17 第 7 章:精益制造
目标
完成本单元后,您应该能够:
- 在任何机械车间实施 5S。
- 描述改善理念。
- 描述实施精益制造。
精益 5S:
“5S”是一种工作场所组织方法,由五个词组成:排序、有序、闪耀、标准化和维持。所有这些词都以字母 S 开头。这五个组成部分描述了如何存储物品和维护新秩序。在做决定时,员工讨论标准化,这将使工作流程在工人之间变得清晰。通过这样做,每个员工都会感受到流程的主人翁精神。
第 0 阶段:安全
人们通常认为正确执行的 5S 计划会提高工作场所的安全性,但这是错误的。安全不是一种选择;这是一个优先事项。
第 1 阶段:排序
审查工作场所的所有物品,只保留需要的物品。
第 2 阶段:拉直
一切都应该有一个地方并就位。物品应分开并贴上标签。一切都应该周到安排。员工不应重复弯腰。将设备放置在使用的地方附近。这一步是精益 5 不被视为“标准化清理”的部分原因。
第 3 阶段:闪耀
确保工作场所干净整洁。通过这样做,将更容易知道事物在哪里以及它们应该在哪里。工作后,清理工作区并将所有东西恢复到原来的位置。保持工作场所清洁应融入日常生活。
第 4 阶段:标准化
标准化工作程序并使其保持一致。在执行前三个步骤时,每个工人都应该清楚自己的责任。
第 5 阶段:维持
评估和维护标准。上述步骤应成为新的操作规范。不要逐渐回到旧的方式。在参与新程序时,想办法改进。当出现新工具或输出需求时,回顾前四个步骤。
改善
精益 5S 流程侧重于消除浪费,而 Kaizen 侧重于持续改进的实践。与精益 5S 一样,Kaizen 确定了工作场所的三个主要方面:M uda(废物),M ura(不一致)和 M uri(对人和机器的压力)。但是,Kaizen 逐步流程比精益 5S 流程更广泛。
Kaizen 流程概览:
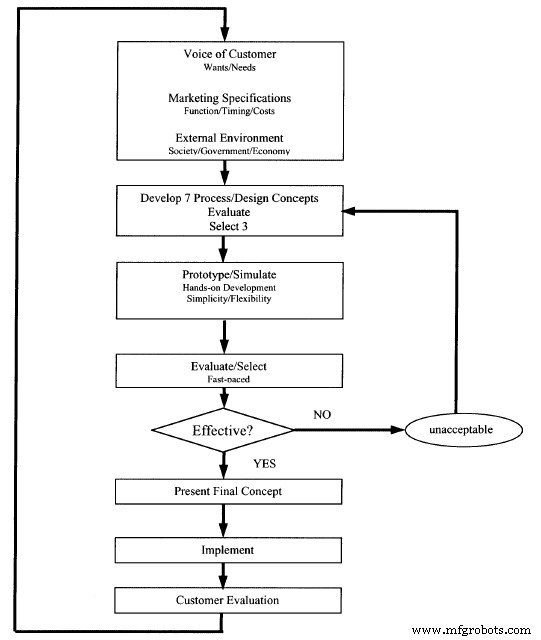
1. 发现问题。
2.组建团队。
3. 收集内外部客户信息,确定项目目标。
4.回顾当前的情况或过程。
5. 集思广益并考虑七种可能的替代方案。
6. 决定七个中的三个最佳选择。
7. 在实施前对这些备选方案进行模拟和评估。
8. 向管理者提出想法和建议。
9. 物理实施改善结果并考虑效果。
精益制造会随着时间的推移而改进,因此继续进行有关保持标准的教育非常重要。当出现新设备或新规则时,改变标准和培训工人至关重要。
精益
将维护部门想象为为内部客户服务:公司的各个部门和员工。
精益不同于依靠规模经济创造利润的传统西方大规模生产模式。你做的越多,产品就越便宜,潜在的利润率就越大。它基于对客户需求的预测,或创造客户需求。它难以应对需求的异常变化。
精益生产响应经过验证的客户需求。拉动加工——客户拉动生产。在大规模系统中,生产者将产品推向市场,推动加工。
建立一种注重改进的长期文化。
尊重受过更好培训和教育、更灵活的工人
精益是一种专注于以下方面的哲学:
- 满足客户需求
- 持续、渐进的改进
- 不断制造更好的产品
- 重视员工的投入
- 着眼长远
- 消除错误
- 消除浪费
浪费:使用太多资源(材料、时间、精力、空间、金钱、人力资源、糟糕的指导)
废物:
- 生产过剩
- 缺陷
- 不必要的处理
- 等待(浪费时间)
- 浪费人的时间和才能
- 步数过多或四处走动交通过多
- 库存过多
精益生产包括与供应商、分包商和销售商合作,简化整个流程。
目标是使生产顺利进行,避免代价高昂的启动和停止。
这个想法被称为“及时生产”,“只生产需要的东西,在需要的时候,只生产需要的数量。”生产过程必须灵活快速。
库存 =正是您所需要的
在大规模生产中=以防万一。储存额外的用品和产品以备不时之需。
术语:
流程简化——生产流程之外的流程
缺陷——批量生产系统在生产结束时进行检查,以在发货前发现缺陷。问题是资源已经被“花费”在制造废品上”尝试立即预防问题,当它们发生时,然后阻止它们。在生产过程中,在生产的每个阶段进行检查。
安全——伤害时间就是浪费时间
信息——在正确的时间需要正确的信息(太多、太少、太晚)
原则:
Poka-yoke – 防错确定问题的原因,然后消除原因以防止进一步的错误
判断错误——过程后发现问题
信息化检查——分析过程中的检查数据
源头检验——流程开始前的检验,以防出错。
平均精益
一个术语适用于简单的成本削减,精益的工作削减解释是平均精益。现代管理者常常认为他们在做精益,却不了解员工和长期关系的重要性。
以可靠性为中心的维护
以可靠性为中心的维护是一种用于设计具有成本效益的维护计划的系统。它可以是一个详细的复杂的、计算机的、统计驱动的,但在它的基础上它是相当简单的。它的思想可以应用于 PM 系统的设计和操作,也可以在您进行维护、故障排除、维修和能源工作时指导您的学习。
这些是 RCM 的核心原则。这九个基本概念是:
- 会发生故障。
- 并非所有故障的概率都相同
- 并非所有失败都会产生相同的后果
- 简单的组件磨损,复杂的系统崩溃
- 良好的维护以最低的实际成本提供所需的功能
- 维护只能实现设备固有的设计可靠性
- 不必要的维护会占用必要维护的资源
- 良好的维护计划会不断改进。
维护包括为确保组件、设备和系统在需要时提供其预期功能而采取的所有措施。
RCM 系统基于回答以下问题:
1、设备的功能和性能要求标准是什么?
2. 它在哪些方面不能履行其职能? (哪些是最可能的失败?每种失败的可能性有多大?失败会很明显吗?会不会是部分失败?)
3. 每次失败的原因是什么?
4. 每次故障发生时会发生什么? (有什么风险、危险等?)
5. 每次失败的重要性如何?全部或部分失败的后果是什么?
6. 可以做些什么来预测或防止每次故障?预测或预防每次故障的成本是多少?
7. 如果找不到合适的主动任务(默认操作)应该怎么做(可能没有任务可用,或者风险成本太高)?
设备的研究是在何时何地以及如何使用的背景下进行的
所有维护操作都可以归为以下类别之一:
- 纠正性维护 - 恢复丢失或退化的功能
- 预防性维护 - 最大限度地减少功能故障的机会
- 替代性维护 - 通过更改系统设计或使用来消除不满意的状况
在预防性维护类别中,完成的所有任务都可以描述为属于五 (5) 种主要任务类型之一:
- 条件导向 - 根据测量条件与标准相比更新寿命
- Time Directed – 无论状况如何,都能重获新生
- 故障查找 - 确定是否发生故障
- 服务 - 添加/补充消耗品
- 润滑 – 油、油脂或其他润滑方式
我们进行维护是因为我们相信硬件的可靠性会随着时间的推移而降低,但我们可以采取一些措施来恢复或保持最初的可靠性,从而为自己带来回报。
RCM 以可靠性为中心。其目标是保持系统或设备设计的固有可靠性,认识到固有可靠性的改变只能通过设计改变来实现。我们必须明白,设备或系统必须在其工作的情况下进行研究。
实施精益制造
在进行更改之前分析原始流程中的每个步骤
精益制造的主要重点是降低成本和增加营业额,并消除不会为制造过程增加价值的活动。基本上,精益制造所做的是通过引入易于应用和维护的工具和技术来帮助公司实现目标生产以及其他事情。这些工具和技术的作用是减少和消除浪费,这些在制造过程中不需要。
制造工程师着手使用 6 Sigma DMAIC(设计、测量、分析、改进、控制)方法——结合精益制造——来满足客户与管材生产相关的要求。
制造工程师负责设计管材生产线的新工艺布局。项目目标包括:
- 提高质量
- 减少废品
- 交付到使用点
- 小批量
- 实施拉动系统
- 更好的反馈
- 产量增加
- 个人责任
- 在制品减少
- 灵活用餐
在进行更改之前,团队对管材生产线流程的原始布局中的每个步骤进行了分析。
1.有尝试了解原始状态过程,找出问题区域,不必要的步骤和非增值。
2. 绘制流程后,精益团队从材料审查委员会(MRB)工作台收集数据,对主要缺陷类型进行测量和分析。为了更好地理解这个过程,团队还对 20 天的生产运行时间进行了研究。
在最初的状态下,该管道由一名操作员和四名操作员组成,由一张使用推送系统的大桌子分隔成两个工位。该表充当了第二个和第三个操作之间的分隔符。
发现的第一个问题是线路不平衡。大约 70% 的时间使用了第一个站点。第二站的操作员在循环时间之间花费大量时间等待。通过合并一号站和二号站,在个人责任、操作员对库存的控制以及出现问题时的即时反馈方面,改进的空间变得明显。时间研究和部门布局反映了这些发现。
认识到第二个问题。由于工艺流程,生产速度不允许两个工位满足生产计划。由于操作员失去了对机器周期的跟踪,机器正在等待操作员的注意。操作员还试图将零件推过第一个工位——过程中的瓶颈工序——然后在最后两个工序继续制造零件。通常情况下,WIP 会累积起来,直到生产出大量有缺陷的零件后才会发现质量问题。
原始状态数据取自更改前的最后 20 天。团队分析原始文件中的每个步骤并进行更改。对原始流程的时间研究结果为减少周期时间、平衡生产线、设计使用 Just In Time 看板和调度、提高质量、减少批量和 WIP 以及改善流程提供了基础。新工艺数据是在实施后一个月开始采集的。这种延迟让机器操作员有机会接受培训并熟悉新的流程布局系统。
采用U型电池设计;零件满足客户的所有要求。原流程中的表被去掉了,几乎消除了WIP。随着在制品的减少和产量的增加。
用于改进流程的一些概念包括员工全员参与 (TEI)、较小的批量、调度、使用点库存和改进的布局。该部门的所有员工和主管都参与了项目的各个阶段。他们的想法和建议被纳入规划和实施过程,以使过程变化得到更广泛的接受。引入了较小的批量,以最大限度地减少在检测到缺陷之前生产的零件数量。引入了看板(以物料搬运架的形式)来控制 WIP 并实施拉动系统。并且单元布局减少了操作之间的行程。
当出现问题时,操作员有权停止生产线。在原始状态下,当操作停止时,操作员仍在继续运行部件。带看板
控制,布局消除了存储 WIP 的能力,要求操作员关闭整条生产线。单元布局为改善运营商之间关于问题和调整的沟通提供了极好的机会,以实现更好的质量。
对原状流程的日常检查,操作人员花费大量时间要么等待物料搬运人,要么充当物料搬运。使用 U 型电池,操作员可以更好地交付到使用点。操作员将成箱的原材料放在六个可移动的滚轮车上,很容易拿到。这六个盒子足够使用 24 小时。
为了减少设置时间,机器维修和调整所需的工具位于单元中。螺丝不规范;工具按大小递增的顺序设置,以便快速识别合适的工具。
三个月来,该过程被监控以验证它是否处于控制之中。比较原始状态和实施布局的时间研究表明,每班生产的成品从 300 件增加到 514 件。新布局消除了第二道和第三道工序之间以及包装步骤之间的双重处理。它还通过使以拉系统顺序循环所有四个操作变得更容易来减少整个时间。两班倒满足客户需求,降低了人工成本。
重新设计的结果如下:
- 在制品减少了 97%
- 产量增加了 72%
- 废品减少了 43%
- 机器利用率提高了 50%
- 劳动力利用率提高了 25%
- 人工成本降低了 33%
- Sigma 等级从 2.6 提高到 2.8
This project yielded reduced labor and scrap costs, and allowed the organization to do a better job of making deliveries on time, while allowing a smaller finished-goods inventory. Daily production numbers and single-part cycle time served as a benchmark for monitoring progress towards the goal. Although the sigma level increase , the 43% reduction in defects, 97% reduction in WIP, and production increase of 72% contributed to the project objective.
Implementing lean is a never ending process; this is what continuous improvement is all
关于。 When you get one aspect of lean implemented, it can always be improved. Don’t get hung up on it, but don’t let things slip back to the starting point. There will always be time to go back and refine some of the processes.
Before Lean Manufacturing was implemented at Nypro Oregon Inc., we would operate using traditional manufacturing. Traditional manufacturing consists of producing all of a given product for the marketplace so as to never let the equipment idle. These goods them need to be warehoused or shipped out to a customer who may not be ready for them. If more is produced than can be sold, the products will be sold at a deep discount (often a loss) or simply scrapped. This can add up to an enormous amount waste. After implementing Lean Manufacturing concepts, our company uses just in time. Just in time refers to producing and delivering good in the amount required when the customer requires it and not before. In lean Manufacturing, the manufacture only produces what the customer wants, when they want it. This often a much more cost effective way of manufacturing when compared to high priced, high volume equipment.
Unit Test:
1. What is 5S?
2. Please Explain each “S” of the 5S.
3. Please Explain Kaizen concept.
4. What is the Pull processing?
5. What is the Poka-yoke?
6. What is the six-sigma DMAIC?
7. What is the objectives for a new process layout of the tube production line?
8. Before making changes, The Manufacturing engineers team do what first?
9. Please lists the results of the redesign.
10. The key to implementing lean new idea or concept is to do what?
CHAPTER ATTRIBUTION INFORMATION
This chapter was derived from the following sources.
- Lean 5S derived from Lean Manufacturing by various authors, CC:BY-SA 3.0.
- Kaizen derived from A Kaizen Based Approach for Cellular Manufacturing System Design:A Case Study by VirginiaTech, CC:BY-SA 4.0.
- Kaizen (image) derived from A Kaizen Based Approach for Cellular Manufacturing System Design:A Case Study by VirginiaTech, CC:BY-SA 4.0.
工业技术