HP-RTM 用于批量生产经济高效的 CFRP 航空结构
大约十年前,当树脂传递模塑 (RTM) 开始过渡到高压 RTM (HP-RTM) 时,它在汽车应用中广受赞誉,将复合材料零件的循环时间从几小时缩短到不到 2 分钟。关于将该技术应用于航空航天部件的说法较少。航空工业在传统 RTM 方面有着悠久的历史,包括用于生产数以千计的碳纤维增强塑料 (CFRP) 风扇叶片和商用飞机发动机的安全壳。空中客车公司甚至使用 RTM 为空中客车 A320 设计了一个 7 米长的一体式复合材料多翼梁襟翼。但是,是否有可能在几分钟内将这种耗时数小时的过程转变为复合材料飞机零件的全自动成型?几位主要参与者表示这是可能的。
为清楚起见,传统 RTM 在此称为 LP-RTM,通常使用 10-20 巴的注射压力。另一方面,HP-RTM 使用 30-120 巴的注射压力。
“我们在 10 年前通过欧盟资助的机身框架制造项目开始使用航空航天 RTM 加工,”Alpex Technologies(奥地利米尔斯)研发主管 Bernhard Rittenschober 说,Alpex Technologies 是串行复合材料创新工具系统的供应商。零件生产。 “当时,预测 [Airbus] A350 的许多部件将使用 RTM 制造,但这并没有实现。”然而,Alpex 继续致力于这项技术,并且作为汽车和航空航天行业的供应商,开始研究如何合并这两个行业中使用的流程。 “我们的想法是使用符合航空航天要求的 [Hexcel] RTM6 环氧树脂,但采用汽车模具最佳实践和自动化注射系统以缩短循环时间,”Rittenschober 解释说。
结果是 2013 年至 2015 年的一项名为 TAKE OFF 的研究计划,由奥地利政府资助,Alpex 与合作伙伴空中客车直升机(德国多瑙沃斯工厂)、设备供应商克劳斯玛菲(德国慕尼黑)、测试专家航空航天和先进复合材料共同参与了该计划(AAC,Wiener Neustadt,奥地利)和树脂供应商 Hexcel(美国康涅狄格州斯坦福德)。该计划表明,HP-RTM 使 A350 门框的成本降低了 30%,并进行了重大技术开发,包括使用双组分 (2K) 树脂系统、通过模内传感器进行智能注射和固化监控以及能够进一步缩短零件周期时间。 Alpex 不断发展,并看到了这种 HP-RTM 技术的潜力,以帮助克服当前的 CFRP 生产问题。
支持这一观点的空中客车运营有限公司的子公司复合材料技术中心 (CTC) 也在十年前一直在开发自动化 RTM,首先使用 LP-RTM,然后在大约五年前过渡到 HP-RTM。 (复合材料世界 在 2016 年参观其设施期间注意到 CTC 的克劳斯玛菲 HP-RTM 机器和开发工作。)“HP-RTM 解决了注射和固化的瓶颈,因为它的高速混合允许使用高反应性树脂,”Jan Schiller 解释说,生产系统的 CTC 项目负责人和 RTM 技术的主要联系人。 “我们开发了一种工艺,可以在 20 分钟的循环时间内生产尺寸为 1-2 米的复杂几何零件,满足航空航天要求(例如,60% 的纤维体积和小于 2% 的空隙)。”他补充说,去年与空中客车供应商进行了访问和讨论后,确定了许多零件可以过渡到 HP-RTM,从而提高 A320 飞机的生产速度。 “我们现在正在为这些开发特定的加工工艺,并在今年努力使它们投入批量生产。”
HP-RTM A350 门框
Alpex 的开发是通过奥地利的 TAKE OFF 计划通过一个名为 SPARTA 的项目完成的。 “空中客车直升机公司选择了这个部分,”Rittenschober 回忆道。 “这个门框就是你在打开门的情况下走进 A350 时所看到的。它高约2米,宽200-250毫米,厚8-10毫米,具有复杂的形状和设计特征,可以满足组装门的各种要求,属于主体结构。” A350 的机门由位于德国多瑙沃斯的空中客车直升机公司使用 LP-RTM 制造的 14 个部件组成。为 SPARTA 选择的框架是门中最具挑战性的部分之一。 “这是一个很好的演示部分,因为我们可以直接将 HP-RTM 与标准航空航天 LP-RTM 进行比较,”Rittenschober 补充道。
Alpex 设计并制造了目前用于空中客车直升机 A350 门框生产的 LP-RTM 工具。对于 HP-RTM 工具的设计和构建, 它将应用更多的汽车思维。 “我们的目标是在航空航天复合材料零件生产中实现汽车类型的自动化,”Rittenschober 说。 “如果空中客车公司未来要制造具有更多复合材料部件的 A320,并且以每月 60 到 100 架飞机的速度生产,这是必要的。”
他继续说道:“我们为宝马生产模具,宝马积极尝试简化其零件和流程以缩短周期时间,而空客则来自以前的航空航天复杂性。例如,当我们开始时,空中客车直升机公司问这个模具有多少个零件。”请注意,当前的 LP-RTM 门生产包括复杂的多件式工具。 “我们解释说 HP-RTM 工具只有一个上模和一个下模,”Rittenschober 说。
因此,Alpex 从简单的模具设计开始,然后添加了一些功能,使加工更加稳健和灵活——例如,用于大批量汽车生产的密封系统。 “此外,我们将所有传感器都集成到模具中,”他指出。
瓶坯和工艺
目前用于 A350 门框的预制件使用编织材料,需要多个减积步骤,因此生产周期为三天。 “我们决定改用非卷曲织物 (NCF),”Rittenschober 说。 “这显着降低了价格和周期时间。我们最终还使用 Hexcel 合格的机织预制件展示了一些部件,但我们看到航空航天以外的复合材料行业发生了转变,SGL 和其他公司的开发从机织织物转向胶带和 NCF 等低成本形式。”
当被问及注射点和纤维清洗的任何问题时,Rittenschober 解释说 HP-RTM 工具只有一个注射点,但没有纤维清洗,因为预制件被夹紧,因此它固定在模具中并且非常稳定。>
另一个关键点是 Alpex 选择使用双组分 (2K) 树脂系统,而不是空客直升机目前使用的单组分 RTM6。 Rittenschober 断言 2K 系统可以更具反应性,更适合 HP-RTM,并且可以节省成本,因为它没有预先混合并且不需要危险材料运输。但是,它确实需要 180°C 的更高温度。 “这对我们来说是最具挑战性的部分,”Rittenschober 说,“因为我们更习惯于在 120°C 下进行加工。”
克劳斯玛菲在其位于德国慕尼黑的轻量级技术中心,在其 RimStar Compact HP-RTM 系统中安装了成品模具,该系统具有自动化的高压(高达 80 bar/1,100 psi)混合、计量和注射。然后它制造了 20 个演示部件。 Rittenschober 描述了基线过程:在 80°C 下注射,升温至 120°C,保持一小时,升温至 180° 并保持 90 分钟固化,降温(2°C/分钟)并脱模。 “注射仅需 20 秒,”他说,“但整个成型周期约为 4 小时。”
周期时间和成本
SPARTA 门框仍然很长的固化周期是由获得空客认证的 Hexcel RTM6 树脂配方和加工驱动的。 “我们能够在 180°C 下实现 30 分钟的固化循环,然后在真空下进行额外的后固化,以消除热应力并确保机械性能,”Rittenschober 指出,并补充说这些性能非常好,可与 LP 相媲美-RTM部分。
“我们展示了您可以使用该流程并自动化生产更大的零件数量,”Rittenschober 说。 “您可以在模具中注射和固化,然后从印刷机中进行后固化。”他承认这需要额外的工具集,但只需要一个压力机和注塑单元。 “有了这个系统,您可以将零件成本降低 700 欧元,这使您能够以每年 500 到 1,000 个零件的生产率轻松支付设备费用,这甚至不是很高的产量。”
CTC 工艺开发和演示器
撇开工具和工艺不谈,HP-RTM 门项目还包括对纤维格式的创新使用。 “我们从已经通过空中客车公司认证的机织纺织品开始,并且非常成功,”席勒回忆道。 “然后我们继续使用 NCF 和更具创新性的纺织品。”后者包括干纤维铺放和与散开的丝束层交织以增加韧性,但后者存在纤维和层紧密堆积的问题,导致渗透性差并阻碍树脂渗透。 “还有一些发展可以解决这个问题,例如使用特殊纤维的 NCF 来提高渗透性,”他补充道。
关于 HP-RTM 的压力,Schiller 强调,使用该工艺的决定更多是由聚氨酯行业的混合技术而非高工艺压力驱动的。 “我们使用 HP-RTM 只是为了获得高反应性树脂的良好混合,”他解释说。 “模具中可能有一些更高的压力,但这是快速注射的次要影响。对于循环时间为 2 分钟的汽车零件,它们必须比我们更快地将树脂浸入干燥的预成型件中。我们 15 分钟的固化时间为树脂渗透留出了更多时间,这也降低了模具中的压力。”
同时,压机吨位取决于零件尺寸。 “制造尺寸达 2 米的零件效果很好(约 1,500 吨),但尺寸为 4-6 米的零件需要计算业务案例,因为压机投资变得非常高,”席勒说。 CTC 于 2018 年在 JEC World 上展示了代表任何可能的航空航天主要结构的 1.5 米 x 0.5 米 CFRP 加强筋。它还将在 2019 年底收到更高吨位的压力机。
2K 树脂和基于传感器的 QA
Schiller 观察到,所有以前的 RTM 飞机结构仅使用由供应商混合的 1K 系统,然后供应商对混合物进行认证并承担确保树脂符合资格要求的责任。 “现在我们正在考虑 2K 系统,但挑战在于确保混合质量,”他解释说。预混 1K 系统需要冷藏运输和储存,以防止在零件加工之前发生反应。因此,2K 系统的优势包括消除这种费用以及更高的反应性以加快处理速度。然而,一个问题是质量保证 (QA) 将从树脂供应商转移到零件制造商。 “这个 QA 需要检测混合比例和 混合树脂质量。新材料的空中客车认证需要两者。因此,这意味着在混合之前测量两种组分和混合后树脂的测量值。今天,我们只有在混合头前有传感器,显示有多少树脂和多少固化剂被计量加入混合物中。这还不够资格。”
与此同时,Alpex 正在努力开发一个在线质量系统,以验证空客要求的 100% 正确混合的树脂。 “从开发之初,我们就与 Netzsch 模内传感器合作,”Rittenschober 指出。 “现在 Netzsch 与奇石乐(瑞士温特图尔)合作,新技术可用。我们可以通过模具中包含的单个传感器监控温度、压力和树脂的固化情况。”
“Alpex 说要使用模内传感器,而混合/注射设备供应商说传感器应该在他们中 系统,”席勒说。 “两个都对。”但他指出,后者也需要改进。 “在汽车 HP-RTM 中,树脂混合比是在整个过程中测量的,所以它是一个平均值,”席勒解释说。 “但是,我需要在过程中的每个离散点进行这种测量,以便我知道混合比始终是正确的,即使在注射过程中的最后半秒也是如此。我们需要在测量系统中获得更好的时间分辨率。” Schiller 建议在混合头之前可能需要传感器,在混合头内部和 在模具中。 “在评估航空航天应用中的 2K 树脂的同时,我们正在开发 QA,并且与机器供应商一起,我们已经确定了具有足够分辨率的传感器系统。它们将在今年内得到验证。”
Alpex 还在试用由 Aerospace &Advanced Composites(AAC,Wiener Neustadt,奥地利)开发的新型混合多功能压电传感器。放在上 在 RTM 模具中,它充当压力传感器来监控模具中的树脂流动前沿。一旦树脂浸渍预制件并开始固化,传感器就会使用阻抗谱的变化来确定固化程度。固化完成后,压电传感器在部件表面共固化,用于结构健康监测,无论是在被动模式下作为声发射传感器,还是在主动模式下使用引导超声波。它们已被证明可用于监测成品零件的冲击和损坏。
请注意,工业 4.0 智能生产系统可以分析此过程数据,以确定进一步提高质量和效率的途径。还可以为每个零件的数字孪生记录此过程数据。
未来潜力
Rittenschober 表示,HP-RTM 技术的唯一真正障碍是认证:“我们正在与空中客车直升机公司一起证明该过程可行,但必须有人对其进行认证。”席勒同意,找出谁将成为第一人始终是一个障碍,但他去年也计算了很多部分的商业案例。 “对于每年 200 个零件来说,这是没有意义的。但是,例如,对于 A320 上的零件,它变得很有吸引力。每个月,我们都会看到 A320 计划的目标率更高。这些零件中有很多是在 1980 年代设计的,并且是手动生产的,因此使用 HP-RTM 可以轻松提高它们的效率。”
由于 CTC 证明的零件循环时间为 20 分钟,HP-RTM 对电动垂直起降 (eVTOL) 飞机市场也很有吸引力,空中出租车制造商建议将每年 5,000 架飞机的产量作为上限优步。
Rittenschober 表示,Alpex 将继续开发一系列 RTM 改进。 “我们相信 HP-RTM 具有真正的潜力,可以通过更具成本效益的 CFRP 飞机结构工业化生产来帮助解决一些问题。” Schiller 表示同意,并指出对于许多目标 A320 应用而言,每个船组都有许多 CFRP 部件。 “因此,更高效流程的好处开始累积。如果我们能在生产中获得第一个应用程序,那么还会有其他应用程序。”
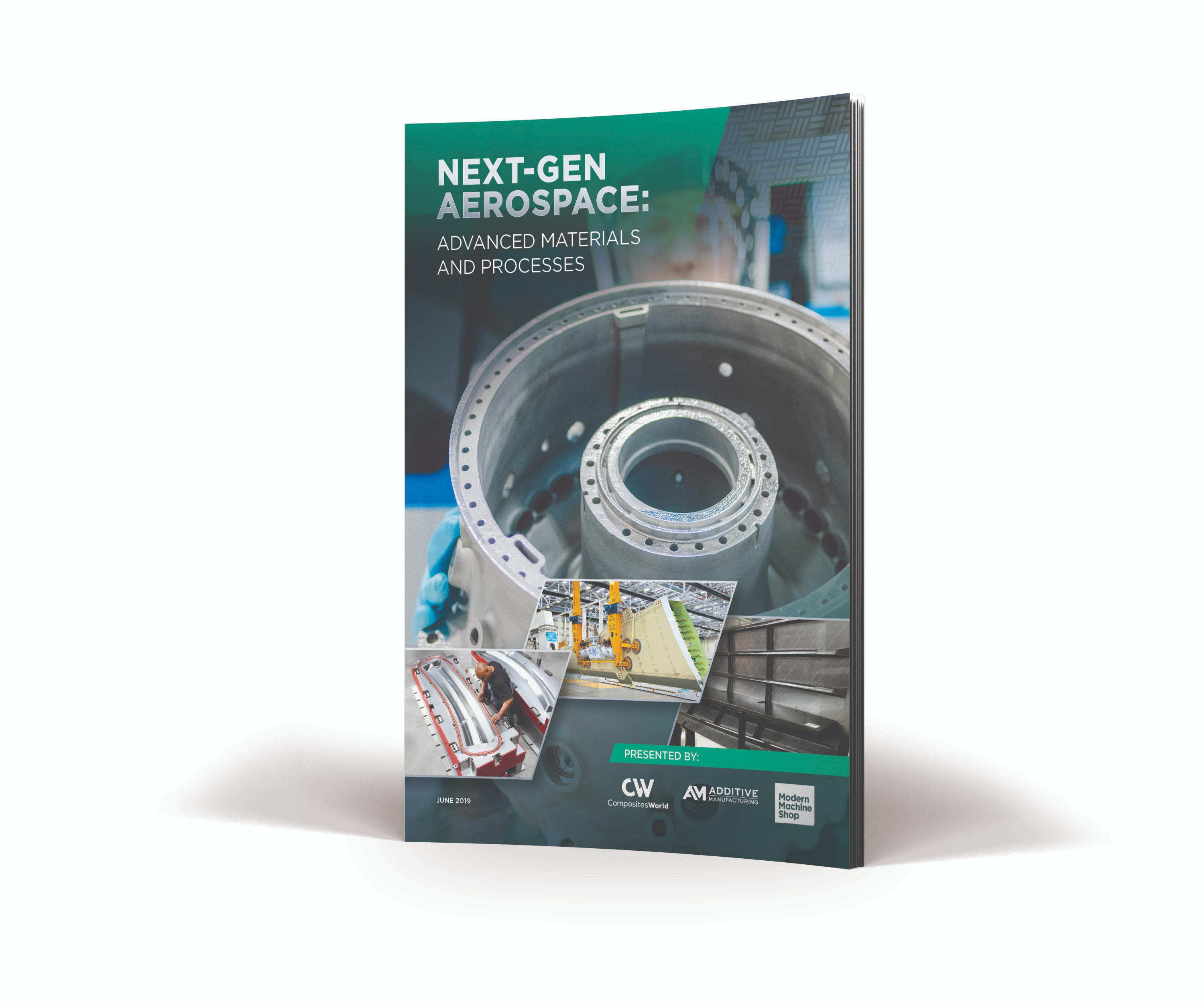
下一代
航空航天制造
预计未来 20 年商用航空业将翻一番,满足对客机和货机的需求将需要新技术和前所未有的制造速度。
从 CompositesWorld, Modern Machine Shop 的一系列故事中了解有关塑造下一代飞机的材料和工艺的更多信息 和增材制造 ,可供免费阅读或下载 .从这里获取。<图片> 图片>
树脂
- 添加剂:用于电线和电缆应用的经济高效的着色剂
- 用于薄壁聚烯烃包装生产的清洗化合物
- Fraunhofer 委托自动化 Engel 生产单元进行热塑性复合材料研发
- 设计用于小批量航空结构的自动化复合材料制造
- 热塑性胶带继续显示出复合航空结构的潜力
- 将 AFP 与 3D 打印结合用于柔性零件生产
- 用于 RTM 襟副翼、外骨骼等的 3D 打印 CFRP 模具
- 卡尔迈耶推出热塑性 UD 胶带生产线
- 融合水刀、激光,提高 CFRP/CMC 加工效率
- Broetje-Automation 扩大 AFP 产品组合,用于连续复合材料生产
- INEOS Styrolution 为 StyLight 热塑性复合材料建立生产基地
- 铸件生产的可追溯性实践