指定和订购定制金属铸件:指南
确保您的定制金属铸造项目成功的 9 个重要考虑因素
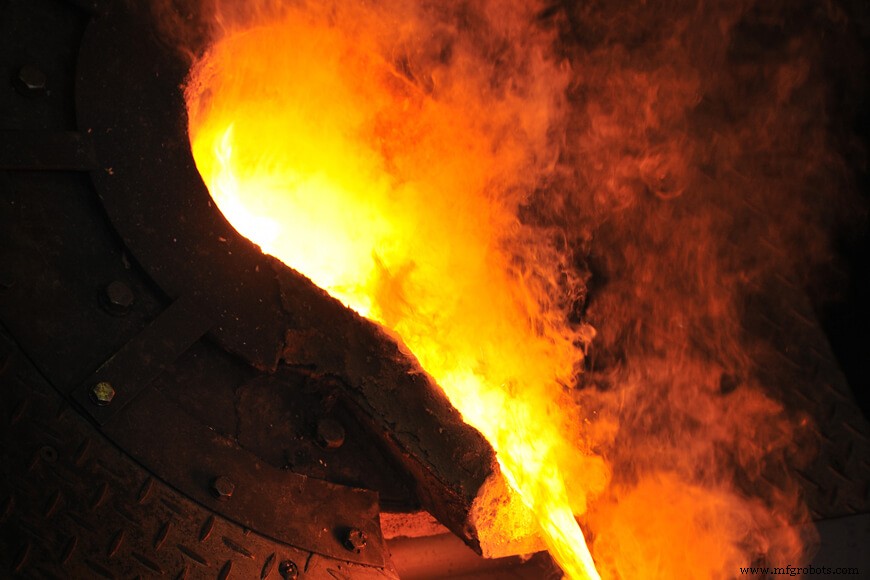
金属铸造是一种通过用液态金属填充模具中的空隙来产生形状(铸件)的过程。铸造金属产品具有出色的强度和耐用性,使其可用于农业、汽车、铁路、家用电器、建筑、造船、石油和天然气开采、水处理、林业和采矿等行业的重型机械应用。很少。
认证供应商铸造厂和订购金属铸件可能是一项耗时的考验,但并非必须如此。通过了解报价和铸造过程,可以避免代价高昂的错误。与供应商代工厂进行清晰而彻底的沟通将产生设计良好且经济的最终产品。
请求报价
索取铸件报价的目的是建立采购铸件成本、质量和交货时间的最佳平衡。虽然自动选择最低报价可能很诱人,但这样做可能会导致交货延迟或铸件质量下降——从长远来看,这两者都可能更加昂贵。
精明的客户必须权衡收到的报价单的所有规定,包括工具要求、公差和精加工余量,以及图纸、规格和加工要求的任何例外情况。其他因素,例如减少的机器工作量、改进的交货条件以及供应商的铸造经验和可靠性,对于确定铸件的实际成本与价值尤为重要。
在向供应商铸造厂索取金属铸件定价时,至少需要考虑九个重要因素:
- 初步铸件设计
- 数量
- 规格
- 健全性
- 测试和检查
- 重量
- 模式
- 加工
- 生产和交付时间表
1。初步铸件设计
铸造金属零件的设计应充分利用铸造工艺。对于高效且成本敏感的生产,铸件设计应选择最简单的生产方法,以达到所需的物理性能、净形状要求和外观。
任何报价请求都应包含详细说明所需零件确切尺寸的图纸。
在设计的几个关键组成部分,了解代工工艺和/或与供应商代工厂的沟通将有助于从代工厂的角度确定最具成本效益的设计。
最小截面厚度
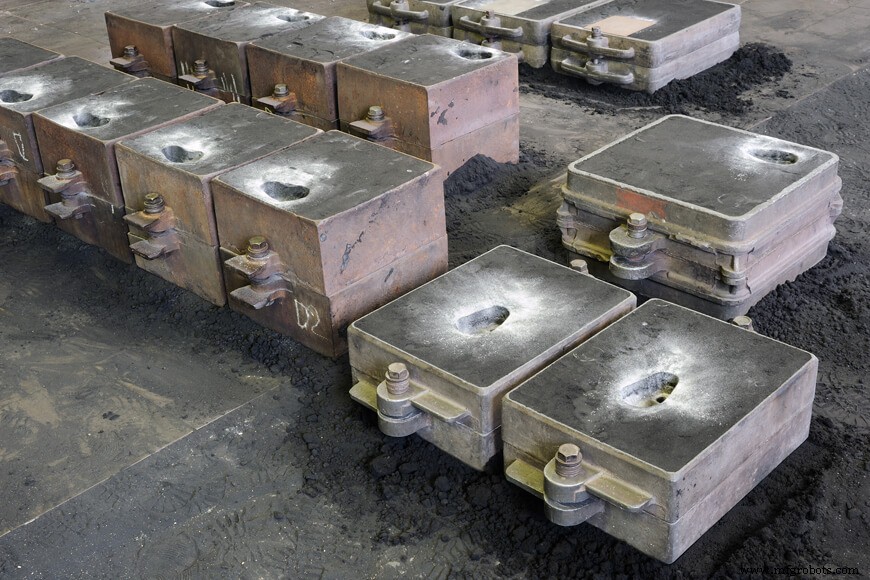
每个铸件都有一个由其强度和刚度决定的最小厚度。比规格更薄的设计可能会使项目无法浇铸。为了获得成功,铸件的设计必须允许液化金属在较薄的部分填充模具。
液化(熔融)金属以极快的速度冷却。进入远离模具浇口的薄部分可能会冷却得太快。通常,使用传统工艺时,设计的区域不应小于 0.25 英寸(6 毫米)。熔模铸造具有更大的自由度,壁厚可以低至 0.030 英寸(0.76 毫米)。
草案和核心
术语“拔模”是指图案垂直面上的锥度。在不干扰模具壁的情况下,需要使用拔模从模具中提取图案。忽略这些角度的限制会导致模具从铸件中取出时撕裂。
有几个因素会影响每个铸件需要多少拔模量:制造工艺、铸件尺寸以及是手工还是机器成型都会改变所需的拔模量。机铸铸件需要较少的拔模。然而,使用湿砂模具生产的铸件将需要比平时更多的拔模。一般的经验法则是每英尺允许 3/16 英寸的吃水(大约 1.5 度)。
型芯是由一块型砂在铸件内形成的中空空间。当无法单独使用图案创建空间或空腔时,核心是必需的。使用型芯可以消除对拔模的需要,但是它们的使用应该受到限制,因为它们会增加铸件的成本。
三个因素会影响可放入铸件中的芯子的最小直径:
- 将放置核心区域的厚度或深度,
- 核心有多长,以及
- 供应商铸造厂将采用的铸造方法。
分型线
在一个平面上分模有利于图案的制作以及模具的制作。与具有不规则分型线的图案相比,具有直线分型线(在一个平面上具有分型线)的图案可以更容易地生产且成本更低。对称的铸件形状很容易暗示分型线。这种铸造设计简化了成型和取芯,应尽可能使用。它们应始终制成“分模”(分离上模和下模),这需要在模具中进行最少的手工操作,提高铸件光洁度并降低成本。
核心
型芯是一个单独的部件(通常由型砂制成),放置在模具内以产生开口和空腔,这些开口和空腔无法单独由图案制成。为了降低铸件的最终成本,设计应尽一切努力消除或减少所需的芯数。
能成功用于铸钢件的芯子的最小直径取决于三个因素:
铁芯周围金属部分的厚度,
铁芯的长度,以及
供应商代工使用的特殊注意事项和程序。
随着围绕芯的金属厚度增加和芯直径减小,芯所经受的不利热条件的严重性增加。来自重型部分的这些不断增加的热量必须通过核心消散。随着热条件的严重性增加,铸件的清洁和取芯变得更加困难和昂贵。
围绕核心的金属部分的厚度和核心的长度都会影响由浮力在核心中引起的弯曲应力,因此会影响供应商获得所需公差的能力。如果核心的尺寸足够大,通常可以使用棒来加强核心。自然地,随着金属厚度和芯长度的增加,抵抗弯曲应力所需的钢筋量也会增加。因此,最小直径的核心也必须增加以适应额外的加强。
当要清洁的区域无法进入时,从铸造型腔中移除型芯的成本可能会变得过高。铸件设计应提供足够大的开口以允许移除型芯。
铸件中不易接近的区域使去除型芯变得更加困难,并影响项目的经济可行性。铸件的设计应始终设计有足够大的开口以允许移除型芯。
除非另有说明,铸件通常带有未加工的铸态表面。为了利用铸造工艺,供应商铸造厂应该知道最终要加工哪些表面(有关更多详细信息,请参见下面的“8. 加工”)以及基准点的位置。提供图纸时必须注明可接受的尺寸公差。公差通常由供应商代工厂和客户商定。
客户的设计工程师和供应商铸造厂之间的密切合作对于优化铸件设计至关重要。所有铸件设计都应在生产前由铸造专业人员检查,以确定铸件项目的可行性。
2。数量
应明确说明要生产的铸件数量或运行时间。订单数量将对价格产生重大影响,较长的生产周期对应较低的单次铸件成本。
所需的零件数量不是一个小问题;零件的项目消耗不仅会决定所需的工具类型,还会决定特定代工厂满足产量需求的能力。
许多代工厂专门从事短期、短期的“工作”工作,而另一些则专注于大批量生产。尽早确定您的需求将有助于确保您与正确的生产设施进行沟通。
3。规格
行业标准规范为铸造客户提供了为几乎所有铸造应用建立标准所需的工具。这些规格不排除客户技术人员可能要求的特殊要求。与标准规格的差异可能会导致误解、更高的成本以及潜在供应商代工厂的资格丧失。如果对规范要求主体中的某条规定采取例外处理(而不是对规范的补充要求采取例外处理),则生成的铸件不能符合这些规范。
应使用国际公认的标准(如 ASTM)指定要铸造的确切金属合金。铸件由两类金属制成:黑色金属(铁基)和有色金属(非铁基)。
铸钢是最常见的黑色铸造金属,但也可以根据所需的物理特性使用其他金属,包括不锈钢、可锻铸铁和球墨铸铁。铝和铜是铸造中最常用的有色金属。

机械性能可以通过使用单独铸造或附在铸件上的测试棒来验证。获得的机械性能代表金属的质量,但不一定代表铸件本身的性能,这些性能受热处理过程中凝固条件和冷却速度的影响,而后者又受铸件厚度、尺寸和形状的影响.某些牌号的硬化能力会限制获得所需机械性能的最大尺寸。
热处理
热处理用于标准化、均匀化和增强特定合金的性能。对于许多合金,热处理是一种常规工艺,用于确保在最终铸造产品中达到规定的最低物理性能。温度控制装置甚至先进的温度记录设备在现代热处理炉上普遍存在,以确保热处理步骤的一致性和质量。
在某些情况下,专门的热处理(如火焰硬化、表面硬化等)可以指定为由供应商铸造厂进行的附加工艺。
4。健全性
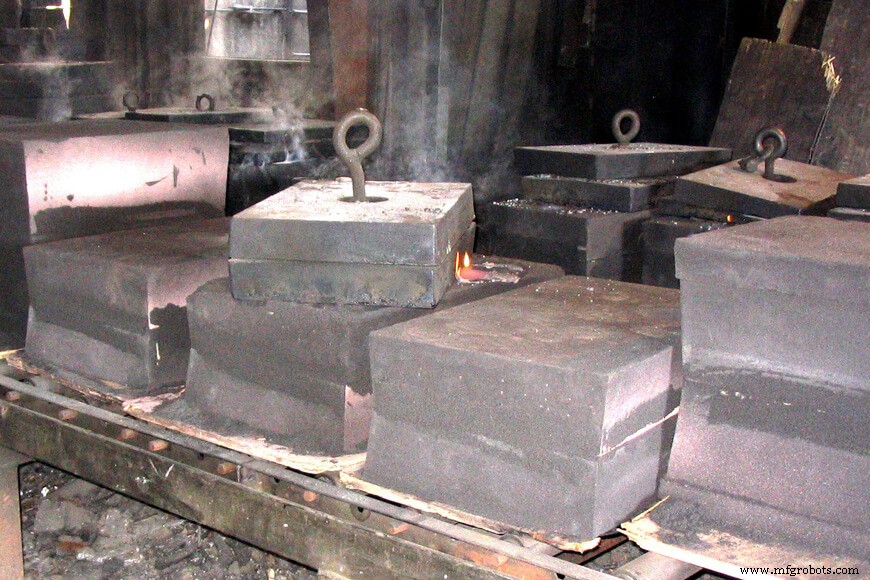
金属部件的完好性是指无杂质和/或不连续性的水平,例如夹砂、夹渣、大孔和收缩。不可能生产出无缺陷的铸件——只有具有不同程度缺陷的铸件。铸件的验收或拒收是根据客户的正式工程要求,通过对零件的检验(按照ASTM等国际公认标准)确定的;接受和拒绝标准由供应商代工厂和客户在生产前达成的协议定义。这些标准会影响铸造成本和所使用的生产工艺。
5。测试和检验
生产后,所有铸件都应进行检测,以确保它们符合规范的要求。还检查铸件的尺寸精度、表面光洁度条件、物理性能、内部健全性和裂纹。在许多应用中,测试是强制性的;可能需要进行额外的测试以确保满足材料规格或其他一般要求。
测试和验收标准必须在生产前明确传达并达成一致。更严格的测试条件会增加总体成本。为了保持成本效益,测试和验收条款应基于每个应用程序的精确要求。
铸件检测有两种类型:破坏性测试和非破坏性测试。
破坏性测试
破坏性测试除了需要的零件外,还需要单独铸造一个测试铸件。然后对试铸件进行破坏,以目视确定内部的完好性(夹杂物的体积、收缩或存在的气体)。破坏性测试只告诉被测件的状况,并不能保证其他未测试件的完好,但在实践中被广泛使用。如果试铸件是合格的,则生产可以在假设以相同方式生产的铸件表现出相同水平的健全性的情况下进行。
无损检测
对铸件本身采用无损检测方法,在不损坏产品的情况下,验证其内部和外部的健全性。检测方法包括外观检测、尺寸检测、液体染料渗透检测(LPI)、磁粉检测(MPI)、超声波检测(UT)和射线检测(X-Ray)。
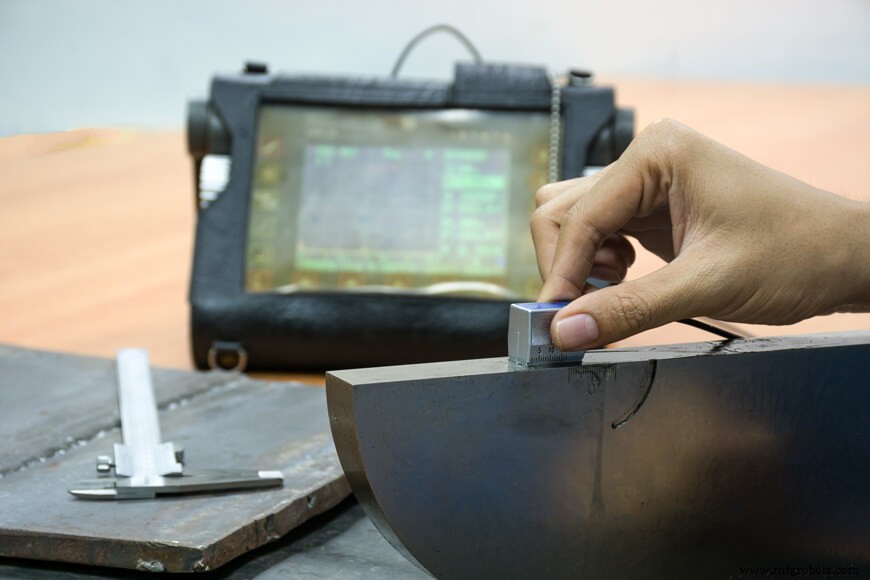
检验完成后,检验合格的铸件有时会按原样使用并运送给客户,但更多情况下需要进一步加工。这可能包括专门的热处理、喷漆、防锈油、其他表面处理(如热浸镀锌)和机械加工。
6。重量
任何铸件的一个重要成本组成部分是材料。铸件的重量越高,该铸件的材料成本就越高。向代工厂提供的零件重量数据越详细,价格计算就越准确可靠。
铸造厂不仅关心铸件的净(产生的)重量;他们最关心的是铸件的毛重。总重量是通过填充由所得铸件组成的模具所需的熔融金属重量以及确保铸造过程产生良好铸造结果所需的所有进料(浇口、冒口等)的重量来衡量的。铸造厂的铸件价格将受到铸件成品率(铸造工艺效率和铸件重量除以注入模具的原料重量)的显着影响。
7。模式
制作模具需要打版,打版是生产图案的过程和贸易。由于图案是铸件的形式,因此铸件不会比制造它的图案更好。如果需要紧密的公差或光滑的铸件表面处理,那么仔细设计、构造和完成模型尤为重要。
图案设备设计和由此产生的成本可能构成客户和供应商代工之间误解的主要来源。即使现有/旧设备可用,也需要建造新的模型设备以适应铸造厂的生产机械,需要用全分芯盒代替半芯盒,需要生产金属模型而不是木模型,和/或安装模式的需求,而不是松散的模式使用只是影响设备成本的许多讨论领域中的一小部分。最低的铸造成本和最高的铸造质量总是从更精密的制模设备演变而来,从而产生最高的制模成本。
8.加工
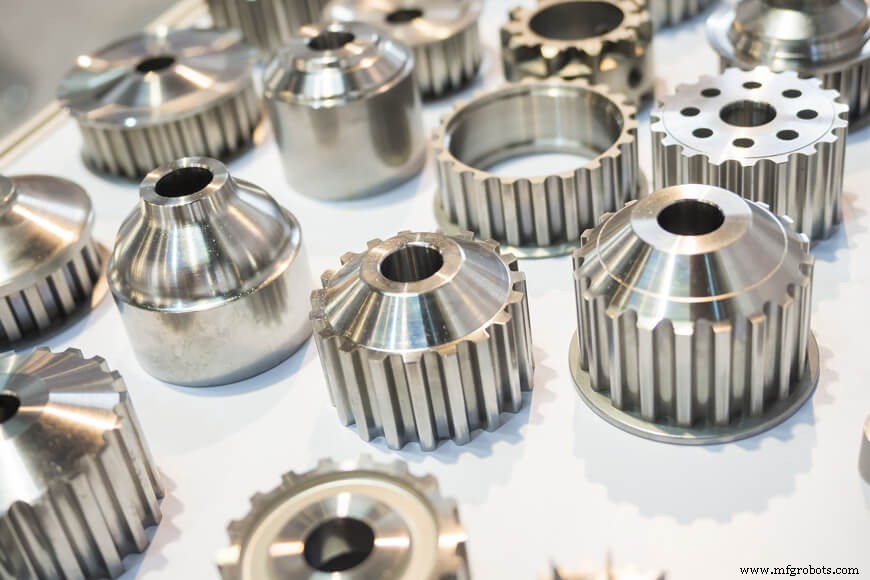
机械去除多余材料的过程称为机械加工,当需要高水平的尺寸精度时,这是一个至关重要的过程。因此,在需要时应分配一定量的附加材料作为加工余量,特别是当铸造的零件或产品具有严格的公差时。
公差是指给定生产方法可达到的尺寸精度。模具膨胀、凝固收缩和热收缩都会影响湿砂铸造过程中成品零件的公差。因此,铸态零件的公差存在限制。当需要更严格的公差时,通常采用后续加工。
并非所有供应商铸造厂都提供内部加工,但他们负责生产能够通过加工进行转换以满足其对零件的特定要求的铸造产品。为了实现这一目标,客户的工程和采购人员与铸件生产商之间必须保持密切的关系。采用合作方式,必须考虑以下几点:
- 铸造工艺及其优点和局限性,
- 加工余量(粗切削后用于精加工的材料量),以确保清理所有加工表面,
- 与应用在加工过程中固定零件的夹具和固定装置相关的产品设计,
- 材料规格和热处理的选择,以及
- 要生产的零件数量。
首次生产时应检查每个铸件设计,以确定是否可以达到所有加工要求。实现此目的的一种方法是创建样品铸件的完整布局,并检查所有需要加工程序的表面是否存在足够的加工余量。
对于更简单的设计,可能不需要完整的铸件布局。但在其他加工尺寸更复杂的情况下,建议对铸件进行彻底检查。这可以通过设计目标点和标出线来指示所有加工表面来完成,从而确保所有生产阶段的一致性。
9。生产和交货时间表
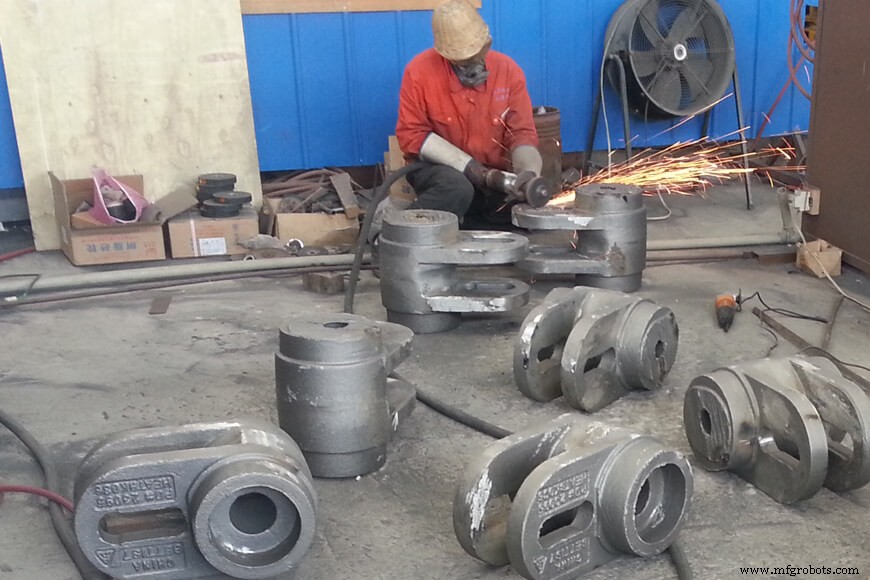
交付和需求要求的沟通对于找到合适的商店以满足短期和长期需求至关重要。
除了上述所有其他考虑因素外,客户和供应商都必须了解生产计划的需求。例如,如果客户要求在六周内交付生产零件,这将大大限制愿意或有能力对此类工作进行报价的代工厂数量——更不用说在如此紧迫的时间内可靠地进行生产了。相反,如果客户正在寻找感兴趣的代工厂来审查他们详细的长期需求(例如,每年 600 件零件“x”,每个订单生产 150 件,初始生产运行需要不早于六个月后),然后他们会发现更多有兴趣并有能力满足他们需求的各方。
报价请求应在要求的交货日期之前提出。由于金属铸造工艺的复杂性,一旦订购了铸件,项目交付周期可以轻松运行长达 24 周,直至全面生产和交付。这段时间可能包括商业考虑(财务管理)、样板和模具构建、取样、检查、样板更改、(完整)生产设置、生产、后期制作流程等。
订购铸件
合作努力对于金属铸造项目的成功外包至关重要 - 供应商铸造厂应参与从设计的早期阶段到制造和产品交付。
一旦供应商代工厂审查了报价请求,他们将与客户一起评估所有成本并确定产品目标。良好的规划对铸造厂和客户都有好处,因为铸造专家会在生产前对项目进行评估,并会推荐最佳材料和方法以实现最经济的解决方案。
通过向铸造厂提供有关其铸造需求的最准确和最详细的信息,客户可以期望收到大量反馈、问题,以及(一旦确认详细信息)来自相关方的定价。适当的准备可以简化订购流程,节省时间并降低产品出错的可能性。
制造工艺