混合型大型增材工具:用于大型零件的更轻、更快、成本更低的模具
三十多年来,商用航空越来越多地采用复合材料。事实上,当今主要商用飞机的几种型号的关键结构部件中有一半以上是复合材料。随着这些材料的使用在零件的体积和尺寸方面的增长,构建工具(尤其是负担得起的工具)以更快地原型制作和制造这些零件变得越来越困难。例如,空中客车公司(荷兰莱顿)的 A350 XWB 上的机翼长 32 米,宽 6 米,代表了有史以来最大的复合航空结构。
“现在市场上有如此突破性的制造技术,我们可以期待在工具进化方面取得重大进展,帮助我们应对我们在复合材料飞机部件开发中面临的挑战,”复合材料制造工程师 M. Pilar Muñoz Lopez 指出。空中客车公司位于西班牙伊列斯卡斯的工厂。“对我们来说,研究这些技术、能力和局限性至关重要,这样我们才能为未来做好准备。”
鉴于工具占飞机结构零件总计划成本的很大一部分,并且考虑到这些零件的尺寸越来越大,因此需要具有更低成本和交货时间的新工具选项。空中客车公司、诺斯罗普格鲁曼航空系统公司 - 航空航天结构业务部(美国犹他州克利尔菲尔德)和大学最近完成了一项关于原型和小批量生产航空结构零件的混合、大幅面增材制造 (LFAM) 工具的有趣研究代顿研究所(UDRI,代顿,俄亥俄州,美国)取得了令人鼓舞的结果。
解决热膨胀问题
大多数碳纤维增强塑料 (CFRP) 航空结构由环氧树脂基体预浸料制成。要成型此类零件,模具必须能经受住高达 180°C/356°F 的烘箱或高压釜固化温度。此外,鉴于 CFRP 的(线性)热膨胀系数(CLTE 或 CTE)非常低,因此在室温和高温下尽可能匹配工具和成型材料 CLTE 至关重要。这可确保模具保持尺寸,从而使所得零件也满足尺寸要求。为了避免最终结构中的变形或应力,避免使用比零件材料冷却得更快的工具材料也很重要。因此,用于成型大型 CFRP 航空结构的最常用工具由 CFRP 本身或因瓦合金制成,因瓦合金是一种以低 CLTE 着称的镍铁合金。两者都是昂贵的,并且可能需要很长的交货时间。此外,因瓦合金加工困难且耗时,运输也很重。虽然钢或铝工具可以降低成本,但它们相对较高的 CLTE 值限制了在许多应用中的使用 - 特别是在成型大型或长部件时。
许多公共和私营部门的研究都评估了用热塑性材料打印的增材制造工具,并得出结论,它们可能提供的好处包括降低成本和缩短生产热固性层压复合材料的交货时间。不幸的是,基于聚合物的 LFAM 模具存在模具孔隙率等问题,这会导致在固化温度/压力下显着的真空损失。解决这个问题需要额外的工具填充返工和表面涂层。更大的挑战是高度各向异性的 CLTE 值,这是由于挤出/印刷过程中的面内原料填料对齐,这可能导致 Z 轴上的膨胀/收缩差异比 X 和 Y 打印轴上的大 5-10 倍。这使得以可重复和可重复的方式获得尺寸精确的零件成为一项挑战 - 特别是当零件很大、具有高纵横比和/或具有复杂的表面时。
“每个对增材制造感兴趣的人都遇到过同样的孔隙率和不受控制的热膨胀问题,几乎没有有效的方法来解决这些问题,”结构材料部先进制造工艺开发 UDRI 团队负责人 Scott Huelskamp 解释说。 “有很多人想要使用 AM 工具,但他们在等待有人解决这些问题。”
鉴于增材制造在降低模具成本和交货时间方面的潜力,该行业已通过探索新的可打印材料、打印机硬件修改和创新建模方法,将大量精力集中在解决扩展问题上。例如,一些团体开发了一个“补偿值”,用于设计 AM 工具以解决 CLTE 差异。然而,Huelskamp 指出,确定哪个 补偿值使用困难且容易出错。此外,这种方法对于阴型腔工具以及在其长度上具有捕获特征的工具无效,这些工具会在工具中的热循环过程中产生能够损坏零件的锁模条件。
“没有任何补偿因素可以解决这类问题,”他补充道。 “迄今为止,还没有任何 AM 工具研究能够完全解决在高温下对低各向同性 CTE 值的需求。如果没有这种特性,工具尺寸和几何形状将始终受到限制,并且较大的工具在固化温度下会出现更高的尺寸误差。”
为了尝试解决 LFAM 工具挑战的新方法,在先进复合材料制造创新研究所(IACMI,美国田纳西州诺克斯维尔)的支持下,几个成员公司开展了一个为期 18 个月的项目,并得到了美国的支持俄亥俄州能源和就业部(俄亥俄州哥伦布市)。该团队由 UDRI 领导,包括空中客车公司和诺斯罗普格鲁曼公司。这些组织之前曾在 IACMI 内外进行过其他研究合作,因此熟悉彼此的能力。
“蛮力”方法
UDRI 已经在 AM 工具研究方面拥有丰富的经验,并且是美国 AM 联盟 America Makes(美国俄亥俄州扬斯敦)的活跃成员。此外,该研究所还为美国空军进行了涉及带金属背衬的 AM 结构的研究,并与大面积增材制造 (BAAM) 打印机的生产商辛辛那提公司(美国俄亥俄州哈里森)合作开发纯 AM 工具。
“我们还与定制复合商合作开发用于 3D 打印机的新原料,但我们所做的一切似乎都没有取得太大进展,而且我们不知道还有其他人比我们更成功,”Huelskamp 回忆道。 “那时我们有了以不同方式解决问题的想法。如果我们无法改变 AM 材料的行为方式或直接预测该行为 ,那么也许我们可以强迫他们间接按照我们想要的方式行事 。”采用 Huelskamp 所谓的“蛮力”方法,UDRI 提出了一项混合 LFAM 研究,该研究将通过应用传统来生产航空结构工具 CFRP 面部皮肤到热塑性复合材料 AM 核心。
该项目的目标很简单:找到一种成本更低、速度更快的方法来制造用于航空结构的大型工具。该团队寻求将成本降低 50% 并生产至少 10 个可接受的原型或小批量生产部件以供后续测试的选项
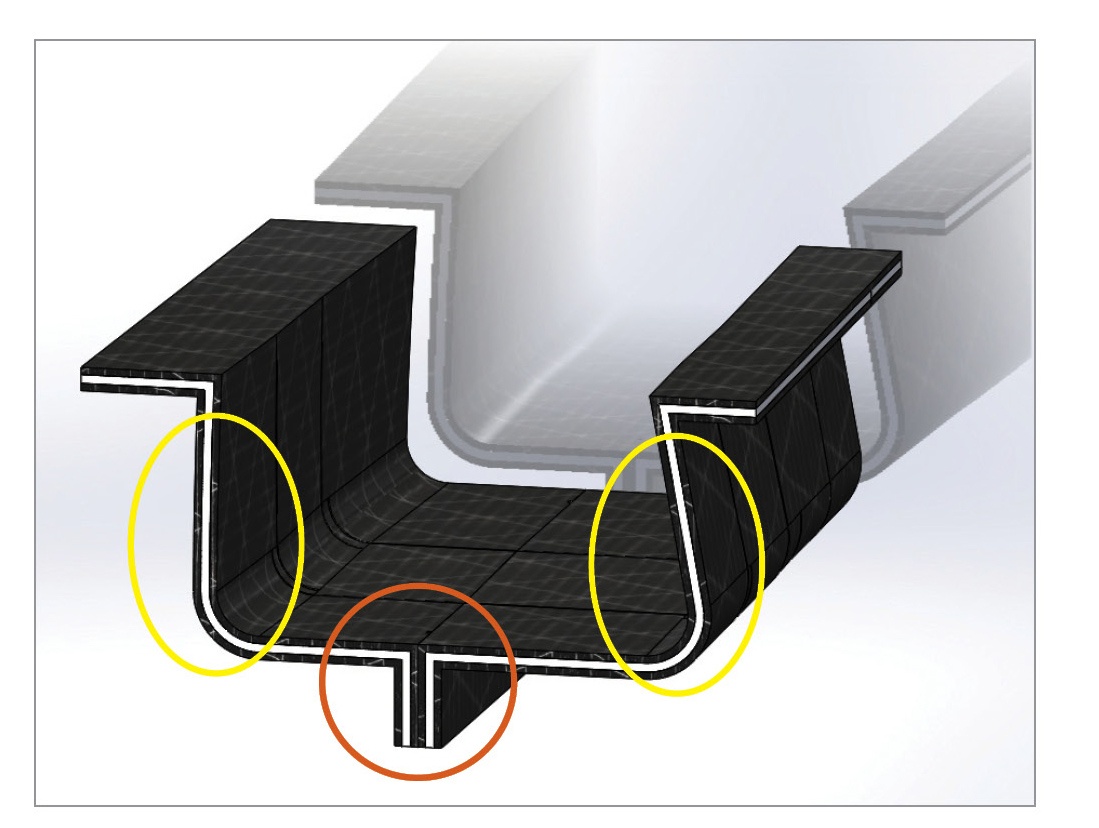
该团队决定使用夹层结构使用来自空中客车公司的工具数据为通用翼梁的一部分生产单面工具。由于 UDRI 设施的空间限制,除了只生产模具来模制全尺寸 C 型梁的一部分之外,没有进行重大的设计更改。
设计了一个凹形工具,以确保使用硬质工具表面形成关键零件的几何形状。这种梁帽工具有一个轻微的向内角度,会产生负吃水和锁模条件,是一个整体工具。这导致研究人员将设计修改为使用垫圈/绳索密封的分体式工具。为了降低风险,该团队开始使用 0.6 米/2.0 英尺的子尺度工具来证明这一概念。一旦工具开发过程和在该工具上生产的原型零件经过测试并发现可以工作,该团队就建造了一个更大的 3.3 米/11 英尺长的工具来模制更大的翼梁部分以进行原型测试。
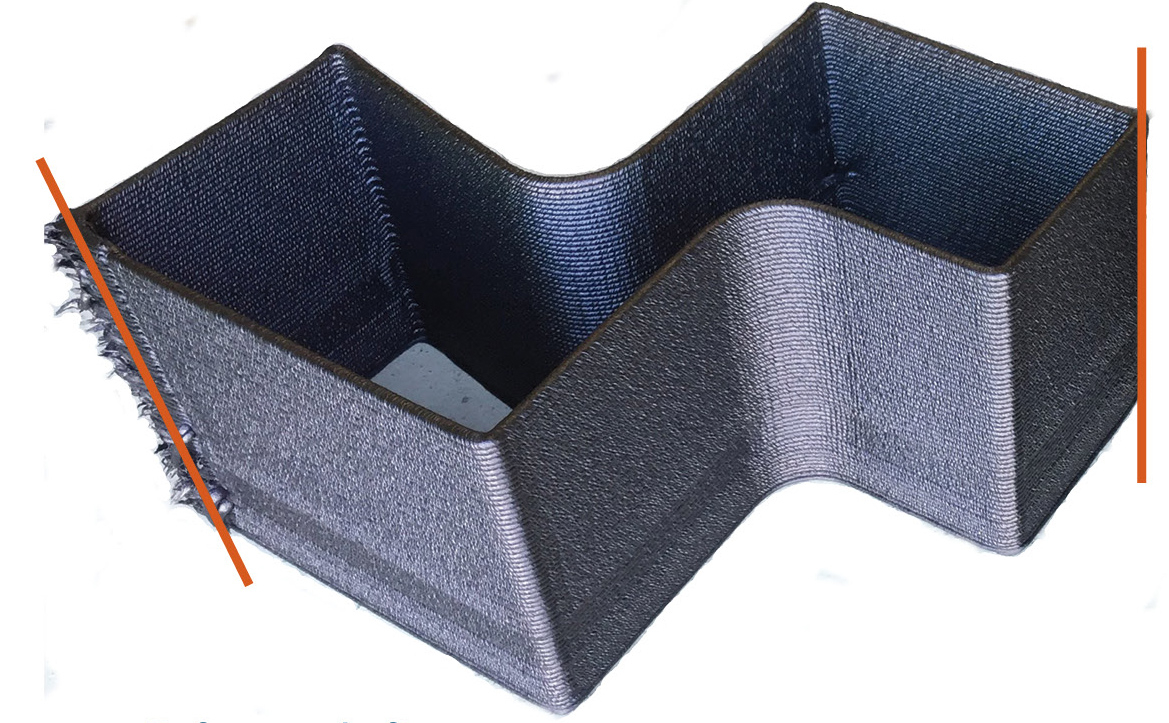
由于 CFRP 工具具有如此低的 CLTE 值,比 Invar 更轻,并且该工具用于原型/小批量生产零件,因此该团队决定使用 CFRP 表面蒙皮来约束 AM 核心。表层使用来自 Hexcel(美国康涅狄格州斯坦福德公司)的 Hextool M81 环氧模具预浸料制成。
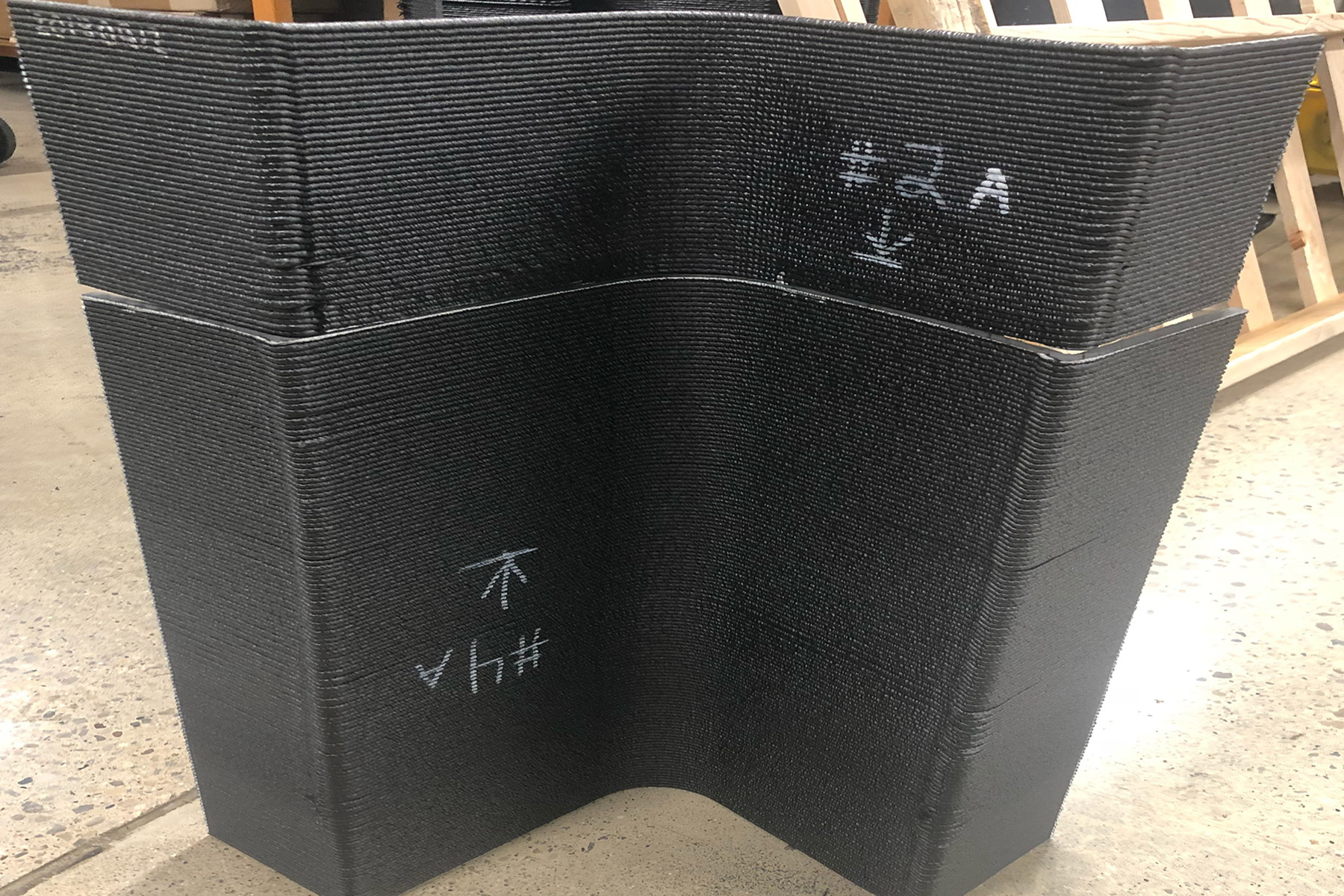
上图显示了子量表右半部分的一部分,BAAM 打印工具,红线表示打印后的切割线。下图显示了部分粘合在一起后的右半工具。图片来源:代顿大学研究所。
材料格式是每平方米 2,000 克/每平方码 59 盎司的短切碳纤维垫,浸渍有 Hexcel 的 8552 增韧环氧树脂。这种材料由于其近乎各向同性的特性而常用于复合模具,这使得模具后加工无需刀具移动,否则可能由残余应力松弛引起。
鉴于核心将在 Additive Engineering Solutions(美国俄亥俄州阿克伦市)的 Cincinnati Inc. BAAM 1000 打印机上打印,并且考虑到 UDRI 和 Cincinnati 在使用高温热塑性聚醚酰亚胺 (PEI) 方面拥有丰富的经验,他们选择了来自 SABIC(沙特阿拉伯利雅得)的 20% 短碳纤维增强型 PEI(Thermocomp EX004EXAR1 Ultem)打印近净形芯。 (碳纤维的存在在打印过程中稳定聚合物并防止其坍塌;在成品结构中,纤维减少了打印方向上的 CLTE。)为了保持低成本,作为模具主体的核心和表面蒙皮直接层压没有粘合剂,但对项目期间开发的知识产权 (IP) 所涵盖的核心表面进行了一些修改。这种方法是有效的,即使经过多次热循环也不会分层。
凝聚制造
在飞机结构 CFRP 工具的常规制造中,首先创建一个低成本的母版。这通常包括在烤箱或高压釜中将工具板块粘合在一起,然后将整体结构加工成所需的零件几何形状。然后将模具材料放置、装袋并在高压釜中固化在母模上。脱模和清理后,将背衬结构粘合到工具上,并再次加工工具表面,以确保良好的几何公差和表面光洁度。
借助混合增材制造工具,该团队开发了一种精简的制造工艺,以减少交货时间和成本。首先,近净形核心(工具母版)被 3D 打印(在短碳纤维/PEI 中)。接下来,将 CFRP 工装预浸料直接层压到芯材的两侧(根据供应商的建议,在一层、四层和七层之间进行热减积)。然后将整个结构真空袋装并高压灭菌。
亚尺度 C-spar 工具的浓缩制造过程。
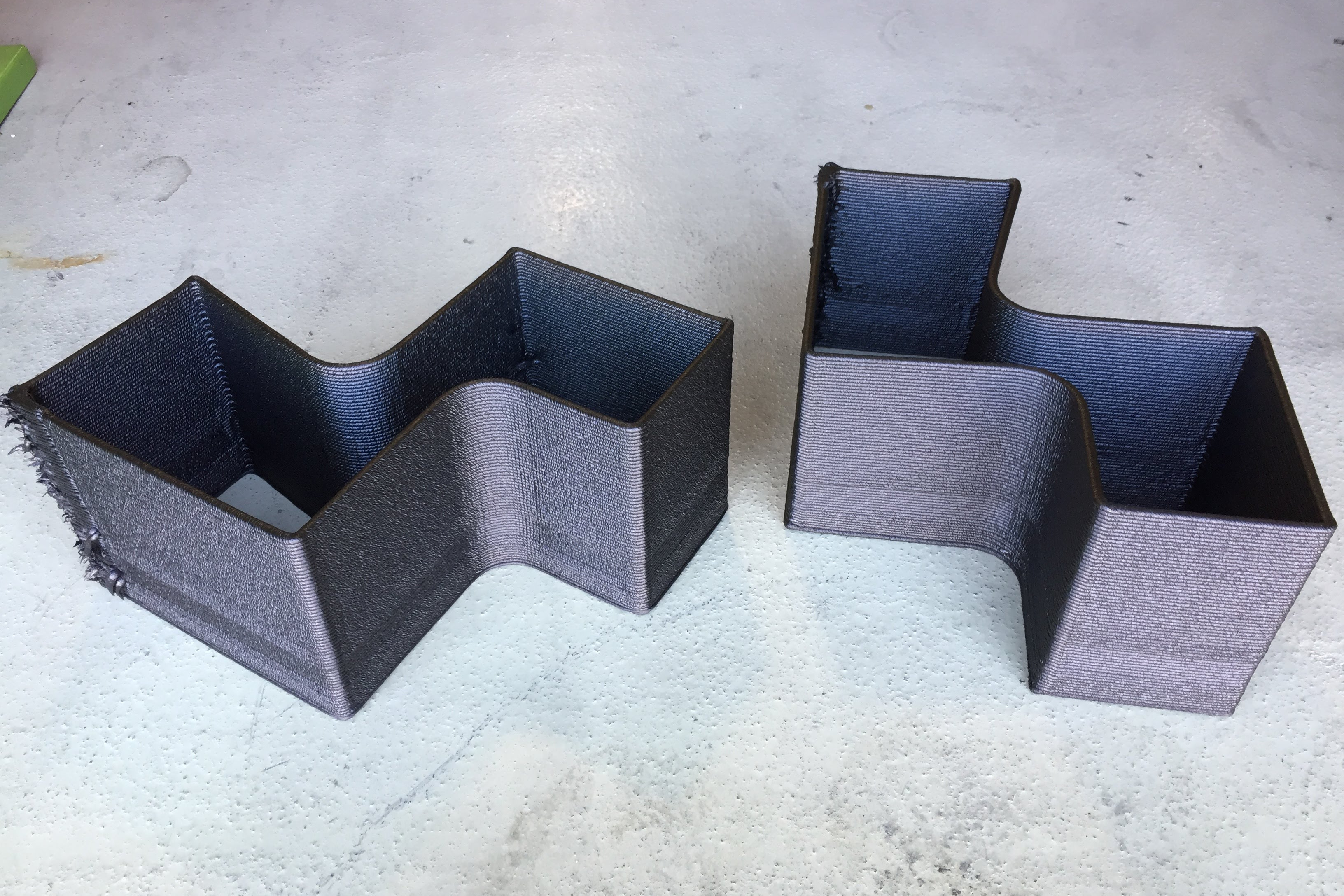
第 2 步:将 BAAM 打印件从中间切割成左右两半。
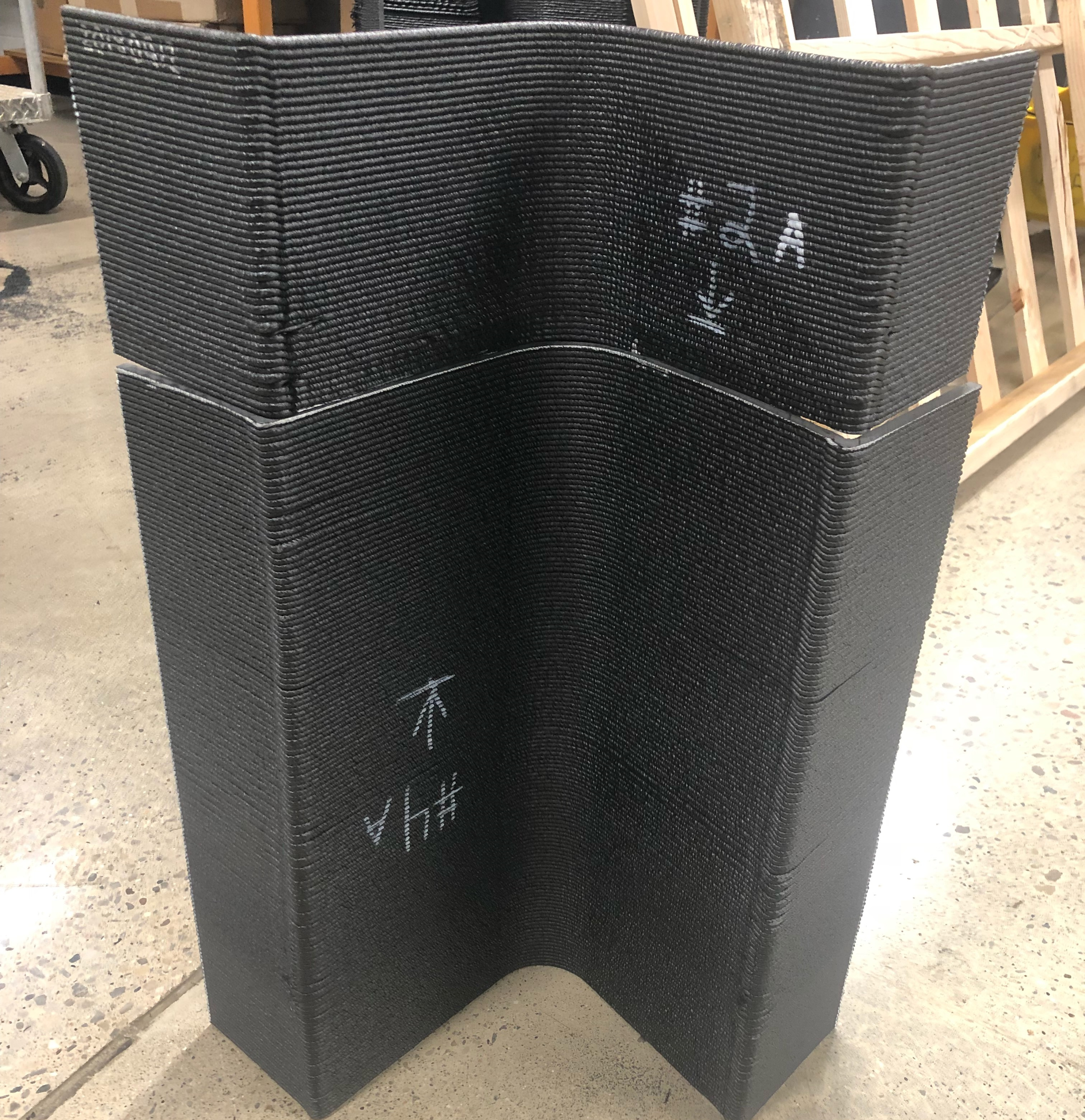
第 3 步:粘合 BAAM 打印以达到所需的长度并固化。
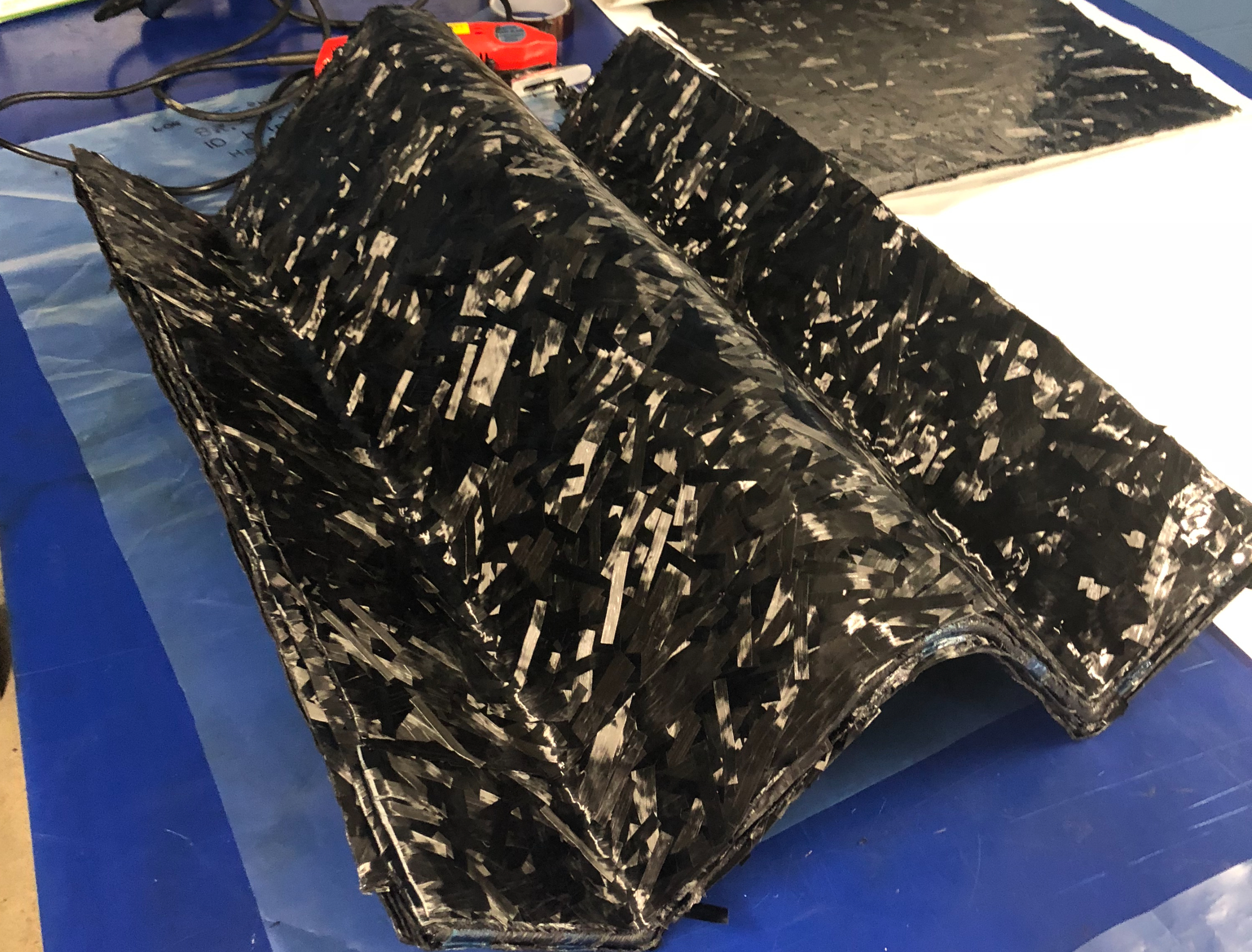
第 4 步:按照制造商的说明,使用热压块将模具预浸料层压到芯材的两侧。
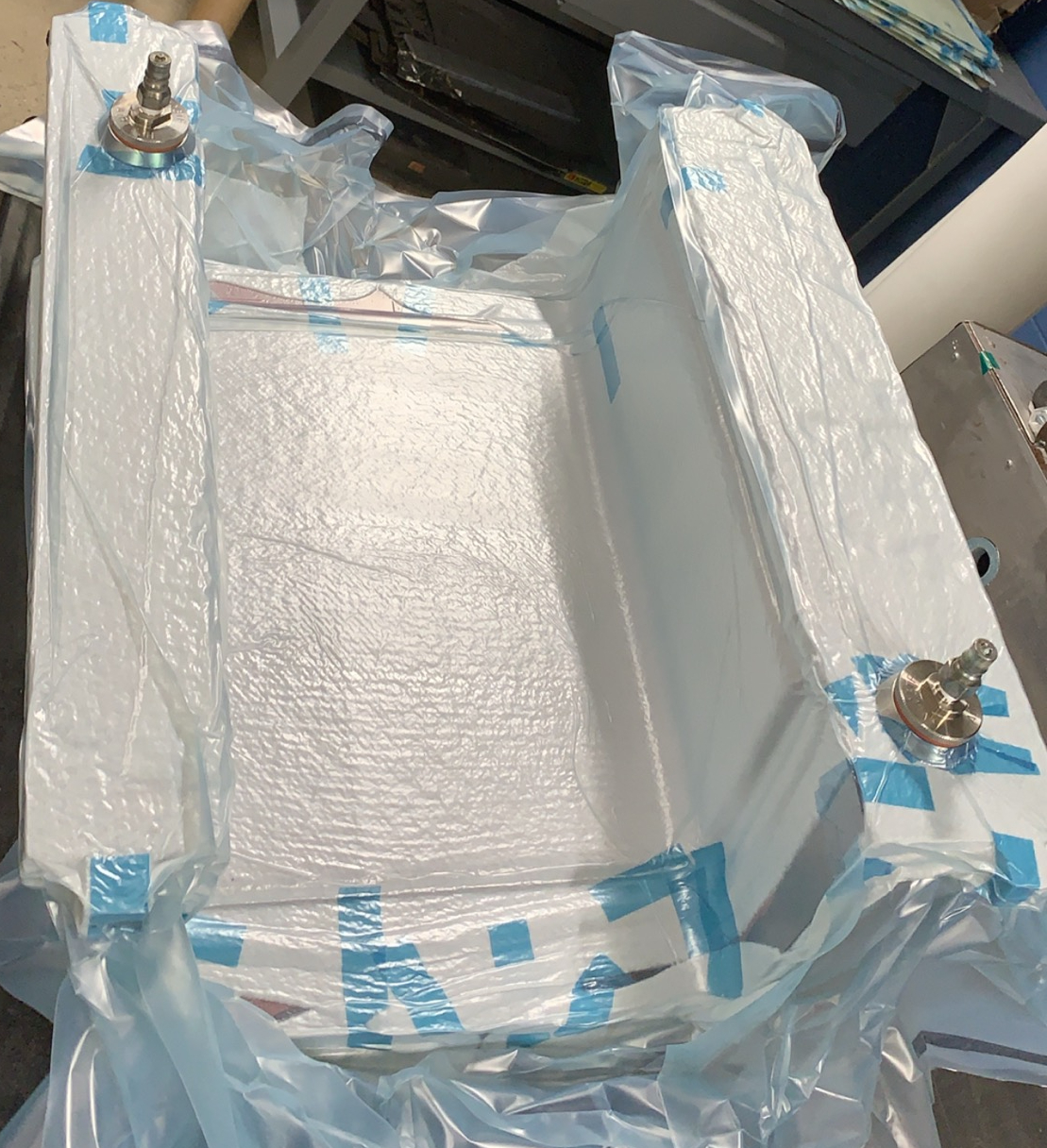
第 5 步:真空袋并在高压釜中固化。
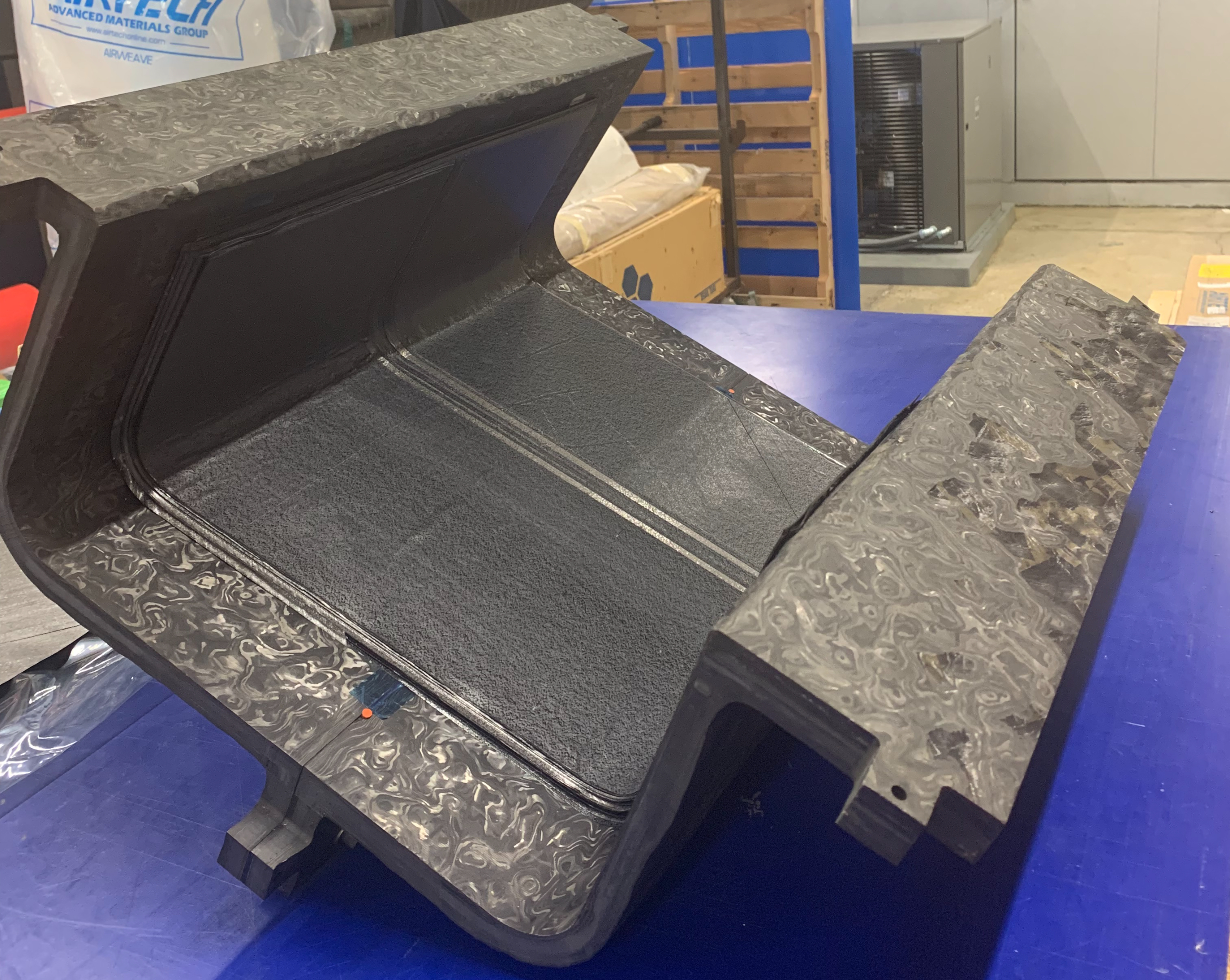
步骤 6:机器固化工具以达到最终尺寸和表面光洁度。
上一页下一页在层压板固化过程中,PEI 芯材和环氧树脂表层之间实现了良好的粘合,因此不需要粘合剂。 CFRP 表皮不仅无孔且比 AM 核心更耐用,而且由于其 CLTE 值低得多,它们还可以在温度偏移期间物理限制核心的运动。只需一次固化和一次加工操作——这都是传统 的主要费用 工具生产——需要达到最终尺寸和表面光洁度。此外,由于采用夹层结构和工具形状,因此不需要背衬,其中包括模具顶部的回位法兰用于横向刚度,模具中心的螺栓接头用于垂直刚度 - 消除了粘合操作。>
初始挑战
研究人员在新流程中面临几个可控的挑战。
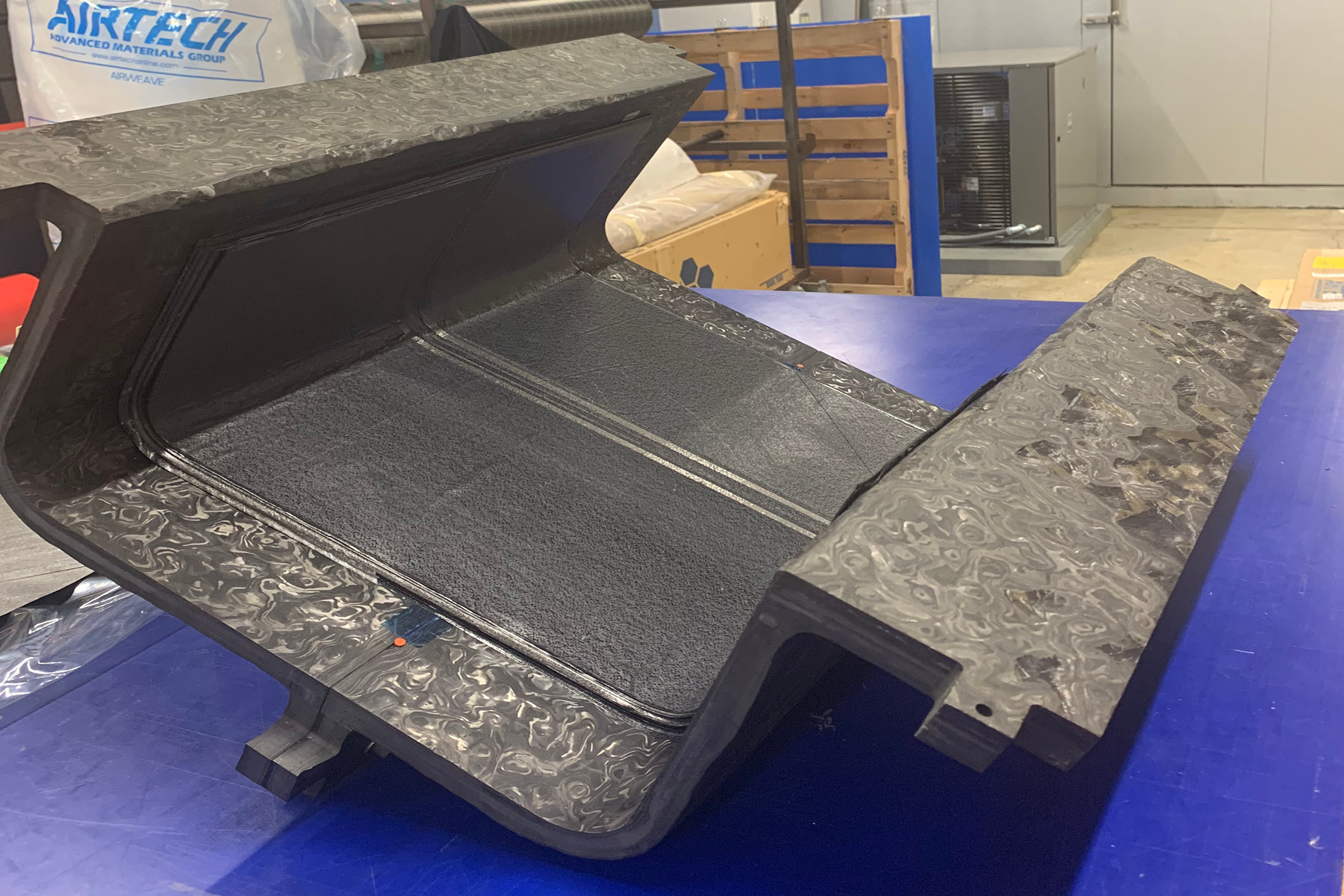
为了便于在 BAAM 上制造,芯的首选制造方向是将横截面打印为垂直构建。对于 0.6 米工具来说,这不是问题;然而,对于更大的工具,3.3 米比 BAAM 1000 可以垂直打印的高度还要高。由于打印机的 Z 轴打印空间限制,研究人员选择将两个亚比例工具的长度减半,然后将它们再次分成左右部分(以解决梁帽底切问题并促进脱模)。
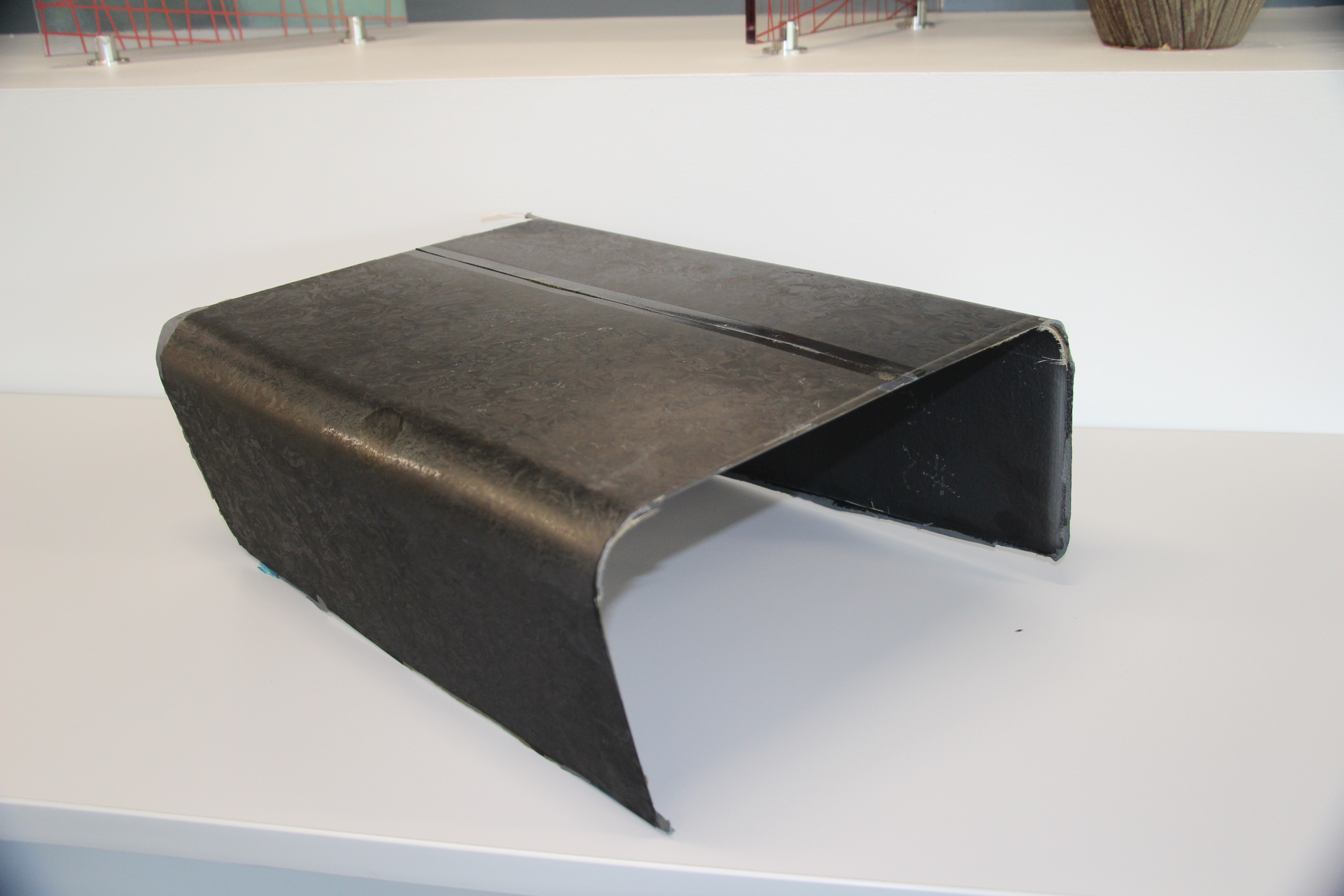
为了提高打印效率,工具部分被背对背打印,然后切成右手和左手部分。为了达到 3.3 米的长度,将两个右侧部分粘合在一起,然后使用汉高公司(美国康涅狄格州洛基希尔)的 Loctite EA9394 环氧树脂粘合剂将两个左侧部分粘合在一起。该团队未加工 AM 核心,认为这对于实现低加工成本和缩短交货时间以及在 AM 核心和每一侧的 CFRP 蒙皮之间建立机械联锁至关重要。每个工具半部的背面层压有五层预浸料,而正面层压有九层,以提供可在后固化加工过程中去除的额外材料。
初步结果
除了控制 AM 核心的 CLTE 外,预浸料还提供了无坑表面,无需密封剂/涂层即可保持真空完整性。这种方法非常成功,以至于它允许使用用垫圈密封的多件式工具设计,研究人员认为,以前在高温下使用的 AM 工具中没有证明过这种设计。此外,工具质量显着减少;子尺度工具的重量是为可比较的因瓦合金设计计算的重量的三分之一。更轻的 CFRP 工具不仅更易于操作和存放在机架上,而且还需要更短的高压釜加热/冷却周期。在用于模制全尺寸 C 型梁的工具上,这种重量优势可能会导致在某些制造空间中是否低于或超过门架/起重机的重量限制。
重要的是,0.6 米混合工具的成本是在制造过程中使用行业标准劳动力计算得出的,为 24,136 美元,其中加工成本和印刷/层压成本大约占 50/50。相比之下,相同的 Invar 工具报价为 46,775 美元——节省了近 50%。 3.3 米刀具的成本并不完整,但在成本/单位长度的基础上预计可节省约 30%,因为材料/印刷成本呈线性增长,但加工成本享有规模经济,从而降低了其影响。混合方法生产的工具满足空客和诺斯罗普格鲁曼公司的运行性能要求,被认为是 Invar 快速原型或低使用工具的可行替代品。工具寿命调查不是本研究的一部分,但可能会大大超出所证明的 12 个周期。
该计划从 18 个月延长至 30 个月,但仍有一些领域需要更多研究,例如了解最终打印的核心几何形状与 CAE 模型中预测的几何形状有何不同。该团队还希望提高预测精度,以便在关键区域添加足够的层,以确保在加工过程中不会出现穿通现象。尽管如此,该团队仍认为这是一个成功的项目,为未来的 LFAM 工具提供了大量机会。
“Northrop Grumman 期待使用 UDRI 制造的 3.3 米长混合工具和我们自己的自动加强筋成型 (ASF) 工艺构建一个 3 米长的梁演示部件,以评估工具的耐用性和尺寸稳定性,”补充道Vern Benson,诺斯罗普格鲁曼公司技术研究员。
树脂