用于生产未来航空结构的压缩 RTM
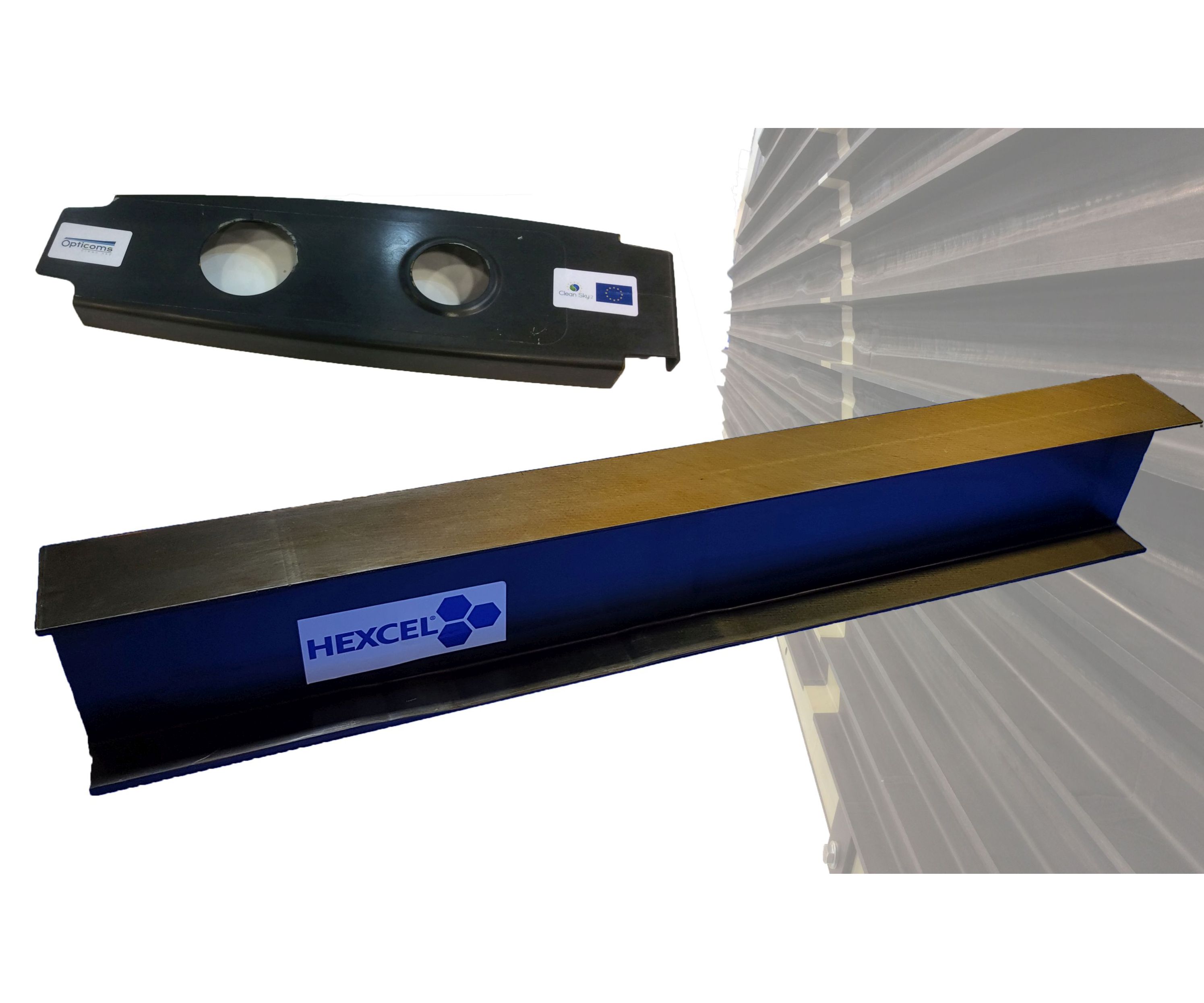
复合材料已在商用客机机身中占据一席之地,因为它们可实现高强度、轻质的结构,与金属相比,其维护成本更低。当前对下一代宽体和窄体飞机的预测显示复合材料机身的持续增长,但前提是材料和工艺能够满足低成本和高生产率的挑战性目标。尽管迄今为止,高压釜固化环氧树脂预浸料在碳纤维增强聚合物 (CFRP) 机身中占据主导地位,但下一代飞机的开发人员正在积极寻求具有集成自动化和在线检测功能的非高压釜 (OOA) 技术作为实现这一目标的关键推动因素。未来的工业 4.0 生产。
设备和自动化供应商 Techni-Modul Engineering(法国库德)及其美国子公司 Composite Alliance Corp.(美国德克萨斯州达拉斯)已与先进材料供应商 Hexcel(美国康涅狄格州斯坦福德)的英国和法国业务部门合作展示 CFRP 加强筋和纵梁的自动化 OOA 生产。这些部件采用 Hexcel 干碳纤维增强材料的自动预成型和压缩树脂传递模塑 (C-RTM) 工艺制成,该工艺可快速渗透 Hexcel HexFlow RTM6 液体环氧树脂,以生产纤维体积为 60% 且空隙率低于 1% 的部件在 2.5 到 3.0 小时的周期内,可以按比例生产多个零件以进行高速生产。
干式加固开发
“我们认为液态复合材料成型 (LCM) 可以解决降低成本、做好准备并提供主要结构性能的三方面挑战,”Rémy Pagnac 解释说, 赫氏液态复合成型技术支持工程师。 Hexcel 开发了 HiMax 非卷曲织物 (NCF) 和 HiTape 单向 (UD) 碳纤维材料,以满足使用 LCM 工艺时的主要结构性能需求。 HiMax 使大型扁平结构(例如机翼蒙皮)能够快速铺设,而 HiTape 能够以最少的浪费为大型复杂结构量身定制铺设。 “我们可以获得与最新一代 UD 预浸料相当的性能,”Pagnac 补充道。
Hexcel 致力于通过 HiMax NCF 减少体积并提高悬垂性,包括细的 20 dTex 针迹纱线。 HiMax 材料是由 Hexcel 于 2016 年收购的位于英国莱斯特的前 Formax 工厂生产的。 该工厂生产的轻质、展开拖曳多轴产品在为赛车游艇、超级跑车和方程式等要求苛刻的应用提供解决方案方面有着悠久的历史1辆赛车。现在,NCF 材料已用于空中客车防务与航天公司(Airbus DS,西班牙加的斯)和 Danobat(西班牙埃尔戈伊巴尔)完成的机翼演示项目,使用后者的自动干材料放置 (ADMP) 技术——一种自动纤维放置(AFP) 用于 NCF(参见“证明大型飞机结构的干织物灌注的可行性”)——以及空中客车赞助的 ZAero 项目,用于零缺陷 CFRP 结构,例如纵梁加强翼蒙皮(参见“复合材料部件的零缺陷制造”) ”)。
通过 HiMax 和 HiTape,Hexcel 集成了薄层、低面积重量的热塑性长丝面纱,作为粘合剂,消除了以往用于预成型和液体成型干材料的粉末粘合剂的需要。对于 HiMax,该面纱夹在 NCF 层之间;对于 HiTape,面纱应用于碳纤维 unitape 的两侧。 “有了这个,您无需使用粉末粘合剂将 UD 层固定到位,”Pagnac 解释说。 “HiTape 是经过校准的,不是割缝胶带,因此没有绒毛,宽度变化更小,以改进 AFP 处理。热塑性薄膜还增加了最终层压板的韧性,我们已经证明我们可以使用下一代 AFP 机器实现高材料沉积率。”在 2015 年 5 月的 SAMPE 论文中,Hexcel 描述了使用 0.25 英寸宽的 HiTape 制造的单曲率预制件,并以 1 米/秒的铺层速度应用配备激光的科里奥利复合材料(法国奎文)AFP 机器。它还与 Electroimpact (Mukilteo, Wash., U.S.) AFP 设备合作,展示了全尺寸翼梁飞机结构的沉积速率高达 150 公斤/小时。
图。 1 压缩RTM
在 C-RTM 中,将干燥的瓶坯放入 RTM 模具中,但模具只是部分 关闭,在干燥的瓶坯和上模具表面之间留下间隙。然后施加真空,注入树脂,压力机关闭模具中的间隙,将液态树脂沿 z 方向向下推入预成型坯中,穿过整个零件。来源 |赫氏

为航空航天调整 C-RTM
C-RTM 首先与用于汽车复合材料的高压 RTM (HP-RTM) 一起推出。与传统 RTM 一样,C-RTM 需要将干燥的纤维预制件放入匹配的金属模具中,将液态树脂注入预制件中,然后使用驱动压力机加热和加压。然而,在 C-RTM 中,模具只是部分 关闭,在干燥的瓶坯和上模具表面之间留下间隙(图 1)。然后施加真空,注入精确剂量的混合树脂,压力机关闭模具中的间隙,迫使液态树脂沿 z 方向穿过整个零件向下进入预成型件。 “这比通过零件平面注入树脂要快得多,”Techni-Modul Engineering 工艺工程师 Thomas Chevallet 解释说。
Techni-Modul Engineering 作为 Clean Sky 2“优化复合结构”(OPTICOMS) 项目的合作伙伴,看到了将 C-RTM 应用于航空航天的机会。在工作包 B-1.2(“更实惠的复合结构”)中组织,OPTICOMS 旨在通过集成结构和自动化制造降低小型飞机(例如支线喷气客机)的生产成本,探索预浸料和液体树脂方法。 OPTICOMS 设计了一种复合机翼演示器,包括带有三个翼梁的上部机翼蒙皮,在一次性过程中作为集成结构生产。全尺寸机翼(图 2)是 AIRFRAME 创新技术演示器 (ITD) 的一部分,用于评估和完善从 2025 年开始生产的下一代飞机的技术准备水平 (TRL) 6 的技术。 Israel Aerospace Industries(以色列洛德)于 2016 年 7 月被选为 OPTICOMS 的协调人。该财团还包括小型飞机 OEM Piaggio Aerospace(意大利萨沃纳)、Techni-Modul Engineering 和 AFP 设备供应商 Coriolis Composites 和 Danobat。
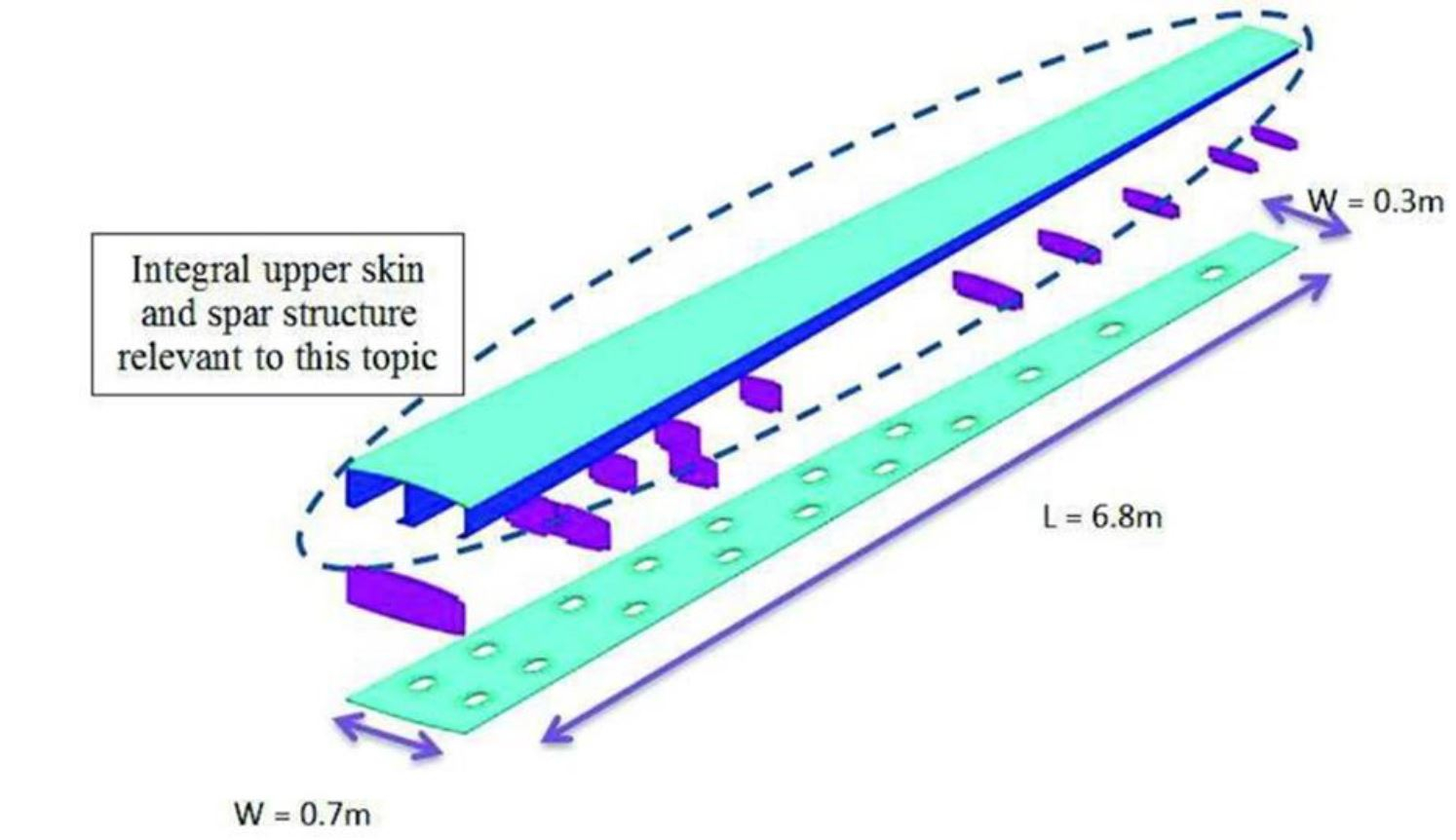
图。 2 Clean Sky 2 OPTICOMS 肋
Techni-Modul 是 Clean Sky 2“优化复合结构”(OPTICOMS) 项目的合作伙伴,该项目设计了一个复合机翼演示器,包括一个下机翼蒙皮、多个肋骨和一个带有三个翼梁的上机翼蒙皮。后者是在一次性工艺中作为集成结构生产的。该演示机将用于从 2025 年开始生产的下一代飞机的评估。来源 |晴空2
“C-RTM 在业内广为人知,”Chevallet 解释说,“但是对于 HP-RTM,仍然需要一台大型印刷机。我们的开发是采用 C-RTM 以使用较低压力进行快速注射,从而降低对高纤维体积、纤维排列和低空隙有非常严格要求的航空航天部件的生产成本。 OPTICOMS 项目中 0.7 米长 x 0.2 米宽的翼肋的注射时间从 40 分钟缩短到 5 分钟。在一个长 900 毫米、高 150 毫米的工字梁纵梁的单独测试程序中,注射时间从一小时缩短到不到五分钟。

Chevallet 补充说:“对于大型零件,例如全翼蒙皮或直升机旋翼桨叶,C-RTM 所提供的注射时间的减少会更大。”他指出,C-RTM 还允许注射高粘度树脂以及低压注射系统和低吨位压力机,从而降低成本。 “C-RTM 期间的模具压力仅为 6 bar,远低于 HP-RTM 中使用的压力,”Chevallet 解释说。 “该工艺获得了航空级质量的复合材料,同时适用于大型、薄型部件和较小且形状复杂的部件。”
自动预成型
虽然更快、更低成本的树脂注射和 OOA 成型是这种方法的关键部分,可用于生产更实惠的航空复合材料,但该工艺链仍然需要多个步骤来切割和铺设材料以及预成型。 “对我们来说,OPTICOMS 也与自动化有关,”Chevallet 说。 Techni-Modul Engineering 不仅为 OPTICOMS 项目提供了 C-RTM 注塑系统,还提供了一个取放机器人和一个热悬垂成型 (HDF) 机器,所有这些都集成到一个全自动生产单元中。
OPTICOMS 于 2016 年启动后不久,Techni-Modul Engineering 子公司 CAC 凭借其自动化 3D 预成型单元在 CAMX 2016(9 月 26 日至 29 日,美国加利福尼亚州阿纳海姆)上赢得了制造类别的 ACE 设备和工具创新奖。该单元能够用干纤维或预浸料生产 3D 预制件,使用真空吸盘抓取、放置和折叠切割层到加热的预制件模具上。 Techni-Modul Engineering 和 CAC 开发了软件来准备 2D 材料的切割层,以塑造成复杂且可开发的表面。该单元在OPTICOMS和工字梁测试项目中得到进一步开发。
步骤 1
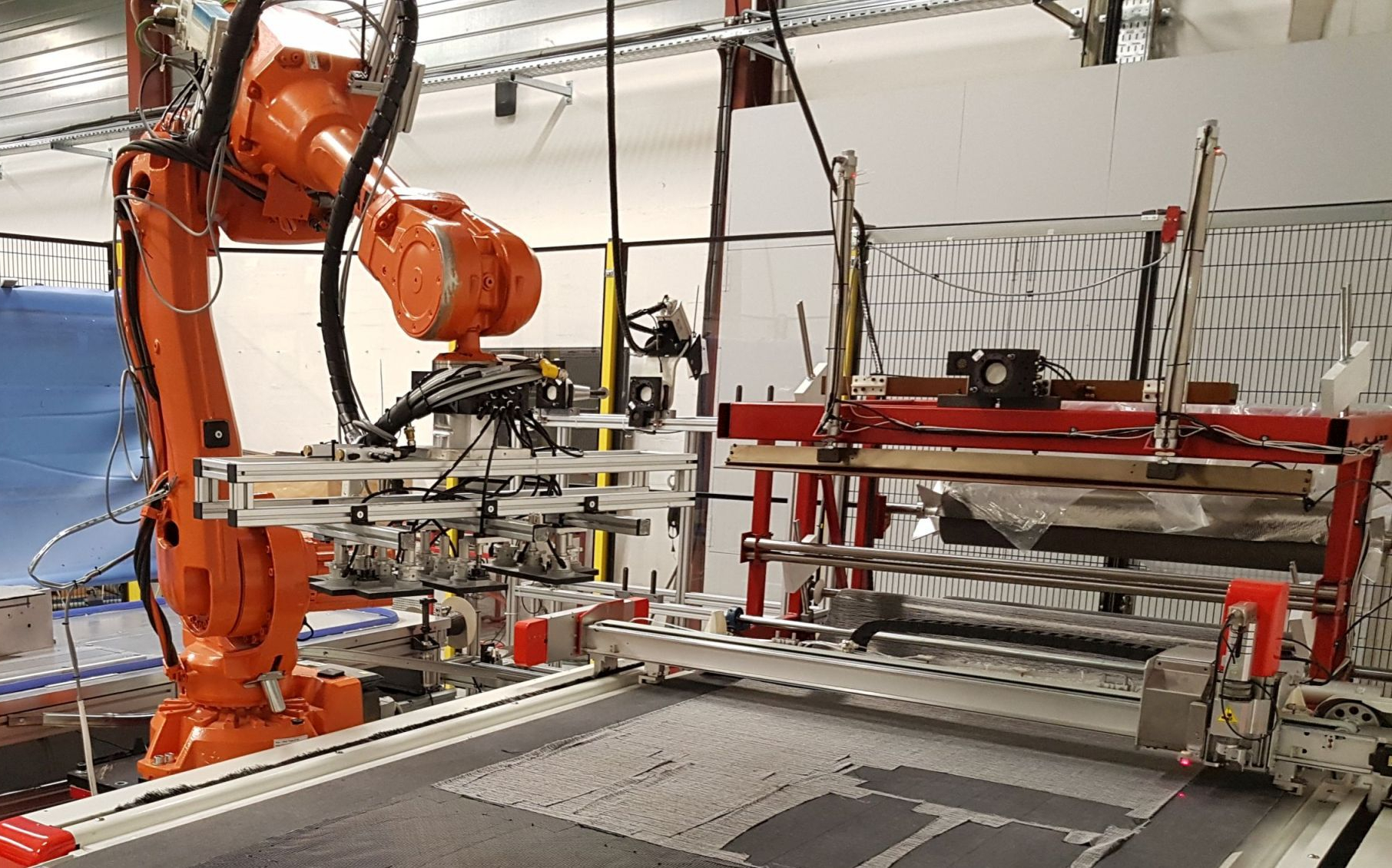
来源,所有步骤图像 |技术模块工程
在 Techni-Modul Engineering 自动化单元中,一个拾放机器人从自动切割机上取下层片,并将它们应用到加热的预成型工具上。
步骤 2

预成型工具位于压实台上,带有铰接的可重复使用真空膜(蓝色,左侧),用于在铺层期间每 5-8 层完成一次加热减厚。
步骤 3
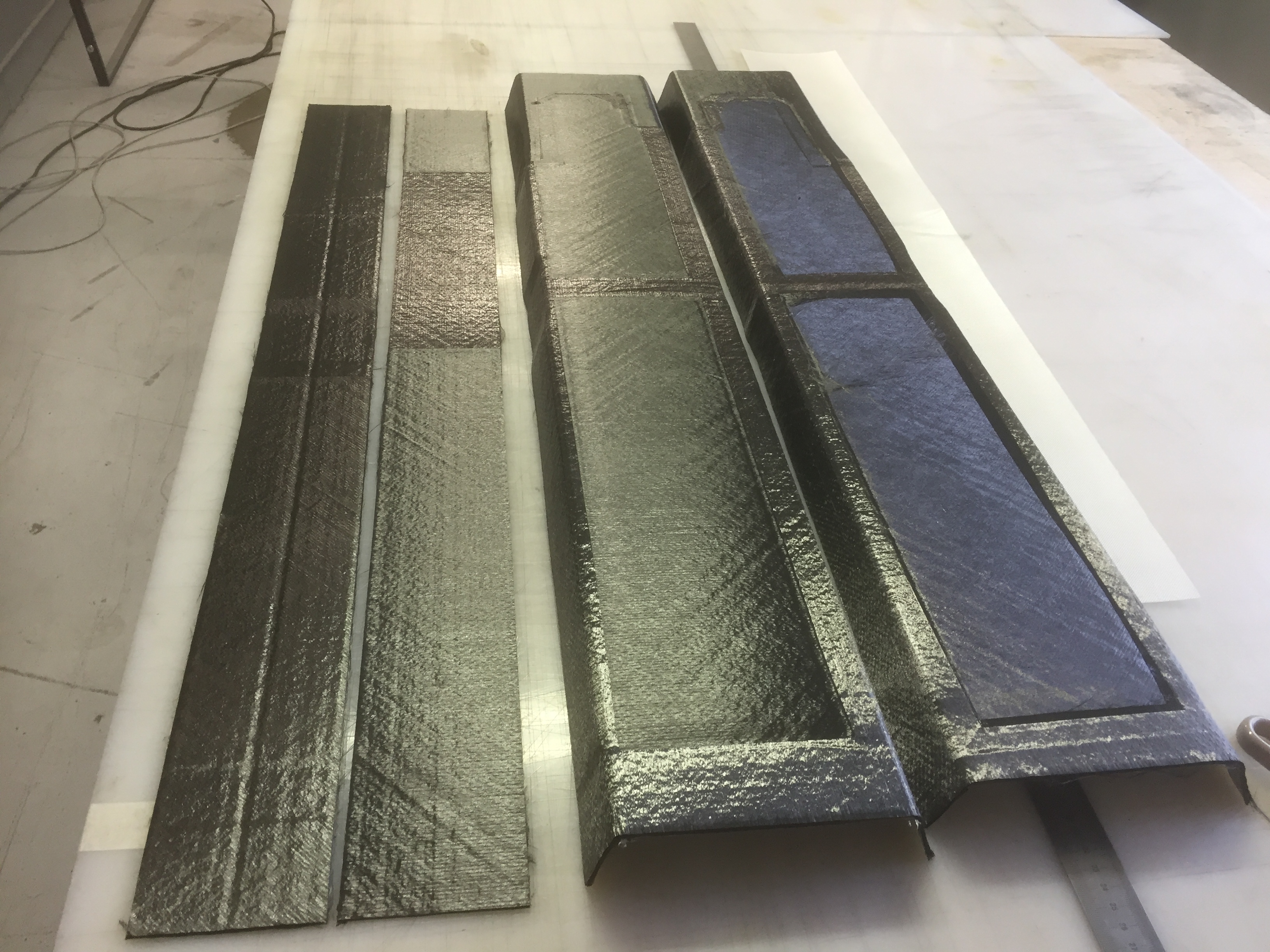
每个纵梁预成型周期生产一个 C 型梁预制件(两个包含工字梁腹板)和一个平翼缘预制件。此处显示了每个工字梁纵梁所需的两组。
步骤 4
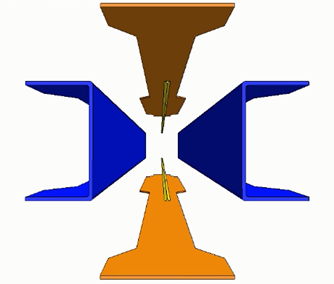
将四个工字梁预成型坯放入RTM模具中,抽真空,5分钟内完成树脂注射。
步骤 5
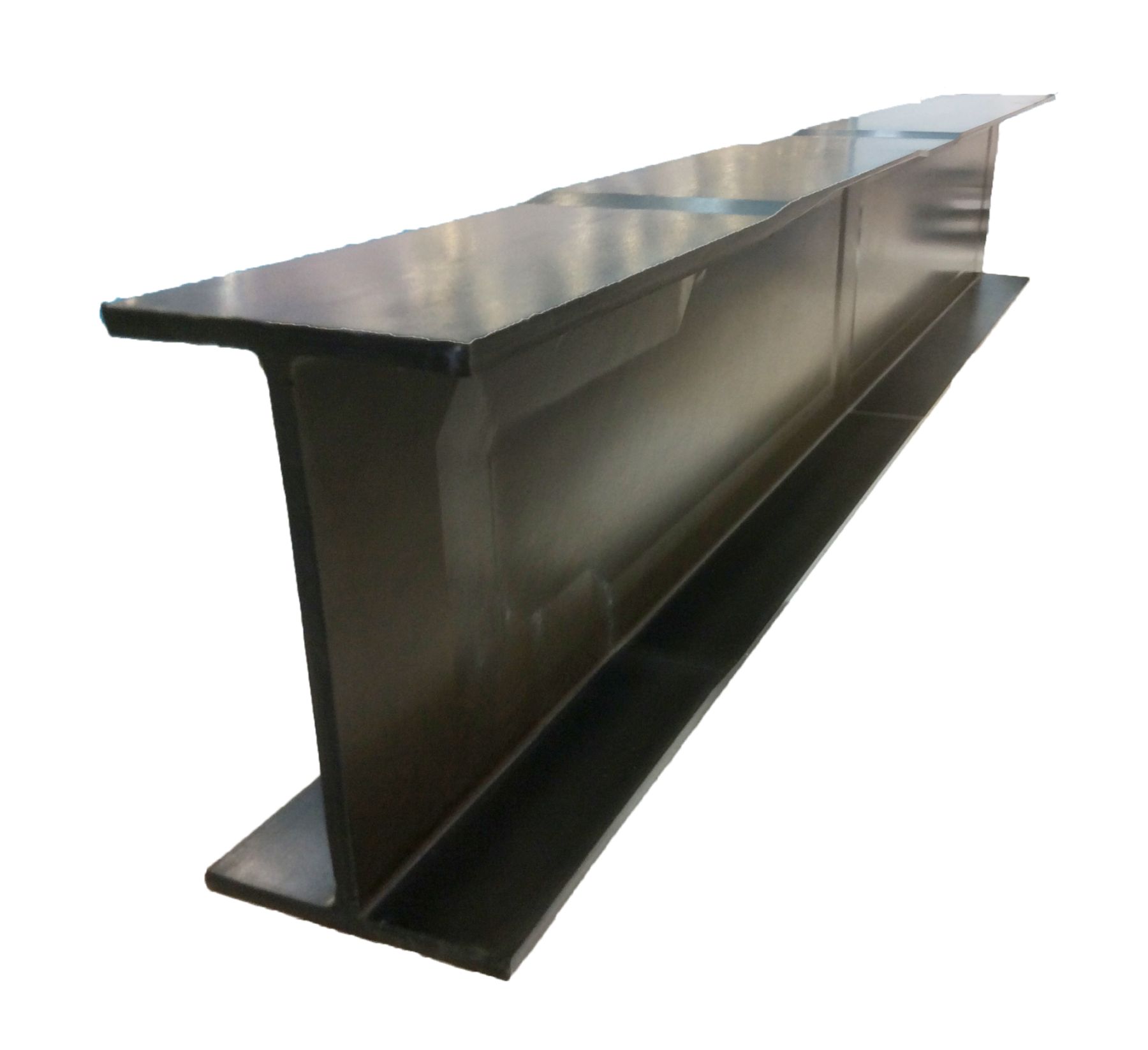
固化 90 分钟后,将纵梁脱模并修整树脂毛边,整个零件周期为 4.5 小时。

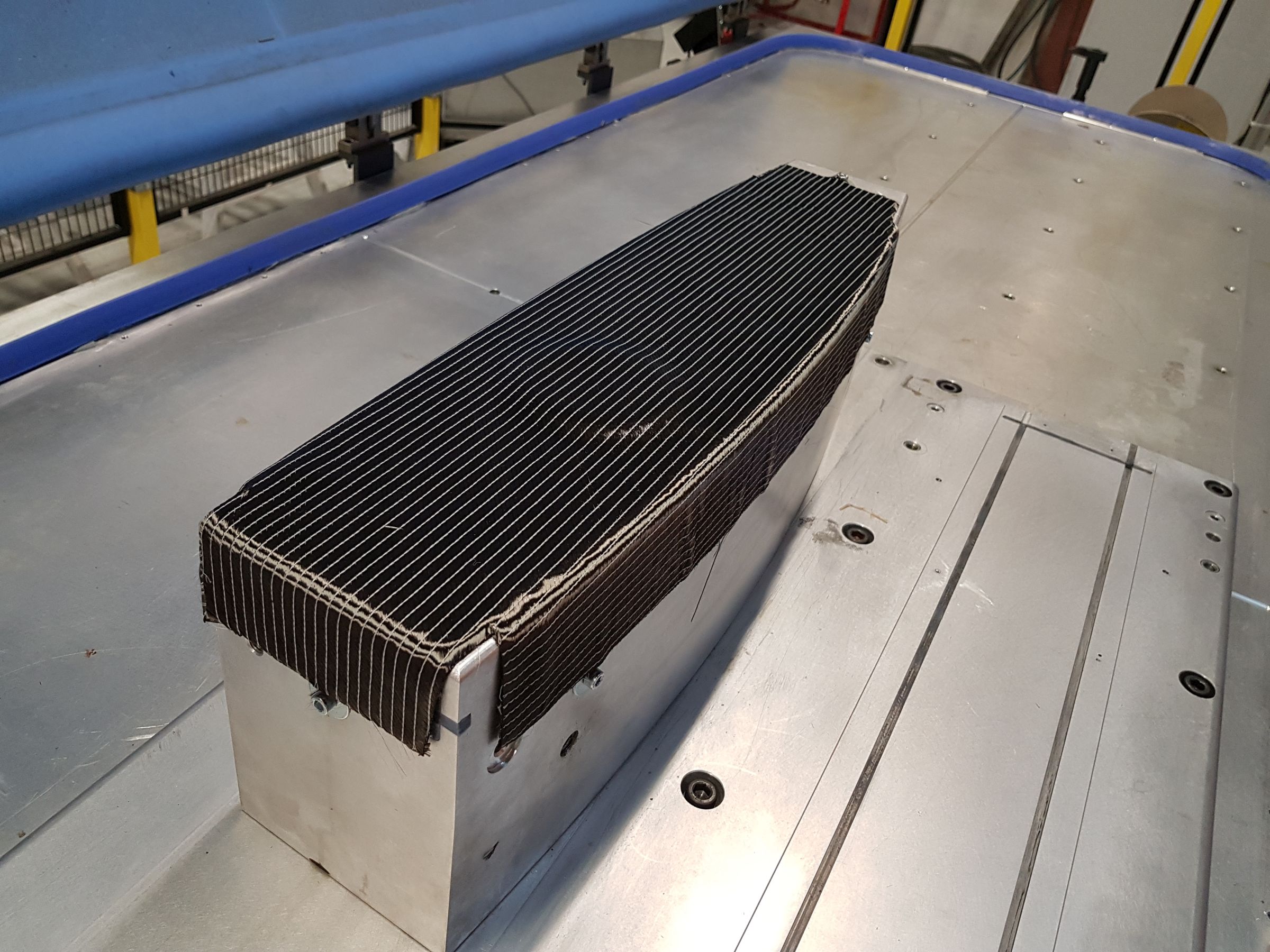
机器人将切割层放置在加热的瓶坯工具上。每 5-8 层,完成一次加热压实以压实瓶坯。

减瘤前贴蓝色离型膜。
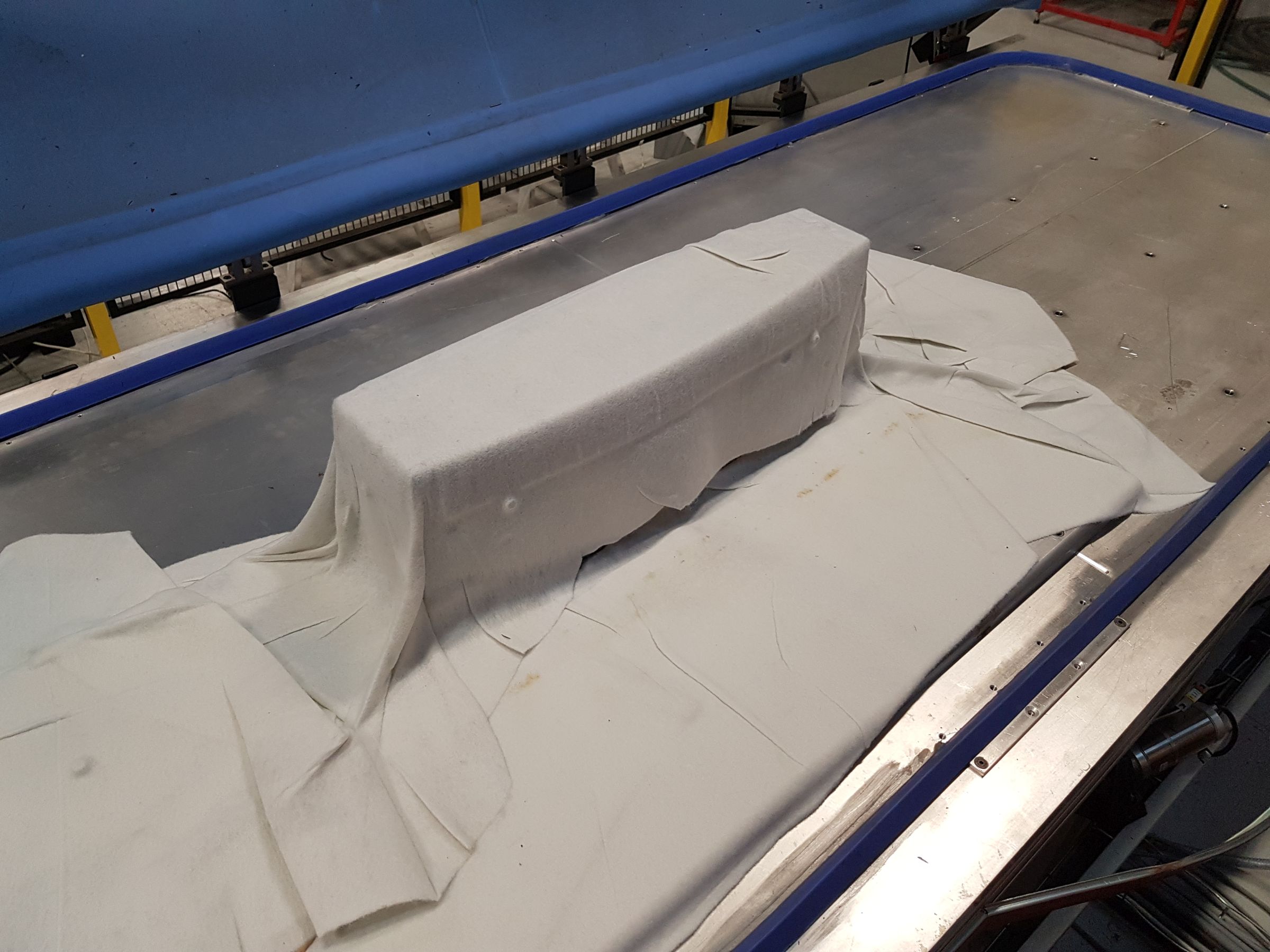
呼吸器用于从瓶坯中抽出空气。
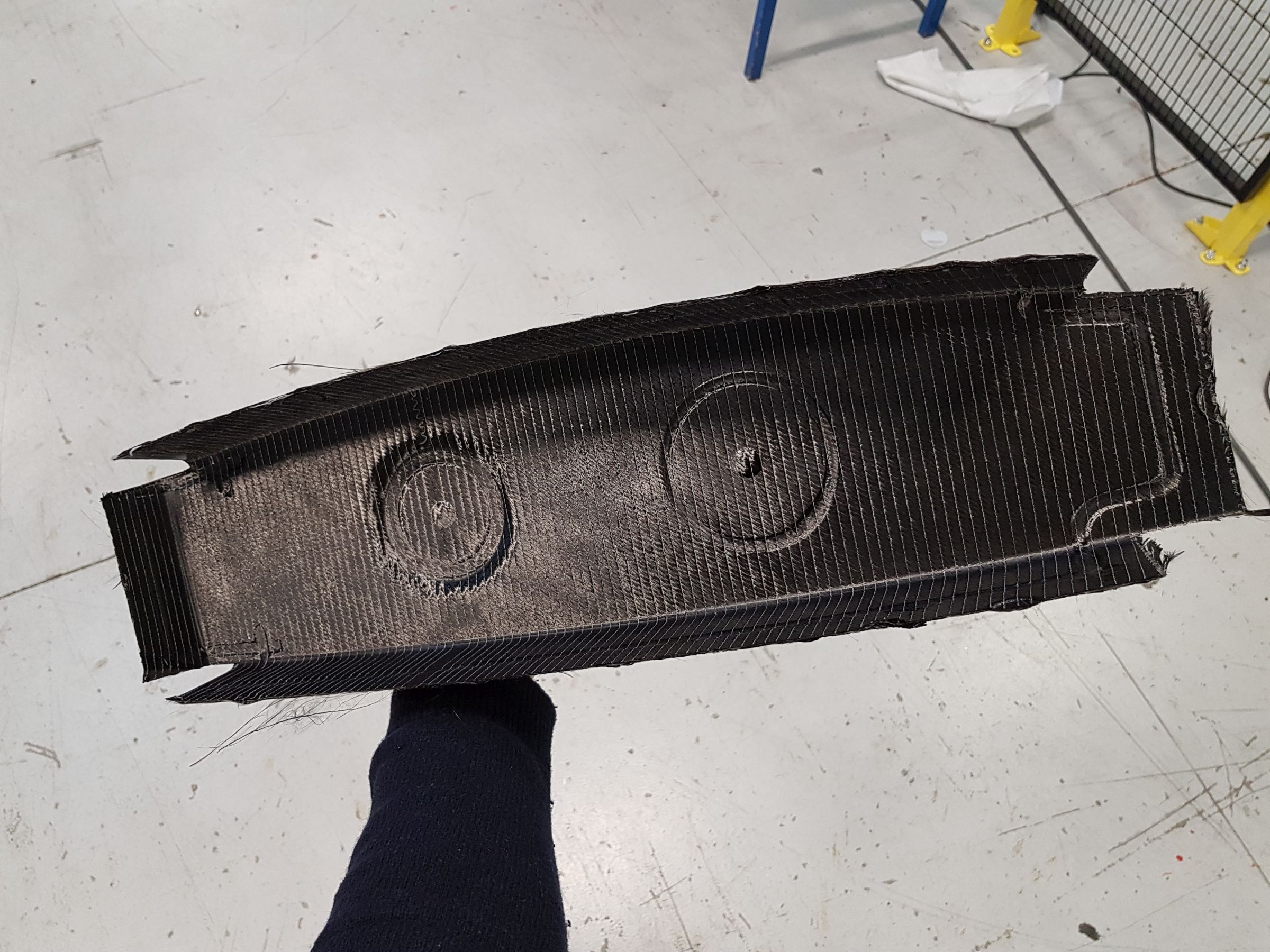
最终减体积后,预制件在工具上冷却并修整切口(下图)。
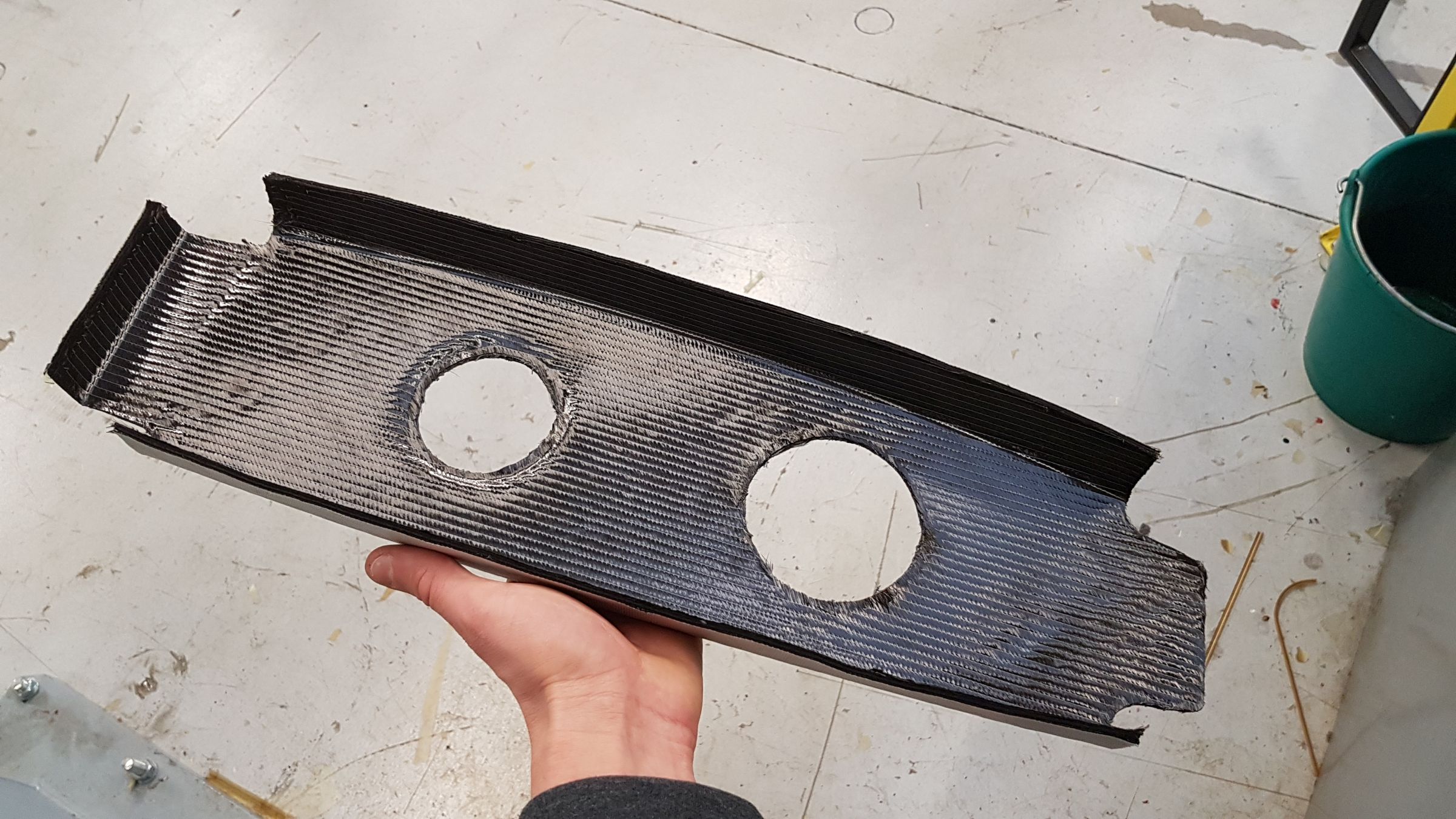
“我们使用机器人取放实现了经典的手动叠层自动化,”Chevallet 说。 “机器人从自动切割机上拾取层片并将其转移到位于压实台上的加热预成型工具 [步骤 1 和 6]。”应用剥离层(步骤 6 中的蓝色薄膜)、透气膜(步骤 6 中的白色材料)和铰接可重复使用的真空膜(步骤 2 和 6 中左侧的浅蓝色),然后抽真空和加热以预成型并去除空气中的空气纺织堆叠(热悬垂成型,HDF),同时熔化薄的热塑性面纱以创建压实的预制件。
“一次可以压实多少层取决于零件的材料和形状,”Chevallet 解释说。 “对于低曲率的零件,例如翼皮,您可以每 50 层压实一次。然而,OPTICOMS 肋具有 90 度角,而测试工字梁纵梁具有 T 形,因此在预成型过程中必须小心不要在层板中形成褶皱。”他补充说,这种复杂的形状可能需要每 5-8 层压实一次,但仍然可以成为大批量工业化过程的一部分:堆叠层,2 分钟 HDF 压实,重新打开并再次堆叠,然后重复压实循环,在转移到 RTM 模具之前对模具上的预成型坯进行最终冷却。
“我们的自动化单元可以以每层 15 秒的速度放置,”Chevallet 指出。 “OPTICOMS 肋条的上篮,总共不到 20 层,在 20 分钟内完成。”工字梁纵梁的上篮时间更长 - 45 分钟 由于其复杂的形状和层压堆叠,包括从 1.2 到 6 毫米的厚度变化。 “这仍然比手动流程快得多,并降低了错误风险,提高了可重复性和质量,同时降低了成本,”他补充道。
步骤 7
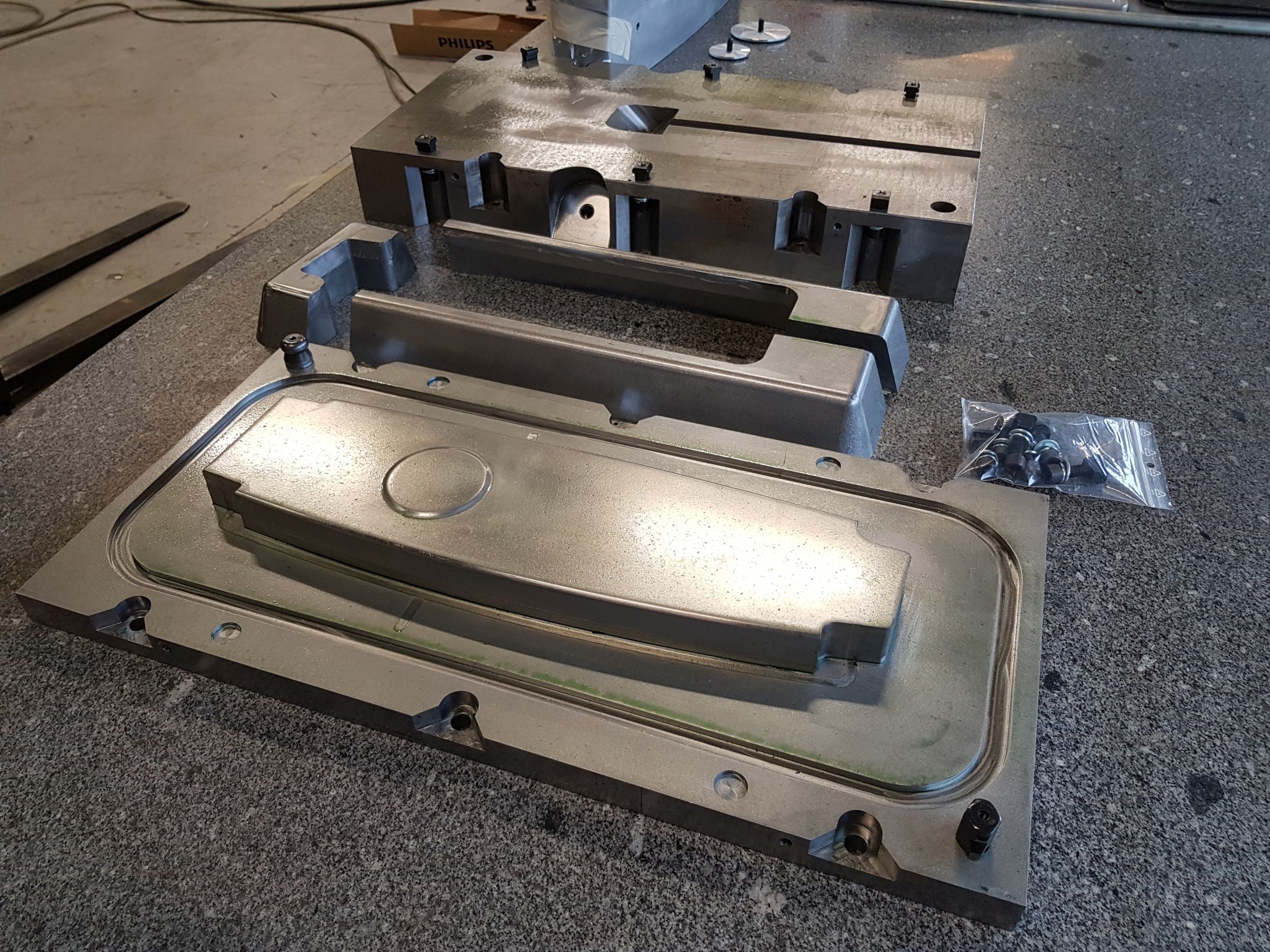
OPTICOMS肋的RTM工具由多个部分组成。
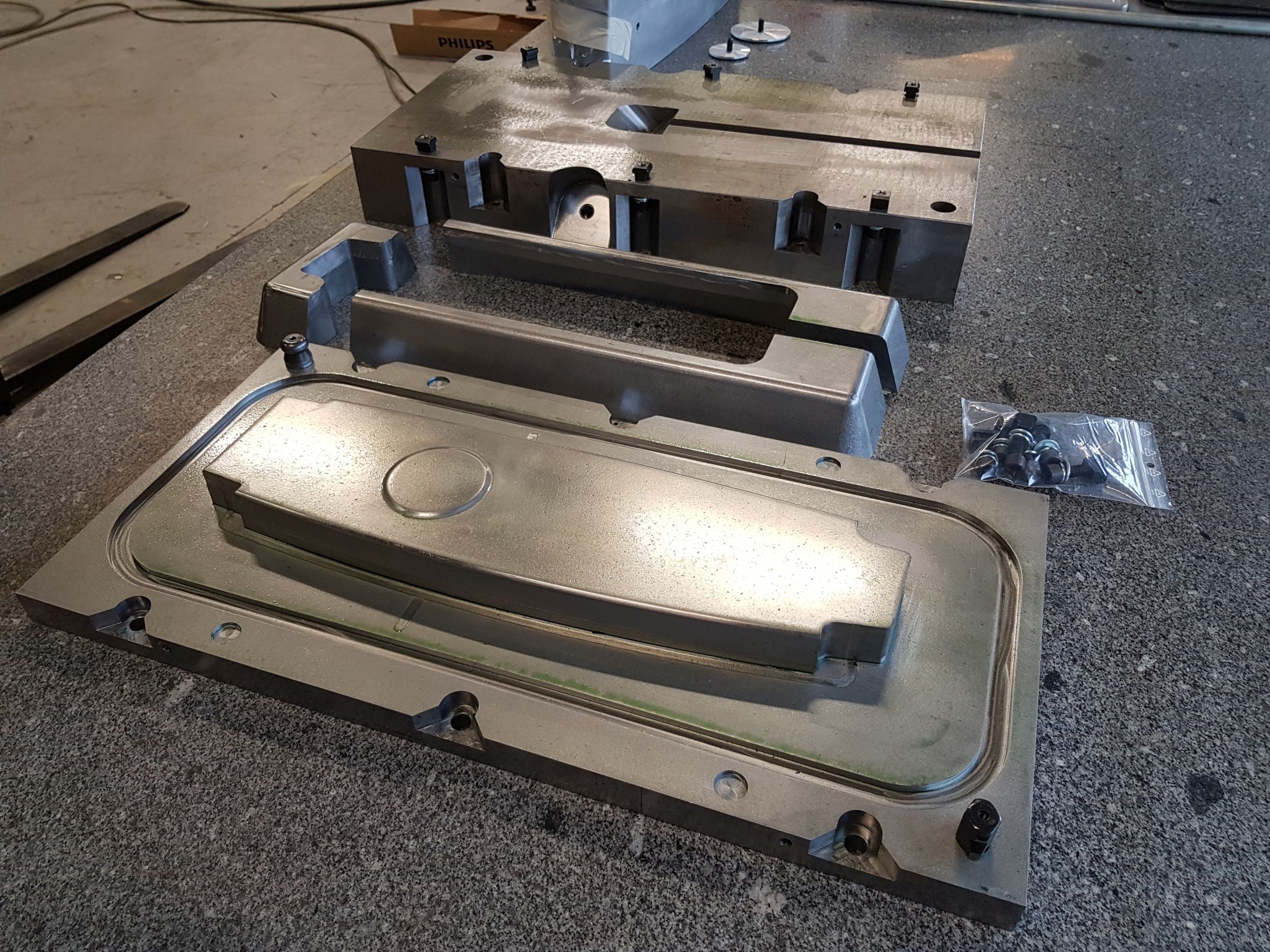
步骤 8
肋预制件被放入 RTM 工具中。
步骤 9
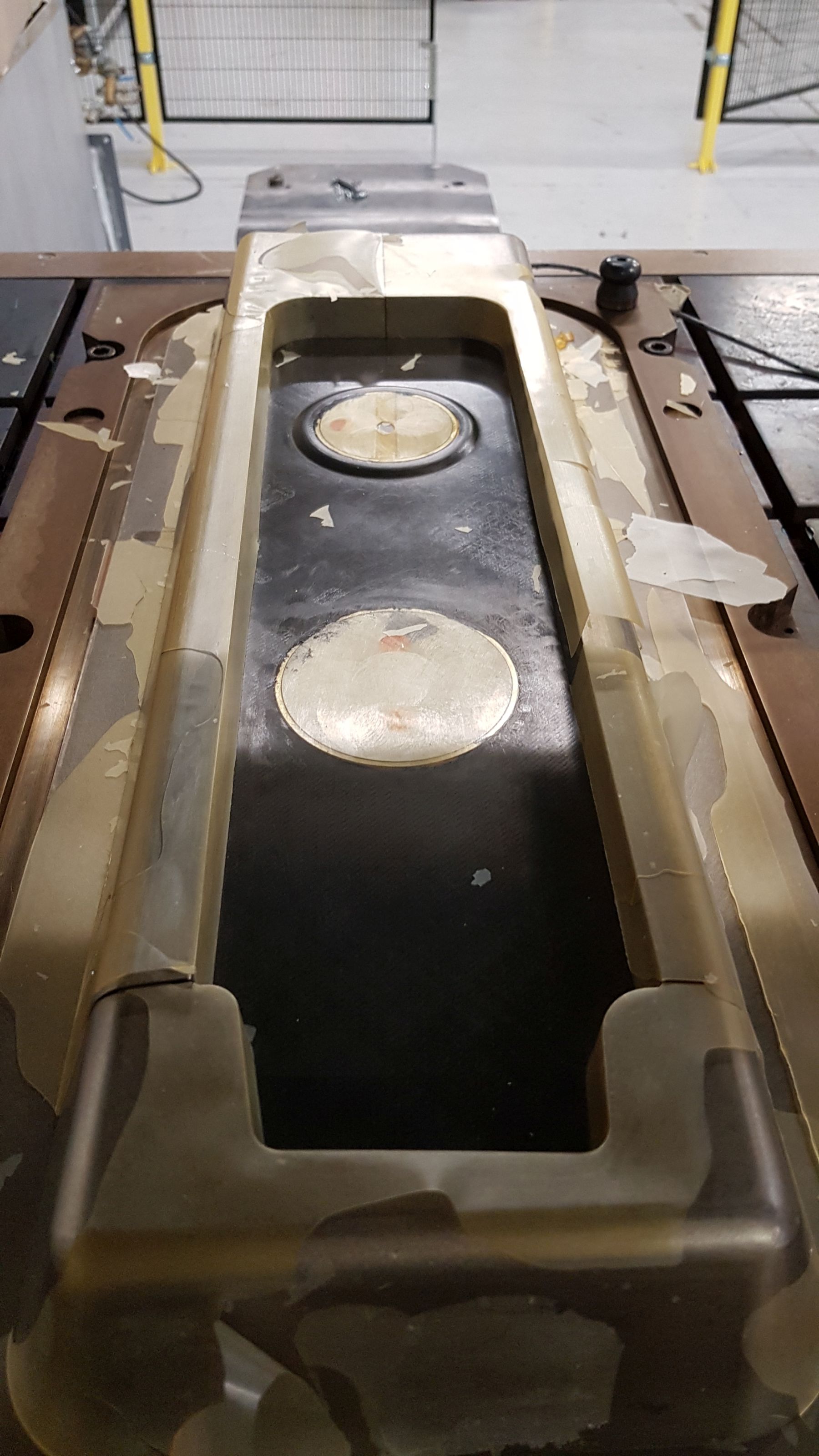
施加真空,注入树脂并渗入预制件,然后固化 90 分钟。在这里,压力机已经打开,露出固化的部分。
步骤 10
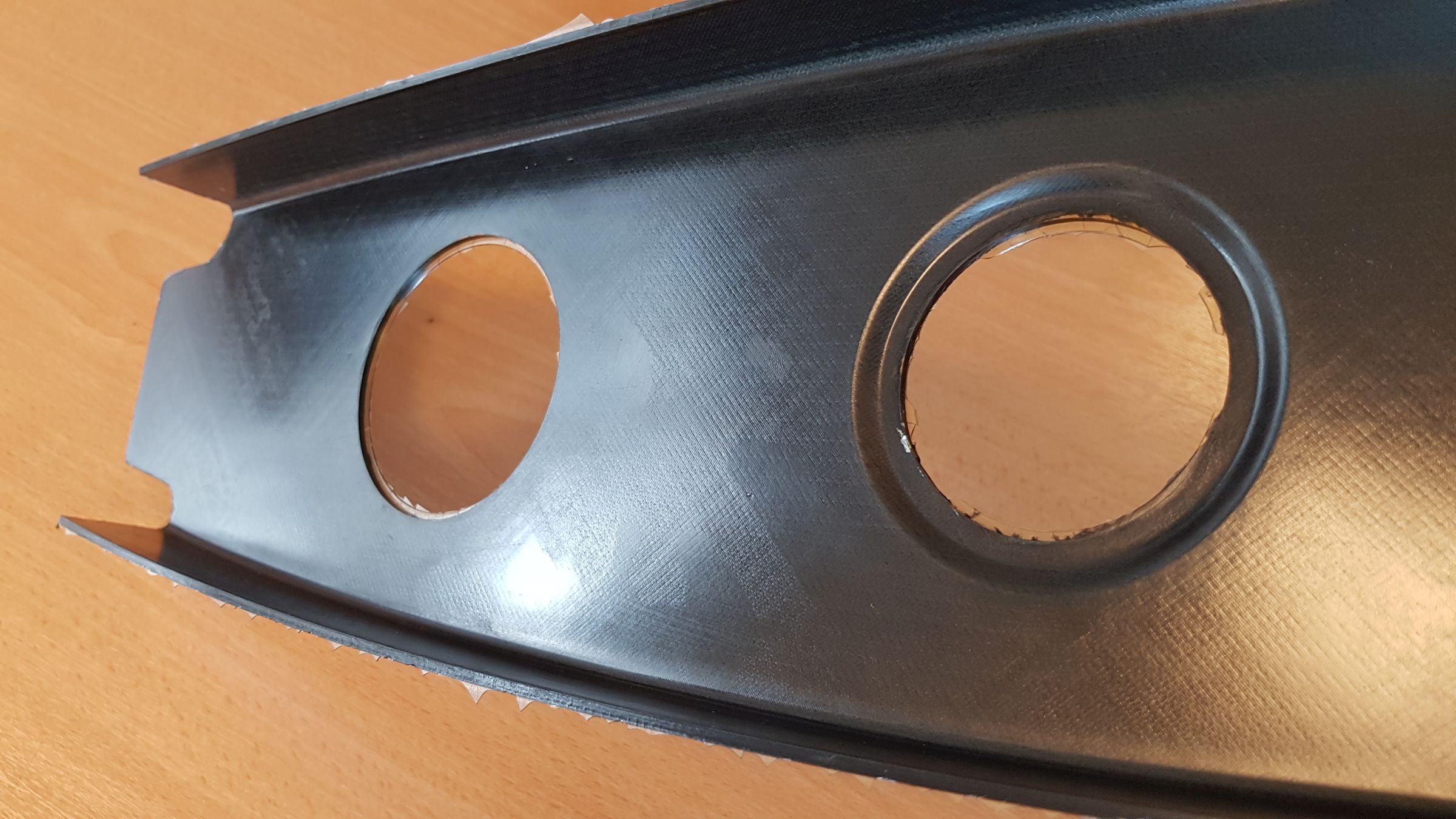
脱模完成后,将在 4 小时的完整零件周期内去除树脂毛边。
智能控制
Techni-Modul Engineering 自动化预成型单元的另一个关键特征是其集成控制系统。被称为 SMART CONTROL,其主干是一个摄像系统和多用途软件,可将加工过程中拍摄的图片与零件的 CAD 数据库进行比较,从而实现瓶坯形状识别、纤维取向控制、层定位以及缺陷和异物碎片 (FOD) 检测)。 SMART CONTROL 反馈会指示机器人如何以正确的顺序和时间拾取和放置层片,而且还会在检测到错误时提醒单元操作员。 Chevallet 解释说:“系统可以进行配置,以便操作员手动移除层片并重新启动系统以更换它,或者我们可以与客户合作创建一个自动化解决方案,用于去除缺陷层片和纠正错误。”
用于检测层边缘和轮廓的相同光学图像也用于控制纤维取向。 Chevallet 承认,如果零件非常大(例如,2 米长,而 200 x 200 毫米长),“您可能需要一台相机 [从] 更高的垂直位置拍摄照片以检测层片的边缘,然后靠近检查纤维取向的部分。您可以为每种类型的零件校准此序列。为了检测皱纹和 FOD,有一个包含不同缺陷的数据库,您可以添加到其中,因此深度学习算法会随着时间的推移而改进。我们的想法是拥有一个自适应系统。”
周期时间和未来生产
OPTICOMS 肋的预制件使用 HiMax 制成,工字梁纵梁使用 HiTape。两者的树脂系统都是 Hexcel 的 HexFlow RTM6 单组分 (1K) 液态环氧树脂,在 180°C 下的固化周期为 90 到 120 分钟。这种固化是 OPTICOMS 肋和测试工字梁纵梁零件周期中最长的一步,如表 1 所示。
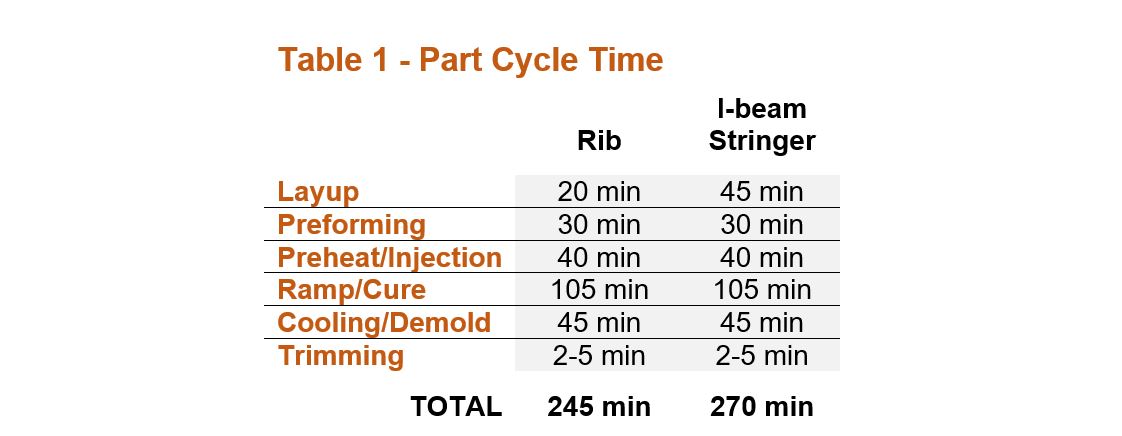
来源 |技术模块工程
迄今为止,这是唯一一种符合航空航天结构 RTM 要求的环氧树脂。然而,人们对在注射头混合的合格双组分系统越来越感兴趣,这些系统提供了更高的固化周期灵活性,并且无需冷藏运输和储存以防止预混 RTM6 过早反应。
空中客车直升机(德国多瑙沃斯)与 Alpex Technologies(奥地利米尔斯)在 SPARTA 项目中合作,展示了使用双组分版本的 HexFlow RTM6 的 HP-RTM 工艺,以在 180°C 下实现 A350 门的 30 分钟固化框架,这是一个形状复杂的主要结构,高 2 米,宽 200-250 毫米,厚 8-10 毫米(参见“HP-RTM 用于批量生产具有成本效益的 CFRP 航空结构”)。空中客车公司还展示了由其复合材料技术中心(CTC,Stade,德国)子公司使用 HP-RTM 制造的 1.5 米 x 0.5 米 CFRP 加强筋,实现了 20 分钟成型周期的部件具有 60% 的纤维体积和小于 2 % 空隙。在过去的一年中,CTC 与多家一级供应商合作,将 A320 的手糊预浸料零件过渡到 HP-RTM。然而,2K 树脂系统必须符合航空结构生产的要求,CTC 担心能否在原位持续确保 2K 树脂系统的混合质量。 Alpex 正在使用 Netzsch(德国塞尔布)和 Kistler(瑞士温特图尔)的模内传感器来帮助实现这一目标,并且正在开发其他解决方案(参见“用于增加复合材料航空结构生产的两部分环氧树脂”)。
即使没有 2K 系统,也有可能实现更高的生产量。 SPARTA 项目中的门框在 180°C 下初始固化 30 分钟后被移除,并在真空下从压力机中进行后固化以消除热应力并确保机械性能。根据 Alpex 的研发主管 Bernhard Rittenschober 的说法,这需要额外的工具集,但只需要一个压力机和注塑单元。他解释说,额外的工具成本被较低的工艺和冲压成本所抵消,并且可以快速收回,即使是每年 500-1,000 个零件的低产量。
“与传统的航空航天 RTM 工艺相比,这些演示者的主要成就是能够通过短树脂注射制造初级航空结构,传统航空航天 RTM 工艺在传统航空航天 RTM 工艺中使用 UD 碳纤维增强材料将树脂渗透到如此大的部件中是一个困难而漫长的过程,”Pagnac 说. “通过这种智能自动化预成型和 C-RTM 处理,我们才刚刚开始实现目标,”Chevallet 补充道。 “它有可能实现更具成本效益、可持续生产的加强筋集成蒙皮结构,为未来的飞机设想。”
树脂