面向生产服务专家的工业 4.0 软件
满足有效提高机器可用性的需求
上周,我与一位生产经理就工业 4.0 进行了深入讨论。他负责一家拥有约 500 名员工和约 150 台机器的工厂。像往常一样,这些机器是由许多不同的制造商在不同年份制造的。他问我工业 4.0 解决方案是否可以帮助他提高机器的可用性,以确保达到生产目标。他很想找到一种解决方案,让他的服务技术人员可以轻松使用——换句话说,不需要需要编程技能的复杂软件工具。
好消息是,对于配备力士乐控制系统的机器,我能够当场向他展示解决方案。由于开放核心工程 (OCE),软件功能可以直接访问 IndraMotion 控制单元。最重要的是,它不需要编写任何额外的 PLC 代码行。该功能可与PLC并行工作在任何设备上。
现在第一步是让控制系统传输有关其组件运行状态的可用数据。控制系统中的 OCE 技术接口将此信息发送到软件进行基于规则的分析——用户无需编写一行 PLC 代码,甚至无需触摸机器。
领先的维护技术人员 - 转向预测性维护
但仅凭这些数据还不能解决任何问题;它首先必须转化为信息和规则。这是由生产规则配置器完成的。例如,维修技术人员知道发动机扭矩的变化表明机械磨损。到目前为止,他们会定期检查每台机器并单独调用数据——这是一个非常耗时的过程。现在,服务技术人员将他们的知识转化为软件执行的规则:如果发动机的扭矩变化给定的量,系统会相应地通知维护组。服务技术人员不再需要手动调用每台机器的值,因为他们知道,只要有偏离规则的情况,他们就可以依靠软件立即通知他们。
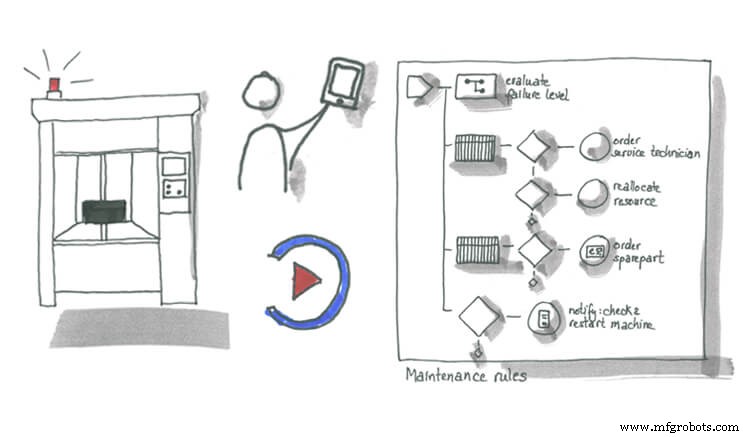
由维修技术人员建模的规则使用定义的公差值和趋势来快速检测此类偏差,并将其报告给适当的维修技术人员。对运行数据的持续基于规则的监控意味着可以动态调整服务间隔以适应实际磨损。在大多数情况下,这将大大降低服务成本,因为它消除了不必要的工作。另一个特别重要的考虑是规则可以方便地集成到现有 IT 系统中,独立于制造商。无需昂贵的培训,维修技术人员自己就可以在机器运行时更改现有规则、建模新规则,甚至将这些传输到控制系统。
数字助理提高了灵活性和速度
这些规则本质上是一个数字辅助系统,可帮助熟练的员工在正确的时间做出正确的决定。回到我们开始的地方:在我们的讨论中,生产经理最初持怀疑态度。他请来了维护组的一名服务技术人员,当我向他展示如何在没有编程知识且不接触 PLC 或机器的情况下在他的 PC 上定义规则时,他非常感兴趣。他称其为数字助理,可提高灵活性并加快维护响应时间。
维护只是可能的应用案例之一,一方面需要在机器的操作和生产数据之间建立联系,另一方面需要在业务流程和行动之间建立联系。并且不要忘记:不改变机器程序。
您能想到哪些应用程序用于生产中的基于规则的分析和支持?
工业技术