单晶硅混合加工过程中切削机理的分子动力学模拟
摘要
在本文中,进行分子动力学模拟以研究结合热和振动辅助的混合加工过程中的切削机理。应用改进的切削模型来研究一个振动周期中的材料去除行为和次表面损伤的形成。结果表明,在混合加工过程中,主要的材料去除机制可以在单个振动周期内从挤压转变为剪切。随着切削温度的升高,裂纹的产生和扩展得到有效抑制,而当占主导地位的材料去除机制变为剪切时出现膨胀。一个振动周期内亚表面损伤的形成机制可以根据应力分布来区分。此外,工件中空位的产生随着温度的升高而变得明显,这是混合加工过程中的一个重要现象。
介绍
单晶硅是一种重要的半导体材料,由于其优异的光学和机械性能,在红外光学、微电子和光电子系统中得到了广泛的应用[1, 2]。然而,由于单晶硅的硬度和脆性,机械加工过程中会产生微观脆性断裂和亚表面损伤。在微铣削过程中,加工引起的内部型边缘崩刃缺陷会在工件中产生[3]。在单晶金刚石切割 (SPDT) 加工中,根据加工参数的不同,可以形成 200 到 600 nm 的损坏层 [4, 5]。尽管可以通过研磨和抛光将亚表面损伤层减少到大约 50 纳米。复杂结构的加工效率和能力有限。为了克服这些问题,已经提出并测试了各种辅助加工技术。尤其是热辅助切割(TAC)[6]和振动辅助切割(VAC)[7]以其非凡的切割性能而受到广泛关注。
对于单晶硅等脆性材料,提高加工温度可以促进脆韧转变。在 TAC 过程中,硅工件被热软化,导致切削力 [8] 和比切削能 [9, 10] 降低。同时,当加工温度升高时,高压相退火成立方硅相变得明显[11]。 With appropriate selection of the machining parameters, desired machined surface with high phase purity and low subsurface damage can be achieved by TAC [12,13,14].除了 TAC,振动辅助切割 (VAC) 是另一种在单晶硅上实现高质量表面的促进方法。自 1960 年代以来,该技术已应用于制造业 [15]。在这项技术的早期发展中,在加工中只进行标称切削方向的线性振动运动,称为线性振动切削(LVC)。 1994 年,Shamoto 和 Moriwaki [16] 提出了椭圆振动切割(EVC)。如下,EVC 在许多脆性材料(如硅 [17、18]、反应结合碳化硅 [7]、碳化钨 [19、20] 和硬化钢 [21])上的加工可行性已得到验证。在 EVC 过程中,由于瞬态切削深度 (DOC) 远小于标称 DOC [22],因此可以有效抑制次表面损伤。此外,由于每个振动周期的分离,刀具和工件之间的接触面暴露在周围的气体或流体中,从而消散了产生的切削热。因此,可以有效抑制刀具磨损,如粘附和热化学反应[23]。
为了进一步提高脆性材料的可加工性,已经进行了结合热和振动辅助的混合加工 (HM) 实验 [24, 25]。结果表明,当采用 HM 方法切割 Inconel 718 时,可有效降低加工表面粗糙度 [26]。通过实验和有限元法 (FEM) 模拟,可以在 HM 过程中实现钛合金的切削力大幅下降和优异的表面质量 [27]。这些结果证明了 HM 方法在脆性材料精密加工中的可行性。然而,由于刀具振动频率高,变形区温度高,很难直接观察和测量加工过程中的物理变量。此外,在纳米表面制造中,瞬态材料去除厚度通常从亚纳米到几纳米不等。因此,由于量子力学效应变得明显,诸如有限元法之类的问题的传统连续介质表示是有问题的。
近年来,分子动力学(MD)模拟因其在研究纳米切削过程中的优势而被广泛应用于辅助加工过程的研究[28,29,30]。基于先前对 TAC 的模拟 [31],当切削温度升高时,切削力、比切削能和屈服应力的各向异性变得更加明显。同时,在较高的切削温度下,工件中的剪切力较低,这导致剪切区更窄,剪切平面角的幅度更大[32]。此外,材料去除率可以随着切削温度的升高而提高,因为会形成更多的切屑 [33]。对于EVC工艺,通过MD模拟发现,与普通切削相比,变形区域的压应力和剪应力可以大大降低[34],有利于抑制次表面损伤。此外,EVC 工艺显示切削屑明显变薄,导致未切削切屑厚度与切削切屑厚度的比率增加 [35]。此外,已经阐明包括振幅比、振动频率和相位差在内的振动参数对材料去除性能有很大影响[34, 36]。
这些显着的成就提高了对辅助加工过程的加工机制的理解。然而,为了节省计算时间和内存,仿真系统通常很小。在之前的 EVC 过程模拟中,振动幅度和标称 DOC 小于 5 nm [22, 36]。因此,瞬态材料去除厚度通常小于 1 nm,无法准确描述实际的材料去除过程。此外,尚未报道 HM 过程的 MD 模拟。 HM过程中材料去除过程和亚表面损伤形成的机制尚不清楚。因此,本文通过MD模拟来揭示HM加工的切削机理。对经典切割模型进行了修改,使振动参数更接近实验值,例如,将振幅放大到 40 nm,标称切割速度为 3.125 m/s。研究了一个振动周期的材料去除机制和切削温度升高的影响。 MD 模拟由著名的大规模原子/分子大规模并行模拟器 (LAMMPS) [37] 进行。采用后处理软件OVITO[38]对仿真结果进行分析。
模拟方法
切割模型细节
图 1 显示了 EVC 过程的示意图,最初由 Shamoto 等人提出。 [39]。刀具轨迹可表示为:
$$x\left( t \right) =A_{{\text{c}}} \sin \left( {2\pi ft} \right) - vt$$ (1) $$z\left( t \ right) =A_{{\text{d}}} \sin \left( {2\pi ft + \varphi } \right)$$ (2)其中 x (t ) 和 z (t ) 表示 x 中的刀具位移 和 z 方向。 A c 和 A d 是标称切削方向上的振动幅度 (x 方向)和标称 DOC 方向(负 z 方向)。参数 f , v , φ , 和 t 分别代表振动频率、标称切削速度、相位差和模拟时间。仿真时间t 我 表示 P 点的时间 我 在图 1 中的工具轨迹上。
<图片>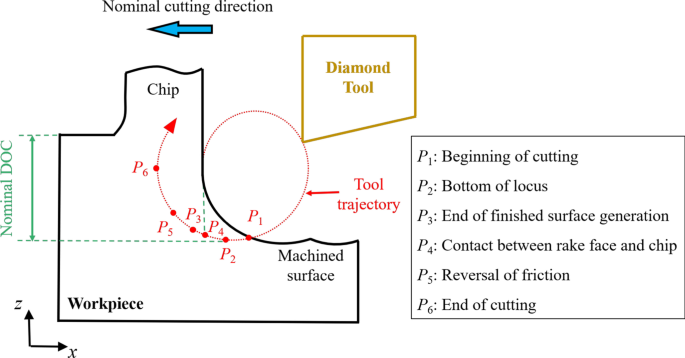
EVC流程示意图
图>根据几何关系[40],t的值 1 和 t 3 可以通过以下方式确定:
$$x\left( {t_{1} } \right){-}x\left( {t_{3} } \right) =2\pi v/\omega$$ (3) $$z\left( {t_{1} } \right){-}z\left( {t_{3} } \right) =0$$ (4)然后,t 当金刚石刀具的瞬态运动方向平行于刀具前刀面时,可得图6:
$$\frac{{A_{{\text{c}}} \sin (2\pi ft_{6} ) + v}}{{A_{{\text{d}}} \sin (2\pi ft_ {6} + \varphi ) }} =\tan \gamma$$ (5)其中 γ 是金刚石刀具的前角。
MD 模型如图 2 所示,单晶硅工件设置为变形体。而金刚石工具被认为是刚体,因为在这个模拟中工具磨损可以忽略不计。经典切削模型中的工件形态根据前一个振动循环中的刀具轨迹重新整形,同时考虑刀具边缘半径。工具轨迹可以如图 2b 所示确定。 P o 和 P b 是刀刃圆的圆心和底点。考虑刀具边缘效应时,瞬态表面生成点P c 在刀具移动过程中沿刀具边缘变化。实际的精加工面是由刀具刃口的包络线生成的。如果P的轨迹 b 由方程表示。 (1)和(2),P的轨迹 c可以通过[41]计算:
$$x_{{\text{c}}} \left( t \right) =A_{{\text{c}}} \sin \left( {2\pi ft} \right) - vt - r\sin \theta \left( t \right)$$ (6) $$z_{{\text{c}}} \left( t \right) =A_{{\text{d}}} \sin \left( { 2\pi ft + \varphi } \right) + r(1{-}\cos \theta \left( t \right))$$ (7)哪里
$$\sin \theta \left( t \right) =\frac{{z^{{\prime }} (t)}}{{\sqrt {x^{{\prime }} (t)^{2 } + z^{{\prime }} (t)^{2} } }}$$ (8) $$\cos \theta \left( t \right) =\frac{{ - x^{{\prime }} (t)}}{{\sqrt {x^{{\prime }} (t)^{2} + z^{{\prime }} (t)^{2} } }}$$ (9 ) <图片>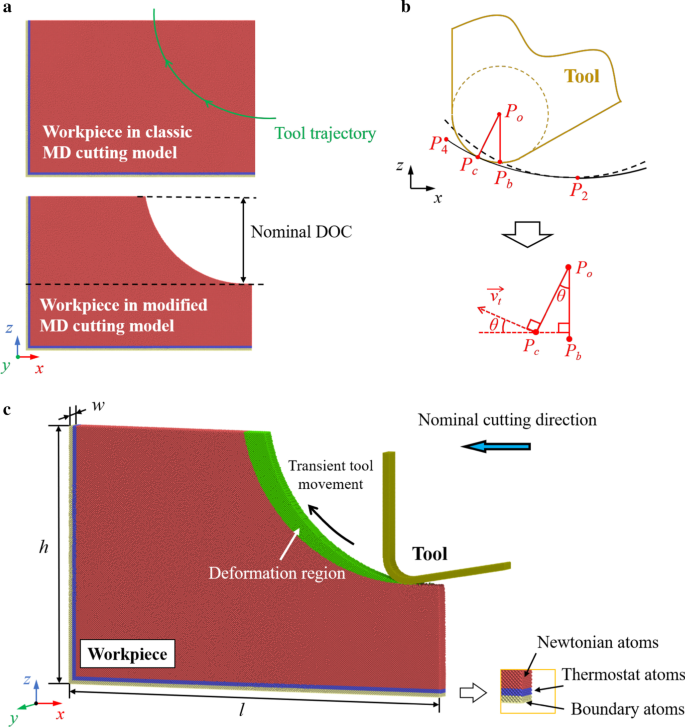
MD 切割模型的方案。 一 工件的修改。 b 刀具轨迹的确定。 c 修改后的 MD 模型的形态。绿色原子代表一个振动周期内的变形区域
图>硅原子分为三组:边界原子、恒温原子和牛顿原子。边界原子固定在其平衡位置以在模拟过程中固定工件。恒温原子保持在环境温度以消散产生的切割热,而牛顿原子遵循牛顿第二定律。
表 1 列出了仿真参数的详细信息。长度 l 和高度 h 决定在切割区和固定边界之间保持足够的距离。沿 y 应用周期性边界条件 模拟块状硅的方向。公称切削方向、刀具前角/后角和相位差是参考实验装置确定的 [42]。将振动幅度和标称DOC扩大到接近实验规模,模拟成本可接受。同时,为了确保去除材料的厚度(图 2c 中的绿色原子),速度比和振动频率分别设置为 40 和 500 MHz。因此,标称切割速度确定为 3.125 米/秒。此外,还进行了不同切削温度的模拟,以揭示热辅助对切削机理的影响。切割温度从 300 K 提高到 1200 K,这在 TAC 等激光辅助加工过程中是可以实现的 [4, 11]。
图>在这个修改后的模型中,只模拟了振动周期中的切削阶段,并保存了工件与刀具分离的时间步长。因此,计算能力可以集中在瞬态切割过程上。最重要的是,可以准确描述瞬态材料去除过程。修改后的模型与经典MD模型的比较如表2所示。
图>潜在功能
在 MD 模拟中,重要的是采用强大的潜力来描述原子之间的相互作用。对于单晶硅,学者们已经开发了许多潜力,例如改进的嵌入原子方法(MEAM)[45]、Stillinger-Weber(SW)[46]、Tersoff[47]和电荷优化多体(COMB)[ 48] 潜力。在这些势中,Erhart 和 Albe [49] 提出的分析键序势(ABOP)引起了越来越多的关注。它是一个三体势函数,允许在加工模拟过程中形成和破坏键。根据之前的研究 [50],ABOP 可以准确地描述硅的二聚体和块体特性。同时,ABOP 制成的硅的机械性能与实验结果一致 [31],这在纳米加工的 MD 模拟中很重要。因此,在本文中,ABOP 势被用来描述硅-硅和碳-碳相互作用。同时,硅-碳的相互作用由莫尔斯电势描述,这已被证明是纳米级切割模拟中的有效电势 [51, 52]。莫尔斯势函数可以表示为:
$$E_{{\text{Si - C}}} \left( {r_{ij} } \right) \, =D_{{\text{M}}} \left[ {{\text{e}} ^{{ - 2a(r_{ij} - R_{{\text{M}}} )}} - 2{\text{e}}^{{ - a(r_{ij} - R_{{\text{ M}}} )}} } \right]$$ (10)其中 D M, a, 和 R M 分别代表内聚能、弹性模量和原子之间的平衡距离。 Morse 势的参数是[53]:D M =0.435 eV,a =46.487 nm −1 , R M =0.19475 纳米。
结果与讨论
切割性能
在普通切削中,主要的材料去除机制受未变形切屑厚度的影响很大 [54]。由于未变形切屑厚度小,主要的材料去除机制是挤压。金属稳定相(Si-II)可以通过高压相变(HPPT)产生,这有助于硅的延展变形。当未变形切屑厚度增加时,主要通过剪切工艺去除材料。而在EVC过程中,由于未变形切屑厚度不断变化,材料去除机制可以在一个振动周期内从挤压转变为剪切。图 3 显示了 300 K 下切割模拟的快照。工件的晶体结构由公共邻域分析 (CNA) [55] 确定。该分析发现以立方或六边形金刚石晶格排列的原子。图 3c、e 中的非金刚石结构主要包含非晶相 (a-Si)、Si-II 和其他缺陷原子 [56]。这些结构不稳定,切割后会转变为 a-Si。从图 3b、c 可以看出,在初始切割阶段,材料主要通过挤压去除。在刀具边缘附近可以观察到一个瞬态停滞点。与普通切削类似,变形区的材料按驻点分为切屑和压缩材料。随着刀具的前进,未变形的切屑厚度增加。工件中产生剪切面和多晶晶粒,表明剪切成为主要的材料去除机制。
<图片>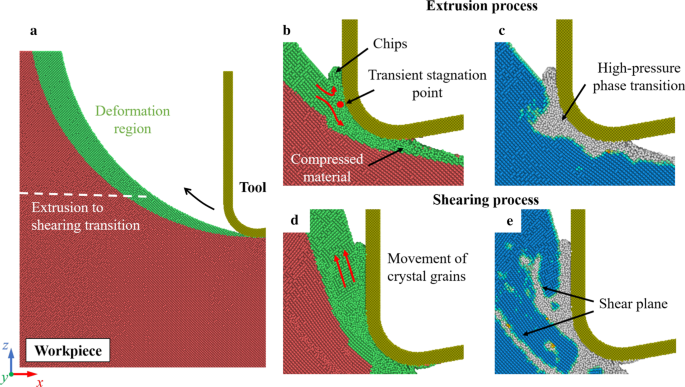
材料去除机制的转变。 一 变形区域的图示。 b , d 挤压和剪切过程。 c , e 工件中晶体结构的鉴定。蓝色原子代表立方金刚石结构,灰色原子代表非金刚石结构
图>图 4 显示了不同切削温度下的工件形态。在 300 K 时,刀具向上运动过程中可以观察到工件出现明显的裂纹和断裂。对于像单晶硅这样的脆性材料,工具向上运动会导致材料撕裂并在工件中留下缺陷,这被认为是 EVC 中的一个特定问题 [42]。虽然这些裂纹可以通过进一步的振动循环消除,但由于工件表面的不规则性,加工稳定性会受到影响。当切削温度升高时,裂纹的产生和扩展得到有效抑制。从图 4d,当切削温度升高到 1200 K 时,没有检测到明显的断裂。然而,观察到在 900 K 和 1200 K 时,当材料去除机制转变为剪切时,加工表面的膨胀变得明显。可以得出结论,随着剪切阶段产生更多的晶粒,膨胀可能是由这些晶粒在高温下旋转引起的。
<图片>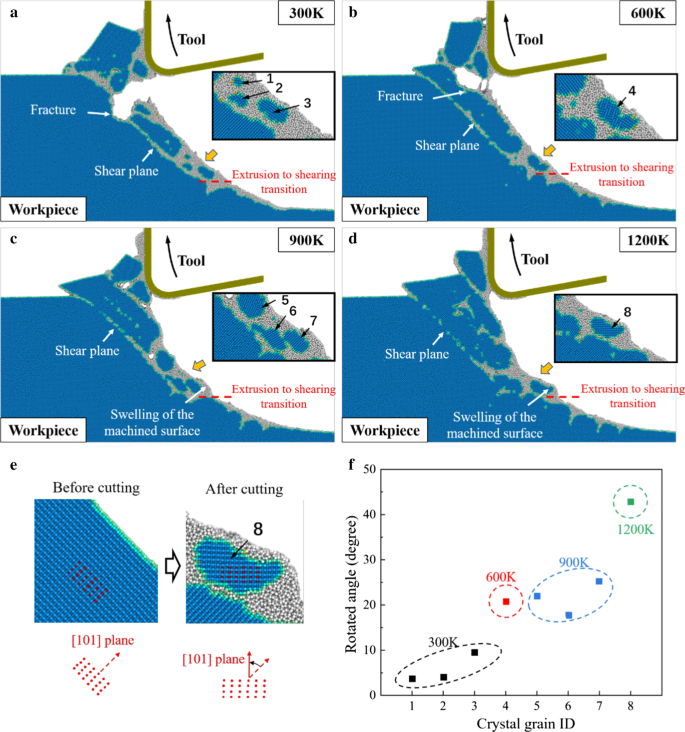
a处HM过程的工件形貌 300 K。b 600 K。c 900 K。d 1200 K。蓝色原子代表立方金刚石结构,而灰色原子代表非金刚石结构。 e 晶粒旋转角的测定。 f 随切削温度升高的旋转角度
图>为了清楚地描述这种旋转,使用晶粒中 24 个标记原子(红色原子)的坐标来计算平均旋转角度,如图 4e 所示。图 4f 总结了 8 个晶粒(在图 4a-d 中编号)的旋转角。可以观察到,在升高的温度下,旋转角明显增加。在HM过程中,a-Si在高温下的粘度可以大大降低,刀具向上运动促进了工件原子的上拉运动。因此,增强了工件中的原子流,促进了晶粒的旋转,导致加工表面膨胀。为抑制晶粒旋转,应控制加热功率,避免工件过热。此外,应谨慎选择振动参数,例如应采用较小的标称切削速度和较高的振动频率,以抑制晶粒的产生并通过进一步的振动循环消除膨胀。如图 5 所示,在适当的振动参数下,P 1 可以定位在挤压阶段,最终加工表面是通过挤压产生的,没有膨胀。
<图片>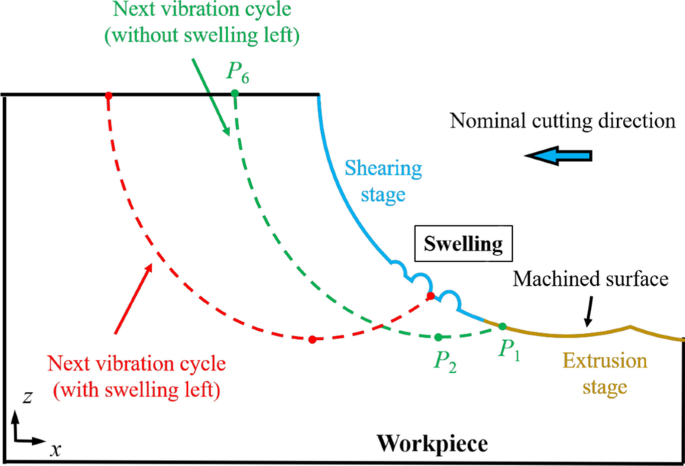
消除HM过程中的溶胀
图>工件应力场
为了进一步研究HM加工过程中的切削机理,计算了工件中的应力分布。在MD模拟中,静水应力可表示为:
$$\sigma_{{{\text{hydrostatic}}}} =\, (\sigma_{x} + \sigma_{y} + \sigma_{z} )/3$$ (11)其中 σ x , σ 是 , 和 σ z , 是来自 LAMMPS 输出数据的应力张量。
挤压和剪切阶段的静水应力分布如图 6 所示。并标记了压缩和拉伸区域的应力峰值。随着刀具运动,刀具和工件之间的接触点沿着刀具边缘循环变化,这导致压缩区域从刀具边缘向前刀面移动。根据之前的报道,从单晶硅相 (Si-I) 到 Si-II 的 HPPT 可以在 10-12 GPa 的压力下发生 [57, 58]。在 300 K 的切削模拟中,挤压和剪切阶段的最大压应力分别达到 18.1 GPa 和 17.6 GPa。该结果表明,在切割过程中可以产生韧性的 Si-II 相,而在剪切阶段仍然存在 HPPT。此外,在挤压阶段,由于硅原子与刀具表面的粘附,拉应力主要集中在刀具后刀面与加工面接触区域附近。随着刀具进入剪切阶段,拉伸区域扩大,工件表面下的拉伸应力集中大大增加,这是由上拉运动引起的。当切削温度升高时,单晶硅的塑性变形能力提高,工件内应力降低。随着温度从 300 K 升高到 1200 K,挤压和剪切阶段的最大压应力分别下降了 16.6% 和 25%。同时,虽然表面下工件的拉应力集中仍然明显,但拉应力的峰值明显下降了30%以上。据报道,单晶硅的断裂韧性在较高温度下可以有效提高[59]。因此,可以有效地抑制刀具向上运动引起的撕裂效应引起的裂纹和断裂。
<图片>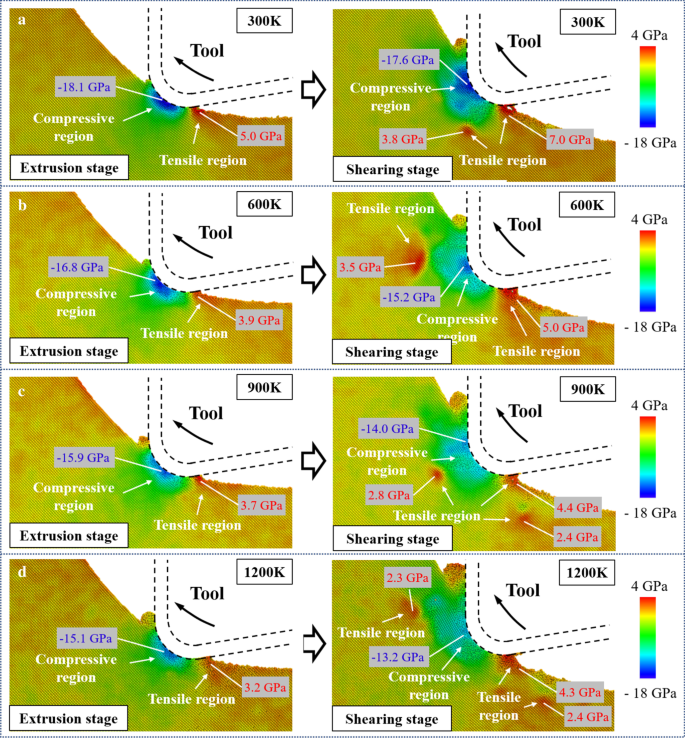
静水应力分布在:a 300 K。b 600 K。c 900 K。d 1200 K
图>单晶硅具有面心立方 (FCC) 晶体结构,具有 12 个滑移系统。基于工具运动,剪切变形的主要滑移系统是 (111)/[\(\stackrel{\mathrm{-}}{1}\)01] 和 (1\(\stackrel{\mathrm{- }}{1}\)1)/[\(\stackrel{\mathrm{-}}{1}\)01] 系统。因此,解析剪应力分量τ s 在 (111)/[\(\stackrel{\mathrm{-}}{1}\)01] 滑移系统中计算。如图 7 所示,解析剪应力分量 τ s 方向 M 滑移面 N 可以通过应力张量计算:
$$\tau_{{\text{s}}} =a_{1} a_{2} \sigma_{x} + b_{1} b_{2} \sigma_{y} + c_{1} c_{2} \sigma_{z} + \left( {a_{1} b_{2} + a_{2} b_{1} } \right)\tau_{xy} + \left( {a_{1} c_{2} + a_{2} c_{1} } \right)\tau_{xz} + \left( {b_{1} c_{2} + b_{2} c_{1} } \right)\tau_{yz}$$ (12)其中 a 1、b 1、c 1是平面N法线方向的方向余弦 而 a 2、b 2、c 2是滑移方向M的方向余弦 .而 τ xy , τ xz , 和 τ yz 是来自LAMMPS输出数据的剪应力张量。
<图片>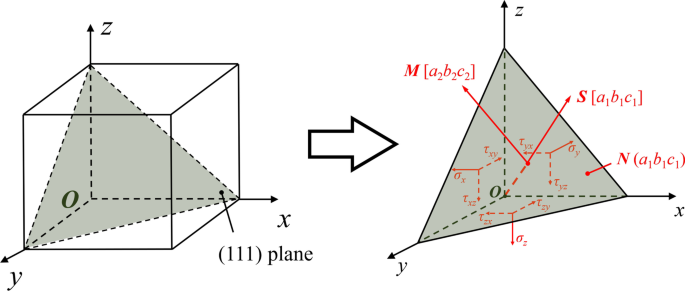
应力张量图示
图>解析剪应力分布τ s 如图 8 所示。τ 为正的区域 s 被定义为剪切区域,因为沿 [\(\stackrel{\mathrm{-}}{1}\)01] 方向的滑动运动被促进,这有助于通过剪切去除材料。而负τ的区域 s 被认为是损伤区域,因为滑动运动在相反方向上是优选的,导致工件表面下损伤的形成。在挤压阶段,剪切区的应力小于损伤区的应力。由剪切变形引起的次表面损伤可以在加工表面下方产生[60]。随着刀具运动,沿 [\(\stackrel{\mathrm{-}}{1}\)01] 方向的剪切应力逐渐增大,导致材料去除从挤压过渡到剪切。此外,由于损伤区域的位置随着刀具运动向上移动,产生的损伤可以通过进一步的振动循环去除,不会留在工件中。当温度从 300 K 升高到 1200 K 时,挤压和剪切阶段损伤区域的剪切应力分别下降了 36.1% 和 42.4%。相比之下,由于工具向上运动,剪切阶段沿 [\(\stackrel{\mathrm{-}}{1}\)01] 方向的剪切应力的减小则不那么明显。滑移运动的临界分辨剪应力(CRSS)可表示为[61]:
$$\tau_{{\text{c}}} \left( T \right) =C\varepsilon^{1/n} \exp \left( \frac{U}{nkT} \right)$$ (13 )其中 U ε 表示滑移的活化能和应变率。参数 n 和 C 是材料常数。可以得出结论,CRSS可以随着温度的升高而明显降低。因此,在升高的温度下可以促进 [\({\overline{\text{1}}}\)01] 方向的剪切变形。
<图片>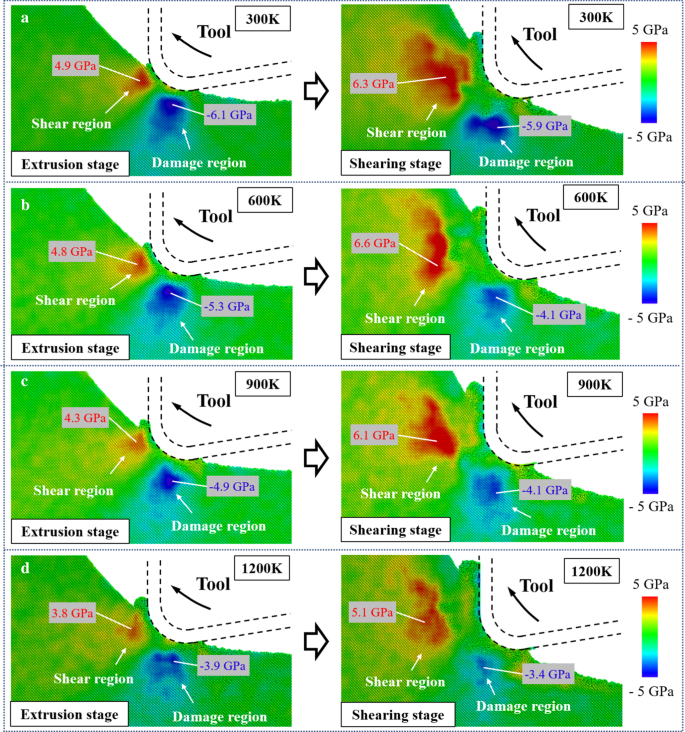
解析剪应力分布在:a 300 K。b 600 K。c 900 K。d 1200 K
图>相变
当切削温度升高时,硅的相变会受到很大影响。在适当的温度下可以促进 a-Si 的弛豫和向 Si-I 的转变 [62]。在图 4 中,工件中的损伤模式在高温下变得更窄。图 9a 显示了在 1200 K 切割时对损坏模式的详细观察。观察到变形区产生的损伤在切割后部分恢复,表明发生了从非金刚石结构到 Si-I 的转变。当切削温度升高时,会产生更多的 Si-I 原子,如图 9b 所示。此外,图 9c 中显示了在 1200 K 下加工工件的构造表面网格(红色)[63]。观察到在表面下工件中形成了一些空位。由于原子更紧密地堆积在 Si-I 相中,向 Si-I 的转变会导致材料收缩,从而导致工件中出现空位。计算了不同温度下的空位体积并显示在图 9d 中。观察到在室温下几乎不产生空位。而当切削温度升高到 900 K 和 1200 K 时,可以检测到空位的明显增加。
<图片>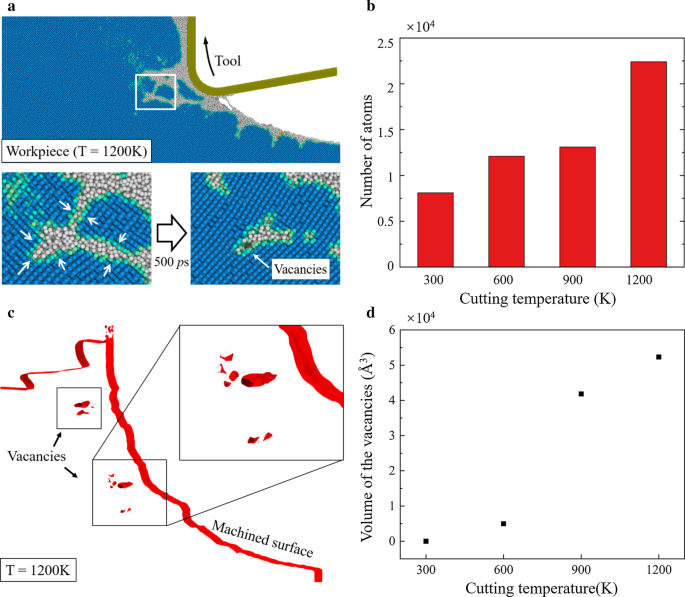
工件中的松弛过程和空位。 一 1200 K 时工件损伤模式的快照。b 从非金刚石结构转变为 Si-I 相的原子数。 c 在 1200 K 时构建的工件表面网格。d 不同温度下空位的体积
图>空位的进一步分析显示在图 10 中。选择加工表面下方的材料元素来监控空位的产生。存在非金刚石结构中的原子数和材料元素的应力演化。得出的结论是,在切削过程中,材料元素首先被压缩,然后由于刀具向上运动而受到拉应力。同时,在 300 K 处可以观察到两个剪切应力峰值,因为损伤区域的剪切应力随着刀具通过而增加。当切削温度升高时,剪应力的降低比拉应力更明显。在 1200 K 时,剪切应力的第二个峰值几乎消失,而拉伸应力在松弛过程中在材料元素中占主导地位。
<图片>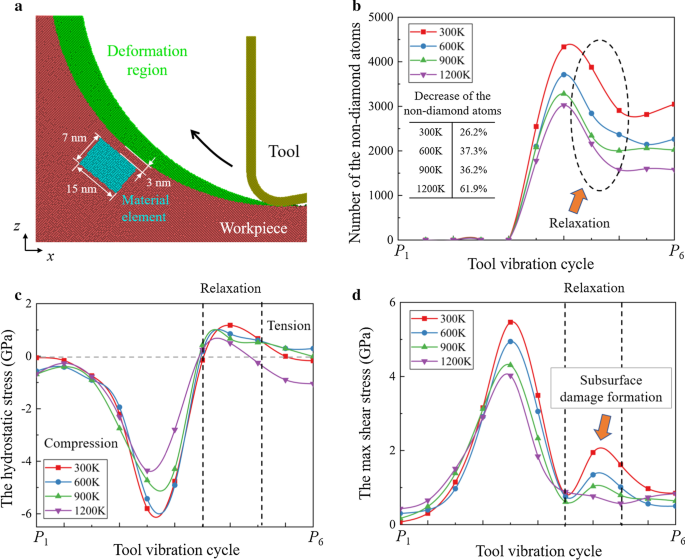
HM 过程中的松弛。 一 物质元素的插图。 b 材料元素中非金刚石结构原子的统计。 c , d 材料元素的应力演化
图>为了探索拉伸应力对空位形成过程的影响,进行了体硅样品的弛豫模拟。如图 11a 所示,初始模型由 40% 的 Si-I 原子和 60% 的 a-Si 原子组成,这是通过熔化淬火方法生成的 [64]。模型的尺寸在 x 中为 21.7 nm × 8.1 nm × 26.1 nm , y , 和 z 方向,其中包含 230,400 个原子。 The initial interface between crystal and non-crystal region is set as (001) crystal plane. Periodic boundary condition is applied in three dimensions to mimic bulk materials. The constructed surface mesh of the relaxed model is present in Fig. 11b. Furthermore, to quantify the vacancies, the solid volume fraction is calculated as the ratio of the solid material volume and the total volume of the simulation sample, as shown in Fig. 11c. It is observed that when temperature is increased, the solid volume fraction decreased obviously under tensile stress. Therefore, to suppress the vacancies, the desired cutting temperature in HM process should be lower than that in ordinary TAC. Meanwhile, the vibration parameters should be optimized to reduce the tensile stress in subsurface workpiece.
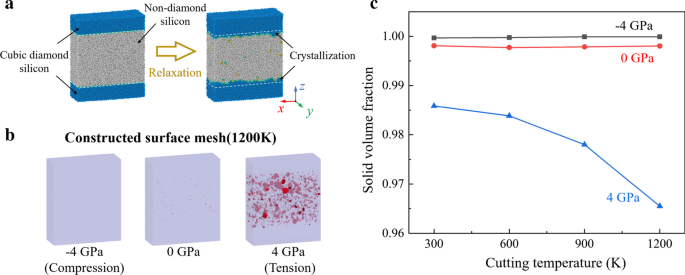
Relaxation simulation of silicon. 一 Scheme of MD relaxation simulation. b The surface mesh of the relaxed model at 1200 K. c The solid volume fraction curves
图>结论
In this paper, MD simulation is carried out to investigate the cutting mechanism of hybrid machining (HM) process. A modified cutting model is applied to reveal the material removal behavior and subsurface damage formation in one vibration cycle. The main conclusions were as follows:
- (1)
During HM process, the dominant material removal mechanism could transform from extrusion to shear in a single vibration cycle. With an increase of the cutting temperature, the generation and propagation of cracks can be effectively suppressed. However, the swelling appears when the dominant material removal mechanism becomes shearing, which is caused by the rotation of the crystal grains in workpiece.
- (2)
Based on the stress analysis, the dominant formation mechanism of the subsurface damage in one vibration cycle can be distinct. In the extrusion stage, the subsurface damage can be generated by the shear stress in the damage region. While in the shearing stage, tensile stress becomes dominant in subsurface damage formation. When the cutting temperature is increased, although the tensile stress concentration in the subsurface workpiece is still obvious, the peak value of the stresses is apparently decreased, which effectively suppress the cracks and fractures in workpiece.
- (3)
When the cutting temperature is increased, less subsurface damage is generated in the workpiece. However, due to the tensile stress, some vacancies can be generated in the workpiece when the cutting temperature is increased. Therefore, the desired cutting temperature during HM process should be lower than that in ordinary TAC and the vibration parameters should be set carefully to suppress the vacancies in the subsurface workpiece.
数据和材料的可用性
The datasets used and analyzed in the current study can be obtained from the corresponding authors upon reasonable request.
缩写
- TAC:
-
Thermal assisted cutting
- VAC:
-
Vibration assisted cutting
- LVC:
-
Linear vibration cutting
- EVC:
-
Elliptical vibration cutting
- DOC:
-
Depth of cut
- HM:
-
Hybrid machining
- 有限元:
-
有限元法
- MD:
-
分子动力学
- LAMMPS:
-
大规模原子/分子大规模并行模拟器
- MEAM:
-
Modified embedded-atom method
- SW:
-
Stillinger–Weber
- COMB:
-
Charge optimized many-body
- ABOP:
-
Analytical bond-order potential
- Si-II:
-
Metallic stable phase
- HPPT:
-
High-pressure phase transition
- CNA:
-
Common neighbor analysis
- a-Si:
-
Amorphous phase
- Si-I:
-
Single-crystal silicon phase
- FCC:
-
Face Center Cubic
- CRSS:
-
Critical resolved shear stress
纳米材料