后壁重启:一站式,拖到胶带到 CFRP 部件
在碳纤维复合材料目前进入汽车应用的初期,制造商宝马集团(德国慕尼黑)似乎脱颖而出。加速树脂传递模塑 (RTM) 以生产其 M 的初步工作 运动模型的车顶在其 i3 上建立了碳纤维增强塑料 (CFRP) 零件的完整供应链 和 i8 车辆,然后是其 7 系列上的多材料碳芯白车身 (BIW) 的全新制造和组装工作单元 .
宝马致力于 i3 2009 年大张旗鼓,但同年,奥迪股份公司(德国英戈尔施塔特)成立了一个专门研究纤维增强塑料的技术中心。 2011 年,奥迪宣布与福伊特复合材料公司(德国加兴)建立合作伙伴关系,以大批量开发和生产 CFRP 零件。第二年,它宣传了使用树脂传递模塑 (RTM) 制成的 CFRP 增强钢 B 柱的开发,和 与 SOGEFI(法国圭扬库尔)合作,将复合螺旋悬架弹簧商业化。 2012年,奥迪还担任了MAI Carbon前沿集群的创始合作伙伴,其中包括宝马、福伊特复合材料、西格里集团(德国威斯巴登)等。
最值得注意的是,奥迪自己对 CFRP 开发的叙述始于其第一代 R8 2006 年发布的跑车。它的特点是敞篷车顶的隔间盖以及树脂传递模塑 (RTM) 制成的侧翼。公司从美观的外观和更小的结构发展到奥迪 R8 e-tron 中的模块化跑车系统 (MSS) .尽管这辆电动超级跑车的主要结构包括由铝铸件连接的挤压铝梁,但所有面板和填充物都是 CFRP,包括带有波纹防撞结构的行李箱插入件,使后部模块吸收的能量是金属框架的五倍.
MSS 的支柱是它的后墙 ,它从 2011 年的初始概念演变为目前为非电动 R8 生产的模块 由 SGL Technologies(原 BENTELER-SGL,Ort im Innkreis,奥地利;参见“工厂参观:BENTELER SGL”)。但奥迪已经在计划下一步:迭代后壁以用于其更大容量的A8 豪华轿车,福伊特复合材料作为其制造合作伙伴。
Voith Composites 是跨国公司 Voith GmbH &Co. KGaA 的 10 年子公司,成立于 1867 年。母公司现在拥有 19,000 名员工,年收入为 42 亿欧元(52 亿美元),并通过以下方式提供制造设备和技术四个部门:Voith Digital Solutions、Voith Hydro、Voith Paper 和 Voith Turbo。 Voith Composites 从生产用于造纸的 CFRP 辊发展到制造汽车和工业 CFRP 传动轴/万向轴和平面层压板。
2011 年,福伊特复合材料开始开发高度自动化的 CFRP 工艺链,旨在生产 A8 后墙。其核心是 Voith Roving Applicator (VRA),它在一条线上将来自 Zoltek(美国密苏里州圣路易斯)的 35K 碳纤维丝束铺成粘合单向 (UD) 胶带,然后切割并堆叠成形成一个定制的空白。 VRA 于 2017 年获得了 JEC 创新奖。它还为后续的预成型和成型操作奠定了坚实的基础。福伊特复合材料和奥迪在 2018 年 JEC World 上再次获得汽车类最高荣誉,用于制造奥迪 A8 的基于 VRA 的数字 4.0 生产线完成 后壁模块。通过与树脂供应商陶氏汽车(美国密歇根州奥本山市)和 Zoltek 合作,这些合作伙伴不仅开发了以高产量生产高性能 CFRP 零件所需的材料、工艺和集成在线检测系统,而且还创造了完整的一套基本的计算机辅助设计/制造 (CAD/CAM) 和模拟工具,这些工具已经被用于开发未来的零件。
效率驱动的设计演变
“我们很早就开始与奥迪合作,”福伊特复合材料业务发展主管 Jaromir Ufer 博士说。首要任务是开发新的A8 后壁设计,这将指导零件的制造方式。
“当我们开始此生产的工程设计时,我们找不到具备我们所需一切的现成 [软件] 产品,”Ufer 解释说。 “所以我们将 ABAQUS 等设计工具整合在一起,但构建了我们自己的材料卡并开发了我们自己的模拟方法。”奥迪已经将减轻 BIW 重量和增加扭转刚度确定为 R8 的主要目标 后壁设计(参见“奥迪 R8 座椅壁:量产前奏”)。对于 A8 模块,提出了一个整体设计,以减少多组件MSS 用少量粘合和铆接附件组装到单个成型的 CFRP 面板上。这种设计推动了具有局部载荷路径的高度各向异性层压板的开发,与三到五个焊接铝部件的组件相比,该设计使成品部件能够在 50% 的重量下提供驱动单元 33% 的扭转刚度。
“用于奥迪 A8 的复合预成型坯 后墙板从 6 层到 19 层不等,其中添加了局部加固——例如,有切口或点载荷的地方,例如儿童提篮约束装置,“Ufer 解释说(图 2)。
福伊特粗纱涂布机
Ufer 指出,此设计和 VRA 的开发是同步进行的。 “只有拥有 VRA 提供的设计自由度,新的 A8 后墙可能。”同样重要的是,纤维供应商 Zoltek 对该计划做出了为期 7 年的价格承诺。
VRA 的流程始于 Zoltek 的 PX 35 碳纤维筒子架。多个 50K 丝束线轴被送入每条 VRA 生产线并展开以生产 50 毫米宽的胶带。接下来,在复合材料部件的树脂传递模塑 (RTM) 过程中,应用一种环氧基粘合剂,该粘合剂随后会与陶氏 VORAFORCE 快速固化环氧树脂基体树脂发生反应。施加少量红外线 (IR) 热量使粘合剂熔化,足以通过随后的固结、切割和堆叠步骤将胶带固定在一起(步骤 1)。
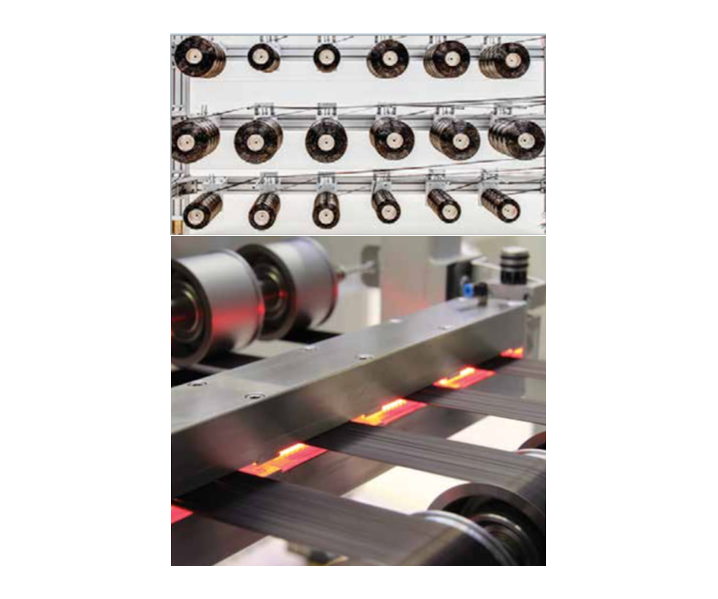
第一步:乙> Zoltek 50K 碳纤维丝束被送入 Voith Roving Applicator (VRA),首先在那里铺展,然后涂上环氧基粘合剂,然后通过红外加热使粘合剂部分熔化。
“这是一个完全自动化的连续过程,”Ufer 说。 “如果由于某种原因需要停止生产线,设备会自动做出反应。例如,IR 加热器会立即关闭并缩回,以防止因过热而损坏磁带。设备中有数百个这样的细节,数字控制使这项技术成为可能。”
第 2 步: 展开的牵引带随后在张力作用下通过多个滚筒时被加固。
使用粘合剂后,胶带在张力作用下通过多个辊时实现固结(步骤 2)。 Ufer 解释说,这也为线路建立了一个缓冲区。 “我们有一个单元可以中断光纤的连续拉动流,提供向带切割和放置机制的脉冲格式的过渡。”这种基于机架的机制 将胶带切割成定制长度,并将它们以 0-360° 的指定角度放置在旋转台上(步骤 3)。每个定制的叠层包括 6 至 19 层胶带,厚度分别为 1.5 至 3.7 毫米。
第 3 步: 然后 VRA 切割胶带,一次最多将四片放在旋转台上,调整层压堆叠内的胶带长度和方向角度(例如,45°/90°/30°)。
福伊特安装了 4 条 VRA 生产线(见开场照片),尽管每条生产线一次最多贴 4 条 50 毫米宽的胶带,但 Ufer 指出,“这些生产线采用模块化方法,因此他们可以一次贴上 10 条或更多条胶带。时间。这取决于零件尺寸和生产率。”
自动化包括质量检查。磁带和预制件的扫描与拒绝算法进行比较。 “VRA 对胶带的 100% 扫描确保了整个生产线的正确纤维分布,”Ufer 解释说。 “我们还使用热成像和激光传感器来检查指定区域的瓶坯。”然后 VRA 可以对它检测到的任何问题做出反应。 “如果一个磁带不正确,”他指出,“VRA 将剪掉不足的长度并生产另一个来替换它。”二维码放置在成品瓶坯上以进行追溯。 (QR 码比射频识别 (RFID) 标签更受欢迎,因为据报道它们能更好地承受树脂注射过程。)
成型、成型和组装
二维堆栈离开 VRA 并穿梭到生产线的成型、成型和装配部分。由复合材料自动化专家 FILL(奥地利 Gurten)提供的第一台压机使用热量和压力将 2D 胶带堆叠成型为 3D 预制件(步骤 4)。 Ufer 解释说,由于预成型件的厚度和形状各不相同,因此压机可以适应施加的压力,因为它可以冲压成型夹紧在成型工具中的预成型件的单独区域。 ALPEX Technologies(奥地利 Mils bei Hall)根据福伊特复合材料公司提供的设计制造了匹配钢 RTM 模具。 “我们虚拟地开发了模具和冲压工艺,”Ufer 说。 “虽然不需要实际的测试循环,但我们确实在加工 A8 之前验证和验证了其他形状和零件的仿真模型 后壁生产工具。这种模塑过程的模拟直接用于实际生产,并有助于加速优化。”
步骤 4 :胶带堆被传送到压力机中,在那里形成最终的 3D 零件形状。
压机保持几秒钟,使粉末粘合剂发生反应并固定形状,从而形成稳定的预制件,可以在树脂注射过程中抵抗纤维清洗。 “粘合剂颗粒还起到保持纤维分离的作用,以改善 RTM 期间的树脂流动,”Ufer 指出。 “这很有帮助,因为在预制件中没有缝合以帮助树脂流动,因此这些粘合剂颗粒充当微流道。”
成型的预制件接下来由机器人转移到 EiMa Maschinenbau GmbH(德国弗里肯豪森)的 CNC 单元中,在那里超声波刀修剪外部最终轮廓。然后将其自动放入由 ENGEL(施韦特贝格,奥地利)提供的 RTM 压机中(步骤 5)。生产线上的所有机器人均由KUKA Robotics(德国奥格斯堡)提供。
第 5 步: 将成型的预成型坯放入 350 kN 的压力机中并使用超 RTM 成型。
用于模制 A8 的 RTM 工艺 后壁与奥迪轻量化中心为之前的 R8 开发的相同 后壁,简称超RTM。它可以使用快速注射但低压成型大型零件。与典型的 HP-RTM 140 bar 相比,Audi A8 超 RTM 期间的模内树脂注射压力 后壁 <15 bar,甚至低于 R8 .因此,只需 350 kN,而不是 2,500 kN 的压力。因此,可以使用更小、更便宜的压机来生产高质量、高纤维量的零件。
VORAFORCE 5300 环氧树脂是一种包含脱模剂的三组分体系,在 120°C 下可在 90-120 秒内固化,加工粘度为 20 cps。对于 A8 后壁,将 1.3 公斤的树脂注射到预制件中,然后固化 120 秒。
固化的零件通过机器人脱模并装入封闭的 CNC 铣削单元中,用于加工切口。接下来,将铣削的零件放入自动洗衣机中,以清除残留的 CFRP 灰尘。
清洗后的后壁被转移到配备两个机器人的组装单元中。第一个机器人将模制零件放入自动铆接机中,记录铆钉安装过程中施加的力。这是整个流程中内置的制造智能的一部分,并添加到每个部分的数字处理记录(即数字线程)中。 然后将零件移动到粘合区域,第二个机器人使用自动溶剂擦拭准备粘合区域。然后,同一个机器人应用快速固化的双组分陶氏 BETAFORCE 9050M 聚氨酯结构粘合剂(步骤 6),该粘合剂与三组分环氧树脂兼容。接下来将部件放入烘箱中进行较短的粘合剂固化周期。
第 6 步: BETAFORCE 聚氨酯胶粘剂以机器人方式应用于粘合附件,然后在较短的烘箱周期内固化。
该生产线为完成的零件保持 5 分钟的周期时间,并且可以在一到两个 8 小时的班次中满足当前对零件的需求。定期使用 3D 激光扫描设备检查零件的 3D 形状和测量值。然后准备好成品部件运往奥迪 A8 位于德国 Neckersalm 的总装线,车程约 3 小时(第 7 步)。
第 7 步: 完成的零件然后准备运送到奥迪 A8 总装线。
直接纤维铺放 =未来的灵活性
凭借已进行的所有投资,令人惊讶的是,福伊特复合材料公司对这项业务并不放心,但该公司确实完成了开发,然后参与了竞争性投标过程以赢得生产。 “我们能够满足奥迪定义的目标零件成本以及质量和零件性能要求,”Ufer 说。考虑到相当多的公司都在争夺该计划,这绝非易事。
Voith Composites 已为其工艺的多个部分申请了专利。 “VRA 已经展示了使用胶带直接纤维铺放 [DFP] 的工业化,通过高度优化的叠层减少了废料和材料,”Ufer 说。它还使用最具成本效益的材料——未经处理的重丝束纤维和粉末粘合剂。它的第二代工艺通过直接应用树脂取代了粉末粘合剂,从而消除了更多的工艺步骤。然而,该公司还开发了其他 DFP 工艺,包括福伊特长纤维预成型机和福伊特预浸料卷绕。
“我们正在为大批量汽车批量生产的碳纤维部件设定新标准,”福伊特复合材料公司总经理 Lars Herbeck 博士说。 “我们建立的智能工厂将 CFRP 组件的自动化生产提升到一个新的效率和灵活性水平,包括几乎任何形状以及单个批量。”这确实是该行业的发展方向。
树脂