消除障碍以优化新安装的磨削工艺
一般来说,新的大批量生产线包括磨削工艺在内的复杂零件,例如汽车发动机或航空发动机叶片和叶片,要经过从机器采购到实际生产的各个阶段,如图 #1 所示。如果这些行包含被认为“高风险的过程 ”它将与“开发时间”一起安排,作为磨床能力评估和购买(步骤 4 和 5)的一部分,通过测试和改进。这是一种有效的策略,可以大大减少与程序启动相关的问题,但可能既耗时又昂贵;很多时候工件样品甚至可能不可用,或者是需要进一步设计更改的原型。在这种情况下或对于不同的组件设计,但不是 完全不同 从现有设计来看,“优化时间”很少安排在实际机器鉴定之前。
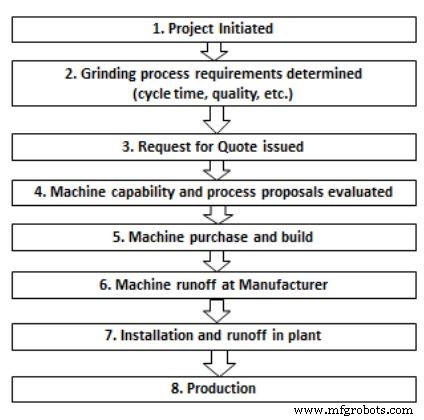
当机器合格并安装“非激进 ”流程,重点是零件质量和周期时间。在新零件设计的不确定性及其对保持零件公差的影响通常比生产所需的更严格的 CpK 规格的情况下,可以很好地选择车轮规格以确保最高质量。此外,由于成本或可用性的原因,通常只提供 50 或 100 个零件进行鉴定,这使得建立长期稳定的工艺成为问题。通常没有太多时间或组件来优化每个零件的工具或磨料成本。安装后,在很多情况下,“如果它没有坏,就不要修复它”的态度占据了主导地位,进程被锁定。很少尝试优化。
因此,将优化的“额外步骤”视为过程的最终“审核”非常重要。大多数情况下,此步骤可能只是一个过程“调整”,因此不需要对整个过程进行重新认证,但偶尔可能会发现足够大的机会,这将保证对循环和/或车轮规格进行重大更改。将进行成本/收益分析以确定是否应该进行更实质性的流程变更。
缺少“优化时间”会导致次优流程有几个原因:
- 自行车可以在机器中正常运行,但不是“车轮友好型”。即车轮寿命可能不够理想
- 车轮技术不断发展。对现有技术的估计可能不适用于新技术
- 零件配置、机器设计和质量要求的细微变化使生产线之外的流程优化变得非常困难。这是因为生产线提供了许多零件和具有真实变化和计量的环境。这两个品质为“优化”流程的“稳健性”提供了测试。
示例:
图#2 中所示的磨削循环由 OEM 发货,安装在工厂中,目前正在生产中。这个循环工作正常,生产出可接受的零件,但它不是“车轮友好型”。
此循环的车轮“不友好”是由于循环开始时的大峰值(功率/力)。砂轮磨损与磨削力的平方成正比,大的力会导致砂轮快速磨损。在这种情况下,减少快速进给并增加中进给将延长砂轮寿命,同时保持循环时间和零件质量。
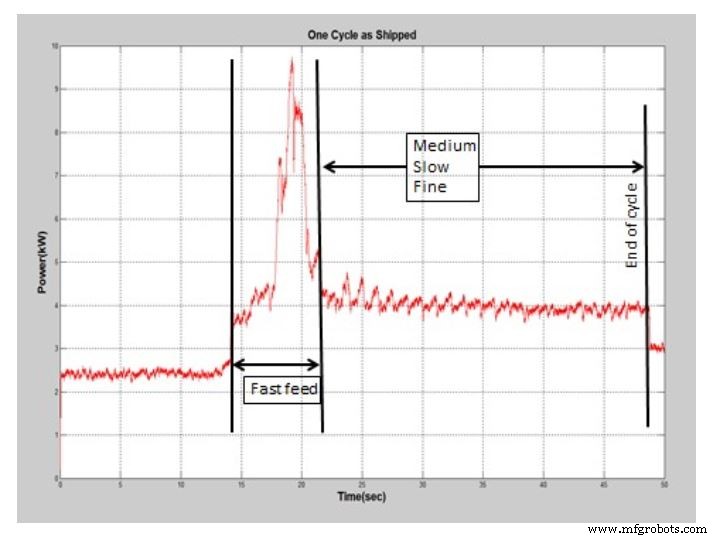
优化过程中的一个循环
在最近的一个不寻常的案例中,制造商同意对研磨过程进行“原位”优化。最初,磨削循环进行了更改,以使其更加“砂轮友好”,如上所述。在这种情况下,更友好的周期也比初始周期短了约 5 秒。
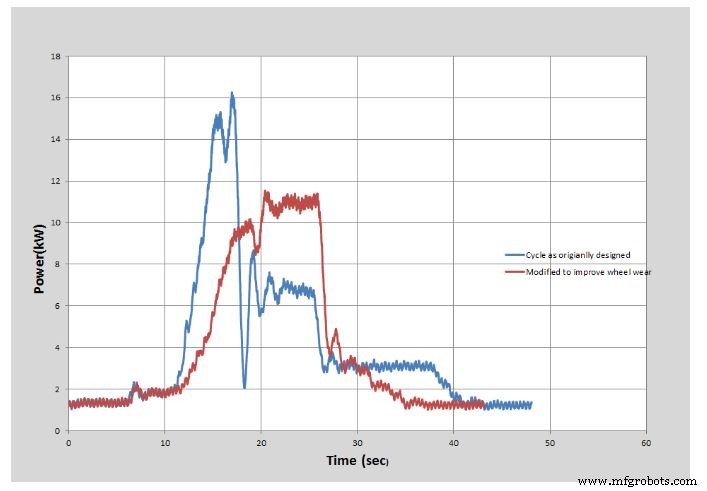
在改进的周期运行了几周以验证持续的零件质量后,每件衣服的零件从 8 个增加到 20 个,并且衣服的深度从 0.03 毫米减少到 0.02 毫米。这个过程现在已经运行了大约 6 周,零件质量没有显着变化。每年节省的成本汇总如下。
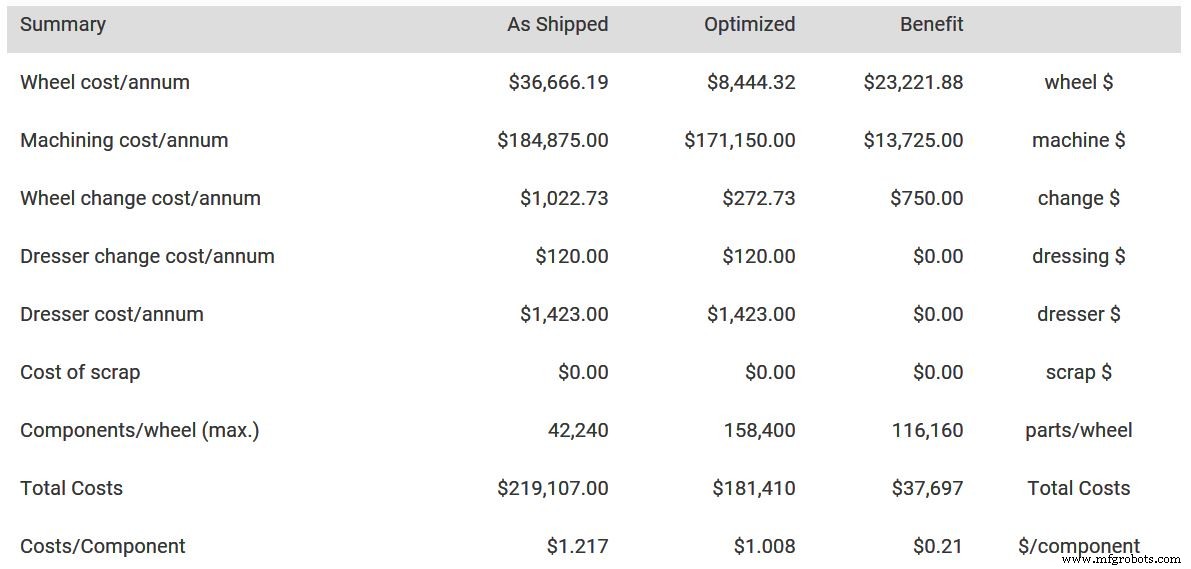
优化策略
如第二个示例所示,解决方案是在生产的早期阶段(图 #1 中的步骤 7 和 8 之间)安排时间和零件,以便与机器制造商和工具/磨料应用工程团队一起进行工艺优化.在这个阶段至少应该使用电力监控设备来协助周期评估和开发。通过这个额外的步骤,可以监控过程在更长的零件运行中的稳定性,这可以使问题暴露出来和/或提供改进的机会。
此步骤的潜在回报是巨大的,因为在此阶段所做的改进/成本节约将贯穿整个项目生命周期。
以前在 Norton Abrasives 上出现过
在 MSCdirect.com 上购买我们精选的诺顿网格轮。
工业技术