智能制造需要流程改进
前言
业界常说,要实现工业4.0,还有很多东西要学。在需要学习的知识中,工艺是最基础的,也是最先被理解的。
在工厂的整个生产过程相关业务中,工艺工作处于基础和领先地位。如果说设备是工厂的肌肉,传感器和网络是工厂的神经,那么工艺就是工厂的灵魂。因此,改进工艺势在必行。
1。 流程工作的改进应从现有流程的精益优化入手,实施流程标准化,推进流程精益化,研究流程稳健性。
无论是传统的生产方式,还是工业4.0环境下的智能工厂,都需要精益稳定的制造流程。这也是我们目前解决效率和质量问题的根本途径。
所谓智能工厂的“智能”,是由技术人员根据具体业务流程提炼出一系列判断因素和思维逻辑形成的,是人类智能无法比拟的。因此,其对制造工艺的要求远高于传统的生产方式。在当前条件下,不完善的工艺只会导致生产效率低下,产品质量不稳定。但在工业4.0的环境下,不稳定的工艺流程会出现不可预知的错误,从而导致智能工厂停运,损失惨重。
2。 为了使流程精益化和稳定,我们不能再使用依赖实际生产的验证方法。
相反,我们必须引入工业4.0的一个重要概念——数字孪生体,即将真实的环境和状态整合到虚拟的数字空间中。模拟它来创建一个与真实工厂完全一样的虚拟数字工厂。虚拟现实环境用于验证、反馈和改进流程、流程和计划。无论是加工过程的细节,还是宏观工艺布局规划的运作,都可以在虚拟数字化工厂进行验证测试,将大大提高工作的成熟度,节省大量的时间和资源。
我们已经开始在铸造、焊接、钣金、机械加工等技术上使用模拟,但目前应用范围较小,标准化程度还不够。之后,要制定详细的计划,建立仿真环境,扩大仿真模拟。在现场,仿真确实有效,逐步实现了对整个环境的实时仿真。
3. 改变技术思维。
一切变化都源于思想的变化。传统工匠的主要工作是编制单一工序的工序规程。未来工艺技术人员的主要工作将是提炼工艺思维逻辑,不断补充、完善和优化庞大的工艺数据库,维护工艺知识数据,实际的工艺设计工作可能由计算机完成。
流程过程将不再是单一流程的形式,而是多个流程的离散流程流。在保证产品质量的情况下,工艺路线尽可能灵活,为智能工厂的决策系统提供尽可能多的资源。通过综合分析各种影响因素,选择并安排最佳路线。
过时的传统工艺理念也应该被淘汰。最典型的就是夹紧对齐和车身公差的打标习惯。
在目前的生产过程中,机床上的装夹和找正浪费了大量的机床工作时间,严重影响了生产效率。由于加工精度的不断提高和机床功能的增加,可以通过精密定位夹具和机床的自对准功能来解决装夹和找正问题。
标记体内公差的习惯,是因为过去使用普通机床加工,以减少人工加工超差的概率,提高产品合格率。这使得产品的实际加工尺寸偏离正态分布,不利于保证大宗产品的质量稳定性。
目前CNC加工 设备得到了广泛的应用,加工精度比以前有了很大的提高。工艺尺寸不再需要使用体内公差标记。
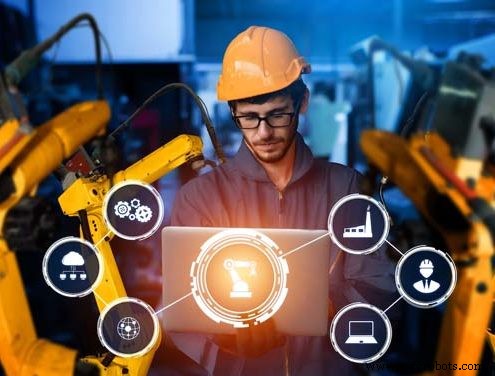
4.研究机器人和快换夹具的应用。
工业 4.0 想要实现的智能不是取代人。智能工厂不是无人工厂,而是让人与机器协同工作,实现更高的劳动生产率。
为此,在智能工厂中,必须努力消除人为不稳定因素。根据制造业现状,实现高度无人化生产既不现实也不经济。在适当的环节引入机器人是提高稳定性和效率的最佳选择。使用机器人和快换治具,可以适应多品种小批量的生产,在保证灵活性的同时提高生产效率和稳定性。
5. 整合现有流程信息系统,实现单一数据源,确保互联互通。
实现所有业务在统一平台下运营是工业4.0的重要目标之一。此前,我们在信息化建设,尤其是流程信息化方面投入了大量资源。在各项业务中,流程信息化水平都比较高。但现有的信息化建设缺乏整体规划,各信息系统相对独立,信息资源不共享,形成信息孤岛,对提升整体业务效率构成较大障碍。所以,现在我们有必要站在公司整体的层面,把流程信息系统整合到一个统一的平台上,真正发挥信息系统的作用。
在实现工业4.0的道路上,我们还有很长的路要走,还有很多知识要学,但这些都不是问题。只要我们抓住机遇,制定切实可行的方案,一步一个脚印地往前走,在这个过程中,我们就能提升自己,让工业4.0离我们越来越近。
相关文章:工业 4.0 如何影响 CNC 加工
制造工艺