使用 PtFS 的 RAPM 开发
本博客是 2020 年 5 月专题“革新复合材料成本范式,第 2 部分:成型”的在线侧边栏,其中讨论了由波音公司领导的 RApid 高性能制造(RAPM,发音为“wrap-em”)计划。 (美国伊利诺伊州芝加哥),DARPA 可定制原料和成型 (TFF) 计划的“成型”部分,可快速、低成本和敏捷地制造小型、复杂形状的复合材料部件。
RAPM 计划中的所有三个材料和工艺轨道——树脂灌注、热固性预浸料和热塑性成型——包括使用功能规范生产 (PtFS) 像素化加热控制和工具系统的试验,由 Surface Generation 提供,位于波音 R&T圣路易斯(见下表)。
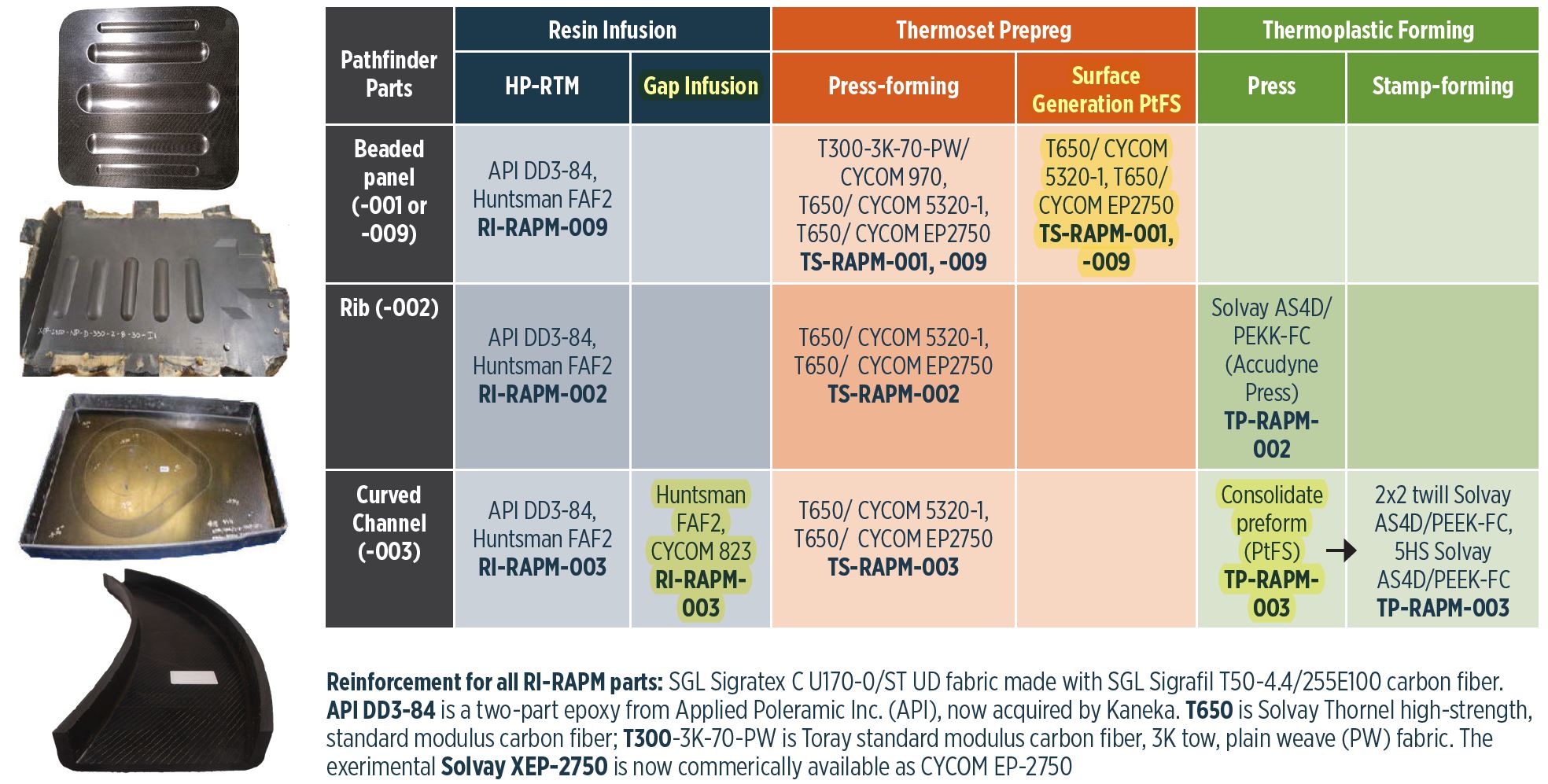
请注意,PtFS 已商业化多年。该博客涉及使用 PtFS 系统的 RAPM 流程开发。此博客的参考资料包括:
- 2019 年 SAMPE(5 月 20 日至 23 日,北卡罗来纳州夏洛特)技术论文和幻灯片演示,“柔性复合材料制造工作单元的可扩展动态控制架构的开发”,Steven M. Shewchuk 1 , 本哈尔福德 2 , Michael P. Matlack 1 , 安德鲁夏普 2 和皮特·梅西 2 . 1 波音公司,美国密苏里州圣路易斯 2 Surface Generation Ltd.(英国拉特兰)。
- 2020 年 SAMPE 技术论文,“复杂热固性层压板的压缩成型”,作者:Travis R. Adams、Timothy J. Luchini、Jared B. Hughes、Steven M. Shewchuk、Adam Martinez 和 Gail Hahn,波音公司。
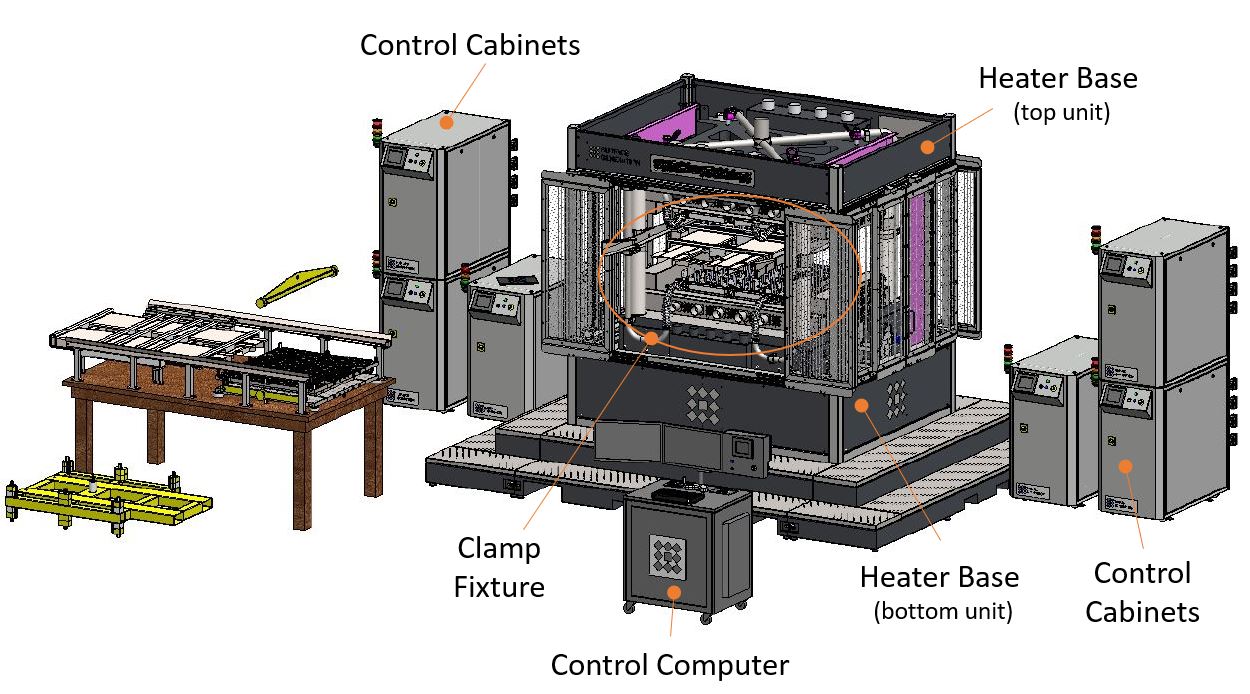
PtFS 系统组件
PtFS 系统是模块化的,可以完全独立或使用现有基础设施的一部分。对于压实/固结压力,该系统可以使用现有的液压机或液压驱动的工具夹具。波音圣路易斯 PtFS 单元配备了后者,一个 150 公吨的夹具 由 Surface Generation 设计。该成型单元可容纳 750 x 750 x 100 毫米的零件体积。
波音圣路易斯 PtFS 单元包括位置和压力控制。 “Surface Generation 的 Orchestrator 软件用于控制 CF-OaO-RAPM PtFS 工作单元,”波音技术研究员兼 RAPM 项目经理 Gail Hahn 指出。 “每个工具都通过位移和压力调整在系统中进行校准。进行压力校准以将液压系统调整为工具在加工过程中将经历的预期压力。工具分离和位移校准是为了设置工具的开/关位置以及慢/快关闭区域,在手动和自动控制过程中保护工具面。”波音复合材料工程师兼 RAPM 研究员 Steven Shewchuk 解释说,位置测量是通过四个弦电位计完成的。 “每个都位于夹具的导柱上,用于测量压板位置,并提供一种安全方法来识别操作过程中的压板移位。压力控制由单个在线压力传感器完成,为夹具的液压泵提供反馈控制。”
夹具的上方和下方是顶部和底部 加热器底座单元 .它们包含所有加热/冷却组件,并根据控制柜的输出进行操作 (波音设置中每个加热器底座三个机柜)。工具面专为每个加热器底座设计,并使用导轨和加载系统进行安装。
每个工具面使用压缩空气加热和冷却,压缩空气直接吹向每个工具面的下侧,并通过扩散器分散。每套匹配的金属工具面 分为 180 个可单独控制的加热器通道 — 顶部工具面为 90,底部为 90。加热器通道在每个工具面的网格中间隔 10.0 厘米。每个通道都有一个加热器、一个两级压缩空气源和两个反馈热电偶 弹簧加载以确保与工具面的背面紧密接触。 RAPM 工具面的加热使用每分钟加热通道 1 立方英尺的压缩空气,而冷却使用每分钟 3 立方英尺。
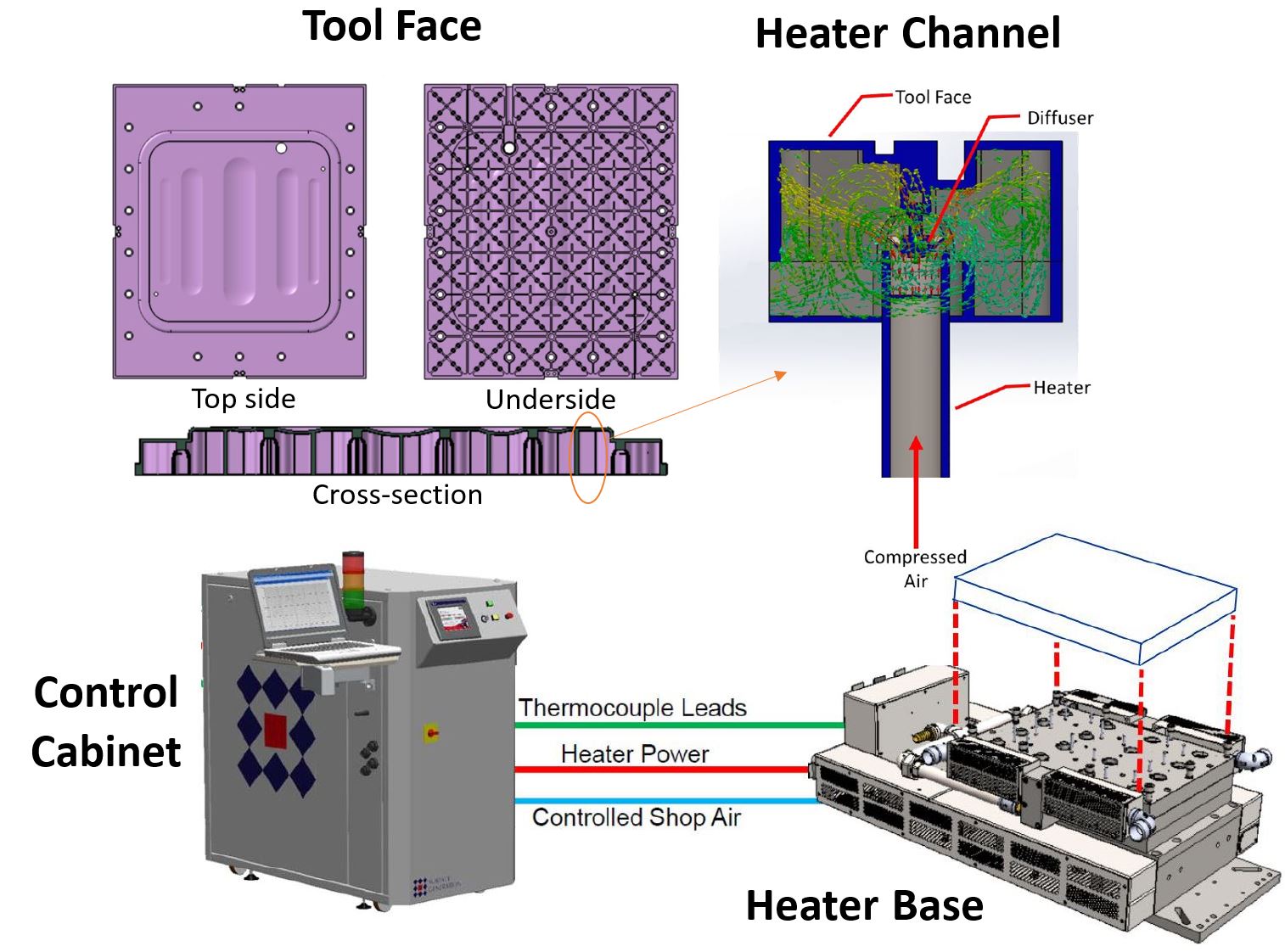
工具面
RAPM 中的工具面由工具钢加工而成,厚度约为 3 毫米。 TS-RAPM-001-201 的下工具面显示在上图中的左上方。工具面的顶部看起来像一个标准的冲压成型工具,但底部露出加热通道。
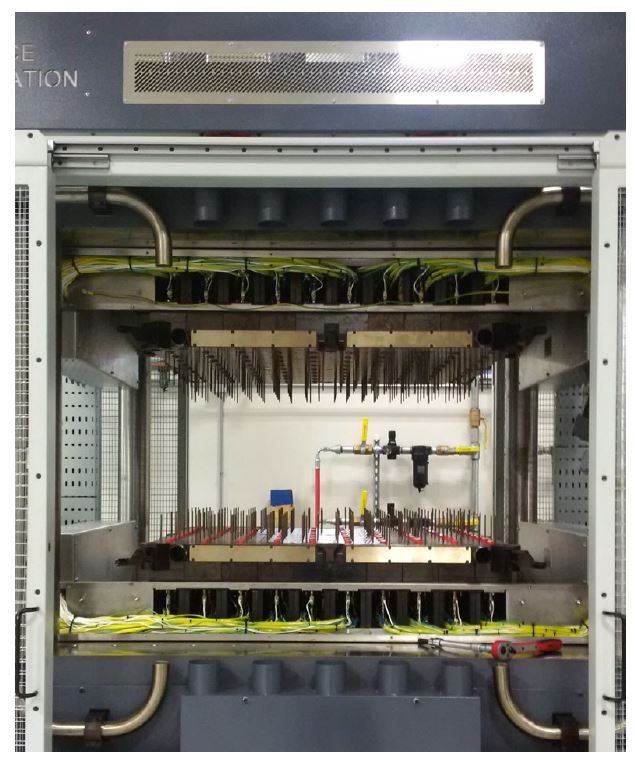
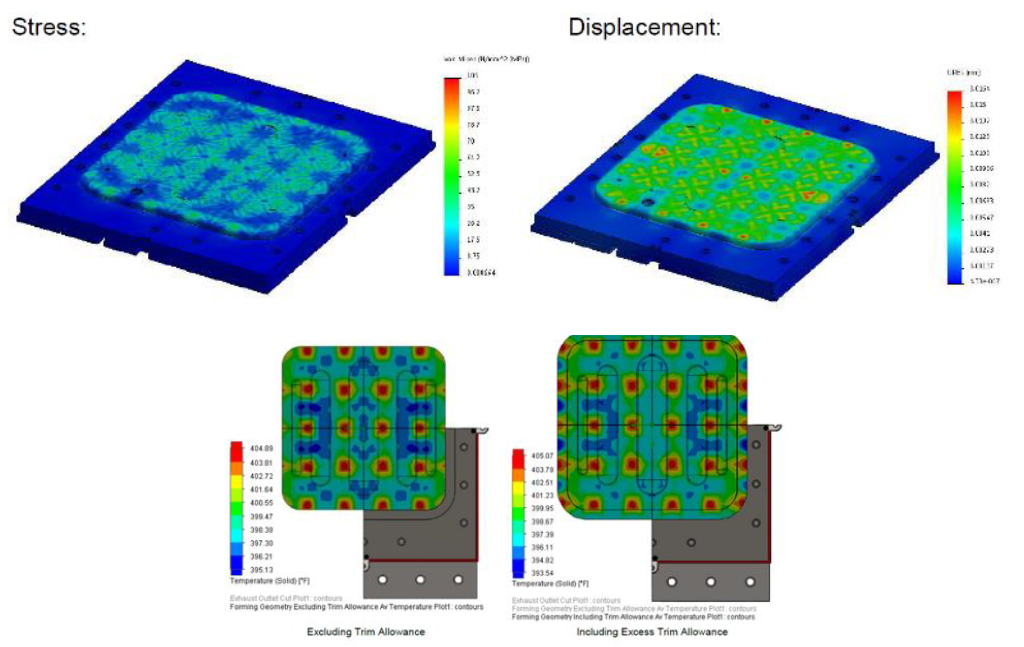
可接受几何形状的工具面可以更换为为同一加热器底座设计的其他工具面。该工具需要相同的加热器通道尺寸、大致的热电偶放置位置以及弹簧加载热电偶行程范围内的深度。
用于更换工具面的导轨加载系统将所有 180 个弹簧加载反馈热电偶对齐到工具面背面的套管中。销对齐工具面并允许在没有精确叉车控制的情况下完成工具加载。 2-4小时即可完成换刀,包括将刀面拆卸和重新组装到相框内的两名操作员。
加工掉尽可能多的材料,以减少热质量并提高加热和冷却速度。因此,RAPM 中使用的每个工具面都需要进行结构有限元分析 (FEA),以确定工具面是否能够承受加工温度和压力。工具面使用线性和非线性 FEA 以及稳态和瞬态计算流体动力学 (CFD) 热分析进行了优化。后者有助于确保均匀的工具加热。每个加热器通道内的工具厚度和空气扩散器都经过修改,以提高温度均匀性。 FEA 和 CFD 之间的迭代循环支持定制几何形状,以帮助保持所需的工具面温度,同时满足工具面支撑所需的安全因素。
加热区和温度控制
加热器通道通常分为多个区域,每个区域指定每个部件的加热器通道数量。每个区域都有一个与之相关的加热曲线,并且可以根据需要在区域内和区域之间设置公差。这允许每个区域中的所有加热器通过动态改变加热器功率水平和压缩空气流速,按照规定的加热曲线加热、冷却或保持温度。
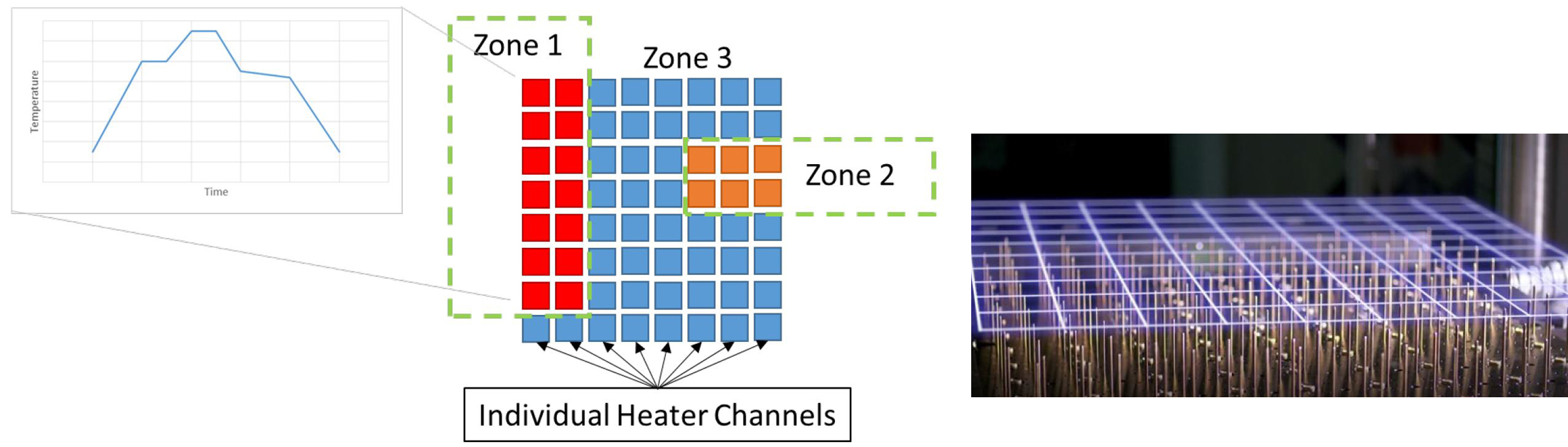
虽然 PtFS 设备控制软件具有模拟和数字两种加热策略,可以针对不同的加热场景进行定制,但 RAPM 单元使用模拟控制。这需要自动调整系统以确定目标温度下的加热器功率水平。设置每个加热器的功率水平以防止加热/冷却斜坡期间过冲或下冲,并保持温度设定点。自动调谐自动为每个指定温度下的每个加热器通道确定修改后的比例积分微分控制方法的常数值。自动调谐完成后,可以为每个区域写入加热曲线。验证所有热曲线以确保复合材料部件暴露在所需设定点 ±5.5°C (±10°F) 范围内的温度下。
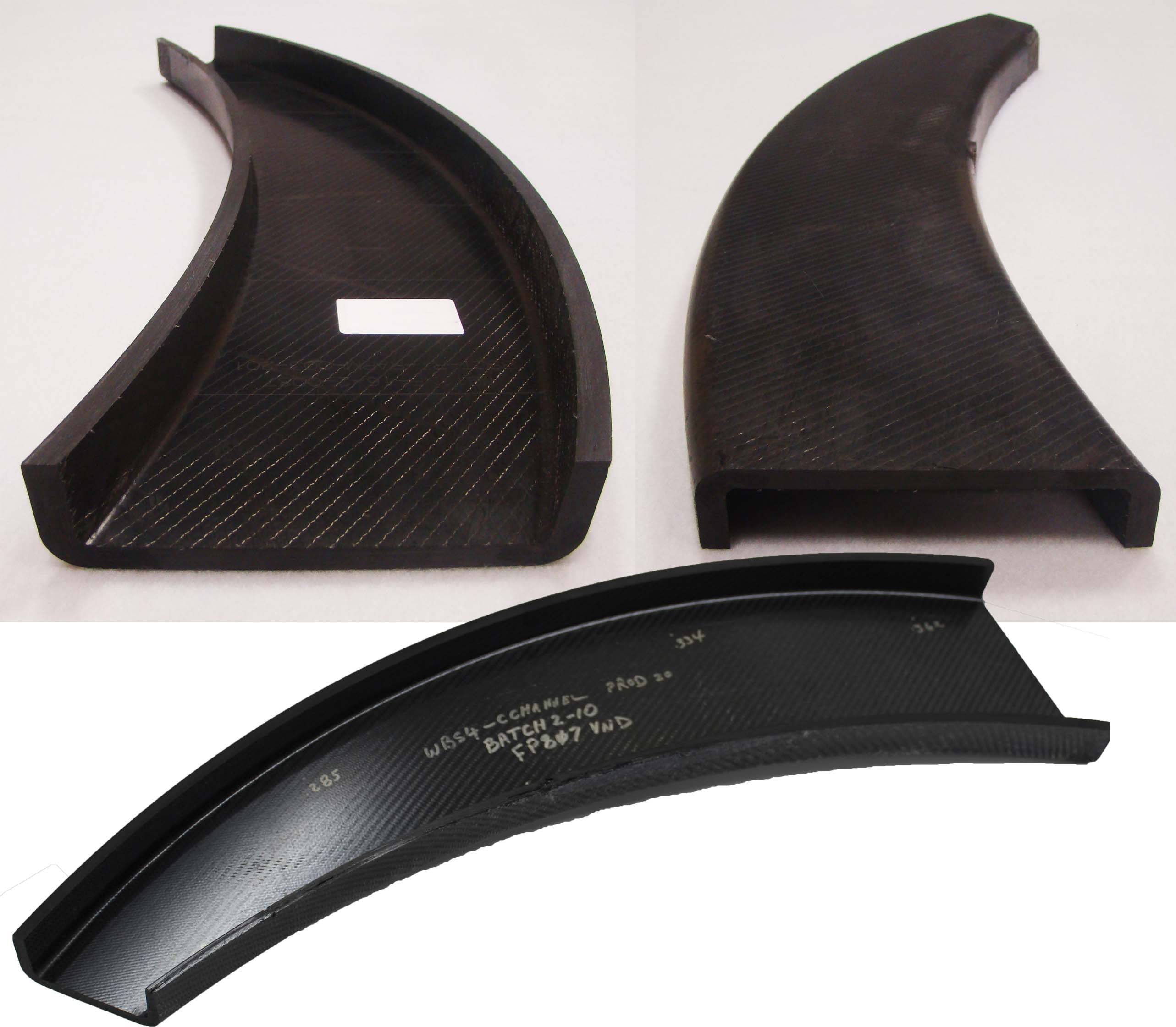
波音 PtFS 电池的最高温度为 440°C。最初,当波音在一天内处理多个高温循环时,有人担心某些组件可能会因处理循环之间缺乏冷却而损坏。但是,冷却系统在 2019 年 9 月至 10 月进行了升级,包括用于散热的额外风扇容量。通过这种改进的冷却,电池可以在 440°C 下连续加工。
使用大量环境温度压缩空气作为冷却方法,工具面冷却在温度范围的顶端附近快速,但在达到 60°C (140°F) 时显着减慢。在加热到热塑性塑料温度 (>350°C) 期间,工具面温度以 41°C/min (74°F/min) 的平均速率上升。在相同运行的冷却过程中,峰值平均冷却速率为 36°C/min (65°F/min)。使用压缩空气进行冷却提供了更连续的冷却斜坡,并结合主动热管理(即在需要时加热),在冷却过程中温度保持相当线性。
等温 TS 预浸料冲压
使用 PtFS 工作单元的第一部分试验是针对采用热固性预浸料压缩成型(冲压)制成的 TS-RAPM-001 珠状检修盖板。这部分的工具占据了 RAPM PtFS 工作单元中 180 个通道中的 112 个。这包括顶部工具面上的 56 个通道和底部工具面上的 56 个通道。然而,实际部分并没有覆盖整个工具——而是只覆盖了每个工具面的 56 个通道中的 30 个,上下。下图显示了用于 RAPM-001 部件的 78 个热电偶 (TC) 的放置 - 39 个用于顶面,39 个用于底面,两者的放置位置相同。 TC 的数量包括每个单元(加热器通道)一个,加上在 CFD 热分析中确定的热区和冷区的额外 TC。
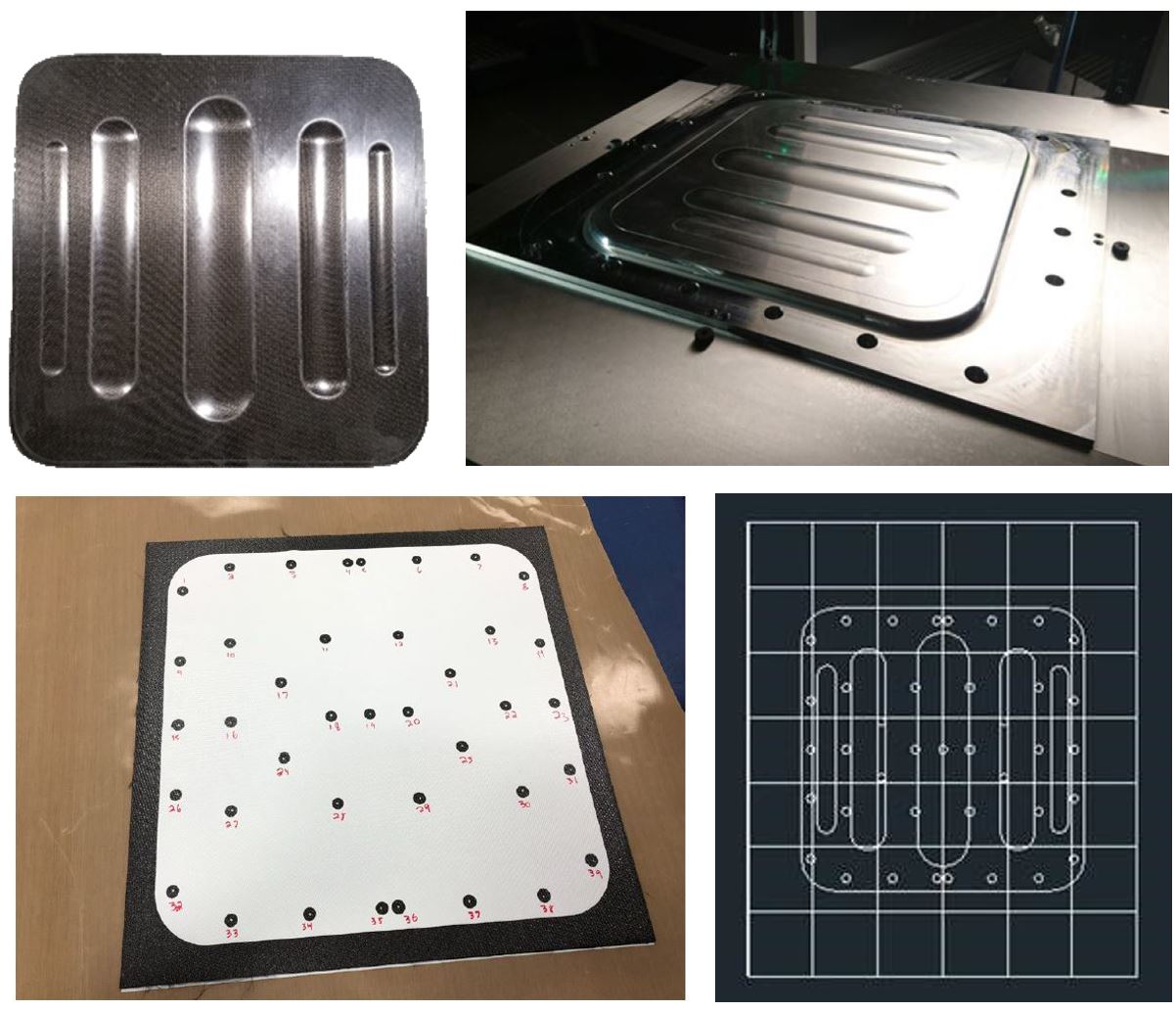
测试空工具面的温度均匀性,然后在 16 层碳纤维编织/环氧树脂层压板的中点嵌入热电偶后重复测试。添加复合材料后,由于复合材料充当传热路径,因此工具面温度分布变得更加紧密。此外,复合层压板内的温度均匀性比工具表面读数更严格。 Run 1 中的单个 TC (见下图,右图顶部) 在所需温度范围以上振荡的部分靠近零件边缘,怀疑是由零件修整线外相邻单元的温度波动引起的。
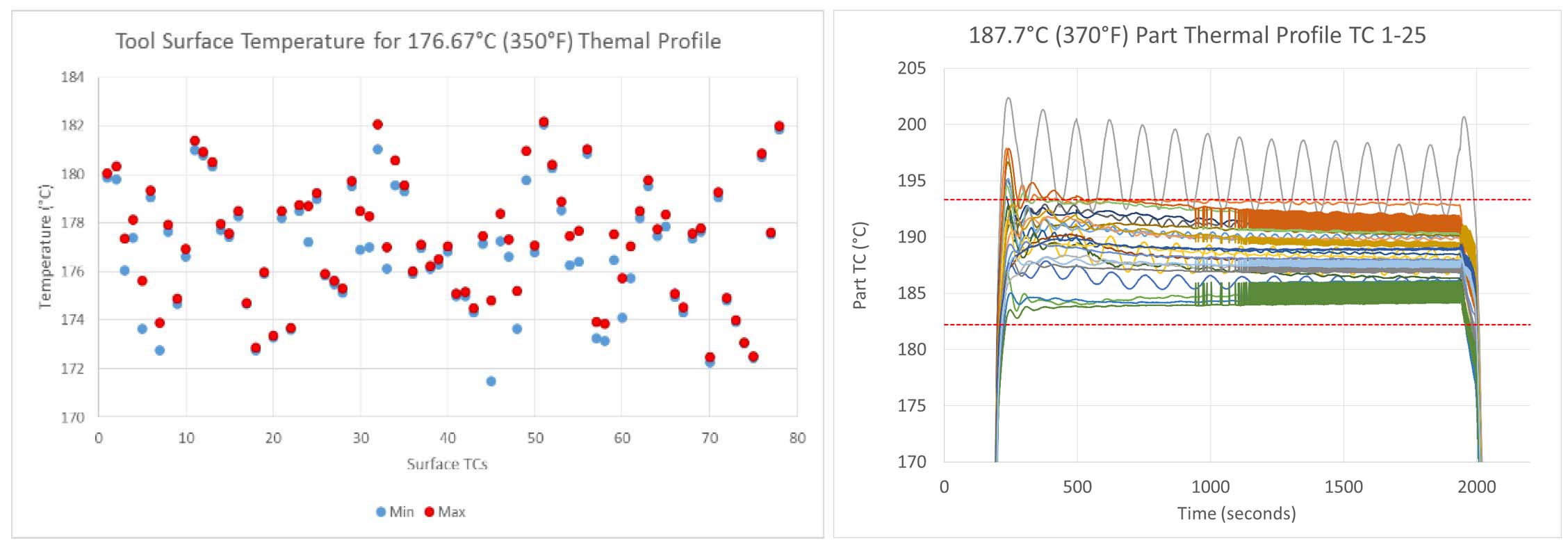
加工的等温压缩成型使工具保持在 176.7°C (350°F) 的±5.5°C (±10°F) 公差范围内。对于 TS-RAPM-001,遵循以下顺序:
- 系统在应用程序中加热到 187.7°C。 8 分钟
- 复合坯料加载到热工具中
- 工具在 12:09 关闭(例如)
- 30 分钟凝胶复合材料时间
- 第一压力阶段:坯料的初始快速加热,同时最大限度地减少树脂挤出
- 第二个压力阶段:升至 300 psi 以确保良好的固结并防止空隙增长
- 从热工具中去除“绿色”复合材料以进行后固化
这个过程确实获得了高质量的零件,并且展示了比当前复合材料工艺更短的零件周期。更高的工艺温度可以更快地使复合材料胶凝,但也可能导致材料降解和放热风险。这是一个令人担忧的问题,因为 PtFS 工具不使用传统的大热质量来吸收放热,而是依靠低热质量工具背面的主动冷却来消散放热。
PtFS 单元还用于制造 TS-RAPM-012 “波浪”挑战部件。使用先前的开发试验,确定使用 177°C 下 30 分钟的等温循环来固化这些部件,然后在相同温度下进行 2 小时后固化。然而,与之前试验的不同之处包括使用 CYCOM 5320-1 环氧树脂(高压灭菌航空航天部件的标准)与 8 线束缎面和单向碳纤维层以及外层相结合的更具侵略性的几何形状和准各向同性铺层一侧采用 108 型玻璃编织布。 RAPM PtFS 控制器被编程为对层压板施加最小的压力,直到达到合适的粘度。在此初始步骤之后,施加最终压力以完成固化。一项试验在烘箱中进行后固化,而其余试验则在 PtFS 夹具中进行后固化,以减少试验之间的时间。生产了多个优质零件。
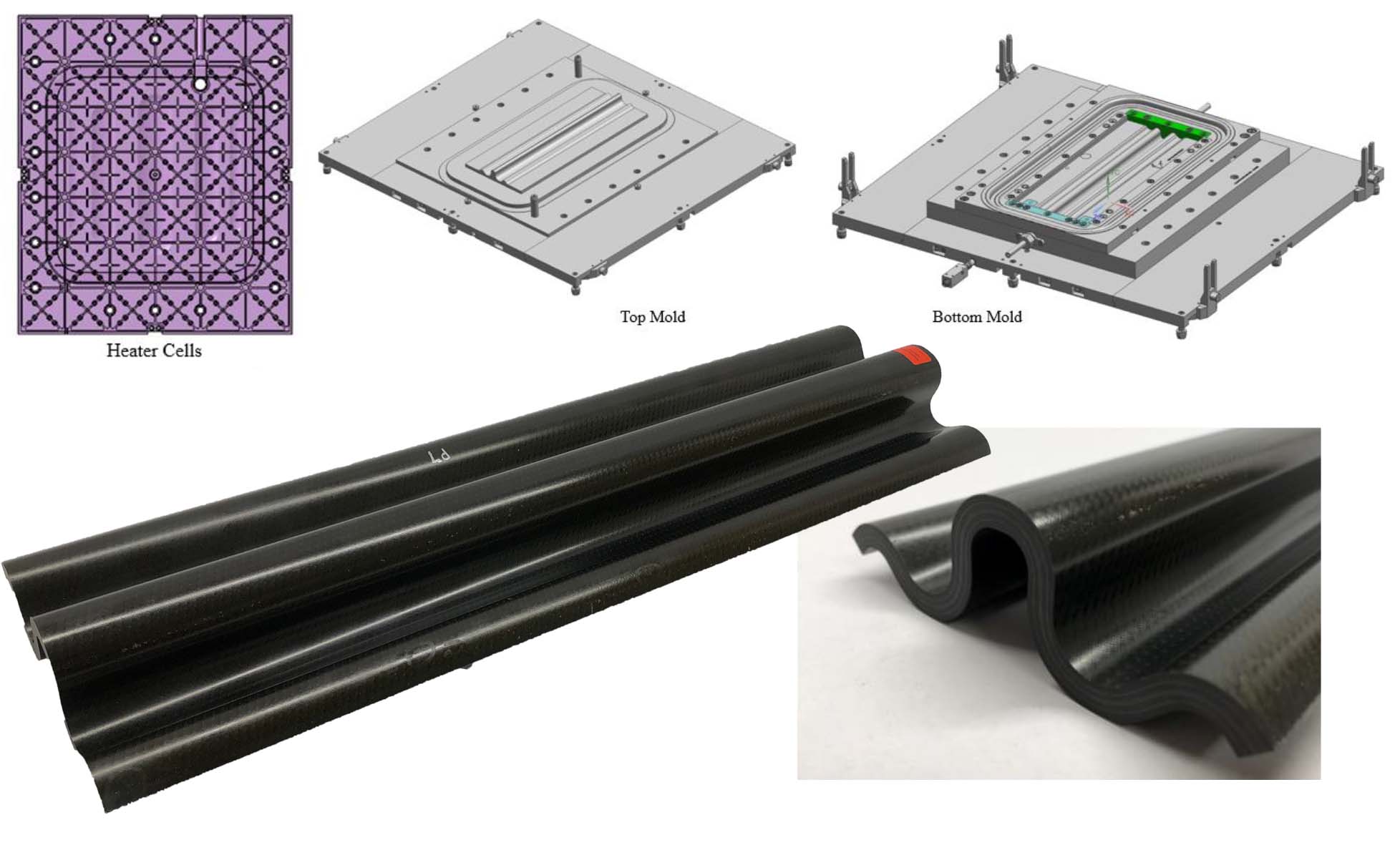
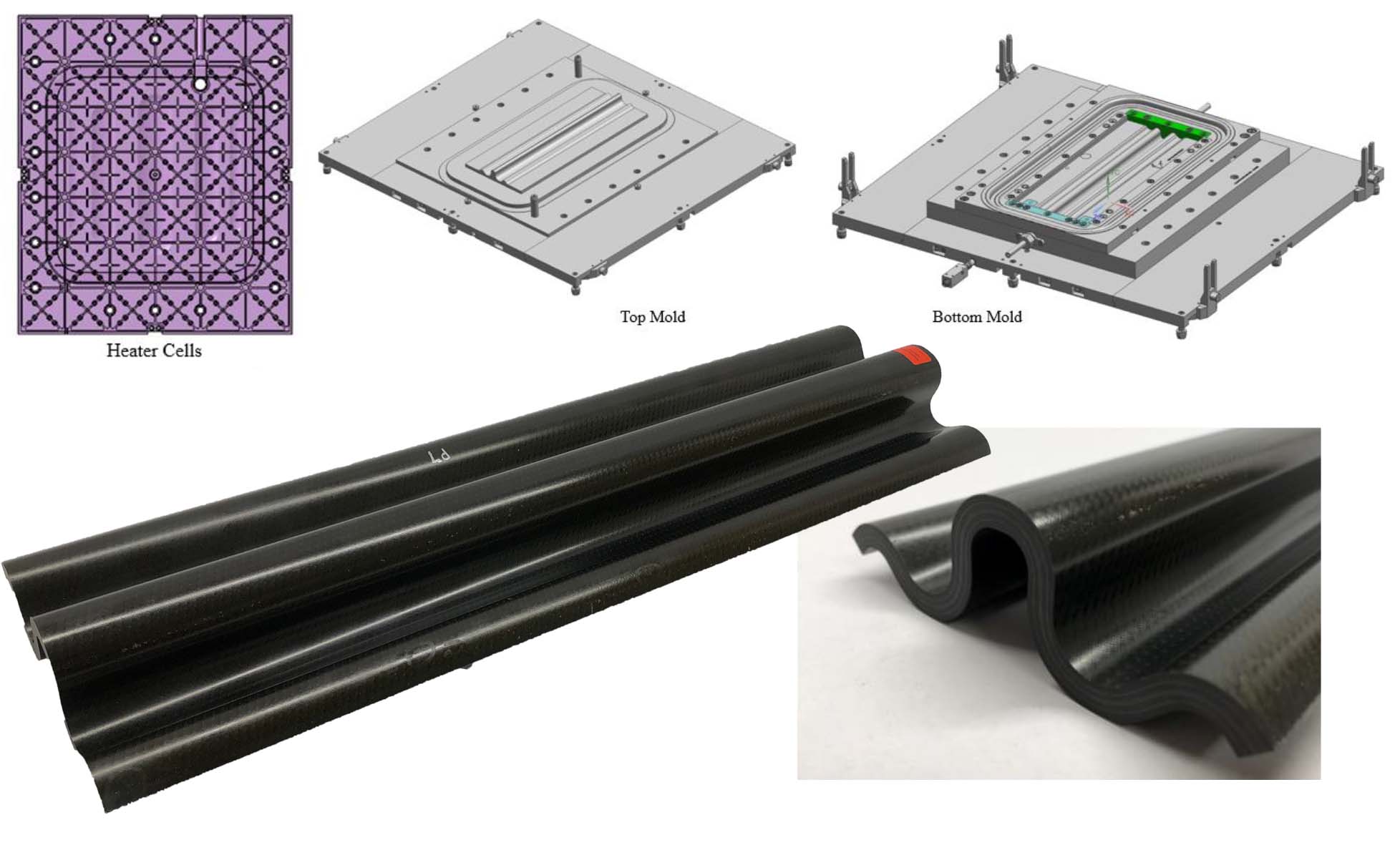
树脂灌注的动态温度循环
使用 PtFS 工作单元的树脂灌注部件试验从 RI-RAPM-003 弯曲 C 通道部件开始。初步试用了三种不同的环氧树脂体系:
- Solvay CYCOM 823,在 80° 下注入,然后在 125°C 下保持稳定
- Huntsman FAF2(快速固化系统)在 100°C 下灌注并保持 150°C
- Applied Poleramic(现已被 Kaneka 收购)API DD3-84(也是一种快速固化系统)在 60°C 下灌注,保压温度为 160°C。
将无卷曲织物预制件灌注,以 2°C/分钟的速度升温至指定的停留温度,然后在冷却前保持 60 分钟。对于快速固化树脂,随着放热反应的进行,PtFS 会自动对特定工具区域进行主动冷却,以保持特定的零件温度。
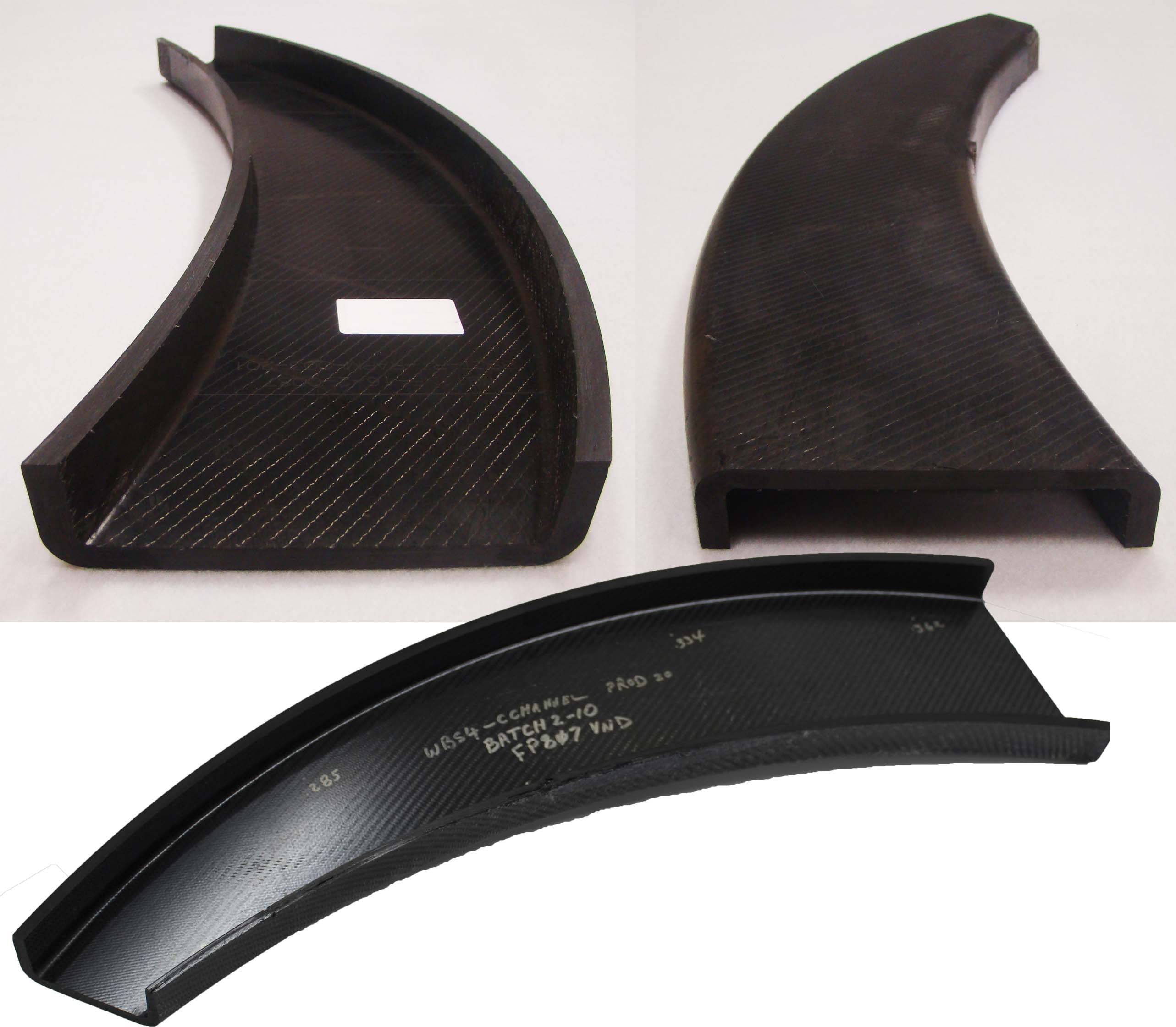
PtFS 设备还能够提供位置控制,以支持 RI-RAPM-003 部件的间隙灌注方法。在这种方法中,工具被关闭到真空垫圈的初始高度,使工具在灌注过程中保持打开 1.3 毫米。灌注完成后,将工具关闭剩余的距离,以沿 z 方向将树脂驱动到预成型件中。使用此工艺成功制造了零件。
热塑性塑料冲压的动态温度控制
PtFS 设备还用于制造热塑性复合材料中的 RAPM-003 弯曲 C 通道。具体来说,它用于将复杂的预制件(沿零件长度从 32 层降低到 24 层)合并为具有锥形横截面的扁平坯料。然后将合并的坯件送到 ATC Manufacturing(美国爱达荷州 Post Falls),该公司用垂直法兰对最终零件进行冲压。
为 TP-RAPM-003 弯曲 C 通道加固的材料是碳纤维 2x2 斜纹织物,粉末涂有聚醚醚酮 (PEEK)。 PtFS 工作单元用于在热塑性装料上超塑性形成 AZ31 镁气囊,加热气囊和装料到 400°C 的 PEEK 工艺温度。 55 分钟。
在此成型温度下,向气囊施加氩气,从而向热塑性复合材料施加固结压力。然后电池冷却气囊并在 30 分钟内充电至 PEEK 结晶温度以下,总循环时间为 3 小时。
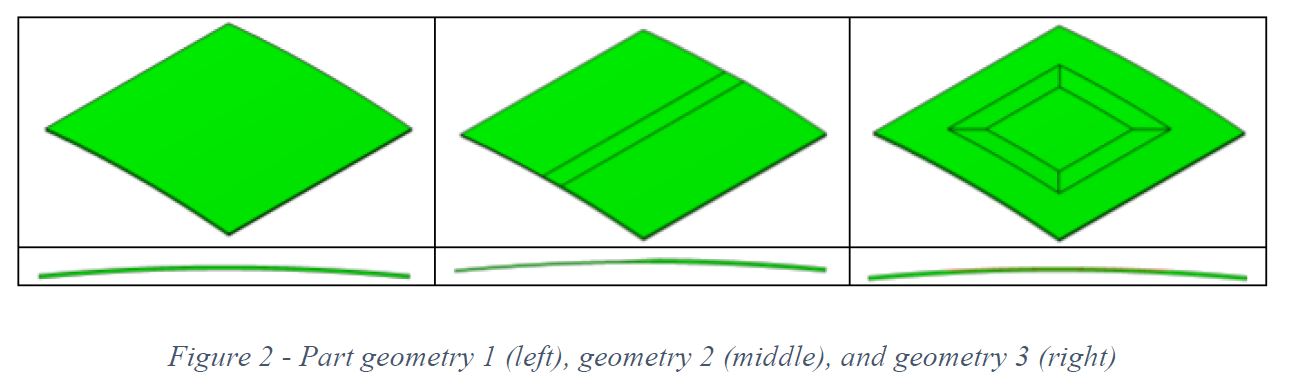
上面的幻灯片 11 显示了在气囊超塑性成型和热塑性塑料固结过程中施加的压力的进展——在气囊达到超塑性成型温度后从 20 psi 增加到 140 psi,该温度通过冷却保持。预成型件被成功整合并发送到 ATC Manufacturing,在那里为这种极具挑战性的几何形状冲压零件。
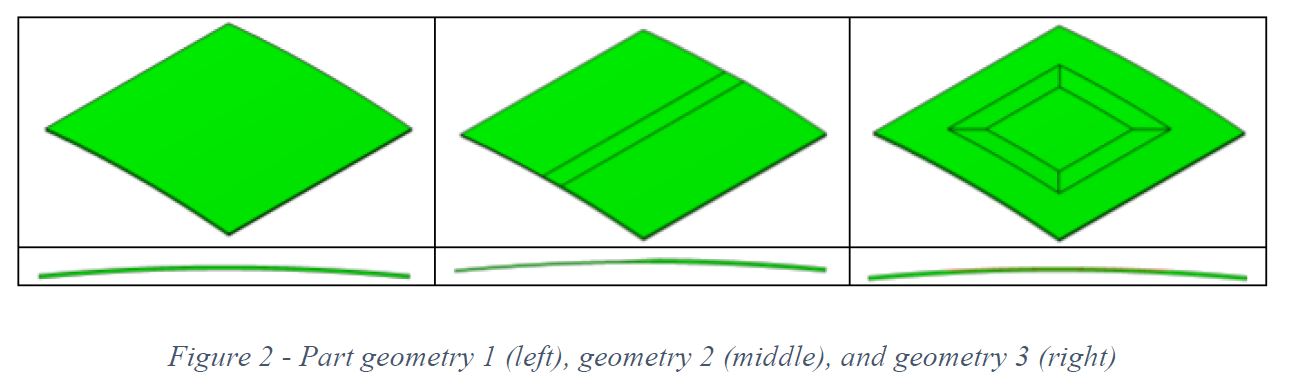
PtFS 单元还用于对由单向 (UD) 碳纤维/聚醚酮酮 (PEKK) 带的平衡和对称叠层制成的 TP-RAPM-017 面板进行一步坯到零件冲压,以研究各种选项如何和零件特征影响膀胱成形。 TP-RAPM-017 面板的尺寸为 40.6 x 40.6 厘米,轮廓柔和,高度为 1.3 厘米。评估了三种不同的零件几何形状 - 平坦(无层落下)、单向层落下和相框 - 厚区域有 32 层,薄区域有 16 层,两者之间的层跌落比为 20:1。所有几何形状的零件周期时间为 1.5 小时。
工具面由 Invar 42 加工而成,以最好地匹配 UD 热塑性复合带的热膨胀。 UD 胶带层套件被切割和整理,超声波焊接在一起并放入固化工具中,在那里它们被加热到 385 ± 15°C。测试各种压力循环,然后将零件冷却到220°C以下,然后释放压力并脱模。
几何形状 1 的压力循环的一个示例是室温下 20 psi,在滞后热电偶达到 310°C 的熔化温度后斜升至 140 psi,然后在压力下以 10°C/分钟的速度冷却,直到测得零件热电偶低于 220°C .试验了 20 psi、30 psi、50 psi 和 70 psi 的初始压力。压力斜坡也从每分钟 10 psi 到每 15 秒 10 psi,直至最大压力 140 psi。
一个值得注意的结果是,所有板都显示出较差的 C 扫描结果,其中板层是超声波定位焊接的。因此,为了获得最佳效果,此类定位焊应位于零件净修边线之外。生产了合格的部件,但有些部件在层的边缘处表现出较差的固结性。这可以通过在加热前将初始压实压力增加到 30 psi 来解决。然而,这种压力的增加确实会导致零件气囊侧的表面粗糙/无光泽。此外,使用 50 和 70 psi 初始压实压力制成的一些几何形状 2 面板在零件中心显示出皱纹。人们认为,这些较高的压力可能会阻止层片在加工过程中相互滑动,从而在零件中形成皱纹。
另一个尝试的变化是用更便宜的氮气代替氩气来对气囊加压,但这也降低了零件质量,包括表面粗糙度/哑光表面,这会导致 C 扫描结果的衰减程度更高,即使在交叉扫描中没有发现孔隙率。部分。
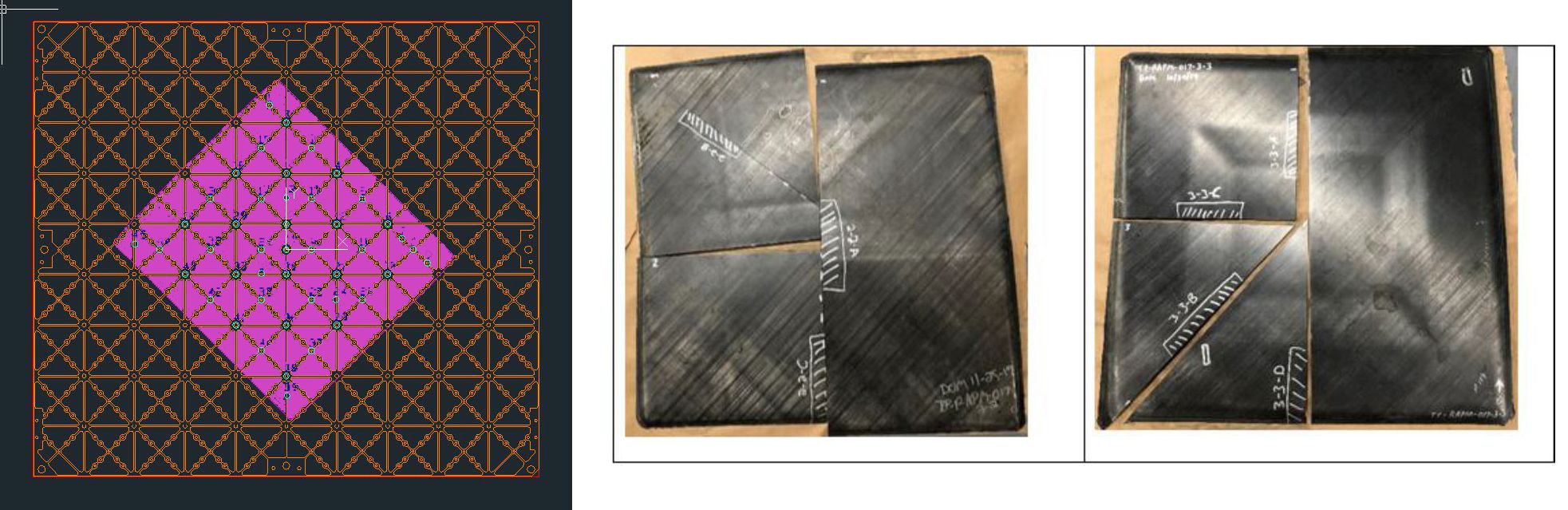
RAPM 中 PtFS 的优缺点
PtFS 工作单元确实显示出快速加热(在 ≈180°C 下环氧树脂固化 <10 分钟)。当与自动化工具更换相结合时,这可以实现快速零件更换并降低复合零件的成本,以实现短期制造。 PtFS 也非常适合高温动态运行(与等温部分循环相反)。
在 RAPM 计划期间,波音圣路易斯 PtFS 单元的能力得到显着提高,这要归功于改进的软件升级以实现更好的热均匀性和夹具控制、改进的冷却能力和热电偶控制,以及自动化压釜压力控制系统。通过使用系统每秒生成和记录的大量数据,包括每个加热器通道设置点、加热器功率杆、压缩空气水平等,可以进一步提高能力。将机器学习应用于这些数据可以生成零件质量和流程改进。进一步的软件增强还可以让这些数据识别处理异常,例如需要过多的能量和特定工具位置的低响应性。
“顾名思义,PtFS 提供了大量定制:从生产到功能规范,”Hahn 说,“但这种定制可能需要投入时间来建立和‘调整’系统以适应新的工具/零件配置。”大多数用于 RAPM 的机加工金属工具面设计是由英国的 Surface Generation 生产的 然而,波音公司和 Surface Generation 确实“培训”了一位美国工具设计师和一家美国工具制造商,以证明可以在美国进行模具面设计通过 Surface Generation 以外的来源。该模具CMD-TP-RAPM-008-503已成功用于制作TP-RAPM-008-203短光纤接入面板。
“虽然工具和/或零件中的某种形式的温度控制有助于所有复合材料零件的成型,”Hahn 解释说,“实际上需要的是控制关键区域和时间的温度,这因零件和工艺而异。因此,了解形成给定零件实际所需的温度控制是关键。 PtFS 中的 180 个区域很有帮助,但也很昂贵,因为每个区域都需要工具中的加工通道。如果零件仅需要沿触发点几何形状的外部和内部区域或特定区域,则不同的解决方案可能更实惠。然而,这确实引发了关于开发复合材料零件制造单元的最佳方法的争论,该单元可灵活处理多种类型的工艺和零件。”
波音和 DARPA 将在 2020 年完成 RAPM 计划并发布进一步结果时,继续为这场辩论添加信息。
树脂