炉顶煤气回收高炉工艺
炉顶煤气回收高炉工艺
在高炉 (BF) 生产铁水 (HM) 领域,显着减少 CO2(二氧化碳)排放的最有希望的技术是从高炉回收 CO(一氧化碳)和 H2(氢气)离开高炉顶部的气体。高炉顶部气体中的 CO 和 H2 含量具有作为还原气体元素的潜力,因此将它们再循环到 BF 被认为是提高 BF 性能、提高 C(碳)和 H2 利用率的有效替代方法,以及减少二氧化碳的排放。这种“炉顶煤气回收”(TGR)技术主要基于在从炉顶高炉去除 CO2 后,通过重新使用还原剂(CO 和 H2)来降低化石 C(焦炭和煤)的使用量气体。这导致能量需求降低。由于具有高生产率、高 PCI(喷煤)率、低燃料率、低 CO2 排放等优点. , TGR-BF工艺被认为是未来很有前景的炼铁工艺之一。
在 TGR-BF 中,氧气 (O2) 被吹入 BF,而不是热空气,以消除顶部 BF 气体中的氮气 (N2)。部分含有 CO 和 H2 的顶部 BF 气体再次用作 BF 中的还原剂。高炉炉顶气中的 CO2 被捕获然后储存。已经针对不同的目标提出、评估或实际应用了几种回收过程。这些过程的区别在于 (i) 有或没有 CO2 去除,(ii) 有或没有预热,以及 (iii) 注入位置。
TGR-BF(图 1)的概念涉及许多技术,包括 (i) 在竖井和炉膛风口中注入还原炉顶气体成分 CO 和 H2,(ii) 由于焦炭含量较低,因此降低了化石 C 输入的消耗率,(iii)在炉膛风口处使用纯 O2 气体代替热风空气(从过程中去除 N2),以及(iv)从顶部 BF 气体中回收纯 CO2 用于地下储存。
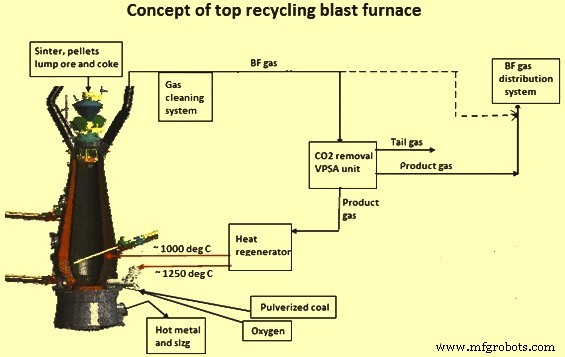
图1 TG-BF的概念
炉顶煤气回收的概念已经在瑞典吕勒奥的 LKAB 实验高炉 (EBF) 进行了实验测试。对EBF进行改造,在EBF附近建设了基于VPSA(真空变压吸附)技术的气体分离装置。
高炉炉顶煤气回收的历史
为了降低还原剂的用量和提高高炉的生产率,在传统高炉工艺的基础上,20世纪出现了几个新的概念。
早在 1920 年代,就开发了一种将热还原气体注入高炉的概念。需要通过将 1000 ℃、27% CO、33% H2 和 26% N2 的预热还原气体注入下部竖井区域来补偿来自炉中风口的较低气体体积。结果发现只有 30% 的焦炭(当时为 345 kg/tHM)对于 BF 工艺是必需的。在 1960 年代中期,这个想法在比利时再次被采纳,并在 1970 年代初期在比利时 Cockerill-Seraing 的 4.6 m 炉床直径的 BF 上进行了第一次试验。将预热至 1000 摄氏度的特定量的 400 N cum/tHM 的重整气体注入高炉的下竖井。观察到每 N 立方米还原气的焦炭置换率为 0.22 公斤至 0.26 公斤。
由于天然气成本高,出于经济原因,未进行进一步调查。 1970 年代后期,在德国开始了一项新工艺的开发工作,其中在两个风口处注入冷纯 O2、燃料和循环气体。基于这个想法,加拿大于 1984 年开发了一种工艺,用于没有第二排风口的传统高炉。这个概念的主要特点是注入煤来替代焦炭。这两个概念都没有实现,只是作为一项研究结束。
几乎与此同时,日本的 NKK 进一步采用了这一想法,在竖井中间安装了第二排风口。在这些风口中注入预热的还原气,包括没有去除 CO2 的回收炉顶气。通过与氧气部分燃烧来加热气体。冷的 O2、煤和冷的循环炉顶气被注入炉膛的风口。 NKK 在具有 3 个风口、内部容积为 3.9 厘米、炉膛直径为 0.95 m 的实验性高炉中测试了该过程。喷煤量可提高至 320 kg/tHM,而焦炭量可降低至 350 kg/tHM。由于日本的电能和天然气价格居高不下,由于回收顶部高炉煤气而导致综合钢铁厂燃料气短缺,停止了该工艺的开发。
1980 年代后期,RPA Toulachermet 在俄罗斯的 2 号高炉进行了 12 次活动,在 1980 年代后期进行了具有炉顶煤气回收的高炉的首次商业运营,有效容积为 1033 立方米。在这个全焦高炉工艺概念中,几乎不含 CO2 的热炉顶煤气与纯 O2 一起被吹入炉膛风口。脱碳后的炉顶气在热炉中加热到 1200 摄氏度。通过这种新工艺,生产了近 250,000 吨铁水 (HM)。达到的最低焦炭率为 367 kg/tHM,而参考值为 606 kg/tHM,这意味着焦炭率降低了 239 kg (39 %)。在这些活动中,出现了严重的风口烧坏现象,导致风口设计发生了变化。二氧化碳清洁系统的问题最终停止了这一过程。考虑到这些背景调查,2004年提出了ULCOS(超低碳二氧化炼钢)TGR-BF的概念。
ULCOS TGR-BF的开发
开发工作分两个阶段进行。在 2004 年至 2009 年的第一个开发阶段,该工艺被命名为“ULCOS 新高炉工艺”。在此阶段,已开发和测试了三个新的工艺概念。在 2009 年开始的被命名为“ULCOS 炉顶煤气回收高炉工艺”的第二阶段,又进行了两次 ULCOS TGR-BF 活动。
在开发过程中,热质平衡模型和高炉的 3-D 轴对称模型用于计算主要数据和过程的内部状态,以选择最佳操作参数。定义并检查了四种替代方案,以了解可能达到的 C 节省以及在这些新概念下运行 BF 的可行性。结论是替代方案 1、3 和 4 应该能够在高煤粉喷射水平的情况下实现 21% 或更高的化石碳节省。备选方案 2 被拒绝,因为预期的 C 节省量较低,并且必须先在同流换热器中分两步加热循环气体,然后通过部分氧化进一步加热。所有替代方案都包括去除 CO2 并将富含 CO 的产品气注入炉膛风口,使用纯 O2 以及将煤与还原气一起注入。在所有的替代方案中,生物质、部分还原矿石和富氢气体的使用都被认为是未来的一种可能性。
在备选方案 1(图 2)中,脱碳产品气在炉膛风口处与纯 O2 和煤一起冷注入,而在竖井风口处注入热源。这种替代方案的一个关键点是炉膛风口处的小冷气流速,与正常的 BF 工艺相比,导致更小的滚道尺寸和更高的火焰温度。此外,由于气体流量小,因此需要新的风口设计。
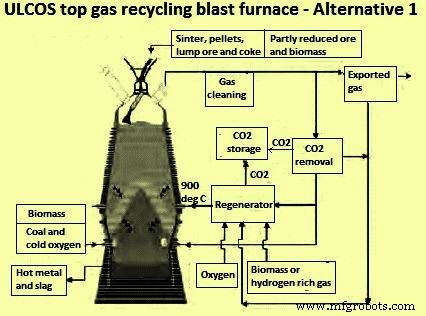
图 2 ULCOS 炉顶煤气回收高炉 - 备选方案 1
在备选方案 3(图 3)中,脱碳产品气与 O2 和煤一起在正常炉膛风口处热注入。为达到高节碳效果,必须在低RAFT(滚道绝热火焰温度)的同时,以高喷煤量运行。
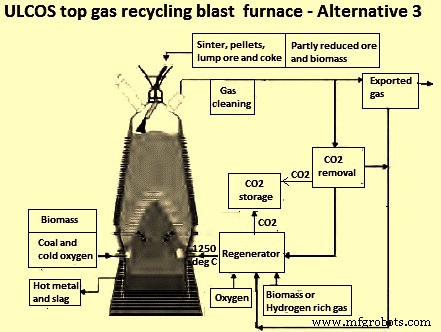
图 3 ULCOS 炉顶煤气回收高炉 - 备选方案 3
在备选方案 4(图 4)中,脱碳产品气在炉膛风口处热注入,在下竖井处热注入。回收气体温度从室温到1250℃不等。
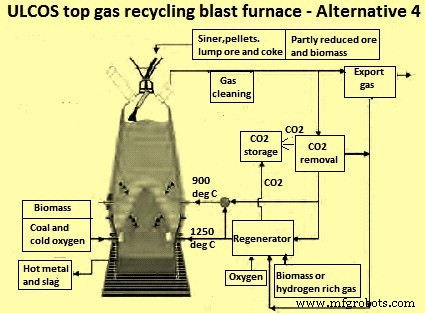
图 4 ULCOS 炉顶煤气回收高炉 - 备选方案 4
在备选方案 1 和 4 中,产品气也通过轴风口注入。不同之处在于气体注入温度和注入点的位置。在所有情况下,至少部分气体在再生系统中被加热。替代方案 1 在 170 kg/tHM 的燃煤率下的预期化石碳节省为 21%,在 180 kg/tHM 的燃煤率下,替代方案 3 为 24%,在 150 kg/tHM 的燃煤率下,方案 4 为 25% .
然后进行了管道条件的数学建模和气化测试,并在同时注入循环气体、纯 O2 和煤粉的约束下,对风口的设计和工程进行了实验室和中试规模调查。根据计算结果对风口的几何形状进行了改进,以避免在运行过程中出现热点和故障,并保持足够的气流冲量以形成足够深度的滚道。
实验BF中TGR-BF过程的活动
试验的目的是演示 EBF 在完全 TGR 模式下的运行,炉膛风口处有纯 O2 和 PCI。这是在三个定义的替代方案下进行的。铁料由 30% 的球团和 70% 的烧结矿组成。 HM 的生产速度保持在每小时 1.5 吨的恒定水平,PCI 速度在 130 kg/tHM 到 170 kg/tHM 之间变化。在不同的试验期间,回收的炉顶气的体积最大化,以获得最大的化石碳节约。然后将EBF试验中获得的结果与模型计算进行比较。
备选方案 3 和备选方案 4 于 2007 年在常规启动后的第一次活动期间进行了测试。备选方案 3 在 2009 年秋季的第二次活动中进行了优化测试,随后对备选方案 1 进行了测试。在 2010 年的第三次也是最后一次活动中,重点是在 900 摄氏度的备选方案 4。备选方案 4 被认为是ULCOS BF 后续工业规模示范项目的首选替代方案。为避免耐火材料H2还原二氧化硅的问题,设定了回注气体温度900℃的极限。
在每次活动期间,使用两个负载内探头从 EBF 中对温度和气体成分以及来自负载材料的样品进行现场测量。为了研究新操作条件下的配料行为,在活动停止前将装有不同烧结矿和球团材料的篮子装入 EBF。这些篮子是在用氮气淬火后的熔炉解剖过程中从 EBF 中回收的。这在 2007 年和 2010 年的活动中已经完成。在 2009 年的第二次活动中,由于 EBF 收费系统存在问题,活动没有准备好结束,因此只能进行淬火,因此没有对篮子进行收费。
在活动期间,从粘性区域回收样品并测量滚道的大小和形状以供进一步调查。这些活动从一周的常规 BF 正常运行(热风鼓风)与烧结矿开始,首先用于加热和热稳定,然后为常规 BF 运行建立参考。参考后,停止鼓风机并将产品气体连接到卵石加热器(再生器)。 TGR-BF 模式的启动是由人工鼓风完成的,其中包括来自喷枪的冷 O2 和来自卵石加热器的热 N2。在逐步的步骤中,来自卵石加热器的 N2 被脱碳的炉顶气(产品气)取代。
ULCOS TGR-BF 活动结果
从活动中得出的第一个结论是,可以运行 ULCOS TGR-BF 流程。在采用新工艺的活动期间未发生安全相关问题。作为第二个重要设施的 VPSA 装置的运行很顺利,没有出现任何重大故障。 EBF 与 VPSA 单元在活动期间运行良好。
然而,必须注意的是,VPSA 装置的运行受到炉顶气体成分变化和 EBF 气体体积变化的影响。因此,这两个单位都将在非常密切的关系中运作。活动期间实现的最大回收炉顶气比例约为90%。
在TGR-BF工艺运行过程中,高炉运行稳定,炉料下降平稳,热稳定性易于保持。 BF 竖井中气体的效率在不同的替代方案中是稳定的,并且存在良好的气体分布,如负载竖井探头的测量所示。然而,由于在新工艺条件下的运行过程中,EBF 不得不停止运行,因此在活动期间发生了一些设备故障。一些长时间的停工需要回到“常规操作”的操作步骤,即冷 O2 人工热风和热 N2 操作。小停工只需要停止注气和添加一些额外的焦炭和/或煤。
用 N2 启动后,当没有顶部 BF 气可用时,产品气可在 1 小时左右再次循环使用。所有问题都如预期得到解决,高炉的热稳定性从未受到严重威胁。在整个运动过程中,获得的经验和增强的信心逐渐使 EBF 恢复更快(在生产水平上)。每次更换备选方案(3 至 4、3 至 1)时,BF 都会停止大约 8 小时,以便与竖井风口进行必要的气体连接和炉膛风口的更换。
在实验室级别进行的实验表明,传统的炉料不会成为新工艺的问题。这在竞选期间得到了证实。没有特定的工艺问题与装载材料的性质有关。探针和挖掘样品的结果都显示了中心工作炉的还原曲线,对于烧结矿和球团样品,炉壁的还原水平较低,而炉中心的还原水平较高。对开挖样品的翻滚测试显示出类似于实验室测试的传统高炉工艺之一的崩解行为。从炉料测试工作可以得出结论,目前常规高炉所用炉料特性似乎对ULCOS TGR-BF工艺没有问题。
在节约碳(煤和焦炭)方面,ULCOS TGR-BF 活动期间取得的成果非常令人鼓舞。所有三个活动的试验表明,通过注入脱碳的顶部 BF 气体实现了还原剂速率的显着降低。在这三个活动中,煤和焦炭的投入从大约 530 kg/tHM 下降到 400 kg/tHM,这意味着碳的大量节省。碳投入从 470 kg/tHM 下降到大约 350 kg/tHM,导致碳节省约 25 %。
尽管由于第二次活动提前停止而无法充分探索备选方案 1,但与传统高炉操作下的参考期相比,通过焦炭输入的 C 最大减少量为 21%。为此,开发了一种新的风口技术。风口设计由同轴管组成,内管用于喷射煤粉,外管用于喷射 O2。安装的三个风口效果很好,拆开后既没有发现损坏也没有磨损。 VPSA能够回收高达88%的高炉炉顶气。
至于替代方案 3,在第一个活动中,C 消耗可减少高达 15%,炉顶煤气回收率约为 72%。这种替代方案的结果(约 15%)低于热量和质量平衡计算的预期结果(24%),因为这是第一次使用炉顶煤气回收模式,并且该过程没有得到优化。在第二次活动中,这种替代方案的效果要好得多,当炉顶煤气回收率高达 90% 时,C 输入的最大减少量约为 25%。
在备选方案 4 的情况下,通过 90% 的炉顶煤气回收率实现了 24% 的 C 节省。在焦炭和煤炭消耗方面,与参考运行期相比,新工艺(备选方案 4)最多可节省 123 kg/tHM。从这些结果可以确定注入气体量(CO+H2)和还原剂速率降低之间的良好相关性。每注入 100 N 立方米的气体(CO+H2),平均可减少焦炭和煤的 C 输入量 17 kg。
EBF 的活动已经证明,与当今 BF 的消耗水平相比,可以在低得多的化石 C 消耗水平上运行 BF 工艺。通过注入还原性脱碳炉顶气,C 可节省高达 25%。与当今最佳操作的 BF 工艺相比,这是一个显着的下降。事实上,BF-TGR技术在现代高炉上的应用有望使碳消耗量从目前的405 kgs C/tHM左右降低到295 kgs C/tHM左右。
VPSA装置运行稳定。已经注意到 VPSA 装置可以处理 97% 的高炉炉顶煤气。注气中CO2平均体积分数在2.67%左右,CO回收率为88%,满足数量和质量要求。结合VPSA和CCS装置,TGR-BF工艺减少的CO2排放量可达1270 kg/tHM,占炼铁过程CO2排放总量的76%。 24%的CO2被气体回收利用,另外52%通过CCS运输和储存在地下。
从工艺的角度来看,就HM的温度和质量而言,ULCOS运行比传统的BF运行更稳定。这似乎主要是由于与低得多的直接还原率 (DRR) 水平相关的溶液损失反应的影响较小。该 DRR 的最低观测值为 5%。运行结果中没有迹象表明这实际上是在 ULCOS TGR-BF 中可以达到的最小值。 HM 的质量在很大程度上受到 ULCOS TGR-BF 运行的影响。特别是,观察到硅含量的显着降低(大于 1% 绝对值)和 C 含量的相关增加。然而必须指出的是,传统 BF 操作中的硅含量要低得多(传统 BF 中的硅含量约为 0.5%,而 EBF 中的硅含量约为 2.0%),因此在 ULCOS 的应用过程中不应预期会有如此大的变化工业规模的BF-TGR工艺。
ULCOS TGR-BF 的测试活动表明,新的 TGR-BF 工艺可行且易于操作。操作安全性好、效率高、稳定性强。测试活动证明,可以在 4 种操作模式(传统、备选 1、3 和 4)之间转换 EBF 操作。它还证明了高炉工艺和气体分离装置 VPSA 在闭环中运行是可能的。获得的 C 节省与流程图计算的预测一致。试验还表明,常规炉料烧结矿、球团矿和焦炭适用于ULCOS TGR-BF工艺。
根据 EBF 活动的经验,对于 ULCOS TGR-BF 工艺的安全和可持续工业应用,需要注意的事项是 (i) 风口水平面的气体泄漏风险可能要求风口水平面与铸造车间物理隔离防火,(ii)由于法兰在高温下弯曲而导致泄漏的风险,(iii)从热炉/加热器延长烟囱以避免周围有毒气体,(iv)避免启动阶段的故障, 操作人员将在功能测试期间接受人工气体培训, (v) 最佳喷射参数对于避免风口鼻部积聚/堵塞很重要, (vi) 对风口进行单独的鼓风流量控制以避免积聚的重要性(vii) 对耐火材料的选择和耐火材料的制造进行修改,尽可能避免使用 C 钢锚,交替通常使用除 C 钢以外的其他材料,或涂有氧化铝的钢,并且 (viii) 通过仔细选择金属部件来避免金属粉尘是很重要的。
试验结果表明,方案4减排效果最好,被选为下一阶段工业规模高炉试验的首选方案。
制造工艺