推进多功能机身演示器 (MFFD)
燃料排放和能源消耗的减少,以及以每月至少 60 架的速度生产单通道商用飞机的能力,正在推动 Clean Sky 2 欧洲伙伴关系为下一代飞机在 2035 年及以后起飞的技术开发.轻质复合材料和更快、更环保的制造工艺正在使这些目标成为现实,尤其是多功能机身演示 (MFFD) 项目。
该项目的主要交付物是由空中客车公司(德国汉堡)与学术界和航空业合作伙伴牵头的,它是一个 8 米长的热塑性复合材料单通道商用飞机机身筒体演示器,将由以下公司生产2022. MFFD 是 Clean Sky 2 的大型客机 (LPA) 创新飞机演示平台 (IADP) 中正在生产的三个全尺寸机身部分之一。
MFFD 项目始于 2014 年,其目标包括:
- 实现每月 60-100 架飞机的生产率
- 将机身重量减轻 1,000 公斤
- 将经常性成本降低 20%。
为实现这些目标,正在完成数十个单独的项目和工作包,生产两个主要结构:上机身外壳和下机身外壳,它们将焊接在一起以形成最终的演示器。事实上,通过焊接进行无尘连接(无紧固件或孔)是该计划的主要组成部分之一。两半均由 Toray Advanced Composites(美国加利福尼亚州摩根山)的 Toray Cetex TC1225 低熔点聚芳醚酮 (PAEK) 碳纤维热塑性预浸料制成。根据 Dr.-Ing。德国航空航天中心(DLR;德国奥格斯堡)连接和装配技术负责人 Lars Larsen 将测试不同制造技术的使用。
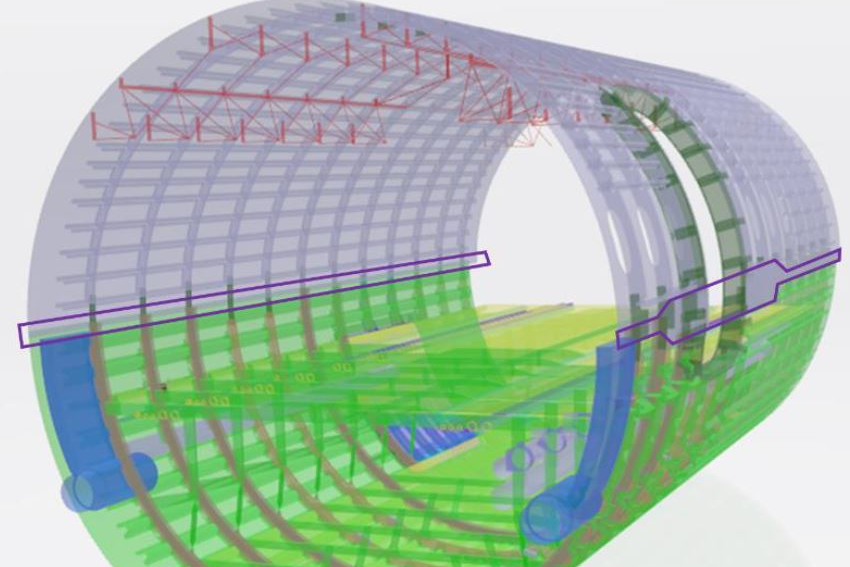
MFFD 的机身下部部分是通过 STUNNING(智能多功能和集成热塑性机身)项目生产的,该项目本身下面有许多项目(例如 MECATESTERS,专注于感应焊接)。下部将包括带有焊接纵梁和框架的下机身外壳、客舱和货舱地板结构以及相关的内部和系统元件。
STUNNING 由 GKN Fokker(荷兰帕彭德雷赫特)领导,主要合作伙伴 Diehl Aviation(德国劳普海姆)、荷兰航空航天中心(NLR;荷兰阿姆斯特丹)和代尔夫特理工大学(TU Delft;荷兰代尔夫特)。该项目旨在进一步成熟自动化装配工艺、热塑性塑料制造和焊接技术、集成设计和制造开发以及先进的电气系统架构。
GKN Fokker 项目经理 Bas Veldman 博士说:“我们的行业影响有两个方面:我们应用于演示器组装的自动化水平,以及开发生产零件的可持续方法。
根据 Veldman 于 2020 年 2 月发表的一篇论文,下机身的模块化组装是实现快速生产时间目标的关键。为了制造机身的主蒙皮,由碳纤维/热塑性预浸料制成的大型预成型件由超声波或激光加热的自动铺带 (ATL) 机铺放,但不进行原位固结。细节由自动纤维铺放 (AFP) 机器铺设。然后机器人将预制件放入阴型固结模具中,装袋后,外皮在高压釜中固结。据 Veldman 称,高压釜外工艺也正在研究中。纵梁和框架将焊接到蒙皮上。
“最初,计划是在今年生产所有零件,”Veldman 说,但由于与冠状病毒相关的延误,“现在也正在过渡到明年。但我们确实有相当多的零件现在已经完成,”包括许多较小的冲压成型零件,如夹子、支柱和支架,这些零件将用于连接飞机座椅和其他部件。强调可持续制造,Veldman 补充说,一些夹子是通过一个名为 ECO-CLIP 的 Clean Sky 2 项目由演示器上其他部件的重复使用边角料制造的。
从 2020 年初开始,生产 8 米长上壳的财团包括空客、Premium Aerotec(德国奥格斯堡),这是工业和结构设计的领头羊; DLR,负责蒙皮铺层和焊接技术开发;以及生产纵梁的 Aernnova(西班牙维多利亚-加斯泰兹)。
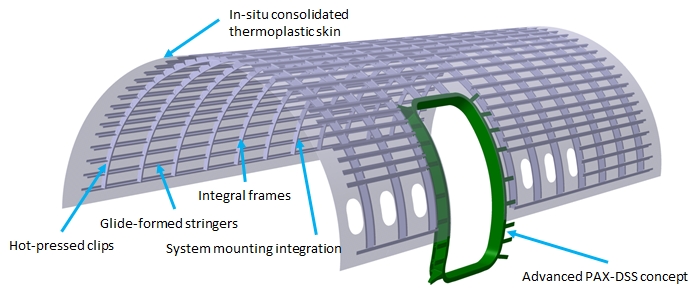
Larsen 说,为了让航空航天业过渡到更昂贵的热塑性材料,“我们必须证明我们可以在生产过程中节省成本。”上半财团正在开发新型先进纤维铺放 (AFP) 技术,特别是碳纤维/PAEK 蒙皮铺层的原位固结,以及用于集成纵梁、框架和结构的连续超声波焊接和电阻焊接的工业化其他组件,提高安全性并降低成本。 DLR 将首先建造一个 1 米长的预演示器测试外壳,以在建造全尺寸演示器之前验证技术,并计划在 2020 年底前制作预演示器外壳的外壳。纵梁定于 2021 年初。
两半的全尺寸版本预计将于 2021 年底完成。完成后,它们将被焊接到弗劳恩霍夫制造技术与先进材料研究所 IFAM(德国斯塔德)的最终演示器中。
树脂