盘条轧制的重要特点
盘条轧制的重要特点
线材通常在高速轧机中轧制,钢温在 1,000 摄氏度以上,最高轧制速度超过 120 米/秒 (m/s),生产的线材卷可长达 10 公里 (km) .线材轧制过程中,通常在连轧机中进行25道次到30道次。
线材是一种应用非常广泛的材料。从汽车工业的零部件、轮胎帘线、电极、螺母和螺栓等连接元件、弹簧、线材和线材产品、钢筋等,一切都以线材为基础。这就是为什么线材轧机通常在设计时考虑到多功能性。该磨机是能源密集型磨机,因此有必要在不影响灵活性的情况下将最佳解决方案纳入磨机设计。所有尺寸范围、材料和合金都需要在线材轧机中高效生产。
线材需要满足线材用户对表面和内部质量以及物理、化学、机械和冶金性能的要求。线材经过后处理,如拉丝、锻造或机加工成所需的形状和热处理,以使产品达到所需的强度。因此,要求线材无论在何处使用都能够保证所生产的零件的良好性能,同时在后加工的不同阶段具有良好的加工性。
线材用户有三个基本要求,即(i)消除或简化一种或多种二次或三次加工以提高生产率和降低加工成本,(ii)改善功能,即延长使用寿命,减轻重量,或为使用线材的最终产品带来其他优势,以及 (iii) 在后加工过程中消除对环境有害的物质的使用。
为了满足消费者日益严格的要求,线材厂需要从不同的角度来具备轧制线材的综合能力,即(i)提高尺寸精度,(ii)实现无尺寸轧制(即轧制(iii) 通过加快换辊工作(缩短换辊时间)提高生产率,以及 (iv) 通过防止在运输过程中出现表面缺陷来提高产品表面质量轧制过程。
线材轧机不仅要供应材料,还要供应线材,以满足它们在二级和三道工序中进行的长期后续加工的要求,直到生产出最终产品。此外,由于最终产品在许多工业领域中被用作重要部件,因此在与客户的综合协作中要求过程合理化。因此,轧机不仅要能够满足用户的质量要求,还要能够满足用户在后续加工过程中对生产率、产量、灵活性和生产成本的要求。高产量和良好的产品质量对于控制生产成本至关重要。
线材轧机的生产能力取决于少量标准产品的批量生产,或者由具有大量钢种和特殊产品质量的线材组成的多样化产品组合。
线材轧机基本上需要 (i) 将初始材料(钢坯)加热到轧制温度的加热设备,(ii) 由带有轧辊、轴承座、导轨和防护装置的轧机机架组成的轧制设备,(iii) 铺设、热处理和卷取设备,以及 (iv) 输送和搬运设备。所有设备要紧密配合,控制轧制温度、间隙时间损失、速度损失、鹅卵石、不合格品以及导致分流甚至废品的质量偏差。
现代线材轧机的要求
线材轧机轧制线材有几个重要参数(图 1)。现代线材轧机通常设计为符合“整体设备效率”(OEE)理念。磨机的OEE值是磨机利用率、磨机效率和磨机产出时间的乘积。工厂利用率是可用运行时间除以计划生产时间并以百分比表示。磨机效率是运行时间除以磨机的可用运行时间并以百分比表示。磨机产出时间是与运行时间相关的主要产品的生产时间。成品率以合格钢卷重量除以坯料重量表示,以百分比表示。
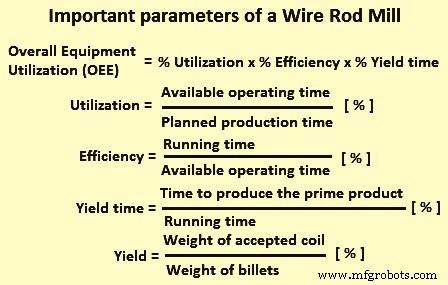
图1 线材轧机的重要参数
线材轧机通常比其他类型的轧机具有更低的 OEE,因为在产品转移过程中更换轧辊和更换机架以及调整槽和导轨的停机时间更长。如果可以减少这种停机时间,则可以提高工厂的 OEE。
磨机的理论生产能力是可以在没有任何损失的情况下获得的能力,即在 100% 利用率、100% 效率和 100% 产量的情况下。然而,实际产能取决于工厂的 OEE 水平。如果磨机的 OEE 水平为 60%,则磨机的磨机产能为理论产能的 60%。具有明确优化轧机的最先进线材轧机的 OEE 水平通常在 80 % 左右。
线材轧机的劣质成本一般确定为检验成本与因内部和外部缺陷导致的线材拒收/分流的总和。对于高性能轧机,它可能在 10% 左右。在具有多种产品组合的线材轧机中,它可以提高高达 30%,该线材由具有大量等级和特殊产品质量的线材组成。
在现代线材轧机中,主要关注的是生产率和质量。高利用率、效率和产量带来高生产率。但高生产率本身并不是线材轧机成功的唯一因素。它必须生产为客户带来价值的产品,并且他们获得的优质线材值得他们为线材支付的费用。
磨机的生产率和利用率取决于由多种原因引起的磨机停机时间,包括磨机布局和产品组合。在轧机中,从钢坯到最终产品的所有步骤都记录了产量,并且跟踪轧机中的材料跟踪轧机中发生的损失。磨机中发生的损失的主要类别是(i)间隙时间损失,(ii)速度损失,(iii)由于鹅卵石造成的损失,(iv)由于质量偏差造成的损失,(v)由于磨机造成的损失停机时间,(vi) 在轧机精加工侧检查期间因线材转移/废品而造成的损失,以及在生产专用线材产品时因增值操作而造成的时间损失。
磨机灵活性
在线材轧机中,钢(钢坯)被加热到其再结晶温度以上,并通过轧机中轧辊的多个凹槽。线材轧机中使用的常见轧辊道次设计有菱形、菱形、箱形道次、方形椭圆形、假圆形椭圆形和圆形椭圆形。线材轧机通常进行尺寸自由轧制,这意味着可以轧制任何尺寸的线材,而不受轧机中轧辊道次尺寸的限制。这也被称为系列的灵活性。此外,上游轧机的道次计划的简化使得换辊频率大大降低。相同轧辊所能轧制的产品尺寸范围(尺寸自由范围)越宽,降低换辊频率的效果就越大。尺寸自由轧制不限于精轧机。也可应用于预精轧机。
为了提高生产率,重点是尽量减少线材轧机的停机时间。当要制造新的最终尺寸和新的钢种和形状时,通常可以通过减少更换轧辊的时间和需求来提高这种关注的有效性。这是通过提高工作范围来实现的,也称为系列的灵活性。当轧制大量具有不同形状和尺寸的不同钢种时,轧制计划的变化最小,就可以提高灵活性。每个钢种在通过辊缝时都有其特定的材料流动方式,例如不同的扩散方式。此外,根据实际钢种,需要减少启动时间和等待正确轧制温度的时间。然而,当要轧制多种等级时,不同的加热周期仍然会导致停机时间过长。为了满足当今小批量、多品种钢材的市场需求,现代线材轧机展现出高度的灵活性已成为必然。
线材轧机的一个特殊方面是使用灵活的辊道设计或具有高工作范围的灵活槽。通过使用灵活的轧辊道次序列,只需改变轧辊距离,就可以在相同的槽中对各种成品进行轧制。因此,可以通过简单地移动辊缝来代替换槽,从而减少了从一种产品更换到另一种产品的停机时间。辊道设计的灵活性、轧机利用率和产量之间存在很强的相互依赖关系。
通过采用灵活的辊道设计,可以减少轧机中重要部分的损失。灵活的轧辊道次设计可最大限度地降低钢种变化过程中凹槽过度填充和形成鹅卵石的风险。当需要引入新尺寸或钢种时,灵活的轧辊道次设计也有利于产品开发。此外,灵活的轧辊道次设计可以显着提高价值提升运行时间。
工厂生产力
线材轧机可以与棒材轧机相结合,通过在精轧块之前有一个冷床出口。通常这样做是为了利用上游轧机的产能。当线材组换辊时,上游轧机生产棒材,以减少轧机的总停机时间。
现代线材轧机一般为单流轧机。在多股轧机的情况下,在每根股上引入第二个中间轧机,以减少同时轧制股数变化的影响。第二中间轧机可以是预精轧块的形式。它也可以是三辊轧机块的形式。三辊轧机的主要特点是与传统的二辊轧机相比,它能够抑制三个槽辊之间的尺寸变化,这三个槽辊轧制了轧材的整个圆周,从而减少了扩散。这种中间轧机被称为定型轧机,其成型是通过低压下完成的。这有助于在轧机上游建立家庭轧制理念,从而减少复位时间。
为了提高轧机速度并因此提高轧机生产率,在常规精加工块之后安装了异径/定径轧机 (RSM)。在传统精加工块之后集成 RSM 显着提高了小尺寸轧机的生产率(高达 60 %)。其极高的精度已在许多安装中得到证明。此外,结合极低温轧制,这会产生更精细的微观结构,从而可以消除额外的二次加工。 RSM 提高了生产率和成品质量,同时降低了运营成本并提高了线材产品的质量。它适用于从粗加工组的第 1 机架到精加工组的最后机架的单辊道次设计。由于它有利于相同的单系列道次设计,因此可以保持较高的轧机效率,而无需考虑最终产品尺寸。
线材轧制过程中通常尽可能避免机架间张力,否则头尾端会超出公差,因为自由端无法在张力下轧制。这一事实可能导致过度填充的凹槽和末端缺陷,例如翅片。但在固定传动的高速无扭滑块中,采用机架间张力来实现稳定的轧制条件。当对轧制的棒材施加机架间张力时,将设置凹槽以提供所需的公差。
线材质量
线材用于多种应用。在许多应用中,对线材的质量要求非常严格。线材的劣质会增加最终产品的缺陷/转移,并对客户端的产量产生不利影响,从而引起客户的不满。
由于线材轧制是一种能源广泛的轧制,因此总是需要将有缺陷的线材卷材的轧制减少到最低限度。有时,当钢坯中的缺陷很大时,甚至会导致轧机出现鹅卵石。由于钢坯的线材长度很长,因此在轧制后的整个线材长度上的质量保证需要时间和精力。因此,钢坯(轧制前的原材料)的质量控制非常重要。有缺陷的钢坯需要通过钢坯检验来识别、隔离和去除。钢坯要检查表面缺陷和内部缺陷。通过对坯料进行磨削(调质),可以去除微小的表面缺陷。
线材(尤其是细线材)要求的重要特性是二次加工的高生产率和最终拉拔后的高强度。高生产率意味着在拉拔和集束过程中尽量减少断线或理想的无断线,更高的直接拉拔性能,以及在高拉拔速度等苛刻拉拔条件下的良好拉拔性能。通过对非金属夹杂物、偏析、脱碳、力学性能和显微组织等质量控制项目采用严格的标准来满足客户日益复杂的这些要求。
通常,许多应用对线材有三个主要要求。这些是(i)更高的强度,(ii)消除或简化后处理,以及(iii)更少使用对环境有害的物质。由于用户端成本降低和许多其他原因,需要更高的钢材强度。由于在用户端,线材经过锻造、拉拔、机加工等不同种类的二次加工以及退火、淬火、回火等热处理,
等,因此,从降低成本、节能和环保的角度来看,强烈要求取消或简化热处理和机械加工(如近净或无屑成形)。
控制非金属夹杂物、析出物、转变和金相组织是提高线材性能的关键冶金措施。非金属夹杂物的控制是提高弹簧钢强度、延长轴承钢使用寿命、去除易切削钢中铅等的主要种子技术之一。硫化物可有效实现这些钢的所需性能。
在线材轧机中,在精确满足规定的线圈材料性能方面没有任何妥协。这就是受控冷却输送机 (CCC) 系统发挥关键作用的地方。需要控制整个盘条线圈始终如一的高质量。
在这方面,CCC 系统对于加工优质线材产品、实现所需的均匀性以及冶金和机械性能起着重要作用。将快冷产品的环向抗拉强度变化严格控制在平均抗拉强度的1%以内。
The CCC system by a proper selection of cooling regime accommodates production of all conventional grades of steel as well as special product grades with alternative cooling modes.当与 RSM 一起用于低温轧制和控制冷却时,它还可以优化碳钢和合金钢牌号的加工,从而产生非常好的性能和尺寸控制组合。
CCC 系统有助于在各种条件下进行处理,包括单个系统内的快速冷却和慢速冷却模式。这种能力使线材轧机能够生产范围广泛的普通碳钢和合金钢,以及不锈钢和其他特种钢。 CCC系统提高了盘条的轧态性能,可以在直接可用的条件下生产更多牌号,并减少或消除球化退火等下游工序。
线材轧机中的热机械轧制 (TMR) 通过动态再结晶来细化最终晶粒尺寸。结合最终的在线水冷和 CCC 系统的卓越控制冷却,TMR 在确定最终产品性能方面发挥着重要作用。这对于随后在下游加工过程中进行球化退火的低合金和中合金钢产品特别有利。强烈控制晶粒尺寸的能力还通过改变相变开始时间和温度来影响随后向硬质产品(如贝氏体和马氏体)的相变。因此,TMR可以最大限度地减少直接下游冷加工并减少退火时间。
CCC 系统加工和低轧制温度的结合提供了降低某些关键等级线材的淬透性的能力。最终,这促进了铁素体的形成并延缓了向贝氏体和马氏体的演变。通过 TMR 实现的细化晶粒尺寸改善了热处理过程中的扩散,并可以减少热处理时间和温度。对于那些未经热处理的棒材,精制和复杂的结构增加了冷变形期间的拉伸拾取,产生了几个优点,例如(i)降低轧制拉伸强度,(ii)改善下游响应,以及(iii)增加工作淬透性。这些改进源于晶粒细化和微观结构控制。 CCC系统对冷却过程的良好控制,加上线材淬透性的降低,使得该过程非常稳定,并减少了形成不需要的硬质相的机会。
制造工艺