压铸缺陷:类型、原因以及如何预防
压铸过程涉及对熔融金属施加高压,该过程类似于塑料注射成型。然而,压铸是复杂的,许多因素可能会影响压铸产品的质量。由于原材料控制不严、工艺和生产计划不完善等原因,压铸缺陷现在已成为主要问题。
因此,无法妥善解决这些铸造缺陷将影响最终产品的质量。但是,需要注意的重要一点是,您可能无法避免 压铸过程中的所有缺陷 .在这种情况下,设计师可能不得不修改模具设计。
因此,我们将在本文中讨论各种类型的模具外壳缺陷,详细说明它们的原因、解决方案以及如何预防它们。让我们开始吧!
压铸缺陷 s :类型, 原因 , 和解决方案 s
在这里,我们将介绍各种压铸缺陷和补救措施。这些缺陷往往是由于填充不正确或凝固阶段不充分造成的,主要有两大类:
内部 压铸缺陷
这些类型的铸造缺陷很难发现,它们会削弱部件的结构阻力。两个主要的内部铸造缺陷是:
1. 气孔率
这涉及冷却后在铸件中形成气泡。您会在压铸件的主体上看到气孔呈圆形或椭圆形结构,它们还具有光滑、明亮的白色或黄色表面。
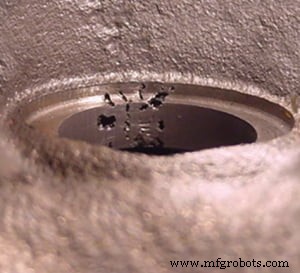
大多数固体金属不能容纳大量溶解气体,但液态金属可以。结果,固体金属中的气体在铸件冷却时会在铸件内形成空隙或气泡。这通常发生在凝固阶段,您可能会注意到铸件内的一些孔。根据气孔的严重程度,它可能导致其他类型的缺陷并增加废品率。
原因:
- 熔融金属合金释放的氢 – 较高的熔炼温度通常会导致熔融金属合金中的氢溶解度较高。压铸中涉及的冷却和凝固降低了氢的溶解度并将其从熔融金属中释放出来。因此,会出现气孔。
- 金属合金填充过程中涉及的气体 – 压铸过程涉及以高速和高压将熔融金属合金填充到模具中。因此,如果液态合金不能稳定有序地流动,就会发生湍流,从而导致气孔。
- 脱模剂产生的气体 – 脱模剂通常在熔融金属合金加热时分解并释放气体。因此,过度使用脱模剂会导致气体挥发。
解决方案:
- 通过在真空中使用助熔剂或在低溶解度气体周围熔化原材料来控制熔化过程,以阻止空气到达熔融金属。
- 确保您使用的是清洁干燥的金属合金锭。
- 使用可识别的压铸参数,包括注射速度。
- 足够的浇道和流道长度将有助于熔融合金稳定流动并轻松排出气体。
- 选择优质的脱模剂,用量合理。
2。 缩孔率
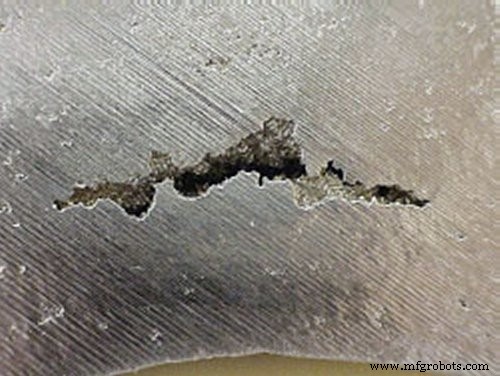
缩松是在铸件冷却凝固过程中形成的,金属合金在冷却时会收缩。因此,如果没有足够的预防措施,这种缺陷很可能发生。但是,当收缩不均匀导致形状变形或在铸件中产生孔洞时,就会成为缺陷。
缩孔可表现为开缩、翘曲和闭缩,影响金属的应力。您会将此缺陷视为棱角分明的边缘,并且它们还可能带有裂缝或树枝状断裂。
原因:
- 冷却系统设计不合理。
- 开模过早。
- 使用极高的浇注温度。
解决方案:
- 改善整体铸造结构。
- 重新设计运行(浇口)系统,使其具有能够实现连续熔融金属流动的冒口。
- 插入内部冷却装置、冷却盘管或肋条以增加散热。
- 调整铸造温度以减少总体积不足。
3. 内含物
这些是铸件内部或其表面上的不规则形状的孔。由于夹杂物,金属铸件中会出现不需要的砂粒、材料、浮渣或脱氧产物。夹杂物会影响金属铸件的力学性能,可以通过X射线或UT进行识别。
原因:
- 由于净化不当或垃圾污染导致的金属杂质。
- 炉料纯度低。
- 金属与周围大气或模具表面的相互作用。
- 脱模剂中含有过多的石墨。
解决方案 s:
- 确保炉料纯净。
- 彻底清除熔渣,对金属液体进行适当净化。
- 正确清洁模腔和钢包。
- 如果脱模剂中含有石墨,请确保搅拌均匀。
肤浅的 死去 选角 缺陷
这些类型的铸造缺陷通常是可见的,它们破坏了部件的表面及其美学质量。它们包括:
1. 裂缝
当材料由于材料内外的应力而破裂时,就会出现裂缝。它们在压铸表面上显示为不规则或线性图案。第一道裂纹发生在冷却凝固过程中。
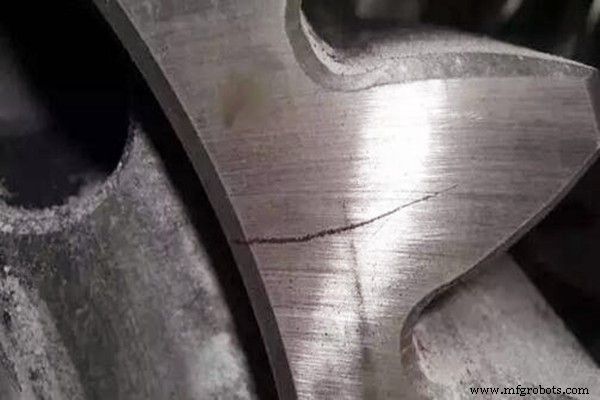
这是因为空腔几何材料在其自然状态下不能收缩。结果,残余应力会在模具中产生裂纹或变形。第二种形式的裂纹是由于部件上的外力而发生的。力来自零件顶出过程中的切削阶段或模具。
裂纹是成型合金中所含合金元素不当造成的。因此,您希望在熔化时使用正确的合金元素。此外,优化组件结构并确保均匀的壁厚将防止这种缺陷。平衡压铸件顶出也是解决这种铸造缺陷的好方法。
2。 冷关
在这里,铸件表面有不规则的直线。线条又窄又小,边缘光滑,可能会因外力而延伸。当模腔中的两个液态金属前沿熔合不当时,会出现压力压铸中的冷隔缺陷。因此,组件上留下了一个薄弱点。
熔液温度低、注射速度低、浇注系统设计不合理、合金流动性差是造成冷隔的部分原因。目视检查将帮助您发现此缺陷。避免冷关的一个好方法是提高模具和熔融金属的温度。您还可以在增加柱塞速度的同时改变游戏的大小和位置。
3. 网络裂缝
网状裂纹在压铸件表面表现为发丝状或网状的凹陷和突起。模具突起随着压铸时间的增加而延伸。模具型腔粗糙、充型温度高、铸造材料不当、热处理不当都可能发生。
您的压铸模具材料和热处理工艺必须足以避免这种缺陷。此外,您必须确保均匀和充分的模具加热以消除内应力。应采用适当的冷却方法确保模腔的热平衡。您希望压铸工艺具有良好的粗糙度。因此,应定期抛光模腔和浇注系统。
4. 拖焊
拖曳是平行于模具开口方向发生的缺陷。它们表现为铸件表面的条状划痕。焊接是由模腔和金属合金的异常粘连引起的。它在组件的某些区域显示为多余或缺少的材料。
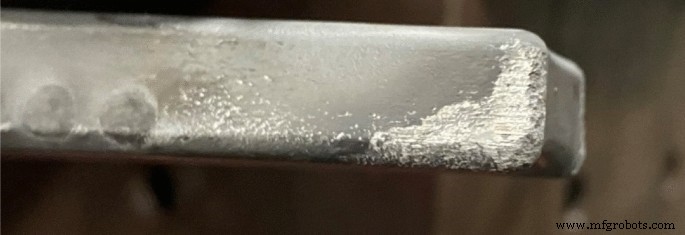
压力压铸中的这些缺陷是由于熔融合金过热、模腔表面损坏或拔模斜度不足造成的。不合理的注射机理和脱模剂质量差也可能导致这些缺陷。
因此,最好使用高质量的脱模剂并优化您的弹出机制。如果模腔表面有损坏,请确保进行适当的维修。您还可以调整浇口方向以保持模芯处于正确状态。
5. 闪烁
这种压铸缺陷会在压铸零件上产生薄的、不规则的金属板形状。其原因包括注射速度快、填充温度高、分型面上的垃圾不干净、模具锁模力不足等。因此,您必须使用正确的加工参数,并确保定期进行模具维护,以防止出现这种缺陷。
6. 起泡 s
压铸涉及压缩机器中的空气,并使用真空阀、溢流口或排气口将零件从铸件中弹出。留在里面的空气会均匀分布在熔化的金属中。湍流使空气集中,形成高压腔——水泡。
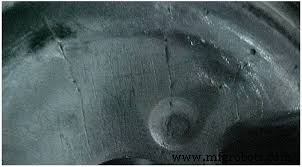
如果组件的温度较低,这种压力压铸中的缺陷就会隐藏起来,从而降低组件的强度。在温度高的情况下,您会注意到表面有气泡。因此,您的压铸参数必须足够。您还应该优化浇注系统以确保适当的排气性能。
7. 变形
当最终零件的形状与图纸不匹配时,就会发生这种情况。变形的发生是由于浇口去除不当、铸件设计不良、过早开模、顶出机构不足以及铸件顶出过程中的阻力。
因此,您必须确保选择合适的浇口移除机制。另外,调整开模时间,保证刚性。优化结构铸件设计并消除不利的脱模因素也有助于防止这种缺陷。
8. 流动标记
这些是压铸件表面上的条纹和非定向线,其颜色与铸件底部的颜色不同。进入型腔的液态金属通常会形成一个薄的、不完整的层,该层可能充满熔融金属。这种填充会在组件上留下痕迹。
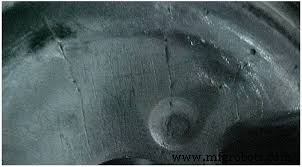
流痕的其他原因包括模具温度低、填充压力低、润滑剂或脱模剂过多以及横截面积小。因此,应提高模具温度调整注射速度、截面积等铸造参数。
9. 短填充
在压力压铸的这种缺陷中,铸件表面区域可能缺少一些材料。由于金属合金流动性差、填充温度低、注射压力低、填充条件差、润滑剂使用过多等原因。
避免短填充的一个好方法是选择正确的金属合金。如果您还提高模具和填充温度以及注射速度和压力,这将有所帮助。改进浇注系统设计和金属液分流也有助于防止短充。
10. 层压 s
层压来自在填充过程中分离的两层的重叠。压铸中的这些缺陷很难检测到。它们在喷砂和翻滚等预加工操作后出现。
在这些阶段,铸件和镶件之间的冲击会导致锌层上升。因此,污垢和液体可能隐藏在这些层的中间。在表面处理过程中,隐藏的物质可能会显示在表面上 像电镀和喷漆,使结果恶化。
11. 水槽
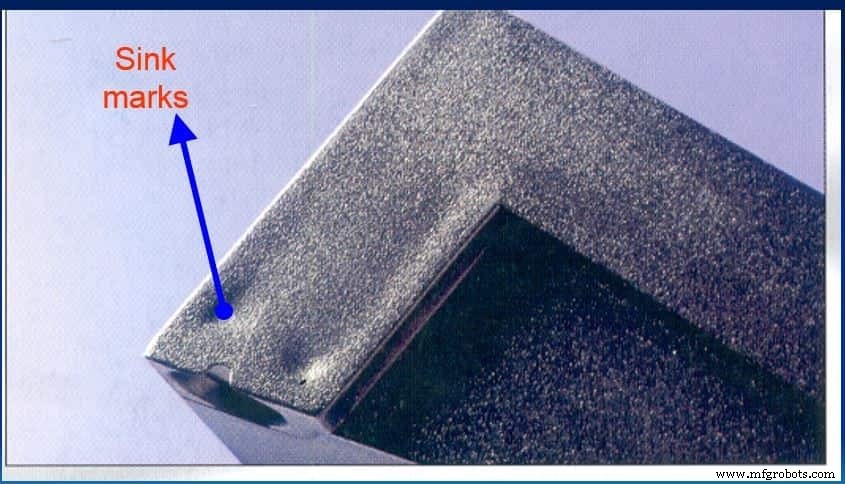
这些是铸件表面的凹陷以及厚壁区域。下陷是由于注射压力低、铸件壁厚不均、模具局部过热、保压时间短等原因造成的。
您可以通过优化铸件设计来确保均匀的壁厚。此外,您可以通过提高模腔的排气性能和增加注射压力来防止下沉。增加保压时间也是一种有效的方法。
避免提示 压铸缺陷
压铸缺陷的发生是由于各种原因。一个很好的成型设计指南 会有效。但是,以下“第一原则”提示将帮助您避免这些缺陷:
有效的评级系统
一个有效的评级系统会告诉您您是否正在减少缺陷或情况是否变得更糟。评级系统将帮助您了解是否需要更正。这很重要,因为您希望在缺陷达到高潮之前解决它。
气孔、缩孔和夹杂物是压铸中的主要缺陷,需要通过判断来了解其严重程度。既然不衡量就无法改进,因此需要一个有效的评级系统来避免这些缺陷。
右壁厚度
壁厚在铸造缺陷中起着很大的作用,不同的壁厚会产生不同的结果。薄壁会使金属合金冻结,增强变形。镁和铝的最小壁厚为1.5-2.5mm,锌为1.0mm。
正确的填充时间
填充时间从合金第一次到达浇口时开始,到型腔被填充时结束。以下是大多数铸造的最长填充时间指南:
合金 | 薄壁 <2mm | 平均墙 >2mm |
铝 大约 2 公斤 | .09 秒 | .1 秒 |
锌 大约 1.4 公斤 | .03 秒 | .05 秒 |
镁 大约 1 公斤 | .02 秒 | .03 秒 |
您可以使用 PQ2 计算来预测正确的填充时间。该计算通过更改以下任何一项来预测浇口速度和填充时间的变化:
- 门区
- 柱塞尺寸
- 机器液压
- 柱塞速度设置
正确的金属流动模式
栅极设计的关键因素是金属流动,这是设计标准的函数。这些简单的步骤将帮助您使用正确的金属流动模式:
- 使用 PQ2 计算来确定浇口尺寸和柱塞,确保使用正确的填充时间、浇口速度和型腔压力
- 然后将演员划分为区域
- 将大门分开,以便同时填满每个杂志
- 在演员阵容中流动
- 避免混合铸造缺陷
正确的模具温度
您必须使用正确的温度来避免铸造缺陷。低温冷却液态金属,并可能通过增加凝固部分来影响表面。高比例的固体金属会导致水流变得僵硬并且不能很好地混合。因此,可能会出现冷流,导致缺陷。
使用 快速直接 到 避免 压铸缺陷
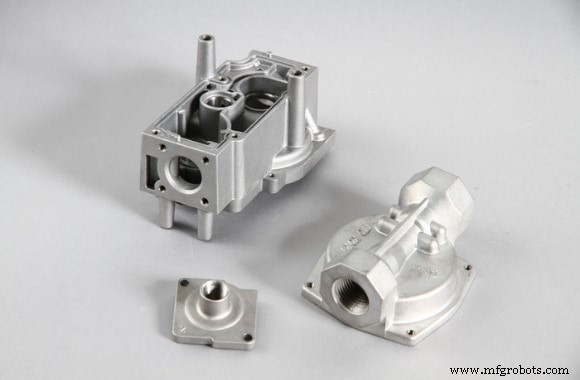
了解压铸缺陷及其原因对于确保零件质量至关重要。但是,要了解的内容还有很多,因此最好与压铸专家合作。 RapidDirect 提供最好的定制压铸服务 一流的材料,专业的技术人员,尖端的工艺。
我们以确保最佳质量为目标来处理您的项目。我们的机械师还持续监控该过程。因此,我们能够消除低效的流程并仅使用高质量的技术。立即上传您的设计文件,获取即时报价。
常见问题解答
如何减少铸造缺陷?您可以使用有效的评级系统来避免铸造缺陷。使用正确的壁厚。模具温度和金属流动模式也是有效的解决方案。
压铸有什么好处?压铸工艺在汽车行业中很受欢迎。设计师和制造商也使用此工艺制作装饰性硬件和其他较小的组件。
如何去除铸件中的孔隙?良好的模具设计将帮助您摆脱气孔。您还可以通过在浇注前向铝金属中添加氮来消除此缺陷。足够的浇道和流道长度将确保稳定的合金流动以轻松排出气体。
工业技术