医疗制造变得更智能
数字化和自动化制造正在医疗制造领域取得长足进步,最近在 COVID-19 大流行期间投入生产线的系统就是明证。
鉴于监管医疗设备制造的严格标准,以数据为中心的工业 4.0 环境是为合同制造商量身定制的,他们既要保持规范,又要应对熟练操作员的严重缺乏。
与以往一样,材料越来越复杂,零件越来越小,几何形状越来越复杂,公差要求也越来越严格。
从广义上讲,医疗保健趋势——人口老龄化、在昂贵的医院环境之外进行更多远程诊断和治疗、更个性化的治疗——正在推动医疗设备的发展。由于持续存在的大流行不确定性和由此导致的供应链受到重创,提高对供应商和供应商运作的可见性是第一要务。
随着医疗保健的数字化,需要保护所有正在收集的数据。为此,明尼苏达大学于 9 月 9 日宣布了新的医疗设备网络安全中心等举措。健康行业的五家重量级人物已在新中心合作:波士顿科学、史密斯医疗、Optum、美敦力和雅培实验室。他们的目标是消除医疗设备中可能用于伤害患者或破坏医疗保健设施的软件漏洞。
医疗保健的高科技未来还意味着更多的机器人诊断和程序,因此需要更多专用于这些系统的医疗工具和零件。例如,位于马萨诸塞州 Hingham 的 XACT Robotics 是 XACT ACE 机器人系统的开发商,于 8 月 30 日宣布,它成功地完成了美国首个评估 XACT ACE 用于经皮肺手术的研究的患者登记。这包括活检以确认癌症的存在。免提机器人系统可以更早、更小地检测癌症。
与此同时,iData Research 预计,到 2025 年,每年将进行 300 万次机器人手术。达芬奇手术系统等设备上的机械臂将需要医生控制的大量微型仪器来执行这些微创手术。机器人手术切口更小,失血少,疤痕少,住院时间更短,恢复更快。
数据驱动的人工智能也将在改善患者预后方面脱颖而出。这条路径的一个明确指标是 Stryker 收购了加利福尼亚州门洛帕克的 Gauss Surgical。Gauss 开发了 Triton,这是一个人工智能平台,用于监测手术期间的失血量。
增材制造还将继续扩大其在生产针对患者的植入物、工具和手术培训模型方面的关键作用。例如,意大利的 Tsunami Medical 使用 GE Additive 激光和电子束 3D 打印系统生产一系列高度复杂的脊柱植入物,令业界赞叹不已。
小零件,分类挑战
随着医疗器械材料的发展和零件的小型化,位于新泽西州艾伦代尔的 Marubeni Citizen-Cincom (MCC) 的 L 系列瑞士式机器正在响应号召。
“Medical 拥有您以前从未听说过的材料,”总裁兼首席运营官 Brian Such 开玩笑说。坚韧的材料可用于简单的零件或更复杂的组件,需要使用许多工具来创建不同的功能。
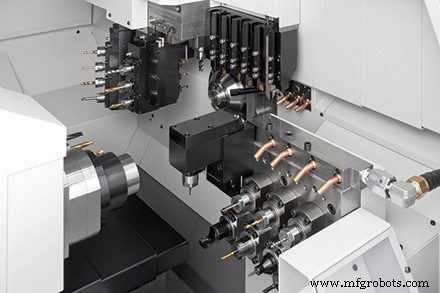
“我们的 L 系列机器是带副主轴的组合机器”,它们在医疗生产中的显着优势在于它们是模块化的,Such 解释说。 “有许多工具随时可用,我们只需滑出一个,然后将三个放在同一个地方。”
为了处理当前医疗钻机和铣床的典型较小直径,MCC 提供高达 4 倍加速度的加速器。 “根据型号,我们的带电工具可以达到高达 6,000 或 9,000 rpm 的速度,但我们可以在不同的刀架中滑动,现在我们达到了 36,000 rpm。如果这还不够,我们可以改装我们的电主轴,最高转速可达 80,000 转。”
例如,Such 指出,客户可能正在钻一个千分之八的孔,“所以你需要一些速度来实现这一点——或者使用 16 千分之二的立铣刀,甚至可能是一个千分之八的立铣刀在某个地方倾斜一个角落.使用我们的 80,000 rpm 电主轴,我们可以滑入这些口袋。同样的工具可以用作面工具、十字工具或后向工具,因此它非常模块化。” MCC 已与高速主轴销售商 NSK 合作打造这些专有主轴。
大约两年前,MCC 通过推出其 L20 机床的 ATC(自动换刀器)版本扩展了机床 B 轴的功能。 “现在我们在 B 轴上有 13 个工具的能力,”Such 说,而通常 B 轴只有四个工具——鉴于当今零件的紧密角度,这“对于医疗市场来说是非常热门的东西”。主页>
2016 年左右推出的另一项 MCC 创新是低频振动 (LFV) 切割。在这个过程中,机床“摆动 Z 轴或 X 轴的切削路径,以非常高的速度进出移动,以便在加工时进行少量空气切割并打破切屑,” 这样说。 “医疗领域喜欢 LFV 技术,大多数第一次使用它的客户都会说,‘如果没有它,我再也不会买机器了。’” 有了 LFV,“您将 100% 打破筹码;中间没有。一旦你让进程运行,它是有保证的。您仍然必须了解您的刀具,刀具仍然可能出现故障,但芯片缠绕问题会消失。”
MCC 的客户范围从拥有 300 或 400 台机器的 OEM 到拥有 10 台机器的小型制造商。这些客户“正在制造所有不同的零件”,从常见的接骨螺钉和脊柱手术笼到各种手术工具,如髋关节和膝关节手术所需的骨铰刀。有大约 4 毫米直径的微小骨螺钉,带有用于缝合的孔。 “有九种不同的工具来切割不同的形状,”Such 说。 “这个小小的接骨螺钉有很多特点——它不仅仅是一个带头的螺钉。”
制作完这些微小的零件后,分类就成了主要问题,这样继续下去。 MCC 为任务量身定制自动化设备。
“这些零件非常小,以至于当它们落入桶中时,那里可能有 300 个。如果您要尝试选择最后一个来测量它,那是哪一个?我们可以有一个设备,它有不同的托盘用于计数,”Such 说。
客户可以将 100 个零件放入一个托盘,然后当托盘移动时,将一个放入下一个托盘,将 100 个放入下一个托盘,一个放入下一个托盘,以此类推。如果有 10 个托盘,它可以在无人看管的情况下运行 8 小时或过夜。通过定期测量零件,客户可以通过收集托盘区分以前的零件是好是坏。
六轴优势
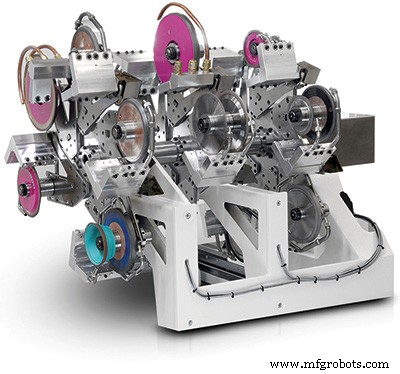
总裁 Eric Schwarzenbach 断言,对位于伊利诺伊州 Mundelein 的 Rollomatic USA Inc. 的切削工具磨床的稳定需求是医疗设备制造弹性的明确指标。
在 OEM 和合同制造商要求制造的众多器械中,Rollomatic 机器包括各种骨科切割工具,如锉刀、骨钻、颅骨穿孔器和关节镜毛刺。在整个大流行期间,尽管骨科或择期手术被推迟,“我们的客户仍像以前一样投资——不多也不少”。 “周围有足够的业务来维持这些公司的运转,并满足他们对再投资的需求。”
他指出,在过去的几年里,用于机器人手术的各种器械的需求正在增长。但这些设备带来了特殊的挑战。
“外科医生用手机钻入骨头的钻头与机器人发出的不同,”他解释说。 “机器人使用比外科医生更长的钻头。制作长钻的性质比短钻更难。首先,手术工具毛坯在瑞士型车床上以软状态加工,然后硬化。这些过程固有地导致这些毛坯翘曲,并且它们越长,它们的弯曲程度就越大。当它们弯曲时,我们无法可靠地装载、研磨和卸载。当我们教客户我们的机器和设置时,我们必须非常小心地深入教授他们,并确保他们了解规避弯曲毛坯的功能。弯曲的毛坯通常由制造商拉直,但即便如此,它们也绝不是完美的——尽管它们不一定是完美的。这台机器能够处理很小的失真。”
该行业变得越机器人化,“就必须越关注钻探点。虽然外科医生总是可以钻入骨头,因为他可以看,看,调整他的手和压力,所以这个点不会走开,但机器人不会。因此,必须将这些点设计为更加以自我为中心。我们帮助医疗设备制造商教他们什么是自定心点。”
Schwarzenbach 还注意到用于骨科刀具的 17-4 不锈钢有更多变体。 “材料变得更软,硬度更低,这对我们来说是一个挑战,要找到合适的砂轮来研磨它们。如您所知,材料越软,就越难研磨。”为了满足这一需求,Rollomatic 与瑞士和美国的车轮制造商合作,采购适用于较软材料的车轮。
“材料越软,它抛出的毛刺就越多,”Schwarzenbach 解释说,“因此去除毛刺是一个问题。我们的客户一般在研磨后使用尼龙刷去除毛刺,尤其是较软的材料。但是没有一个轮子或过程是完美的;总会有一点松动的毛刺需要通过某种方法去除。我们使用尼龙或有时带有陶瓷或研磨剂的浸渍刷来去除这些毛刺。”
他继续说,医疗工具的快速断开手柄是另一个增长领域。这些工具可以由外科医生卡入手机或固定在机械臂上。这种握法“变得比我们所见过的要复杂得多。我们对他们中的大多数人使用削皮机。”
Schwarzenbach 说,Rollomatic 的六轴功能是医疗制造商的游戏规则改变者,他们需要更大的编程灵活性和更轻松的车轮设置。
“你不需要使用复杂的轮子;你可以使用更简单形状的轮子,尤其是在钻孔点上,”他说。 “你可以比在五轴机器上更容易地制作钻孔点。并且不要忘记:现在钻孔点正变得低至 50 到 60 度(含)。它们非常陡峭,与以 120 度或 130 度钻入金属的硬质合金钻头不同。我们的六轴机床确实比设置五轴机床更容易磨削这些钻孔点。”
而且,Rollomatic 的快速换轮装置提供了更多优势,他补充道。 “我们一直在销售更多的换轮机。基本的车轮更换器有六个工位,因此您可以放入六个车轮组以增加灵活性,这适用于较短的批次。更短的批次需要更多的灵活性和频繁的转换。换轮机非常适合这一点。”虽然 Rollomatic 销售给医疗行业的机器中约有 80% 保留了前后装有一对轮子的标准主轴,但一些制造商“开始接受我们的新技术”。
力测试的作用
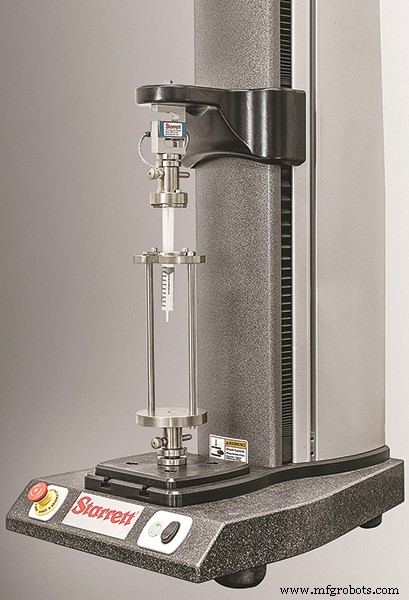
从制造准备到零件制成后,力测试设备及其集成软件执行医疗产品的重要功能——通常以患者舒适为目标。
例如,可以测试针的轮廓和涂层以了解它们进入皮肤的难易程度,而可以评估粘合剂以了解它们与皮肤的粘附程度或去除的难易程度。
The L.S. 的技术支持工程师 Jacob Morales 解释说,在制造之前,“您可以构建测试以确保您的设备在制造中使用之前以应有的方式运行。”马萨诸塞州阿索尔市的 Starrett Co. 对于绷带,“您可以在将粘合剂用于生产线之前对其进行测试”,批次范围从 100 个样本到 10,000 个样本不等。 “后处理,您可以再次运行这些测试以确保一致性。”
当按照 ASTM 和 ISO 标准进行制造以及制作对可追溯性至关重要的文档时,此类测试尤其重要,施泰力 (Starrett) 力和材料测试技术经理 Eric Perkins 补充道。 Starrett 软件可以进行力和材料性能测试,只需单击右侧图标,软件就可以进行适当的测试。力测量涵盖通过/不通过场景,包括测试峰值负载、平均负载、压缩测试等。注射器是需要施加单轴力的主要示例,可以使用样品物质进行测试,以确定受控注射速率的注射力。
虽然这些测试提供了样本信息,但它们并不总是返回特定于构成样本的材料的数据。材料测试更进一步,例如使用材料特性来测试伸长率和应力应变。
Morales 解释说,Starrett 软件可以集成到制造过程中。
“如果您有一个测试样本的力系统,您可以使用输入输出系统对其进行编程,以便测试持续运行。制造设备将样品移至机器并发送信号;机器通过运行测试做出响应,并根据测试结果提供信号输出。您的其他制造设备可以做出适当的响应。如果您得到的结果超出公差范围,该信号可以提醒操作员。”
这种灵活性意味着“您可以将力系统连接到 PLC 并使其与生产环境保持一致,因此您已经消除了潜在的人为数据输入错误,”珀金斯说。 “用户可以在每次排队时自动测试产品。”
从 Starrett 的基本 L1 force 软件到更先进的 L2、L2Plus 和 L3 选项,“我们让客户能够完全按照任何制造标准状态进行测试,”Perkins 说。由于 Starrett 软件跨平台兼容,因此添加光学和视觉系统可创建极其广泛的计量解决方案。
然而,这种级别的定制并不止于软件。 Starrett 一直在与制造商合作创建完全自动化的系统。
“我们正在使用机器人将零件插入我们的力测试系统,”珀金斯说。 “我们正在使用气动夹具来抓取零件。”借助与这种自动化水平相结合的不断运行的测试平台,“我们的系统将判断您的零件是好还是坏,然后机器人会执行所需的任何程序并将这些零件放入指定的箱子中。”
GE 的大局观
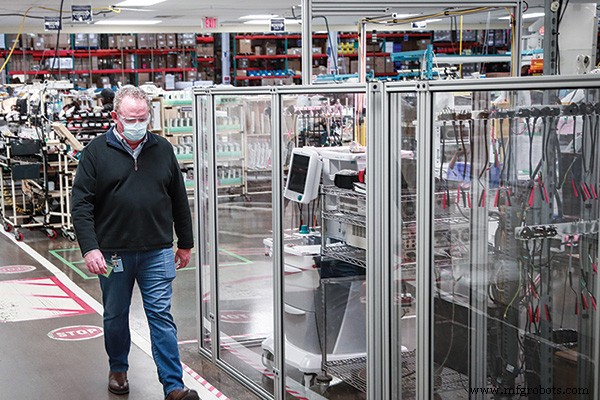
在大流行期间,改善医院工作流程和保持供应链弹性一直是 GE Healthcare 的首要任务。
“我们看到对更多自动化的要求越来越高——不仅仅是从典型的生产力角度来看,而且在利用自动化方面,我们可以在不同地点维持生产,”位于密尔沃基的 GE Healthcare 先进制造执行总工程师 Jimmie Beacham 说。 “这比必须培训新的或循环的劳动力更容易。在自动化有意义的地方,这不一定与劳动力有关,而是与劳动力的供应链安全有关。如果我必须将生产从一个地区转移到另一个地区,如果流程已经自动化,那会容易得多。”
他补充说,这种理念的一个主要部分是防错。 “我们会培训操作员并制定书面程序,”Beacham 解释说。 “现在我们正在考虑采用其他技术,将运营商需要做的事情数字化并与他们互动。假设您有扭矩站,您要在其中拧紧螺栓,然后是复杂的组件,然后是协作机器人。我们正在研究以数字方式连接所有这些的技术——这些技术与操作员同步工作,因此它可以与那个人进行交互,并且不需要操作员记住这一切。当我们在全球三个地区生产相同的产品时,这给了我们很大的灵活性。我们现在有一个控制过程。当操作员必须循环执行操作的几个复杂部分时,我们不依赖于记住纸质程序。”
这对于生产一系列智能诊断设备的 GE Healthcare 来说至关重要。增材制造是其中的重要组成部分,GE Healthcare 在这方面也改进了其流程。
“当我们刚开始的时候,我们大概 80% 到 90% 的时间都投入了研发,试图弄清楚添加剂的工作原理,如何开发材料和参数以满足我们的工程要求,”他说。 “现在我们的执行率约为 80%,我们正在将产品投入生产,另外 20% 的时间用于为新漏斗开发新材料。我们在蒙特雷有一个生产设施,墨西哥,我们有一个非常活跃的渠道。然后我们会在使用点运行其他一些附加应用程序。”
最终,尽管大流行证明具有挑战性,但 GE 医疗保健却经受住了这场风暴。
“我们面临的最大挑战是供应,让人们安全地进入工厂,”Beacham 说。 “在某些情况下,比如呼吸机,我们非常依赖自动化来满足前所未有的需求。我们请了很多人来做这项工作,但我们仍然必须找到创造性的方法来生产客户迫切需要的大量产品。我们了解到我们可以以不同的方式制造产品;这激发了更多的想法。”
自动化控制系统