复合材料 4.0:数字化转型、自适应生产、新范式
Composites 4.0 是工业 4.0 宇宙中的一个小星系,工业 4.0 是商品和服务设计、生产、交付、运营、维护和退役方式的数字化转型。对于复合材料制造,目标是利用自动化、传感器和数据、5G 通信、软件和其他不断发展的数字技术,使产品和流程更加高效、智能和自适应。
复合材料制造商正在沿着一个范围进行这种数字化转型。初始步骤包括在线检测和优化流程,以减少浪费和成本,同时提高零件质量和产量。更先进的解决方案致力于智能、自主的生产,不仅敏捷,而且响应甚至预期 不断变化的市场和客户需求。
“Composites 4.0 不是终点,而是一种工具,”亚琛工业大学(德国亚琛)AZL 亚琛综合轻量化生产中心董事总经理 Michael Emonts 博士解释说,他的 iComposite 4.0 项目展示了一个自适应流程链将汽车底板成本降低 50-64% 的潜力。
复合材料部件生产商 Dynexa(德国劳登巴赫)的董事总经理 Christian Koppenberg 表示:“仅仅让事情数字化和数字化转型实际上改变了您的业务背后的流程并开辟了新的机会和商业模式,两者之间存在差异。
“复合材料 4.0 不仅仅是使用机器人,”德国航空航天中心 (DLR) 轻量生产技术中心(ZLP,奥格斯堡)的负责人 Michael Kupke 博士断言,该中心开发了配备人工智能 [AI] 的工作单元协作机器人可以从生产复合材料后压舱壁转换为机身面板,无需重新编程或重新培训。 “这项技术可确保您不必教机器人,因为没有商业案例。 Composites 4.0 不仅仅是提高效率和降低成本。公司思考和处理生产方式的改变将决定哪些公司能够生存,哪些不能。”
自适应预成型,RTM
“iComposite 4.0 项目的想法是通过将喷涂的干燥长玻璃纤维(25-30 毫米)结合起来,然后通过自动纤维铺放,用单向 (UD) 碳纤维网格进行加固,用具有成本效益的粗纱和丝束制造预制件(法新社),”埃蒙特斯解释道。 “所选择的演示器,一个后部的车辆底板,以前是用更昂贵的纺织品制成的,这也产生了超过 60% 的废物。”
Composites 4.0 转型需要集成纤维喷涂、纤维沉积和随后的树脂传递模塑 (RTM) 工艺,以便它们相互反应并根据步骤之间测量的零件质量进行调整(图 1)。 “我们使用 Apodius GmbH [德国亚琛] 的机器视觉系统以及光学激光传感器和摄像头模块来表征喷涂瓶坯的表面拓扑结构,”Emonts 说。 “Apodius 调整了软件来分析每个方向的纤维百分比。 iComposite 4.0 系列将其与数字设计进行比较,并确定它是否满足机械要求。如果是,则应用标准 UD 网格进行加固。如果不是,它决定在何处放置额外的 UD 纤维层。”
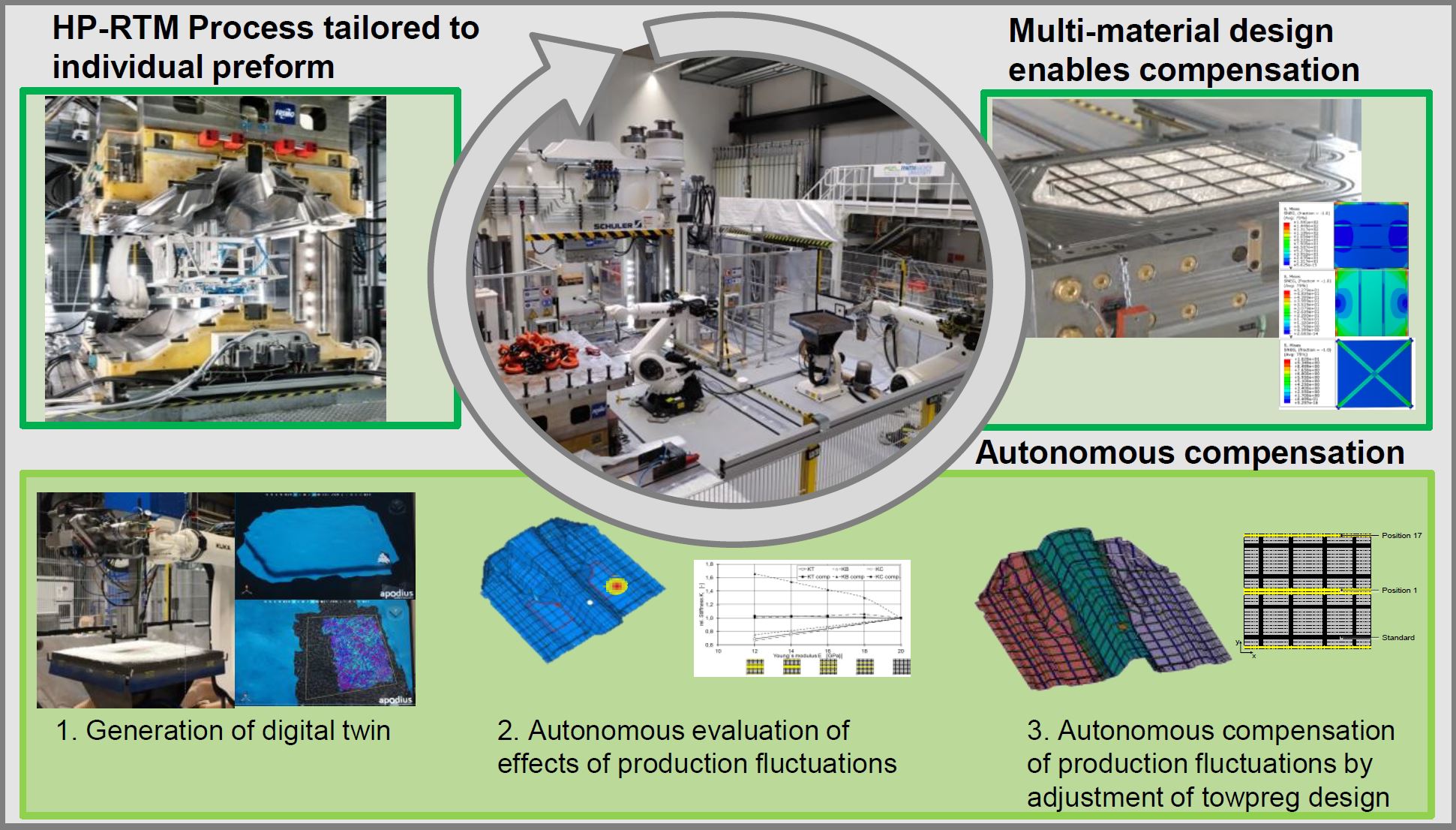
但是,这些额外的 UD 层可能会导致零件厚度和几何形状超出公差。 “因此,”他解释说,“我们将预成型生产线与自适应 RTM 工艺相结合,如有必要,可以通过增加压力机某些部件的压力来调整部件厚度。”这也是自动化的,旨在取代生产线操作员的干预,但它确实需要使用测量数据和标准 FEA 软件来模拟零件性能。
“目前,零件机械性能的模拟是离线进行的,”埃蒙特斯说。 “我们生成了一个过程和零件变化的数据库,创建了对每个变化做出反应的算法,并通过 FEA 验证了这些。因此,基于线路测量的变化,算法指导它执行适当的缓解。为了使生产线就地自适应,下一步将是添加机器学习。”同时,AZL 正在推进众多复合材料 4.0 项目,包括混合热塑性复合材料的自我优化生产和带基剪裁坯料集成硬化的注塑件。
零缺陷 CFRP 机翼蒙皮
ZAero 项目(参见“复合材料零件的零缺陷制造”)是另一个重要的复合材料 4.0 项目,于 2016 年启动。它旨在提高大型碳纤维增强塑料 (CFRP) 结构(例如机翼蒙皮)的生产率。通过使用预浸料 AFP 或 Danobat 的(Elgoibar,西班牙)自动干材料放置(ADMP,请参阅“证明干织物的可行性,大型飞机结构的灌注”)的自动在线检测可以减少缺陷。树脂灌注或预浸料固化过程中的过程监控可以预测固化状态并缩短周期时间。收集的过程和缺陷数据与 FEA 一起用于预测零件性能。然后将其输入到决策支持工具中,以解决已识别的缺陷。开发了 CFRP 机翼蒙皮的零件流动模拟,当输入该工具时,有助于优化返工策略(图 2)。今天,许多此类零件在制造过程中进行返工,但仅在 NDI 之后。 早期返工和改进过程控制确实是 ZAero 项目的目标,也是其目标提高 15% 的生产率、减少 15-20% 的推动因素生产成本和浪费减少 50%。
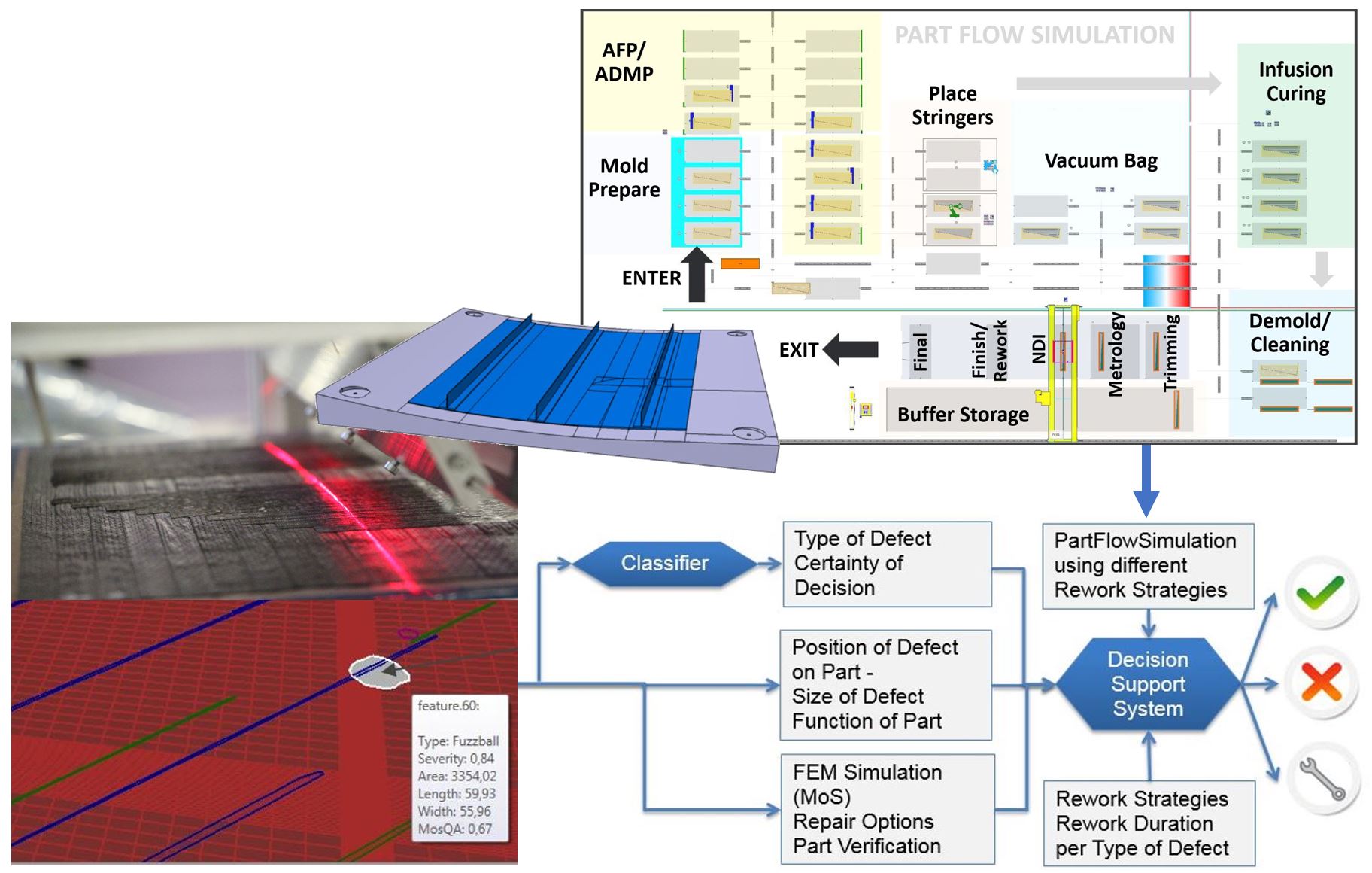
到 2019 年 9 月的最终审查,项目负责人 Profactor(奥地利斯太尔)开发的预浸料 AFP 传感器不仅实现了自动化在线检测,还可以用于原位校正零件。 Profactor 机器视觉主管 Christian Eitzinger 博士说:“该传感器可以检测标准缺陷,例如间隙、重叠、FOD、绒毛球和扭曲的丝束,以及每根丝束的早剪和晚剪。”丢失的丝束可以通过将附加丝束精确放置在被省略的位置来自动纠正。然而,必须停止机器以去除绒毛球或扭曲的丝束。 “使用达索系统(法国巴黎)的 CATIA 3D 体验构建的数据库使我们能够根据缺陷的大小、形状和类型计算对零件性能的影响。处理层中的所有缺陷只需几秒钟。然后机器操作员决定哪些缺陷可以留下,哪些必须返工。”
对于灌注过程监控和控制,空中客车公司(法国图卢兹)与子公司 InFactory Solutions(德国陶夫基兴)合作开发了三个传感器,用于测量温度、固化状态和树脂流动前沿(参见“用于监测树脂灌注流动前沿的传感器”)。 ) “我们已经将这些与 CATIA 3D Experience 集成在一起,并表明可以可靠地获取数据并将其添加到每个零件的数字线程中,”Eitzinger 说。 (请参阅在线侧边栏“复合材料 4.0:数字线程与数字孪生”。)
三部分演示中的最后一个是带有三个纵梁的上机翼盖子部分(参见在线边栏“ZAero 项目更新”)。对于这部分,Profactor 的决策支持工具在合作伙伴 FIDAMC(西班牙马德里)进行了现场演示,该工具连接到基于 Siemens PLM(美国德克萨斯州普莱诺)Tecnomatix Plant Simulation 软件的部件流模拟,该工具在 Profactor 位于奥地利的服务器上运行。除了构建缺陷数据库之外,ZAero 还进行了机器学习实验。手动设计的生成计算机模型结合深度神经网络检测和分类缺陷,在真实的 ADMP 监测数据中实现了 95% 的不同区域(间隙、重叠、拖曳、模糊球)的正确分类率,即使在 人工创建的缺陷数据用于深度网络训练(类似于如何针对一系列故意缺陷校准超声波检测系统)。
“我们肯定会追求某种形式的下一阶段,”Eitzinger 说。同时,Profactor 正在将用于自动铺设过程中的纤维取向和缺陷的模块化传感器商业化。 InFactory Solutions 还提供其 AFP 和树脂灌注传感器,纤维铺放合作伙伴 Danobat 和 MTorres(西班牙纳瓦拉的 Torres de Elorz)现在正在销售具有集成在线检测功能的设备。
Dynexa 的数字化转型之旅
Dynexa 是一家复合材料零件制造商,专门生产 CFRP 管和轴。 “我们一直试图将一切数字化,”总经理 Koppenberg 说。 “我们已经摆脱了手动和模拟流程,将大部分内容集成到我们的 ERP [企业资源规划] 系统中。但我们如何在制造业中做到这一点?我们明白,我们放入工作协议或程序的一切都是代码,这是数字化转型的基础。但是它存储在哪里?在本地服务器上,在云端还是在机器内?我们会问五个人,得到七个关于我们应该做什么的答案。” (参见在线侧边栏,“复合材料 4.0:从哪里开始?”)
幸运的是,德国政府已经为大学设立了一项计划,为中小企业(SME)提供免费的工业 4.0 咨询。 Dynexa 开始与达姆施塔特“Mittelstand (SME) 4.0”能力中心合作。 “他们说不要担心数字架构,而要多看看你需要测量什么以及如何做到这一点,”Koppenberg 回忆道。 “我们选择了一个涉及大量人工测量的流程,我们知道在这个流程中我们存在质量、时间和成本问题。”
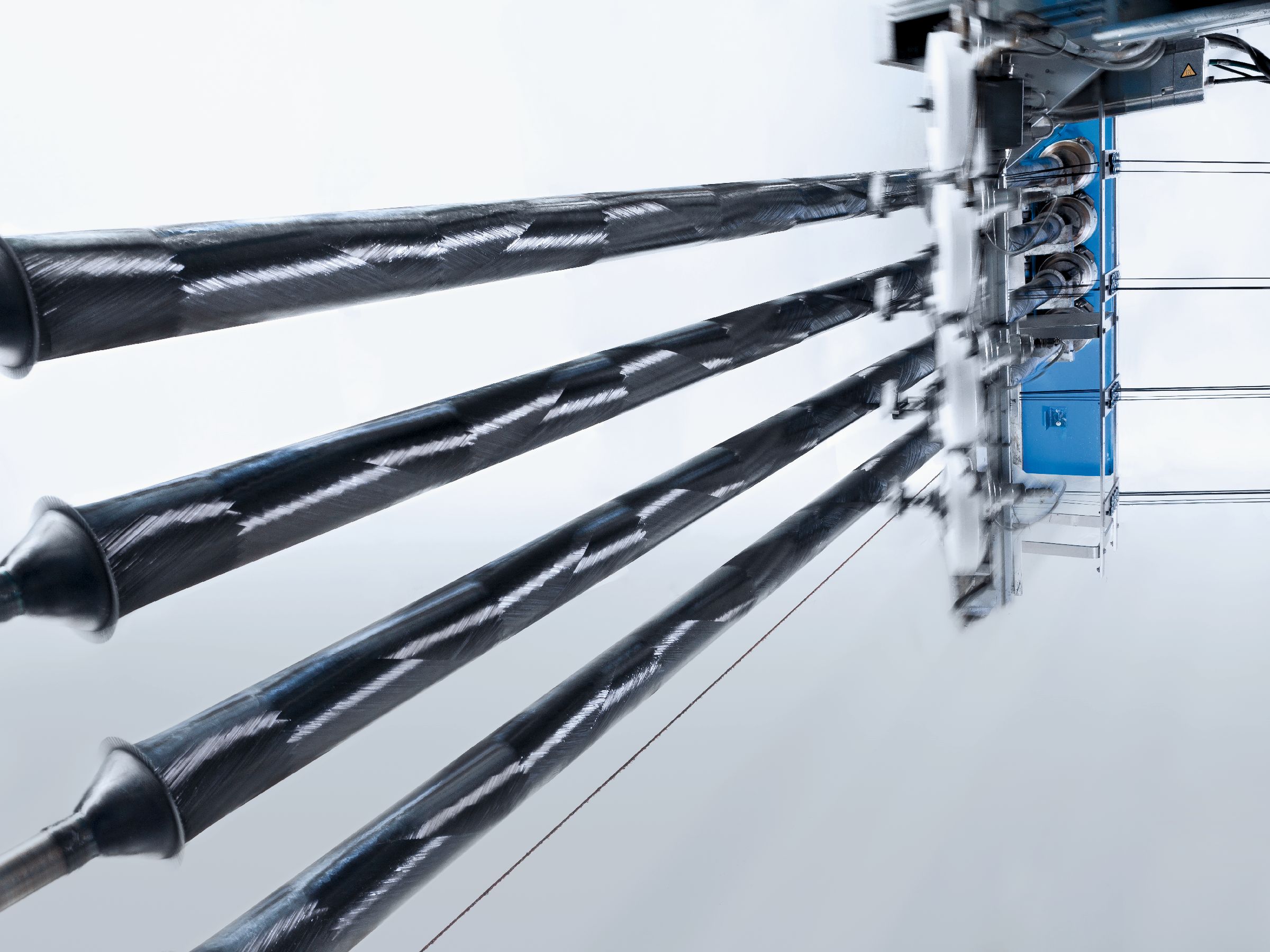
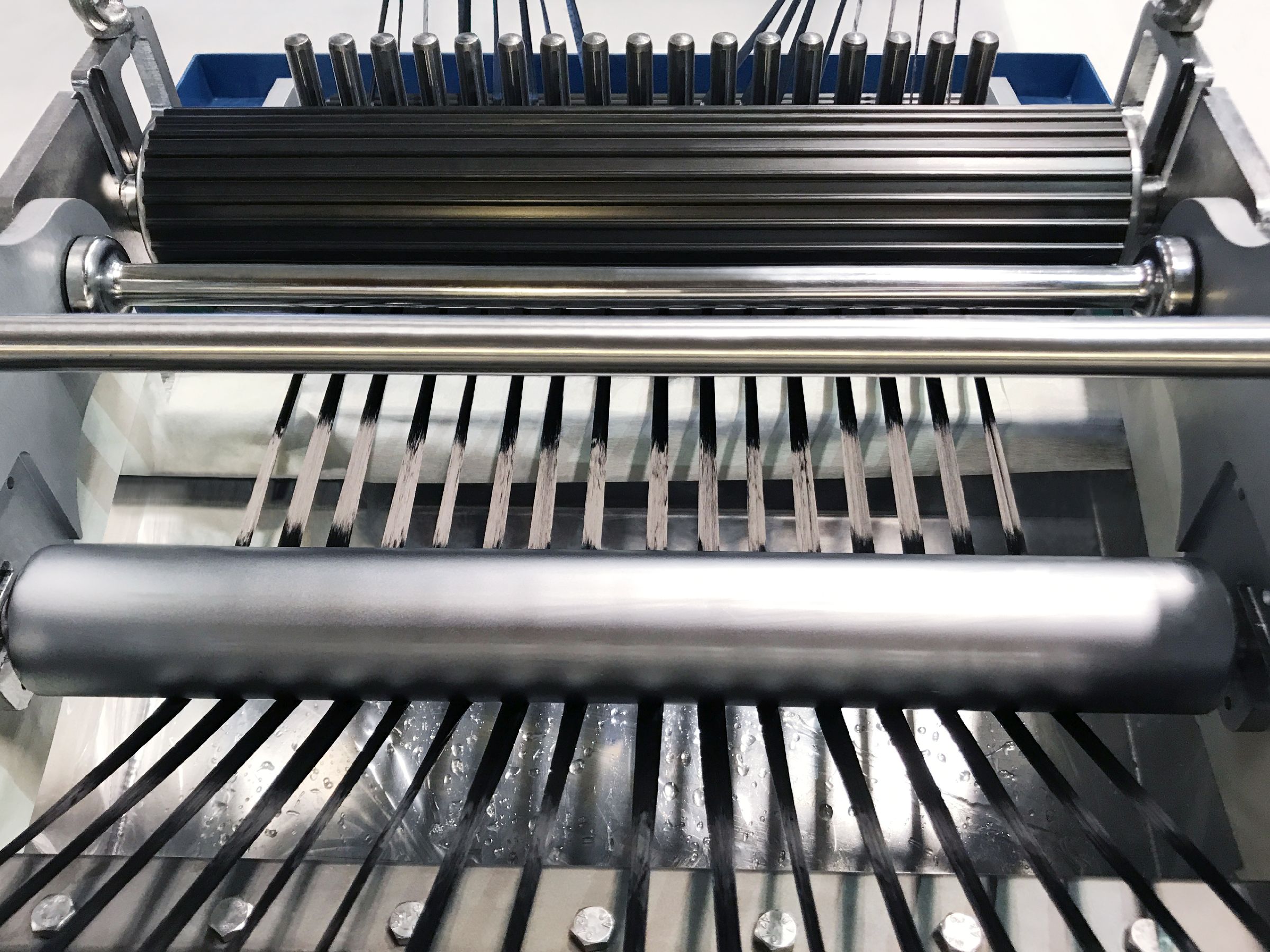
Dynexa 使用湿法长丝缠绕工艺。(参见“准备用于汽车试验场的复合输出轴。)”关键步骤是树脂拾取,其中干纤维运行到压实辊上,压实辊从树脂浴中滚出。紧靠压实辊的是一个刮刀,它决定了在缠绕之前与干长丝结合的树脂量。 “如果我们吸取太多树脂,我们可能会超过规定的管径,”Koppenberg 说,“但如果树脂太少,我们就有可能跌落到允许的最小直径以下。”
“如果不进行测量,你只能知道固化后的最终直径,当所有的价值都已经投入时,”他指出。 “因此,操作员必须停止机器,测量零件,将其记录下来,然后重新启动。根据多年的经验,我们知道在每个缠绕阶段的层压板厚度应该是多少。因此,操作员比较测量结果并根据需要调整刮刀以纠正树脂拾取,但这非常手动,并且依赖于操作员的技能和经验。”
为了将其数字化,Dynexa 与无数激光和相机制造商进行了交谈。 “他们会说,‘我们有解决方案’,但没有人能够让它发挥作用,”科彭伯格指出。然而,达姆施塔特大学的团队通过计算由于某些物理因素(例如来自湿表面的光反射)而需要进行的校正,从而能够使用相机。 “现在,我们将绕线机连接到以非常标准化的方式运行的测量设备,”他补充道。
该团队开发了一个校正表和决策算法的数据库,使纤维缠绕机能够了解正在缠绕的特定管的每个阶段的目标。 “如果测量设备的输入显示树脂拾取不在应有的位置,”Koppenberg 解释说,“长丝缠绕机会通过调整刮刀将其恢复到规格来做出响应,而无需停止缠绕进行测量。”
现在每台绕线机都有数字测量系统,和 以太网卡。 “最昂贵的部分是安装和连接到服务器的电缆,” Koppenberg 打趣道,“但现在我们可以与每台机器交谈并收集所有数据。”还有另一个好处。 “以前,操作员在机器上编程,但是一旦我们将它们连接到服务器,我们就可以在任何台式机或笔记本电脑上进行编程。这进一步减少了停机时间并消除了另一个生产瓶颈。”
这第一个数字化步骤使 Dynexa 能够改进其过程控制、质量和效率,使其更具成本效益。这也推动了进一步的转型。
改变复合材料的范式
Dynexa 的销售和营销主管马蒂亚斯·布鲁克霍夫 (Matthias Bruckhoff) 表示:“我们正处于为客户提供新生态系统的分步过程中。”他举了一个例子:“在亚马逊,你可以看到你买了什么,什么时候买的,以及推荐的新产品。我们过去常常接受客户的要求,然后使用我们的计算和工程工具在几天内做出回应。现在,这将是在线的。我们的客户将在几分钟内查看产品并计算他们的需求、成本和交付。这不是新的,但它是 对于我们的行业。正如我们将机器操作员解放出来专注于更多机器和更高级别的任务一样,我们现在也将解放我们的工程团队,专注于更专业和更复杂的产品。”
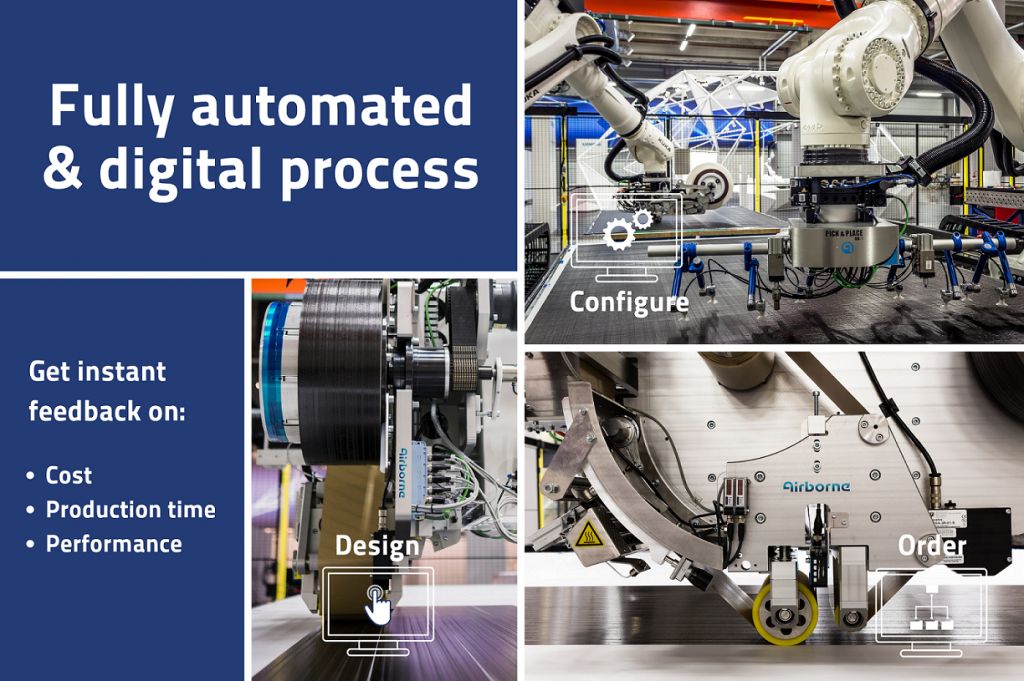
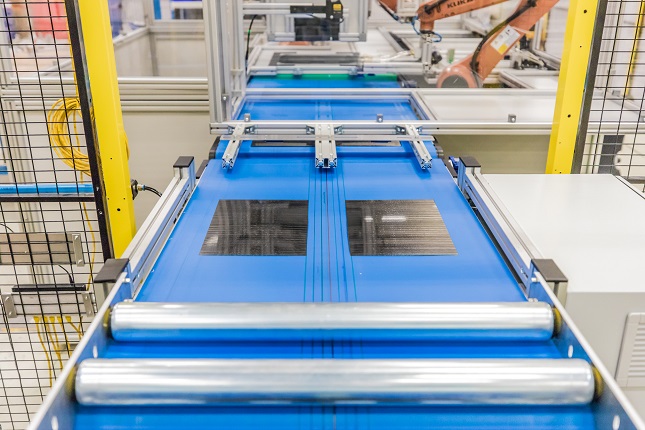
Airborne(荷兰海牙)于 2019 年 9 月推出了用于复合材料自动化制造的按需制造门户(参见“Airborne 推出复合材料打印门户”)。使用此工具,客户将设计输入到基于 Web 的平台中。然后,系统即时创建机器代码并确定生产持续时间和成本。然后可以定制产品,并在订购后在自动化制造单元中生产。该门户网站是使用 Airborne 的自动层压单元 (ALC) 启动的,用于处理热固性预浸料。它将扩展到其他工艺,例如,为 SABIC(沙特阿拉伯利雅得)特种业务部门开发的大容量热塑性复合材料 (TPC) 生产线。
“这个门户是我们如何看待复合材料制造的数字化未来的关键组成部分,”Airborne 首席技术官 Marcus Kremers 说。 “五年前,我们从零部件制造业务模式转变为帮助客户实现自动化和数字化。我们正在开发一系列解决方案,让客户可以轻松地使用复合材料进行构建。”该产品组合包括 ALC、自动蜂窝封装、自动层板套件和使用 TPC 胶带的大批量生产线,被 SABIC 称为数字复合材料制造线 (DCML),被 Airborne 称为 Falcon。后者是 Airborne 定制解决方案的一个例子。 “我们将我们的复合材料和零件制造知识嵌入到这些自动化系统中,这样客户就不必是专家了,”克雷默斯说。
Airborne 具有三种商业模式:购买自动化、租用自动化或将其留给 Airborne 以通过制造即服务 (MaaS) 进行运营。机载自动化单元具有传感器和在线检测系统,可根据客户定义的缺陷和容差数据库生成警报。 “Falcon 系列对视觉质量缺陷的容忍度非常低,”克雷默斯指出,“但我们的航空航天自动化更多地受到结构公差的驱动。我们也在不断推进我们的技术以实现自学和自适应。例如,我们用于 ALC 胶带铺设的下一个软件版本将能够识别缺陷并即时修改生产程序。”
从长远来看,我们的愿景是扩大按需门户网站,以收集分布在多个公司和地区的复合材料零件的生产能力。 Kremers 引用了 Protolabs(美国明尼苏达州 Maple Plains),该公司可在短短一天内按需提供注塑成型、钣金、CNC 加工或 3D 打印原型。同样,Plyable 的(英国牛津)在线应用程序提供制造复合材料的模具,提供从聚氨酯板到钢的各种材料,包括复合材料和 3D 打印工具。 “这是组织价值链的一种不同方式,”克雷默斯说。 “我们正在制造机器和软件,使复合材料零件成为可能。”
AZL Aachen 也在通过其超快速固结机来实现这一目标,该机器旨在在不到五秒的时间内生产多层 TPC 层压板。它于 2019 年商业化,使用 Conbility(德国亚琛)机器人、激光辅助 AFP 涂布机和 25 毫米宽的 UD 胶带以及片流原理——高速印刷行业的最先进技术——生产各种厚度的 TPC 层压板,只需固定或完全加固,局部增强。 “我们的愿景是提供支持在线平台的可扩展机器,”Emonts 说。 “生产线可以有多个工位,每个工位都有多个 AFP 涂抹器。客户将输入要求并获得胶合板、成本和交付选项。完成后,施胶者相互沟通以组织生产,而不是操作者。这是定制复合材料的完全智能生产。”
自动化自动化
ZLP 的主要重点是 CFRP 结构的自动化生产。 “仅对一个零件或程序进行自动化是很难证明的,”ZLP 灵活自动化团队负责人 Florian Krebs 指出。 “但是,如果您从特定任务的机器转移到几乎无需额外设置即可重新配置的自动化平台,现在您就有了业务解决方案。平台越灵活,投资回报越快。”
开场图片中显示的工作单元是作为 ZLP 项目 PROTEC NSR 的一部分设计的,以构建一系列遵循相同工艺路线的部件:干式非卷曲织物的取放叠层和树脂灌注(参见在线侧边栏“否教学机器人的商业案例”)。 “这个过程是为空客 A350 后压舱壁设计的,但你也可以在这条线上制作机身面板或机翼盖,因为步骤相似,”克雷布斯说。
“要实现灵活的自动化平台,需要某些技术砖,包括机器人算法、传感器以及如何理解它们产生的数据,”库普克说。 “例如,PROTEC NSR 生产线的设计旨在实现最大程度的模块化——所有模块相互互连,以展示一个自我配置、校正和优化的系统,在规模和复杂性上可扩展。”
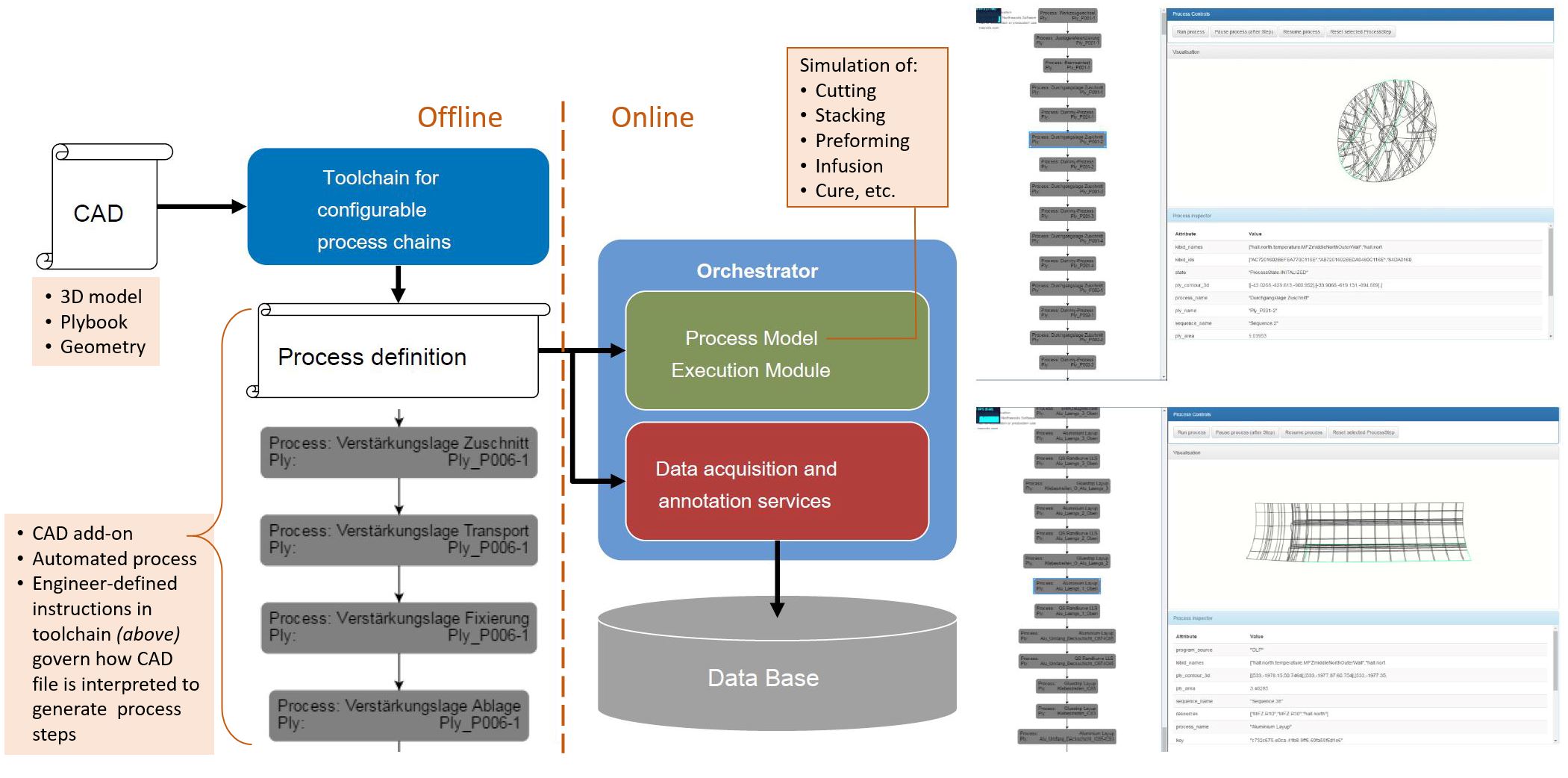
他解释了如图 5 所示的模块,其中包括 CAD 模型、流程定义、允许模拟和执行流程的流程模型、制造执行模块、获取数据的传感器、注释数据的软件和用于存储的数据库。
“在这张图的左侧,你制定了一个计划。然后执行模块实施该计划,”Kupke 说。 “在流程步骤中,我们从所有相关机器和流程中获取数据,例如切割机、机器人、建筑物(温度、压力、湿度)、取放过程中的摄像头等。我们分析数据在过程中实时进行,并使用元数据自动注释收集到的数据,将其输入到数据库中,从而构成了过程数字孪生的基础。数字孪生最重要的一点是拥有一个中央存储库,一个事实来源。每个部件的 CAD 模型和流程定义都是其单一事实来源的一部分。”
安装这些模块后,生产线只需按一下按钮即可自主运行。根据 CAD 模型、生产计划和相机,机器人推断下一个裁片并在桌子上寻找它(例如,从 100 个其他裁片中)。 “他们决定如何配置夹具以将其捡起并将其放置在工具中,并知道将其放置在哪里。”根据生产计划,机器人确定所有流程步骤的每个开始/结束路径,并知道每个步骤何时完成。 “通常,这些路径是由人类教授的,”库普克指出。 “但在我们的系统中,每条路径都是自动、无碰撞和实时定义的。如果您更改 CAD 模型或流程定义,则机器人将适应,无需任何额外的教学工作。但是如果你完全改变这个部分呢?使用这种类型的自动化,您可以非常快速地进行更改。这是实现柔性生产的途径。我们在 ZLP 的角色是通过开发技术砖并将它们连接在一起来铺平这条道路。”
机会与本体
COVID-19 大流行凸显了灵活生产的价值。它还创造了一个越来越不可预测的商业环境。 “在过去的两三年里,一切都变得更加不稳定,”Dynexa 的 Bruckhoff 指出。 “我们的客户希望得到非常快的答复,以便对他们的客户做出回应。通过提供我们新的在线生态系统,我们使整个供应链更具竞争力。”
这是航空业公认的。 “我们需要生产线和整个站点的数字化基础,以实现横向和纵向集成,”德国工程师协会航空航天技术部主席 Marc Fette 说,他是复合材料技术中心 (CTC, Stade,德国),空中客车公司的 R&T 子公司。 Composites 4.0 中的 CTC 项目包括材料和资产跟踪、协作机器人、高级流程链等。但 Fette 强调需要本体——一种用于数字通信和数据交换的术语和通用协议。 (请参阅在线侧边栏“复合 4.0 架构和本体”。)
“您需要为给定工厂中的所有机器和生产系统建立整体网络,”他解释说,“但这还必须扩展到整个价值创造链,包括工程、采购、物流以及材料和工艺认证等学科, 一方面。另一方面,所有利益相关者,例如供应商,都必须被考虑并参与到这个变更过程中。我们看到了很多试点项目,但当你仔细观察时,仍然缺乏针对每个公司或生产链的整体方法的战略。”
他继续说道:“我们拥有庞大的全球供应商网络,他们有相同的要求,以便作为数字连接的供应链运作。我们的大多数供应商都是为飞机制造商、空中客车公司和波音公司工作的中小企业。如果没有关于共同标准的讨论,那么您将这些挑战转嫁给供应商。他们很可能无法负担所有机器都遵守两套不同的标准,包括文档、评估数据、网络安全等。”
Fette 承认这些都是伟大的想法,并表示飞机原始设备制造商正在制定计划来应对这些挑战。 “但是像这样的障碍很多,而且真的很复杂,不仅涉及技术,还涉及社会、经济、人体工程学和法律问题——这是一个心理上的变化过程。我们才刚刚开始。但要取得成功,我们必须明白,这些新系统依赖于人,而这些人必须参与其中,不仅在 OEM 中,而且在整个全球网络中。”
“所有行业的市场都变得越来越分散,每个人都面临着范式转变,”ZLP 的 Krebs 指出。 “Many people don’t see that as an opportunity,” adds Kupke, also of ZLP. But those who do see that opportunity envision democratized access to composites enabled by Composites 4.0, and with that, a much broader market, including applications that we are only beginning to conceive.
树脂