如何优化汽车行业的铝加工
随着汽车行业越来越多地使用铝制造的发动机、动力总成、水泵和制动系统部件,OEM 及其供应链合作伙伴面临的挑战是提供更高效的铣削操作。刀具选择是该领域真正实现市场差异化的关键,在整个发动机部件加工操作范围内正确应用优化的铣刀可以带来显着的收益。
用于传统乘用车和混合动力乘用车的铝制发动机的生产数量继续同比增长。事实上,现在每年生产近 1 亿个。这些发动机容纳的零件通常形状复杂,并且在铸造后需要一系列不同但必不可少的铣削操作。
山特维克可乐满现在拥有一整套用于汽车行业铝材加工的产品,从第一阶段的立方加工到粗加工、半精加工和精加工。每个工程铣刀,总共五个,旨在提供优化的质量和每个零件的成本。为了帮助实现后者,该系列中的某些刀具完成了多项任务,例如在一次操作中同时执行粗加工和精加工以缩短循环时间。
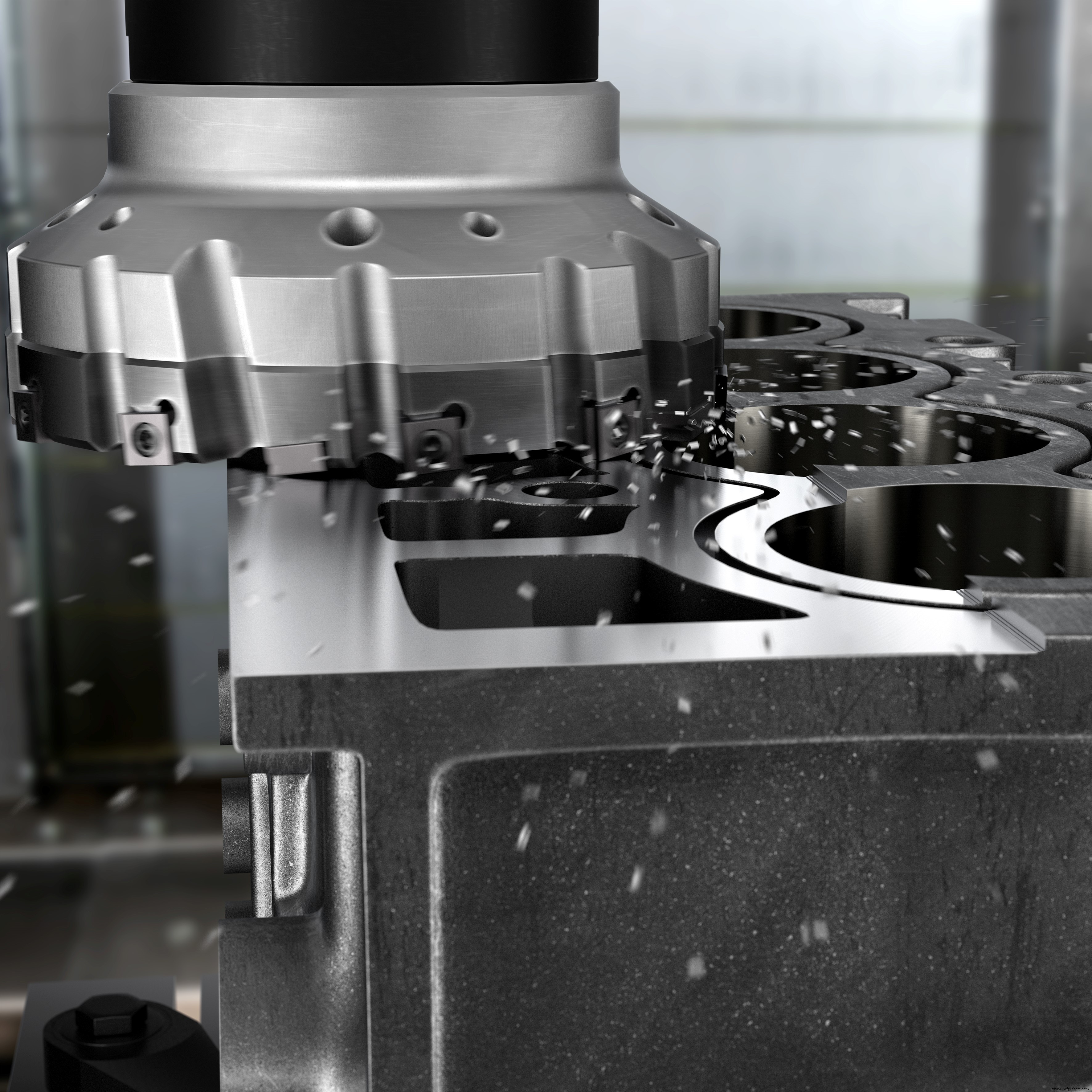
M5C90 就是一个很好的例子,它是一种结合了粗加工和半精加工成一个工具。 M5C90 是一种高速端面铣刀,专为消除客户设施的冗长设置时间而定制。与传统刀具相比,M5C90 的齿数减少,这主要是由于其精加工行/内径上独特的径向和轴向刀片定位(无需刀片调整)。这种定位确保了气缸盖、气缸体、制动系统零件和所有铝制部件的无毛刺铣削和最佳表面光洁度,可以实现宽刀具啮合(不适用于薄壁零件)。
为了提供使用 M5C90 的潜在收益的示例,请考虑正在进行的客户案例试验,该试验涉及由 AlSi12Cu1 制成的制动系统阀体。该刀具具有 10 个硬质合金刀片的外径阵列和 4 个内径的刀片(外加一个 Wiper 刀片),以 8000 RPM 的主轴速度和 4021 m/min 的切削速度进行部署。 (13,192 英尺/分钟)和 0.25 毫米/齿(0.009 英寸/齿)的进给量。此外,轴向切深为 2 毫米(0.078 英寸),径向切深为 140 毫米(5.51 英寸),金属去除率为 5600 厘米 3 /分钟。 (342 英寸 3 /分钟)。虽然刀具的总寿命尚未确定,但同样的刀具在使用 18 个月后仍在机器内。
对于那些需要刀具还可以加工薄壁铝制零件(如变速箱外壳和外壳)的人,山特维克可乐满提供了另一种同样有效的刀具,即 M5F90。 M5F90 是另一种一次性粗加工和精加工刀具。专用于薄壁铝零件的加工和锪孔加工,刀体(25-80 毫米,直径 0.98-3.15 英寸)装有钎焊 PCD 刀尖。每个尖端都包含一个粗加工边缘和一个精加工边缘。粗加工区域作为传统铣刀,所有切削刃具有相同的直径和高度,而精加工区域由径向和轴向阶梯切削刃组成。这一概念使紧密的间距能够提供无毛刺加工和出色的表面光洁度。 在下面的短视频中,山特维克展示了用于汽车铝加工的 M5 系列铣刀。
可以显着节省时间,正如客户案例试验所证明的那样,该案例试验涉及铝(高硅含量)气缸盖的面铣。在这里,将 M5F90 与竞争对手制造的特殊 PCD 刀具一起使用,不仅节省了 150% 的循环时间,而且消除了毛刺的产生。切削数据包括:15,915 RPM 主轴转速; 2000 米/分钟。 (6562 英尺/分钟)切割速度;进给率为 0.16 毫米/齿(0.006 英寸/齿);和 1.5 毫米(0.06 英寸)的切削深度。
在另一个 M5F90 示例中,与使用竞争对手的具有六个 PCD 刀片的 63 毫米(2.48 英寸)直径可转位刀具相比,铝制链条箱的循环时间减少了 44%。更重要的是,该解决方案消除了之前需要的刷毛去毛刺操作。
另一种新的工程工具是 M610,它被开发用于铣削具有双金属接口的发动机气缸体的甲板面/顶部,通常是铝和灰口铸铁 (CGI)。
在双金属材料方面,一系列热性能和机械性能使得加工具有挑战性。用于该应用的现有铣刀很复杂,需要进行调整,从而导致生产率下降。此外,此类工具通常会导致组件的 GCI 部分出现碎屑。
相比之下,M610 无需设置和调整,因此可以部署高进给率而不会出现碎屑、毛刺或刮伤零件。这种能力很重要,因为表面缺陷有可能在气缸体和气缸盖之间产生泄漏,从而影响动力和性能。一些全球汽车 OEM 已经从采用 M610 中受益。
参考一位特定客户,在完成双金属发动机缸体的燃烧面时获得了巨大的竞争优势。与竞争对手的带刀夹的可调刀具相比,M610 与竞争对手的 480 刀具相比,刀具寿命提高了 833%,完成了 4000 多个零件。此外,M610 的速度提高了 10 倍。 15 刀片 M610 的切削数据包括:3000 m/min。 (9843 英尺/分钟)切割速度;进给速度为 5720 毫米/分钟。 (225 英寸/分钟);主轴转速 3820 RPM;进给率为 0.15 毫米/齿(0.006 英寸/齿);铝的切削深度为 0.5 毫米(0.02 英寸),铸铁的切削深度为 0.05 毫米(0.002 英寸)。
该系列中的其他工具包括 M5Q90 切向粗加工刀具,它在一次操作中执行第一阶段立方(铸造后的第一次加工)而不会产生毛刺。该刀具配有 PCD 切向刀片,可提供平滑稳定的切削动作,从而降低功耗并消除振动。
铝制气缸盖和缸体是受益于 M5Q90 的组件之一。举例来说,铸造气缸盖上的立方加工操作通常包括加工凸轮轴面、入口/出口面和燃烧面。在客户案例研究中,在卧式加工中心上对由 AS-9 铝合金铸造的气缸盖进行粗面铣削产生了令人印象深刻的刀具寿命结果。以 3000 米/分钟的速度。 (9843 in./min.) 切削速度,每齿进给 0.2 mm (0.008 in.) 和 2.0 mm (0.079 in.) 轴向切削深度(完全啮合到 40 mm (1.57 in.),超过 10,000 个零件完成了。
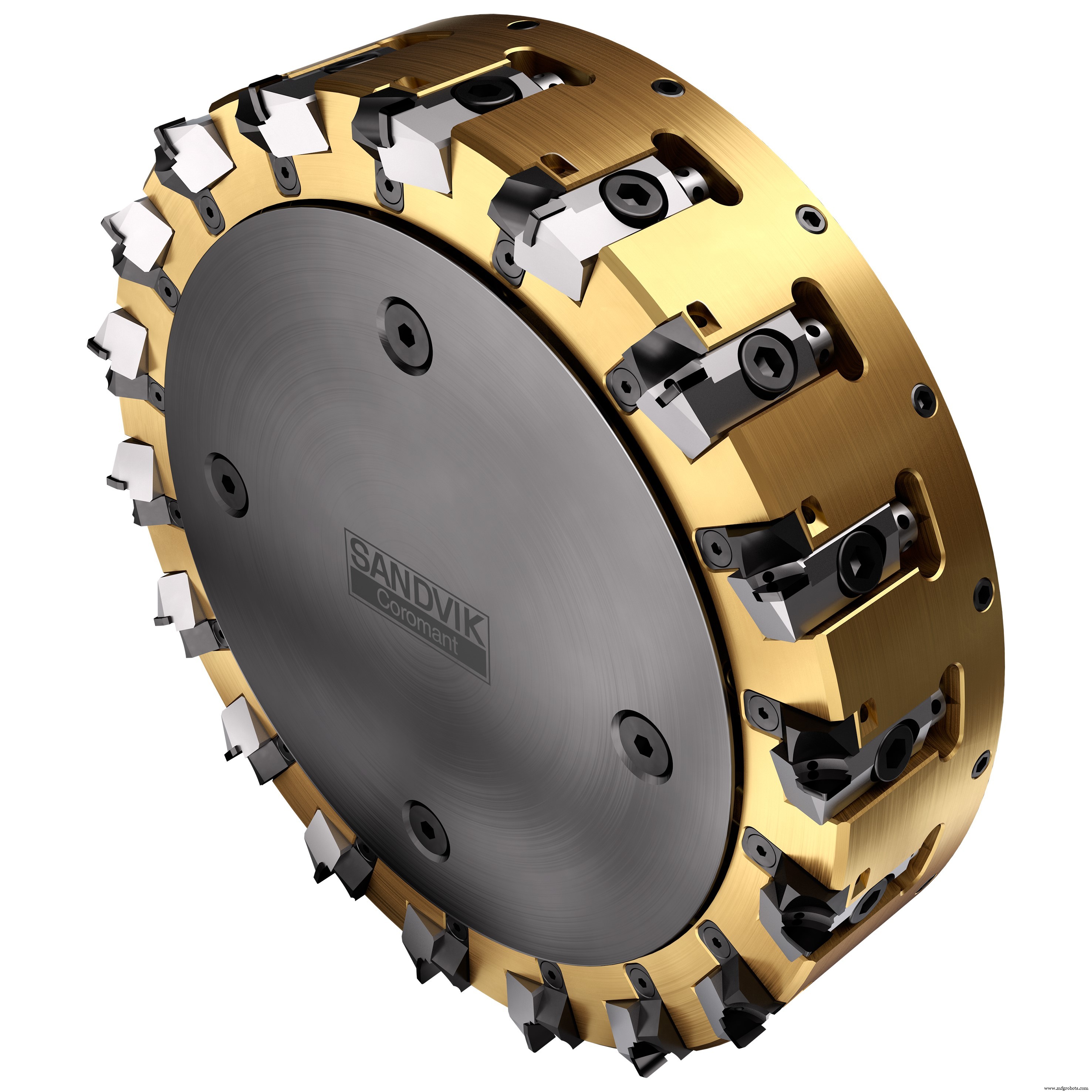
另一个工具是用于第二阶段粗加工/半精加工的 M5R90。此标准刀具与可调节刀片配合使用,支持最大 8 毫米(0.315 英寸)的切削深度,半径为 0.4 或 0.8 毫米(0.016 或 0.031 英寸),具体取决于所使用的刀片。易于调整的刀夹在许多汽车应用中都大有裨益,最近的客户试验涉及发动机盖的端面铣削就可以看出这一点。 M5R90 由 MRHB Si12 铝合金铸造而成,与现有的竞争对手刀具相比表现极为出色。基于相同的切削数据,M5R90 将刀具寿命从 8000 个工件延长到 10,000 个工件。此外,由于刀盘移动会影响表面光洁度,因此竞争对手的刀具需要在每加工 1000 个零件后进行调整。相比之下,M5R90 在需要对墨盒进行任何调整之前就生产了 8000 个零件。
该系列还包括 M5B90 超精加工面铣刀,它具有独特的刀片轴向和径向定位。正如最近乘用车气缸盖制造商发现的那样,这种配置与修光刃刀片一起确保了无毛刺切削和出色的表面质量。该公司遇到了工艺不稳定和毛刺问题,而另一个问题是无法预测的刀片寿命,这取决于不同设置的墨盒调整。改用 M5B90 刀具提供了平滑的精加工操作,具有可预测的磨损和无毛刺。该工具仅产生非常薄的切屑,这些切屑在切削过程中很容易去除,以避免对部件表面造成任何损坏。此外,更换为 M5B90 后,刀具寿命平均从 30,000 个零件延长至 45,000 个零件。
CoroDrill ® 和 CoroTap ® 与标准 CoroMill ® 一样,系列钻孔和攻丝工具也可以作为加工铝制汽车部件的同一系列解决方案的一部分提供给客户 Century 590面铣精铣刀。
在所有情况下,减少循环时间和每个零件成本,同时提高刀具寿命和质量的潜力是非常现实的,正如所描述的客户案例示例所见。在大批量生产盛行的汽车行业,即使是周期时间的一小部分节省也可能等同于可观的财务回报。考虑到这一点,任何能够证明能够带来更大收益的技术都不容忽视。
工业技术