关于冲压工艺的16个要点【实践经验】
冲压工艺是一种金属成型工艺,其中金属板被赋予所需的形状。冲压过程可能包括不同的其他钣金操作,如冲压、弯曲、落料、剪切、穿孔等。
在本文中,我们将从Shane的实践经验中了解钣金冲压工艺的各个方面。
1。来自废物的信息
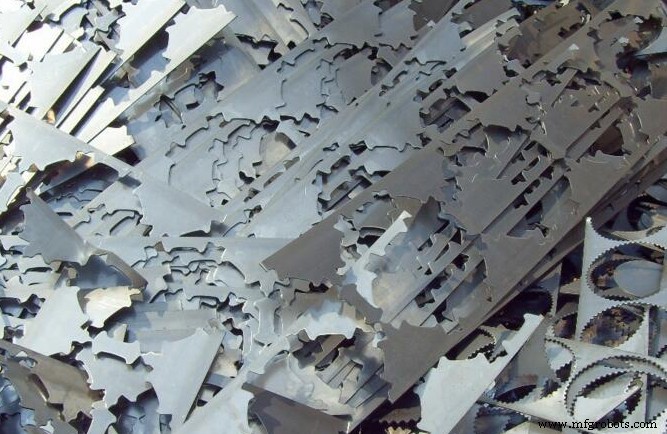
废料本质上是形成的孔的反射。那是相反位置的相同部分。通过检查废品,可以判断上下模的间隙是否正确。
如果间隙过大,废料的断面会粗糙起伏,光亮区狭窄。间隙越大,断口与亮区的夹角越大。
如果间隙太小,废料会呈现出小角度的断面和宽大的亮带区。过大的间隙会形成带有大卷曲和边缘撕裂的孔,导致从截面中突出的轻微薄边缘。
太小的间隙形成带轻微卷曲和大角度撕裂的带,导致截面或多或少垂直于材料表面。
理想的废料应该具有合理的塌陷角和均匀的亮带。这样可以将冲压压力保持在最低限度,并形成一个干净的圆孔,毛刺少。
从这个角度来看,增加间隙以延长模具的使用寿命是换来牺牲成品孔的质量。
2。模具间隙的选择
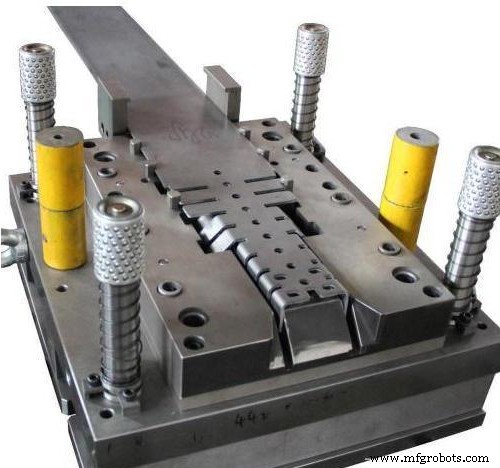
模具的间隙与被冲压材料的类型和厚度有关。不合理的清关会导致以下问题:
(1)间隙过大,冲压工件毛刺比较大,冲压质量差。
间隙过小,虽然冲裁质量好,但模具磨损严重,大大降低模具使用寿命,容易造成冲头折断。
(2)间隙过大或过小都容易在冲头材料上产生粘连,造成冲压时材料弯曲。
间隙过小容易在凸模底面与钣金之间形成真空,造成废料反弹。
(3)合理的间隙可以延长模具的使用寿命,有良好的卸料效果,减少毛刺和翻边,保持板材清洁,孔径一致,不会划伤板材,减少磨削次数,保持板直,冲压定位准确。
请参考下表选择模具间隙(表中数据为百分比)
间隙选择(总间隙) | |||
材料科学 | 最低 | 最佳 | 最大值 |
红铜 | 8% | 12% | 16% |
黄铜 | 6% | 11% | 16% |
低碳钢 | 10% | 15% | 20% |
铝(软) | 5% | 10% | 15% |
不锈钢 | 15% | 20% | 25% |
% × 材料厚度 =模具间隙 |
3。如何提高模具的使用寿命
对于用户来说,提高模具的使用寿命可以大大降低冲压成本。
影响模具使用寿命的因素如下:
- 材料的种类和厚度;
- 是否选择合理的下模间隙
- 模具的结构形式
- 材料冲压时是否润滑良好
- 模具是否经过特殊表面处理
- 如镀钛、碳钛氮化
- 上下炮塔对齐
- 合理使用调整垫片
- 斜边模具是否使用得当
- 机床模座是否磨损
4.冲压特殊尺寸孔需要注意的问题
- 如果最小孔径在φ0.8—φ1.6范围内,请使用专用冲头。
- 冲厚板时,请使用相对于加工孔直径较大的模具。
例1.根据下表的加工条件,虽然加工孔径对应A站的模具,但请使用B站的模具。
材质纹理 | 板厚(mm) | 孔径(毫米) |
低碳钢(40kg / mm 2 ) | 6.0 | 8.2-12.7 |
不锈钢(60kg/mm 2 ) | 4.0 | 8.2-12.7 |
例2.根据下表的加工条件,虽然加工孔径对应B工位模具,但请使用C工位模具。
材质纹理 | 板厚(mm) | 孔径(毫米) |
低碳钢(40kg / mm 2 ) | 6.0 | 22.9-31.7 |
不锈钢(60kg/mm 2 ) | 4.0 | 22.9-31.7 |
(3)一般冲头边的最小宽度与长度之比不小于1:10。
例3.对于矩形冲床,当刃长为80mm时,刃宽≥8mm是最合适的。
(4) 凸边最小尺寸与板厚的关系。
建议冲头边缘的最小尺寸为板厚的2倍。
5。模具研磨
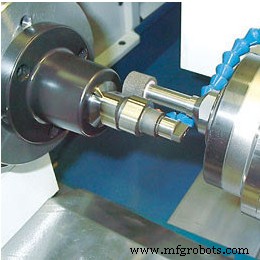
1.模具研磨的重要性
模具的定期磨削是冲裁质量一致性的保证。
定期修磨模具,不仅可以提高模具的使用寿命,还可以提高机器的使用寿命。掌握正确的研磨时间是很有必要的。
2。模具的具体特性需要磨刀
对于模具研磨,没有严格的打击次数来确定是否需要研磨。
主要取决于边缘的锐度。
主要由以下三个因素决定:
(1)检查切削刃的圆角。如果圆角半径达到R0.1mm(最大R值不超过0.25mm),需要磨削。
(2)检查冲孔质量,是否有大毛刺?
(3)根据机器冲压的噪音判断是否需要打磨。
如果冲压时同一个模具有异响,说明冲头已经变钝,需要打磨。
注意:如果刃口变圆或刃口后部粗糙,也要考虑磨削。
3.研磨方式
模具的磨削方法有很多种,可以通过专用磨床或平面磨床来实现。
凸模和下模的磨削频率一般为4:1;研磨后请调整模具高度。
(1) 磨削方法不正确的危害:
不正确的磨削会加剧模具边缘的快速损伤,导致每次磨削的打击次数显着减少。
(2)正确磨削方法的好处:
通过定期磨削模具,可以保持冲压的质量和精度稳定。
模具刃口损伤较慢,使用寿命较长。
4.磨削规则
模具磨削应考虑以下因素:
(1)边角为R0.1-0.25mm时,取决于边角的锋利度。
(2)砂轮表面应清洁。
(3) 建议使用松、粗、软的砂轮。如WA46KV。
(4)每次磨削量(切削量)不得超过0.013mm。
磨削量过大会导致模具表面过热,相当于进行了退火处理,使模具软化,大大降低模具的使用寿命。
(5) 磨削时必须加入足够的冷却液。
(6)磨削时,凸模和下模要固定好,使用专用工装夹具。
(7)模具的磨削量一定。如果达到这个值,冲头就报废了。
如果继续使用,很容易对模具和机器造成损坏,得不偿失。
(8)打磨后边缘用油石处理,去除过分锋利的边缘和线条。
(9) 打磨后的刀片应清洗干净,去磁,上油。
注:模具的磨削量主要取决于冲压板的厚度。
6.使用前注意打孔
1.商店
(1)用干净的布擦拭上模套内外。
(2) 存放时,注意不要划伤或凹痕表面。
(3) 防锈油。
2。使用前的准备
(1)使用前彻底清洗上模套。
(2) 检查表面是否有划痕和凹痕。如果有的话,用油石把它去掉。
(3)内外油。
3.上模套安装冲头时的注意事项
(1) 清洁冲头,给长柄上油。
(2)将冲头插入大工位模上模套底部,不用用力。
不能使用尼龙锤。
安装时,不能通过拧紧上模套上的螺栓来固定冲头。只有在正确定位冲头后才能拧紧螺栓。
4.将上模组件安装到转塔中
要想延长模具的使用寿命,上模套外径与转塔孔的间隙应尽量小。
因此,请谨慎执行以下程序。
(1) 对键槽和转塔孔内径进行清洗和上油。
(2)调整上模导套键槽与转塔孔键相匹配。
(3)将上模套笔直插入塔孔中,注意不要倾斜。
上模导套应靠自重滑入转塔孔内。
(4)如果上模套向一侧倾斜,可用尼龙锤等软质材料工具轻轻敲右。
反复敲打直至上模导套因自重滑入正确位置。
注意:不要对上模导套外径施力,只对凸模顶部施力。
请勿敲击上模套顶部,以免损坏转塔孔,缩短个别工位的使用寿命。
6.模具保养
如果冲头被材料咬伤无法取出,请按以下几项检查。
1.冲头和下模的修磨。
具有锋利边缘的模具可以加工出漂亮的切割断面。如果边缘变钝,则需要额外的冲压压力。而且工件断面粗糙,阻力大,会导致冲头被材料咬伤。
2。模具间隙。
如果模具的间隙相对于板厚选择不当,则冲头在与材料分离时需要很大的脱模力。
如因此原因冲头被材料卡住,请更换间隙合理的下模。
3.加工材料的状态。
当材料脏了或有脏物时,脏物附着在模具上,使凸模被材料咬住而无法加工。
4.变形材料。
打完孔后,翘曲的材料会夹住凸模,使凸模咬合。
有翘曲的材料在加工前应平整。
5.过度使用弹簧。
会造成弹簧疲劳。请经常检查弹簧的性能。
7.上油
油量和注油次数取决于加工材料的条件。
冷轧钢板、耐腐蚀钢板等不生锈、无氧化皮的材料,应在模具内注油。
注油点为导套、注油口、刀体与导套接触面、下模等。注油使用轻机油。
对于有锈迹和氧化皮的材料,在加工过程中,锈粉会被吸入冲头和导套之间,产生污垢,使冲头不能在导套内自由滑动。
在这种情况下,如果你涂抹油,它会使锈垢更容易粘附。
因此,在冲洗这种材料时,相反,擦油,每月分解一次,用蒸汽(柴)油清除冲头和下模的污垢,重新组装前擦干净。
这样可以保证模具具有良好的润滑性能。
8.模具使用过程中的常见问题及解决方法
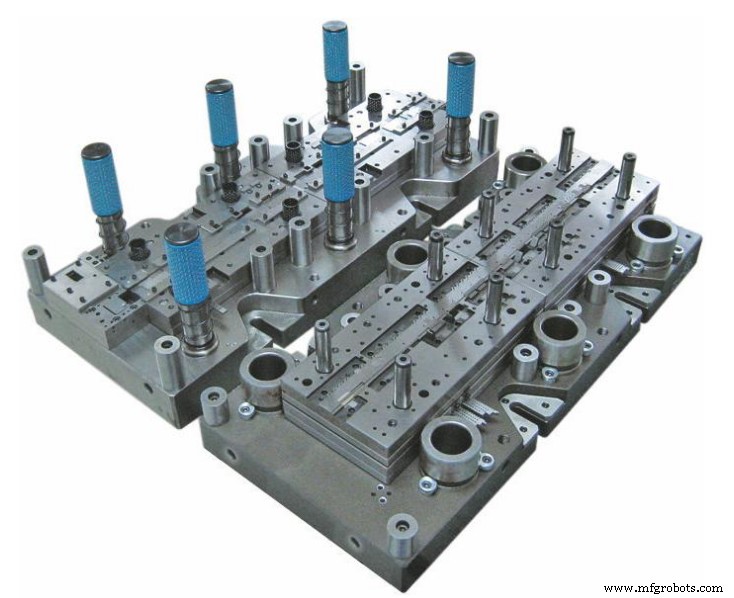
问题 1:板从钳口出来
原因 | 解决方案 |
卸模不完整 | 1。使用带坡度的冲头 |
2。在板上涂抹润滑剂 | |
3。采用重型模具 |
问题 2:严重的模具磨损
原因 | 解决方案 |
模具间隙不合理(太小) | 增加模具间隙 |
上下模座错位 | 1。 2.上下模具的工位调整和对中。炮塔水平调整 |
磨损的模具导向部件和刀塔刀片没有及时更换 | 替换 |
冲头过热 | 1。向 sheet2 添加润滑剂。 3、保证凸模与下模之间的润滑。同一程序中使用多套相同规格尺寸的模具 |
磨削方法不当会导致模具退火,加剧磨损 | 1。软砂轮2. 3、经常清洗砂轮。小咬4。冷却液充足 |
步冲 | 1。增加步距2。采用桥式步进 |
问题3:冲床带和冲床粘连
原因 | 解决方案 |
模具间隙不合理(太小) | 增加模具间隙 |
冲边钝化 | 及时打磨 |
润滑不良 | 改善润滑条件 |
问题4:垃圾反弹
原因 | 解决方案 |
下模块问题 | 使用防弹材料降低模具 |
对于小直径孔,游隙减少10% | |
直径大于50.00毫米,间隙加大 | |
模具边缘侧添加划痕 | |
打孔 | 增加模具深度 |
安装卸料聚氨酯顶杆 | |
采用斜切刃 |
问题5:卸载困难
原因 | 解决方案 |
模具间隙不合理(太小) | 增加模具间隙 |
打孔磨损 | 及时打磨 |
春季疲劳 | 更换弹簧 |
打孔附着力 | 去除粘连 |
问题 6:冲压噪音
原因 | 解决方案 |
卸载难度 | 增加下模间隙和良好的润滑 |
增加放电力 | |
表面柔软的放电板 | |
工作台和转塔中的板材支撑有问题 | 球形支撑模具 |
减小工作尺寸 | |
增加工作厚度 | |
片材厚度 | 使用斜边打孔 |
9.使用特殊成型工具的注意事项
1、不同型号机器的滑块行程不同,要注意成型模合模高度的调整。
2、必须保证成型足够,所以需要仔细调整。每次最好不要超过0.15mm。
如果调整过大,容易造成机器和模具的损坏。
3.拉伸成型时请选择轻质弹簧组件,以防止因变形不均匀导致钣金撕裂或难以卸料。
4.在成型模具周围安装滚珠支撑模具,防止板材倾斜。
5、成型位置尽量远离夹具。
6.成型最好在加工程序结束时实现。
7、一定要保证板子润滑良好。
8、订货时注意专用成型工具的良率。若两次成型距离较近,请务必与我司销售人员沟通。
9、由于成型工具卸料时间长,成型加工时必须采用低速,最好有延时。
10.使用矩形刀的注意事项
1、步距尽量大,大于刀具全长的80%。
2.最好通过编程实现跳步。
3. 建议使用斜边模具。
12、如何在不超过机器公称力的情况下进行冲压?
生产过程中需要冲出直径大于114.3mm的圆孔。
这么大的孔会超过机器公称力的上限,特别是对于高剪切强度的材料。
这个问题可以通过多种打孔方法打大孔来解决。
用小尺寸模具沿大圆圆周切削,可使冲裁力减少一半或更多。您已经拥有的大多数模具都可以这样做。
11.一种打大圆孔的简单方法
这个凸透镜的模具可以做成你需要的半径尺寸。
如果孔径超过冲头的公称力,我们推荐方案(A)。
用这个模具冲出圆的外围。
如果孔径能在冲头的公称力范围内冲出,径向冲模和凸透镜冲模可以在不转动冲模的情况下冲四次所需的孔(B)。
12.最后向下形成
在选择成型模具时,应避免向下成型操作,因为它会占用过多的垂直空间,并导致额外的板材矫平或弯曲工序。
向下成型也可能落入下模,然后被拉出转塔。
但是,如果向下成形是唯一的工艺选择,则应将其视为钣金处理的最后一步。
13.防止材料变形
如果需要在板材上冲大量孔而板材不能保持平整,原因可能是冲压应力的积累。
冲孔时,孔周围的材料被向下拉伸,增加了板材上表面的拉应力。
向下运动也导致板下表面的压应力增加。
对于冲孔数量较少,效果不明显,但随着冲孔数量的增加,拉应力和压应力也呈指数增长,直至板材变形。
消除这种变形的一种方法是:
每隔一个孔打孔,然后返回打剩余的孔。
虽然这会在板材上产生相同的应力,但它会瓦解因在同一方向上一个接一个冲孔而引起的拉/压应力的积累。
这样第一批孔就可以共享第二批孔的变形效果了。
14.如果你的不锈钢翻边变形了
翻边前在材料上涂抹优质的成型润滑剂,可以更好地使材料与模具分离,并在成型时在下模表面平滑移动。
这使材料有更好的机会分散弯曲和拉伸时产生的应力,从而防止成型翻边孔边缘变形和翻边孔底部磨损。
15.克服卸货困难的建议
1.使用带有细橡胶颗粒的冲头。
2.增加下模间隙。
3.检查弹簧的疲劳度。
4.使用重型模具。
5、适当使用斜边模具。
6.润滑板。
7、大工位模具需安装聚氨酯出料头。
16.垃圾反弹的主要原因
1、切削刃的锋利度。切削刃的圆角越大,越容易造成废料反弹。
2. 进模模数。在每个工位冲压模具时,对入口模数的要求是一定的。入口模量小,易造成废料反弹。
3、模具的间隙是否合理。模具间隙不合理容易造成废品反弹。
4、加工后的板材表面是否有油渍。
但是,您必须进行例行和定期维护,以确保冷却剂和输送系统达到预期效果。
这是 Shane 的客座帖子 来自 MachineMfg 团队
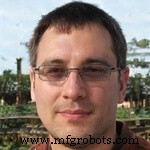
Shane 在机械工程行业工作了 5 年多。他热爱写作,专注于分享与金属和金属加工相关的技术信息、指导、详细解决方案和想法。通过他的文章,用户总能轻松解决相关问题,找到自己想要的。
工业技术