力测试表明Ni-P涂层和Ni-P-Al2O3涂层之间几乎没有区别。使用寿命试验确定化学镀复合镀液的MTO约为4。总之,化学镀Ni-P-Al2O3复合镀是扩大镁合金应用的重要技术。
缩写
- E 0 :
-
开路电位
- i 正确:
-
腐蚀电流密度
- Mg:
-
镁
- MTO:
-
金属周转率
- Ni-P:
-
镍磷
- SEM:
-
扫描电镜
- XRD:
-
X射线衍射
纳米材料