使用此清单确保注塑成型设计可投入生产
注塑成型能够以较低的每个零件的价格大批量生产相同的零件。该过程包括通过加压喷嘴将熔融材料注入耐用的金属模具中,一旦材料凝固就弹出零件,然后重复。各种日常用品,包括水瓶、塑料玩具和电子产品外壳,都是用注塑成型制成的。虽然热塑性塑料和热固性塑料是注塑成型中最常用的材料,但金属也可以注塑成型。
当您使用注塑成型制造零件时,您需要考虑许多影响最终产品质量和功能的变量。注塑件出现故障的原因有很多——包括流线、缩痕和翘曲——但您可以通过遵循一些关键设计原则来避免大多数问题。
在 Fast Radius,我们每天与客户合作开发他们的注塑成型零件。工程师经常带着需要调整的优秀零件设计来找我们,然后才能有效地制作它们。我们的制造设计 (DFM) 专家评估和调整了数千个零件设计,他们确定并汇总了他们看到的最常见问题。修复设计中的这些常见错误可以防止代价高昂的错误并节省大量设计修改时间。
在您提交要注塑成型的零件设计之前,请根据以下设计规则列表对其进行检查:
使用适当的拔模角度
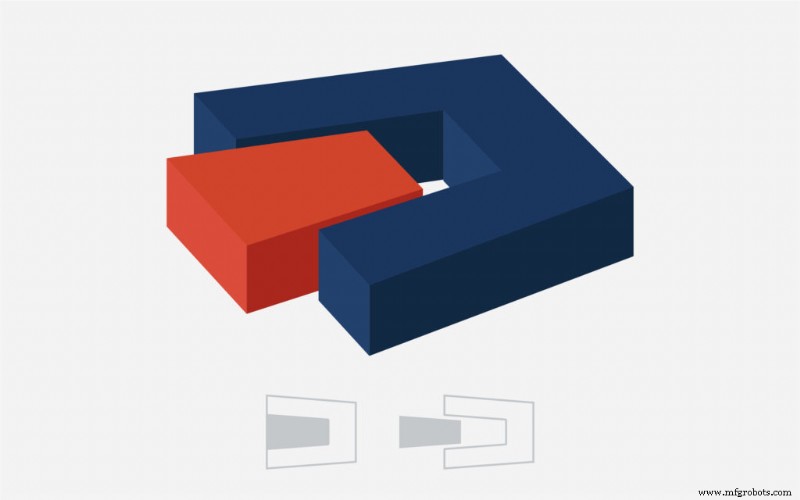
1.5-2 度的拔模量通常是大多数零件的安全最小值。
拔模斜度是指注塑件表面添加的与拉力方向一致的平缓锥度,使零件能够从模具中取出而不会因摩擦或吸力而损坏。
零件所需的拔模角度取决于几个因素,包括壁厚、零件材料的收缩率、拉伸深度以及零件在后期生产过程中是否需要表面处理或纹理处理。虽然零件深度每增加 1 英寸,平均拔模量应增加 1 度,但对于大多数零件而言,1.5-2 度的拔模量通常是安全的最小值。
尽可能保持壁厚均匀
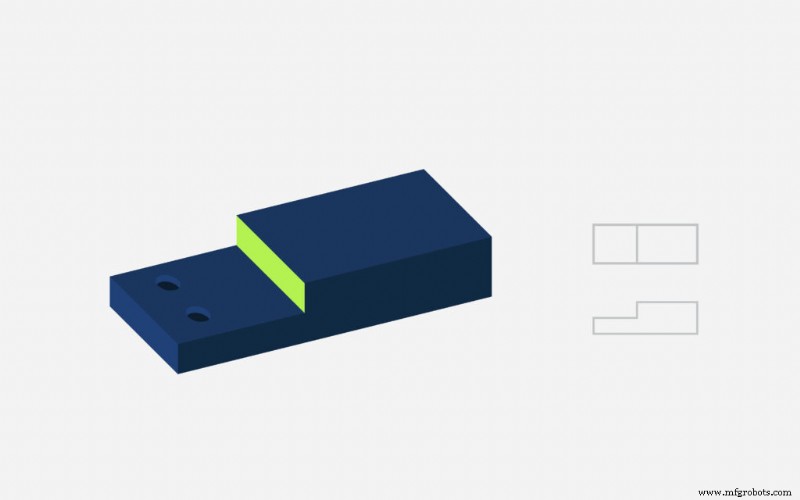
如果可能,注塑成型的部件应在整个零件上具有均匀的壁厚。壁厚的变化会导致注射材料以不同的速度冷却,从而导致缩痕、空隙和翘曲。
通常,1.2 毫米到 3 毫米之间的壁厚是理想的(尽管根据材料可能会有一些变化)。壁厚应几乎始终保持在 5 毫米以下,因为较厚的壁会增加生产周期时间,并且还可能对零件的机械性能产生负面影响。
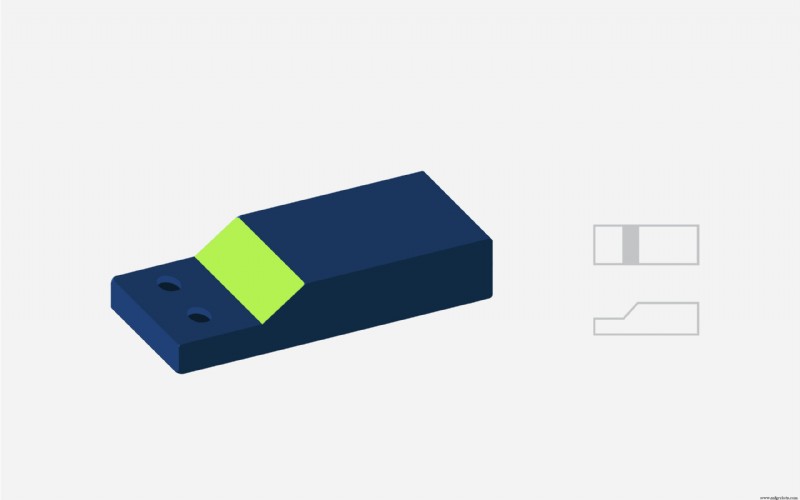
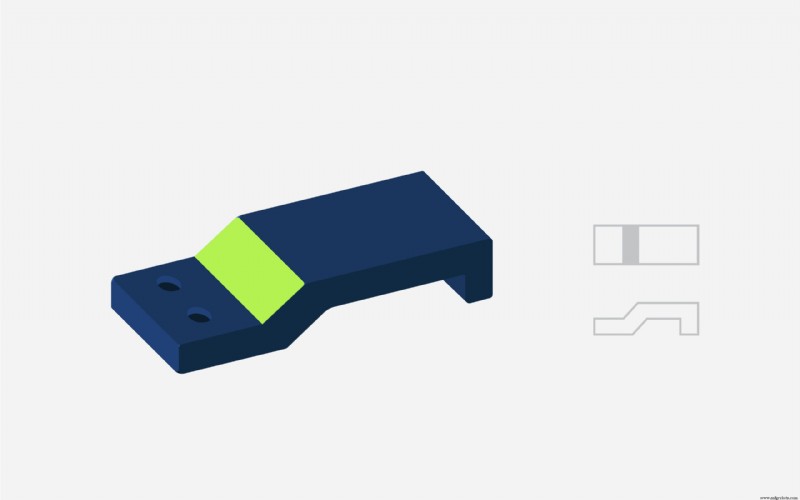
如果零件需要改变壁厚,则应使各部分之间的过渡尽可能渐变。您可以通过在零件设计中加入倒角(斜角或边缘)或圆角(圆角或边缘)来做到这一点,这有助于确保熔融塑料射束完全填充模具,彻底均匀冷却,并防止翘曲或不翘曲-均匀收缩。
一般来说,不同壁厚的截面之间的过渡长度应为壁厚变化的3倍(例如,如果壁厚减少1mm,则过渡应跨越3mm)。
避免倒扣
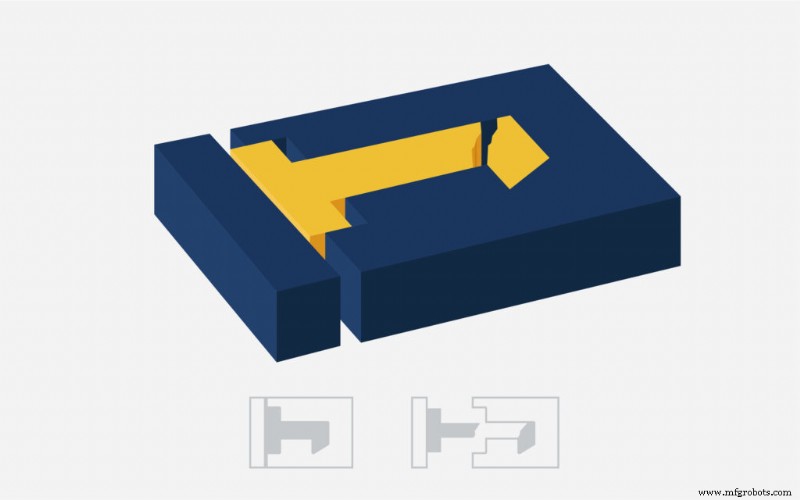
底切是凹入或悬垂的表面或特征——例如螺纹、凹槽或卡扣配合——可防止零件通过单向、单向拉力而不受损坏地从模具中弹出。可以通过将特征定向到与绘制线平行或将动作合并到模具设计中来避免底切。
修圆锐利的棱角
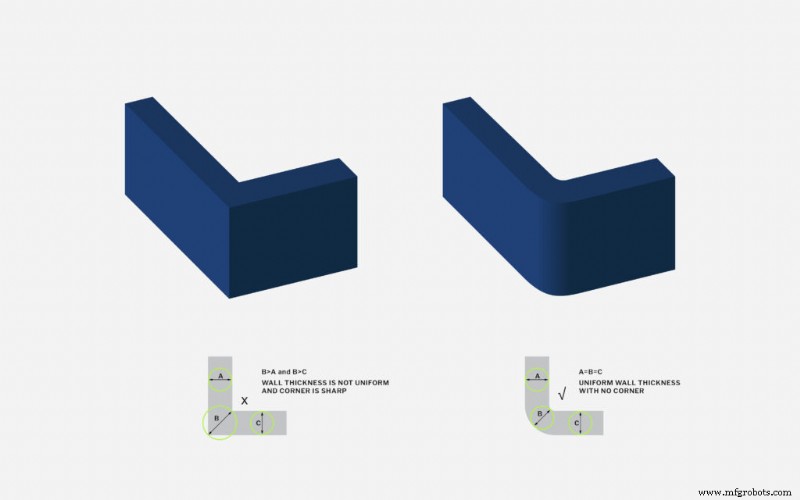
只要有可能,设计师和工程师应该选择圆形特征而不是尖锐的边缘和角落。边缘需要额外的压力来填充,这使得注射更难以有效且均匀地流入模具。在顶出过程中,锋利的边缘也容易粘在模具上,从而增加零件损坏和缺陷的风险。圆角内圆角和外圆角可以避免这两个问题。
内角或部分墙与地板相接的角的半径应至少为相邻墙厚的 50%。外角或零件壁顶部的角应具有相邻壁的 150% 的半径,以使塑料更有效地流动。这也有助于减少残余应力和开裂。
零件内所有垂直特征的底部(例如凸台、肋或卡扣配合)也必须是圆形的。凸台半径应为相邻墙的 25%,最小半径为 0.015”(或 0.381mm)。
战略性地定位分界线
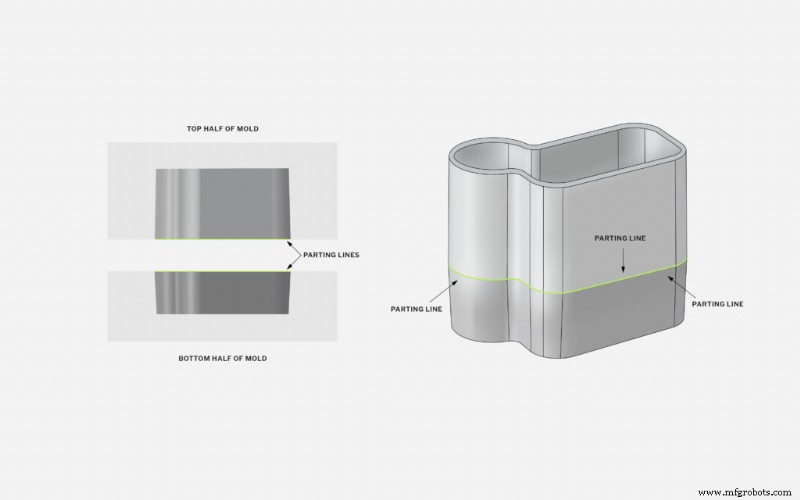
称为分型线的物理标记将出现在模具的两半相交处。在许多情况下,分型线很容易看到和感觉到,但这不仅仅是一个美学问题。分型线的位置决定了模具的打开方式(以及您需要向零件特征添加拔模的方向),它会影响模具工具的成本和任何所需的后处理。
您通常可以通过沿边缘而不是平坦表面放置分型来改善零件的外观和功能。这有助于隐藏接缝并减少飞边(模具聚集处周围材料过多)的机会。
考虑顶针位置
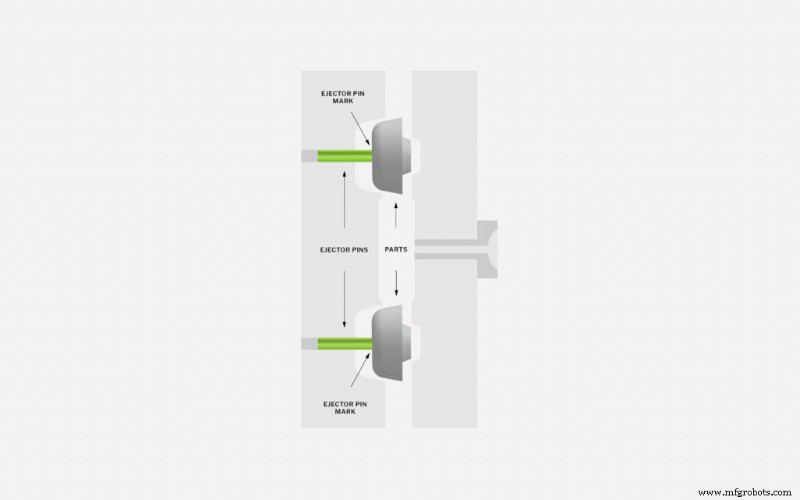
为了正常工作,顶针需要垂直于顶针运动方向放置的平面或垫。销钉的位置和数量应根据零件形状、拔模角度、侧壁纹理和壁深来确定——所有这些都会影响零件如何粘附在模具壁上。
材料选择也应考虑到引脚的位置或尺寸。例如,粘性较高的树脂往往需要更大的力才能弹出。同样,较软的塑料可能需要更多数量的销或更宽的销,以有效分配顶出力并避免损坏零件。
优化支撑肋尺寸
在两个部分墙以 90 度角相交的情况下,或者特定部分的长度被部分的壁厚削弱的情况下,肋通常用于加强部分墙。
需要注意的是,较厚的肋骨并不一定意味着更大的支撑力——事实上,太厚的肋骨通常会导致凹痕。支撑肋的基部厚度最多应为相邻墙体厚度的三分之二。
注意模具壁厚
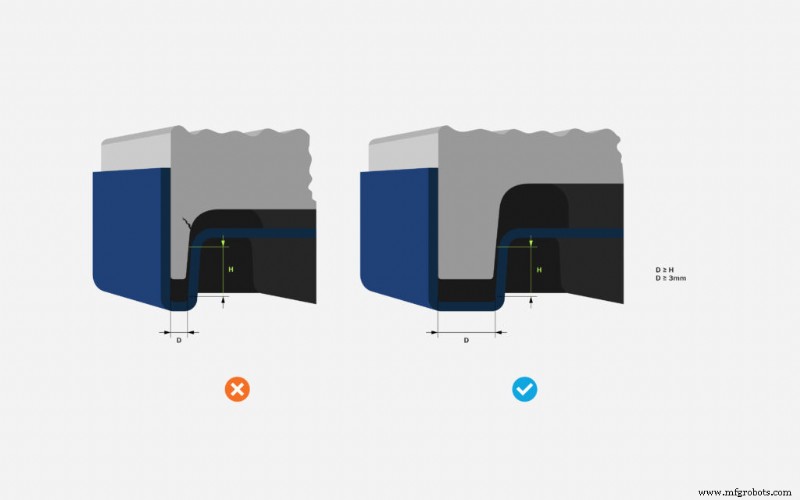
模具壁的厚度是另一个重要的考虑因素——主要取决于零件特征之间的空间。确保肋条和凸台等垂直特征彼此之间、零件壁或薄区域不要太靠近,因为这会使冷却过程复杂化。
模具壁厚也会影响模具成本。大多数注塑模具是通过 CNC 加工制造的,模具中较薄的金属壁更难正确加工。更薄的壁也会导致模具生命周期更短。
虽然允许的最小模具壁厚取决于零件材料的物理和机械质量,但零件特征之间 3mm 的间隙通常是可以接受的。
高效设计注塑成型零件
设计错误代价高昂。重新切割工具以修复设计错误可能会使产品团队延迟数周并花费数千美元。一个好的制造合作伙伴将帮助您避免使用 DFM 进行代价高昂的修改,但该过程也会增加您的时间线。在将设计提交给制造合作伙伴之前检查您的设计是否存在本指南中的问题,这将有助于您更快地获得更好的零件。
注塑成型中有很多事情可能会出错,因此您需要找到一个您可以信任的合作伙伴来正确处理您的零件。在 Fast Radius,我们在这里让您的事情变得更轻松,我们为您的项目的成功投资。立即联系我们,开始您的下一个注塑项目。
要了解有关注塑成型的更多信息——从材料选择到单腔和多腔模具之间的差异,再到我们如何利用该工艺制造抗击 COVID-19 传播的面罩——请访问 Fast Radius 学习中心.
准备好使用 Fast Radius 制作零件了吗?
开始报价工业技术