基于实际粒子模型的 HCCI/ZTAP 耐磨复合材料中陶瓷几何结构的数值优化
摘要
为了降低氧化锆增韧氧化铝(ZTA)陶瓷颗粒增强的高铬铸铁(HCCI)基复合材料的热应力,进行有限元模拟以优化陶瓷的几何构型。之前的模型简化了陶瓷颗粒预制棒的整体结构,并增加了边界条件来模拟颗粒,这会导致结果出现不可控的误差。在这项工作中,等效晶粒模型用于描述实际预制件,使模拟结果更接近实际实验结果。模拟复合材料的凝固过程,实现铁水与陶瓷颗粒之间的渗透。得到凝固过程中的热应力和压缩应力分布。结果表明,在预制件上增加10mm圆孔可以提高复合材料的性能,有利于防止裂纹的产生,增加材料的塑性。
介绍
随着工业化进程的不断推进,传统的单一耐磨材料逐渐难以满足冶金、电力、建材等领域对耐磨件的性能要求[1, 2]。陶瓷颗粒增强金属基复合材料,如氧化锆增韧氧化铝(ZTA)陶瓷颗粒增强的高铬铸铁(HCCI)基复合材料(以下简称HCCI/ZTAP复合材料)是最流行的耐磨材料之一。将ZTA陶瓷的高硬度与HCCI优异的韧性完美结合,充分利用两者的互补关系,赋予金属基复合材料优异的耐磨性[3, 4]。
HCCI/ZTAP复合材料仍有一定的开裂倾向,可能影响产品的外观和稳定性[5,6,7]。复合材料的开裂与塑性和应力条件有关。优异的塑性和较低的热应力可以降低复合材料开裂的可能性[8]。如果陶瓷颗粒与金属之间的热膨胀系数差异过大,复合材料中的热应力会相应增加。当热应力高时,复合材料内部可能会产生裂纹,特别是在陶瓷颗粒和金属之间的界面处。裂纹的不断延伸和扩展最终可能导致复合材料断裂甚至整层剥落[9, 10]。 HCCI/ZTAP复合材料也存在上述问题。当熔融金属渗入聚集颗粒中时,温度降低,导致金属与陶瓷颗粒的结合能力差。因此,为了进一步提高HCCI/ZTAP复合材料的性能,研究并降低其开裂倾向具有重要意义[11, 12]。
在HCCI/ZTAP复合材料中,复合层设计为工作面,其余基体为金属,使复合材料同时具有较高的耐磨性和塑性[13]。在HCCI/ZTAP复合材料中采用渗透法制备复合层。复合材料的显着特征之一是其可设计性 [14]。根据实际需要,将陶瓷颗粒制备成具有特殊结构和尺寸的预制件,然后将预制件与熔融金属紧密结合制备ZTAP/HCCI复合材料[15]。
为了降低热应力,我们选择了六边形陶瓷颗粒预制件。在六角形预制件中,熔融金属渗透预制件的最大距离与方向无关,因此提高了金属渗透的均匀性,减少了预制件中的应力集中[16, 17]。尽管采用六角形预成型件来降低材料开裂的倾向,但材料成型过程中的热应力仍然存在。改善陶瓷颗粒预制件的结构可以有效降低应力集中。
在复合预制件结构的优化中,有限元法可以减少重复实验。在以往的研究中,由于陶瓷颗粒绘制和计算的复杂性,通常将陶瓷颗粒预制件作为一个整体进行简化。深入研究发现,简化模型存在一些缺陷,不能在更广的范围内使用。等效粒子模型的建立可以进一步将模型与实际情况相结合,减少模型带来的误差[18]。采用有限元分析软件 COMSOL Multiphysics 方法对 HCCI/ZTAP 复合材料凝固过程和压缩过程中的应力场进行建模[19]。 COMSOL Multiphysics 是一款大型高级数值仿真软件[20, 21]。
在论文中,我们使用有限元软件来模拟不同条件下复合材料的应力。本文使用的 COMSOL Multiphysics 版本为 4.5a。本研究系统地分析了有限元软件中的几何模型对计算结果的影响,有利于多孔预制件的设计和开发。仿真与实验对比,不断优化模型。
方法
复合材料生产中的主要问题之一是应力集中,它直接影响复合材料的耐磨性和塑性。改善陶瓷颗粒预制件的结构可以有效降低应力集中。本研究旨在探讨预制件结构对应力分布的影响,提高复合材料的性能。
几何模型的建立与优化
在凝固过程中,结晶器与液态金属的温度不同,液态金属凝固较快,因此铸造过程中各位置之间的传热是不稳定的,传热方程可写为[22]:> $$\rho C_{{\text{P}}} \frac{\partial T}{{\partial x}} =\frac{\partial }{\partial x}\left( { \lambda \frac{\部分 T}{{\partial x}}} \right) + \frac{\partial }{\partial y}\left( { \lambda \frac{\partial T}{{\partial y}}} \right) + \frac{\partial }{\partial z}\left( { \lambda \frac{\partial T}{{\partial z}}} \right) + \rho Q$$ (1)
其中 \(\rho\) 是密度; \(C_{{\text{P}}}\) 是热容; \(\lambda\) 是热导率; T 是瞬态温度; 问 是热;坐标 x , y , 和 z 称为子系统的相对坐标。
由于凝固过程中各点的温度不同,铸件内部存在可变的内应力。如果铸件可视为线弹性体,当内应力小于屈服极限时,随着弹性变形过程,可用虎克定律方程来描述。
$$\left\{ {\begin{array}{*{20}l} {\varepsilon_{xx} =\frac{1}{E}\left[ {\sigma_{xx} - v\left( {\ sigma_{yy} + \sigma_{zz} } \right)} \right]} \hfill \\ {\varepsilon_{yy} =\frac{1}{E}\left[ {\sigma_{yy} - v\ left( {\sigma_{xx} + \sigma_{zz} } \right)} \right]} \hfill \\ {\varepsilon_{zz} =\frac{1}{E}\left[ {\sigma_{zz } - v\left( {\sigma_{xx} + \sigma_{yy} } \right)} \right] \to \varepsilon_{ij} =\frac{1 + v}{E}\sigma_{ij} - \frac{v}{E}\delta_{ij} \sigma } \hfill \\ {\varepsilon_{xy} =\frac{1}{2G}\sigma_{x} } \hfill \\ {\varepsilon_{yz } =\frac{1}{2G}\sigma_{yz} } \hfill \\ {\varepsilon_{zx} =\frac{1}{2G}\sigma_{zx} } \hfill \\ \end{array} } \right.$$ (2)其中 E 是杨氏模量; \(\sigma =\sigma_{{ii + \sigma_{11} }} + \sigma_{22 + } \sigma_{33}\); \(v\) 是泊松比;单位张量 \(\varepsilon_{ij} =\frac{1}{2}\gamma_{ij}\);剪切模量 \(G =\frac{E}{{2\left( {1 + v} \right)}}\).
则内应力大于屈服极限,铸件变形较大。总应变由弹性应变和塑性应变组成,\(\sigma_{ij} =\sigma_{ij}^{e} + \sigma_{ij}^{p}\)。该方程可视为弹塑性线性硬化模型。弹性变形和塑性变形是线性的,本构方程可以写成[23]:
$$\sigma =\left\{ {\begin{array}{*{20}l} {E\varepsilon } \hfill &{\varepsilon \le \varepsilon_{{\text{s}}} } \hfill \ \ {\sigma_{{\text{s}}} + E_{1} \left( {\varepsilon - \varepsilon } \right)} \hfill &{\varepsilon> \varepsilon_{{\text{s}}} } \hfill \\ \end{array} } \right.$$ (3)其中 \(\sigma\) 是应变; E 是杨氏模量; \(\varepsilon\) 是压力; \(\varepsilon_{{\text{s}}}\) 是屈服强度。
高铬铸铁工件由于耐磨性差,使用寿命较短。复合材料与单一 HCCI 相比具有许多优点。在HCCI/ZTAP复合材料的制造过程中,ZTA陶瓷颗粒预先制备成多孔预制件。预成型使ZTA陶瓷颗粒与HCCI结合更紧密,陶瓷颗粒在受到冲击时不易脱落。为了进一步提高HCCI/ZTAP复合材料的性能,需要优化预制件的结构。
在铸造过程中,熔融金属可以填充圆孔,增加金属的比重。在HCCI/ZTAP复合材料的应用过程中,发现颗粒聚集位置更容易开裂,因此在该位置增加了圆孔。
ZTA陶瓷颗粒形状为任意多边形,预制件中颗粒较多。如果所有的粒子都画出来,工作量就大了。在先前对陶瓷金属基复合材料的模拟中,大多数陶瓷颗粒的预制件被视为一个整体。如图 1 所示,本文分别建立了宏观和微观模型。建立一个合理的模型需要反复与实验相互验证。在优化模型中,计算结果与实验结果吻合较好。模拟结果包括铸件在载荷作用下的热应力、温度场、凝固过程中的相变场和应力应变。对建立的有限元模型进行合理有效的调整,使优化后的有限元模型能够在更广的范围内使用。
<图片>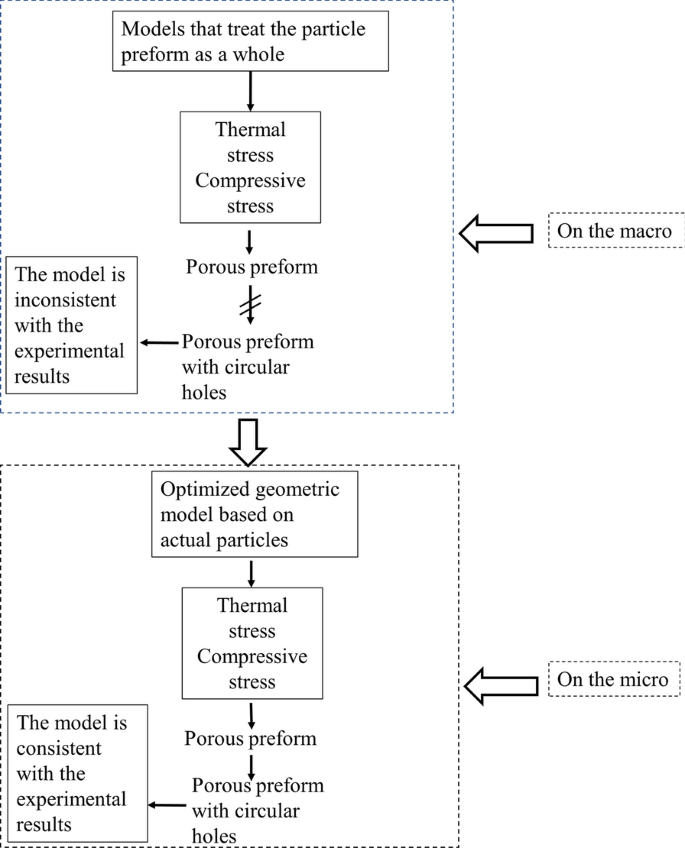
HCCI/ZTAP材料几何模型优化流程图
图>在使用有限元软件建立几何模型时,为了减少计算时间和建模工作量,经常使用简化的几何模型。如图 2 所示,由于将三维六边形多孔预制件简化为二维模型,并且仅选择一层颗粒来投影二维模型,因此颗粒之间存在间隙。这样,粒子在三维空间中的堆积可以有效避免对二维几何模型的影响,合理简化模型,提高计算效率。
<图片>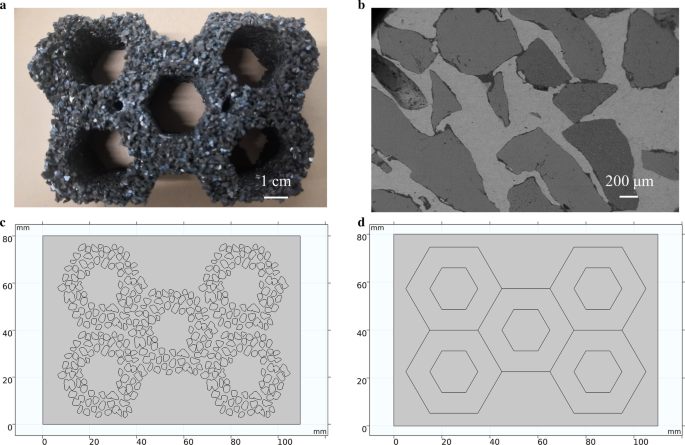
ZTA陶瓷颗粒和HCCI/ZTAP复合材料的几何模型。 一 多孔性能,b HCCI/ZTAP复合材料的复合区,c 基于实际粒子的优化几何模型,d 初始几何模型
图>本文选择ZTA陶瓷颗粒作为复合材料的增强相。 ZTA陶瓷颗粒是在氧化铝中加入氧化锆并烧结而成的多相结构陶瓷,其中氧化锆的质量分数为18%,氧化铝的质量分数为82%。高铬铸铁是复合材料的基体,含铬12%以上,是一种优良的耐磨材料。
材料参数对有限元计算结果影响很大。本文模拟计算所需的材料参数是通过实验和文献获得的。 ZTA陶瓷颗粒和HCCI的材料参数如表1所示。
图>实验
为了测试HCCI/ZTAP复合材料的塑性和耐磨性,对复合材料进行了系统测试,进一步确定了预制件结构的影响。 SHT4305万能试验机用于测量HCCI/ZTAP复合材料的压缩性能。压缩试验样品尺寸为10 × 10 × 25 mm,施加载荷为30吨,压缩速度为0.5 mm/min。
HCCI/ZTAP复合材料的耐磨性测试是必要的。优异的耐磨性是检验耐磨复合材料性能的最重要标准。 HCCI/ZTAP复合材料主要用于选矿、水泥制造、造纸等行业,大部分工况为三体磨粒磨损。为了尽可能模拟HCCI/ZTAP复合材料在实际工况下的使用性能,采用MMH-5型三体磨粒磨损试验机对HCCI/ZTAP复合材料进行了测试。测试仪履带材质为M2工具钢,硬度820-860 Hv,外径380mm,宽度20mm。根据不同的工况选择磨料的种类和尺寸。本文采用石英砂作磨料,硬度1000~1200 Hv,试验载荷40 N,试样转速30 r/min。
使用纳米压痕仪在选定的 100 × 100 μm 2 中进行 100 点杨氏模量测试 微区。纳米压痕仪型号为iMicro。
材料的耐磨性可以用质量减少、体积减少等来衡量。量筒测量的体积损失变化很小,很容易造成人为读数的误差。因此,在相同磨损条件下,用质量损失Δm来评价材料的磨损性能。材料损耗计算公式如下:
$$\Delta m =m_{1} - m_{2}$$ (4)其中 m 1 和 m 2分别代表磨损前后样品的质量。
结果与讨论
基于简化的整个模型的模拟
在本研究中HCCI/ZTAP复合材料凝固过程中的热应力模拟中,所有模拟结果均选择10 s时的热应力分布,因为10 s前后热应力变化较大。与图 3 右侧的刻度相比,红色表示压力较高,蓝色表示压力较低。在图 3a 中,应力集中出现在预制件的边缘,特别是在中间位置,预制件的上侧和下侧出现红色。与图 3a 的正确比例相比,它表明这里的应力是巨大的。颗粒聚集的地方,也就是六边形孔壁的交点处出现蓝色,说明这里的应力很小。在图 3c 的几何模型中,圆孔被添加到预制件的颗粒聚集体中。图 3c 中的应力分布与图 3a 相似,只是圆孔周围有更明显的应力集中。图4中预成型圆孔周围的应力分布与图3相似
<图片>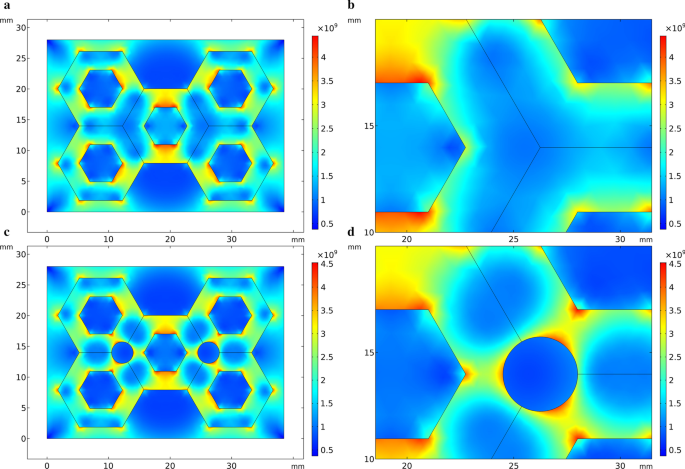
简化模型中凝固过程中的热应力分布。 一 初始执行,b 初始表演的局部放大图,b 添加了圆形孔的瓶坯,d 增加圆孔的表演部分放大图
图> <图片>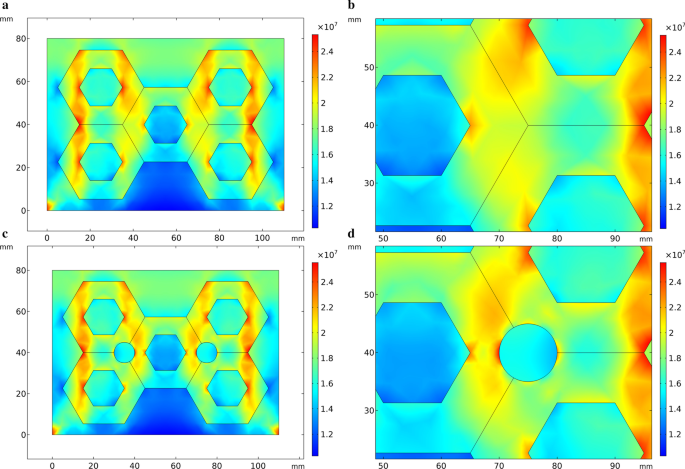
简化模型中的压应力。 一 初始执行,b 初始表演的局部放大图,b 添加了圆形孔的瓶坯,d 增加圆孔的表演部分放大图
图>最终的计算结果需要直观,因此对结果进行了后处理,绘制了应力横向对比图。先在几何模型中画一个二维的横截面,因为主要的观察部分是在圆孔的周围,也就是粒子聚集的地方,所以二维的横截面穿过圆孔。应力图的纵坐标为截面线上的应力值,横坐标为x 模型的轴坐标,如图5所示,在简化模型中,圆孔坐标为(12, 14), (27, 14)。图 5c 是凝固应力的线图。在图 5c 中,与没有圆孔的预制件相比,具有圆孔的预制件在横坐标 12 和 27 处的应力显着增加。图 5d 是压缩应力的对比图。曲线的总体趋势与图5c相同,圆孔的位置应力将显着增加。
<图片>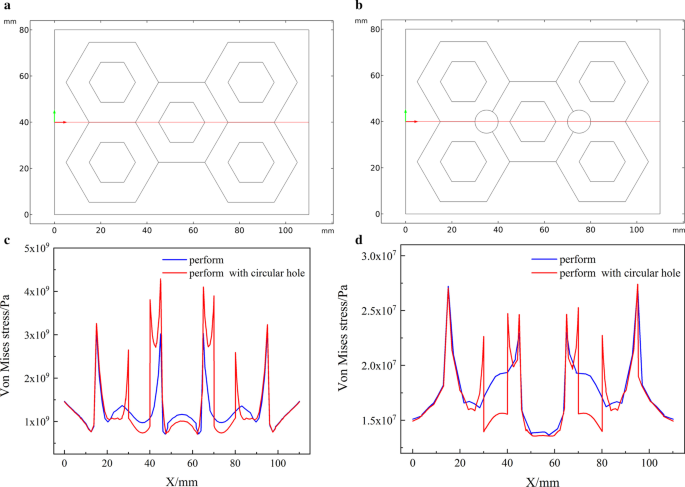
简化模型的二维横向位置和应力横向比较。 一 初始执行,b 初始表演的局部放大图,c 添加了圆形孔的瓶坯,d 增加圆孔的表演部分放大图
图>基于等效颗粒模型的模拟
图 6 显示了基于实际颗粒的 HCCI/ZTAP 复合材料模型的热应力分布,与图 3 类似。但是,在图 6 中,ZTA 陶瓷颗粒不再简化为整体预制件,而是建立为单独的颗粒,可以观察到周围的颗粒大部分呈现红色。 ZTA陶瓷颗粒形状不均匀,应力高于周围值,尤其是颗粒尖点处。图中的热应力分布。 3b和6b明显不同。图 6b 中预制件的圆孔呈蓝色,表明此处应力较小。圆孔周围应力集中的计算结果相反。几何模型的简化程度和绘制方法导致计算结果不同。
<图片>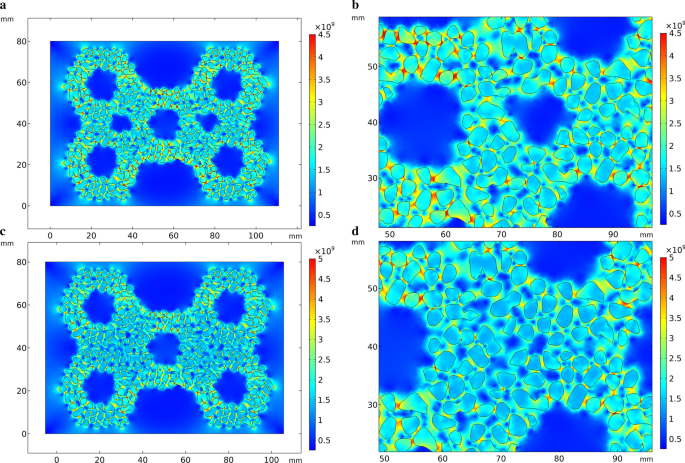
优化模型中凝固过程中的热应力分布。 一 初始执行,b 初始表演的局部放大图,c 添加了圆形孔的瓶坯,d 增加圆孔的表演部分放大图
图>图 7 中用于模拟压应力的几何模型与图 6 类似。图 7 中,与右侧的比例尺相比,应力集中在模型的上部和预制件上,特别是陶瓷瓶坯两侧的边缘,呈黄绿色。在预制件的颗粒聚集部分,该区域在图 7a 中以绿色显示,表明这里的应力很小。在图 7b 中,在预制件的聚集体处添加了圆形孔。圆孔区颜色为绿色和黄色,说明没有明显的应力集中。
<图片>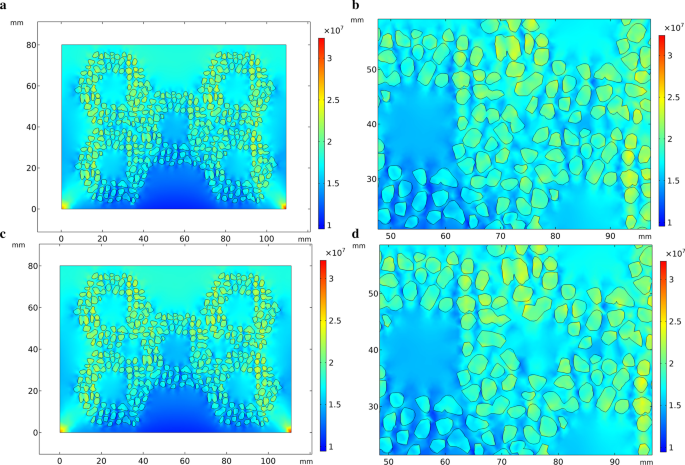
优化模型中的压应力。 一 初始执行,b 优化后的局部放大图,c 添加了圆形孔的瓶坯,d 增加圆孔的表演部分放大图
图>在基于实际粒子的模型中,圆孔坐标为(12, 14) (27, 14)。图8为凝固应力对比图,比较圆孔有无对应力的影响。圆孔预制件的应力在横坐标12和27处显着降低,其位置与圆孔位置基本重合。带有圆孔的预制件剩余坐标的应力有小幅增加。在图 8a、b 中,除了带有圆孔的瓶坯外,两条曲线基本重合;圆孔坐标附近的应力显着下降。
<图片>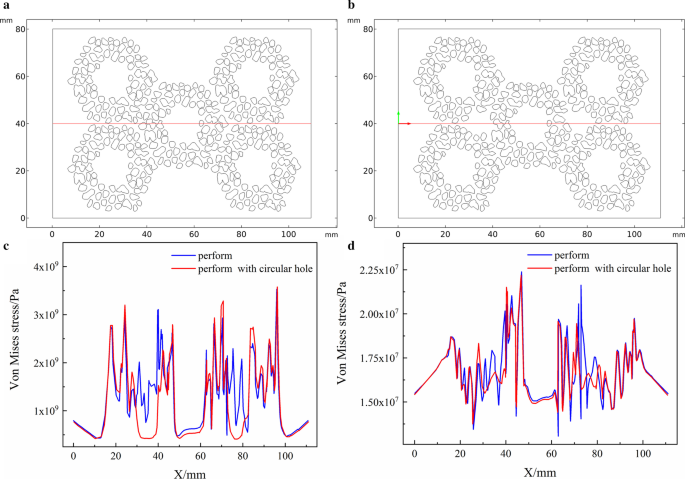
优化模型的二维横向位置和应力横向比较。 一 初始执行,b 添加了圆形孔的瓶坯,c 凝固应力,d 压缩应力
图>实验验证
从图 9 可以看出,在磨损试验中,使用优化预制件的复合材料与使用原始预制件的复合材料的质量损失没有太大差异,表明耐磨性没有显着牺牲,还可以提高HCCI/ZTAP复合材料的整体塑性。
<图片>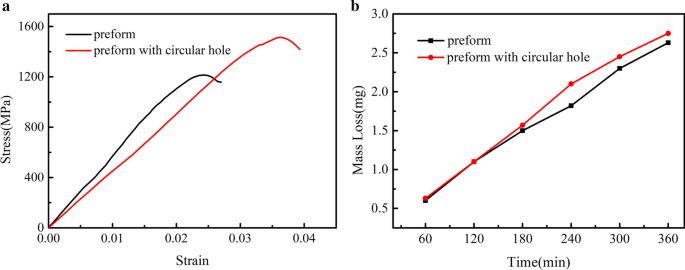
HCCI/ZTAP复合材料压缩应力-应变曲线及复合蜂窝壁交界处三体磨料的质量损失
图>通过在颗粒聚集区添加小尺寸圆柱孔来优化多孔预制件,这改变了 HCCI/ZTAP 复合材料中陶瓷颗粒的体积分数。 ZTA陶瓷颗粒在复合材料中的含量是影响其力学性能的重要因素。如图 9 所示,圆孔预制件的抗压强度和压缩变形量较初始预制件的样品显着增加,说明 ZTA 陶瓷颗粒聚集区的小圆孔有利于提高HCCI/ZTAP 复合材料的强度和塑性。在多孔预制件的团聚区增加小圆柱孔会增加金属基体的含量,从而增加HCCI/ZTAP复合材料在压缩应力下的压缩应变,也影响其压缩强度。当应力达到峰值时,可以认为试样已经发生损伤。随着应变的不断增加,材料的内部损伤也在不断积累,应变阻力逐渐降低,最终发生剪切破坏。
所有样品的硬度显微分析如图10所示。如图10a、b所示,测试区域分别选择在圆形颗粒和尖角颗粒周围,以更好地对应模拟结果。图 10c、d 与应力的局部放大图进行了比较。在模拟中,应力集中往往发生在粒子的尖角周围。试验结果表明,尖角颗粒附近的模量大于圆角附近的金属基体,进一步验证了基于实际颗粒的模型的合理性。
<图片>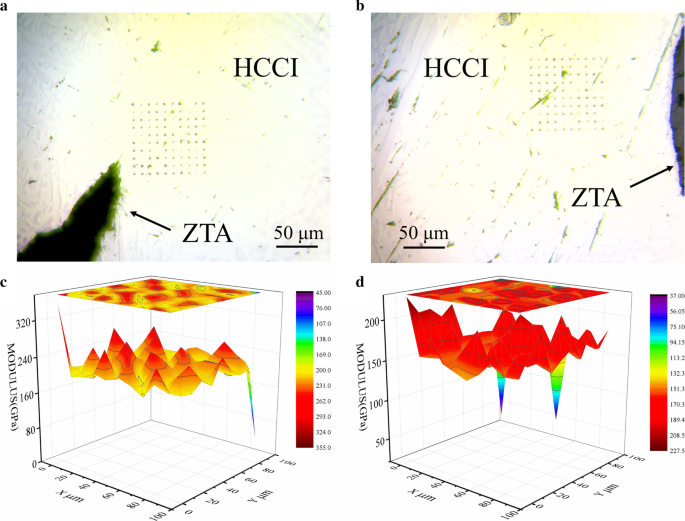
复合材料的压痕分布和复合材料颗粒周围的杨氏模量分布。 一 颗粒形状尖锐,b 颗粒的形状是圆形的,c 颗粒的形状很尖锐,d 颗粒的形状是圆形的
图>在瓶坯的颗粒聚集区增加了一个圆孔,它具有三个功能。第一个作用是降低HCCI/ZTAP复合材料中陶瓷颗粒的体积分数,降低残余应力;第二个作用是减少瓶坯陶瓷颗粒的团聚;第三个作用是增加塑性较好的金属基体的体积分数,阻碍裂纹扩展。 HCCI/ZTAP复合材料的塑性随着残余应力的增加而降低。陶瓷颗粒的体积分数降低,残余应力变小。在 ZTA 陶瓷颗粒预制件中添加圆形孔可以减少裂纹,因为裂纹不稳定性倾向于沿直线延伸。当HCCI/ZTAP复合材料的复合区产生裂纹时,裂纹容易沿预制件中的六边形孔壁延伸,产生裂纹扩展。圆孔增加了六边形孔壁交界处HCCI基体的含量,阻碍了裂纹的扩展,从而起到了增韧结构的作用。
结论
HCCI 和 ZTAP 之间热膨胀系数的巨大差异会导致复合材料出现裂纹。利用有限元软件对HCCI/ZTAP复合材料的凝固和压缩过程进行了模拟,并基于简化的整体模型和预制件等效晶粒模型分析了数值和应力分布。根据计算结果对瓶坯结构进行优化。通过对模拟和实验结果的分析,可以得出结论,在六边形多孔预制件上增加圆形孔将导致凝固过程中的热应力和压应力降低。经过模型的优化和调整,仿真结果与实验结果趋于一致。本文方法可为各种金属基复合材料铸造系统工艺参数的模拟和优化提供重要参考。
数据和材料的可用性
本文包含支持本文结论的数据集。
缩写
- HCCI:
-
高铬铸铁
- ZTA:
-
氧化锆增韧氧化铝
- HCCI/ZTAP:
-
氧化锆增韧氧化铝陶瓷颗粒复合材料增强高铬铸铁基复合材料
纳米材料