高效铣削简介
以下只是与高效铣削相关的几篇博文之一。要全面了解这种流行的加工方法,请查看下面的任何其他 HEM 帖子!
高速加工与 HEM I 如何防止切屑变薄 I 深入切削深度 I 如何避免 4 种主要类型的刀具磨损 I 摆线铣削简介
高效铣削 (HEM) 是一种在金属加工行业迅速普及的策略。大多数 CAM 包现在都提供模块来生成 HEM 刀具路径,每个都有自己的专有名称。在这些软件包中,HEM 也可以称为动态铣削或高效加工等。 HEM 可以显着提高车间效率、延长刀具寿命、提高性能并节省成本。旨在实现更高速度和进给的高性能立铣刀将帮助机械师充分利用这种流行的加工方法的优势。
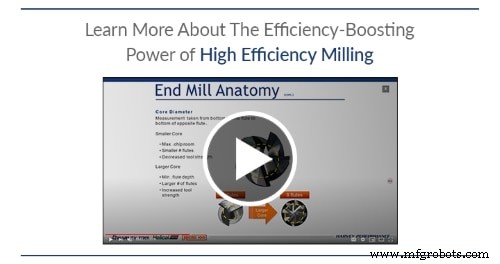
高效铣削定义
HEM 是一种粗加工铣削技术,它利用较低的径向切削深度 (RDOC) 和较高的轴向切削深度 (ADOC)。这样可以将磨损均匀地分布在切削刃上,散发热量,并减少刀具故障的机会。
这种策略不同于传统或传统铣削,后者通常需要更高的 RDOC 和更低的 ADOC。传统铣削会导致切削刀具的一小部分热量集中,从而加速刀具磨损过程。此外,虽然传统铣削需要更多的轴向走刀,但 HEM 刀具路径使用更多的径向走刀。
有关优化与 HEM 相关的切割深度的更多信息,请参阅深入了解切割深度:外围、开槽和 HEM 方法。
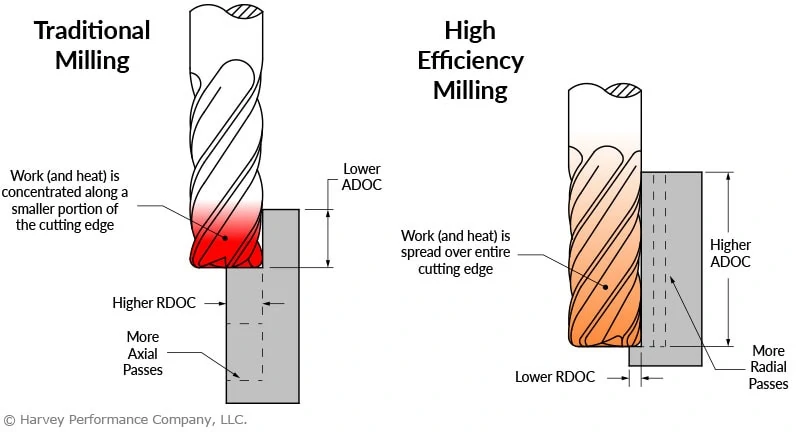
内置 CAM 应用程序
随着更快、更强大的机器的发展,加工技术一直在进步。为了跟上步伐,许多 CAM 应用程序都为 HEM 刀具路径开发了内置功能,包括摆线铣削,这是一种用于创建比刀具切削直径更宽的槽的加工方法。
HEM 主要基于围绕径向切屑变薄的理论,或随 RDOC 变化而发生的现象,并且与切屑厚度和每齿进给量有关。 HEM 调整参数以在整个粗加工操作中保持刀具上的恒定负载,从而提高材料去除率 (MRR)。通过这种方式,HEM 不同于其他高性能刀具路径,后者涉及实现显着 MRR 的不同方法。
点击此处了解更多关于高效铣削的效率提升能力
几乎任何 CNC 机床都可以执行 HEM——关键是快速的 CNC 控制器。从常规程序转换为 HEM 时,每行常规代码将编写大约 20 行 HEM 代码。需要一个快速处理器来提前查找代码并跟上操作。此外,还需要先进的CAM软件,通过调整IPT和RDOC来智能管理刀具负载。
高效铣削案例研究
以下示例显示了机械师使用 Helical Solutions HEV-5 工具在 17-4PH 不锈钢中执行 HEM 操作时的结果。在执行 HEM 时,这种直径为 ½ 英寸的 5 刃立铣刀在径向上仅与零件接合 12%,但在轴向上接合率为 100%。该机械师能够减少刀具磨损,并且能够使用单个刀具完成 40 个零件,而使用传统粗加工刀具路径只能完成 15 个零件。
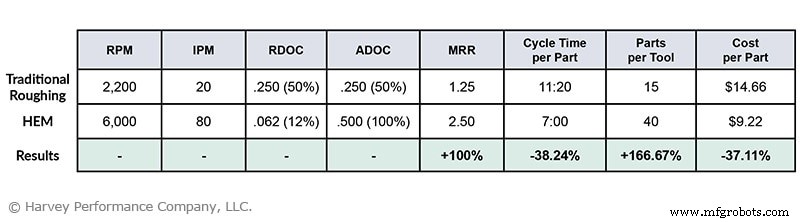
HEM 对粗加工应用的影响也可以在下面的案例研究中看到。在使用 Helical 的 H45AL-C-3(一种 1/2 英寸、3 刃粗加工机)加工 6061 铝时,这位机械师能够在 3 分钟内完成零件,而使用传统粗加工刀具路径需要 11 分钟。一种工具能够使用 HEM 制造 900 个零件,比传统方法提高了 150% 以上。
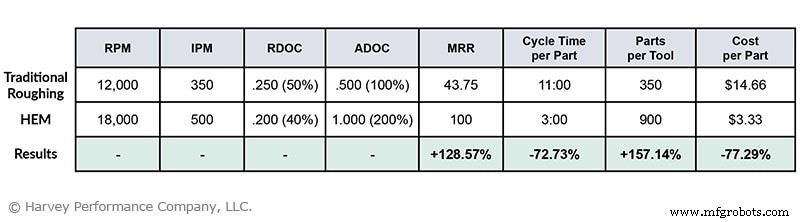
工具对 HEM 的重要性
一般来说,HEM 是运行工具的问题,而不是工具本身。几乎所有工具都可以 执行 HEM,但使用能够承受 HEM 严苛条件的工具将取得更大的成功。虽然您可以穿着任何类型的鞋子参加马拉松比赛,但您可能会从跑鞋中获得最佳成绩和性能。
HEM 通常被认为是大直径刀具的一种加工方法,因为该加工方法具有激进的 MRR 以及尺寸在 1/8 英寸以下的刀具的脆弱性。但是,也可以使用微型工具来实现 HEM。
为 HEM 使用微型工具可能会带来额外的挑战,在开始操作之前必须了解这些挑战。
HEM 的最佳工具:
- 高刃数可提高 MRR。
- 加大芯径以增加强度。
- 针对工件材料优化的刀具涂层以提高润滑性。
- 可变音高/可变螺旋设计可减少谐波。
关键要点
HEM 是一种加工操作,在世界各地的商店中越来越受欢迎。与传统铣削相比,HEM 是一种粗加工铣削技术,它使用更低的 RDOC 和更高的 ADOC,在刀具的切削刃上均匀分布磨损,减少热量集中并减缓刀具磨损速度。在最适合提升 HEM 优势的工具中尤其如此。
数控机床