在西班牙为 Clean Sky 2 推进热塑性复合材料和 RTM
EURECAT Centro Tecnológico de Catalunya(EURECAT 加泰罗尼亚技术中心,西班牙巴塞罗那)是一家私营的非营利性研发组织,拥有 11 个设施、650 名员工和 5000 万欧元的年收入。 “它是西班牙第二大研发中心,” EURECAT 航空航天市场项目总监 Angel Lagraña Hernandez 解释道。他解释说,EURECAT 的部分收入来自加泰罗尼亚政府,其余的一半必须来自私营公司——主要是中小型企业 (SME)——而另一半可能是公共公司,例如欧盟资助的清洁天空 2 程序。 “我们现在有 18 个 Clean Sky 项目,”Lagraña 指出,“我们获得这些项目完全是根据对提案征集的响应提交的竞争性提交。”
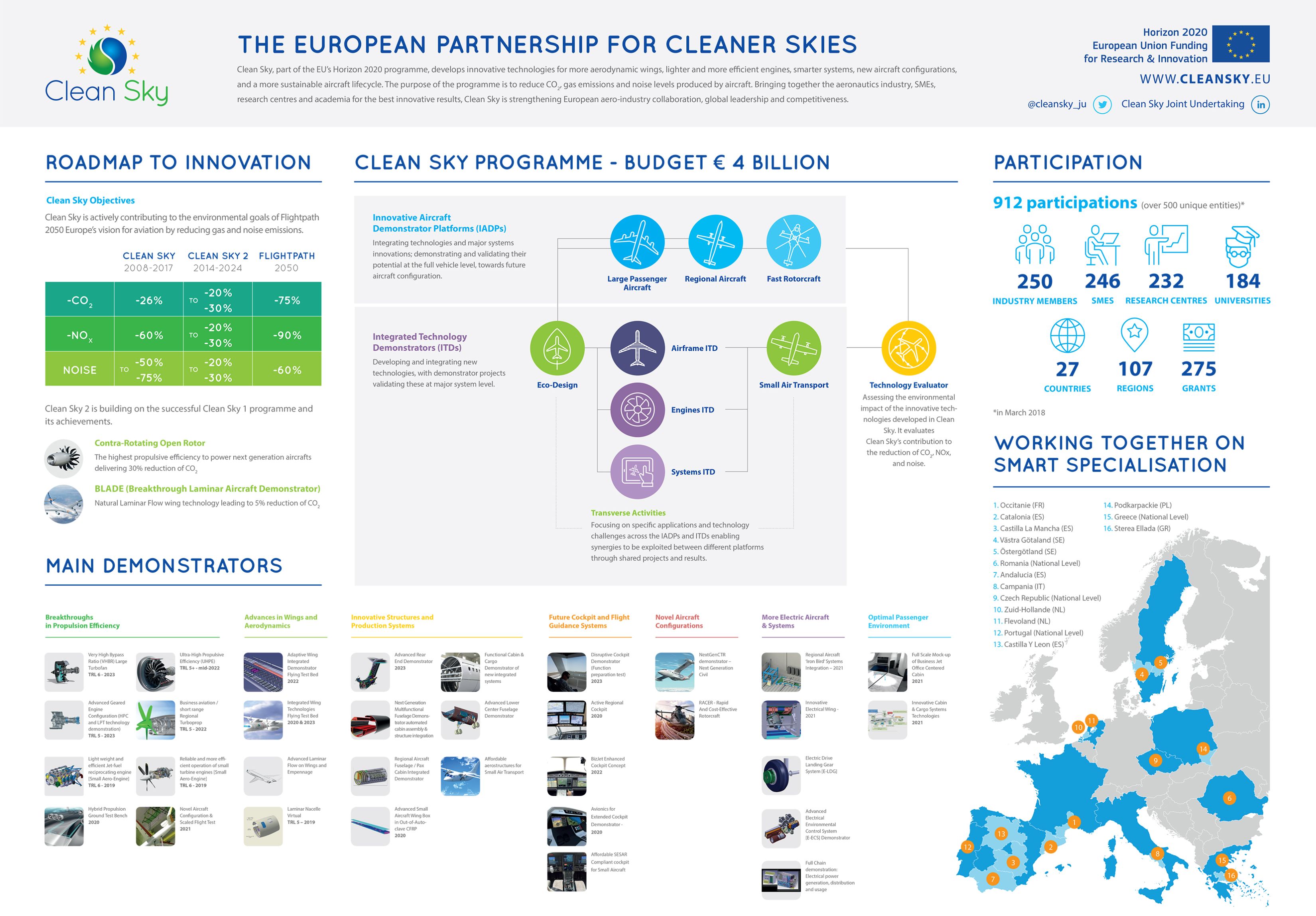
复合材料如何在 Clean Sky 2 的众多目标和计划的技术演示中发挥作用的示例包括:
- 下一代多功能机身演示器——利用热塑性塑料打造更清洁的天空
- 循环经济:支线飞机复合机身初具雏形
- 利用赛车专业知识打造 Clean Sky 的 FastCan
“EURECAT 是高度横向的,除了在航空航天领域的工作之外,还在汽车、铁路和其他行业工作,”Lagraña 说。 “它还在 IT 领域开展了很多活动,例如数据分析和区块链等。Composites 4.0 是其战略领域之一。”在复合材料中,他指出 EURECAT 主要用于非高压釜 (OOA) 技术。 “我们专注于热塑性塑料和液体压缩成型,包括实时过程监控,包括在加工过程中监控树脂的玻璃化转变温度 (Tg)。” (继续阅读本博客末尾的 COFRARE 部分,了解有关此 Tg 监控的更多信息。)
EURECAT 在 Clean Sky 2 中最新的复合材料相关项目包括:
- 基尔伯曼 展示热塑性复合龙骨梁(该项目已获得欧盟地平线研究和创新计划下的清洁天空 2 联合项目的资助,GAP n° 785435 KEELBEMAN);
- WINFRAME 4.0 为清洁天空(2008-2017)中的绿色支线飞机(GRA)演示机建造热塑性复合材料(TPC)窗框,并扩展到清洁天空2(2014-2024)中的支线飞机IADP(创新飞机演示平台);
(该项目已获得欧盟地平线研究和创新计划下的清洁天空 2 联合项目的资助,GAP n° 821323 WINFRAME 4.0。) - COFRARE 2020 用于使用树脂传递模塑 (RTM) 和 TPC 剪切带制成的热固性机身框架。
(该项目已获得 GAP n° 821261 COFRARE 2020 下欧盟地平线研究和创新计划下的清洁天空 2 联合项目的资助。)
热塑性复合龙骨梁
清洁天空 2 - JTI-CS2-2017-CFP06-LPA-02-20。项目工期:2018年3月至2019年12月
KEELBEMAN 项目的目标是为 A320 型飞机开发一种面向制造的龙骨梁结构,通过热塑性复合材料实现高飞机生产率,但成本可承受。除了作为项目协调员的 EURECAT,合作伙伴还包括:
- 空中客车 (法国图卢兹)担任主题经理
- CETMA (欧洲技术设计和材料研究中心,意大利布林迪西)
- CT 工程组 (CT Ingenieros,西班牙马德里),一家拥有众多全球办事处的公司,该公司与空中客车公司签订了多年的飞机开发合同,例如通过其德国汉堡办事处对机身、机翼和后端进行研究;后端研究(西班牙);机身和动力装置相关结构的研究(法国图卢兹)和机翼开发(英国布里斯托尔)
- 索菲特 (西班牙塞维利亚),一家航空结构制造和装配专家,拥有复合材料方面的专业知识和生产能力。
CT Engineering Group 通过其图卢兹办事处提供了龙骨梁几何形状的完整建模,而 Sofitec 则开发了无损检测 (NDT) 检查。 “对于这样一个封闭的盒子结构,这是非常具有挑战性的,”Lagraña 指出。
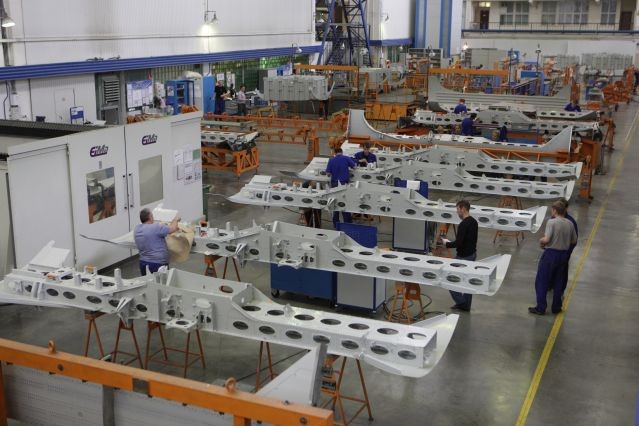
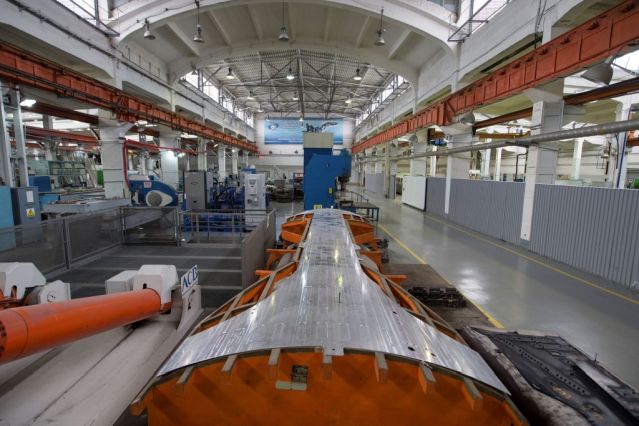
这里展示的是 A320 龙骨梁组件,由 Irkut Corporation(俄罗斯莫斯科)用金属制成。据报道,伊尔库特于 2004 年与空中客车公司签订合同,供应包括前起落架舱、龙骨梁和襟翼轨道在内的部件,平均每三架 A320 系列飞机就安装这些部件。来源 |伊尔库特
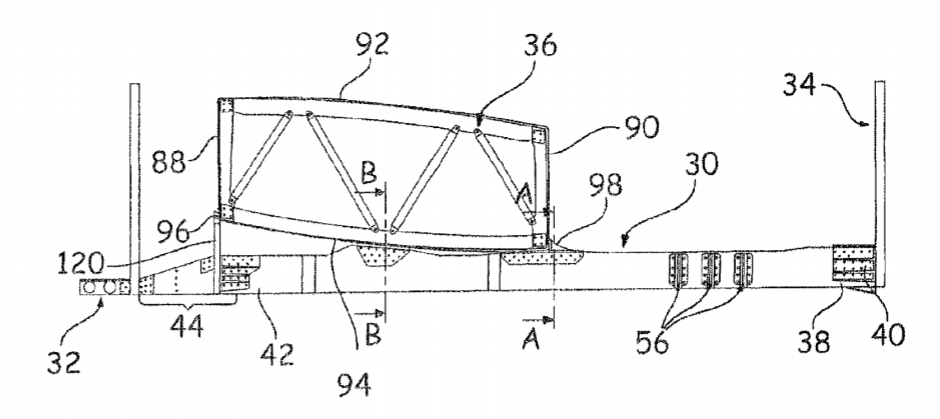
龙骨梁结构的发展
“今天,大多数飞机龙骨梁都是用金属制成的,除了空中客车
A350 是整体式碳纤维复合材料,”Lagraña 说。 “这需要大量的铆钉和大量的组装时间。”他解释说,龙骨梁是机身中的关键结构,“曾经有过龙骨梁在着陆过程中断裂,导致整个机身开裂折断的情况。
根据 Steve Wilhelm 2011 年的一篇文章,A350 龙骨梁由 70% 复合材料制成,长 54 英尺(16.5 米),由 10,000 个紧固件组装在一起,重 1.2 吨,构成了飞机的主干。 Wilhelm 指出,具有竞争力的波音 787 飞机“不依赖于如此坚固的龙骨结构,因为更多的船体强度来自端到端固定在一起的复合材料桶。”文章随后引用了 G2 Solutions LLC 航空咨询公司(美国华盛顿州柯克兰)的管理合伙人 Michel Merluzeau,他将空中客车的设计描述为“更传统”和“风险更小”,但指出龙骨梁“对于那架飞机的结构完整性。”
空中客车公司实际上在 2001 年率先为 A340 使用了复合龙骨梁。但如上所述,所需的大量铆钉阻碍了使用复合材料可能减轻的重量。因此,KEELBEMAN 项目的一个关键目标是通过使用焊接在一起的热塑性复合材料部件来最大限度地减少紧固件。
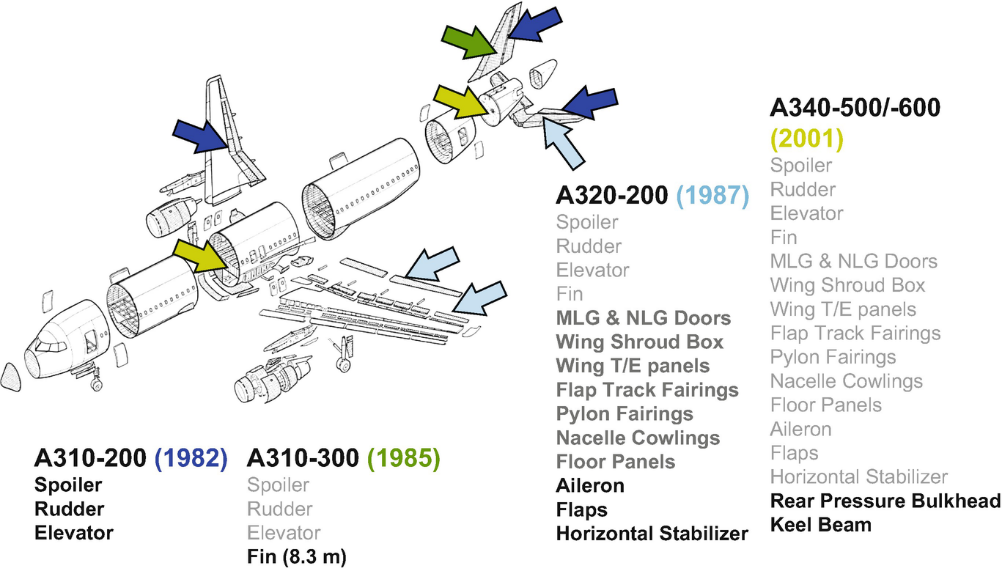
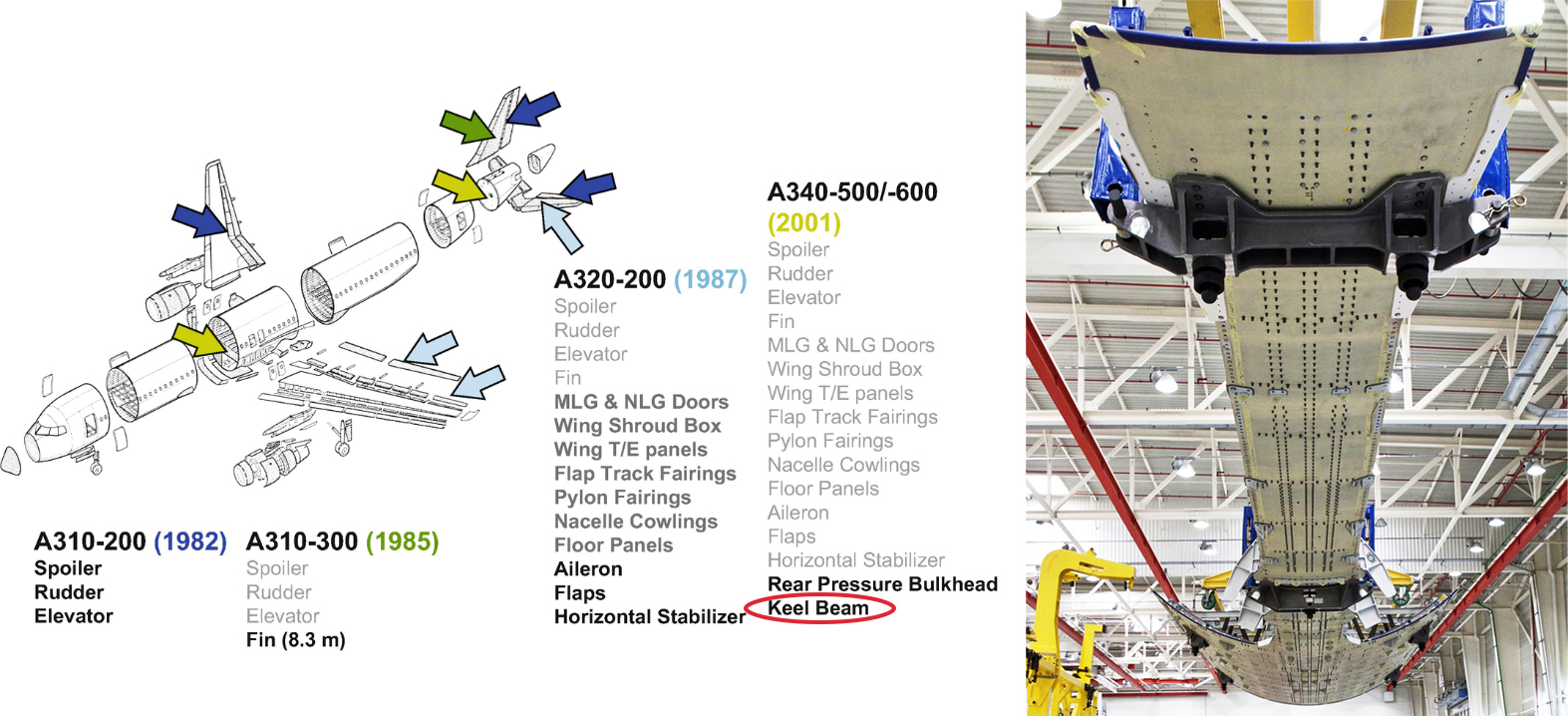
TPC龙骨梁
“使用焊接组装的热塑性复合龙骨梁的开发是空中客车未来飞机开发的一部分,其中包括明日之翼和明日机身等项目,”拉格拉尼亚说。 “在 KEELBEMAN 中,我们制作了一个 250 毫米 x 500 毫米 x 1 米长的带纵梁龙骨梁的演示部分,并展示了尽可能自动化地焊接这种结构的可行性。”
Lagraña 指出,演示器墙板和纵梁是使用碳纤维/聚醚酮酮 (PEKK) 单向 (UD) 胶带在 CETMA 开发的连续压缩成型 (CCM) 工艺中制成的(参见“航空航天级压缩成型”和“PEEK 与 PEKK对比 PAEK 和连续压缩成型”)。 “还有用于横向加强筋的肋条,它们是由 EURECAT 使用传统的非等温压缩成型制成的,”Lagraña 补充道。
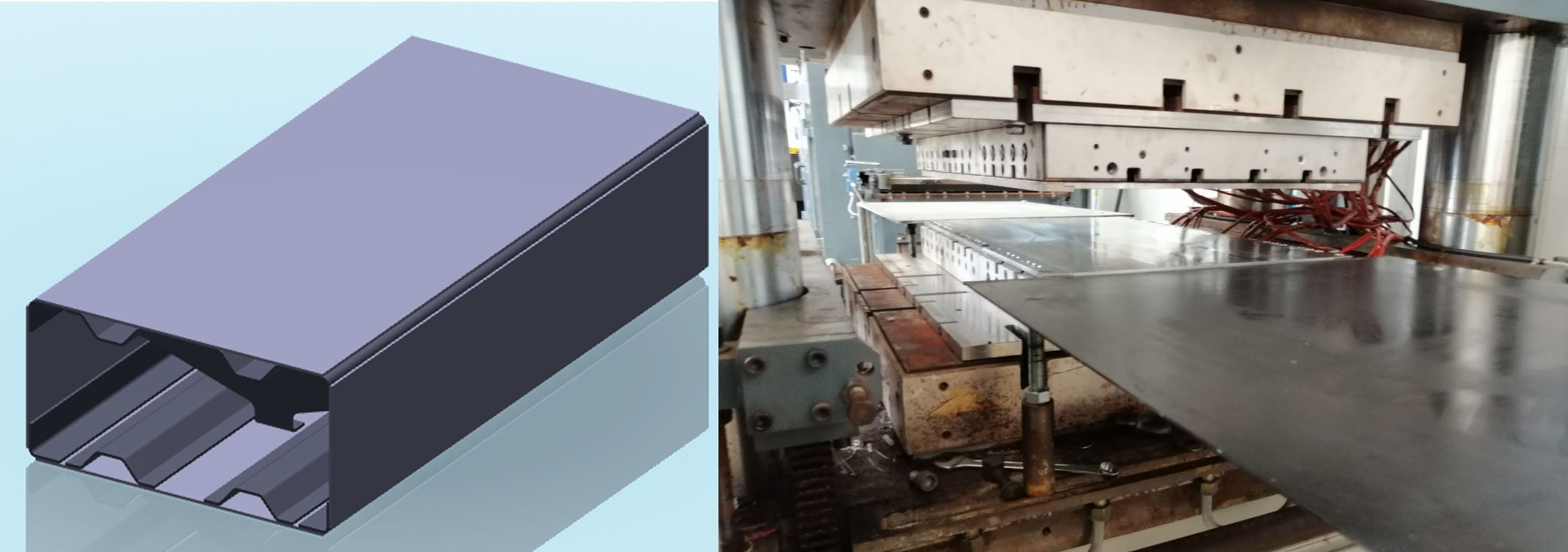
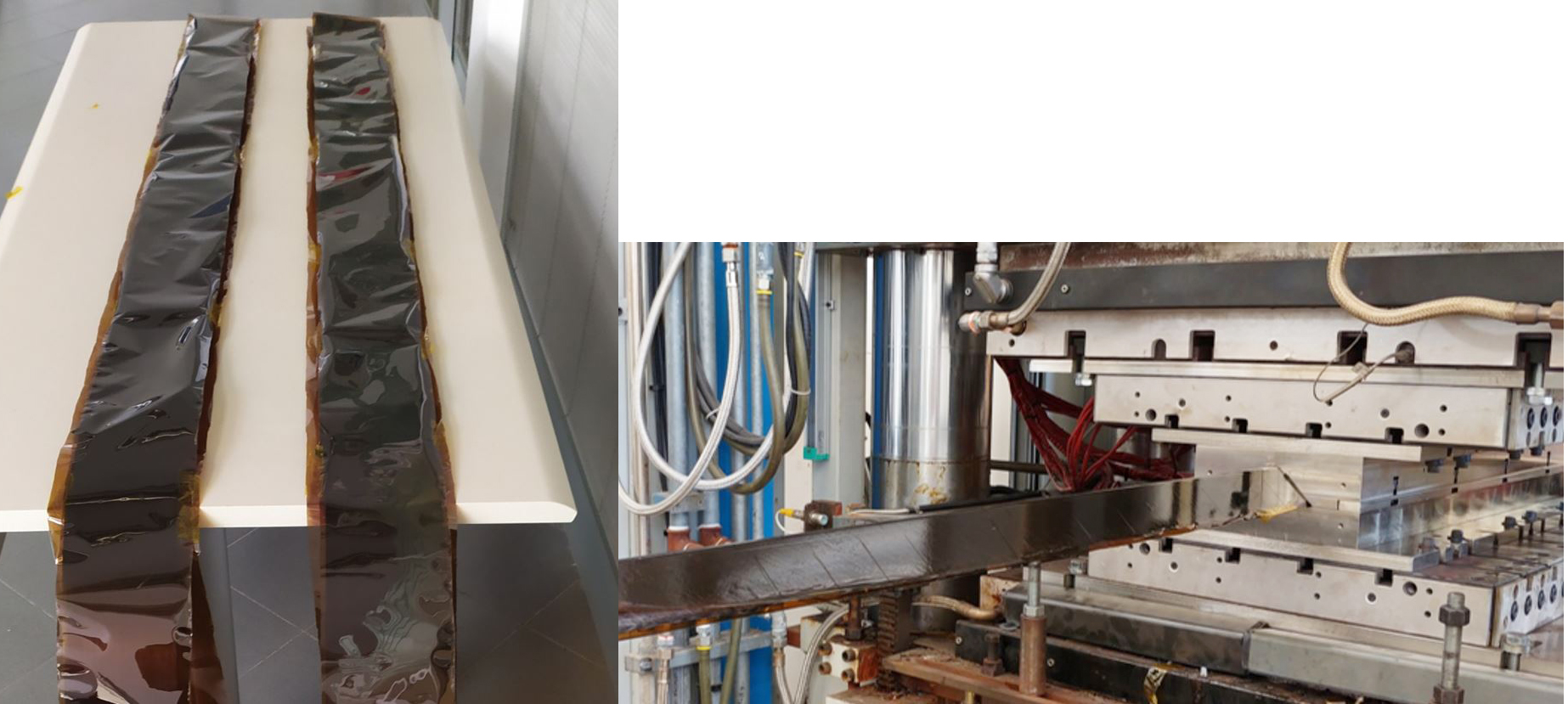
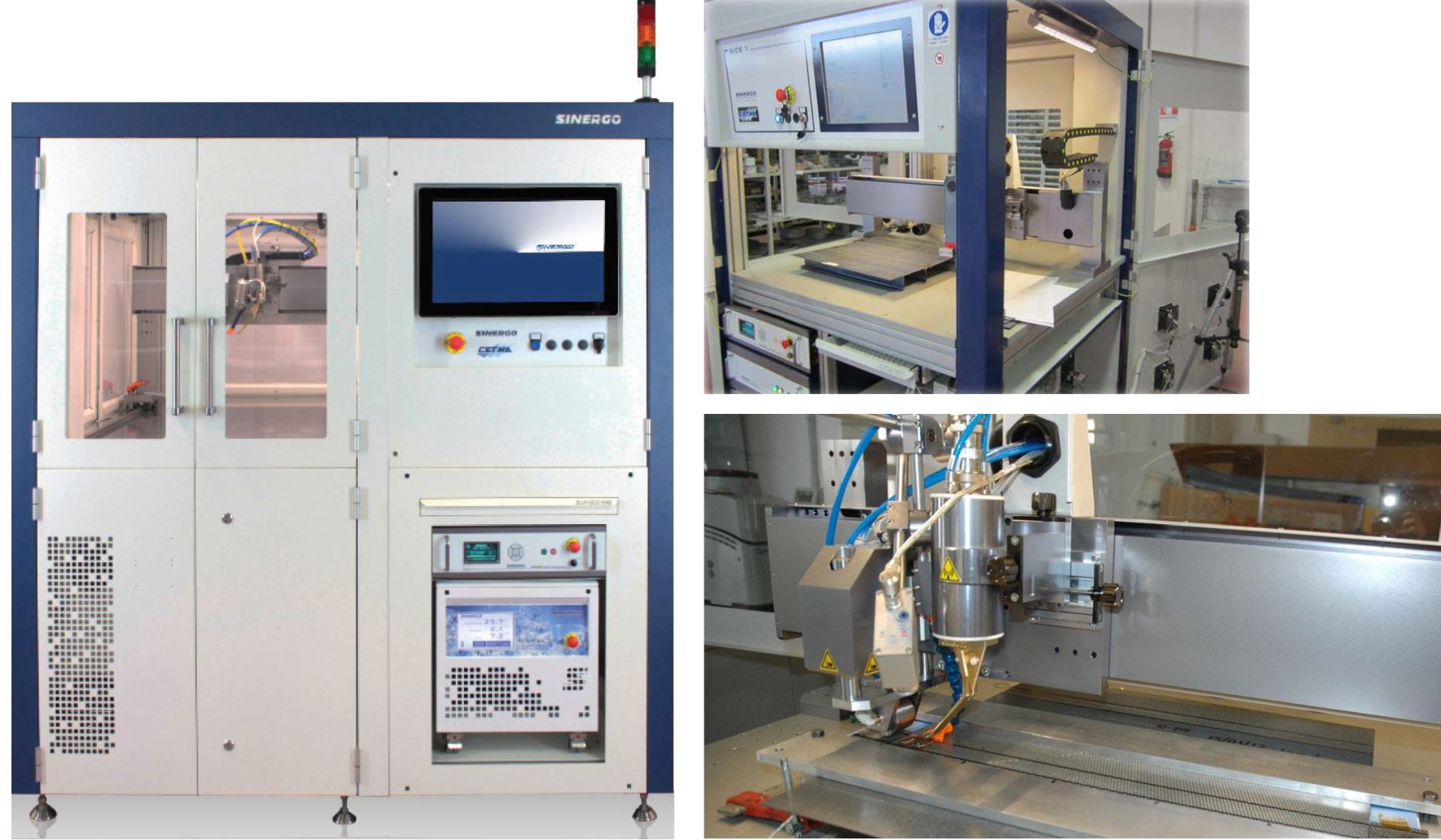
感应焊接是关键推动因素
Lagraña 指出,CETMA 不仅在 KEELBEMAN 的零件生产中发挥了关键作用,还在使用其专利感应焊机和技术组装演示器方面发挥了关键作用。这种焊接最初是在第一个 Clean Sky 计划的 ECO FAIRS 项目(2011-2014 年)中开发的,以及上面显示的 TPC 结构的等温和非等温压缩成型。在 ECO FAIRS 中,CETMA 使用所有这些技术,基于现有的阿古斯塔韦斯特兰直升机尾翼上面板(纵梁加筋蒙皮面板)以及弯曲的舷外整流罩演示器生产了原型演示器。虽然这些是使用 CETEX(由 TenCate 提供,现在是 Toray Advanced Composites)T300 3K 5HS 碳纤维织物和双面 PPS(聚苯硫醚)薄膜制成的,但 CETMA 也证明了使用 PEEK 和 PEI 复合材料进行感应焊接。
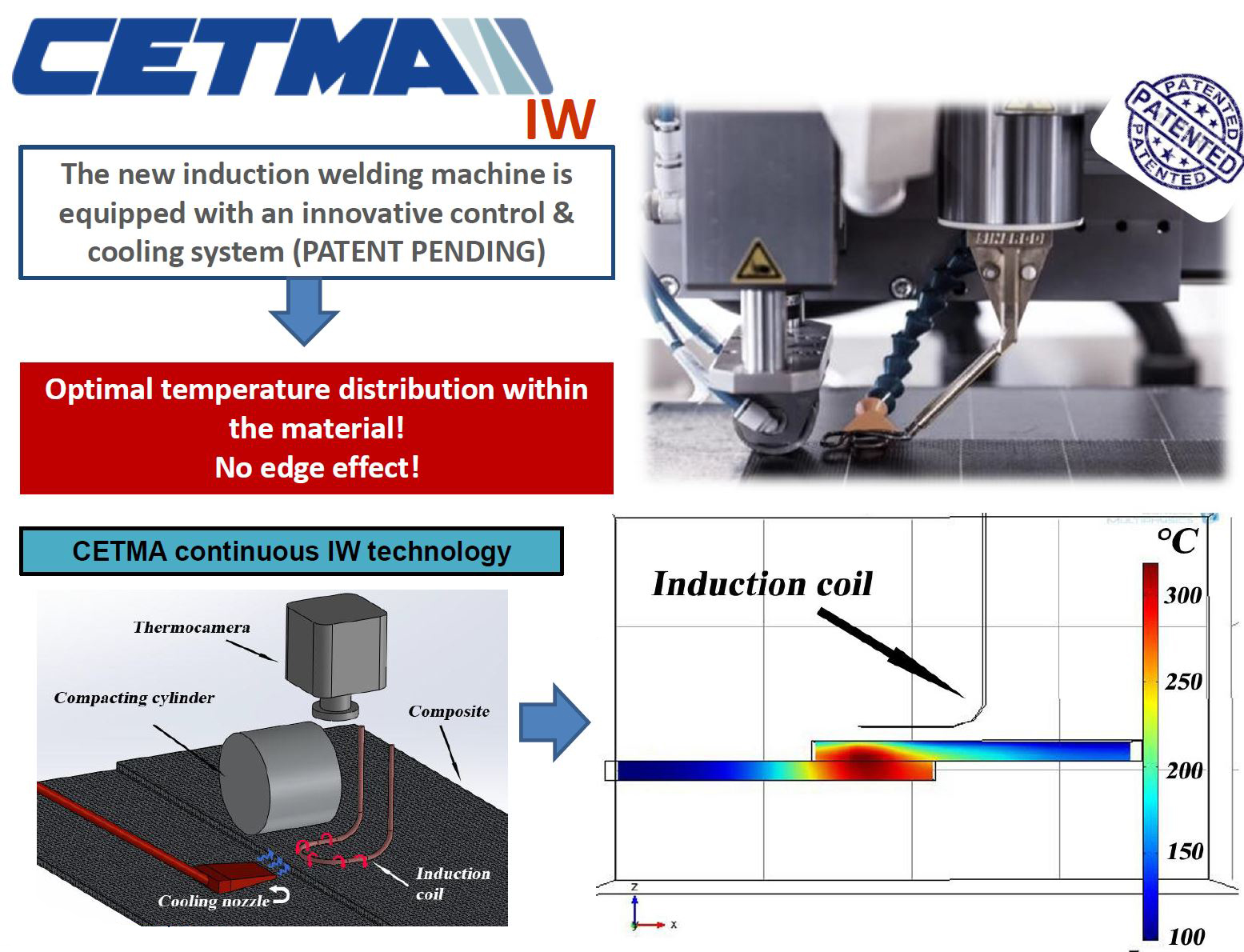
CETMA 选择感应焊接 (IW) 作为最有前途的热塑性复合材料焊接技术,并与焊接和电子工程专家 SINERGO srl(Valdobbiadene,Treviso,意大利)合作开发了一种新型感应焊接机。 SINERGO 提供的基于龙门的 SICE 1 WIDE 机器(见下图) 能够连续焊接长达 1 米乘 1 米的航空级零件。它包括一个强大的控制系统,以确保在焊接材料内实现优化的温度分布。该机器配备冷却气缸以施加固结压力,并配备空气冷却系统以在需要时去除热量,例如在边缘处,感应涡流的流动受到限制,从而导致高电流密度和过热.也可以将CETMA感应焊头安装在6轴机械臂上,用于焊接几何复杂的形状。
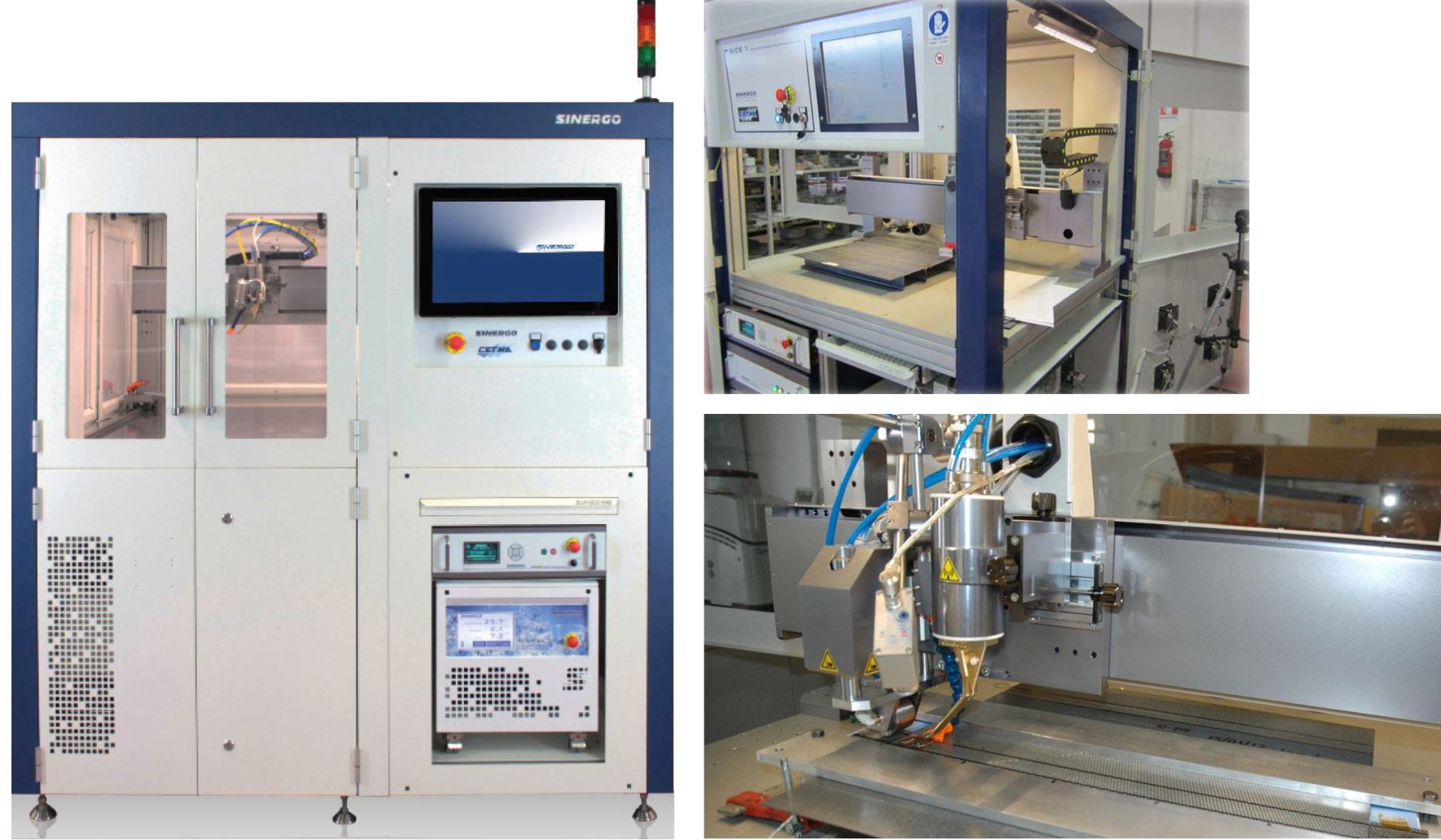
CETMA 还开发了通过使用仿真工具优化其感应焊接工艺的能力,使用 COMSOL Multiphysics(COMSOL Inc.,Burlington,Mass,美国)有限元建模 (FEM) 软件进行数值分析。它通过大量的物理测试验证了这些模型。 CETMA 通过对焊接试样的单搭接测试证实了其优化的工艺参数,其中剪切强度值非常接近文献报道的最大值。 CETMA 表示,值得注意的是,这些也远高于使用结构粘合剂时的最大值。
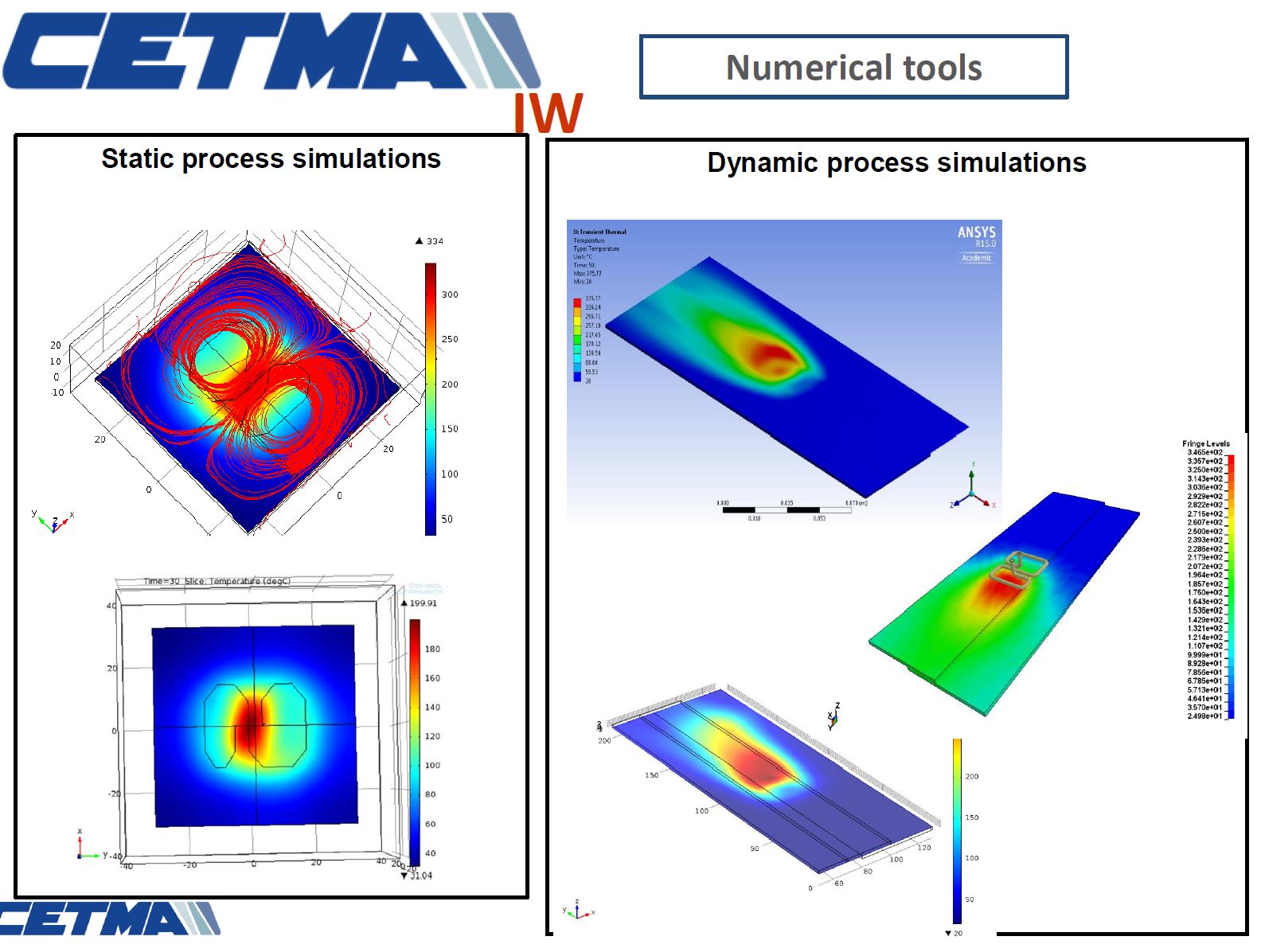
CETMA 已经证明了其对多种材料的焊接能力,包括编织和 UD 碳纤维,以及 PEEK、PEI、PEKK、PP、PA6、PA12,甚至使用热塑性 PVB(聚乙烯醇缩丁醛)混合材料焊接到 CF/环氧树脂用于从热固性基材过渡到用于焊接的热塑性表面的层。 (本节的大部分细节来自 CETMA 能力介绍和 CORDIS 最终报告 用于 ECO FAIRS。) CETMA 于 2014 年申请了欧洲专利,发明人 Silvio Pappada 和 Andrea Salomi 于 2016 年获得专利 EP2801472A1。CETMA 已发表了大量关于该技术的论文和演讲,包括:
- “支持非高压釜技术开发的有限元模拟”,A&D,2012 年 10 月 11-12 日
- “支持 PPS 碳复合材料连续感应焊接的有限元模拟”,SEICO,2013 年 3 月 11 日至 13 日,“巴黎”
- “开发用于航空航天领域热塑性复合材料的新型感应焊接机”,意大利航空航天协会第 22 届会议那不勒斯,2013 年 9 月 9 日至 12 日
- “航空航天领域的感应焊接”,TPRC,热塑性复合材料欧洲联盟,网络会议,2013 年 12 月。
- “航空航天领域热塑性部件的全面测试”,SEICO 14,2014 年 3 月 10-11 日“巴黎”
- “航空航天领域的新型感应焊接设备”,JEC 杂志,第 87 期,2014 年 3 月,第 89-91 页。
KEELBEMAN 状态和前进的道路
空客于12月参观了CETMA,观看了1米演示器部分的最终焊接,KEELBEMAN团队还举行了技术准备水平(TRL)的最终审查。 Lagraña 说:“我们正在取得良好的结果,并且正在使技术从 TRL 3 成熟到 TRL 4。”下一步可能包括进一步开发 TRL 6 并生产全尺寸龙骨梁,该梁将安装在 Clean Sky 2 的一个演示器中,例如 WP 2.3.2 全尺寸下中机身,但这还没有决定了。
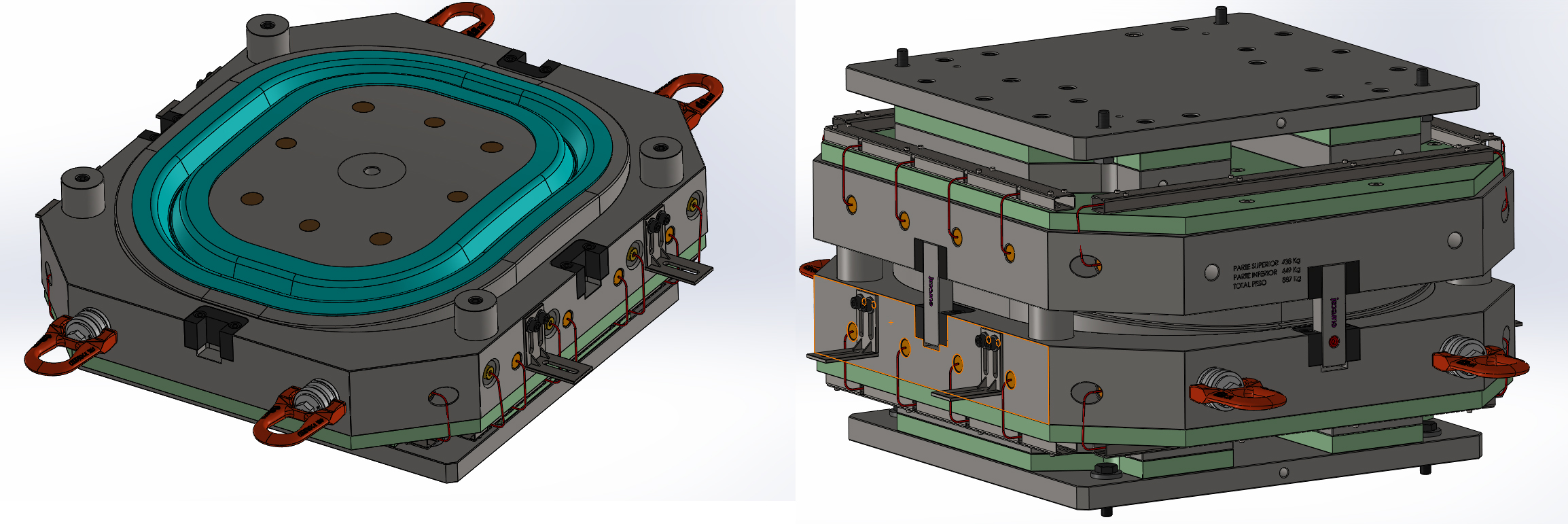
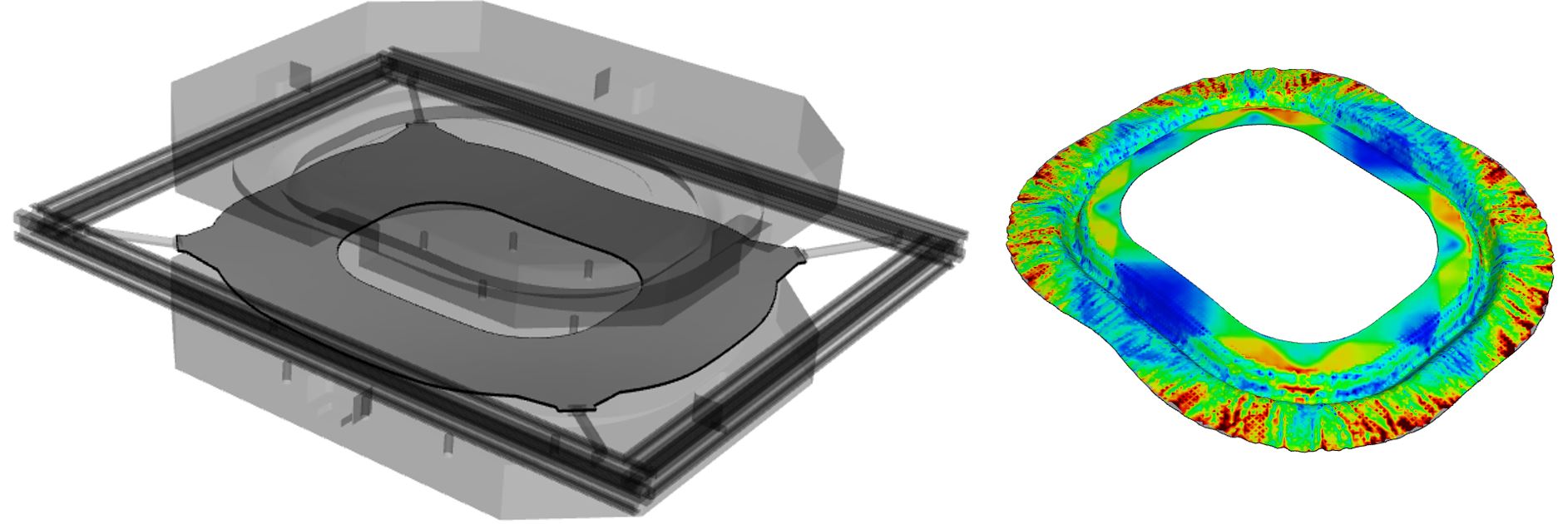
WINFRAME 4.0 TPC 窗框项目
EURECAT 的另一个热塑性复合材料 (TPC) 计划是 WINFRAME 4.0,其目标是为支线飞机机身/机舱集成地面演示器开发和制造 24 个窗框(参见 Clean Sky 2 支线飞机和 Full -scale 创新机身和客舱示范 以下)。 WINFRAME 4.0 合作伙伴包括:
- 跨国航空航天公司莱昂纳多 (意大利罗马)担任主题经理
- EURECAT
- 索菲特。
“我们使用的方法可以每 10 分钟生成一个窗框,”Lagraña 说。生产步骤包括:在烤箱中加热 TPC 层压板坯,转化为模具,在压力机中关闭模具,加热和加压 10-20 分钟,然后将成品零件脱模。 “这种方法不仅可以实现比液体成型更短的周期,而且还可以降低成本,”他补充道。 “该工艺在汽车行业广为人知,它采用高度自动化的配置压缩成型,提高了零件的质量,但使用的航空航天材料不同,在这种情况下,碳纤维增强 PPS 和 Toray 的碳纤维Advanced Composites(前身为 TenCate)。到该项目结束时,我们将实现这些技术的 TRL 6,”Lagraña 说。
COFRARE 项目:RTM C 型框架和热塑性剪切带
COFRARE 2020 项目是初始 COFRARE 2.0 项目的扩展:
清洁天空 2 - JTI-CS2-2015-CFP02-AIR-02-16。 “高生产率低成本复合材料车架制造工艺开发 2016-2018年。
Clean Sky 2 COFRARE 2.0 项目的目标是开发一种具有竞争力且可行的碳纤维复合框架制造工艺,用于支线飞机的复合板机身。合作伙伴包括:
- 位于那不勒斯的一级航空航天供应商和工程/工业化公司 DEMA (Design Manufacturing SpA,Somma Vesuviana,意大利)
- EURECAT
- LGAI 技术中心 S.A.,Applus+ Laboratories 的一个部门 在西班牙巴塞罗那提供测试。
下一代 COFRARE 2020 项目的目标是制造用于 Clean Sky 2 机身/机舱集成地面演示器的全尺寸复合框架和剪力拉杆。该演示器由 Clean Sky 2 的支线飞机 IADP(创新飞机演示器平台)组织,并在 2015 年 3 月联合技术计划文件的第 5.2.2 节中有详细说明:
“区域飞机是Clean Sky的关键元素 通过专用的 ITD(集成技术演示器) - 绿色支线飞机 (GRA) ,为构建尊重环境的航空运输系统提供必要的基石,确保安全和无缝的移动性,并在欧洲建立行业领先地位。 在晴空2 , ... 支线飞机 IADP 的示范目标比当前的Clean Sky复杂、全面和具有挑战性 GRA项目 ,被迫在预算和时间限制内工作。 ……”
2015 年联合技术计划概述了支线飞机的发展,包括两个飞行试验台和五个大型综合地面演示机。后者包括全尺寸创新机身和客舱演示器 :“机身将全面展示复合材料、结构和制造技术 旨在[实现]减轻重量和成本,并通过整个生命周期的生态设计和能源消耗优化(朝着零影响)最大限度地减少对环境的影响。”
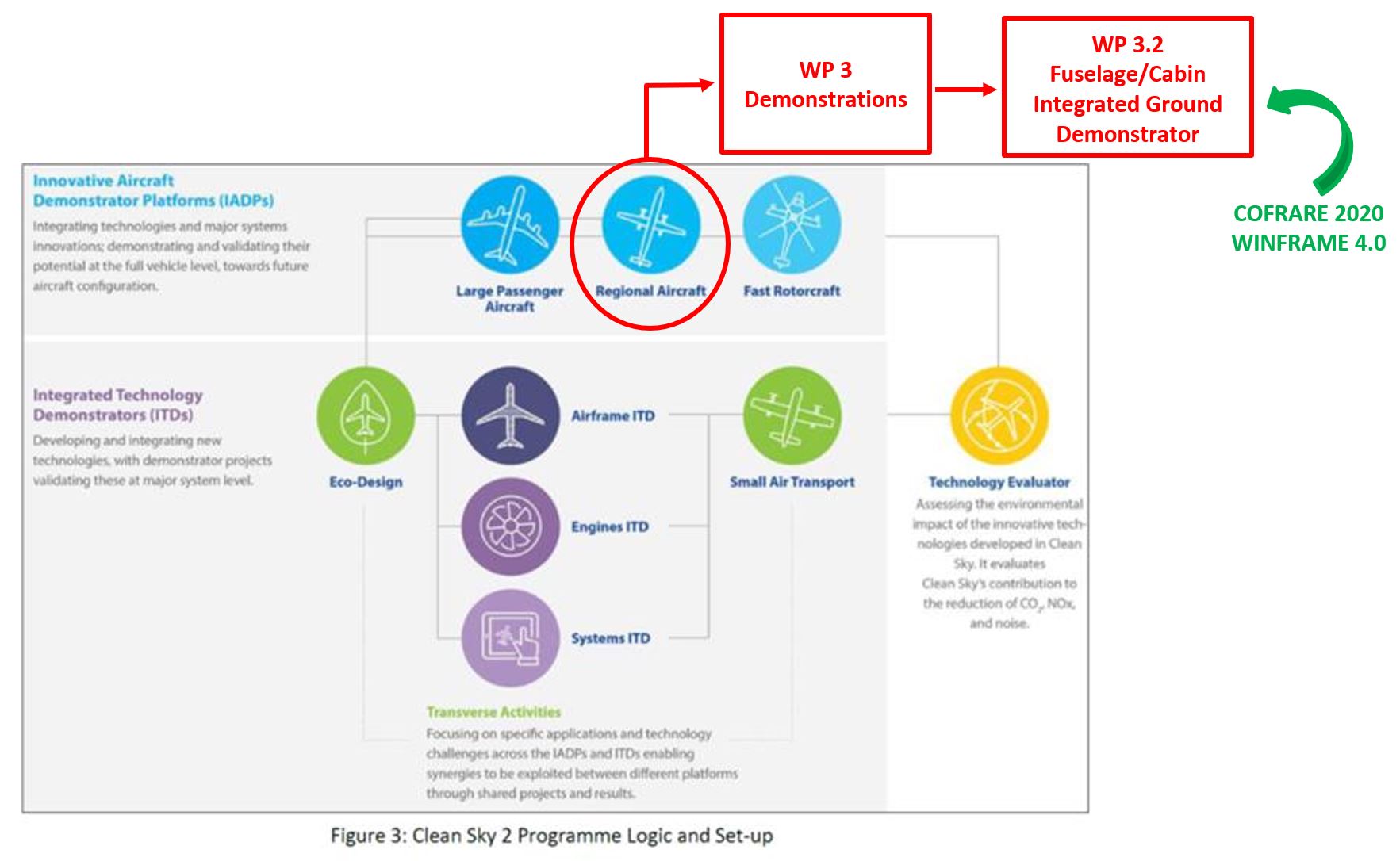
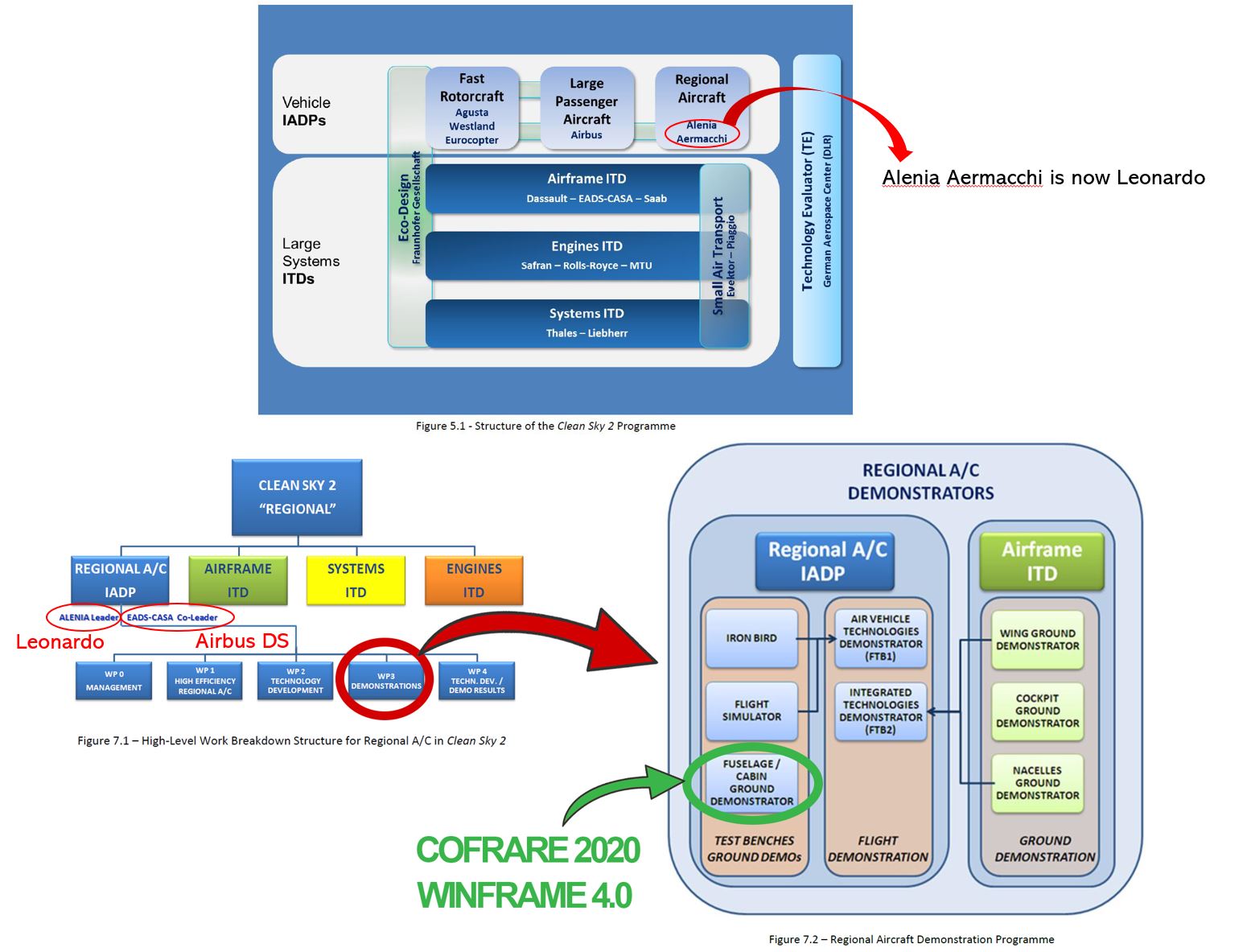
COFRARE 2020 项目合作伙伴包括:
- 莱昂纳多 作为主题经理
- EURECAT
- DEMA
- 飞机零部件和组件制造A.阿贝特 (意大利诺拉/马里利亚诺)。
“在 COFRARE 2020 中,我们正在使用 RTM(树脂传递成型)制造机身框架,它将被集成到机身演示器中,”Lagraña 解释说。 “我们正在使用 Shikibo(日本大阪)的 Ziplus 技术,该技术生产非常适合树脂注射的瓶坯。” Shikibo Ltd. 隶属于 Composite Alliance Corp.(美国德克萨斯州达拉斯市),提供各种纺织预成型技术。
该计划的一个有趣方面是使用 Synthesites(比利时 Uccle)的传感器实时监控树脂到达、温度、压力、Tg 和固化。 “传感器位于复合材料部件和 RTM 工具的特定区域,以优化树脂注射策略,”Lagraña 指出。使用 ISOJET(法国科尔巴)提供的高度自动化系统实现注射,该系统也是 Composite Alliance Corp 的一部分。合成传感器是介电传感器,但与大多数介电分析 (DEA) 不同,后者基于交流电 (AC) , Synthesites 使用直流电 (DC)。 “我们的传感器在使用树脂等高电阻材料时表现良好,而且因为我们施加的是单一电压,所以我们不必分析多个频率,但即使在固化结束时我们也能实现高精度,”Synthesites 主管 Dr.尼科斯·潘泰莱利斯。
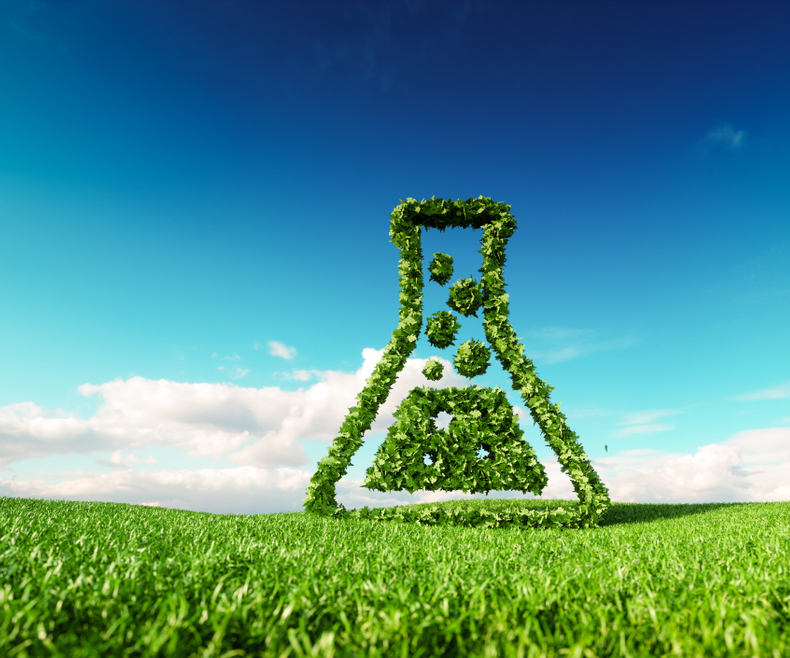
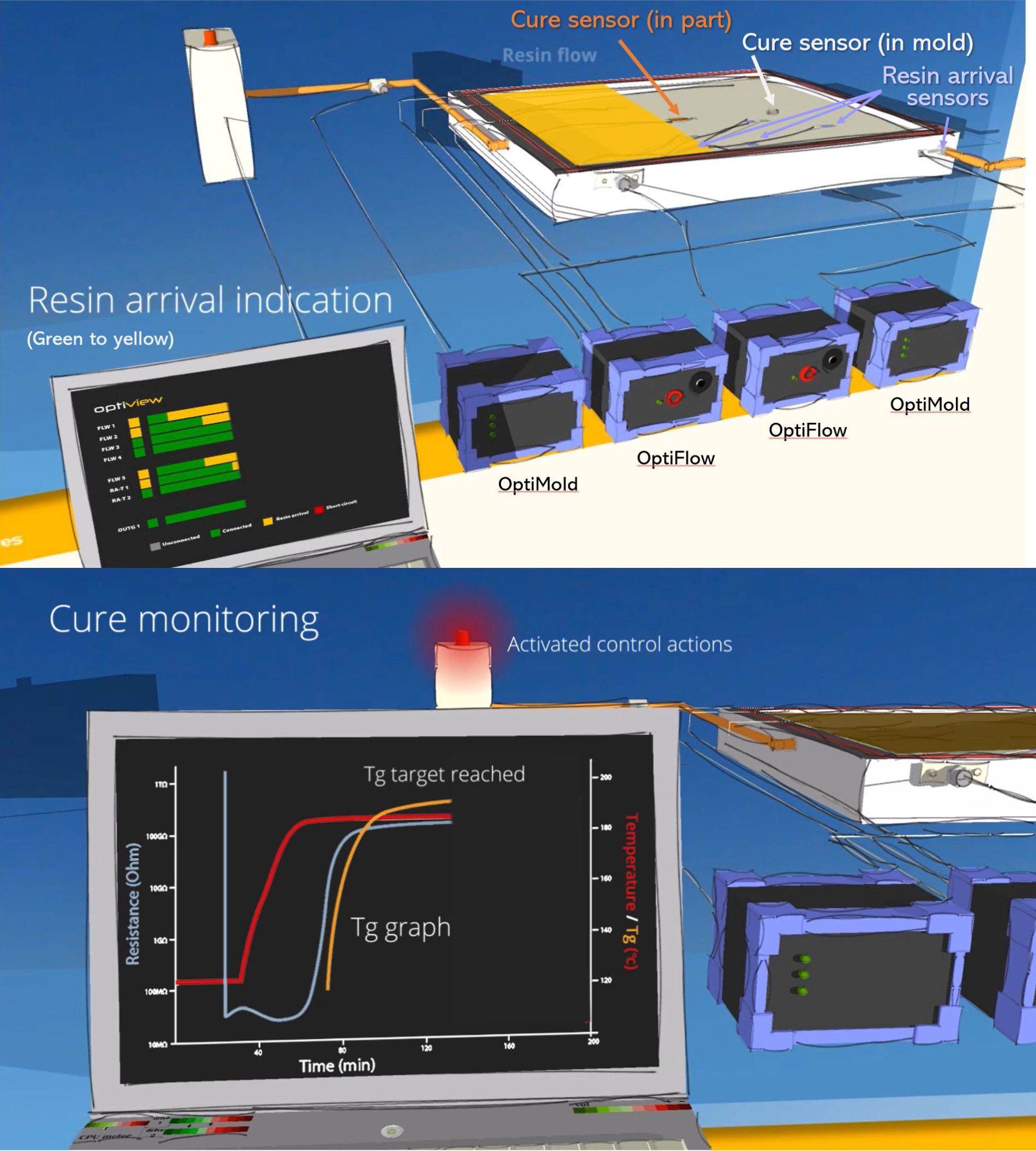
“我们在 2011 年的 SAMPE 会议上遇到了 Synthesites,”Lagraña 回忆道。 “他们谈到传感器可以缩短固化周期。我们正在探索如何自动化机身框架的预制件,甚至使用 HP-RTM(高压 RTM)进行更快的处理,但您仍然需要 3-4 小时的处理时间。然而,借助 Synthesites,我们通过监测 Tg 将固化周期缩短了 50%。我们现在正在测试属性。这些传感器可以在高压下工作,但在我们的 RTM 处理中,我们只使用了 8 巴的压力。”
Synthesites 直流电介质传感器、OptiFlow 液态树脂流量监控系统和 OptiMold 固化监控系统已在多家风力叶片制造商的生产中进行了演示。庞巴迪航空航天公司(英国贝尔法斯特)也使用它们为 C 系列现在的空中客车 220 生产液态复合材料模压机翼。德国航空航天中心(德国施塔德 DLR)已经证明固化周期减少高达 50%高压釜预浸料和 RTM,而国家复合材料中心(NCC,布里斯托尔,英国)已经证明,即使对于高反应性树脂,通过传感器测量树脂温度和电阻率进行的实时 Tg 计算与从固化面板测量的 Tg 一样准确使用差示扫描量热法 (DSC)。
使用 TPC 剪切拉杆连接框架
COFRARE 2020 的另一个关键部分是一种更大批量的生产方法,用于生产将 RTM 机身 C 型框架连接到复合机身面板所需的数百个剪切带和支架。 “我们正在为通过压缩成型生产的热塑性复合材料支架开发 255 种不同的几何形状,”Lagraña 说。 (注意,GKN Fokker 有多个 Clean Sky 2 项目,它将为大型客机 IADP 的多功能机身演示器生产 TPC 支架;COFRARE 2020 中的这项工作适用于较小的支线飞机。) 基本方法如下所示,使用匹配的钢工具和热压机。 “这种压缩成型工具的成本仅为 2,000 欧元,与 RTM 工具相比,这是非常实惠的,”他补充道。 “冲压还实现了非常短的循环时间。”
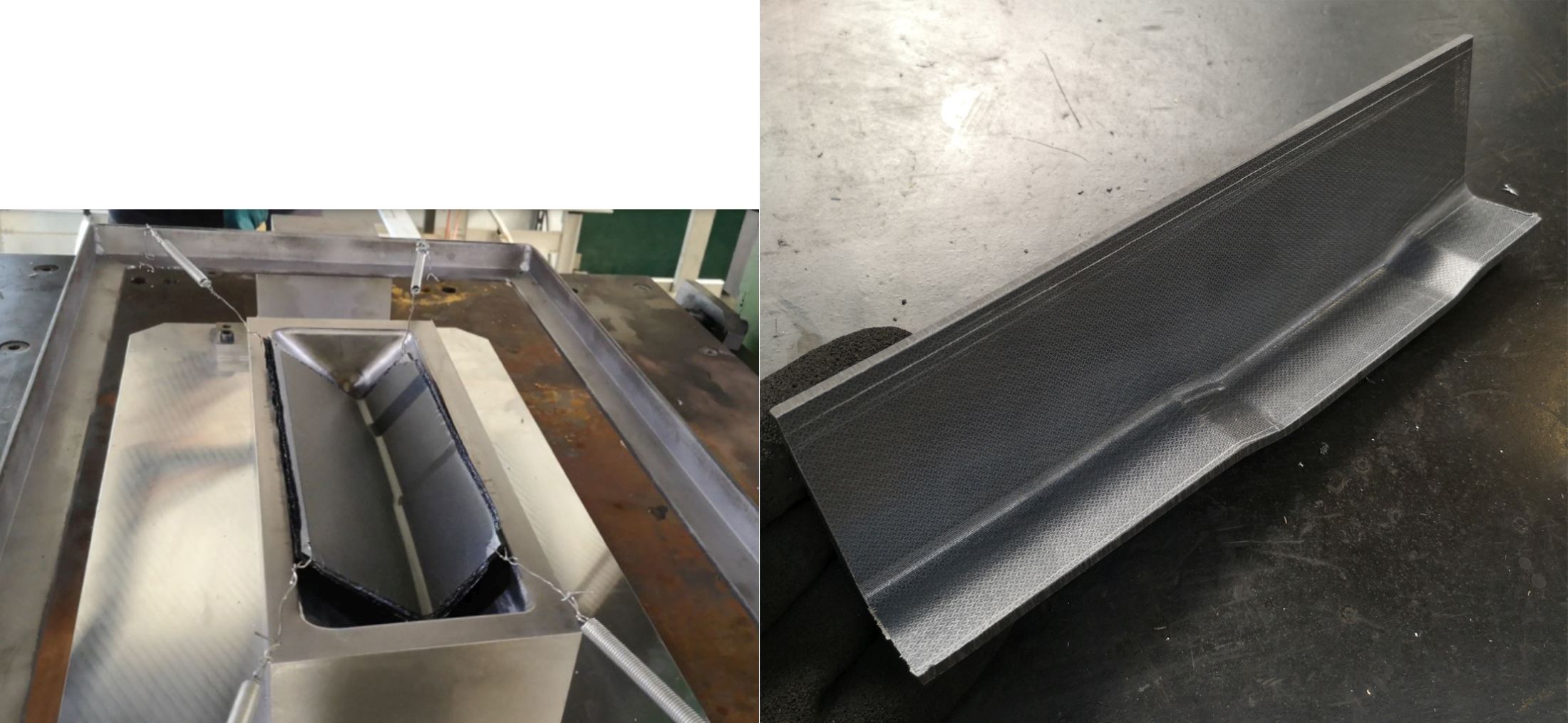
Lagraña 说,EURECAT 投资于保持在复合材料技术开发的最前沿。 “我们相信清洁环境的压力将大大增加复合材料在所有运输中的使用,并且可负担性和性能将相辅相成。这就是为什么我们专注于向客户提供自动化、非高压釜技术的原因。”
请继续关注我即将发布的关于 Clean Sky 2 STUNNING 和 MECATESTERS 项目的博客,其中将讨论多功能机身演示器的焊接 TPC 支架的开发以及该项目的 PAEK 的完整表征。我还将更详细地介绍 Synthesites 以及 CETMA 在复合材料方面的更多发展。 2020 年对于复合材料来说将是非常有趣的一年!
树脂