装配设计基础 (DFA)
术语“制造和装配设计”(DFMA)和“装配设计”(DFA)是指一组实践和原则,旨在根据给定的制造方法和在这样的情况下,调整产品开发的概念和设计阶段。确保生产和组装的简便性和成本效益的方式。
几十年来,DFA 框架采取了多种不同的形式,从 1970 年代开始。一项开创性的发展是日立的装配评估方法 (AEM),它使用点损失标准来评估特定产品(特别是自动装配)的装配难易程度。我们今天所知的“装配设计”概念是在 1977 年提出的,它制定了标准和策略来确定给定产品是否适合自动化装配,以及理想的装配系统和自动化程度。
设计用于装配的零件可能与改进其功能、质量和一致性相吻合。此外,坚持设计装配原则有助于减少必要的生产设备和零件库存(在许多情况下,这些次要优势实际上成为比降低装配成本更重要的卖点)。遵循 DFA 指南还有助于在产品周期的早期突出潜在的设计问题——这有助于简化原型制作过程并进一步降低生产费用。
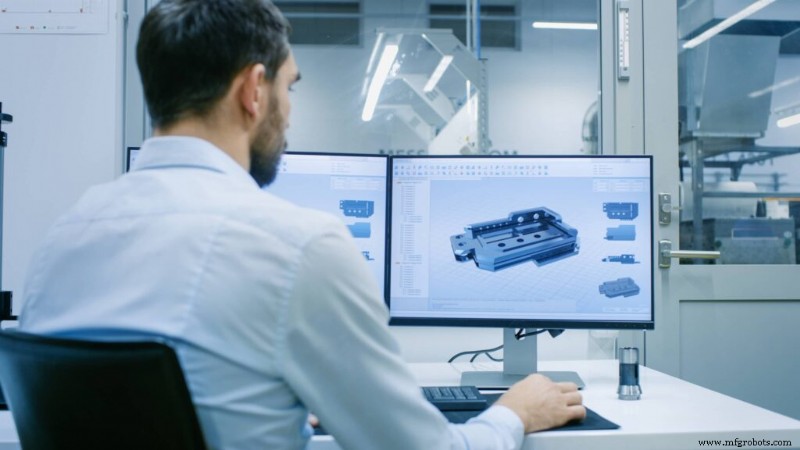
以下是关于如何开始将 DFA 原则纳入您的产品开发流程的快速入门:
尽量减少零件数量
DFA 的第一条规则?只要不影响零件的生存能力,就尽可能组合零件。更少的零件数量可以加快最终组装速度。
但是,最小化零件数量与消除零件中的特征不同。事实上,远非如此——这种做法有助于减少所需紧固件的数量并消除不必要的劳动力成本。
将紧固件构建到零件设计中
减少零件数量的一种具体方法是将紧固件直接结合到零件本身中(而不需要螺钉、螺栓或其他附加组件)。扣合和活动铰链是紧固件组装模板的两种常见设计,不需要任何额外的工具或专业设备即可构建。螺钉和紧固件可能是特定零件和应用的必需品,但一般来说,如果可能,它们应该被淘汰。
注意对称
关于对称和组装的一般准则:零件应该是对称的,以便在组装过程中易于定位,或者它们应该是明显不对称的,以便可以轻松挑选和定位。
避免设计左手或右手零件(因为这实际上会使您的工具需求翻倍),即使这会导致过时或不必要的功能,而这些功能不会影响零件的功能。
杜绝错误安装零件
在零件之间包括自对准功能以防止不同组件错误连接是提高装配过程效率的另一种方法。
紧固件因需要大量装配劳动力而臭名昭著。因此,确保每个零件的方向易于确定对于保持快速组装和成本效益至关重要。即使是像圆形零件上的凹槽这样简单的东西也可以大大简化流程。
优化您的容差
现代加工和工具设备能够实现非常严格的公差。然而,并非所有产品都能从如此严格的标准中受益——加工具有如此精确公差的零件和工具的成本很快就会变得异常昂贵和耗时,从而抵消任何成本或效率优势。
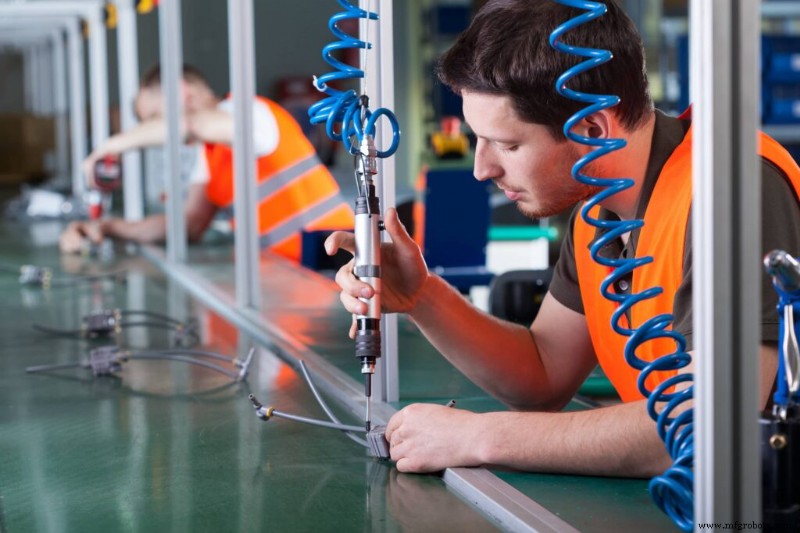
如果一个或多个组件不符合规格,则具有多个零件加工成极严格公差的组件也会增加性能问题的风险。允许您稍微放松一下公差通常有助于降低成本并同时提高设计的弹性。
使用 COTS 零件进行设计
顾名思义,商用现货 (COTS) 零件是您可以从供应商处购买的零件,而不是自己制造。常见的 COTS 零件包括外壳、弹簧、齿轮、销、传感器等组件。这些零件相当标准化,大多数装配工人和自动化装配解决方案都了解使用和装配它们的要求。
将您的定制加工和制造需求保持在最低限度有助于简化设计过程,同时还可以减少采购充足库存和原材料或组件的障碍。这种好处对于未来可能出现需求激增的零件尤其有价值。
跨程序集使用相同的工具
使用单一工具进行整个组装——或者更好的是,整个产品线——可以提高组装和拆卸的能源、劳动力和成本效率。
如果装配体在不同部分使用不同的螺钉或紧固件类型,则在装配过程中,每种附加的紧固件类型都需要额外的工具。不要将内六角头与内六角头混用。
发现确保您的零件符合 DFA 准则的可靠方法
在当今的随需应变世界中,有效应用制造和装配设计原则至关重要。然而,利用 DFMA 指南提供的全部优势通常需要兼顾许多因素——包括设计软件的选择和使用、应用程序的技术要求、环境因素、材料选择和采购、预算限制、紧迫的时间表等等。
与具有广泛设计和工程专业知识的按需制造商合作是在当今竞争激烈的市场中取得领先的关键。这就是快速半径出现的地方。我们为使新事物成为可能并利用最新和最好的技术以提高效率来改造久经考验的传统组件而感到自豪。我们还提供一系列产品咨询服务,帮助您开发和准备生产零件。立即联系我们了解更多信息。
工业技术