多层热塑性胶带、AFP 和树脂灌注用于更民主的复合材料
Novotech(意大利那不勒斯)最初是从意大利南部的那不勒斯“Federico II”大学衍生出来的,该大学由 Leonardo Lecce 教授于 1992 年创立。“我们支持通用航空公司并在意大利提供研发服务,”Lecce 说谁现在是 Novotech 的首席执行官。 “我们为飞机部件提供了结构分析,还帮助进行了飞机开发。”
位于为波音 787 制造复合材料机身部分的莱昂纳多工厂附近,Novotech 于 2014 年开始专注于复合材料。它从科里奥利复合材料公司(法国奎文)购买了一个自动纤维铺放 (AFP) 单元,并从高压釜中开发出来( OOA) 加工,包括树脂灌注和热塑性复合材料制造,具有使用 AFP 进行原位固结的特殊专业知识。
Novotech 参与了众多行业研究项目,包括:
- MESEMA (用于更多电动飞机的磁弹性能源系统)
- SARISTU (智能智能飞机结构)
- ASAM (飞机机构的高级仿真)
- LAMITECH (混合复合材料自动分层的创新测试方法)
- PROALATECH (创新 CFRP 尾翼的结构表征和修复解决方案分析)
- 脸 (友好的机舱环境)
- AIRGREEN 2 - CLEAN SKY 2(为下一代支线飞机开发创新机翼概念和方法)
- 姐姐检查 (AFP无损检测创新系统调查与整合)
- TRINITI - CLEAN SKY 2(飞机用多材料热塑性高压氮气罐)
- NHYTE - H2020(OOA 制造的新型混合热塑性复合材料航空结构)
“我们还与英国的氰特 (Cytec) 建立了特殊的关系,开发新的复合材料和工艺,”Lecce 说。请注意,Cytec 已被 Solvay 收购,所引用的地点是位于英国 Heanor 的 Solvay Composite Materials——该地点具有悠久的创新历史,包括最近通过 RAPM 计划测试的双隔膜成型工艺。 “我们最近的此类活动是开发一种 OOA 热塑性工艺,该工艺使用一种新的创新压机,将 PEEK(聚醚醚酮)和 PEI(聚醚酰亚胺)组合成一种新的复合材料。”这种新材料、设备和工艺现已在碳纤维增强塑料 (CFRP) 飞机纵梁中得到验证,该纵梁采用 AFP 原位固结和 NHYTE 项目焊接制成。
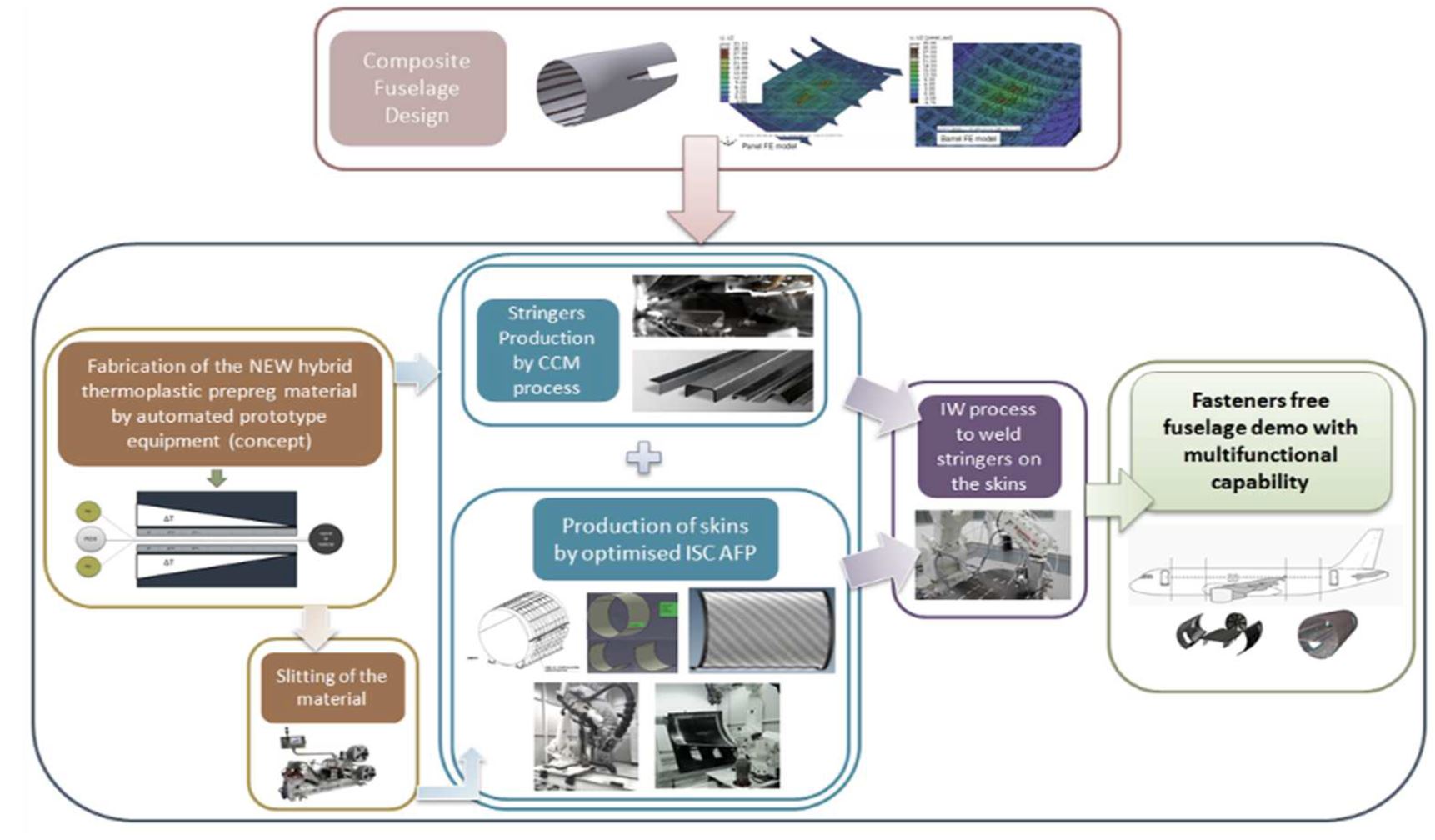
NHYTE
NHYTE 是由欧盟委员会地平线 2020 计划资助的一个研究项目,于 2017 年 5 月至 2020 年 10 月进行。“NHYTE 是关于使用无定形粘合来实现热塑性复合材料的可持续温度和工艺条件,”NHYTE 项目协调员 Marco Barile 博士解释说和 Novotech 的 CTO。这种非晶键合(见下图)是 NHYTE 的另一个合作伙伴——莱昂纳多(意大利罗马)的航空结构部门获得专利的概念,该部门在意大利南部拥有多个生产设施。
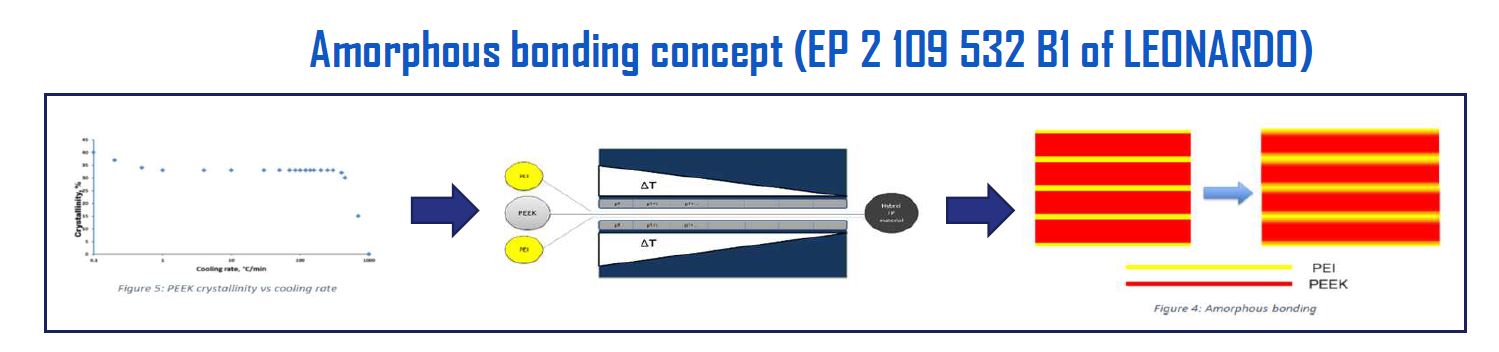
图片来源:NHYTE项目
“借助 NHYTE 开发的材料,我们可以通过热塑性复合材料 (TPC) 的 AFP 原位固结 (ISC) 克服当前的材料限制。对于半结晶 PEEK 聚合物,我们可以在略高于 215 度玻璃化转变温度 (Tg) 的温度下加热非晶 PEI 层,而不是在略低于 400 摄氏度的温度下进行加工。 PEI 的熔化和冷却也更快,与 PEEK 相比不必如此控制。” Barile 指出,这个概念可以使用其他无定形热塑性塑料。选择 PEI 是因为它与 PEEK 结合良好,PEEK 是一种在多个 AFP 飞机结构演示器中得到充分证明的材料。
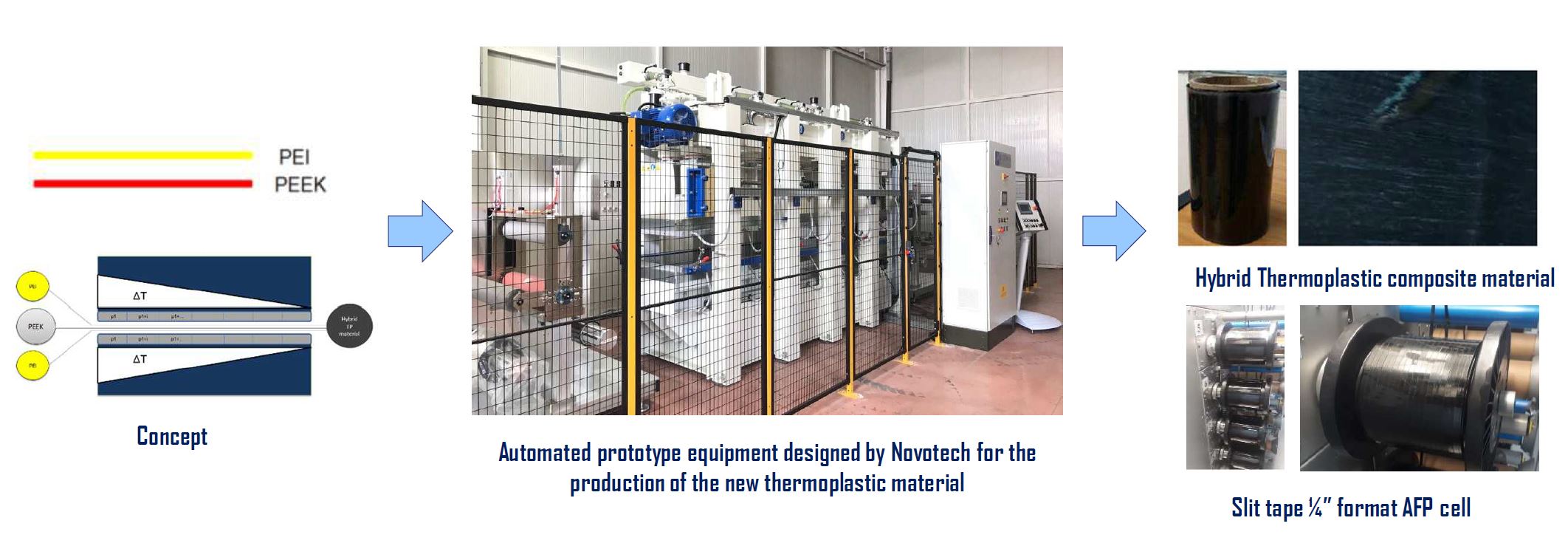
NHYTE 开发的这种新材料是在由 NOVOTECH 设计的连续压机中生产的。 Orma Macchine(意大利贝加莫)提供压机机身,COMEC Innovative(意大利基耶蒂)提供收卷和放卷模块。 “这台印刷机可以生产一卷连续的材料,然后我们将其切割成用于 AFP 机器的切条带,”Barile 说。三种不同的材料从左侧进入印刷机,如上图所示。 “我们在顶部和底部有 PEI,然后在中间有 PEEK,”Barile 解释说。
作为一种半结晶聚合物,PEEK 提供了初级结构所需的高机械性能,而无定形 PEI 层为粘合提供了快速、简单的熔化。 “我们控制材料沿压板的压力和冷却,从压机开始时的约 400 摄氏度开始到压机结束时低于 200 摄氏度。结果是一种材料是三个输入层的组合。”
这种新型热塑性胶带在制造过程中已经固化,因此在 AFP 过程中,只需将其加热以熔化和压实 PEI 层即可实现非晶粘合。结果是一个层压板,包括完全固结的 PEEK 到 PEI 胶带和 PEI 到 PEI 层,如 Leonardo 专利所示。与当前使用 PEEK 和 PEKK(聚醚醚酮)胶带的 AFP ISC 相比,这种 AFP 工艺的障碍更少。正如我 2018 年关于原位固结的专题的第 2 部分所述,当前的 AFP ISC 需要将胶带和基材加热至熔化温度,将胶带放置在基材上,然后用滚筒固结,以便精确控制冷却过程,从而实现半结晶聚合物以达到足够高的结晶度 (30-40%) 和低空隙 (<3-5%) 的结构特性。
AFP ISC 的批评者声称它太慢了——60-100 毫米/秒的沉积速率,而“两步”方法的沉积速率为 600-700 毫米/秒,包括快速 AFP 铺层,然后在烤箱或高压釜中进行第二步以完全巩固/退火层压板中的热应力。 “使用我们的材料,您可以获得不像典型的原位固结那么慢的 AFP 沉积速率,并且 AFP 期间所需的加热也可以保持在 300 摄氏度以下,”Barile 说。 “您可以使用我们现在拥有的标准材料缩小性能差距。”在这里,Barile 将热塑性复合材料的 AFP ISC 与波音 787 和空客 A350 飞机中使用的热固性复合材料进行比较。 “对于机身部分等大型部件,问题在于使用高压釜固化时的可负担性。热塑性塑料可以实现更实惠的生产过程,但使用目前市场上可用的航空级材料,您会遇到高温和 AFP 速度慢的问题。我们的方法有助于解决这些问题。通过连续压机,我们可以在胶带中达到约 30% 的结晶度。因此,您在零件中具有这种结晶度,并且仅在 AFP 期间使用非晶层。尽管这仍然是一种可以改进的实验材料,但 NHYTE 项目的目标是拥有一种可用于结构航空航天应用的一步式制造工艺。”
磁带和 AFP 优化
“第一批多层胶带材料是在 Novotech 中制造的,”Barile 说。这些胶带使用 Sabic(沙特阿拉伯利雅得)的 Ultem 1000 未填充切膜用于 PEI 和来自 Solvay 的 APC-2/AS4 碳纤维增强 PEEK 胶带。总厚度约为 0.26 毫米,包括 1 或 2 密耳(0.001 或 0.002 英寸)厚的 PEI 层。在项目的第一阶段,测试了两种变体的多个试样的层间剪切强度 (ILSS),以验证混合热塑性材料的制造过程。 NHYTE 合作伙伴 Applus Laboratories(西班牙巴塞罗那)还对小试样进行了全方位机械性能测试,包括拉伸和压缩强度和模量、裸眼压缩 (OHC)、填充孔张力、冲击后压缩 (CAI),几乎不可见流体调节后的冲击损伤 (BVID) 和性能。
“我们没有与热塑性复合胶带供应商相同的经验,因此可以提高材料质量。例如,纤维体积在整个厚度范围内从低到高变化,这会影响胶带和层压板的特性,包括 ILSS。但 NHYTE 旨在展示我们已经完成的概念。”
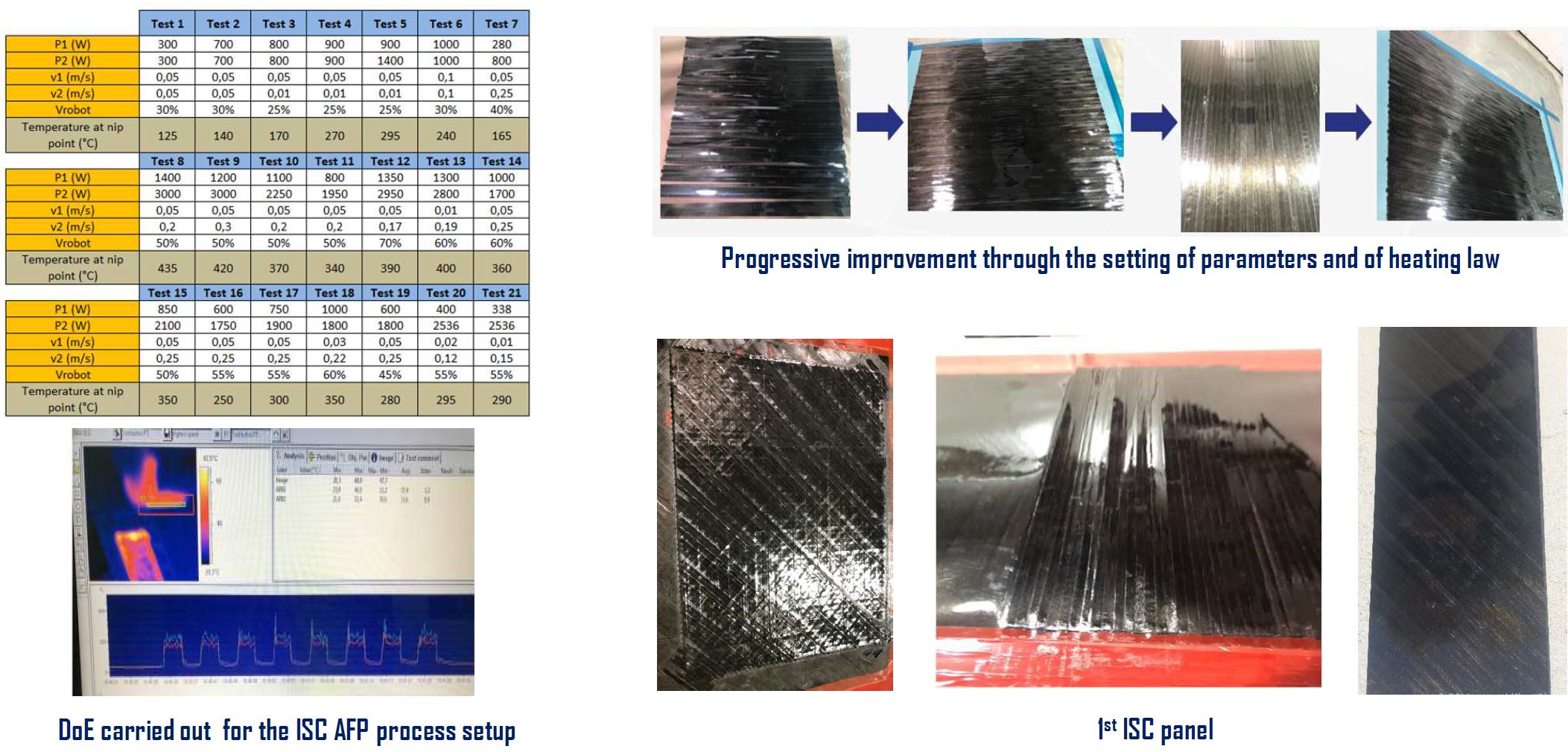
如上图所示,优化新材料的 AFP 工艺需要大量的实验工作。 “我们还使用实验设计 (DOE) 方法来优化 AFP 参数,并且 NHYTE 合作伙伴南布列塔尼大学(USB,洛里昂,法国)开发了一种工具,通过预测性数值模拟来改善激光加热负载。”巴里尔笔记。
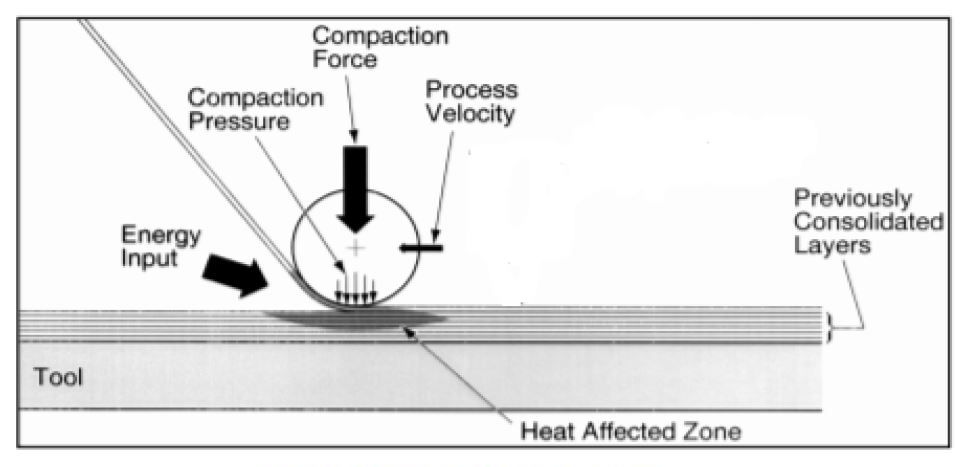
该模拟首先用于 APC-2 胶带以验证预测工具的质量,然后将其应用于新的多层材料。一篇关于这项工作的论文已提交在Composite Structures期刊上发表 . “您正在模拟咬合点的热导率,”Barile 说。 “然后我们通过实验验证了数值模拟中的预测。这需要确定沉积速度、聚合物的熔体流动和复合层板的老化 [蒸煮] 之间的最佳折衷。这是原位固结过程中几个变量的平衡。我们观察进入的胶带在已经放置在工具上的胶带上的温度降低。如果您可以控制这种温度变化,就可以降低层压板中的残余应力。因此,我们致力于评估铺设期间的温度变化。您必须根据路径的形状和薄片的方向自定义加热。
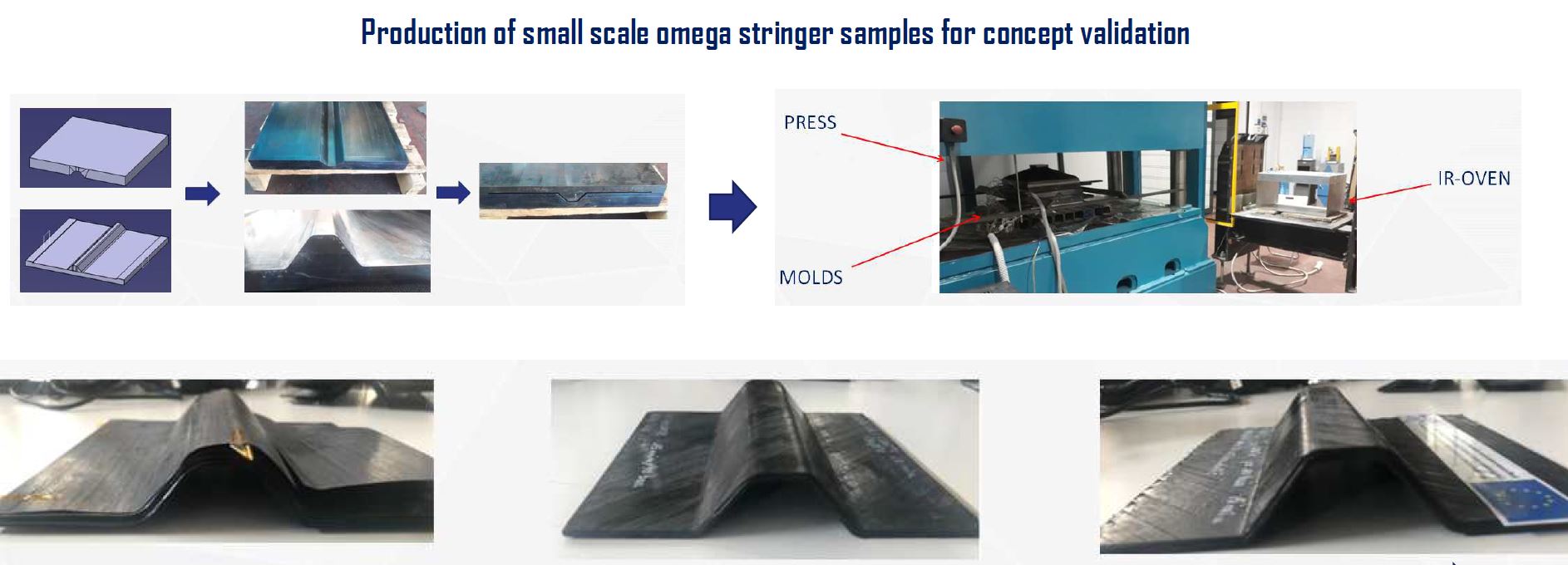
纵梁和机身演示
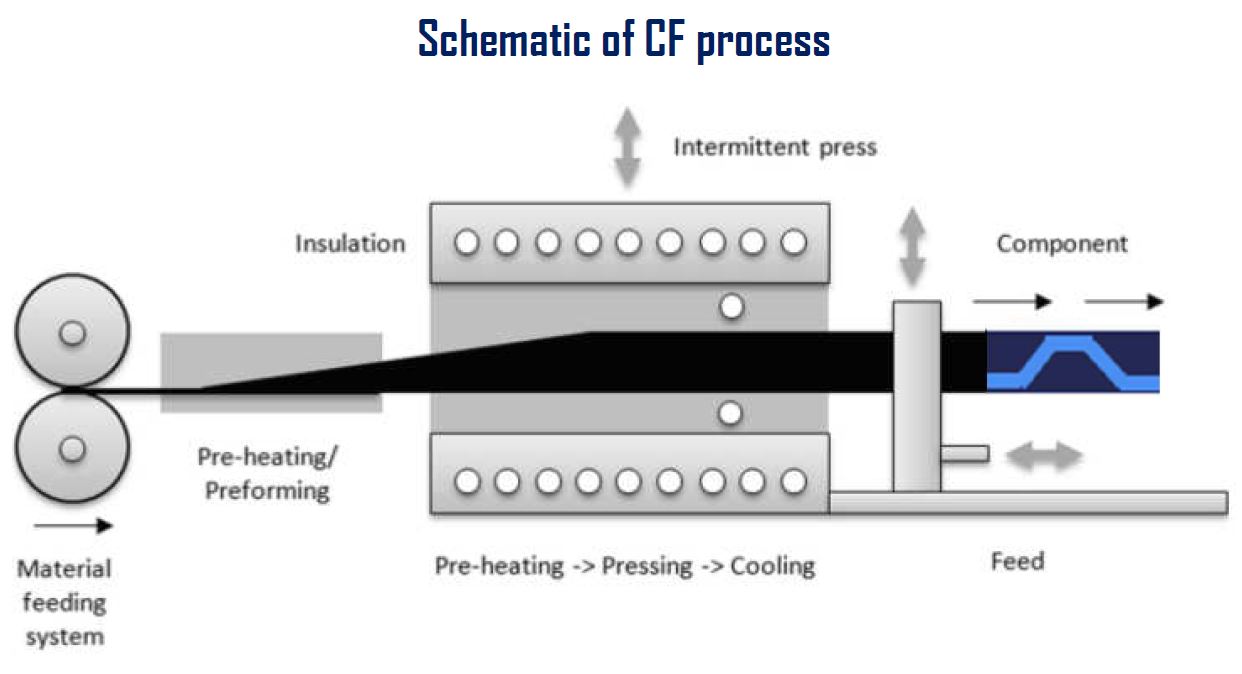
下一步是生产纵梁演示器,首先是用固定压力机制作的小规模样品,然后作为连续纵梁成型工艺的演示器,以验证工业零件生产所需的条件。然后使用研发组织 CETMA(意大利布林迪西)开发的感应焊接将这些纵梁连接到 AFP 机身蒙皮演示器上。
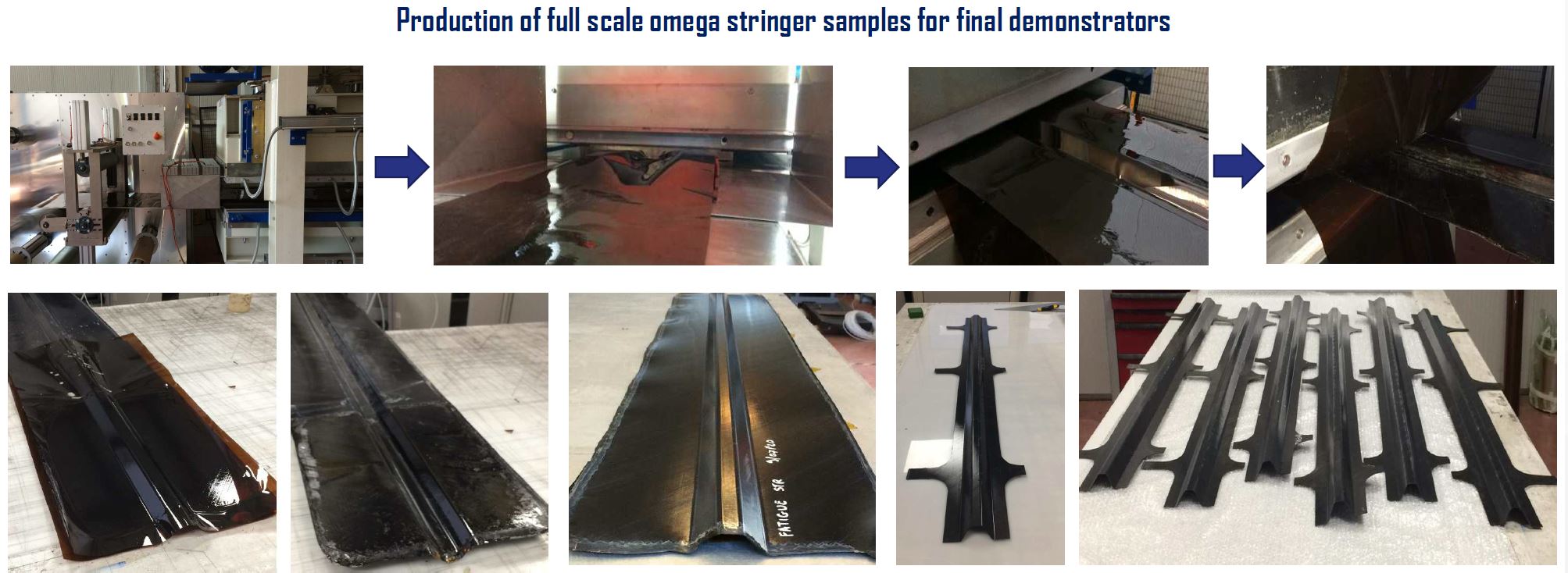
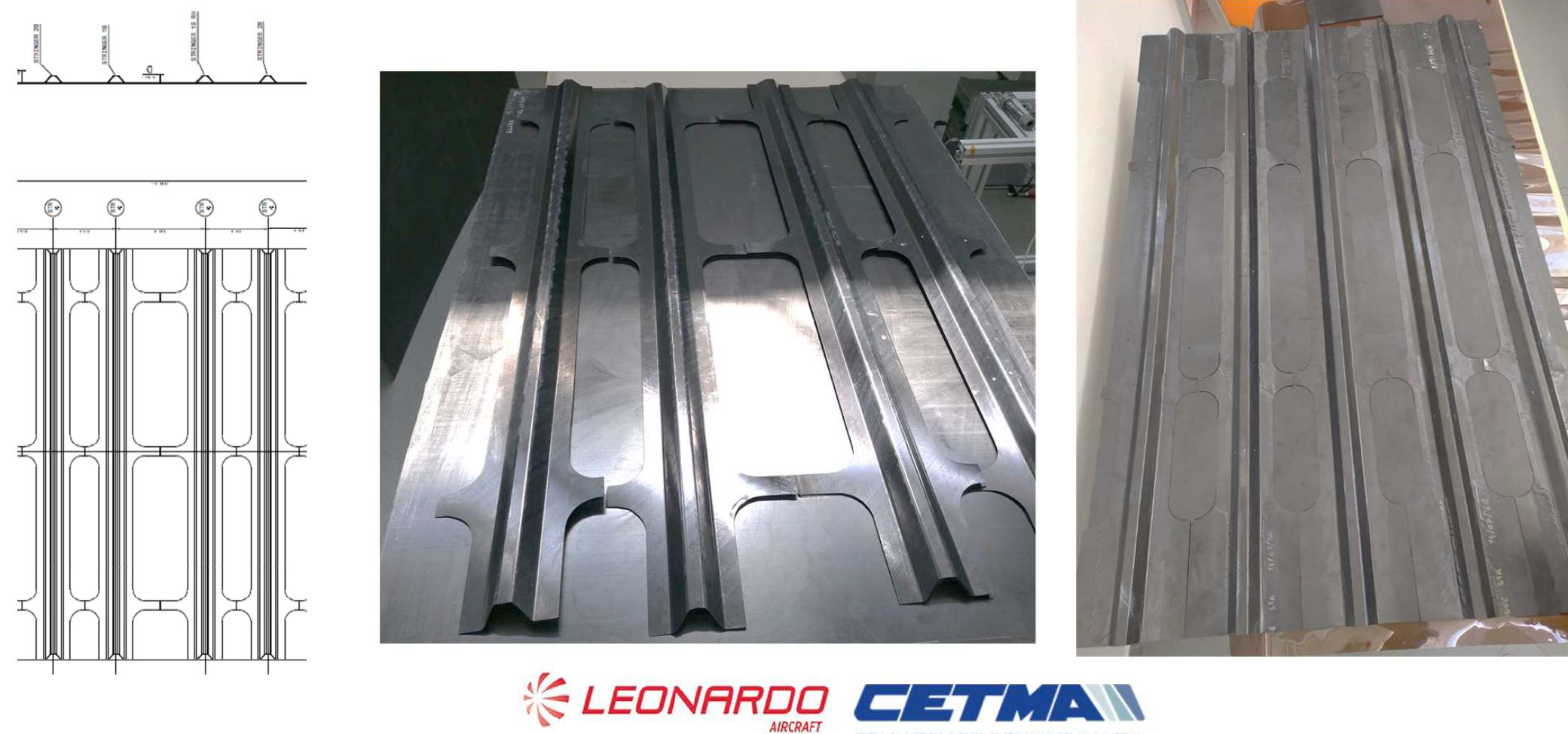
新的多层材料是否为感应焊接提供了任何优势? “它的处理方式基本相同,”Barile 说。 “然而,CETMA 定义焊接工艺参数并不容易,因为与标准胶带相比,我们的新材料的碳纤维含量更少。”随后,Applus 对纵梁演示器和最终机身面板演示器进行了测试。 NHYTE 项目合作伙伴巴斯大学(英国巴斯)和 Leonardo Aircraft 也使用 NDI 来评估面板和纵梁的质量。
“我们制作了很多优惠券和小零件,以及大型演示器,”Barile 指出。 “考虑到与现在的标准相比,制造过程的成本更低,Applu 的测试结果非常好。与目前可用的标准热塑性胶带材料相比,我们的强度和刚度特性降低了 20-25%,但我们已经确定对工艺的改进应该有助于改善这一点。”
NHYTE 于 2020 年 10 月 30 日结束。“我们的想法是继续进行一个新项目,以包括我们想到的所有改进,”Barile 说。 “我们已经证明了如何使用 AFP 原位固结、连续成型和感应焊接来制造材料以及如何加工。现在我们需要进一步优化以实现产业化。” Novotech 正在寻求与拥有新合作伙伴的同一个财团合作。
值得注意的是,Leonardo 还致力于使用感应焊接和可快速加热和冷却的 TPC 胶带改善 AFP 原位固结。此外,IMDEA 材料研究所(西班牙马德里)和 FIDAMC(西班牙马德里)的研究人员刚刚发表了关于 PEI/PEEK 多层复合材料的令人鼓舞的结果,后者多年来一直是 AFP 原位整合的领导者。如需更多技术论文,请参阅 NHYTE 的出版物。
SWING 项目
新通用航空智能机翼 (SWING) 是一个由 Piaggio Aerospace(意大利维拉诺瓦 d’Albenga)认可并由意大利经济发展部 (MISE) 共同资助的项目。除 Novotech 外,意大利项目财团还包括作为协调员的技术开发公司 Protom(那不勒斯)、Laer Aeronautical Manufacturing(Airola)、A. Abete Aerostructures(Nola)和航空航天设计专家 ItalSystem(Avellino)。 SWING 的目标之一是采用 Piaggio 的 P.180 Avanti 来适应自动化的非高压釜 (OOA) 复合材料工艺,包括 AFP 和液体树脂灌注 (LRI),以实现经济高效和可持续的小型飞机生产em> 前翼作为示范平台。
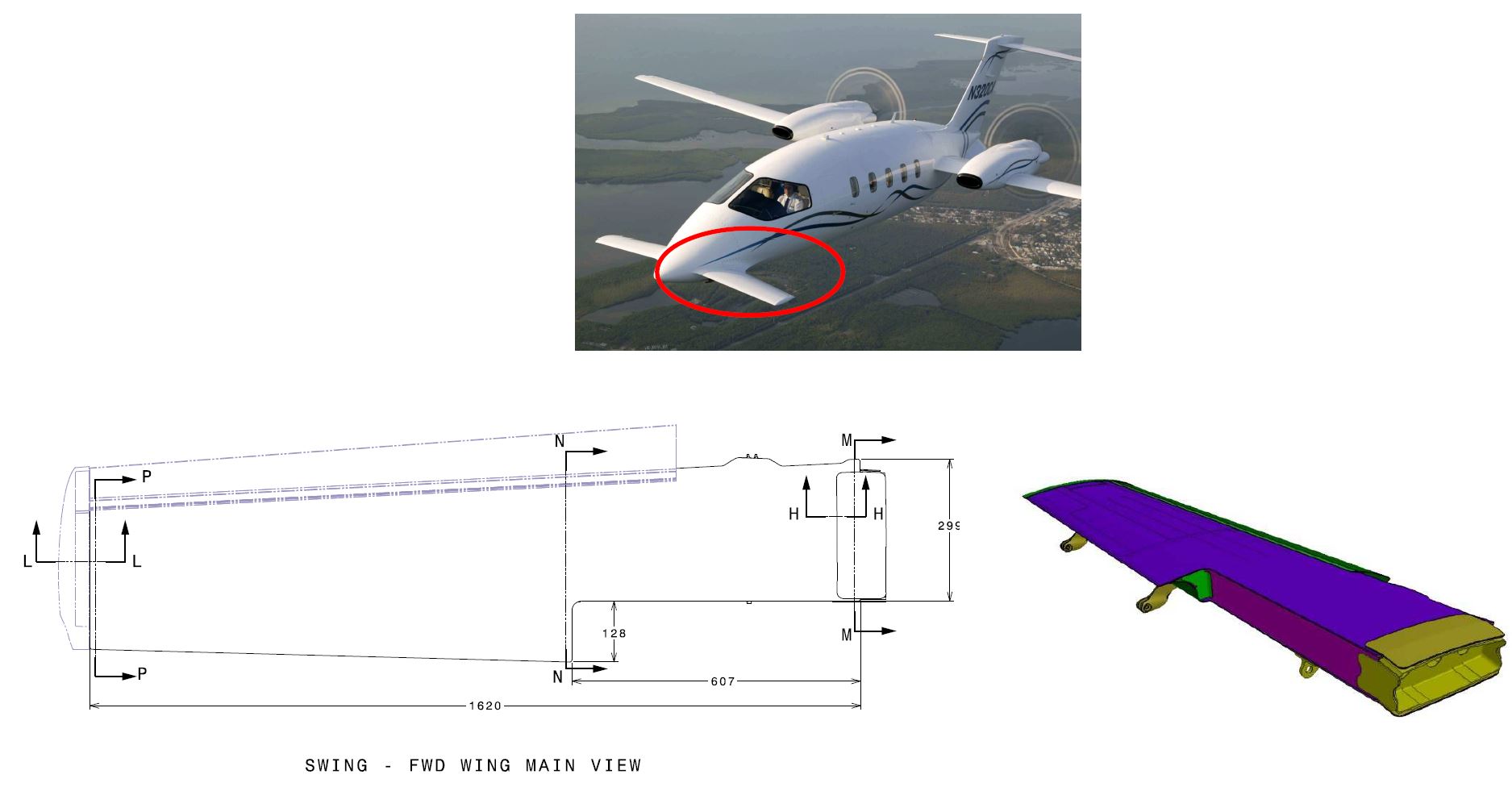
“我们的想法是将 P.180 的前翼制造成两个主要部分:一个上面板和一个下面板,两者都用集成的纵梁和翼梁模制而成,”Lecce 说。
“对我们来说,这始于我们作为英国索尔维合格实验室的工作。自 2015 年以来,我们一直在 AFP、LRI 和热塑性复合材料的新材料和新工艺方面进行合作。我们使用 Solvay 的 PRISM TX1100 干纤维胶带制造干预成型件,用于 AFP。然后将这些预成型件注入 Solvay PRISM EP 2400 增韧环氧树脂并在烘箱中固化。我们在清洁天空 2 绿色支线飞机项目的 AIRGREEN 2 项目框架内进行这项工作,然后继续推进 SWING 项目。”请注意,PRISM TX1100 和 PRISM EP 2400 已获得联合飞机公司的认证,可用于生产第一款用于商用飞机的树脂灌注机翼 - AeroComposit 制造的 Irkut MS-21 单通道喷气客机。
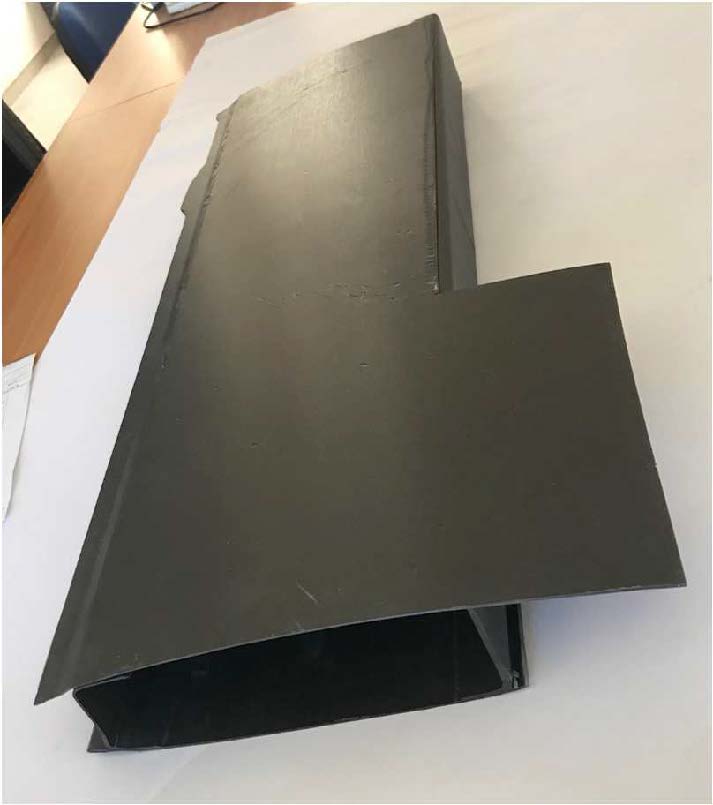
模制的上下面板将使用结构粘合剂连接起来,然后在明年进行静态测试。 “与此同时,我们正在表征另一种基于 TX1100 干胶带和 Covestro(德国勒沃库森)的树脂混合物的复合材料,它可以作为航空级树脂的有效替代品,特别是对于需要更高生产率的行业,”Barile 补充道。 “这种树脂的性能不如那些系统,但它可以很好地进行灌注并满足机翼盒的要求。如果你想降低成本,就必须有一些妥协。我们希望这一发展有助于将 AFP 技术引入通用航空。它还可以用于汽车领域。”
TRINITI
Novotech 还参与了 Clean Sky 2 项目 TRINITI——飞机用多材料热塑性高压氮气罐——该项目于 2019 年启动,将于 2021 年结束。 Novotech 进入该项目再次源于与一家意大利航空航天公司的开发。 “我们正在努力验证使用我们的多层胶带生产运载火箭低温燃料箱与当前使用的纤维缠绕工艺相比 AFP 的潜力,”Barile 解释说。 “本质上,TRINITI 将开发类似于 NHYTE 的多层材料概念,然后使用 AFP 原位固结制造储罐。”
“相对于 FW,AFP 的优势在于,”他继续说,“您可以决定将材料放置在哪里。您不会受到围绕零件连续缠绕的细丝的限制。考虑一个在端盖处有很多材料的罐,因为在纤维缠绕过程中无法切割材料。通过使用 AFP 在需要的地方切割和重新启动光纤/胶带,材料仅在需要的地方使用。因此,您可以管理胶带之间的间隙,这对于防止气体渗透很重要。要使用长丝缠绕来做到这一点,您必须增加应用的材料,即使因为使用 AFP 时您使用的是切割胶带,而不是丝束。然后通过原位固结,不需要高压釜。我们已经证明 AFP 可能是一种可行的替代方案,而且价格非常实惠。”
“目前,CETMA 正在进行气体渗透测试,以评估多层材料的性能与规格的对比,”Barile 说。主题经理 Diehl Aviation(德国吉尔兴和德累斯顿)提出了用于飞机灭火系统的高压长存储氮气罐的要求。这些储罐必须能够承受地面 -55°C 至 85°C 的温度、飞行操作期间 -40°C 至 70°C 的温度以及高达 1,000 bar 的压力。
“目标是减少重量和制造步骤,”他指出。 “但是,必须定义使用这种方法的制造成本。通过不放置不必要的材料来减轻重量,但与 AFP 相比,纤维缠绕是一个更快的过程。”另一个因素是这种类型的罐通常有一个金属或塑料衬里,外包装有 CFRP。 Barile 说 TRINITI 正在尝试一种无衬里(V 型)坦克。 “我们将通过使用低空隙 AFP 层压板来避免气体渗透。我们现在正在 CETMA 测试不同的材料组合并准备向下选择。然后我们将建造一个原型坦克,但坦克的设计取决于向下选择的材料和最终工艺。所以,这就是我们现在正在努力的方向。测试活动将由 CTL Composites(爱尔兰戈尔韦)进行。”
海鸥
具有挑战性的海鸥项目始于三年前。 “我们的目标是开发新一代小型水上飞机,采用我们开发并获得专利的新型复合材料制造技术、混合电力推进和自动折叠机翼,”Lecce 解释道。 “其目的是设计一种短距起降 (STOL) 飞机,与垂直起降 (VTOL) 飞机相比具有竞争力,但价格更实惠。我们相信这可能是一架从任何表面操作的个人飞机,是未来航空和机动性的重要可能性。”
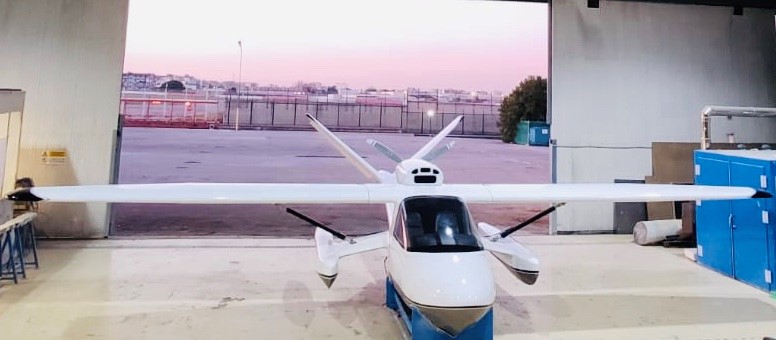
海鸥团队测试了混合动力推进系统,建造了第一个水中原型,并于 10 月开始进行水中测试。 “测试完成后,我们将在几个月内建造一个飞行原型,”莱切说。 “这是一支非常有经验的团队,由在通用航空领域拥有 50 多年经验的重要公司组成。”
海鸥飞行原型机将采用复合材料机身、尾翼和机翼。 “我们将再次推动使用 AFP 和树脂灌注的自动化制造应用,”Barile 说。 “使用这些工艺的复合材料的主要问题之一是材料成本。事实上,我们正在努力做的是找到一种在成本方面更加民主的材料和过程的组合。”
树脂
- Fraunhofer IPT 开发用于储氢、发动机叶片等的热塑性复合材料
- Composites Evolution 展示高性能预浸料、新型热塑性 UD 胶带
- 设计用于小批量航空结构的自动化复合材料制造
- 热塑性胶带继续显示出复合航空结构的潜力
- 用于复合材料的可再加工、可修复和可回收的环氧树脂
- 结合 AC 和 DC 介电测量以监测复合材料的固化情况
- 索尔维与莱昂纳多启动热塑性复合材料联合研究实验室
- 卡尔迈耶推出热塑性 UD 胶带生产线
- SWM 推出用于树脂灌注的 Naltex 流动介质
- 热塑性门是汽车复合材料的首创
- 热塑性复合材料联盟旨在为汽车和航空航天进行大批量生产
- 服务于以色列和美国的复合材料世界