使用分子动力学模拟对砷化镓进行纳米切割的次表面变形机制
摘要
在纳米切割过程中,单晶砷化镓面临着各种表面/亚表面变形和损坏,严重影响了产品的性能。在本文中,通过对砷化镓纳米切割的分子动力学模拟来研究表面和亚表面变形机制。在机械加工的地下发现位错。通过配位数研究相变和非晶化。结果表明在切割过程中存在配位数为 5 的中间相。建立具有不同切削速度的模型来研究对位错的影响。通过具有不同切割方向的模型研究了晶体各向异性对位错类型和密度的影响。此外,还对次表面应力进行了分析。
介绍
砷化镓 (GaAs) 是一种典型的 III-V 族化合物,也是最重要的半导体材料之一。单晶砷化镓以其直接带隙、高电子迁移率和高电阻率等优异特性在红外光学器件和微波器件等各个领域得到广泛应用。随着其生产的不断发展,对表面粗糙度、表面形状精度和亚表面损伤的要求越来越高。纳米切割技术有利于提高砷化镓光学元件的性能,扩大其应用领域。砷化镓晶体的纳米切割工艺面临着脆性裂纹、各向异性等次表面损伤等诸多难题。因此,研究砷化镓的纳米切削机理对于解决加工问题、提高砷化镓的表面质量、开发相关的纳米加工技术具有重要意义。
许多研究对砷化镓进行了纳米级实验。方等人。 [1] 比较了砷化镓和硅的纳米压痕和纳米划痕特性。泰勒等人。 [2] 研究了具有立方角尖端的砷化镓 (100) 中的超低负载纳米压痕。布拉德比等人。 [3] 在球形压痕中发现了砷化镓的弹出事件。方等人。 [4, 5] 研究了软脆半导体的加工性能,首次通过金刚石车削获得了砷化镓镜面。尽管已有许多关于砷化镓的压痕和物理性质的研究报道,但对其纳米切割过程和损伤形成机制知之甚少。这主要是因为进行实验和随后的表征非常困难。一方面,由于纳米尺度和高切割速度,几乎不可能使用在线测量来检查纳米切割过程和测量纳米数据。另一方面,进行一系列纳米加工和测量实验成本高昂。
分子动力学 (MD) 模拟是探索纳米加工机制的最有效方法之一。岛田等人。 [6, 7]证明MD模拟是描述纳米加工过程的有效方法。科曼杜里等人。 [8] 用MD模拟发现了硅在纳米切割过程中的结构转变现象。裴等人。 [9] 用纳米加工的大规模 MD 模型研究了铜的位错形成。赖等人。 [10]研究了临界前角和锗材料变形对纳米切削的影响,并进一步研究了部分重叠的纳米切削工艺[11]。此外,多尺度建模方法在超精密加工领域得到了很大发展 [12,13,14]。多尺度仿真结合了不同尺度的仿真方法,如纳米尺度的MD模型和纳米/微米尺度的FE模型[15],以更全面、更真实的方式研究加工过程。本文着眼于纳米切削过程的次表面变形机制,因此选择MD模拟作为研究方法。
至于所研究的材料,纳米加工中的大多数MD模拟研究都集中在硅和锗等元素半导体或铜和铝等金属上。关于砷化镓纳米切割数值分析的研究报道较少。范等人。 [16] 通过 MD 模拟和车削实验研究了砷化镓的韧性响应。易等人。 [17]通过MD模拟研究了砷化镓在纳米划痕过程中的相变和各向异性。本文通过一系列三维MD模拟研究了单晶砷化镓纳米切割过程中的塑性变形。还系统地研究了切削速度、切削方向等切削参数的影响。
方法
建立了MD模拟模型,研究了脆性晶体砷化镓在纳米切削过程中的变形行为。三维 MD 模拟模型如图 1 所示。工件为单晶砷化镓,在闪锌矿晶格中结晶,Ga 和 As 原子占据两个 FCC 亚晶格。工件尺寸为85纳米 × 30纳米 × 35纳米。工件模型由三层组成:边界层、恒温层和牛顿层。工件由边界层固定,而恒温层设置在293 K的恒温,以模拟真实加工过程中的散热。牛顿层是将揭示纳米切割过程机制的切割区域。牛顿层中原子的运动遵循经典的牛顿第二定律。为模拟真实切削过程中的金刚石刀具,建立了刀具刃口半径为10 nm的半球金刚石刀具模型,切削深度设置为4 nm。金刚石刀具设定在一定的速度下切入工件。由于计算资源的限制,模型被缩小和简化,但仍然有说服力地解释纳米尺度的延性变形和损伤形成。将金刚石工具简化为一个半球,研究工具两侧的侧流和堆积等水平方向的延性去除行为,这是三维模拟的重要特征。为了研究工艺参数的影响,建立了具有不同切割速度和方向的模型。表1列出了模型的参数。
<图片>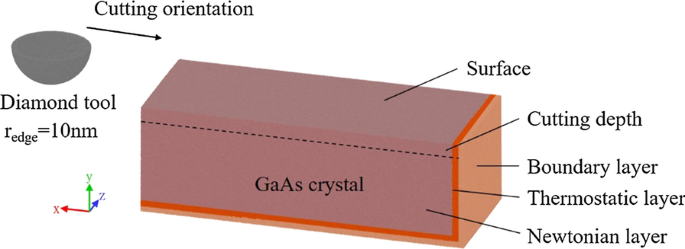
MD仿真模型
图> 图>势是计算原子间力和能量的基础,也是MD模拟中最重要的设置之一。在之前的研究中,确定了一个由三种电位组成的电位系统,用于模拟砷化镓和金刚石工具模型[18]。在该系统中,使用 Tersoff-Brenner 势来描述 Ga 和 As 之间的相互作用,显示出良好的模拟效果[19]。建立指数排斥势以通过量子化学方法描述金刚石工具和砷化镓工件之间的相互作用,其形式为简化的 Born-Mayer 势 [18]。 Tersoff-ZBL 势能用于金刚石工具。潜在系统总结在图 2 中。
<图片>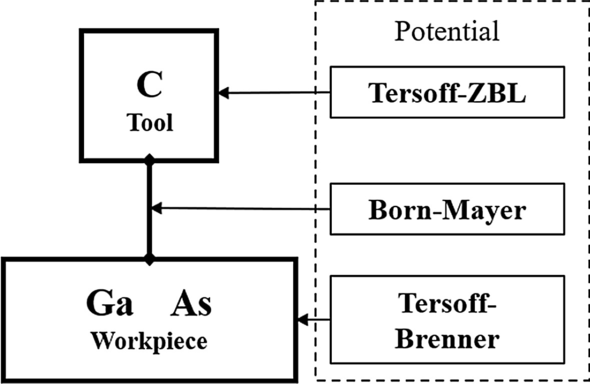
模型中的位势系统
图>LAMMPS用于进行MD模拟,而可视化和分析通过OVITO进行,包括位错分析(DXA)、应力计算和协调分析。工件的松弛设置为 NPT 系综,以最小化系统能量并稳定自由表面,而纳米切割过程设置为 NVE 系综。模拟中积分的时间步长为 1.0 fs。
结果与讨论
一般说明
如图 3 所示,沿 (010) 上的 [\(\overline{1}\)00] 方向以 60 nm 的切割距离加工砷化镓工件,切割速度为 400 m/s飞机。工件用原子在 y 中的位移着色 -方向。观察到工具前面的原子向上流动,通过挤压变成碎片。大量原子向下流动并形成加工表面。在加工凹槽的两侧,由于工具的挤压和犁动,原子堆积了 2 nm 的高度。结果表明,当加工在纳米尺度时,脆性砷化镓晶体的变形和去除代表了一种延展性行为。在模拟过程中,很少有砷化物簇沉淀到加工表面。该研究揭示了退火后存在砷化物沉淀 [20]。 Tersoff-Brenner 电位能够模拟砷化物簇的沉淀 [19]。在切割过程中,表面材料被切割热加热,然后退火,形成砷化物簇。然而,这种沉淀并不是纳米切割过程中的主要问题。因此,这些原子将被隐藏在后续的分析中。
<图片>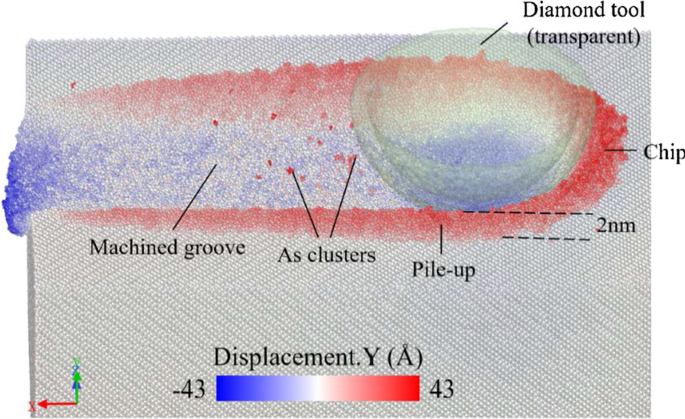
用原子在 y 中的位移着色的纳米切割模拟结果 -方向
图>比较图 4 中加工过程中的切削力曲线。最初,切向力和法向力随着刀具切入材料而上升。横向力在 0 附近波动,因为力在 z 中抵消 -方向。当力稳定后,法向力和切向力分别在 1700 nN 和 700 nN 左右波动。发现 y 中的力 -方向在切削过程中占主导地位,因为模型中显示的金刚石刀具的有效负前角很大。负前角带来较大的压应力,导致切削过程中法向力较大。
<图片>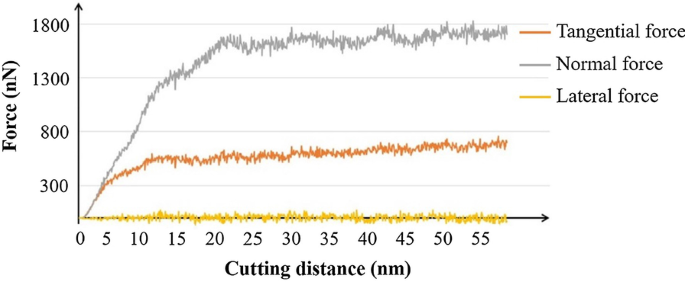
纳米切削过程中的切削力
图>错位和堆叠错误
次表面损伤的形成是纳米切割机理研究的重要组成部分。有必要弄清楚砷化镓在加工过程中的损伤形成机制,以进一步优化加工参数。晶体在原子结构上具有各向异性,是加工过程中最严重的问题之一,会影响不同取向的加工性能。
加工后表面位错的分布如图 5 所示,刀具运动沿 (010) [\(\overline{1}\)00] 切削方向。在加工槽周围观察到位错,形成约 8 纳米的位错层。机械加工的次表面中存在两种主要类型的位错。 1/2[110]位错主要在加工槽的两个侧壁内滑动,而1/6[112]位错分布在槽底下方。 1/2[110] 和 1/6[112] 位错分别被证明是完美位错(蓝线)和部分位错(绿线)。位错的形成意味着局部原子的传递运动,这意味着变形和去除处于延展状态。证明脆性材料在足够小的尺度上也表现出韧性状态。
<图片>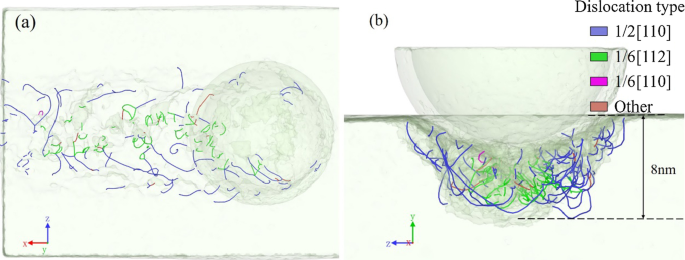
a 中加工过的地下位错分布的透视图 是 -direction 和 b x -方向
图>计算出的 von Mises 应力包括剪切应力分量,通常用于确定位错的形成。图 6 是位错和 von Mises 应力分布的截面图。由于挤压,高应力区域集中在工具下方。当刀具施加的应力超过工件材料的屈服强度时,材料会沿滑移面滑动,滑移材料的相对运动会带来位错。因此,由于加工区域的高应力,位错成核并延伸到单晶中。原子运动会释放局部能量。
<图片>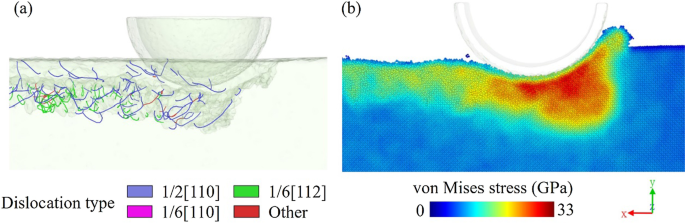
一 位错分布和b 纳米切削模型亚表面的von Mises应力分布
图>脆性材料和韧性材料中的位错有很大不同。砷化镓是典型的脆性晶体,位错集中在加工面附近。然而,铜等韧性材料中的位错会在切割过程中延伸并滑入工件深处并形成高密度位错簇 [21],如图 7a 所示。位错是由材料的延展性变形引起的。延性材料的位错簇的扩展导致大范围的延性变形和扩散应力。然而,脆性材料(如砷化镓)中位错的局部化表明,韧性变形仅发生在表面附近,而没有完全释放应力。当应力集中到阈值时,可能会出现其他类型的损坏,例如相变或裂纹。在我们之前的研究[18]中,研究了砷化镓的裂纹形成,发现随着切削速度的增加,去除模式将从具有位错形成的韧性模式转变为具有裂纹的脆性模式。位错的形成会释放可能导致裂纹萌生的应力,此时变形方式将趋于延性而不是脆性。
<图片>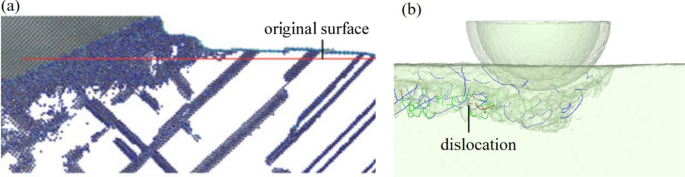
不同单晶材料纳米切割中的位错:a 铜 [21] 和 b 砷化镓
图>图 8 显示了在加工过的地下发现的堆垛层错。工件中的原子根据配位数着色。为了方便检查,隐藏了具有原始闪锌矿结构的四配位原子。可以观察到,在加工过的次表面中存在周期性放置的三配位原子。结合槽底下发现的局部位错,主要从晶界或自由表面发射的局部位错可能导致层错或孪晶的形成[22, 23]。模型中的堆垛层错不是完全错位的原子平面,而是单晶和非晶层边界上的几个小区域,因此堆垛层错边界处存在局部错位。也可以推断实际加工的地下可能存在堆垛层错。
<图片>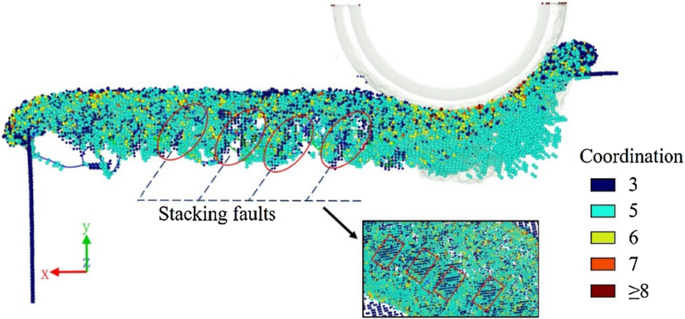
加工过的地下层错
图>相变和非晶化
由于纳米切割过程中的高应力,材料的晶格结构可能会发生变化。通过对相变过程的研究,可以更好地理解砷化镓的切割过程,有助于优化工艺参数或设计纳米切割前的预处理实验。
单晶砷化镓在常压常温下具有闪锌矿结构。然而,当压应力达到 17 GPa 时,结构变为六坐标 GaAs-II [24]。随着应力增加超过 60 GPa [25],相变最终形成纤锌矿结构。
图 9a 显示了在 (010)[\(\overline{1}\)00] 方向切割速度为 400 m/s 时模型的结构变化。观察到加工区的一层呈现出厚度约为6 nm的非晶结构,没有晶体的特征结构。
<图片>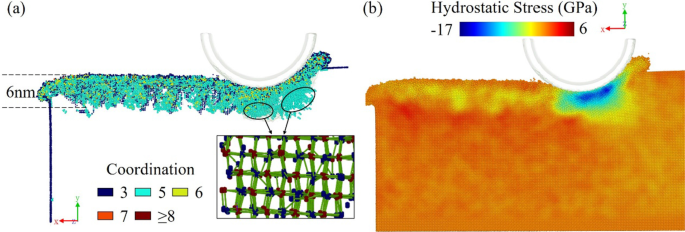
a的分布 高配位原子和五配位结构和b 静水应力分布
图>很明显,加工位置下的一些原子变成了五配位结构。类似于压缩应力形成的硅晶体的 bct-5 结构,这种五配位结构被认为是形成六配位 GaAs-I 的中间体。静水应力随着刀具切削而增加并引起晶格畸变。然而,如图 9b 的静水应力分布所示,最大静水应力为 17GPa,刚好达到从 GaAs-I 到 GaAs-II 的转变临界值。静水应力高于 17 GPa 的亚表面区域非常小,工件的大部分区域具有低于过渡阈值的静水应力。因此,很难找到具有六配位结构的大块原子,而五配位结构是从GaAs-I到GaAs-II的中间相。
图 10 描绘了切削过程中选定区域的径向分布函数曲线,该区域是金刚石工具下方的区域。计算加工前、加工中和加工后的径向分布曲线。工件开始时为有序闪锌矿结构,其曲线由规则的峰组成。当金刚石刀具到达选定区域时,径向分布函数在近程和远程均呈现无序状态。这意味着该区域中存在原子无序排列的强非晶化。然而,加工过的地下曲线意味着结构可以在短程恢复并变得有序,而在长程上则是无序的。随着应力的释放,材料将结构改变为具有最小能量状态的结构。具有中间相的原子可能会变为非晶态或其他状态。因此,曲线显示出具有非晶砷化镓的稳定加工状态。可以发现在加工过程中3.3Å处有一个侧峰,刀具离开时峰消失了。这种现象揭示了中间相的形成和消失,可以看作是切削过程中的弹性变形。在没有工具作用力的情况下,部分原子恢复为闪锌矿结构,其余原子转变为其他稳定相或非晶态,代表永久塑性变形。
<图片>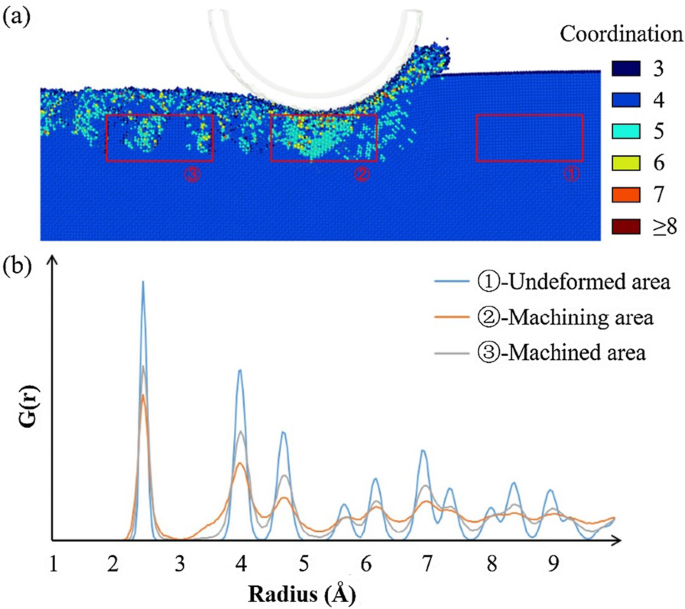
选定区域径向分布函数:a 选定区域; b 对应的径向分布函数曲线
图>切割速度和方向对次表面变形的影响
表层/次表层损伤的形成受多种因素的影响,不同的切削参数会影响位错的形成。
图 11a-c 中比较了不同切削速度下的位错分布。随着切削速度的增加,位错密度逐渐降低。加工过的次表面富含位错,尤其是当切削速度降至 200 米/秒时。当切削过程处于高应变率下时,位错形核和扩展的时间不足。因此,位错较少,由位错引起的塑性变形也不太占主导地位。材料会迅速变形和紊乱,恢复时间也短,更容易形成结构不规则的非晶原子。因此,较高的切削速度是抑制位错形成的一种方式。图 11d-f 是三个相应模型中 von Mises 应力分布的横截面视图。在较高的切削速度下,由于切削能量较大,刀具附近材料的应力相对较高。比较这三种模型,800 m/s 模型在刀具前具有更高的应力集中,并且加工过的次表面呈现出具有更高值的更连续的应力区域。相反,由于低速模型中位错的形成,应力被释放。位错引起的塑性变形会释放局部应变能和晶格弯曲和弹性变形引起的应力。因此,在切削速度较高的工件中,由于没有位错,应力状态会很严重,更容易在切削过程中形成裂纹。
<图片>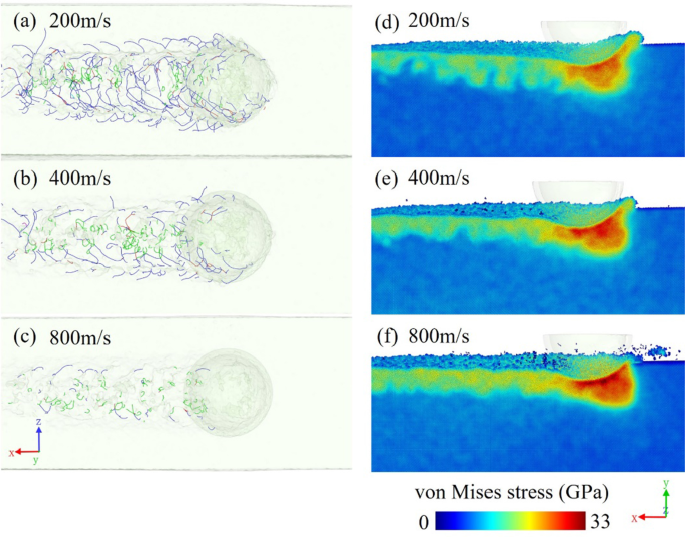
a不同切削速度的模型中位错分布和von Mises应力分布透视图 , d 200 米/秒,b , e 400 m/s 和 c , f 800 米/秒
图>各向异性是晶体纳米切割过程中的一个严重问题 [26, 27],包括单晶砷化镓。由于其单晶结构,砷化镓晶体在不同的晶体取向上表现出不同的特性。建立了三个具有不同切割平面和方向的模型来研究各向异性。切割方向为 (010)[\(\overline{1}\)00], (\(\overline{1}\)10)[\(\overline{1}\)\(\overline{1}\ )0] 和 \((\overline{2}11)\,[\overline{1}\overline{1}\overline{1}]\)。图 12a-f 反映了位错分布之间存在的巨大差异。如上所述,(010)[\(\overline{1}\)00] 模型中存在两种位错。当切削方向沿\((\overline{1}10)\,[\overline{1}\overline{1}0]\)方向时,大部分位错位于加工槽的底部,而一些聚集的位错延伸到工具前面的表面。在图 12b 的侧壁两侧几乎没有发现位错。在\((\overline{2}11)\,[\overline{1}\overline{1}\overline{1}]\) 切割方向,观察到从中间向两侧延伸的树状位错,覆盖加工的地下,如图 12c 所示。然而,与第一个模型不同的是,\((\overline{1}10)\,[\overline{1}\overline{1}0]\) 和 \((\overline{2} 11)\,[\overline{1}\overline{1}\overline{1}]\) 模型,并且大多数位错是沿 [110] 方向的完美位错。同样,在\((\overline{1}10)\,[\overline{1}\overline{1}0]\) 和\((\overline{2}11) 的加工区域也没有发现堆垛层错\,[\overline{1}\overline{1}\overline{1}]\) 模型,对应缺少部分位错。这也证明了材料各向异性的影响。
<图片>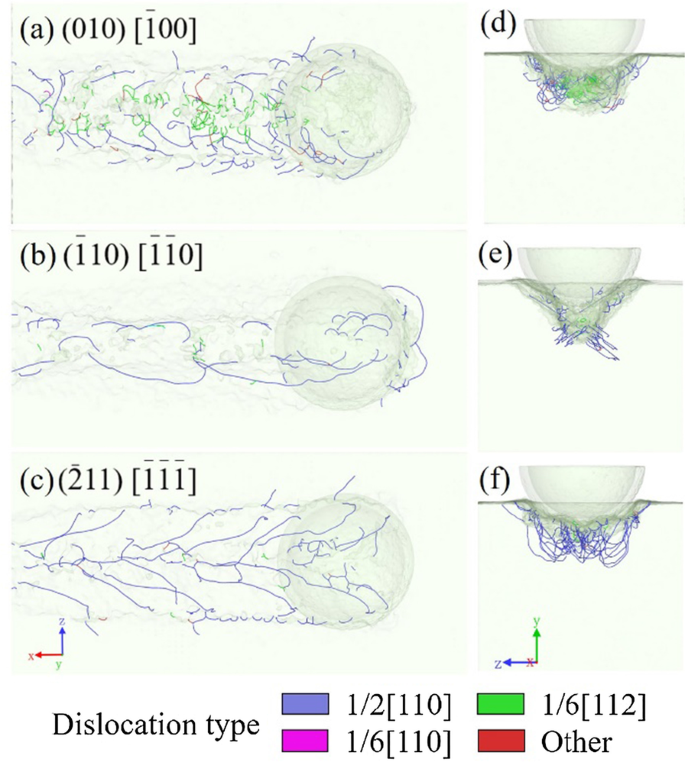
沿 a 切割方向的模型中位错分布的透视图 , d \((010)\,[\overline{1}00]\), b , e \((\overline{1}10)\,[\overline{1}\overline{1}0]\) 和 c , f \((\overline{2}11)\,[\overline{1}\overline{1}\overline{1}]\)
图>图 13a-f 比较了三种不同切削方向模型的位错分布和 von Mises 应力分布。晶体取向对应力传播有明显的影响。在 (010)[\(\overline{1}\)00] 和 \((\overline{2}11)\,[\overline{1}\overline{1}\overline{1}]\) 模型中,应力集中在金刚石刀具前方,但延伸方向不同。但是\((\overline{1}10)\,[\overline{1}\overline{1}0]\)模型的应力集中区域更宽,工具前方的高应力区域延伸到表面。由于晶体取向的不同,沿滑移方向的应力分量会不同,从而导致位错的出现不同。当应力方向与滑移面的夹角较小时,更容易出现滑移,材料会发生塑性变形。相反,当垂直于解理面的拉应力与沿滑移面的剪应力之比增大时,裂纹和脆性断裂趋于萌生。
<图片>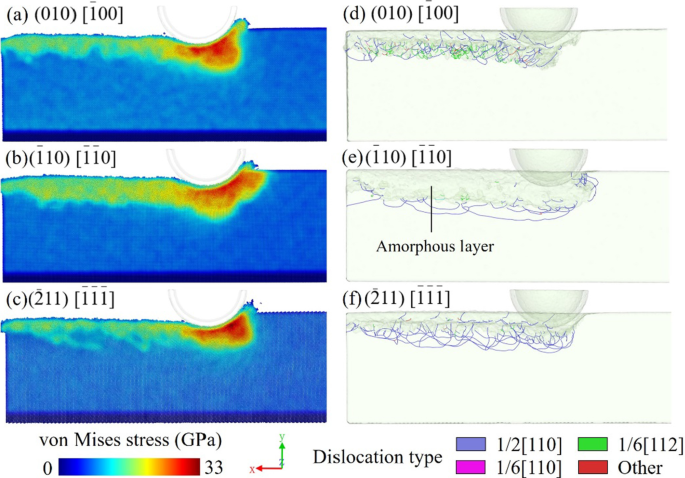
沿a切割方向的模型中的Von Mises应力分布和位错分布 , d \((010)\,[\overline{1}00]\), b , e \((\overline{1}10)\,[\overline{1}\overline{1}0]\) 和 c , f \((\overline{2}11)\,[\overline{1}\overline{1}\overline{1}]\)
图>比较应力和位错分布,具有较高位错密度的模型可能在加工的次表面具有较低的应力。图 13e 显示了 \((\overline{1}10)\,[\overline{1}\overline{1}0]\) 模型的次表面较厚的非晶损伤层,对应于其他型号。这种现象表明各向异性可能对损伤类型有影响。在\((\overline{1}10)\,[\overline{1}\overline{1}0]\)模型中,由于位错形成较少,集中应力难以释放。结果,在严重的应力状态下,原子的排列受到干扰。加工过的次表面应力范围较大,残余应力较高。相反,\((\overline{2}11)\,[\overline{1}\overline{1}\overline{1}]\) 模型由于较大位错密度。位错的形成释放了切削过程中的部分应力。在之前的研究中[18],当韧性损伤模式从位错转变为非晶化时,加工后的次表面呈现出严重的应力状态和非晶损伤。在非晶和单晶的边界处更容易形成亚表面裂纹。可以推断,当切割方向沿着\((\overline{1}10)\,[\overline{1}\overline{1}0]\)方向时,裂纹更容易发生。位错的形成可以减少脆性损伤的形成。除了解理机制外,这也是裂纹形成受各向异性影响的一个原因。
在切削过程中,靠近刀具的材料受到高应力和剧烈压缩,会引起材料相变、非晶化等结构变化。在非晶层之下,由于广泛的应力效应,将在更大的区域发生滑移,并且在单晶中会形成位错。这些是砷化镓纳米切割中的主要延性变形。不同的切削条件会影响局部应力状态和位错形成的难易程度。当由于加工速度快或各向异性而难以产生位错时,由于未释放应力引起的非晶化,塑性变形模式将趋于以非晶为主。在这种情况下也容易形成裂纹。相反,如果条件适合材料滑移,位错将是塑性变形的主要成分。
结论
MD模拟用于研究砷化镓晶体纳米切割过程中损伤形成的机制。还分析了该过程的原子运动和切削力。 The dislocation, stacking fault, and phase transformation are mainly studied as the surface/subsurface damages. The conclusions can be summarized as follows:
- 1.
In the nano-cutting of gallium arsenide, the dislocation and structural transformation are found as the main deformation mechanism in the machined subsurface.
- 2.
Dislocations and stacking faults are observed in the machined subsurface groove, and the formations of stacking faults and partial dislocations are consistent.
- 3.
An intermediate phase with five-coordination is found in front of the tool because hydrostatic stress is close to but not higher than the transition threshold (17 GPa). An amorphous layer forms in the machined subsurface.
- 4.
With increasing cutting speed, the dislocation density decreases because of the high strain rate. Anisotropy has a great effect on the dislocation type and density. Partial dislocations are easier to form in the (010) [\(\overline{1}\)00] model. Moreover, the \((\overline{1}10)\,[\overline{1}\overline{1}0]\) model has a lower dislocation density and a more severe amorphization.
数据和材料的可用性
The datasets generated or analysed during the current study are not publicly available due the data also forms part of an ongoing study, but are available from the corresponding author on reasonable request.
缩写
- MD:
-
分子动力学
- GaAs:
-
Gallium arsenide
- FE:
-
Finite element
- FCC:
-
Face centered cubic
- Tersoff-ZBL:
-
Tersoff-Ziegler–Biersack–Littmark
- LAMMPS:
-
大规模原子/分子大规模并行模拟器
- OVITO:
-
Open visualization tool
- NPT:
-
Number-pressure–temperature, isothermal-isobaric ensemble
- NVE:
-
Number-volume-energy, microcanonical ensemble
纳米材料